我国的棉花加工工艺流程Word文档下载推荐.docx
《我国的棉花加工工艺流程Word文档下载推荐.docx》由会员分享,可在线阅读,更多相关《我国的棉花加工工艺流程Word文档下载推荐.docx(11页珍藏版)》请在冰豆网上搜索。
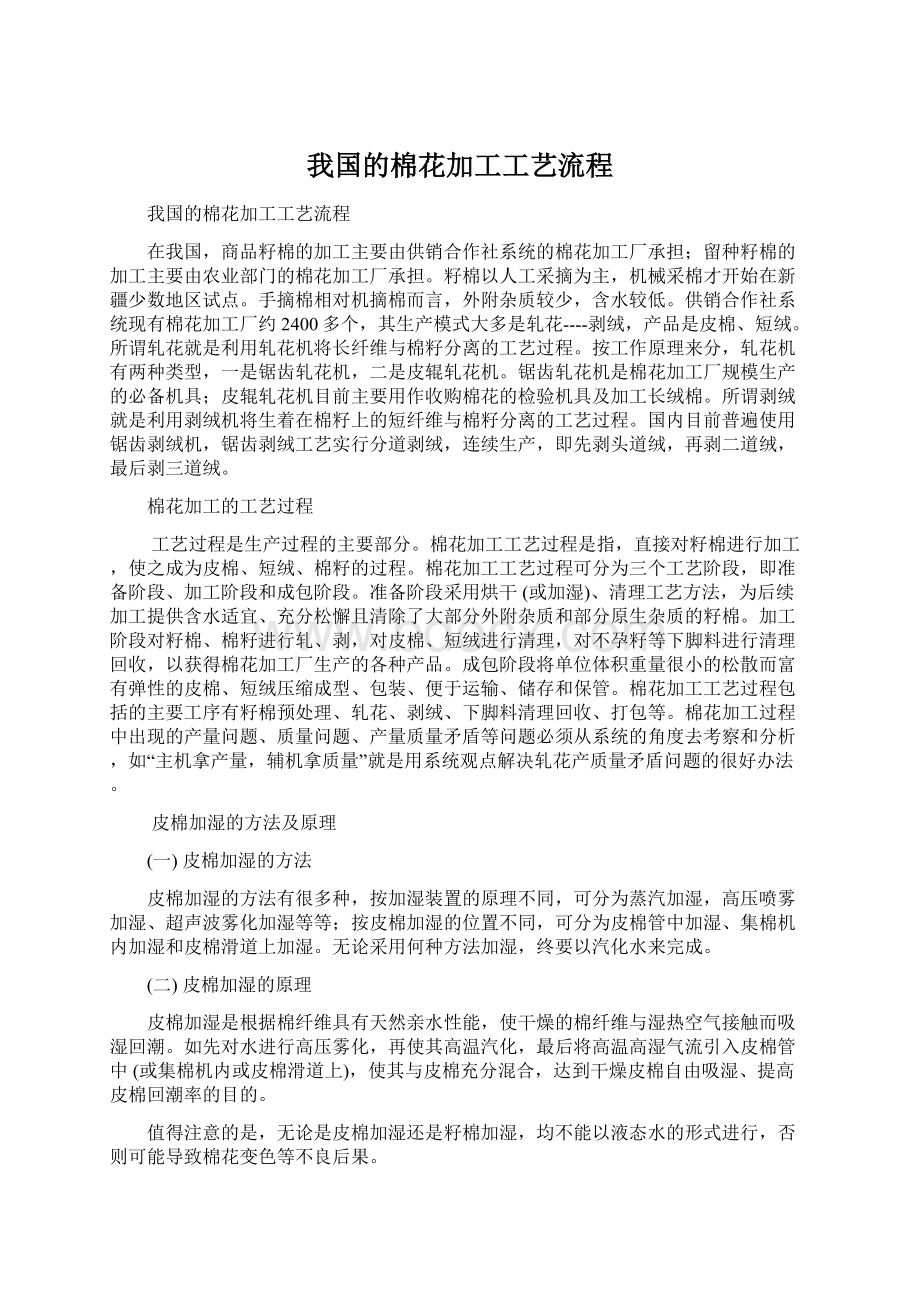
按皮棉加湿的位置不同,可分为皮棉管中加湿、集棉机内加湿和皮棉滑道上加湿。
无论采用何种方法加湿,终要以汽化水来完成。
(二)皮棉加湿的原理
皮棉加湿是根据棉纤维具有天然亲水性能,使干燥的棉纤维与湿热空气接触而吸湿回潮。
如先对水进行高压雾化,再使其高温汽化,最后将高温高湿气流引入皮棉管中(或集棉机内或皮棉滑道上),使其与皮棉充分混合,达到干燥皮棉自由吸湿、提高皮棉回潮率的目的。
值得注意的是,无论是皮棉加湿还是籽棉加湿,均不能以液态水的形式进行,否则可能导致棉花变色等不良后果。
冲击式籽棉清理机
1、结构及作用 冲击式籽棉清理机由喂花清软特杂质部分、清花部分、回收部分组成。
如图19-1所示。
(1)喂花清软特杂质部分主要由喂花辊、软特杂回收辊等组成。
喂花辊直径为380mm,是由表面安装高为50mm的刺钉制成的滚筒,转速为35r/min;
软特杂回收辊直径为150mm,其表面也安装有50mm高的刺钉,转速为600r/min。
该部分的作用是:
将籽棉均匀、疏松地喂入清花部分,并通过软特杂回收辊清除籽棉中的软特杂质。
(2)清花部分主要由五个相同的清花刺辊和五个相同的清花锯片滚筒组成。
清花刺辊包括刺钉在内,其直径为291mm,转速为600r/min,两相邻清花刺辊的刺钉最小间距为14mm。
清花刺辊的中心在两锯片滚筒中心连线的垂直平分线上,清花刺辊刺钉尖端与锯片齿尖最小间距为9mm。
清花锯片滚筒是由若干张锯片和隔圈间隔装在一起而成的,外径为300mm,锯片齿形为直角,齿矩为12.5mm,转速为420r/min,片距为15.8mm,两锯片滚筒齿尖最小间距为5mm。
利用清花刺辊和清花锯片滚筒对籽棉的冲击、撕拉等方式,使粘附在籽棉上的杂质受到抖动而被分离,并顺着锯片间隙掉落在排杂螺旋后而被清除。
(3)回收部分主要由上回收辊、中回收辊、下回收辊、可调格条栅、固定钢丝刷、排杂调节板等组成。
上回收辊是由4只叶片制成的滚筒,直径为216mm;
中回收辊是由8只叶片制成的滚筒,直径为200mm;
下回收辊又称U形齿条回收辊,其表面固装着U形齿条,外径为400mm,转速为170r/min;
可调格条栅由细钢筋连结定板、动板构成;
排杂调节板是指靠近U形齿条辊的可调节的弧形动板。
U形齿条辊齿尖与可调格条栅间距为10mm,与排杂调节板间距为5mm。
钢丝刷与U形齿条间隙0~5mm,U形齿条辊与中回收辊间距为5mm,外弧板、中间弧板与中回收辊间距为105mm,中间弧板、边缘弧板与上回收辊间距为12mm,中、上两回收辊最小间距为17mm。
利用上、中、下回收辊提取清花部分排落而夹在杂质中的单粒籽棉、小花头和僵瓣棉,并能根据不同级别的籽棉调整格条栅,使之达到良好的清杂回收效果。
2、工作原理冲击式籽棉清理机主要是利用清花锯片滚筒与清花刺辊两者的表面线速差及锯齿和刺钉对籽棉的冲击、撕拉抖动等作用来清除杂质的。
具体过程如下:
首先,籽棉经喂花辊由直径较小、但转速较高的软特杂回收辊对其中的布条、绳头等软特杂质给以缠绕、然后进入清理部分;
紧接着被第一个清花刺辊打向下面的第一个清花锯片滚筒上,并沿着清花刺辊和锯片滚筒之间的工作通道,被其余四对清花刺辊和锯片滚筒清理,循序向上前进;
又因清花刺辊和锯片滚筒存在线速度差,使籽棉在机内受到冲击、撕拉而被松解。
粘附在籽棉上的杂质由于受到抖动而被分离,并顺着锯片间隙下落入底板;
被清理的籽棉则由上部出棉口进入下道工序。
清理过程中随杂质排落的部分籽棉沿底板滑落到钢丝刷上,被U形齿条回收辊钩住带走,并经中、上两回收辊重新拨回籽棉工作通道再次进行清理。
而叶屑、不孕籽等杂质则因不易被锯齿钩住,在钢丝刷的弹动和锯筒离心力以及格条栅的摩擦撞击作用下,落入排杂螺旋并被排出机外。
3、影响清杂效果的因素
(1)清花刺辊与清花锯片滚筒的表面线速在其他条件一定的情况下,清花刺辊与锯片滚筒表面线速越高,籽棉受到的冲击作用越强烈,籽棉中的杂质越易被抖落,清杂效果越好。
但两者表面线速过高就易损伤纤维和棉籽,产生新杂质。
一般清花刺辊刺钉的线速不得高于11m/s,而锯片滚筒的线速度不得高于8m/s。
清花刺辊与锯片滚筒两者表面线速比值也影响清杂效果的高低。
二者线速比值越大,籽棉所受到的撕拉作用越强烈,籽棉中的杂质越易被清除,清杂效果越好。
通常,清花刺辊钉与锯片滚筒锯齿的线速比不应高于1∶0.6,否则,纤维和棉籽易受损伤,排落单粒籽棉量也增多,衣分亏损增大。
(2)清花锯片滚筒的锯片片距清花锯片滚筒不仅对籽棉进行冲击,同时,还对籽棉及其中的杂物进行筛选。
这是因为锯片的表面线速低于刺钉的表面线速,在刺钉打击籽棉使其向前运动时,锯齿对刺钉打击的籽棉产生摩擦阻滞作用,从而使籽棉得到撕拉。
又由于锯片滚筒片距比籽棉瓣的腰径小,比杂质的直径大,因此,锯齿对籽棉及其中的杂质起到一定筛选作用。
一般锯片片距越大,杂质越易从锯片中间附落,清杂效果越好。
但同时,也会排落单粒籽棉,加重回收部分的负担,甚至使单粒籽棉随杂质一同排出机外,造成衣分亏损。
反之,片距小,较大的杂质就不易排落,甚至随籽棉一同进入下道工序,因而清杂效果较差。
锯片片距一般不能大于籽棉瓣的腰径或单粒籽棉的直径,即通常小于20mm。
(3)相邻两清花锯片滚筒齿尖间距相邻两清花锯片滚筒齿尖间距大,杂质易从其中落下,排杂效果好,但同时也会排落部分单粒籽棉。
反之,其间距小,不仅有些杂质难以排落,甚至造成两锯齿同时作用在棉籽上,使棉籽破碎,降低皮棉质量,严重者还会发生锯齿相碰等机械事故。
因此,相邻两清花锯片滚筒齿尖间距最小为5mm,最大一般不超过18mm。
(4)清花刺辊刺钉与清花锯片滚筒锯齿尖间距由于刺钉与锯齿对籽棉共同作用,使籽棉中的杂质才得以清除。
所以清花刺辊的刺钉与清花锯片滚筒的锯齿之间间距大,则刺钉对籽棉的打击作用低。
与此同时,也减弱了锯齿对籽棉的阻滞作用,使清杂效果变差;
反之,如果此间距小,刺钉与锯齿对籽棉的撕拉作用强烈,清杂效果好,但同时也会出现排落单粒籽棉增多现象,甚至造成刺钉与锯齿同时打击棉籽,降低皮棉质量。
因此,此间距必须大于棉籽腰径,通常刺钉与锯齿的最小间距为9mm。
(5)下回收辊锯齿与钢丝刷、格条栅及排杂调节板的间距下回收辊锯齿与钢丝刷、格条栅及排杂板的间距越大,杂质越不易被下回收辊锯齿钩取,清杂效果越好。
但同时杂质中夹带的单粒籽棉和小花头也越多,造成衣分亏损;
反之,如此间距过小,则杂质易被锯齿钩取,使之又重新带入回收的籽棉中,因而使清杂效果降低。
因此,生产过程中,应使排落杂质中夹带的单粒籽棉和小花头尽可能的少。
通常锯齿与可调格条栅的间距为10mm,锯齿与钢丝刷的间距为0~5mm,锯齿与可调排杂板的间距为5mm。
(6)籽棉回潮率及含杂量和台时清理籽棉量对于回潮率低的籽棉,由于籽棉和杂质间的粘附力小,籽棉纤维蓬松而有弹性,杂质易被清除,清杂效果好;
反之,籽棉纤维回潮率高,杂质与籽棉纤维粘附力大,杂质不易被清除,清杂效果差。
对于含杂量高的籽棉,清杂效果好;
反之,籽棉含杂少,清杂效果差。
这是因为含杂多的籽棉,其外附杂质多,易被清除,而含杂少的籽棉,不孕籽等天然杂质占的比重较大,不易被清除。
台时处理籽棉量多,清花锯齿滚筒和清花刺辊的负荷重,籽棉不易被充分开松,清杂效果差些,如台时处理籽棉量稍少些,则籽棉能被刺钉和锯齿充分开松和撕拉,于是籽棉中的杂质能充分排出,清杂效果好些。
棉花加工传统工艺
棉花加工传统工艺指的是主机----轧花机采用5571型或其改进机型(本书统称80型)的棉花加工生产线工艺流程。
棉花加工传统工艺不够完善,是一个厂一个样或一条生产线一个样。
较有代表性的棉花加工传统工艺流程。
存放在露天货场或仓库的籽棉采用气力输送方式运送到生产车间。
在气力输送管道上,设有1~2个重杂物沉积器,以清除籽棉中的重杂物。
外吸棉的控制是通过人工调节设置在回风管上的风门启闭来实现。
棉籽分离器使籽棉与含尘空气分离,随后籽棉被卸入刺钉滚筒式的籽棉清理机,而含尘空气被导入空气管,经风机再入除尘设备净化处理。
籽棉被清理、膨松后,由三管配棉装置将其分送给每台锯齿轧花机。
经锯齿轧花机加工,长纤维与籽棉分离。
随后,皮棉采用共同集棉方式送往总集棉机,压成片状后经皮棉滑道送入打包机成包;
棉籽由螺旋输送装置送往剥绒车间加工;
轧花过程中排落的下脚料(主要是不孕籽等有效纤维)由气力输送装置送往清理回收车间加工。
凡供榨油用的棉籽都要进行剥绒,且实行分道剥绒,供留种用的棉籽可减少剥绒次数或不剥绒。
剥绒前,棉籽先要进行清理,然后棉籽由螺旋输送装置送往头道剥绒机加工。
经过头道剥绒机加工,较长的短纤维与棉籽分离。
随后,棉籽又由螺旋输送装置送往二道剥绒机加工。
经过二道剥绒机加工,次长的短纤维与棉籽分离。
接着,棉籽又由螺旋输送装置送往三道剥绒机加工。
经过三道剥绒机加工,大部分剩余短纤维与棉籽分离。
剥得的各道短绒由各道的共同集绒装置分别送往各自的总集绒机,压成片状后送入短绒清理机清理,之后分类成包;
剥绒过程中排落的下脚料(主要是落绒等)由输送装置送往清理回收车间加工;
剥过三道的光棉籽由输送装置送往仓库装袋。
棉花加工传统工艺生产线的加工量是以生产线上80型锯齿轧花机台数来表示的,有一台型、两台型、三台型、四台型4种类型的加工生产线。
80型锯齿轧花机台时皮棉产量约为350~500kg,若加工时间按120天,每天按20小时生产,则一台的年加工能力约为920吨皮棉;
两台的年加工能力约为1840吨皮棉,其它台型依次类推。
MQP-400型皮棉清理机
一、结构与作用
MQP-400型皮棉清理机主要由集棉、给棉、清棉和刷棉四大部分组成。
1.集棉部分
主要由四通阀、变径管、直角管、集棉尘笼,前、后剥棉罗拉等机件组成。
(1)四通阀在具有四条通道的空腔中心,装有一可绕中心轴转动的叶片,叶片位置的变化,可通过阀体外侧的摇臂手柄来实现。
向前拨动,皮棉进入清理机清理,向后拨动,关闭皮棉进入清理机的通道,使皮棉直接进入与总集棉机相接的皮棉道。
因此,四通阀也是皮棉清理或不清理的控制阀。
通过拨动其手柄,即可实现调整皮棉是否进行清理的目的。
(2)变径管和直角管变径管由白铁皮制成,位于四通阀的上端,与四通阀和直角管相连接,上大下小,截面形状为矩形。
其目的是利用管道的扩散作用,降低皮棉的输送风速,减少阻力,有利收集皮棉。
直角管也是用白铁皮制成,与变径管和集棉尘笼相连接,主要用于改变皮棉的输送方向。
(3)集棉尘笼位于清理机上部,是由几个圆环和辐条与尘笼轴焊接,以形成尘笼骨架;
再在骨架表面蒙上冲孔铁皮,形成圆筒。
尘笼直径为610mm,长1980mm。
传动轴左端伸出机外,装有一个51齿的链轮,其线速低于剥棉罗拉线速。
集棉尘笼的作用主要是收集松散皮棉,实现含尘气流和棉纤维的分离。
同时还可通过改变尘笼轴的转速来适应轧花生产率的变化。
(4)剥棉罗拉位于集棉尘笼的底部,有前、后两只,其直径为154mm。
用45号钢管表面加工成一定形状的沟槽制成的齿形圆辊,两端焊有轴头,转速为94r/min。
前剥棉罗拉通过旋转对吸附在尘笼网面上的皮棉进行压实,同时与后剥棉罗拉配合形成喂棉对辊。
将皮棉喂入下部皮棉清理机给棉部分,后剥棉罗拉主要起剥落尘笼表面棉胎的作用。
将松散的皮棉与气流分离,并将松散的皮棉压成棉胎送往给棉部分。
2、给棉部分主要由牵伸罗拉、牵伸光辊、给棉罗拉、给棉板等机件组成。
(1)牵伸罗拉和牵伸光辊牵伸罗拉和牵伸光辊简称为牵伸对辊。
对辊位于剥棉罗拉的下方,给棉罗拉和给棉板的上方,后面为牵伸罗拉,前面为牵伸光辊。
牵伸罗拉和牵伸光辊的直径为114mm,转速为151r/min,两辊间隙为6mm。
由于牵伸罗拉和牵伸光辊的转速远高于剥棉罗拉的转速,当皮棉通过该牵伸对辊时,棉层将变得更薄。
(2)给棉罗拉和给棉板给棉罗拉即齿形辊,直径与牵伸罗拉相同,而转速较高,一般为161r/min。
两端轴承座装有弹簧,使给棉罗拉受到68kg弹簧压力的作用,紧紧靠向给棉板。
给棉板工作曲率半径逐减少,为增强变形的能力,中间设有支承点。
给棉罗拉与给棉板配合,在给棉板尖端向上5mm处形成0.3mm的狭小间隙,使给棉罗拉和给棉板对皮棉具有握持分解疏理和进一步清杂的作用;
同时具有喂棉的作用。
通过牵伸罗拉、牵伸光辊和给棉罗拉与给棉板的配合,为清棉部分提供薄而均匀的棉胎。
3.清棉部分主要由有齿条刺辊、除尘棒、刺辊护罩及排杂箱等机件组成。
(1)齿条刺辊位于给棉部分的下部,毛刷滚筒的前端。
刺辊是由直径为400mm,齿条呈螺旋状嵌压入辊筒表面的槽内而成的,刺辊长2008mm,槽宽1.075mm,深1.525mm,螺距为3.175mm,齿条刺辊转速为1214r/min,其作用是利用齿条对皮棉进行梳理清杂。
(2)除尘棒共有五根,均匀地分布在齿条刺辊的周围,两端用螺丝固定在机架上。
五根除尘棒刀刃与刺辊间距均为1.6mm,尘棒根部除第一根与刺辊间隙为1.6mm,其余四根的间隙均为4.3mm,目的是增强纤维的嵌入,防止优棉外出。
除尘棒的作用是对暴露在齿条刺辊表面,且随刺辊一起运动的杂质产生冲击作用,使其与纤维分离。
(3)刺辊护罩位于齿条刺辊的外围,呈圆弧形,可上下调整,其弧面与刺辊的间隙为2~6mm。
刺辊护罩既防止杂质带入皮棉,起挡杂板的作用;
同时还可防止落棉,对皮棉起托附作用。
(4)排杂箱位于齿条刺辊下方,与吸杂管相连接,清理出的杂质落于排杂箱,由吸杂管吸进清理回收设备。
通过齿条刺辊与除尘棒等机件的配合,对皮棉进行充分梳理清杂,改善皮棉的外观形态,并清出排落的杂质。
4.刷棉部分主要由毛刷滚筒、毛刷护罩,顺棉板、补风调节板及阻风板等机件组成。
(1)毛刷滚筒由6只铝质法兰,固装在一根直径为60mm的轴上,外包镀锌铁皮,并装有28根毛刷条组成。
毛刷条是用专用压板压上的,毛刷滚筒直径为450mm,转速为1606r/min。
铝法兰是用锁紧套固定的。
毛刷与锯齿的接触量为零,它不同于轧花机毛刷伸入到锯齿根部,是因为齿条绕刺辊螺旋缠绕,运行起来就像一个摆动的锯条切割毛刷,毛刷损坏严重。
毛刷滚筒的作用是通过其高速旋转产生高速气流,将刺辊上的皮棉吹刷下来,关入皮棉道。
(2)毛刷护罩它是罩在毛刷滚筒下面的弧板,护罩壳后下端装有补风调节板,以使毛刷得到适量的空气补充。
护罩壳后端与皮棉道相连,前接顺棉板,与下方阻风板组成皮棉通道。
毛刷护罩的作用一是保护毛刷滚筒,二是它与毛刷滚筒表面形成风道,以引导气流通过刷棉点,有利于刷棉。
(3)补风调节板位于毛刷滚筒后方,与毛刷护罩下壳相连。
它与阻风板间有一定间隙,约24mm。
适当调整此间隙,可以得到适量的空气补充给毛刷,使之增加刷棉效果。
(4)阻风板又称后挡风板,位于毛刷滚筒后部与皮棉道相接。
其端部与毛刷滚筒的间隙以不与毛刷条相碰为准,一般为3mm。
阻风板的作用是切断气流,防止回棉,使棉纤维顺利进入皮棉道。
(5)顺棉板位于毛刷滚筒的前端,刷棉点的上方。
它与齿条刺辊的间隙为3mm,以不碰刺辊为好。
其作用是使毛刷吹刷下来的皮棉顺利进入皮棉道,起导流板的作用,同时减少此处风量补入影响刷棉,起挡风板的作用。
该部分的作用是通过毛刷滚筒的作用,将齿条刺辊上的棉纤维吹刷下来,并顺利送入皮棉道。
二、工作原理及过程
皮棉清理机是利用高速旋转的齿条刺辊对给棉罗拉与给棉板夹持的棉纤维进行钩拉分解梳理,并使杂质产生的离心力大于杂质与纤维的粘结力,以及通过除尘棒对杂质的冲击刮剥等作用,将杂质从棉纤维中分离,并排出机外。
皮棉在轧花机毛刷风力和皮棉清理机引风机的吹吸作用下,通过四通阀、变径管、直角管进入集棉尘笼,并被吸附在尘笼网表面上。
含尘气流从尘笼两侧进入分配风管,经风机排入除尘部分。
随着尘笼的旋转,尘笼表面的松散棉纤维被前、后剥棉罗拉压实并剥落,并将其喂给牵伸罗拉和牵伸光辊。
由于牵伸罗拉和牵伸光辊转速较高,棉层被牵伸变薄,并喂给棉罗拉和给棉板。
在给棉罗拉和给棉板的共同作用下,棉层变得更薄,并被夹持在两者之间,同时喂给齿条刺辊。
刺辊对皮棉进行充分的钩拉和分解梳理。
被钩持的棉纤随清棉刺辊作高速旋转运动,当与毛刷滚筒相遇时,被毛刷刷入皮棉道,送往集棉机进行打包。
由于不孕籽等杂质的比重较大,在随齿条刺辊高速运动的过程中,因离心力的作用而使其向外移至刺辊表面;
并在其未遇毛刷滚筒之前,由五根除尘棒冲击排除,待落入排杂箱后,被吸杂风机吸出机外。
三、影响清杂效果的主要因素
1、皮棉回潮率的高低皮棉纤维回潮率高,棉纤维的弹性差,不蓬松,一经打击就易变形,使分疏作用降低,影响清杂效果,同时还易造成机械堵塞。
若皮棉纤维回潮率低,虽然纤维蓬松,分疏作用好,但由于纤维的强度相对减弱,易造成棉纤维的断裂和损伤。
皮棉纤维回潮率一般在6.38%~9.89%为宜。
2.清理棉层的厚薄清理棉层的厚薄与生产率的高低基本是一致的。
通常生产率高时,清理棉层厚,锯齿钩取的纤维数量多,杂质易包裹在纤维中而不易清除。
反之,生产率低时,清理的棉层薄,锯齿钩取的纤维数量少,分疏作用好,清杂效果也好。
因此,轧花机产量不易过高。
否则,皮棉清理机清杂效果较差,并且易堵塞。
3.齿条刺辊与给棉罗拉的表面线速比齿条刺辊与给棉罗拉的表面线速比简称梳刷比。
梳刷比越高,锯齿钩取纤维数量越少,锯齿对纤维的分梳作用越好,清杂效果好。
反之,梳刷比越小,锯齿钩取的纤维数量多,杂质不易暴露,而且锯齿对皮棉纤维分疏作用差,清杂效率低。
如为增加清杂效果,单纯提高梳刷比,易损伤棉纤维强度,甚至轧断纤维,同时机械使用寿命也受到影响。
兼顾各方面的效益,齿条刺辊与给棉罗拉表面线速比一般控制在20~29之间,最高不超过30。
以梳刷比为27∶1为例,就是说给棉罗拉每给入1mm的棉层,将在刺辊表面均匀分布27mm长,使杂质充分暴露,有利清杂。
4.给棉罗拉的压力及其与给棉板的间隙给棉罗拉的压力大,且给棉罗拉与给棉板间隙小,则给棉罗拉与给棉板对皮棉纤维的夹持作用好,当锯齿钩拉皮棉纤维时,皮棉纤维能得到充分的分解梳理。
但压力过大,间隙过小,当清理皮棉量突然增大时,皮棉在此易受阻,使之不能顺利通过,造成此处堵塞,并造成机件损坏。
反之,给棉罗拉压力小,且给棉罗拉与给棉板的间隙大,则给棉罗拉与给棉板对皮棉纤维的夹持作用差,锯齿钩拉纤维会造成片状或块状钩取现象,使粘附在纤维中的杂质难以清除,碰到除尘棒时,易排落纤维,造成衣分亏损。
一般给棉罗拉的压力为68kg,给棉罗拉与给棉板的间隙为0.3mm。
5.除尘棒的数量、角度及安装位置除尘棒的数量多,纤维受到冲击次数多,杂质易排除,但也易排落纤维,造成衣分亏损。
除尘棒数量应根据具体情况适当取舍,一般设5~6根除尘棒为宜。
除尘棒的角度通常指除尘棒的工作面与齿辊在该点切线的夹角。
该角度越小,杂质在除尘棒的冲击下越易排出。
反之,则不易排出。
因此,在制作和安装除尘棒时,应注意该角度值的大小。
除尘棒的安装位置是指除尘棒刀口与刺辊锯齿的间距以及除尘棒距给棉板的距离。
除尘棒与锯齿的间距越小,离给棉板越远,杂质在离心力的作用下越易被排除。
但也易排落纤维造成衣分亏损增加。
反之,虽不易排落纤维,但排杂效果差。
因此,除尘棒的安装位置必须适当控制。
一方面要考虑除尘棒的数量,另一方面还要考虑除尘棒的刚度、直度和刺辊的圆柱度。
一般除尘棒刀刃口与锯齿之间距为1.6mm最佳。
6.齿条刺辊的锯齿完好率皮棉清理机主要是依靠齿条刺辊表面的锯齿对纤维产生钩拉疏理作用来清杂质。
刺辊表面锯齿完好无损,能产生较强的钩拉疏梳理作用,清杂效果好。
若锯齿损伤较多,则钩拉梳理作用降低,不仅清杂效果差,而且易排落纤维,造成衣分亏损。
因此,在生产过程中,应加强维修工作,发现倒齿、歪齿,要及时校正,以保证皮棉清理机的正常工作状态。
除此之外,影响清杂效果的因素还有锯齿与给棉板、给棉罗拉的间隙等,在生产过程中应注意检查。
发现不合标准的间隙或锯齿,要及时调整和维修,以确保各部件的完好及各间隙的正确性,使其符合使用要求,以提高清杂效果。
棉花加工新工艺
棉花加工新工艺指的是主机----轧花机采用MY-121、MY100-16、6MY120A-17、MY80、6MY88-17(本书称新型锯齿轧花机)机型的棉花加工生产线工艺流程。
棉花加工新工艺是在棉花加工传统工艺的基础上,吸收了国外先进棉花加工工艺中的自动化控制、籽棉烘干、皮棉清理等装置,并结合我国棉花生产、收购的特点而制定。
新工艺与传统工艺相比,籽棉预处理和轧花部分差异较大,剥绒部分相差无几。
货场或仓库的籽棉采用气力输送方式运送到车间。
在安装重杂物沉积器之前的输送管道上还安置了通大气阀,以实现外吸棉的自动控制。
当籽棉含水较高不适合轧花工艺要求时,籽棉经外吸棉分离器、籽棉自动控制箱进入烘干系统的热空气管道内,并由热空气吹送至烘干机烘干,再由内吸棉分离器卸入高效清花机清理;
当籽棉含水适宜时,通过调整使籽棉直接进入内吸棉分离器,再由内吸棉分离器卸入高效清花机清理。
与籽棉分离之后的含尘空气经回风管导入除尘设备净化处理,再排入大气。
籽棉清理、膨松后,采用正压配棉装置或螺旋配棉装置等配送给大型锯齿轧花机。
经锯齿轧花机加工后,纤维与棉籽分离。
可根据皮棉的质量情况确定皮棉是否进行清理,当皮棉质量符合要求时,通过调整皮棉清理机(简称皮清机)的四通阀,使皮棉不经皮清机直接由共同集棉装置送往打包机成包;
一般情况下,皮棉应送皮清机清理。
籽棉量的自动控制是通过设备电机间的连锁和储棉箱(或配棉箱)上设置的微动开关的连锁连动实现的。
当正压配棉箱内的籽棉达到一定高度时,其上部的微动开关被触动,从而控制高效清花机下部的内储棉箱上的喂料电机停止工作,同时使籽棉自动控制箱上的直流喂料电机也停止喂料;
当籽棉自动控制箱内的籽棉达到一定高度时,其上部的微动开关被触动,使通大气阀通空,停止外吸棉。
不选用烘干工艺时,内储棉箱上的喂料电机直