汽车车身覆盖件冲压工艺文档格式.docx
《汽车车身覆盖件冲压工艺文档格式.docx》由会员分享,可在线阅读,更多相关《汽车车身覆盖件冲压工艺文档格式.docx(16页珍藏版)》请在冰豆网上搜索。
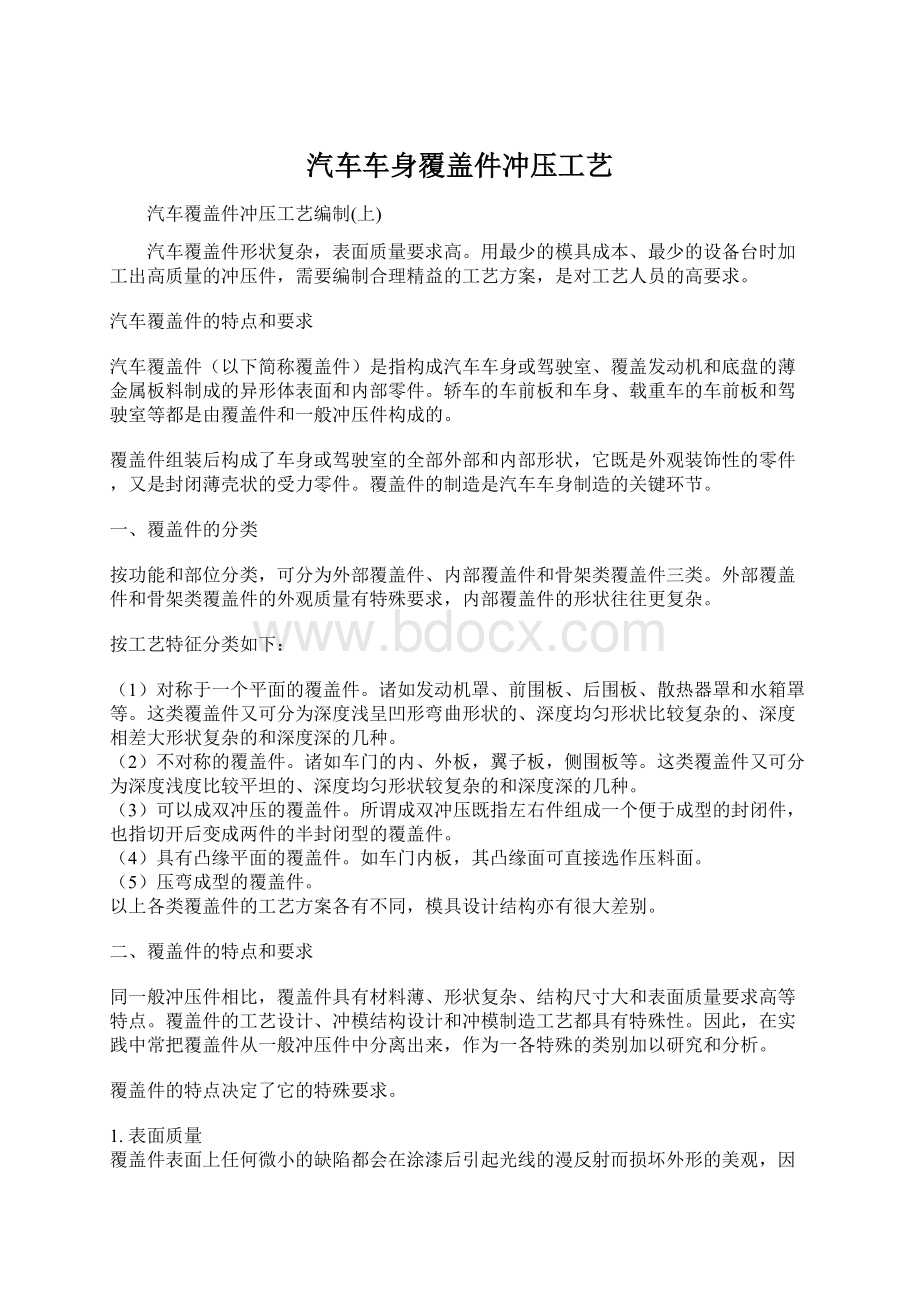
覆盖件的特点决定了它的特殊要求。
1.表面质量
覆盖件表面上任何微小的缺陷都会在涂漆后引起光线的漫反射而损坏外形的美观,因此覆盖件表面不允许有波纹、皱折、凹痕、擦伤、边缘拉痕和其他破坏表面美感的缺陷。
覆盖件上的装饰棱线和筋条要求清晰、平滑、左右对称和过渡均匀,覆盖件之间的棱线衔接应吻合流畅,不允许参差不齐。
总之覆盖件不仅要满足结构上的功能要求,更要满足表面装饰的美观要求。
2.尺寸形状
覆盖件的形状多为空间立体曲面,其形状很难在覆盖件图上完整准确地表达出来,因此覆盖件的尺寸形状常常借助主模型来描述。
主模型是覆盖件的主要制造依据,覆盖件图上标注出来的尺寸形状,其中包括立体曲面形状、各种孔的位置尺寸、形状过渡尺寸等,都应和主模型一致,图面上无法标注的尺寸要依赖主模型量取,从这个意义上看,主模型是覆盖件图必要的补充。
3.刚性
覆盖件拉延成型时,由于其塑性变形的不均匀性,往往会使某些部位刚性较差。
刚性差的覆盖件受至振动后会产生空洞声,用这样零件装车,汽车在高速行驶时就会发生振动,造成覆盖件早期破坏,因此覆盖件的刚性要求不可忽视。
检查覆盖件刚性的方法,一是敲打零件以分辨其不同部位声音的异同,另一是用手按看其是否发生松驰和鼓动现象。
4.工艺性
覆盖件的结构形状和尺寸决定该件的工艺性。
覆盖件的工艺性关键是拉延工艺性。
覆盖件一般都采用一次成型法,为了创造一个良好的拉延条件,通常将翻边展开,窗口补满,再加添上工艺补充部分,构成一个拉延件。
工艺补充是拉延件不可缺少的组成部分,它既是实现拉延的条件,又是增加变形程度获得刚性零件的必要补充。
工艺补充的多少取决于覆盖件的形状和尺寸,也和材料的的性能有关,形状复杂的深拉延件,要使用08ZF钢板。
工艺补充的多余料需要在以后工序中去除。
拉延工序以后的工艺性,仅仅是确定工序次数和安排工序顺序的问题。
工艺性好可以减少工序次数,进行必要的工序合并。
审查后续工序的工艺性要注意定位基准的一致性或定位基准的转换,前道工序为后续工序创造必要的条件,后道工序要注意和前道工序衔接好。
覆盖件模具
一、覆盖件冲模
1.拉延模
拉延模是保证制成合格覆盖件最主要的装备。
其作用是将平板状毛料经过拉延工序使之成型为立体空间工件。
拉延模有正装和倒装两种型式。
正装拉延模和凸模和压料圈在上,凹模在下,它使用双动压力机,凸模安装在内滑块上,压料圈安装在外滑块上,成型时外滑块首先下行,压料圈将毛料紧紧压在凹模面上,然后内滑块下行,凸模将毛料引伸到凹模腔内,毛料在凸模、凹模和压料圈的作用下进行大塑性变形。
倒装拉延模的凸模和压料圈在下,凹模在上,它使用单动压力机,凸模直接装在下工作台上,压料圈则使用压力机下面的顶出缸,通过顶杆获得所需的压料力。
倒装型式拉延模只有在顶出压力能够满足压料需要的情况下方可采用。
2.修边模
修边模用于将拉延件的工艺补充部分和压料凸缘的多余料切除,为翻边和整形准备条件。
在小批量生产时,可以用手工和其他简单装备代替。
修边模修边往往兼冲孔。
修边模在修边的同时,要将废料切成若干段,每段长在200~300mm之间,分割后的废料便于打包外运。
3.翻边模
翻边模是将半成品工件的一部分材料相对另一部分材料发生翻转,根据翻边的冲压方向不同,翻边模可分为垂直翻边模和水平翻边模两大类。
水平翻边(含倾斜翻边)则需要斜楔结构完成翻边成型工作。
番边模也是制成合格覆盖件的必要装备。
二、覆盖件夹具
1.焊装夹具是覆盖件总成焊装的重要装备,按照总成的内容和层次,可分为若干种类夹具,通常冠以各种总成的名称。
2.检验夹具
检验夹具是对覆盖件及其总成件进行综合性检测的主体量具,其检测内容主要是立体型面、轮廓形状和尺寸。
检测数据和检查基准书内规定的公差要求进行对照,用来判断工件是否合格。
三、模型
1.实体模型
传统的冲模加工方法是采用实体模型作为加工依据。
实体模型具有直观、采集数据可靠、加工设备要求低等优点。
因此,目前国内大多数厂家仍采用实体模型加工方法。
工艺模型通常利用主模型按冲压工序的需要,高速冲压方向,并增加工艺补充部分改制而成。
由于工艺模型的型面都取覆盖件的内表面,所以工艺模型可直接用来仿型或数控仿型加工拉延模的凸模和压料圈。
至于拉延模的凹模加工,目前有两种方法:
其一是按凸模的工艺模型反制一个凹的工艺模型,再按凹的工艺模型由计算机直接生成凹模的加工程序,这种方法正逐渐取代前一种方法。
由此可见,实体模型只需制造一个具有凸模形状的正工艺模型,即要满足模具加工的需要,工艺样架等过渡模型已不再采用。
2.数学模型
应用电子计算机建立覆盖件的数学模型,为汽车模具的计算机辅助设计与制造创造了条件,数学模型可以在计算机的屏幕上进行模拟装配、调整冲压方向,这是实体模型无法实现的。
因此,采用数学模型加工模具代表了模具工业的发展方向,它将彻底改变模具质量依靠工匠技艺的状态。
四、覆盖件模具的成套性
覆盖件具的成套性有两个含意,一个是指全车模具的成套性,另一个指某个覆盖件所需若干模具的成套性。
汽车车身由数百个冲压件构成、全车所需冲模高达一千套以上(见下表)。
全车模具的协调一致和成套性供应是保证全车质量的关键。
如果把全车模个的成套性视为一个大的系统工程,则每个覆盖件的成套模具就是一个子系统,子系统的成套协调是保证全车质量的基础。
采用计算机辅助设计和辅助制造方法,可有效地保证模具的成套性。
几种汽车产品选用模具数量
工艺设计内容
工艺设计是在模具设计制造之前的技术准备工作,通常由用户方进行,其主要内容有以下诸项:
(1)根据生产纲领确定工艺方案。
(2)根据覆盖件结构形状,分析成型可能性和确定工序数及模具品种。
(3)根据装配要求确定覆盖件的验收标准。
(4)根据工厂条件决定模具使用的压床。
(5)根据制造要求确定协调方法。
(6)提出模具设计技术条件,其中包括结构要求、材料要求等。
工艺设计内容是贯彻执行生产纲领的具体要求和体现,是生产纲领和模具设计制造之间的桥梁和纽带。
工艺设计要求方案正确、内容可靠、符合实际和实施容易,不允许有任何大的漏洞,其责任份量很重,往往是成败的关键。
成型可能性分析
覆盖件成形的可能性分析是一项艰苦细致的工作。
由于覆盖形状十分复杂,其成型可能性计算没有固定的方法。
下面仅介绍几种最基本的分析方法。
1.用基本冲压工序的计算方法进行类比分析
覆盖件的形状不论多么复杂,都可以将它分割成若干部分,然后将每个部分的成型单独和冲压的基本工序进行类比,然后找出成型最困难的部分,进行类似的工艺计算,看其是否能一次成型。
基本的冲压工序有圆筒件拉伸、凸缘圆筒件拉伸、盒形件拉伸、局部成型、弯曲成型、翻边成型、胀型等。
它们都可以作为分析覆盖件相似部位的基础,用各种不同方法进行近似估算。
由于覆盖件上的各部位是连在一起的,相互牵联和制约,故不要把变形性质不同的部分孤立地看待,要考虑不同部位的相互影响,才不会造成失误。
2.变形特点分析
覆盖件的成型工序,大都可以认为是一种平面应力状态下进行的,垂直板料方向的应力一般为零,或者数值很小,可以忽略不计。
因此板料的变形方式,基本上可以分为以下两大类。
(1)以拉伸为主的变形方式。
在以拉伸为主的变形方式下,板料的成型主要依靠板料纤维的伸长和厚度的变薄来实现的。
拉应力成分越多,数值越大,板料纤维的和厚度变薄越严重。
因此,在这种变形方式下,板料过度变薄甚至拉断,主成为变形的主要障碍。
(2)以压缩为主的变形方式。
在以压为主的变形方式下,板料的成型主要依靠板料纤维的缩短和厚度的增加来实现的。
压应力成分越多,数值越大,板料纤维的压缩和厚度增加越严重。
因此,在这种变形方式下,板料的失稳和起皱应成为变形的主要障碍。
任何覆盖件的成型,都不外是拉伸和压缩两种变形方式的组合,或以拉伸为主,或以压缩为主。
由于板料在拉伸或压缩的过程中,具有失稳起皱和变薄拉破的危险,因此工艺上必须明确,板料在一定变形方式下极限变形能力究竟有多大,该工件能否一次成型。
如果从变形区应力应变状态的特点来看,概括起来,变形的主应力状态有如下四种类型,如图1所示。
图1平面应力状态下的主应力状态图
(1)拉-拉。
变形区内两个主应力均为拉应力。
(2)拉-压。
变形区内两个主应力,一个为拉应力,另一个为压应力,但绝对值,拉应力大于压应力。
(3)压-拉。
变形区内两个主应力,一个为压应力,另一个为拉应力,但绝对值,压应力大于拉应力。
(4)压-压。
变形区内两个主应力均为压应力。
同应力状态相对应,应变状态有如下四种类型,如图2所示。
图2应变状态图
板面内两个主应变均为拉应变,厚度方向变薄严重。
板内两个主应变,一个为拉应变,另一个为压应变,但绝对值拉应变大于压应变,厚度方向变薄。
板内两个主应变,一个为压应变,另一个为拉应变,但绝对值压应变大于拉应变,厚度方向变厚。
板内两个主应变均为压应变,厚度方向变厚严重。
一般情况下,板料成型时变形区应力状态图与应变状态图的对应关系如图3所示。
图中的拉-拉与压-压主应力状态图都可能对应两种主应变状态图,其余则一一对应。
图3应力与应变状态的对应关系
由此,我们可以概括地认识到板料的一般变形规律与成型性能。
总的说来,板料能否顺利成型,首先取决于传力区的承载能力,即传力区是否有足够的抗拉强度。
其次根据变形方式,分析变形区变形的主要障碍。
在以拉伸为主的变形方式下,变形区均匀变形的程度将决定其变形程度的大小。
如果变形不均匀,或只集中某一局部变形,就会因集中应变而出现缩颈,变形不能继续进行。
对此,工艺上往往采取增加凹模圆角半径或改善润滑的方法使其变形均匀化。
在以压缩为主的变形方式下,变形区的抗失稳起皱能力将决定其变形程度的大小。
对此,工艺上采取适当增加压料力的办法,以提高压料面的质量。
降低凹模和压料圈的压料面表面粗糙度,增加摩擦等措施,可以改善变形条件。
根据上述方法,对覆盖件局部形状予以判断分析,可以粗略地掌握覆盖件的变形特点。
但不可不否认,由于形状的边界条件不同,这种判断往往是不够确切的。
因此,判断工件是否能够成型,最好的办法还是参考以前加工过的工件,用类似的方法进行判断,如果应用坐标网格应变分析法,将试验数据和工件尺寸形状对照分析,可以得出更有价值的结果。
3.成型度α值判断法
对不规则形状拉延件的成型,还可以用成型度α值进行估算和判断。
成型度:
α=(l/l0-1)×
100%
式中l0——成型前毛坯长度;
l——成型后工件长度。
在拉延件最深或认为危险的部位,取间隔50~100mm的纵向断面,计算各断面的成型度值(见图4),利用表1的数据进行成型分析和判断。
图4成型性研究
表1不规则形状、大尺寸覆盖件的成型难易判断值
表2中所给数据,α值是单轴方向的值。
当必须考虑两轴方向时,根据拉伸、压缩情况,即根据属于两向胀型还是两向压缩变形,α值多少有些变化。
一般大型拉延件是通过拉伸和胀型的复合成型来实现的,既有外部压料面材料的流入,又有凹模洞口内材料的伸长,所以必须应用α值对覆盖件成型性进行判断,同时还要考虑具体成型条件,对判断值α要作修正(见表2),进行综合性估测。
表2成型难易判断值αmax修正值
工艺方案
覆盖件的冲压工艺方案编制依据是产品的生产纲领。
工艺方案应保证产品的高质量、生产的高效率和降低成本。
1.小批量生产的覆盖件冲压工艺方案
小批量生产是指月产量小于1000件,此时的生产稳定性极差,限期生产形状改变可能性大,模具选择只要求拉延和成型工序使用冲模,模具寿命在5万件。
其他工序,如落料、修边可在通用设备上剪裁,翻边使用简易胎具,冲孔用通用冲孔模或钻床手工钻孔。
如果过多地选用冲模,虽然对保证质量有益,但对提高生产效益并无意义,且会使成本骤增。
小批量生产的拉延模,常采用锌铝合金和HT200、HT250灰口铸铁制造,也可采用焊接骨架结构作模体,表面用环氧树脂。
有些厂则常用焊接板式模,航空主机厂用铅锌模最为普遍。
小批量生产的拉延模设计原则是低费用和短周期制出。
2.中批量生产的覆盖件冲压工艺方案
当月产量大于1000件,且小于10000件(卡车)或30000件(轿车)是被视为是中批量生产。
其生产特点是比较稳定地长期生产,生产中形状改变时有发生。
模具选择除要求拉延模采用冲模外,其他工序如果影响质量和劳动量大也要相应选用冲模,模具寿命要求在5万件到30万件。
模具选择系统为1:
2.5,亦即一个覆盖件平均选择2.5套冲模。
拉延模常用HT200、HT250灰口铸铁制造,表面火焰淬火处理。
模具结构采用导板导向,机械取件,固定或气动定位毛料,壁厚中等,设计中要适当考虑合理性。
3.大批量生产的覆盖件冲压工艺方案
当月产量大于10000件(卡车)或30000件(轿车),且小于100000件时,属于大批量生产。
生产处理长期稳定状态,形状改变可能性小,工艺难易程度困难,工艺方案要为流水线提供保证,每道工序都要使用冲模,拉延、修边冲孔和翻边模同时安装在一条冲压线上,工序间的流转,50年代基本是人工送料和取件,工业化国家实现机械化和自动化,60年代以后开始进入全自动化时期。
多工位压床的出现,更加提高了生产效率和工件质量。
在冲压生产线上,一般都配有各种送料装置、取件装置、翻转装置、废料排除装置和传送带。
与早期的由压力机驱动的同步冲压生产线不同,现代的冲压生产线自动化系统,机器人实际上控制关冲压生产线。
压力机以单次行程规范工作,由自动化系统控制着生产线上各台压力机在什么时候冲压和各工序间的工件运动。
从整条生产线上传出的工件是按一定的节拍连续不断地运动,从而明显地提高了生产产量。
该系统还可以保证工件表面的高质量要求,大幅度减少压力操作人员,解决了安全及下料的难题,最大限度地提高了设备利用率。
大批量生产的冲模选择系数一般为1:
4以上,冲模结构要求功能齐全,对于容易损坏的模具,不但要求快速更换易损冲头,而且要制造备模,以使模具修复时冲压生产线照常运转。
拉延件设计
1.拉延件的冲压方向
覆盖件的拉延件设计,首要是确定冲压方向。
确定拉延冲压方向,应满足如下几方面的要求。
(1)保证拉延件凸模能够顺利进入拉延凹模,不应出现凸模接触不到的死区,所有需拉延的部位要在一次冲压中完成。
(2)拉延开始时,凸模和毛料的接触面积要大,避免点接触,接触部位应处于冲模中心,以保证成型时材料不致窜动。
(3)压料应尽量保证毛料平放,压料面各部位进料阻力应均匀。
拉延深度均匀,拉入角相等,才能有效地保证进料阻力均匀。
图5(a)中凸模两侧的拉入角心可能作到基本一致,使两侧进料阻力保持均衡。
凸模表面同时接触毛料和点要多而分散,并尽可能分布均匀,防止成型过程中毛料窜动,如图5(b)所示。
当凸模和毛料为点接触时,应适当增加接触面积,如图5(c)所示,以防止应力集中造成局部破裂。
图5冲压方向的选择
如果有反成型,且反成型有直壁部分,则冲压方向实际由反成型的位置决定。
当冲压方向和覆盖件在汽车上的坐标关系完全一致时,则覆盖件各点的坐标数值可以直接用在模具上。
当冲压方向和覆盖件在汽车上的坐标关系有改变时,则覆盖件各点的坐标数值应该进行转换计算方可用在模具上。
如果只改变一个坐标线时,且拉延方向是以垂直于覆盖件对称面的轴进行旋转来确定的,则平行于对称面的坐标是不需转换计算的。
可见,冲压方向和汽车坐标完全一致,能够带来很多方便。
2.压料面的确定
覆盖件拉延成形的压料面形状是保证拉延过程中材料下破不裂和顺利成型的首要条件,确定压料面形状应满足如下要求。
(1)有利于降低拉延深度。
平压料面夺料效果最佳(见图6),但为了降低拉延深度,常使压料面形成一定的倾斜角。
图6拉延模的压料面
1—凸模2—凹模3—压料圈
(2)压料面应保证凸模对毛料有一定程度的拉延效应。
压料圈和凸模的形状应保持一定的几何关系,使毛料在拉延过程中始终处于紧张状态,并能平稳渐次地紧帖凸模,不允许有多余的产生皱纹。
为此,必须满足下列条件(见图7,图8)。
图7压料面展开长度比凸模表面展开长度短
图8压料面形状(前围外盖板)
l>l1β>α
式中l——凸模展开长度;
l1——压料面展开长度;
α——凸模表面夹角;
β——压料面表面夹角。
还要注意有些拉延件虽然压料面展开长度比凸模短,但在拉延过程中,每一瞬间这种关系不能维持,发生压料面展开长度比凸模长的瞬间,就会形成皱纹,并最后留在拉延件上而无法消除(见图9)。
图9凸模从开始拉延到最后的过程中,
四个瞬间位置形成皱纹的情况
(3)压料面平滑光顺有利于毛料往凹模型腔内流动。
压料面上不得有局部的鼓包、凹坑和下陷。
如果压料面是覆盖件本身的凸缘上有凸起和下陷时,应增加整形工序。
压料面和冲压方向的夹角大于90º
,会增加进料阻力,也是不可取的。
平面夺料面不但有利于成型,而且加工也容易,应尽量采用。
单曲率压料面和双曲率压料面多用在拉延深度较深的拉延模。
3.工艺补充部分设计
为了给覆盖件创造一个良好的拉延条件,需要将覆盖件上的窗口填平,开口部分连接成封闭形状,有凸缘的需要平顺改造使之成为有利成型的压料面,无凸缘的需要增补压料面,这些增添的部分称为工艺补充部分。
工艺补充是拉延工艺不可缺少的部分,拉延后又需要将它们修切掉,所以工艺补充部分应尽量减少,以提高材料的利用率。
工艺补充部分除考虑拉延工艺和压料面的需要外,还要考虑修边和翻边工序的要求,修边方向应尽量采取垂直修边。
可能采用的几种修边型式如下。
图10工艺补充部分的几种况
(1)修边线在拉延件压料面上,如图10(a)所示。
此时压料面应是覆盖件的凸缘面,修边采取垂直修边。
为了在模具使用中打磨压料筋槽不致影响修边线,修边线至拉延筋的距离A一般取25mm。
(2)修边线在拉延件底面上,如图10(b)所示。
采用垂直修边,工艺补充尺寸一般取:
B=3~5mm;
C=10~20mm;
D——按保留有多于1.5根完整拉延筋形状考虑。
R凸=3~10mm,深度浅和直线部分取下限,深度深和曲线部分取上限;
R凹=8~10mm。
(3)修边线在拉延件短斜面上,如图10(c)所示。
E=B=3~5mm;
α≥5º
。
(4)修边线在拉延件长斜面上,如图10(d)所示。
垂直修边,修边线是按覆盖件翻边展开确定的,所以拉延轮廓外形不能完全平行修边线,图中F是变化的,不同情况取不同最小值,F还和拉延件在修边时的定位有关,如图11所示。
一般取:
F≥8mm(用拉延槛定位);
F=3~5mm(用侧壁定位);
β=6º
~12º
(5)修边线在拉延件侧壁上,如图10(e)所示。
采用水平修边或倾斜修边,修边线至凹模圆角半径的距离G是一个变量,它决定水平修边凹模镶块的强度。
图12所示为水平修边和倾斜修边示意图。
修边凹模镶块的刃口宽度b一般取12mm,α角取30º
,b局部最小尺寸不小于8mm,α最小为15º
图11拉延件在修边时的定位
图12水平修边和倾斜修边示意图
4.工艺孔及工艺切口
覆盖件需要局部反拉延时,如果采用加工该部圆角和使侧壁成斜度的办法,仍然拉不出所需深度时,往往采取冲工艺切口的办法来改善反拉延的条件,使反拉延变形区从内部工艺补充部分得到补充材料。
工艺孔或工艺切口必须在修边线之外的多余材料上,修边时不应影响工件的形状。
(1)工艺孔。
工艺孔在拉延前预先冲制,一般和落料工序合并,采取落料冲孔复合模。
工艺孔的数量、尺寸大小和位置需要由拉延模试冲确定,见图1-13。
图13预冲工艺孔拉延车门外板
(2)工艺切口。
工艺切口一般在拉延过程中切出,废料不分离,和拉延件一起退出模具。
工艺切口的最佳冲制时间是在反拉延成型到最深,即将产生破裂的时刻,这样可以充分利用材料的塑性,使反拉延成型最需要材料补充的时候能够获得所需要的材料(见图1-14)。
工艺切口也要由试冲决定。
图14窗口反拉延、切两个工艺孔
5.拉延筋和拉延槛
覆盖件拉延成型时,在压料面上敷设拉延筋或拉延槛,对改变阻力,调整进料速度使之均匀化和防止起皱具有明显的效果。
归纳起来敷设拉延筋的主要作用有如下几点。
(1)增加局部区域的进料阻力,使整个拉延件进料速度达到平衡状态。
(2)加大拉延成型的内应力数值,提高覆盖件的刚性。
(3)加大径向拉应力,减少切向压应力;
延缓或防止起皱。
拉延筋和拉延槛的形状见图1-15。
拉延筋的断面形状为半圆形,一般取筋半径R=12~18mm,筋高h=5~7mm(钢件)或3~5mm(铝合金件)。
拉延筋的凹槽一般不和工件吻合,通过修整凹槽的宽度来改变进料阻力。
拉延槛的阻力更大,它多用在深度浅的拉延件上。
图15拉延筋和拉延槛
a拉延筋;
b拉延槛
拉延筋和拉延槛的敷设原则如下。
(1)拉延件有圆角和直线部分,在直线部分敷设拉延筋,使进料速度达到平衡。
(2)拉延件有直线部分,在深度浅的直线部分敷设拉延筋,深度深的直线部分不设拉延筋。
(3)浅拉延件,圆角和直线部分均敷设拉延筋,但圆角部分只敷设一条筋,直线部分敷设1~3条筋。
当有多条拉延筋时,注意使外圈拉延筋“松”些,内圈拉延筋“紧些”,改变拉延筋高度可达到此目的。
(4)拉延件轮廓呈凸凹曲线形状,在凸曲线部分设较宽