注塑成型调校的主要参数Word下载.docx
《注塑成型调校的主要参数Word下载.docx》由会员分享,可在线阅读,更多相关《注塑成型调校的主要参数Word下载.docx(16页珍藏版)》请在冰豆网上搜索。
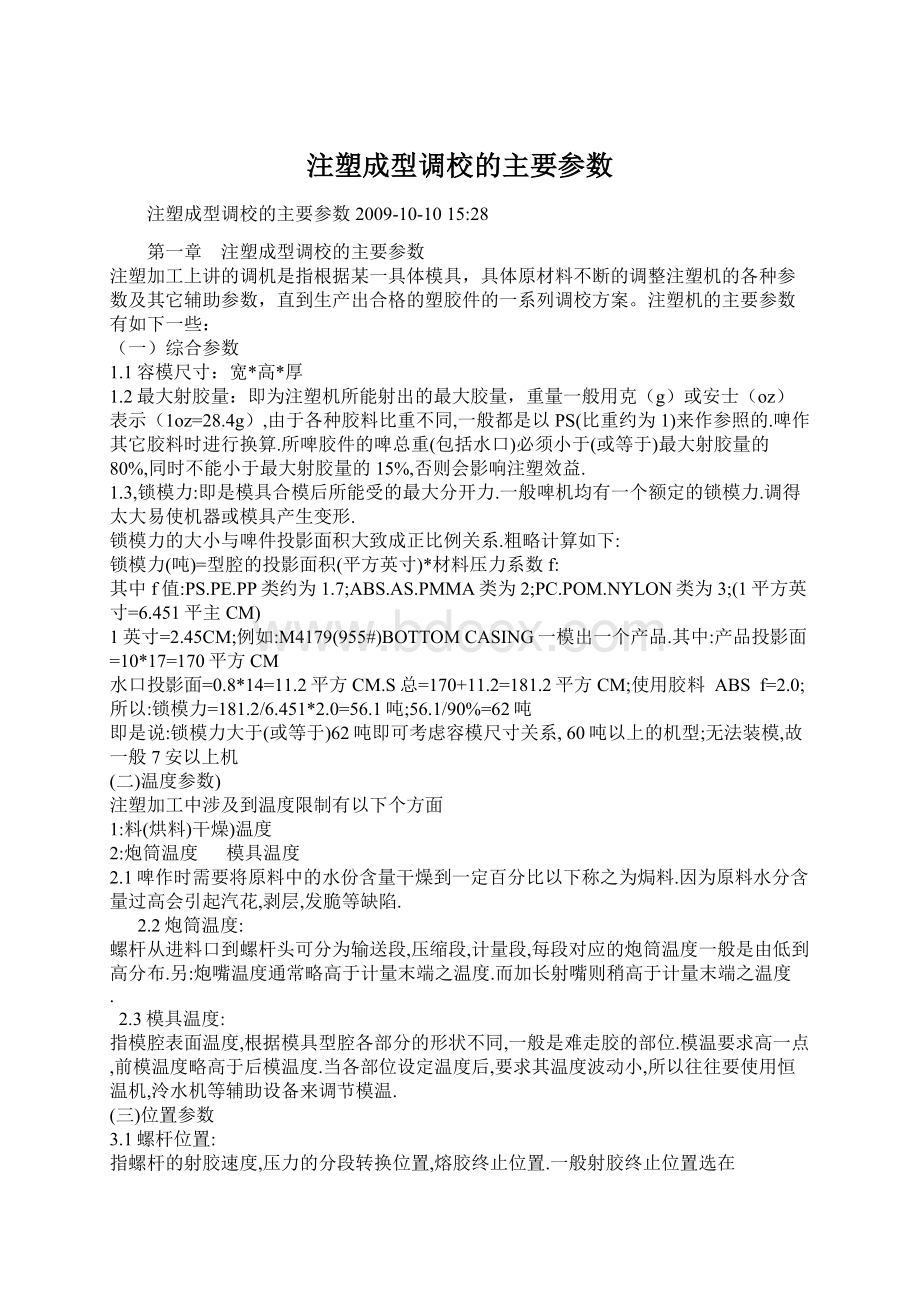
ABS
f=2.0;
所以:
锁模力=181.2/6.451*2.0=56.1吨;
56.1/90%=62吨
即是说:
锁模力大于(或等于)62吨即可考虑容模尺寸关系,60吨以上的机型;
无法装模,故一般7安以上机
(二)温度参数)
注塑加工中涉及到温度限制有以下个方面
1:
料(烘料)干燥)温度
2:
炮筒温度
模具温度
2.1啤作时需要将原料中的水份含量干燥到一定百分比以下称之为焗料.因为原料水分含量过高会引起汽花,剥层,发脆等缺陷.
2.2炮筒温度:
螺杆从进料口到螺杆头可分为输送段,压缩段,计量段,每段对应的炮筒温度一般是由低到高分布.另:
炮嘴温度通常略高于计量末端之温度.而加长射嘴则稍高于计量末端之温度.
2.3模具温度:
指模腔表面温度,根据模具型腔各部分的形状不同,一般是难走胶的部位.模温要求高一点,前模温度略高于后模温度.当各部位设定温度后,要求其温度波动小,所以往往要使用恒温机,泠水机等辅助设备来调节模温.
(三)位置参数
3.1螺杆位置:
指螺杆的射胶速度,压力的分段转换位置,熔胶终止位置.一般射胶终止位置选在10~20MM为宜
3.2索退位置
当螺杆回料完停止转动后,螺杆有一个向后松退的动作,称之为索退,一般索退距离为5MM左右,太大会产生汽泡等缺陷.
3.3开模位置
即后模面离开前模面的距离,其大小为能顺利取出胶件为宜,太大会延长周期.
3.4顶针位置
即为模具顶针顶出后模面的距离.使产品顶出后面且能顺利取出胶件为宜.注意不要使顶针顶到尽头,必须留有足够的余量,以免造成模具顶针板弹弓被顶断.
(四)压力参数)
4.1射胶压力
螺杆给予熔胶的推进力,称之为射胶压力,根据螺杆位置的各个分段,可设置螺杆不同的推进力给熔胶.各段推进力大小的设置,主要取决于熔胶在模具型腔里的位置,当流经的模腔形状复杂,胶位薄,熔胶受到的阻力就大,则需要较大的的推进力;
当流经的位置形状简单,熔胶受到的阻力小,则可设置小的推进力,从而减轻啤机的损耗.
4.2保压
当熔胶注满模腔后,为了补偿胶料冷却收缩使模腔形成的空间和压实胶料,这时螺杆还需给予熔胶一定的推进力,该力即为保压.保压用HP表示,一般大胶件采用中压,小胶件采用低压.(一般情况下,保压压力小于射胶压力)
4.3背压
当射胶,保压完成后,螺杆开始旋转,这样,原来在螺杆槽内和料门内的胶料通过螺杆槽被压入炮筒的前端(计量室),这时熔胶对螺杆有一反作用力迫使螺杆向后退,称之为回料.为了增加熔胶在炮筒前端(计量室)的密度,和调节螺杆后退的速度,必须给螺杆增加一个可调的推力,这个力称之为背压.调节背压可以调节色粉与塑胶原料的混合程度,影响塑化效果,适当的背压可以减轻胶件的混色,气泡,光泽不均等缺陷;
但背压不能太大,太大背压会使熔胶产生分解,从而引起胶件变色,黑纹等缺陷.另加大背压就势必延长了生产周期,加剧了啤机的损耗.(一般为10千克/平方厘米左右)
4.4锁模低压
亦称低压保护,是啤机对模具的保护装置.从模具保护位置到前后模面贴合的那一瞬间,这段时间内锁模机构推动模具后模的力是比较低的,同时当推进过程中,遇到一个高于推动力的阻力时,模具会自动打开,从而停止合模动,这样,
合模时前后模之间如有异物,模具就可以得到保护锁模低压一般是有行位的
模具比没行位的模具大一些,取值5~20千克/平方厘米.
4.5锁模高压
page1of12
亦称锁模压力,当合模使前后模面贴合后,锁模力自动由低压转为高压,目的是前模面和后模面贴合时有一定的压力,锁模压力不能太高,太高会压伤模面;
调节时,使前后模有一定的压力即可,一般取80~100千克/厘米.(一般锁模状态:
高速-低压低速-高压合模)
4.6顶针压力
啤机施加于模具顶出板后面的顶出力,大小为顶落塑胶件为宜.
(五)速度参数)
5.1射胶速度
射胶速度即指啤机在射胶进螺杆推动熔胶时螺杆的移动速度.射胶速度主要受射胶压力,模具型腔对熔胶的阻力,熔胶本身具备的精度等因素的影响,射胶压力大于熔胶粘度和型腔阻力时,设置的射胶速度才得以充分发挥,根据螺杆位置的各个分段,可设置不同的射胶速度,如:
射胶一段,此时熔胶流经水口到胶件,需要低速中压,射胶二段,此时熔胶填充型腔,需要高速高压,射胶三段,熔胶填充胶件周边,需要中速低压,而且射胶速度随着模腔的填满阻力的增大而慢慢降低,直到为零.具体各段的射胶速度的设定,要根据熔胶流经模腔的形状而定.
5.2螺杆转速
螺杆向炮筒计量室供料时的转速,称之为螺杆转速,它影响螺杆的后退速度,当背压设定后,螺杆转速越高,后退速度越大,调节螺杆的转速则可以调节胶料的塑化效果,改善制品的色调不均,混色等缺陷,但螺杆转速过高会导致胶料过度剪切而产生分解,同时还造成空气混入料筒,使制品产生气泡.PC/PVC/POM/PMMA等粘度较大或热敏性塑料都不宜用高螺杆速度.
5.3震雄注塑机有两级熔胶速度控制选择:
一般而言,前段是用较大的速度熔胶以提高效率,后段减速以保持熔胶位置稳定.
螺杆索退时的后退速度,称之为索退速度,一般选择中,低速为宜.
5.4开锁模速度
开模速度一般为前后模面分开时采用慢速,所以模板不同的模具在设不定期时有差异,两板模一般设置:
慢,快,慢;
三板模一般设置:
中,慢,慢.锁模速度一般为:
快速,低压低速,高压高速.
5.5顶针速度
顶针顶出胶件的速度,称之为顶针速度,不同结构的胶件其设置不同,一般采用中速.
(六)保压时间
6.1焗料时间:
焗料所需的时间,不同的胶料所需的时间不同,应参照不同胶料特性设置。
6.2射胶时间
螺杆注射胶料所需的时间,其设定一定和螺杆位置移动吻合.
6.3保压时间
螺杆进行保压到开始回料的时间,一般为1~5秒,不可太长,太长则浪费时间.
6.4冷却时间
螺杆开始回料到模具准备打开这段时间为冷却时间,冷却时间不可小于回料时间.
6.5周期时间
啤机由开始啤作到下一个啤作的开始所需的时间.要求是在啤出合格胶件的前提下,越短越好.
以上项目为各个设定的简单介绍,具体各参数的设定,取决于各种不同的模具.应分别而论.
第二章
几个重要控制参数的注塑工艺分析
本章将粗略地归纳一下注塑生产中的几个重要的工艺参数的调节以及相互间的关系.
(一)
塑胶的粘度及条件对粘度的影响
熔融塑料流动时大分子之间相互摩擦的性质称为塑料的粘性.而把这种粘性大小的系数称为粘度,所以粘度是熔融塑料流动性高低的反映.粘度越大,熔体粘性越强,流动性越差,加工越困难.
工业应用上,比较一种塑料的流动性并不是看其粘度值,而是看其熔体流动指数大小(称MFI):
所谓MFI,就是在一定熔化温度下,熔体受到额定的压力作用下,单位时间内(一般为10分钟)通过标准口模的熔体重量.以g/10min表示,如注塑级的PP料,牌号不同,MFI的值可以从2.5~30间变化,塑料的粘度并非一成不变,塑料本身特性的变化,外界温度,压力等条件的影响,都可促成粘度的变化.
1.1分子量的影响
分子量越大,分子量分布越窄,反映出来的粘度愈大.
1.2低分子添加济的影响
低分子添加济可以降低大分子连之间的作用力.因而使粘度减小,有些塑料成型时间加入溶济或增塑剂就是为了降低粘度,使之易于模成型.
1.3温度粘度的影响
温度对大多数熔融塑料的粘度影响是很大的,一般温度升高,反映出来的粘度越低,但各种塑料熔体粘度降低的幅度大小有出入:
PE/PP类塑料,升高温度对提高流动性,降低熔体粘度作用很小,温度过高,消耗加大,反而得不偿失
PMMA/PC/PA类等塑料,温度升高粘度就显著下降,PS
ABS升高温度对于降低粘度于成型亦有较大好处
1.4剪切速度的影响
有效的增加塑料的剪切速度可使塑料粘度下降,但有部分塑料,如PC亦有例外,其粘度几乎不受螺杆转速的影响.
Page2of12
1.5压力的影响
压力对粘度的影响比较复杂,一般PP&
PE类粘度受压力的影响不是很大,但对PS的影响却相当显著,实际生产中,在设备较完善的机器上,应注意发挥高速注射,即高剪切速度的作用,而不应盲目地将压力提高.
(二)注射温度的控制对成型加工的影响
所谓炮筒温度的控制是指塑料在料筒内如何从原料颗料一直均匀地被加热为塑性的粘流体,也就是料筒烤温如何配置的问题.
2.1料筒温度的调节应保证塑料塑化良好,能顺利注射充模又不引起分解.
这就要求我们不能因受制于塑胶对温度的敏感性而有意识地降低塑化温度,用注塑压力或注射速度等办法强行充模.
2.2塑料熔融温度主要影响加工性能,同时也影响表面质量和色泽.
2.3料温的控制与制件模具有关,大而简单的制件,制件重量与注射量较接近的,需用较高的烤温,薄壁.形状复杂的也要用高烤温.反之,对于厚壁制件,某些需要附加操作的,如装嵌件的,可以使用低的烤温,鉴别塑料溶体温度是否得宜可以用点动动作在低压速下对空注射观察,适宜的料温应使喷出来的料刚劲有力,不带泡,不卷曲,光亮连续.
2.4料温的配置一般都是从进料段到出料段依次递升,但为了防止塑料的过熟分解和制件颜色的变化也可略低于中段,料温配置不当有时会造成卡螺杆故障--螺杆不转或空转,这还可能是注射压力过大或螺杆止逆环(介子)失效造成料筒前端的稀薄熔料向进料区方向反流.当这些反流的料灌进螺纹端面与料筒内壁间的微小间隙而受到较低温度冷却时,将冷固成一层薄膜紧紧卡在两个壁面之间,使螺杆不能转动或打滑.从而影响加料.此时,切勿强行松退或注射,建议加料口冷却水暂时关闭,强化升高加料段温度直至比塑料熔点高30~50摄氏度,并同时地出料段温度降低至熔化温度附近,待10~20分钟后,小心地转动螺杆,能转动时才重开机,然后缓慢加料.
(三)注射周期中压力的控制
3.1实际施用的压力应比充满型腔压力偏高,在注射过程中,模控压力急剧上升,最终达到一个峰值,这个峰值就是通常所说的注射压力.注射压力显然要比充满型腔压力偏高.
3.2保压压力的作用:
模腔充满塑料后直到浇口完全冷却对闭前的一段时间,模腔内的塑胶仍然需要一个相当高的压力支持,即保压,其具体的作用是:
A:
补充靠近浇口位置的料量,并在浇口冷凝对闭以前制止模腔中尚未硬化的塑料在残余压力作用下,向浇口料源方向倒流.
B:
防止制件的收缩,减少真空泡.
C:
减少因制件过大的注射压力而产生粘模爆裂或弯曲变形的现象.所以保压压力通常是注射压力的50%~60%.保压压力或时间太长太大的话有可能将浇口及流道上的冷料挤进制件内,使靠近浇口位置上添上冷料亮斑,同时毫无好处地延长了周期.
3.3注射压力的选择
A.根据制件形状.厚薄选择.B.针对不同的塑料原料选择.
在生产条件和制件质量标准许可的情况下,建议采用就温低压的工艺条件.
3.4背压压力的调节
背压所代表是塑料塑化过程所承受的压力.有进也称之为塑化压力.
A.颜色的混和效果受背压的影响,背压加大,混和作用加强.
B.背压有助于排除塑料件的各种气体,减少银纹和气泡现象.
C.适当的背压可以避免料筒内局部滞料现象,所以清洗料筒时往往将背压加大.
(四)注射速度的控制
4.1速度高低的影响:
低速充模优点是流速平稳,制件尺寸比较稳定,波动较小,制件内应力低,内外各向应力一致性较好,缺点是制件易出现分层结合不良的熔点痕,水纹等,高速充模可采用较低的注射压力,改进制品的光泽度和平滑度,消除了接缝线现象及分层现象,收缩凹陷小,颜色更均匀一致.缺点是易产生”自由喷射”,即出现滞流或涡流.温升过高,颜色发黄,排气不良及有时脱模困难.粘度高的塑料有可能产生熔体破裂,制件表面产生雾斑,同时也增加了由内应力引起的翅曲和厚件沿接缝线开裂的倾向.下图是表面因注射速度不当引起的缺陷形态:
夹水纹(慢)
射纹(快)
0
烧焦(快)
水波纹(慢)
4.2采用高速高压注射的情况:
1.塑胶粘度高,冷却速度快,长流程制件.2.壁厚太薄的制件.3.玻纤维增强的塑料.
4.3多级调速的应用:
由于浇道系统及各部位几何条件不同,不同部位对于充模熔体的流动(特别是速度)提出要求,这就出现了多级注射,我们可以根据制品的形状,对相对薄壁的,形状复杂的部分实行快速充模,而对于入水口和易烧焦处用低速或中速充模.大部分产品都可以采用低速—高速—中速充模过程,从而达到改变制品表观和内在质量的目的.这一设置方法甚至成为现时通用的公式.
第三章
几种原料的性能介绍
塑胶的分类
page3of12
一.
按用途分类塑胶分为工程塑胶和普通塑胶
工程塑胶—泛指一些具有能制造机械零件或工程结构材料等工业品质的塑料.常见的有ABS.PA.PC.POM.聚缩醛.聚酯树脂.聚砜.PMMA及氯素树脂等.
四大工程塑胶:
ABS.POM.PC.PA.
二.
按照受热性能,可分为热固性塑料和热塑性塑料.
热固性塑料—是经加热固化后不再在热的作用下变软而重复成型的塑料.
特点—质地坚硬,耐热性好,尺寸稳定,不溶于剂.
常见的有:
酚醛塑料.环氧树脂.不饱和聚脂.脲甲醛.聚氯酯.
热塑性塑料—是指可以多次重复加热变软冷却结硬成型.主要由分子结构为线状或链状的聚合树脂构成.
PE.PP.PS.ABS.PA.PMMA.PC.聚酯酸纤维等.
丙烯氰-丁二烯-苯乙烯树酯(ABC)
尼龙(PA)
聚碳酸酯(PC)
聚乙烯(PE)
聚甲醛(POM)
聚丙烯(PP)
聚笨乙烯(PS)
苯乙烯-丙烯氢聚合体(SAN
AS)
聚甲基丙烯酸甲酯(PMMA)
丙烯氰-丁二烯-苯乙烯树酯(ABS)
原料待性
俗称高度不碎胶ABS树脂是由丁二烯,丙烯氰,苯乙烯三种单体组合而成.其中丙烯氰为橡胶特征.ABS为非结晶性聚合物.手触有刚性感,轻敲声音清脆,难折断.折弯处会发白.容易燃烧.但不完全.火焰呈黄色.有很浓密黑碳.ABS料不起泡呈胶化状.PS.HIPS表面会起泡.
ABS有良好的成型加工性,具有良好的综合机械强度,特别是耐寒性,电性能.在工程塑胶中,其加工性能最好.
加
工
特
性
焗料温度
加工前干燥温度80~85摄氏度,干燥时间为1~2小时.
炮筒温度
喷嘴温度:
210~230摄氏度
螺杆前段:
200~220摄氏度
螺杆中段:
190~210摄氏度
螺杆后段:
180~200摄氏度
一般不能高于250摄氏度,否则会生降解.
模具温度
一般制品精度低时50~60摄氏度,表面质量要求高时60~80摄氏度.
调
较
征
1.
与聚苯乙烯相比.ABS熔体的粘度是较高的,所以在注射时采用较高的压力.ABS制件水纹特别顽固的原因往往是注射压力不够.
2.
注射速度:
宜用中速.在薄壁或复杂制品难以充满时才用高速.
原料特性
尼龙是指聚胺类树脂构成的塑料.尼龙是结晶性塑料,机械强度高,韧性好,有较高的抗拉,抗压强度,制品轻量,易染色,易成型.因有较低熔融粘度,能快速流动,易充模,充模后凝固点高,快速定型,故成型周期短,生产效率高,易吸水,啤出后一般要进行调湿,退火处理以保证尺寸及机械强度稳定性.PA燃烧较缓慢,移走火源,如果环境温度不太高,会自己熄灭.火焰上方呈黄色,下方呈蓝色,在近火焰处表面会熔融滴落.也会起泡,熄灭后有似烧焦羊毛或指甲气味.
90~110摄氏度
尼龙6:
225~300摄氏度
尼龙66:
260~300摄氏度
20~40摄氏度
因尼龙粘度低,流动性好,注射压力不用大,但其凝固速度快,如压力过低则易出现走胶不足,皱纹,气泡,熔接痕等问题.
注射速度调节以壁厚不同而易,厚壁则慢速,薄壁用快速.
3.
制品要进行调湿处理和熟处理.
Page4of12
聚碳酸酯是一种新型的工程塑料.它性能优异,不仅透明度高,冲击韧性好,而且耐蠕变,尺寸稳定性好,其晶核极小,可以视为非结晶性聚合物,融熔粘度高,俗称防弹玻璃胶.无延展性.手触有刚性感,轻敲有轻脆感.燃烧现象接近PS.但速度缓慢.会慢慢熄灭.熄灭后有花果臭气味.火焰呈黄色.带黑烟碳素.燃烧后塑料熔融起泡.
110~120摄氏度
280~310摄氏度
280~330摄氏度
280~330摄氏度
注射压力变化对熔体粘度影响较小,但由于它的熔体流动性较差,故在实际操作中一般选用较高的注射压力,一般为80~120MPA(约800~120千克/平方厘米)
一般采用较高的注射速度.如速度太慢则易出现皱纹,料流痕等缺陷.
保压压力和保压时间以制品外观无缺陷为标准,过大的保压压力会产生内应力.
原料特
聚乙烯分为低密度聚乙烯(LDPE),中密度聚乙烯,高密度乙烯(HIPE)三类,一般说低密度聚乙烯由于大分子链中含有较多支链,不仅密度低,而且结晶度也低,所以质地柔软,透明性好,适用于制作薄膜和日用品,高密度聚乙烯由于大分子中支链较少,不仅密度高,而且结晶度也高,所以产物刚性大,机械强度高,但透明性较差,适于制造各种工业配件.
聚乙烯结晶性材料.
加工前段粒料一般不需要干燥.
200~210摄氏度
料筒前段:
料筒中段:
180~200摄氏度
料筒后段:
170~190摄氏度
35~65摄氏度
树脂的熔融粘度与剪切速度有关,提高射胶速度能改善熔体的流动性.
聚乙烯为结晶性材料,塑料制件在冷却过程中收缩大,因而模具须均匀冷却,以免引起因收缩不均而翘曲变形.
3.聚乙烯胶件无良好的熔剂.故而其粘合性能差,喷油,移印,丝印油的附差力差.
俗称赛钢料.聚甲醛是一种没有侧链,高密度,高结晶性的线型聚合物,具有明显的熔点.结晶度高,成型收缩大,厚壁制品须充分补缩.属硬胶.一般用于齿轮类.不易碎裂,耐温性能好,耐磨性强.但价格较贵.可用于磨擦频率高的产品.熔点在175摄氏度左右.手触有刚性.易燃烧.火焰上呈黄色.下呈兰色.无黑烟.但非常刺鼻.似鱼腥味.
加工特性
80~90摄氏度
180~190摄氏度
螺杆中段:
170~180摄氏度
螺杆后段:
160~170摄氏度
80~100摄氏度
注射压力因浇口大小.壁厚薄.流道长短而异,一般在100MP左右.
注射速度宜选偏高为好,以改善熔体流动性.避免熔体过早冷却而形成水纹.
成型周期不能太长,否则熔料可能在料筒内分解(聚甲醛的熟稳定性差,残量不能太大.
4.
成型温度范围窄.
Page5of12
俗称百折软胶.聚丙烯有良好的电性能,其化学稳定性,机械性能和耐熟性高于聚乙烯,缺点是耐寒性差,耐氧化性更差,着色困难.光洁度较差,易缩水.变形,燃烧有少量黑烟.有后油气味.
加工前粒料一般不需要干燥.(熔点:
140~160摄氏度)
160`180摄氏度
40~80摄氏度
树脂的熔融粘度与剪切速率有关,射胶速度能改善熔融料的流动性.
注射时选择适当的温度是非常重要的.因为聚丙烯分子在低温度高压下易发生取向,前向后会产生应变和降低冲击速度.
聚苯乙烯(PS)
聚苯乙烯具有价廉.容易着色.透明.吸湿性低,电性能好,以及加工性良好等特点,广泛应用于电子电器工业,化学工业.冷冻工业以及日用品等方面.
聚苯乙烯的主要缺点是性脆和耐热性低,为了改进这些缺点.发展了聚苯的改