供应链环境下核心企业生产计划研究Word文档格式.docx
《供应链环境下核心企业生产计划研究Word文档格式.docx》由会员分享,可在线阅读,更多相关《供应链环境下核心企业生产计划研究Word文档格式.docx(4页珍藏版)》请在冰豆网上搜索。
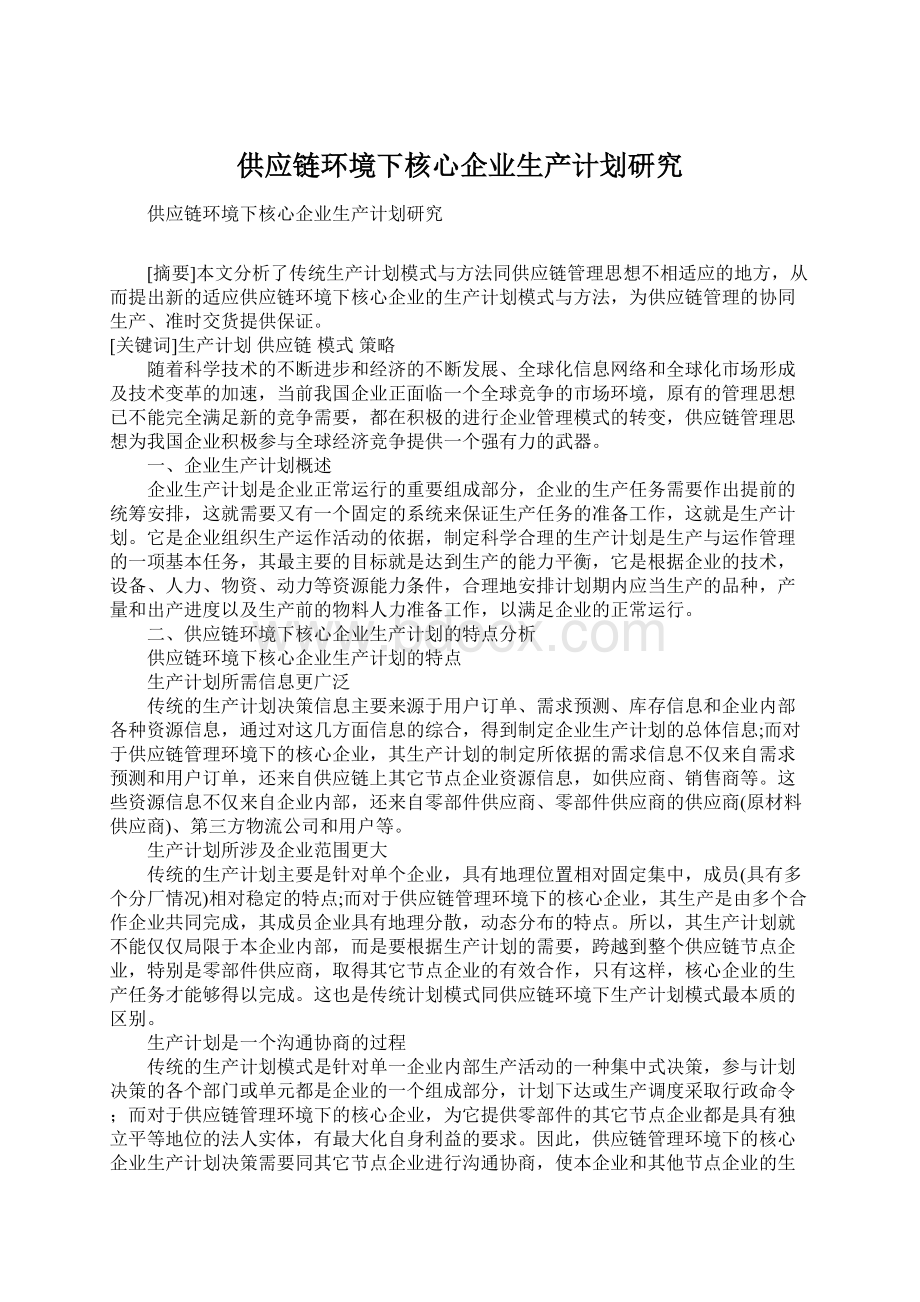
供应链环境下核心企业生产计划的特点
生产计划所需信息更广泛
传统的生产计划决策信息主要来源于用户订单、需求预测、库存信息和企业内部各种资源信息,通过对这几方面信息的综合,得到制定企业生产计划的总体信息;
而对于供应链管理环境下的核心企业,其生产计划的制定所依据的需求信息不仅来自需求预测和用户订单,还来自供应链上其它节点企业资源信息,如供应商、销售商等。
这些资源信息不仅来自企业内部,还来自零部件供应商、零部件供应商的供应商(原材料供应商)、第三方物流公司和用户等。
生产计划所涉及企业范围更大
传统的生产计划主要是针对单个企业,具有地理位置相对固定集中,成员(具有多个分厂情况)相对稳定的特点;
而对于供应链管理环境下的核心企业,其生产是由多个合作企业共同完成,其成员企业具有地理分散,动态分布的特点。
所以,其生产计划就不能仅仅局限于本企业内部,而是要根据生产计划的需要,跨越到整个供应链节点企业,特别是零部件供应商,取得其它节点企业的有效合作,只有这样,核心企业的生产任务才能够得以完成。
这也是传统计划模式同供应链环境下生产计划模式最本质的区别。
生产计划是一个沟通协商的过程
传统的生产计划模式是针对单一企业内部生产活动的一种集中式决策,参与计划决策的各个部门或单元都是企业的一个组成部分,计划下达或生产调度采取行政命令;
而对于供应链管理环境下的核心企业,为它提供零部件的其它节点企业都是具有独立平等地位的法人实体,有最大化自身利益的要求。
因此,供应链管理环境下的核心企业生产计划决策需要同其它节点企业进行沟通协商,使本企业和其他节点企业的生产计划同步响应。
递阶式的计划信息反馈机制
传统的生产计划信息反馈机制是一种直线性的链状反馈机制,生产计划的反馈信息是从企业内部的一个部门直线传递到另一个部门。
而供应链管理环境下的由多个供应商、生产企业、批发商、零售商组成的负责的网络化结构,使得供应链管理环境下的信息反馈方式,不是递阶管理,也不是矩阵管理,而是网络化的管理。
计划运行的不确定性和动态性因素
随着全球市场竞争的日益激烈和卖方市场向买方市场的转变,相应地增加了企业生产计划运行的不确定性和动态性因素,这是传统计划模式与供应链计划模式所要共同面临的一个问题。
而在供应链管理下,各成员企业还要考虑与其它成员企业一起协作来共同完成供应链的生产任务,所以其生产计划要考虑更多的不确定性和动态因素,相应的也对计划的柔性和敏捷性提出了更高的要求。
三、供应链环境下核心企业生产计划模式
针对供应链环境下核心企业生产计划的特点,本文提出了供应链环境下核心企业生产计划总体模型。
即在接到客户订单后,通过供应链信息集成平台,以及生产能力和成本分析,决定是不是接收订单;
决定接受订单后开始制定生产计划。
在供应链环境下核心企业生产计划分为两个部分:
一是核心企业独有的全局的生产计划,另一个是由节点企业提供的局部的生产计划。
在该过程中生产计划的制定应该有核心企业集团构造由多个节点企业共同完成的核心企业主题计划,然后把计划分分解分配到各个节点企业中。
最后协商和协调后形成完整的协同生产计划。
1.供应链信息集成平台
供应链信息集成平台本质上是一个由内到外、内外整合的协同价值链。
供应链成员、在商业合作伙伴的关系架构下,能够根据彼此之间的互信来共享特定的企业信息,以在供应链体系内发挥各自的核心竞争力,分担整体供应链成败的共同责任并共享成果。
每一个接入供应链信息集成平台的成员只要借助于统一的交易标准即可集成在该信息集成平台下。
供应链信息集成平台,为供应链企业之间的信息交流提供共享窗口和交流渠道,同时保证供应链同步化计划的实现,实现按照客户需要订单驱动生产组织方式,降低整条供应链的库存量。
生产能力/成本分析
生产能力/成本分析主要是由核心企业和节点企业一起进行订单决策,根据订单内容、销售预测信息和产成品库存信息,以及核心企业和节点企业资源约束、生产成本等信息,决定是否接受用户的订单。
在供应链中,完成总装任务的核心企业其建成投产的资金大、周期长,以及风险、技术等因素,使得核心企业的数量是有限的,这类合作伙伴的选择是困难的。
因此,核心企业的能力扩展往往局限在核心企业内部,其能力约束表现为刚性约束。
所以,在生产能力/成本分析时,核心企业的资源约束就成为了最重要的考虑一个因素。
核心企业主生产计划
核心企业主生产计划主要是根据供应链信息集成平台中各成员企业生产能力约束,在尽量满足订单的指导原则下进行主生产计划的制定,并通过同各节点企业协调来修正供应链核心企业主生产计划,核心企业主生产计划内容包括确定产品的产量和交货期。
节点企业生产计划
各成员企业在满足协同生产计划协商结果的约束下,结合企业的具体生产情况,详细编制各自的生产作业计划,然后把相关的计划信息集成到协同生产管理信息集成平台,以实现供应链范围内的各企业计划信息共享。
5.成本核算
本模型把成本分析纳入了生产计划决策过程中,使得生产计划更能反映企业的经营日标。
传统企业资源计划系统虽然有成本计划和成本核算模块,但其作用仅仅是事前计划以及事后结算和分析,缺乏事中控制,使得计划与实际情况相互脱离,没有真正起到成本控制的作用。
四、供应链环境下核心企业生产计划策略
在供应链环境下,企业的竞争己经不是单个企业间的竞争了,而是供应链与供应链之间的竞争。
传统的MRP系统只考虑了本企业内部资源的利用问题,而对供应链中的其它节点企业关注不足,因此传统的MRP系统必须进行协调合作才能适应供应链生产计划的要求。
1.建立MRP系统群
在供应链环境下,核心企业和各个节点企业的MRP系统不再是一个封闭的系统,而应该是一个通过现代IT技术,Web技术,由供应链联系起来的、开放的MRP系统群。
由于供应链上的各个节点企业可能采用了不同公司的MRP系统,因而可以通过点对点的整合方法或者)基于中间层的整合方法将独立的MRP系统连接成相互协作的整体。
2.协调零部件供应批量,加大安全库存
对于核心企业来说,短缺的零部件将导致产品不能及时交货,面临违约的风险,而多余的零部件又会造成额外的库存成本,会在整条供应链上会造成巨大的成本,为此本文提出以下协调策略:
(1)对于短缺的零部件,要在平时加大安全库存,保证生产的顺畅进行。
(2)打价格战,对于那些力量比较强大的零部件供应商,而且该零部件又属于关键零部件,则应该适当给予该零部件供应商价格折扣或者其他的优惠方式,改变某个零部件供应商的最优送货量。
核心企业与零部件供应商为了提高供应链整体效益进行协商,各方都要以合作的态度考虑对方的利益,任何为了追求自身最优而转嫁风险的行为都是不可取的。
设定一个使供应链整体最大获益各零部件提前期
当零部件之间只有相互配合才能进行装配时,不能按时到达的零部件就成为了生产的瓶颈,而准时到达的却又成为不必要的库存。
为此,可采取以下协调策略:
(1)在开始设定提前期的时候,应该把核心企业的MRP系统和零部件供应商的MRP系统进行综合考虑,在以往统计数据的基础上,考虑零部件之间装配时的特定比例,重新编排生产计划,调整设定一个使各方都能接受、并使供应链整体能获得最大效益的各零部件提前期。
(2)核心企业必须和零部件供应商在生产过程上实现信息共享,关注零部件供应商MRP系统的运行情况,综合协调各方利益,调整各个零部件的提前期。
(3)如果某零部件的提前期波动比较大,且又属于关键零部件,那么核心企业就应该对此零部件设置比较高的安全库存,来削弱提前期波动的影响。
生产商与零部件供应商建立一致的物理清单
在核心企业的MRP系统中客户订单能否准时完成,零部件供应商的配合是关键。
如果零部件供应商对核心企业所需求的各种零部件型号没有一个清晰的了解,那么它们对核心企业的需求就无法做出快速响应。
所以,核心企业在建立自己物料清单时,应该邀请零部件供应商一起参与设计,充分听取零部件供应商的意见;
如果可能的话,核心企业也可以帮助零部件供应商建立它们物料清单来配合主生产厂商,形成长期的合作联盟,这无论对核心企业还是零部件供应商都是有利的。
笔者在对生产计划的简要概述后,对供应链环境下核心企业生产计划的特点进行了详细的分析。
在此基础之上,提出了供应链环境下核心企业生产计划的总体模型并提出了一些相应的协调策略,包括多个MRP系统集成策略、批量之间的协调策略、提前期之间的协调策略、物料清单的协调策略等多个协调策略。
参考文献:
[1]马士华,林勇,陈志祥.供应链管理[M].北京:
机械工业出版社,2001.
陈荣秋.生产计划与控制[M].武汉华中理工大学出版社,1995.
周三多,蒋俊,邹一峰.生产管理[M].南京:
南京大学出版社,1999.