注射用重组人干扰素a2b工艺规程Word格式.docx
《注射用重组人干扰素a2b工艺规程Word格式.docx》由会员分享,可在线阅读,更多相关《注射用重组人干扰素a2b工艺规程Word格式.docx(29页珍藏版)》请在冰豆网上搜索。
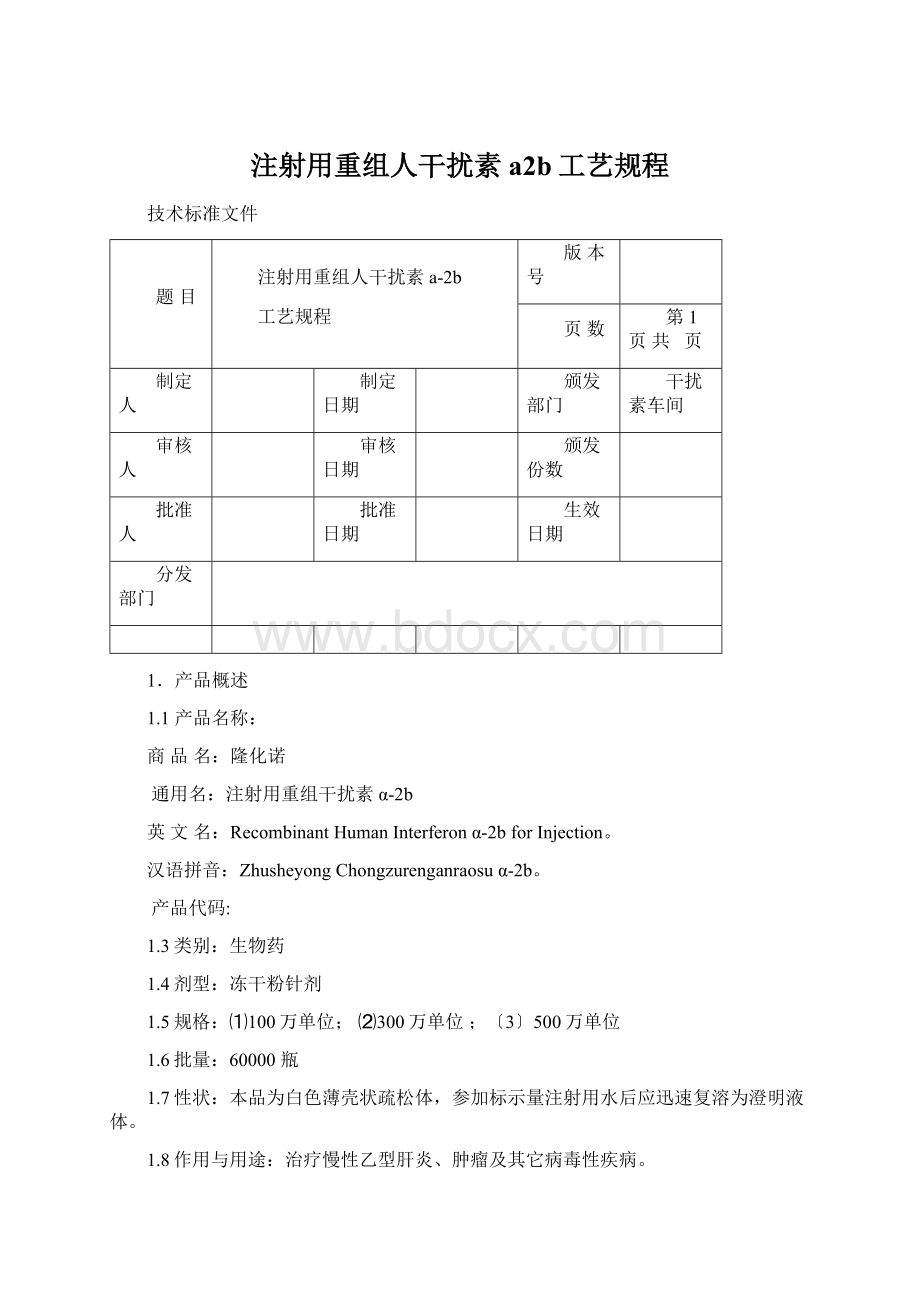
1.10贮藏:
2~8℃避光保存。
1有效期:
2年6个月
2批准文号:
100万单位:
国药准字S19980006;
300万单位国药准字S19980005;
500万单位国药准字S20000041;
3考前须知:
1.本品冻干制剂为白色疏松体,溶解后为无色透明液体,如遇有浑浊、沉淀等异常现象,那么不得使用。
包装瓶有损坏、过期失效不能使用。
1.13.2.以注射用水溶解时应沿瓶壁注入,以免产生气泡,溶解后宜于当日用完,不得放置保存。
1.14禁忌:
1.14.1.对重组人干扰素α-2b或该制剂的任何成分有过敏史。
1.14.2.患有严重心脏疾病。
1.14.3.严重的肝、肾或骨髓功能不正常者。
1.14.4.癫痫及中枢神经系统功能损伤者。
1.14.5.有其他严重疾病不能耐受本品者,不宜使用。
2.处方及处方依据:
规格:
100万单位/瓶;
批量:
60000瓶
批处方
投料量
重组干扰素α-2b
600亿单位
600亿单位/效价
人血白蛋白
2
2/效价
20%甘露醇
2/含量
Na2HPO4
51.96g
51.96g/含量
NaH2PO4
g
g/含量
注射用水加至
60000ml
规格:
300万单位/瓶;
1800亿单位
1800亿单位/效价
51.96g含量
g/含量
500万单位/瓶;
3000亿单位
3000亿单位/效价
2.2处方依据:
100万IU/瓶国药准字S19980006;
300万IU/瓶国药准字S19980005
500万IU/瓶国药准字S2*******
2.3生产批件:
药品GMP证书及生产批件复印件:
见附录
3.工艺
原辅料
说明
百级区
脱包消毒
万级区
备料a
十万级区
µ
m过滤器
压缩空气
配制b
注射用水
无菌过滤c
洗烘瓶e
胶塞清洗灭菌
灌装+半加塞d
冷冻枯燥f
西林瓶
胶塞
说明书
外包材
封箱捆轧
入库
标签
压塞
铝盖
主要检查工程
铝盖处理
轧盖
a称量检查
b配制系统SIP、CIP
目检
c过滤器灭菌+完好性
过滤后药液澄明度
d装量检查
贴签g
e洗瓶澄明度检查
f温度、真空度+时间
g标签数额平衡
装盒
装箱
3.2生产过程及技术参数
配料
仓库配料人员应认真对照生产领料单〔附件1〕核对原料“合格证〞上的代号、名称、规格、有效期,按生产领料单上物料品名及数量仔细称量,在生产核料单〔附件2〕和配料标签上注明物料的物料编码、名称、批号、重量,由QA中控人员监督复核生产核料单、重量、配料标签与封签,内容无误后,由配料人和复核人共同在生产领料单和核料单签字。
配料完毕交车间核料人员。
核料
车间核料人员接收生产核料单及由仓库配料间配封好的物料,认真核对物料的品名、规格、批号、重量等,进一步确证无误后,在生产核料单上车间收料处注明日期及签名。
将核准物料传递到原辅料暂存间。
由配料人员确认电子秤已经校正后,根据核料单上的领取数量核对领来的原辅料的种类、数量。
配制过滤
3.2.3.1主要设备为250L配制罐及过滤系统,所在区域为C级区。
3.2.3.2确认配制罐及过滤系统已灭菌,操作室无与生产无关的物品。
.3配制罐及过滤系统在线灭菌121℃、30min,对滤芯做完整性测试(μm≥μm≥)〔MILLIPORE〕。
3.2.3.4配制过滤过程
A.mol/L磷酸盐缓冲溶液。
B.mol/L磷酸盐缓冲溶液,甘露醇注射液、再参加人血白蛋白和适量的10℃以下注射用水,搅拌均匀,测pH值。
C.辅料溶液p—molmol/L磷酸溶液调节。
D.将处方量的原液参加配制好的辅料溶液中,加注射用水至规定体积,搅拌均匀测pH值。
药液p—molmol/L磷酸溶液调节。
μμm的过滤器精滤,通过管道输送至灌装间。
取50ml?
药液送质量部QC测pH值、可见异物和细菌内毒素。
中间体质量检验合格后,按标示量的100%计算装量。
F.过滤结束后,对过滤器进行气泡点试验,μm≥μm≥〔MILLIPORE〕
G.将可拆卸的部件送至清洗间清洗,将配制过滤系统在线清洗灭菌。
H.清场,去除与生产无关物品,清洁地面并去除废弃物,经检查合格后,挂上清场合格证。
3.2.3.5工艺技术要求:
A.工艺用水:
注射用水符合公司内控标准。
B.注射用水及氮气均应经0.22μm滤膜过滤。
C.配制好的药液应在6小时内除菌过滤结束;
除菌过滤后的药液应在6小时内灌装完毕。
D.除菌过滤器在使用前应清洗灭菌。
灭菌物品存放规定:
A.不锈钢盘、桶等工器具及灌装机部件经清洗、灭菌后应存放在百级层流下,且存放时间不得超过8小时,否那么应重新清洗、灭菌。
B.已灭菌的无菌服只能当班使用。
3.2.4洗瓶
3.2.4.1洗烘瓶:
主要设备为QCL40立式洗瓶机和KSZ920/120A隧道式灭菌烘箱,所在区域为D级洁净区,隧道烘箱出口在灌装A级区。
3.2.4.2生产流程:
注射用水冲洗1次
压缩空气吹1次
循环水冲洗2次
循环水超声波清洗
管制抗生素瓶
瓶
冷却
330℃灭菌
压缩空气吹2次
灌装
3.2.4.3生产过程:
A.理瓶
---根据内包材配料/核料单核对领取批量的2ml管制抗生素瓶;
---在理瓶间〔控制区〕除去内包装,码盘过程中检查有无缺陷,经传递窗传入瓶暂存间。
B.生产前准备
---清场检查,更换模具;
---各传动部件检查,滤芯气泡点试验,水电气检查,超声波、循环泵和各管路检查;
---隧道烘箱网带检查,往清洗槽注水,更换本批生产状态标志,准备生产。
C.清洗灭菌操作
---将隧道式干热灭菌器翻开预热,设定灭菌温度330℃;
---翻开洗瓶机超声波,开启循环泵、增压泵和相关清洗管路,按生产流程进行清洗、灭菌、枯燥。
D.生产操作全过程应随时注意观察设备的运行状况和各仪表指示变化,发现异常及时报告并妥善处理,保证生产的正常进行。
E.停机
---停止洗瓶相关操作,关闭注射用水、压缩空气,清洗槽排空;
---隧道烘箱在管制抗生素瓶全部传出后进行“日间停止〞操作。
F.打印隧道烘箱灭菌记录,并将记录贴在批生产记录上。
G.记录:
认真、及时、完整填写批生产记录及其它相关记录。
H.清场
---将本批剩余未清洗瓶子退库;
---不锈钢盘、工器具等清洗消毒后保存;
---滤芯气泡点试验;
---清洁设备外表、墙面、地面、地漏等;
---清场结束由IPC人员检查并发放清场合格证。
3.2.4.4工艺技术要求:
A.工艺用水:
B.循环水经1.0μm过滤器过滤,注射用水及压缩空气经0.22μm过滤器过滤,每批生产前后均需作0.22μm滤芯完整性测试。
C.循环水压力0.2~0.4MPa,注射用水压力0.2~0.4MPa,压缩空气压力0.2~0.4MPa。
D.洗净的瓶子在传送时应有防止污染的措施,并应在2小时内灭菌。
E.灭菌后的瓶子应在100级层流下存放,并在8小时内使用完,否那么应重新清洗、灭菌。
3.2.5胶塞处理
.1主要设备为KJCS-5全自动胶塞清洗机,所在区域为C级洁净区,出料口在无菌万级区局部百级下。
.2生产流程:
出料
冷却70℃
枯燥
纯蒸汽灭菌121℃,30min
喷淋
注射精洗5min
.3生产过程:
A.根据内包材配料/核料单核对领取相应规格的胶塞,并核对数量。
B.生产前准备:
清场检查,滤芯气泡点试验,水电气检查,更换本批生产状态标志,准备生产。
C.参数设定及核对:
注射精洗时间
灭菌时间
灭菌温度
5分钟
30分钟
121℃
真空枯燥时间
真空枯燥循环次数
出料温度
15分钟
70℃
D.加料:
将胶塞放入进料桶中,真空吸料。
E.清洗灭菌:
按设定程序进行清洗、灭菌、枯燥。
F.生产操作全过程应随时注意观察设备的运行状况和各仪表指示变化,发现异常及时报告并妥善处理,保证生产的正常进行。
G.出料:
由无菌万级区的出料人员操作,设备运行结束后打印本批操作记录,并将其附在批生产记录中。
H.记录:
及时、准确、完整地填写批生产记录及其它相关记录。
I.清场
---将本批剩余胶塞退库,清洗胶塞机腔体;
---清场结束由QA人员检查并发放清场合格证。
.3工艺技术要求:
B.注射用水及压缩空气经过滤器过滤,生产前后均需作完整性测试。
C.灭菌后的胶塞应在100级层流下存放在洁净、枯燥、无菌的不锈钢桶内,并应在8小时内使用完。
3.2.6铝盖处理
3.2.6.1主要设备为KJCS-5全自动铝盖清洗机,所在区域为C级洁净区,出料口在百级区域。
3.2.6.2生产流程:
3.2.6.3生产过程:
A.根据内包材配料/核料单核对领取相应规格的铝盖,并核对数量。
清场检查,水电气检查,更换本批生产状态标志,准备生产。
将铝盖放入进料桶中,真空吸料。
由C级区的出料人员操作,设备运行结束后打印本批操作记录,并将其附在批生产记录中。
---将本批剩余铝盖退库,清洗铝盖机腔体;
3.2.6.4工艺技术要求:
纯化水符合公司内控标准。
B.压缩空气经过滤器过滤,生产前后均需作完整性测试。
C.灭菌后的铝盖应在100级层流下存放在洁净、枯燥、无菌的不锈钢桶内,并应在8小时内使用完。
3.2.7灌装加塞
主要设备为DGS-8灌装加塞机,所在区域为A级区。
3.2.7.1生产流程:
半压塞
灌装
管制抗生素瓶冲氮
3.2.7.2生产过程:
A.生产前准备
---清场检查,安装模具并用75%酒精擦拭;
---水电气、层流装置检查,终端滤芯气泡点试验,更换本批生产状态标志。
---从对开门烘箱取出已灭菌的工器具,安装振荡盘和陶瓷泵、连接灌装管路;
---胶塞出料后转移至百级下备用;
---与配制人员协作完成药液的压滤,将缓冲罐转移至灌装区百级下,与计量泵相连接;
---确认管制抗生素瓶清洗、枯燥灭菌合格〔由QA人员确认〕。
B.生产操作
---开启主机,排除系统内气泡;
---试装,检查可见异物及调节装量;
---启动输送带、理塞、真空泵,选择“无瓶不灌〞;
---调节灌装速度,在出料口将灌装好的产品整齐地排列在不锈钢盘内放入冻干机内。
---灌装过程每小时取1次样〔每次每灌装头1支,共8支〕,检查装量及可见异物。
C.灌装结束后,排出剩余药液,收集至容器中,贴上可回收标签传递至配制岗位存放。
D.终端滤芯气泡点试验。
E.记录:
F.清场
---将剩余胶塞、管制抗生素瓶收集清理,作报废处理;
---可拆卸部件及工器具传至非无菌万级区工器具清洗间进行清洗、灭菌;
---75%酒精清洁设备外表、墙面、地面、层流装置等;
3.2.7.3工艺技术要求
A.控制装量ml。
B.无可见异物。
3.2.8冻干
3.2.8.1主要设备为上海远东YO-20〔CIP.SIP〕型真空冷冻枯燥机
3.2.8.2生产流程:
保温
二次枯燥
预冻
一次升华
3.2.8.3生产过程:
---清场检查,确认设备已清洁、灭菌枯燥;
---检查设备各装置仪表的运行情况,更换本批生产状态标志,准备生产。
B.预冻:
依次开启循环泵、压缩机,对制品降温。
当制品温度降至≤-40℃时,设定导热油温度为-45℃保温2小时;
并对捕水器进行制冷,使其降温至-55℃以下。
C.一次升华:
依次开真空泵、小蝶阀、中隔阀、罗茨泵,选择掺气程序,设定真空度为15Pa,当前箱真空到达设定值时,将导热油温度设定为-20℃,保持1小时;
将导热油温度设定为0℃,保持1小时,将导热油温度设定为5℃,保持2小时,将导热油温度设定为10℃,保持2小时,将导热油温度设定为15℃,保持1小时,将导热油温度设定为20℃,保持1小时,观察制品的枯燥层和冻结层的交结面应到达瓶底并消失,否那么继续保温。
D.二次枯燥:
将导热油温度设置在35℃,保持4小时;
观察冻干曲线,制品温度曲线趋于平稳且接近设定温度30℃时,二次枯燥结束。
E.保温3小时。
F.保温结束前半小时关闭真空控制。
当前箱真空度≤2Pa时,关闭中隔阀,做压力上升试验,60秒内压力升高值应小于1Pa,否那么继续保温。
G.翻开中隔阀,自动压塞;
停机出料。
H.在线清洗:
出料结束后启动程序进行清洗。
I.记录:
J.清场
---清洁冻干机设备、墙面、门窗、地面、地漏等;
---清场结束由QA人员检查合格后发放清场合格证。
3.2.8.4工艺技术要求
A.生产全过程应密切注意温度和真空度的变化情况,并随时监控冻干曲线和冻干报表。
B.设备运行时密切注意压缩空气、冷冻水、纯蒸汽、注射用水等生产介质的供给情况,观察设备运行情况,防止设备受损或影响产品质量。
灭菌条件为:
121℃,30min;
清洗、灭菌有效期为24h。
.1主要设备为ZG-300C轧盖机,所在区域为C级区,进瓶端输送网带设局部百级层流装置。
.2生产过程:
A.根据内包材配料/核料单核对领取相应规格的铝塑组合盖,并核对数量。
B.生产前准备
---清场检查,动力电源检查;
---安装模具并用75%酒精擦拭,更换本批生产状态标志,准备生产。
C.轧盖操作:
调节理盖机速度使铝盖满布轨道,启动输送带,调节轧盖速度≤150瓶/分。
D.记录:
E.清场
---生产结束,将不合格品标明品名、批号、数量传至不合格品间;
---剩余铝盖用洁净塑料袋装好贴签退库;
---清洁设备外表、墙面、地面、输送带层流装置等;
.2工艺技术要求
A.初检:
紧密,不松动,边缘整齐,无切皮。
B.紧密性检查:
一手按瓶,一手大拇指、食指、中指卡住瓶盖边缘呈三角直立,向一方轻轻拧盖,以拧不动为合格。
灯检
.1冻干粉针在普通照明光环境下进行目检。
A.生产前准备:
清场检查,灯检仪器检查,更换本批生产状态标志,准备生产。
B.灯检:
---核对待检品名称、规格及数量;
---灯检工用各自的色标笔在铝盖上标记。
C.假设有以下情形作为不合格品处理:
---瓶子外观即瓶身、瓶底如有裂纹、瑕癖及瓶外壁不洁等。
---冻干药品外观有明显塌料、熔化现象。
---铝盖松动、裙边、皱折、卷边、铝盖轧破等封口不良。
---铝盖塑料局部松动较大、缺损、外形不规那么、较脏或混有其它类型的铝盖。
---检出色块、玻璃屑、纤维或其它异物。
D.灯检合格品插上“已合格〞标志、未检产品插上“待检〞标志。
灯检可回收品和不可回收品必须严格区分统计管理。
E.记录:
---如果一天不能检完,应将未检的产品送回原存瓶架,不合格品送至不合格品间并计数、登记、签名;
---检查合格的产品整齐码放在不锈钢盘中,放上合格标签,转入外包或贴上物料标签转入灯检暂存间上锁存放;
---清洁灯检台面、地面等;
清场结束由QA人员检查合格后,发放清场合格证。
A.灯检员视力应在以上,无色盲,每年检查一次。
B.灯检人员每2小时应休息一次,每次15分钟。
.11贴签包装
.11.1主要设备为KK916贴签机和批号打印机。
.11.2生产过程:
---清场检查,电源、压缩空气检查;
---检查贴签机、喷码机、打码机、打包机运行是否正常,更换本批生产状态标志。
B.领取包装材料
---由外包班长到仓库领取包装材料并核对品名、入库序号、规格、数量;
---将领来的瓶签、说明书、合格证放入标签柜内,小盒及大箱整齐地码放在外包材料存放间。
C.准备药品:
将待包装药品自灯检暂存间转入包装间,并核对品名、规格及数量。
D.贴签
---根据批包装指令在瓶签上刻印正确生产日期,有效期,批号;
---QA负责核对、检查,要求端正、适中、牢固,批号等清楚正确,字迹清晰。
E.打码
---小盒、大箱需喷印或打印产品的生产日期、批号、有效期;
---QA负责核对、检查,要求清晰准确、无遗漏。
F.包装:
将已贴标签的产品每10只放入1小盒中,并在小盒中放入1张说明书。
每个大箱装20个小盒和1张合格证。
G.装箱,包装规格:
100万单位×
40盒/箱;
300万单位×
40盒/箱。
H.合格证:
每箱1张,并按批包装指令刻品名、规格、批号、包装规格。
I.产品零头:
每批包装结束后产生的零头核对数量后,单独装箱,放入合格证,并在合格证上标明零头数量,外箱上贴上标签。
经QA人员核对后入库。
J.入库
---入库人员在仓库指定的库位将本批的产品码放整齐;
---与仓库相关人员进行交接,装零头的箱子应特殊说明,并核对入库数量;
---仓库管理人员复核验收后,在入库单上签字,并将入库单带回车间。
K.记录:
L.清场
---清点不合格品,用塑料袋装好,贴上标签,转入不合格品间;
---清点剩余及报废的标签、说明书、合格证数量及报废数量,将剩余的包装材料核实数量后,退库;
---将报废的包装材料核实数量后销毁;
---检查包装区域内无遗留产品、半成品、瓶签、说明书、合格证等包装材料;
---贴签机、打码机、打包机、操作台等;
---清洁墙面、门窗、地面等;
清场结束由QA人员检查合格后发放清场合格证。
A.如果同一批产品不能在同一天内包装结束,那么包装完的成品应在当天入库,未包装好的产品应记录数量后锁在存放柜里。
B.所有标签类文字材料需严格管理,控制包材偏差,防止包装材料在包装过程中流失。
岗位
洗瓶
洗塞
冻干
包装
人数
1
6
3
8
区域
灯检包装
级别
C级
D级
A/B级
A/C级
一般区
3.5生产过程质量控制要点:
工序
监控要点
频次
1.细菌内毒素≤
1次/周
2.电导率≤μs/cm
3.80℃以上保温或65℃以上保温循环
随时/每班
4.pH值、氯化物、铵盐
1次/2h
胶塞处理、
西林瓶洗涤
1.胶塞漂洗水澄明度白点毛点总数≤8个/150ml,水分≤3%
2.西林瓶灌装过滤水检查澄明度白点毛点总数≤3个/5瓶
配料称量
核对称量
每批
配制
1.在线清洗
2.在线灭菌
3.核对总体积
过滤
1.气泡点试验μm≥0.31MPa
μm≥0.24MPa〔MILLIPORE〕
过滤前后
2.清洗3.pH值4.中间体含量
灌装、加塞
1.过滤药液澄明度
2.灌装后澄明度
1次/h
3.灌装量检查
1次/30min
4.浮游菌监测
1.冻干曲线2.在线清洗3.在线灭菌
轧盖紧密度和外观
1.密封完好性
2.冻干制品外观检查
贴签、包装
1.标签数额平衡
2.包装质量检查
3.清场检查
成品
1.无菌
2.内毒素检查
3.化学工程检查
4.BPR
进入洁净区(室)人流和物流严格分开。
各工序生产结束后由岗位操作人员进行平衡率、收率的计算,防止产生偏差等事故。
发现计算收率与理论收率的比值超出了合理的范围,有显著差异,那么必须查明原因,在得出合理解释,确认无潜在质量事故后,经批准方可按正常产品处理或进行下一步的生产。
生产操作严格按工艺流程进行,各生产工序衔接合理。
每一生