聚氯乙烯PVC注射成型常见故障分析及排除方法Word格式.docx
《聚氯乙烯PVC注射成型常见故障分析及排除方法Word格式.docx》由会员分享,可在线阅读,更多相关《聚氯乙烯PVC注射成型常见故障分析及排除方法Word格式.docx(9页珍藏版)》请在冰豆网上搜索。
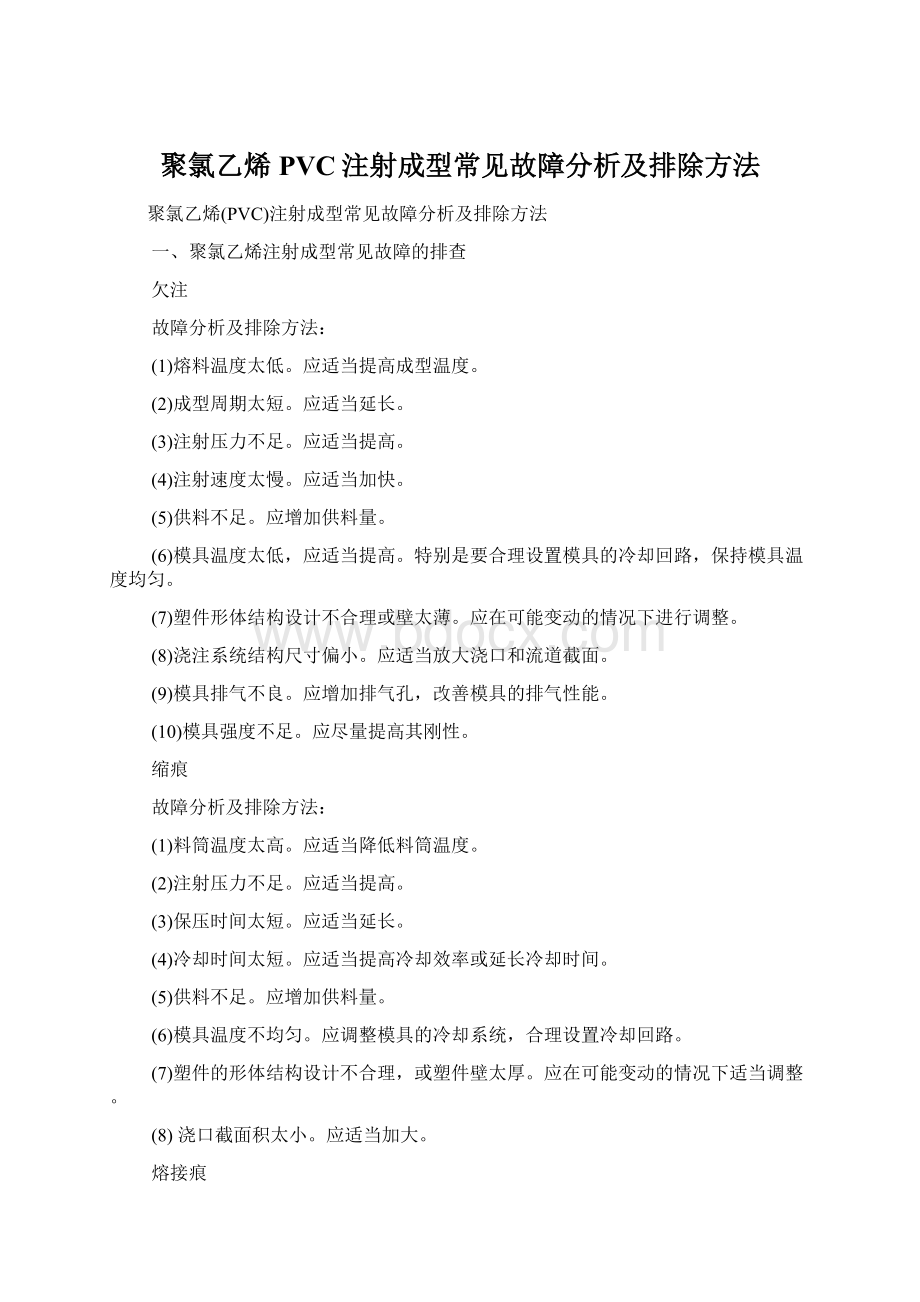
应增加排气孔,改善模具的排气性能。
(10)模具强度不足。
应尽量提高其刚性。
缩痕
(1)料筒温度太高。
应适当降低料筒温度。
(2)注射压力不足。
(3)保压时间太短。
(4)冷却时间太短。
应适当提高冷却效率或延长冷却时间。
(6)模具温度不均匀。
应调整模具的冷却系统,合理设置冷却回路。
(7)塑件的形体结构设计不合理,或塑件壁太厚。
应在可能变动的情况下适当调整。
(8)浇口截面积太小。
应适当加大。
熔接痕
(3)注射速度太慢。
(4)模具温度太低,应适当提高。
(5)浇口截面积太小。
(6)模具排气不良。
(7)冷料穴结构尺寸太小或位置不当。
应合理调整。
(8)原料内混入杂质。
应彻底清除异物杂质或换用新料。
(9)脱模剂用量偏多。
应尽量减少其用量。
(10)镶件设置不合理。
应适当调整。
(11)原料着色不均匀。
应选用分散性较好的着色剂,以及延长混色的搅拌时间,使原料着色均匀。
流料痕
(5)模具温度不均匀。
(6)浇口截面积太小。
(8)原料着色不均匀。
应选用分散性较好的着色剂,以及延长混色的搅拌时间。
光泽不良
(2)成型周期太长。
应适当缩短。
(3)螺杆背压太低。
(5)浇注系统结构尺寸偏小。
(7)原料内混入杂质。
(8)脱模剂用量偏多。
(9)原料未充分干燥。
应适当提高干燥温度及延长干燥时间。
气泡
(4)注射速度太快。
应适当减慢。
(5)保压时间太短。
(8)浇口截面积太小。
(10)原料未充分干燥。
色泽不均
(3)原料着色不均匀。
烧焦及黑纹
(3)注射压力太高。
应适当降低。
(4)注射速度太快。
(5)螺杆背压太高。
(7)模具排气不良。
溢料飞边
(1)熔料温度太高。
应适当降低料筒温度及喷嘴温度。
(2)注射压力太高。
(3)注射速度太快。
(4)保压时间太长。
(5)供料量太多。
应适当减少。
(6)合模力不足。
(7)模具温度太高。
(8)塑件的形体结构设计不合理,应在可能变动的情况下适当调整。
(9)模具强度不足。
应设法增加其刚性。
根据塑件的形体及模具结构进行应适当调整。
翘曲变形
(1)料筒温度太低。
(5)保压时间太长。
(6)模具温度太高。
(7)模具的冷却系统设置不合理,冷却回路应根据塑件结构的冷却要求合理设置。
(9)顶出装置设置不合理。
应尽量加大顶出面积及增加顶出点。
银丝纹
(5)模具温度太低。
(6)注射量太少。
应适当增加。
(7)浇口截面积太小。
(8)模具排气不良。
(9)模具冷料穴太小,应适当加大。
(10)原料内混入杂质。
(11)原料未充分干燥。
分层剥离
(1)熔料温度太低,应适当提高料筒及喷嘴温度。
(2)注射速度太快。
(3)模具温度太低。
(4)原料内混入杂质。
表面变色
(4)螺杆背压太高。
表面划伤
(3)保压时间太长。
(4)模具温度太低。
(5)顶出装置设置不合理。
(6)模具脱模斜度不足。
应适当放大。
脱模不良
(1)注射压力太高。
(2)保压时间太长。
(3)冷却时间太长。
(4)供料量太多。
(5)模具温度太高。
(7)顶出装置设置不合理。
(8)模具强度不足。
(9)模具脱模斜度不足。
(10)塑件形体结构太复杂。
应在可能变动的条件下进行调整。
二、软质聚氯乙烯注射成型常见故障的排查
制品表面光泽度差
(1)加工温度太低,物料塑化不良。
应适当提高加工温度,改善塑化效果。
(2)模具温度太低。
应适当提高模温度。
(3)物料流动性太差,应更换原料或调整原料配方。
(4)模具型腔表面光洁度太差。
应适当提高模具型腔表面光洁度。
(5)成型过程中助剂析出,在模具表面形成结垢。
应及时清除模具表面结垢,如果比较严重,应调整配方。
(6)回用料的用量太多。
应适当减少回用料的用量。
(7)料温太高,树脂分解。
应适当降低注射温度,改进热稳定系统。
收缩变形
(1)保压时间太短。
应延长保压时间,特别是浇口附近发生收缩时,可用延长保压时间的方法来解决。
(2)保压压力太低。
应适当提高保压时间。
(3)注射压力太低。
应适当的提高注射时间。
(4)成型温度太高。
应适当降低成型温度。
(5)加料量不足。
应适当增加加料量。
(6)模温太高或加热不均匀。
应提高模具的冷却效率。
(7)开模过早,制品冷却不足。
应延长制品在模内的冷却时间。
(8)制品厚薄相差太大,在制品厚的部分由于压力不足,容易产生凹陷收缩。
应修改制品设计。
(9)浇口截面积太小。
欠注,缺料
(1)注射压力或保压压力太低。
应适当提高注射压力或保压压力。
(2)保压时间太短。
应适当延长保压时间。
(3)加工温度太低。
应适当提高加工温度。
应适当提高注射速度。
(5)模具或喷嘴温度太低。
应适当提高模具或喷嘴温度。
(6)喷嘴处有杂质或分解物堵塞。
应清理注塑机喷嘴。
(8)模具排气孔堵塞。
应清除模具排气孔中的堵塞物。
(9)注塑机注射量太小。
应适当提高注射量。
飞边
(2)物料温度太高。
应适当降低物料温度。
(3)注射量太大。
应适当降低调整注射量。
(4)锁模力太低应适当提高锁模力。
(5)模具分型面配合精度较差。
应提高模具分型面的配合精度。
(6)模具刚性较差,模具发生变形。
应适当提高模具刚性。
(1)注射压力太低。
应适当提高注射压力。
(2)注射速度控制不当。
应适当调整注射速度。
(3)注射温度太高,树脂分解。
(4)模具排气孔堵塞。
(6)原料未充分干燥。
冷料斑
(1)加工温度太低,塑化不良。
(2)螺杆背压太低。
应适当提高背压。
(3)模具中没有冷料穴或太小。
应修改模具,增加或扩大冷料穴。
银丝
(1)原料中水分或挥发物含量太高。
应充分干燥原料。
(2)料筒温度太高。
(3)回用料的用量太多。
焦化分解
(1)注射温度太高,物料焦化分解,随熔料注入模具形成制品上的焦点。
应适当降低注射温度,清除料筒和流道死角中的异物杂质。
(2)注射速度太高。
应适当降低注射速度。
(3)喷嘴处有杂质或分解物堵塞。
应清理注射喷嘴。
(4)原料热稳定性太差。
应更换原料或调整配方,改进热稳定系统。
(5)润滑剂用量不足。
应适当增加润滑剂用量。
应改善模具排气系统。
(7)模具的浇口截面尺寸太小。
应适当扩大模具浇口截面尺寸。
感谢您的阅读,祝您生活愉快。