中国化纤产业发展与环境保护白皮书39Word下载.docx
《中国化纤产业发展与环境保护白皮书39Word下载.docx》由会员分享,可在线阅读,更多相关《中国化纤产业发展与环境保护白皮书39Word下载.docx(35页珍藏版)》请在冰豆网上搜索。
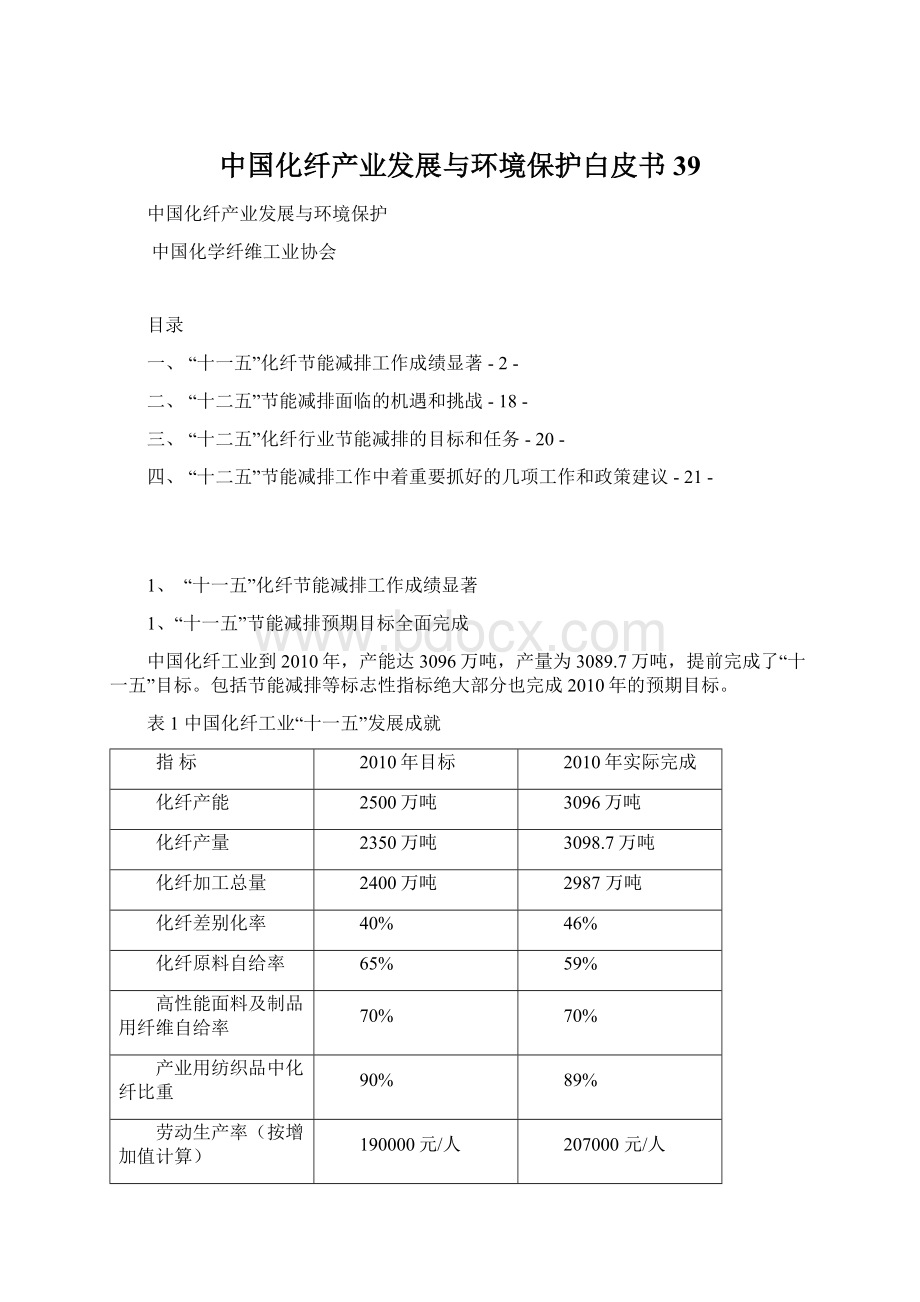
吨纤维废水排放量降低10%;
吨纤维废气排放量降低10%
吨纤维废水排放量降低29.75%;
吨纤维废气排放量降低26.5%。
从完成“十一五”的目标上来看,行业综合指标,除了化纤原料自给率没有达到预期效果,由于
单位能耗换算成万元增加值能耗。
气体总量没有完成,单位废气排放完成,原因在于化纤总量的增加。
节能降耗、节水减排(固、液、气)取得的成绩如下:
1、节能
21世纪起始10年,是我国化纤工业国产化、大型化、低成本工程技术进步最快的10年,在“节能”方面表现尤为突出。
表12中国化纤行业“十一五”节能统计表
2005年
2010年
综合能耗
单耗(KG标煤/T)
742.5
497.8
总耗(万吨标煤)
1175.9
1538.1
其中:
电耗
单耗(千瓦时/T)
1188.6
715.3
总耗(亿千瓦时)
188.2
220.99
燃料煤耗
512.8
426.22
812.2
972.7
2010年全行业总能耗1538万吨标煤,单耗从2005年的742.5KG标煤/吨降到497.8KG标煤/吨,下降%,实际节能万吨标煤。
2010年电耗221亿度,单耗从2005年的1679.4千瓦时/吨降到715.3千瓦时/吨,下降57.4%,实际节电298亿度。
2010年燃料煤耗972.7万吨,单耗从2005年的668.61KG标煤/T降到426.22KG标煤/T,下降35.8%,实际节燃料煤548万吨。
占中国化纤总产量52%的涤纶长丝节能效果最好:
表13涤纶长丝行业2010年和2005年度能耗统计表
418.0
278.3
320.1
442.5
1100
645
84.2
102.6
284
199
217.5
278.6
2010年涤纶长丝行业总耗能442.5万吨标煤,单耗从2005年的418.0KG标煤/吨下降到278.3KG标煤/吨,下降33.4%,实际节能222万吨标煤。
2、降耗
“节能”和“降耗”是企业为了提高竞争力必然的主动行为,在新时期,化纤产业相当品种的原料和辅料消耗指标已经进入世界先进行列,有些已经接近理论值。
以粘胶纤维行业为例:
表18粘胶行业主要原料消耗统计表
年份
产量(万吨)
浆粕
单耗(Kg/T)
总耗(万吨)
2005
116.16
1038
120.55
2010
183.5
1028
167.91
浆粕消耗:
2010年比2000年单耗下降15Kg/T,行业总体降耗2.21万吨;
2010年比2005年单耗下降10Kg/T,行业总体降耗1.63万吨。
表19粘胶纤维行业主要辅料消耗统计表
产量
(万吨)
烧碱
硫酸
二硫化碳
总耗
单耗
(Kg/T)
559
64.99
860
99.93
203
23.53
2010
551
89.94
810
132.23
187
30.54
2010年比2005年单耗下降8Kg/T,降耗1.31万吨
2010年比2005年单耗下降50Kg/T,降耗8.16万吨
2010年比2005年单耗下降16Kg/T,降耗2.61万吨
合计
2010年比2005年降耗12.08万吨
再以聚酯为例:
表20聚酯(纤维级)行业主要原料消耗表
PTA
EG
(Kg/吨)
总消耗
1270
862
1094.74
338
429.26
2050
859
1763
335
687
PTA单耗从2000年的865KG/T降到2005年的862KG/T,降耗3.81万吨;
MEG单耗从2000年的340KG/T降到2007年的338KG/T,年降耗2.54万吨,合计近6.35万吨。
到2010年,PTA单耗降到859KG/T,比2005年再降3Kg/T,实际降耗6.15万吨;
MEG单耗将降到335KGT,比2005年再降3Kg/T,实际降耗6.15万吨,合计降耗12.3万吨。
再以涤纶长丝为例:
表21涤纶长丝行业主要原料消耗表
吨产品聚酯消耗量(KG)
POY
FDY
工业丝
791
1008
1070
799
1670
1005
1050
1600
涤纶长丝行业和聚酯行业一样,进入21世纪,大量新技术、新装备、新工程的应用,极大提高了生产的稳定性,检修周期和检修时间大大缩短,原料消耗大幅降低,2010年在产量达到1670万吨的情况下,POY、FDY吨产品聚酯消耗量比2005年减少3kg/T,涤纶工业丝原料单耗大幅下降20kg/T。
3、节水
表22中国化纤产业“取水”统计表
全行业
取水量(T/T)
19.1
14.2
取水总量(万吨)
30233
43826
其中:
粘胶行业
134.0
114.4
15560
20986
2010年,化纤全行业取水4.38亿吨,单位取水量14.2吨/吨,比2005年的19.1吨/吨,下降25.7%,实际节水近1.51亿吨。
其中,粘胶纤维行业用水量占全行业的47.9%,是节水的重中之重。
2010年该行业单位用水量从2005年134T/T降到114.4T/T,下降14.6%,节水总量3603万吨,尽管如此粘胶行业节水问题仍然任重而道远。
4、减排
(1)“固体废物”减排
表23化纤行业固体废物产生及处理利用情况表
工业固体废物产生量(万吨)
其中:
危险废物(万吨)
工业固体废物综合利用量(万吨)
危险废物排放量(万吨)
2004年
322
14.46
287
342
27.73
315
2006年
376
26.13
363
2007年
355
12.41
341
2008年
339
31.85
323
2009年
373
41.49
347
根据国家统计局全口径统计:
中国化纤行业固体废物排放量虽然逐年增长,但大大低于产能增长的速度,低10个点以上。
重要的是工业固体废物综合利用率逐年上升,2004年、2005年、2007年分别为89.1%、92.2%、96.1%,而且危险废物从2004年起做到零排放。
2010年化纤行业的固体废物的综合利用率提高到98%。
(2)“废水废液”减排
表24中国化纤行业“废水废液”排放统计表
废水排放
单位排放(T/T)
16
11.24
总量(万吨)
25333
34739
COD排放
单位排放(Kg/T)
75.2
33.6
11.91
10.38
2010行业废水排放总量为3.47亿吨,吨纤维排放比2005年减少4.76吨,减排14707万吨。
2010年行业废水吨纤维排放量进一步减少,为11.24T/T,比2005年减少29.75%。
COD单位排放将降到33.6Kg/T,COD排放总量为10.38万吨,比2005年减少12.8%。
全行业COD达标排放,其中粘胶行业大部分企业废水在一级处理后,送社会管网处理也能达标排放。
废水废液减排任务最艰巨的是粘胶行业,但是经过努力,全面完成目标,对完成行业废水排放目标完成做出突出贡献。
粘胶行业废水排放表,
(3)“废气”减排
表25中国化纤行业废气排放量统计表
总量
单位排放量(万NM3/T)
2.15
1.58
排放总量(亿NM3)
3408.91
4881.73
工艺废气
1.77
1.36
2800.8
4202
燃烧废气
0.38
0.22
608.11
679.7
从单位排放量分析:
单位排放量:
2010年比2005年减排26.5%
其中工艺废气:
2010年比2005年减排23.2%
其中燃烧废气:
2010年比2005年减排42.1%
由于化纤总产量的扩大,排放总量继续在明显增加,具体来说:
排放总量:
2010年比2005年增加1473亿NM3,增长43.2%
2010年比2005年增加1401亿NM3,增长50%
2010年比2005年增加71.6亿NM3,增长11.8%
废气中主要污染物排放:
表26中国化纤行业废气排放中主要污染物统计表
(粘胶行业为主)
CS2
单位排放量(KG/T)
121.3
53.35
排放总量(万吨)
14.09
9.79
H2S
52.24
22.94
6.07
4.21
CS2和H2S的排放主要集中在粘胶行业。
CS2:
2010年比2005年减少56.02%
H2S:
2010年比2005年减少56.09%
从排放总量分析:
2010年比2005年减排4.3万吨,减少30.52%
2010年比2005年减少1.86万吨,减少30.64%
表27中国化纤行业废气排放中主要污染物统计表
SO2
7.06
6.52
5.05
4.84
4.19
11.5
13.2
12.2
11.7
粉尘
0.06
0.10
0.03
0.02
0.04
0.1
0.2
0.061
0.045
在全行业燃烧废气排放中,在产量逐年增加的前提下,工业SO2排放总量从2006年开始逐年下降,单位排放量一直呈现下降趋势;
化纤行业工业粉尘总体排放量和单位排放量都非常少,总量在千吨左右徘徊,单位排放量控制在0.05KG/T以下。
SO2:
2009年比2005年降低%
粉尘:
2009年比2005年基本持平
总结以上:
气体减排是我行业减排的重要内容,也是国家约束性指标的突出目标,根据我行业的具体情况,工艺减排主要集中在粘胶行业,燃料废气减排主要是在行业的能源需求,体现在国家统计中的SO2粉尘
从单位排放来看,四项指标均有大幅降低,减排总量没有完成国家要求的10%减排目标,气体减排方面仍有巨大差距。
同时,在减排方面也取得了长足的进步。
与2005年相比,2010年化纤吨纤维取水量下降25.7%,废水排放量下降25%;
2010年粘胶行业水重复利用率在75%以上,较好企业已达95%以上,聚酯行业水重复利用率在95%以上。
表2、中国化纤行业2010年比2005年节能减排统计
2010/2005比例
实际节能减排效果
单位综合能耗
吨纤维能耗比2005年下降30%
节能608万吨标煤
单位用水
吨纤维取水量下降40.3%
节水2亿吨
固体排放
固体废物综合利用率提高到98%
液体排放
COD排放总量减少12.8%
减排1.53万吨
气体排放
CS2排放总量减少1.2%
H2S排放总量减少1.0%
SO2排放总量减少21.1%
粉尘排放总量减少38.7%
CS2减排1600吨
H2S减排400吨
SO2减排1.1万吨
粉尘减排3600吨
近几年,中国化纤行业一直在积极推动以节能、降耗、节水、减排、清洁生产、循环经济六项内容的行业节能减排工作,并已取得了明显成效。
2010年,化纤行业单位综合能耗预计比2005年下降30%,节能608万吨标煤;
吨纤维取水量下降40.3%,节水2亿吨;
固体废物综合利用率提高到98%;
COD排放总量减少12.8%,减排1.53万吨;
气体排放也有明显下降。
表3、装置单位综合能耗变化表
品种
“十五”期末
“十一五”期末
单位综合能耗与”十五”末比
装置规模(万吨/年)
聚酯
40
↓4%
粘短
3
6
↓12%
锦纶
7
氨纶
0.35
↓36%
聚酯装置单位综合能耗“十一五”期末与“十五”末比降低4%,达到95.6kg标煤/吨。
粘胶短纤装置单位综合能耗“十一五”期末与“十五”末比降低12%,达到1192标煤/吨。
锦纶装置单位综合能耗“十一五”期末与“十五”末比降低4%,达到176kg标煤/吨。
氨纶装置单位综合能耗“十一五”期末与“十五”末比降低36%,达到2.07吨标煤/吨。
2、技术进步是行业基本完成节能减排目标的基础
“十一五”是我国化纤行业创新发展的新阶段,大量的新技术、新工艺应用开发的密集时期。
对行业节能减排来说,规模化和大量采用节能减排的新技术甚至高新技术是我行业节能减排基本达到预期目标的根本动力。
(1)规模化
科技进步为我国化纤工业的快速发展提供了强大推动力,通过十多年的技术创新,化纤行业的装备和技术水平有了大幅度提升。
单线产能迅速增加,综合能耗明显降低。
表4、中国化纤各主要品种最大单线产能变化表单位:
万吨/年
“九五”期末
聚酯聚合
10
2
锦纶聚合
氨纶聚合
聚酯单线年产能由6.6万吨提升到10万吨、15万吨、20万吨、30万吨、40万吨;
粘胶短纤单线产能由2万吨提升到3万吨、4.5万吨、6万吨/年;
锦纶聚合单线产能由2万吨提升到3万吨、7万吨/年;
氨纶聚合单线产能由1000吨/年升到3500吨/年。
规模化带来的最大效益是生产成本的下降,包括吨能耗及物耗的变化。
表61998年和2008年涤纶长丝生产成本经济下降统计表
“九五”时期
“十一五”时期
下降
投资成本(元/吨)
4000-7500
1000-2200
3000-5300
加工成本(元/吨)
1500-2500
800-1200
700-1300
运行成本
能耗(kg标煤/吨)
400-650
220-320
180-330
物耗(kg/T)
1025-1040
1005-1015
20-25
用工(人/万吨)
150
60
90
经过“十五”期间大型国产化聚酯工程成套装置及配套直纺长丝设备与工程的推广和应用,我国涤纶长丝生产技术已达到国际先进水平。
以直接纺、大容量、多头纺、多品种、短流程长丝技术,采用外环吹或中心环吹技术,能耗大幅度降低,产品质量明显提升。
2008年,单位生产能力投资成本比1998年下降70%以上,单位产品加工成本也下降50%左右,运行成本中能耗下降50%左右,每吨产品物耗下降大于20kg,每万吨产品用工人数减少90人,仅为60人。
(6)产业结构升级成果显著:
1优质资产在行业内比重已经提高到70%
表102010年和2005年产能对比表
2010年(万吨)
化纤总量
3096.4
1923
粘胶纤维
224.63
111.4
粘胶长丝
20.43
21.9
粘胶短纤
204.2
89.5
合成纤维
2871.83
1811.6
涤纶
2475.52
1552.6
长丝
1697.44
974
短纤
675.3
550.4
锦纶
189.20
96.7
腈纶
84.9
79
维纶
9.57
7.7
氨纶
38.99
18.3
丙纶
57.3
2010年化纤产能达到3096万吨,比2005年增加1.6倍,年均增长10.0%。
以2005年作为技术水平的划界点,聚酯涤纶行业中优质资产比例73.2%,锦纶行业也达到63.2%,粘胶行业为58.8%,腈纶行业为45%。
以单线产能为标志的优质资产在,
5、清洁生产和循环经济
清洁生产是一种持续地将污染预防应用于生产全过程的战略,强调从源头抓起,着眼于生产全过程控制。
通过清洁生产不仅会提高资源、能源利用率和原材料转化率,减少对资源的消耗和浪费,从而保障资源的永续利用,而且把污染消除在生产过程中,尽可能地减少污染物的产生和排放量,以减轻或者消除对人类健康和环境的危害。
循环经济是以产品清洁生产、资源循环利用和废物高效回收为特征的生态经济。
由于它将对环境的破坏降到最低程度,并且最大限度地利用资源,因而大大降低了经济发展的社会成本,有利于经济的可持续发展。
循环经济以资源的高效利用和循环利用为目标,以“减量化、再利用、资源化”为原则,以物质闭路循环和能量梯次使用为特征。
对于化纤行业而言,新技术、新装备的应用在降低能耗和生产成本的同时,也满足了社会对行业在节能、减排等循环经济硬指标上的要求。
“十一五”期间,节能减排工作不仅贯彻关于国家综合治理方案,而且抓住以清洁生产与循环经济的关键内容予以推动,对推动“十一五”节能减排的技术和工程发挥了较好的作用。
中国化纤行业“十一五”期间,节能减排技术推广应用统计。
在“十一五”期间,对节能减排工作起到重要影响的主要工程和技术以及承担的企业如下表:
这些技术和工程是关键的技术与工程。
以聚酯、涤纶长丝和粘胶行业为例:
表28“十一五”期间对节能减排起到重要影响的主要工程和技术以及优势企业
企业
技术名称
技术主要内容
应用前景分析
连续聚合清洁生产产业化关键技术开发
上海聚友化工
年产1-10万吨差别化聚酯连续聚合柔性生产线
自主开发的低温短流程连续聚合聚酯技术,通过在线添加改性剂,可连续生产阳离子可染聚酯、低熔点聚酯、高收缩聚酯、水溶改性PET产品。
环保效果添加剂加入方式、热媒系统设计等成套技术的先进性保证了装置的的节能、低耗,从而降低了污染物的排放,装置的环境友好程度增加。
单体乙二醇与副产物乙醛的高效回收回用技术
开发高效的导向筛板塔酯化蒸汽精馏系统;
运用空气气提技术与装备分离净化酯化废水技术,并对聚酯生产企业产生的废水中的有机物乙醛利用专有的技术进行回收,将回收的乙醛制成醋酸或销售到下游的需求客户手中,形成资源的循环利用。
PET连续聚合装置废液COD值从26000-30000降到3000以下,经处理后达到排放标准,废液中乙醛回收率≥99.5%;
连续聚合聚酯装置酯化废水减排技术
夹带乙二醇(EG)的水蒸气,进入酯化工艺塔进行精馏,蒸汽中的EG富集在工艺塔底。
酯化废水用中温空气作气提处理,水与空气在萃取气提塔内逆向流动,废水中的乙醛等轻组分被吹出。
吹出物可进一步处理得到高纯度乙醛,或直接将吹出气导入热媒炉焚烧。
采用高分馏效率复合结构酯化工艺塔,每吨聚酯产品相当于减少EG消耗0.4公斤,少排COD5公斤;
每套10万吨/年。
中国纺织工业设计院
利用气提焚烧技术处理聚酯装置、SSP(固相增粘)装置的工艺尾气
用气相热介质(热风或蒸汽)对酯化水作气提,可以除去其中的乙醛;
把气提的尾气及聚酯装置各个部位产生的工艺尾气引入热媒炉焚烧,可杜绝乙醛向大气的直接排放,从而达到清洁生产的要求。
采用上述气提技术,可使废水的COD值降低20,000-25,000(g/L),从而大大减轻污水处理的负荷。
上海石化
连续聚合聚酯装置酯化蒸汽能量回收技术
通过增加换热器将生产中产生的部分废水,在用冷却水冷凝成液体前抽出去,靠这些低品质蒸汽的蒸发潜热将进第一酯化釜的浆料从30℃加热到95℃,这样既可以减少循环冷却水的用量,又能对反应原料进行预加热。
可节约重油消耗2.9kg/t,减少循环冷却水量折合标油为0.72kg/t,合计可节约标油3.62kg/t。
按全年产量35万吨计算可节约标油1267吨。
每吨标油按2660元计算可节约费用:
337万元。
低温短流程差别化聚酯装备和技术
改造老装置对酯化工艺逐步进行优化,解决能耗、EG单耗高问题。
实施后EG单耗从333.5kg/t降328kg/t,重油单耗从68kg标油/t降到61kg标油/t,废水排污量从58吨/月降到48吨。
年经济效益550万元
熔体直接纺丝清洁生产产业化关键技术开发
江苏盛虹
高效节能型涤纶长丝纺丝技术与装备
采用20头纺双机高效新型卷绕设备和技术,half板或外环吹风技术使产品冷却均匀,并采用双油嘴上油技术,突破一些定型温度上下限的理念。
生产20D/12F、20D/144F、25D/144F、30D/24F、50D/144F、150D/288F、300D/576F等规格产品达到国际领先水平。
采用连续聚合纺丝清洁生产产业化关键技术,开发高功能、高品质、低排放、低能耗特征的系列化纺织产品,高效节能型