冲压模课程设计06Word下载.docx
《冲压模课程设计06Word下载.docx》由会员分享,可在线阅读,更多相关《冲压模课程设计06Word下载.docx(13页珍藏版)》请在冰豆网上搜索。
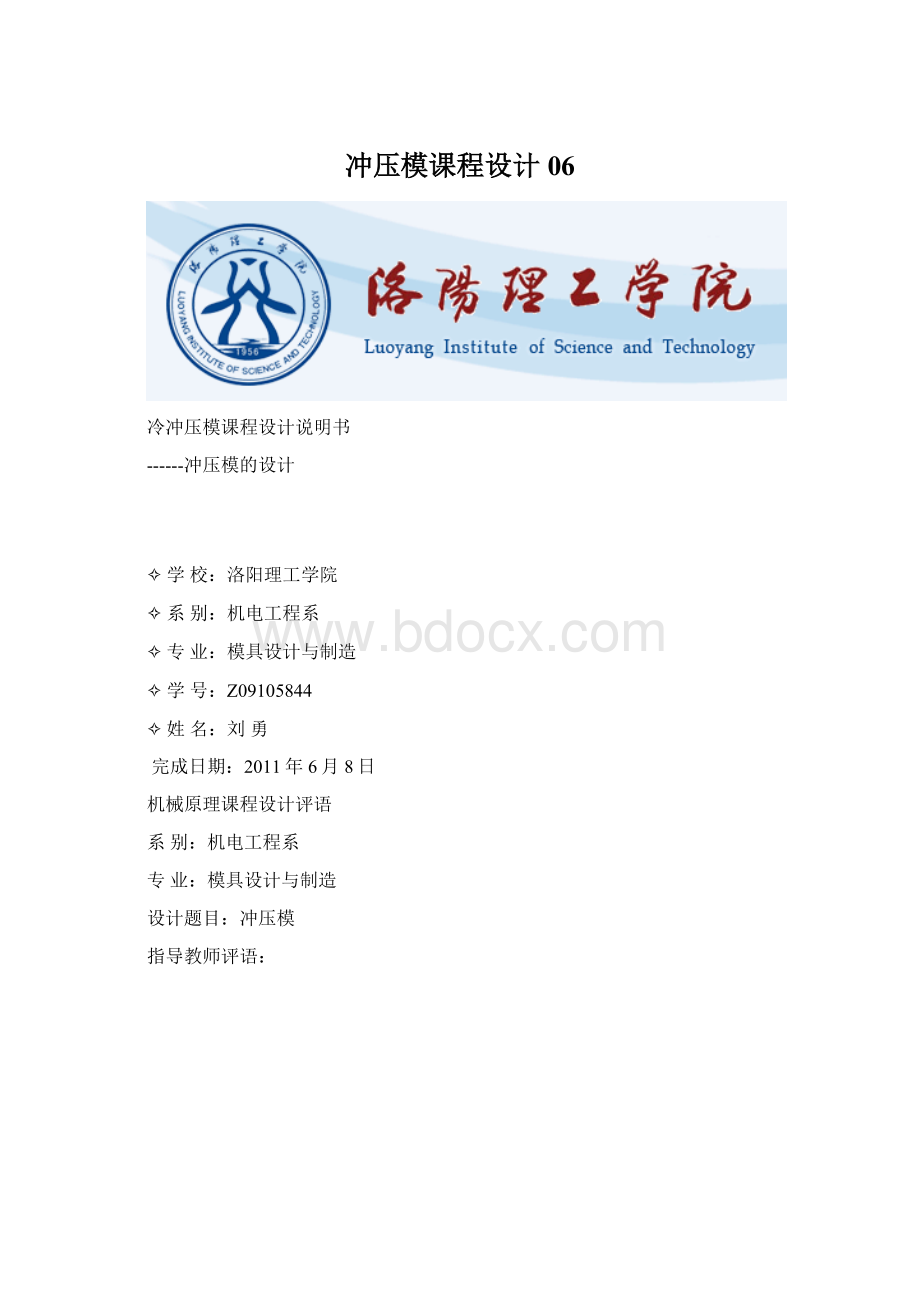
系专业
学生姓名班级学号
课程设计篇幅:
图纸张
说明书页
年月日指导教师
洛阳理工学院
前言
该课程设计是由冲孔落料件设计,冲压模设计组成,冲压模具主要是将板料分离或成形而得到制件的加工方法。
因为模具的生产主要是大批量生产,而且模具可以保证冲压产品的尺寸精度和产品质量,模具的设计与制造主要考虑到模具设计能否满足工件的工艺性设计,能否加工出合格的零件,以及后来的维修与存放是否合理等。
本次课程设计的垫片,不仅要考虑是做出的零件能满足工作要求,还要保证它一定的使用寿命。
关键词:
冲孔落料工艺性
(1)课题来源及要求
本次模具设计的课题属于零件设计类,来源于生产实际问题,是一个圆环垫片,该零件需通过冲孔落料二道工序完成。
(2)设计内容
a分析零件的成形工艺性,进行制品的基本参数的计算、冲压模的设计计算,选用压力机,确定模具类型及结构;
b模具和成型机械关系的校核;
c模具零件的必要计算;
d绘制模具装配图一张,绘制主要工作零件凸模、凹模、凸凹模图各一张;
e编写设计说明书;
(3)介绍的内容与意义
此次课程设计说明书涉及的知识面广、衔接紧密、结构整合或综合性强、实用性强。
本说明书介绍了冲裁件的工艺性分析、冲压工艺方案的确定、模具结构形式的确定、设计工艺计算、模具总体结构设计、主要零部件设计、冲压设备的选取等。
本说明书对冲压模具设计的基本流程介绍相对比较全面,理论联系实际,同时也培养了个人的较强实践动手能力和对模具设计专业知识的系统化、完整化,以及对于工程技术的严谨性。
(4)设计过程
为缩短本次设计的时间,让模具设计充分理解其设计意图,在模具各部分设计中采用了计算机辅助设计(AutoCAD)系统,让模具各部分的结构明确的展现在我们面前,提高效率。
一、零件原始数据
零件原始数据:
如图所示的垫片,外形直径D=18mm,内孔直径d=8mm,厚度t=1.5mm,材料为Q195,生产批量:
大批量。
二、冲压件工艺分析
1、冲压工序
只有冲孔、落料两道工序。
2、材料性能
Q195是普通碳素结构钢,具有良好的冲裁成形性能,其抗拉强度为315~390Mpa,抗剪强度为260~320MPa。
3、零件结构
该零件结构简单且中心对称,无尖角,对冲裁成形加工较为有利。
零件中间有一圆孔,孔的最小尺寸为d=8mm,满足冲裁最小直径dmin≥1.0t=1.5mm的要求。
同时,经过计算,孔的边缘距离零件外形的最小尺寸b1=1/2×
(18-8)=10mm,满足冲裁最小孔边距bmin≥1.0t=1.5mm的要求。
所以,该零件的结构满足冲裁件的结构要求。
4、尺寸精度
查表得,该工件内外形所能达到的经济精度为IT12~IT14级,所以未注公差由IT14级查取。
由此,通过普通冲裁可以达到零件的精度要求。
综合以上材料性能、零件结构、尺寸精度的分析,该零件可以采用普通冲裁的方法获得。
三、冲裁方案及模具类型的选择
1、冲压工序安排方案
该零件包括冲孔和落料两个基本工序,可提出的加工方案如下:
方案一:
采用先落料,后冲孔。
采用两套单工序模生产。
方案二:
落料—冲孔复合冲压。
采用复合模生产。
方案三:
冲孔—落料连续冲压。
采用级进模生产。
三种类型模具优缺点比较如下:
方案一的优点是模具设计、制造简单、周期短、模具结构简单,甚至可以采用标准化的模具成形零件,因此,模具和制件的制造成本均低。
但因采用两副模具分别进行落料和冲孔,其冲压生产率低,不能满足垫圈零件大批量生产的需求。
方案二的优点是冲压的生产效率高,且制件的平整度较高。
但模具结构较第一种方案复杂,因此设计制造周期较长,模具成本较高。
方案三优点是冲压生产过程易于实现机械化和自动化,生产效率较高。
但模具结构较第一种方案复杂,因此设计制造周期较长,模具成本较高;
与第二种方案比生产的零件精度稍差欲保证冲压件的形位精度,需在模具上设置导正销导正,模具制造、装配较复合模略复杂
综合以上分析,以满足制件质量和生产纲领为主要因素,方案一显然不能满足要求;
方案二和方案三,宜采用方案二生产。
现对复合模中凸凹模壁厚进行校核,当材料厚度为t=1.5mm时,可查得凸凹模最小壁厚为δ=4mm,现零件上的最小孔边距为bmin=18mm,有bmin>
δ,满足该凸凹模结构要求,所以可以采用复合模生产,即采用方案二
2、选用模具确定
按照落料凹模安装位置,复合模又分为正装和倒装两种形式。
正装复合模冲裁时的冲孔废料由上向下推出,如多孔件,而孔的废料落在下模表面,需要及时清除,而倒装式复合模工作时产生的孔废料直接由下模部分漏出,比较可知倒装模操作方便,且安全。
所以选用倒装式复合模进行加工。
综上得,该零件采用冲孔落料倒装式复合模生产。
四、零件的工艺计算
1.排样、计算条料宽度及确定步距
一般而言,排样原则有:
a.提高材料利用率η。
对冲压件来说,由于产量大,冲压生产效率高,原材料费用常会占到冲件总成本的60%以上,所以材料利用率是η是一项很重要的经济指标;
b.使工人操作方便、安全,减轻工人的劳动强度,保证有较高的生产效率。
应尽量选条料宽、进距小的排样方法;
c.使模具结构简单,模具寿命较高;
d.排样应保证冲压件的质量。
根据零件形状,比较可知应采用单排的有废料排样方法最合适,
(1)搭边值的确定
由零件外形尺寸D=∅18mm,查《冲压工艺与模具设计》表2-12得
两工件间的搭边a1=1.5mm,实际取a1=1.0mm;
工件边缘搭边a=2mm,实际取a=1.2mm。
(2)条料宽度的确定(导料销导向)
条料宽度计算公式:
B=(D+2a+∆)0-∆
查表2-13得,∆=1.0mm代入公式,得
B=(18+2X1.2+1.0)0-1.0mm=21.40-1.0mm
a)确定步距
S=D+a1=18+1=19mm
b)材料利用率
η=A1/hB×
100﹪=π×
(182-82)/19×
21.4×
100﹪=50.2﹪
2、冲压力的计算
(1)冲裁力的计算
计算冲压力的目的是为了合理的选用压力机和设计模具。
压力机的吨位必须大于所计算的冲裁力,以适应冲压的要求。
平刃口冲裁时,其冲裁力F可按下式计算:
F=KLtτb
其中F——冲裁力[N];
K——系数,考虑冲击载荷因素,通常取1.3
t——材料厚度,[t]为mm;
τ——材料抗剪强度,[τ]为MPa;
L——冲裁周长,[L]为mm。
材料Q195的抗剪强度τb=260~320MPa,取τb=300MPa,
冲孔冲裁力:
F1=1.3×
π×
8×
1.5×
300=14.695kN
落料冲裁力:
F2=1.3×
18×
31.5×
300=33.064kN
F=14.695+33.064=47.759KN
(2)卸料力、推件力的计算
卸料力:
F卸=k卸F
推件力:
F推=nK推F
其中,n=h/t=9/1.5=6
由材料厚度t=1.5mm,查表2-11得
卸料力系数K卸=0.042,推件力系数K推=0.055,
代入,计算得
卸料力:
F卸=0.042×
33.064=1.389kN
推件力:
F推=0.055×
6×
14.695=4.849kN
该模具采用弹性卸料装置和下出料装置,
所以,总的冲裁力为:
F总=F+F卸+F推=47.759+1.389+4.849=53.997kN
根据总的冲裁力,初选设备为开式压力机JB23-6.3。
3、压力中心的计算
零件外形为中心对称图形,所以该零件的压力中心即为零件的几何中心。
4、刃口尺寸计算
间隙值Zmin=0.132mm,Zmax=0.240mm
Zmax-Zmin=0.108mm
(1)冲孔
采用凸、凹模分开加工方法。
由表2-7查得凸、凹模制造偏差分别为δp=-0.020mm,δd=+0.020。
因|δd|+|δp|=0.040mm,Zmax-Zmin=0.108mm
满足|δd|+|δp|≤Zmax-Zmin的条件。
按IT14级查得:
∆Φ8=0.36mm,由表2-6查得磨损系数x=0.5.
dp=(dmin+XΔ)0-δp=(8+0.5×
0.36)0-0.02mm=8.180-0.02mm
dd=(dp+Zmin)+δd0=(8.18+0.132)+0.020mm=8.31+0.020mm
(2)落料
∆Φ18=0.43mm,由表2-6查得磨损系数x=0.5.
Dd=(Dmax−x∆)+δd0=(18-0.5×
0.43)+0.020mm=17.79+0.020mm
Dp=(Dd-Zmin)0-δp=(17.79-0.132)0-0.02mm=17.660-0.02mm
五、模具主要零部件的确定
1、落料凹模设计
凹模采用整体式,凹模孔均采用线切割机床加工,在不影响其壁强度的情况下,采用螺钉或销钉,跟凹模固定板经行连接。
根据《实用冲模设计与制造》落料凹模的厚度经验公式为H=Kb(H≥15mm)
式中:
H——凹模厚度(mm)
K——系数
b——凹模孔的最大宽度(mm)
落料凹模的壁厚c=(1.5~2)H(c≥30mm)
c——落料凹模的壁厚(mm)
H——落料凹模的厚度(mm)由材料厚度t=1.5mm,最大外形尺寸b=18mm,查《冲压工艺与模具设计》表3-3得
k=0.40,
代入,计算得h=0.40×
18=7.2mm≤15mm,因此取16mm。
C=(1.5~2)×
16=24~32mm
因零件结构较简单,取较小值,C=25mm。
凹模的长度:
L=b+2C=18+2×
25=68mm
凹模的宽度:
B=b+2C=80+2×
选用模板:
100mm×
16mm
2、标准模架的选用
标准模架的选用,依据凹模的外形尺寸确定,因冲压件精度要求不高,故选用后侧导柱模架,根据计算结果,查GB2872.1-90得,模架的规格如下:
上模座:
100mm×
30mm
下模座:
40mm
导柱:
A20mmh5×
110mm
导套:
A20mmH6×
63mm×
32mm
垫板:
6mm
卸料板:
10mm
凸模固定板:
100mm×
12mm
凸凹模固定板:
12mm
3、冲孔凸模的设计
凸模由凸模固定板固定,两者采用过渡配合关系。
冲孔凸模高度L=h1+h2+a+t
L——冲孔凸模长度(mm)
h1——凸模固定板厚度(mm)
h2——卸料板厚度(mm)
t——材料厚度(mm)
a——附加长度,它包括凸模的修模量。
凸模进入凹模的深度及凸模固定板与卸料板的安全距离等。
这一尺寸如无特殊要求,可取10~20mm使用弹性卸料装置时,按实际情况设计凸模高度,a取15mm
L=h1+h2+h3+a=12mm+10mm+15mm=37mm
4、卸料装置中弹性元件的选用与计算:
因为模板为矩形,选弹簧数k=6,F。
≥F卸/n=1389N/6=231N。
弹簧所需压缩量
S预和S工作选用1个料厚,S修磨一般选用6mm
S总=S预+S工作+S修磨=1.5mm+1.5mm+6mm=9mm
根据F。
,由《冷冲压工艺与模具设计》附录R可查得:
d=2.5mm,D2=14mm,Flim=278N,ρ=4.73mm,f=1.995mm
n=S总/f=9÷
1.995=4.5H。
=ρn+d=4.73×
4+2.5=21.42mm
取H。
=22mm
综上所得,选用Ф2.5×
14mm×
22mm
5、凸凹模的设计:
凸凹模高度:
H=h凸凹模固定板+h卸料板+h弹性元件
h凸凹模固定板=(60%~80%)H整体式凹模厚度
则取h凸凹模固定板=12mm
H=12mm+10mm+22mm=44mm
根据《冷冲压模具设计与制造》表2.23查的凸凹模最小壁厚a=4.0mm。
分析工件工艺,以上条件均能满足。
6、其他零部件的选用
模柄采用嵌入式模柄,根据设备上模柄孔尺寸,选用规格B30×
75的模柄。
其它零部件参照标准选用。
六、冲压设备的选用
冲压设备选择的要求:
1、压力机的行程大小,应能保证成型零件的取出与毛坯的放入。
2、压力机的工作台面尺寸应大于冲模的平面尺寸,还需留有安装固定的余地,但是在过大的工作台上安装很小尺寸的冲模时,工作台的受力条件也是不理想的。
3、所选的压力机的闭合高度应与冲模的闭合高度相适应。
模具的闭合高度H0:
模具在闭合时,上模座的上表面到下模座的下表面之间的距离。
压力机的闭合高度H:
滑块在下死点时,工作台面到滑块下端面的距离。
该距离一般是可以调整的,故一般的压力机均有最大闭合高度Hmax和最小闭合高度Hmin。
根据冲压力的大小,选择开式双柱可倾压力机JB23-6.3,其主要参数如下:
公称压力:
63kN
滑块行程:
35mm
最大闭合高度:
120mm
闭合高度调节量:
40mm
滑块中心线到床身距离:
110mm
工作台尺寸:
200mm×
310mm
模柄孔尺寸:
φ30mm×
50mm
七、模具装配图
1、绘制装配图
见图纸1
2、主要零件材料选择及热处理
按模具标准,选取所需的标准件,查清标准件代号及标记,写在总图明细表内,并将各零件标出统一代号。
(1)上模座:
上模座的作用是与压力机相连接,将模具的上模部分安装在压力机上。
根据《中国模具设计大典》上所推荐,选用HT200。
不必进行热处理,因为上模座在模具工作中只承受冲击力,要求材料具有较好的强度和韧性。
(2)垫板:
垫板在模具工作过程中,承受卸料组件、冲头传递过来的较大的冲击载荷。
因此要求材料有较好的强度、硬度和一定的韧性。
根据《中国模具设计大典》推荐,选用45钢,热处理到HRC43~48。
(3)凸模固定板:
凸模固定板,主要起固定凸模的作用。
上模的冲头、小导柱都是固定在固定板上。
该板几乎不承受载荷,对材料没有什么较大要求,根据《中国模具设计大典》推荐,选用45钢即可。
(4)卸料板:
卸料板在工作过程中起到卸料和压料的作用。
工作时,通过卸料板把条料紧紧的压在凹模板上,接着冲头开始工作,易保证产品精度。
凸凹模开始分离时,卸料板通过弹簧的作用,将条料卸下。
根据《中国模具设计大典》推荐,选用45钢。
(5)凹模板垫板:
由于在工作过程中承受很大的冲击载荷,根据《中国模具设计大典》推荐,选用45钢,热处理到HRC43~48。
(6)下模座:
下模座其作用与上模座相似,根据《中国模具设计大典》推荐,选
用HT200。
(7)模架的选取
在定好排样图和选定模具的基本形式后,便可以选模板了。
根据《中国模具大典》的推荐,选定各模板的尺寸。
模具设计时,螺钉和销钉的选用应注意以下几点:
1.同一组合中,螺钉的数量一般不少于3个(被联接件为圆形时为3~6个,为矩形时4~8个),并尽量保证定位可靠。
2.螺钉和销钉的规格应根据冲压工艺力大小和凹模厚度等条件确定。
螺钉规格可查表,销钉的公称直径可取与螺钉大径相同或小一个规格。
螺钉的旋入深度和销钉的配合深度不能太浅,也不能太深,一般可取其公称直径的1.5~2倍。
3.螺钉之间、螺钉与销钉之间,螺钉、销钉距凹模刃口及外边缘的距离,均不应过小,以防降低模板强度,其最小距离可查表。
4.各被联接件的销孔应配合加工,以保证位置精度。
销钉与销钉之间采用H7/n6或H7/m6配合,查表可选用螺钉规格为M10
八、结束语
通过对边板冲孔落料倒装复合模的设计、计算,使我对冲裁模的设计流程有了更深一层的了解,包括冲裁件的工艺分析、工艺方案的确定、模具结构形式的选择、必要的工艺计算、主要零部件的设计、压力机型号的选择、总装图及零件图的绘制。
在设计过程中,有些数据、尺寸是一点也马虎不得,只要一个数据有误,就得全部改动,使设计难度大大的增加。
在这次设计中,我感觉要完成这次设计不仅要有扎实的专业知识,还要有过硬的计算机基础作保障,方才能很好的完成这次设计。
所以说我们
今后的学习中,不仅要学好应该所学的,还要尽可能多的去拓展我们在其它方面的领域,只有这们我们才能立于不败之地。
九、致谢
感谢指导师王老师严肃的科学态度,严谨的治学精神,精益求作作风,他将成为我工作、学习中的榜样。
他为每位同学的课程设计都细心的指导,积极与同学进行沟通与交流,在沟通与交流中,我学到了很多冲压模具设计的知识与设计理念。
在此谨向王老师予以诚挚的谢意和崇高的敬意。
还要感谢我的同学们,感谢他们的积极配合,在相互交流与帮助下顺利完成了此次毕业设计。
十、参考资料
[1]姜奎华.《冲压工艺与模具设计》.机械工业出版社
[2]编委会.《中国模具设计大典》.江西科学技术出版社
[3]张正修.《冲模结构设计方法、要点及实例》.机械工业出版社
[4]洪慎章.《实用冲模设计与制造》.机械工业出版社
[5]王新华、陈登.《简明冲模设计手册》.机械工业出版社