液压机总体及控制系统设计文档格式.docx
《液压机总体及控制系统设计文档格式.docx》由会员分享,可在线阅读,更多相关《液压机总体及控制系统设计文档格式.docx(47页珍藏版)》请在冰豆网上搜索。
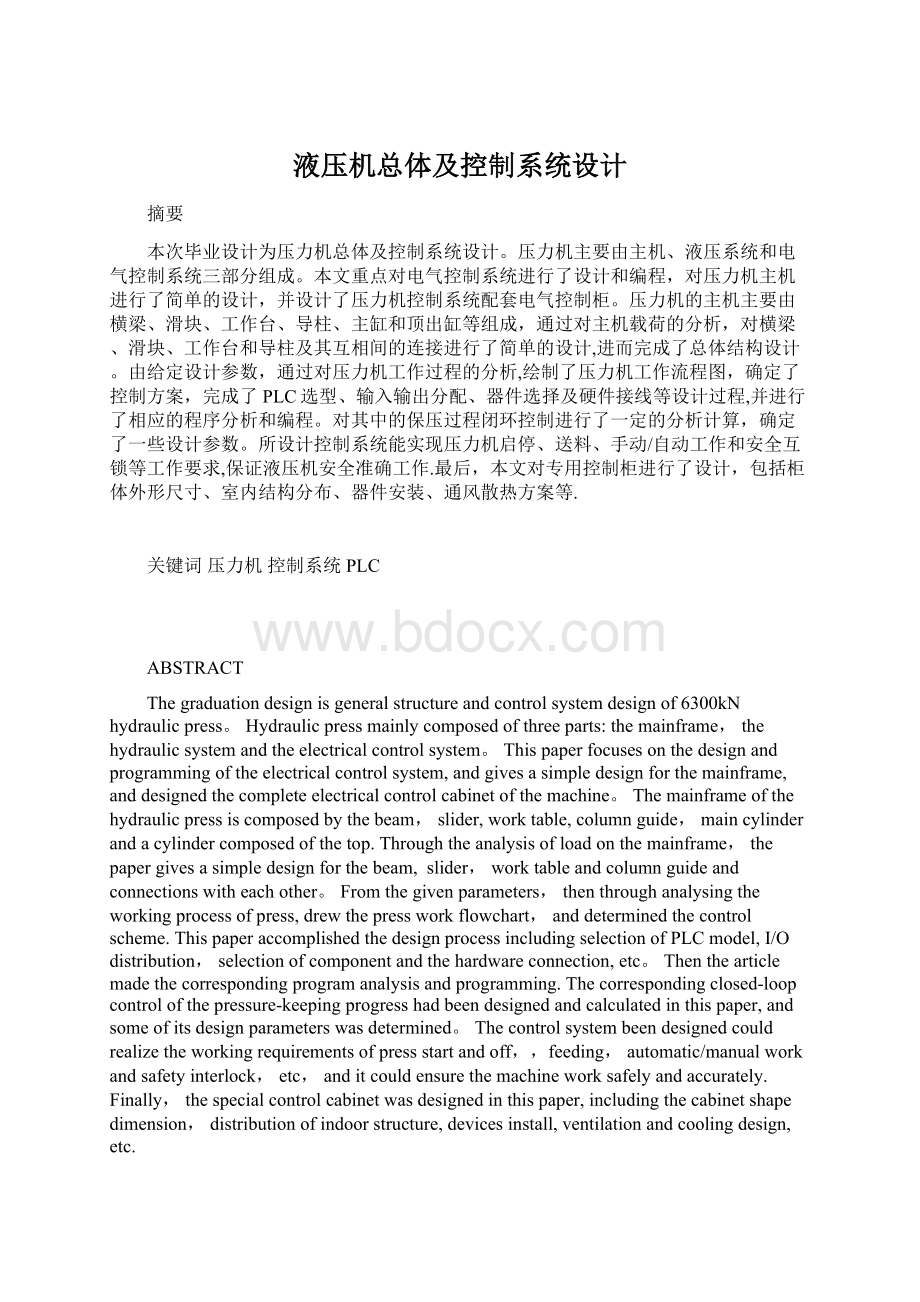
它具有下列一些特点:
1。
结构上易于得到较大的总压力,较大的工作空间及较长的行程,因此便于压制大型工件及较高的工件;
2。
与锻锤相比,工作平稳,撞击和振动很小,噪音小,对工人健康,厂房低级,周围环境及设备本身都有很大好处;
3.与机械压力机相比,本体结构比较简单,容易锻造,随着液压元件标准化、系列化、通用化程度的提高,以及专业丁点生产的逐步实现,比较适合与中小厂自行制造;
4。
随着大功率高轻型的出现,液压机快速性能已经有了很大的提高,工作速度状况越来越适应于更大范围的应用。
1.2国内外液压机技术发展现状及发展趋势
2。
1发展状况
由于液压机的液压系统和整机结构方面,已经比较成熟,国内外液压机的发展主要体现在控制系统方面。
微电子技术的飞速发展,为改进液压机的性能、提高稳定性、加工效率等方面提供了可能。
相比来讲,国内机型虽种类齐全,但技术含量相对较低,缺乏技术含量高的高档机型,这与机电液一体化,中小批量柔性生产的发展趋势不相适应。
在国内外液压机产品中,按照控制系统,液压机可分为三种类型:
一种是以继电器为主控元件的传统型液压机;
一种是采用可编程控制器控制的液压机;
第三种是应用高级微处理器(或工业控制计算机)的高性能液压机。
三种类型功能各有差异,应用范围也不尽相同。
但总的发展趋势是高速化、智能化.
1)继电器控制方式是延续了几十年的传统控制方式,其电路结构简单,技术要求不高,成本较低,相应控制功能简单,适应性不强.其适用于单机工作、加工产品精度要求不高的大批量生产(如餐具、厨具产品等),其也可组成简单的生产线,但由于电路的限制,稳定性、柔性差。
现在,国内许多液压机厂家是以这种机型为主,使用对象多为小型加工厂,或加工精度要求不高的民用产品.国外众多厂家只是保留了对这种机型的生产能力,而主要面向以下两种技术含量高的机型组织生产。
2)可编程控制器是在继电器控制和计算机控制发展的基础上开发出来的,并逐渐发展成以微处理器为核心,把自动化技术,计算机技术,通讯技术溶为一体的新型工业自动控制装置。
目前已被广泛的应用于各种生产机械以及自动化生产过程中。
随着技术的不断发展,可编程序控制器的功能更加丰富。
早期的可编程序控制器在功能上只能进行简单的逻辑控制。
后来一些厂家开始采用微电子处理器作为可编程序控制器的中央处理单元(CPU),从而扩大了控制器的功能,使其不仅可以进行逻辑控制,而且还可以对模拟量进行控制。
因此,可编程控制器控制方式是介于继电器方式和工业控制机控制方式之间的一种控制方式。
可编程控制器有较高的稳定性和灵活性,但在功能方面与工业控制机相比有一定差异。
3)工业控制机控制方式是在计算机控制技术成熟发展的基础上采用的一种高技术含量的控制方式。
这种控制方式以工业控制机或单片/单板机作为主控单元,通过外围接口器件(如A/D,D/A板等)或直接应用数字阀实现对液压系统的控制,同时利用各种传感器组成闭环回路式的控制系统,达到精确控制的目的。
作为液压机两大组成部分的主机和液压系统,由于技术发展趋于成熟,国内外机型无较大差距。
主要差别在于加工工艺和安装方面。
良好的工艺使机器在过滤、冷却及防止冲击和振动方面,有较明显改善。
在油路结构设计方面,国内外液压机都趋向于集成化、封闭式设计。
插装阀、叠加阀和复合化元件及系统在液压系统中得到较广泛的应用.国外已开始广泛采用封闭式循环油路设计.这种油路设计有效地防止泄油和污染.更重要的防止灰尘、污物、空气、化学物质侵入系统,延长了机器的使用寿命。
由于加工工艺等方面的原因,国内采用封闭式循环油路设计的系统还不多见。
在安全性方面,国外某些采用微处理器控制的高性能液压机利用软件进行故障的检测和维护.
2发展趋势
1)高速化,高效化,低能耗。
提高液压机的工作效率,降低生产成本。
2)机电液一体化.充分合理利用机械和电子方面的先进技术促进整个液压系统的完善。
3)自动化、智能化.微电子技术的高速发展为液压机的自动化和智能化提供了充分的条件。
自动化不仅仅体现的在加工,应能够实现对系统的自动诊断和调整,具有故障预处理的功能。
4)液压元件集成化,标准化.集成的液压系统减少了管路连接,有效地防止泄漏和污染.标准化的元件为机器的维修带来方便。
1.3本文研究主要内容
本文主要对630吨粉末成型压力机总体及其控制系统进行设计。
本文重点设计的是压力机的电气控制系统,简要地设计了压力机主体和电器控制柜及其装配。
研究设计过程如下:
首先,确定压力机的总体方案,对主机进行设计,确定液压机的总体布局;
其次,设计液压机的控制系统,通过工况分析,选择控制方式,设计电气线路,确定电器型号及安装,检验控制系统安全性和合理性等。
第2章630KN压力机总体方案设计
2.16300KN压力机的组成
完整的压力机应有主机、液压控制系统、电气控制系统组成。
以现有630T压力机为蓝本,本次设计也采用传统“三梁四柱”的主机机型,该型主机主要由主缸、横梁、滑块、导柱、工作台组成,其结构图见图2。
液压控制系统主要由液压泵、执行元件、控制元件、辅助元件等组成。
本设计的液压系统的电气控制系统是以可编程控制器(PLC)为主控元件的新型控制方式,主要由PLC、压力变送器、输入电路和输出电路等组成。
图2.1压力机主机结构图
1—副油箱2—横梁3—主缸4-导柱5—顶出缸6—工作台7—滑块
2压力机的工况特点
所设计压力机的主要技术参数如下表:
表2。
1设计参数
参数项
参数
公称压力(最大负载)
6300KN
主缸回程力
1250KN
顶出缸顶出力
1000KN
滑块行程
1000mm
顶出行程
355mm
滑块速度
空程下行
100mm/s
工进
6mm/s
回程
60mm/s
顶出活塞速度
顶出
80mm/s
退回
160mm/s
本压力机根据其工作要求,分为手动和自动工作两种工作模式。
两种工作模式的各自的工作过程如下:
自动工作:
滑块快进→滑块工进→保压→泄压→滑块回程→顶出缸顶出→顶出缸退回。
其工作循环过程见图2.2。
滑块快进
滑块工进
保压
泄压
滑块回程
顶出缸顶出
顶出缸退回
图2.2压力机自动工作循环过程
手动工作:
滑块启动后可在任意位置手动停止,手动缩回;
顶出缸手动顶出,手动退回。
2.3四柱液压机总体布局方案设计
了解了四柱液压机的组成、工作过程之后,可初步确定压力机的总体布局,布局图如图2.3所示.
图2。
3四柱液压机总体布局
1主机2副油箱3油管4液压站5电气柜6控制台
图2。
3为压力机整体布局简图,分为三个部分,即:
主机、液压系统、电气控制系统.液压系统的所有部件都集中安装在液压油箱处,使液压站布局结构变得紧凑。
电气控制元—8—件集中设计在电气柜中.启动、停止、快进、顶出、调整、等控制按钮设置在控制台上。
4压力机主机零部件设计
2.4。
1主机载荷分析
根据表2.1,本次设计压力机的最大工作负载为6300KN,主缸回程力为1250KN,顶出缸顶出力为1000KN。
由于工作时的负载远大于其它工况时的负载,因此在进行载荷设计时,取负载6300KN对压力机进行受力计算。
压力机结构形式为“三梁四柱”式,工进加压的负载作用在横梁和导柱上,受载时横梁受压,导柱受拉,受力如图2。
4所示。
F-负载T-导柱拉力
图2.4横梁、导柱受力图
2导柱设计
材料选择:
导柱在工作过程中主要承受拉力,材料必须具备较高的抗拉强度.导柱材料选择45圆钢,也可选用锻件形式。
热处理要求:
导柱除了承受拉力之外,外圆柱表面与滑块之间还存在摩擦力。
为了减少导柱表面的磨损,通过表面热处理提高表面硬度增加表面耐摩性.总的热处理工艺为调质和表面淬火。
理论设计计算:
液压机的最大主题:
负载约为6300kN,通过力传递后,最后由四根导柱承受6300kN的拉力,作用在每根导柱上的拉力为1575kN。
由许用拉应力公式(2—1),可计算导柱的安全直径D。
(2-1)
式中:
—许用应力;
取45钢
=80~100MPa;
F—轴向拉力;
A-横截面积。
即:
圆整后取导柱直径D=160mm,考虑到立柱带螺纹部分的应力集中对承载能力的削弱,以及为了防止四根导柱因瞬间的受力不均而被破坏,导柱直径可适当加大,取D=180mm.
结构形式:
上、下横梁用立柱调节圆螺母支承,两端用锁紧螺母锁紧。
3横梁设计
上横梁位于立柱上不,用于安装工作缸,承受工作缸的反作用力.对中小型液压机其结构形式主要有铸造和焊接两种。
本次设计的630吨四柱液压机的上横梁采用铸造结构,材料为ZG35.
形状尺寸要求:
上横梁通过立柱连接主机机身上半部,并安装工作油缸.为使其组成空间合乎要求,以及活塞平稳运行,因此要求上横梁安装油缸孔的轴线与安装油缸的台肩平面应垂直,上横梁与调节圆螺母接触面与主油缸台肩接触应平行,以及立柱穿过孔的的上下平面应平行等.
与油缸的连接方式:
依靠圆螺母固定油缸。
2.4.4滑块设计
滑块主要作用:
与主油缸活塞杆连接传递压力机的压力;
通过导向套沿导柱导向面上下往复运动;
安装工具等。
需要较好的强度、刚度及导向结构。
滑块材料亦采用ZG35。
结构形式:
根据压制工艺的性质,滑块无论如何都不能弯曲,因此滑块常是上面敞开的箱形梁,高度可设计低一点.
形状和尺寸要求:
滑块是液压机的主要运动部件,为保证液压机的精度要求,要求四导柱导向套孔轴线应相互平行,它应与连接活塞杆孔的中心线平行;
这些孔轴线都应与活动横梁下平面想垂直;
与活塞杆接触平面对下面要求平行。
与活塞杆的连接方式:
连接方式可分为可动连接和固定连接。
固定连接结构是通过活塞端面和以及圆柱面与滑块配合连接成不能具有相对运动的整体.本设计的连接方式是通过活塞杆头螺纹与螺母连接紧固于滑块内。
2.4.5工作台设计
结构形式:
工作台是主机的安装基础。
工作中承受机器本身的重量及全部载荷。
本设计选材料为ZG35,铸造结构.
形状尺寸要求:
工作台是整机的基础性零件,是安装磨具的标准,还要安装顶出缸和其他零部件。
因此对工作台面的不平度、各部件安装定位基面均应有必要的技术要求。
与顶出缸的连接方式:
采用螺钉及法兰盘将顶出缸固定在工作台上。
固定模具的结构:
为了固定模具,一般在工作台面上设有T型槽,按GB158—59标准尺寸进行加工。
第3章压力机电气控制系统设计
3.1控制系统方式选择
由前所述,液压机的控制系统主要有继电器控制方式、可编程控制器控制方式和工业控制计算机控制方式三种类型。
其中,传统的继电器控制方式存在较多的不足,设备体积大,在复杂控制系统中可靠性低,维护部方便,节点复杂,通用性和灵活性差;
而工业控制计算机(简称工控机)控制方式是新型的高智能控制方式,虽然其强大的运算和处理能力能满足各种复杂的控制过程要求,但其成本也是比较昂贵的。
而可编程控制器(PLC)相对于工控机具有很大的成本优势,相对于继电器又具有突出的控制优势,其时间响应快、控制精度高、可靠性好、控制程序可随工艺改变、易于计算机相连接、维护方便、体积小、质量小、功耗低,等等,目前为各种普通用途中、小型液压机广泛采用。
考虑到本设计中的630吨压力机的特点,选择PLC作为控制系统的核心元件。
3。
2PLC概述
2.1PLC的定义
可编程控制器(ProgrammableController,PC或PLC),它是在20世纪70年代以来,在继电器控制技术和计算机控制技术的基础上发展起来的一种新型工业自动化设备。
它以微处理器为核心,集自动化技术、计算机技术、通信技术为一体,被广泛应用在自动化控制的各个领域中。
1982年2月国际电工委员会(IEC)在颁布可编程控制器标准草案中,对可编程控制器定义为:
“一种专为在工业环境下应用而设计的数字运算操作的电子系统。
它采用可编程的存储器,在其内部存储执行运算、顺序控制、定时、计数和算术运算等操作指令,并通过数字或模拟的输入和输出,来控制各种类型的机械设备和生产过程。
”可编程控制器及其有关设备应按易于与工业系统连成一个整体和具有扩成功能的原则进行设计。
3.2。
2可编程从控制器的发展史
美国数字设备公司(DEC)于1969年研制成功了第一台可编程控制器PDP—14,并在汽车自动装配线上试用成功,从而开创了工业控制的新局面.从此这一技术在工业领域迅速发展起来.
从第一台PLC诞生,经过几十年的发展,PLC现已发展到第三代.各代的特点与应用范围如下表3.1所示.
表3。
1各代PLC的特点和应用范围
年代
功能特点
应用范围
早期:
20世纪60年代末~70年代中期
采用分立元件和中小规模集成电路CPU,磁芯存储器
取代电气控制、能同时完成逻辑控制,模拟量控制
中期:
20世纪70年代中期~80年代中、后期
增加复杂数值运算和数据处理,远程I/O和通信功能,采用大规模集成电路,微处理器,加强自诊断、容错计算
适应大型复杂控制系统需要并用于联网、通信、监控等场合
近期:
20世纪80年代中、后期~现在
高速大容量多功能,采用32位微处理器,变成语言多样化,通信功能进一步完善,智能化功能模块齐全
构成分级网络控制系统,实现图像动态过程监控,模拟网络资源共享
3PLC的发展趋势
随着应用领域的日益扩大,PLC技术及其产品仍在继续发展,主要朝着以下的方面发展。
1)微型化、网络化、开放性;
2)智能模块化;
3)编程语言的标准化和高级化;
4)网络通信功能标准化.
4PLC的基本组成
PLC的硬件构成主要有:
1)中央处理器(CPU);
2)存储器(系统存储器和用户存储器);
3)输入、输出接口;
4)电源。
PLC的软件构成包括系统软件和用户程序,其应用程序的编程语言最常用的是梯形图(LAD)和指令表(STL)。
36300KN压力机控制系统分析
1压力机对控制系统的控制要求
1.压力机的基本工作过程
液压机的工作流程由送料车送料、送料车退回、滑块快速下行、慢下加压、保压延时、卸压回程、顶出缸顶出、顶出缸退回9个过程组成。
在自动控制的压力机中,从滑块开始下行至顶出缸退回7个过程可做到全自动依次运行,只有人工按停止按纽或急停按纽干预方能停车.
2.设备控制要求
压力机的自动控制系统要求能实现自动及手动两种控制方式,在正常工作时选择自动控制方式。
液压机自动工作状态:
将转换开关打到自动工作状态,按下滑块下行启动按钮,则压力机依以下步骤自动工作.
1)液压机滑块靠自重快速下行。
2)液压机滑块慢下加压.
3)达到设定压力开始保压.
4)保压延时到卸压回程。
5)回程到位后,延时一定的时间顶出缸顶出。
6)顶出到位后,延时一定的时间顶出缸退回。
7)延时一定的时间进行下一个工作循环。
压力机手动工作状态:
将转换开关打到手动工作状态,手动工作过程如下:
1)按“压制”、“回程"
按钮,压力机滑块动作;
按“停止”按钮或压下行程开关,滑块停止.
2)按“顶出”、“退回”按钮,顶出缸动作,压下限位开关停止。
其他控制要求:
1)压力机压制药柱时,为防止防爆门未关闭就加压带来的安全隐患,要求滑块在防爆门关闭的情况下才能下行。
2)滑块回到原位时,顶出缸才能顶出;
同样,顶出缸回到原位,滑块才能下行。
3)自动保压过程为闭环控制。
4)保压值可手动设定。
3.3.2控制系统原理分析设计
由上述的工作过程分析,结合PLC闭环控制的特点,可设计出本压力机工作和控制的原理如图3.1所示。
图3。
1压力机控制原理框图
3.4PLC输入输出量分析
3.4.1输入输出分配
压力机的控制系统中,各硬件的作用不同,则在控制系统中的位置也不同,其中,控制按钮、行程开关和压力变送器系发讯元件,要放在输入端;
继电器、接触器、信号灯、电磁阀等为收讯元件,要放在输出端。
因此,PLC的输入输出可表示成图3。
2.
图3.2PLC输入输出框图
4.2输入量分析
本设计压力机的电气控制系统中,需要主电机(用M1表示)启停按钮各一个,送料电机(用M3表示)往返按钮各一个,滑块下行、返回和停止按钮各一个,顶出缸顶出和停止按钮各一个,急停按钮一个,滑块行程限位开关三个,顶出缸限位开关两个,送料车限位开关两个,自动/手动工作切换开关一个,防爆门关闭行程开关一个,保压电动机(用M2表示)可以靠自动工作过程中PLC内部程序控制实现启停,不占用输入口。
因此,总计约20个开关输入量。
由于保压过程为闭环控制,需要PLC的模拟量处理,因此初步预计模拟量输入压力传感器(或压力变送器)一个,压力设定电位器一个,共2个模拟输入量。
4.3输出量分析
压力机动力系统共有三个压力机,主电动机为星—三角形启动,需要三个交流接触器;
保压电动机直接启动,需要一个交流接触器;
送料电动机直接启动,往返(正反转)各需要一个交流接触器;
根据压力机的液压系统中电磁阀的数量,共有10个电磁线圈,总计约16个开关输出量。
根据保压过程闭环控制过程及保压回路所用比例阀,需要一路模拟量输出。
5PLC选型及硬件配备
根据上述控制特点,采用小型PLC即可满足功能要求。
由于西门子S7-200系列属于小型PLC,其许多功能达到大、中型PLC的水平,而价格却和小型PLC的一样。
特别是S7-2000PU22*系列PLC,由于它具有多种功能模块和人机界面可供选择,所以系统的集成非常方便,并且可以很容易地组成PLC网络。
可用梯形图、语句表和功能图三种语言来编程。
且指令功能强,易于掌握、操作方便.近年来,S7—200PLC已在工业各领域得到了广泛的应用。
S7-200CPU22*系列PLC共有五种CPU模块,其各自的