某工程TBM施工组织设计Word下载.docx
《某工程TBM施工组织设计Word下载.docx》由会员分享,可在线阅读,更多相关《某工程TBM施工组织设计Word下载.docx(73页珍藏版)》请在冰豆网上搜索。
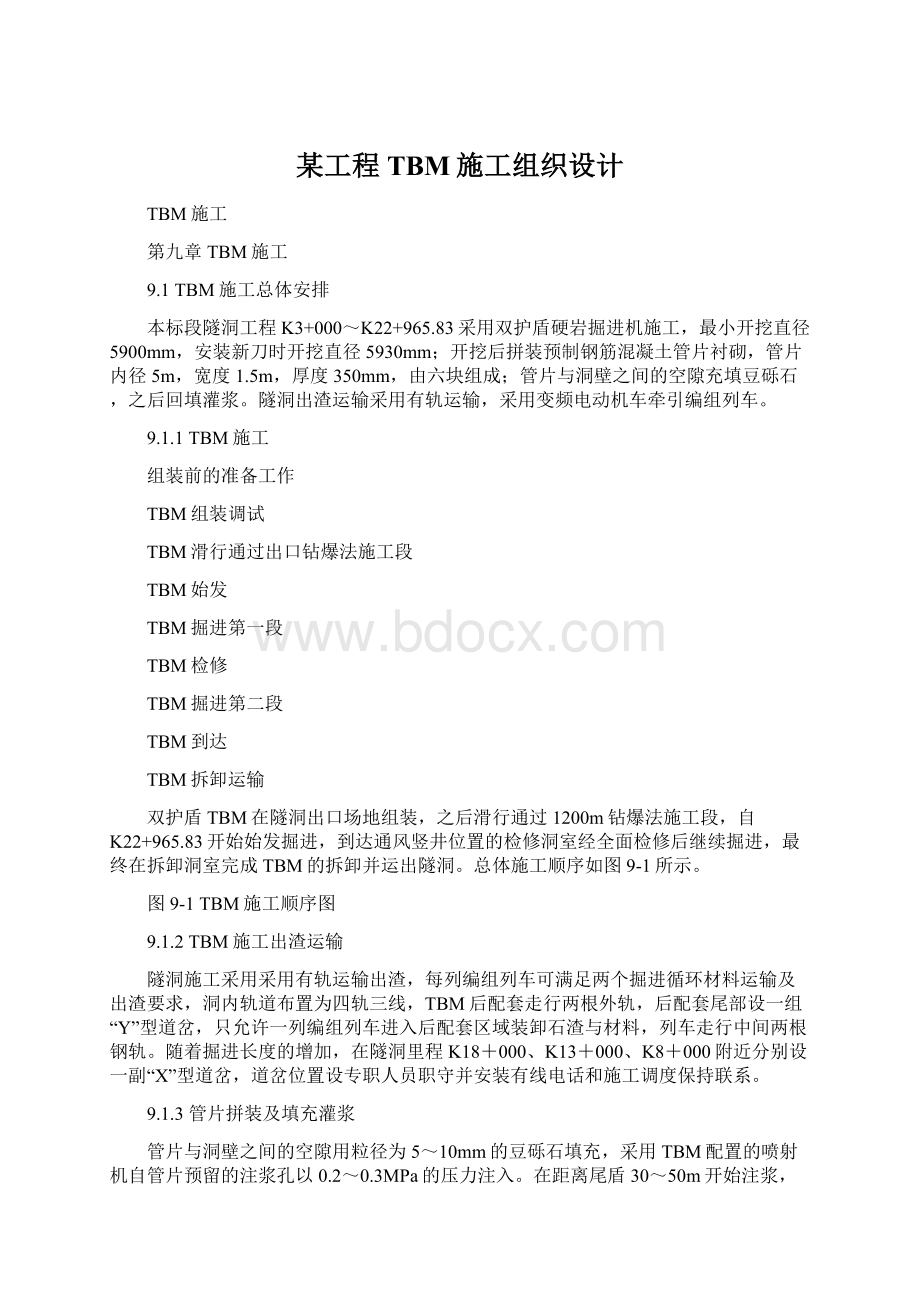
在隧洞出口建立变频恒压给水系统,分别为洞内外施工及生活给水;
施工过程中的排水主要依靠自流;
在洞内出现大流量的涌水时在主机部位以水泵抽排,并后配套尾部适当位置以砂袋设置围堰,防止水倒灌;
同时沿懂壁铺设一路DN200mm排水管,以加强排水效果。
隧洞的污水排入洞外处理池,经沉淀处理后排入宝库河。
通风:
采用压入式通风,在隧洞出口安装轴流风机,经软风管向工作面通风;
TBM掘进通过通风竖井后,将风机安装在通风竖井后,采用风机压入与竖井抽排相结合的方式通风。
9.2TBM现场组装、调试
在隧洞出口场地组织TBM组装调试,主机与后配套分别在两个场地同时进行。
由承包商和TBM制造商共同快速、安全地完成组装调试工作。
9.2.1组装准备
9.2.1.1组装要求
(1)制定详细、可行的组装计划
(2)提前做好技术培训,使参加组装人员了解TBM的结构性能。
(2)制定合理的组装材料、机具、配件计划。
(4)严格控制组装质量,做好组装记录。
(5)设置专职的质量控制组和安全控制组,全程监控TBM的组装工作。
9.2.1.2组装人员准备
根据TBM的结构特点,按专业分工并进行岗前培训,经考核合格后方可持证上岗。
为保证组装安全与质量,TBM组装期间采用两班制作业,每班工作8小时,白班工作时间为7:
00~15:
00,小夜班工作时间为15:
00~23:
00。
大件吊装全部安排在白班,每班设专职人员对组装调试安全与质量进行监督。
9.2.1.3组装场地准备
根据组装需要,结合工地出口场地实际情况,主机组装场地从距洞口30m的位置开始,主机与后配套组装场地布置参见图9-2。
图9-2TBM组装场地示意图
(1)根据施工组织设计,确保组装的空间和龙门吊安装的位置。
(2)地面硬化至要求的接地比压,完成主机部件摆放区域划分、与地面直接接触各主要部件安装位置的确定并标注。
(3)完成龙门吊安装的准备工作。
(4)完成主机组装基础的施工并达到强度要求,预埋TBM向洞内滑行所需钢轨并保证其标高与钻爆法施工段滑行轨道标高一致。
主机组装基础参见图9-3。
(5)完成后配套组装用轨道铺设。
图9-3主机组装基础及滑轨示意图
9.2.1.4组装设备准备
主机的组装使用1台2×
50t龙门吊,后配套组装使用两台25t汽车吊。
组装设备、机具根据组装需要配置,在组装场地内合理位置安排电源、高压风源、水源的接口,并根据要求安排电焊机、气割设备、探伤设备和叉车等。
9.2.1.5组装方案准备
为保证组装工作安全、快速、有序进行,首先制定详细的组装方案并付诸实施。
内容包括:
(1)制定组装顺序。
(2)根据组装顺序确定运输到场的顺序。
(3)安全措施:
制定起重设备安全操作规程、通用与专用工具操作规程、安全用电、消防、保安措施并贯彻落实,对人员进行岗前安全教育,必须使用安全帽、安全带、工作服等,设专职安全员,所有组装工作由组装调试指挥人员统筹安排,按照合理的顺序进行施工,确保人员、设备的安全。
(4)消防器材配备:
洞内合理配备灭火器、灭火砂等消防器材。
9.2.2基本技术要求
为保证TBM在组装过程的顺利、安全、准确,确保其原有的设计精度,应遵循以下技术要求:
(1)平稳吊装,确保安全。
(2)拆箱注意保持其原有设计尺寸,避免损伤构件原有加工精度。
(3)以适当的方式与材料认真清洗各个安装部件和配件。
(4)对照图纸正确安装。
(5)根据螺栓的级别按正确的顺序与扭矩紧固。
(6)电气与液压件安装应给予高度重视,以免由于错接而导致误动作。
(7)专用的设备和工具要根据说明书严格操作,保证安装设备的精度和可靠性。
9.2.3组装顺序
主机组装与后配套组装分别在各自的场地同时展开,TBM各部件运输到场,主机部件摆放于主机组装基础之后,后配套部件根据组装顺序,主要摆放于后配套组装区域;
经过开箱验收后开始组装,采取边运输边开箱验收边组装的方式。
9.2.3.1主机组装
主机组装前在基础的预埋钢轨上涂抹黄油,之后按照TBM组装流程逐步完成组装工作,主机组装流程参见图9-4。
9.2.3.2后配套组装
后配套组装在已经铺设好的轨道上进行,组装采用两台25t汽车吊机进行。
为最大程度避免与主机组装之间的干涉,从最后一节后配套台车开始组装,两台吊机配合,逐节完成所有后配套的组装工作,按照台车门架在轨道上拼装、安装相关辅助设备、连接电气液压等管线的顺序进行。
加工专用的走行式门架支撑连接桥前端,连接桥组
图9-4主机组装流程图
装完成后,首先进行连接桥与主机的连接,之后顺序完成后配套与连接桥的连接,使整套TBM连接为一个整体,最后安装皮带、硫化皮带。
组装流程见图9-5。
9.2.3.3主机和后配套连接
组装完毕的后配套和主机连接在一起,对接主机与后配套之间的各种管线。
整机组装的检查:
复核所有设备的安装固定,检查管路、线缆的连接情况。
9.2.4整机调试
组装工作完成后,立即进行整机调试,调试前需制订详细地调试方案,分系统进行,以确保TBM性能达到设计标准,主要包括以下几个方面:
(1)支撑系统
(2)主推进系统
(3)辅助推进系统
(4)刀盘主驱动
(5)刀盘辅助驱动
(6)管片拼装
(7)豆砾石回填
组装后配套尾部平台车
组装后部平台车
组装卸渣区平台车
安装尾部车上给水、排水、高压供电设备
组装安装设备平台车4
安装前部车上通风设备、除尘器
组装设备平台车3
安装设备车上空气压缩机、变压器
组装设备平台车2
安装车上液压泵站、管片运送系统
组装设备平台车1
安装车上配电柜、豆砾石注浆系统
安装连接桥
连接桥上设备、操作室安装、连接控制电缆
将连接桥和后配套连接
图9-5后配套组装流程图
(8)注浆
(9)材料运输
(10)通风系统
(11)供电系统
(12)通风系统
(13)给水排水
(14)PLC程序控制系统
(15)皮带机等辅助设备
调试过程中,须配备抢修工具、必要的配件等,同时详细记录各系统的运转参数,与制造商提供的设计参数对比,对不相符的项目查找原因并采取相应措施,由制造商负责确保设备性能达到设计标准。
9.3TBM滑行
TBM由组装位置到洞口、以及在隧洞出口1200m钻爆法施工段的通过,将采取相同的滑行的方式。
在尾盾拼装钢管片,以辅助推进油缸顶推钢管片推动整机向前滑动,主机部分在预埋的滑轨上向前滑动,后配套走行于铺设的钢轨上;
每向前滑行一个循环即1.5m,铺设一块钢管片,以12.5m(约8个掘进循环)作为一个完整的滑行工作循环,每个滑行工作循环的第一块钢管片锚固于洞底,其他钢管片与第一块钢管片顺次前后连接,所有钢管片可以循环使用;
当整机向前滑行约8个循环后,在连接桥位置铺设钢轨,同时重新锚固下一个滑行工作循环的第一块钢管片,并拆除其他钢管片。
9.3.1滑行准备工作
(1)加工滑行专用钢管片,钢管片结构参见图9-6;
图9-6TBM滑行用钢管片
(2)TBM进洞前,在洞外组装及滑行基座上预埋钢轨,在钻爆法施工段锚固30×
100mm钢板作为TBM滑行时主机的滑轨,洞外滑轨位置参见图9-3,洞内滑轨位置如图9-7所示。
(3)检查TBM滑轨,对损坏、变形的必须修复。
(4)检查滑轨安装位置,如不符合要求,必须进行调整。
(5)准备编组列车,满足滑行期间钢轨、电缆、风水管延伸等需要。
(6)清理钻爆法施工段,确保洞内没有干涉TBM通过的设施及杂物。
(7)复核钻爆法施工段隧洞的轴线误差。
9.3.2滑行
(1)在洞外组装基座尾部拱底TBM尾盾管片拼装位置钻Φ50mm孔,孔深50cm,共两排,每排3个孔;
(2)将钢管片安装在TBM尾盾位置,用φ45×
400mm销子固定在已经钻好的6个孔中;
(3)在滑轨上涂抹黄油,以辅助推进油缸顶推钢管片,推动TBM主机在滑轨上向前滑动,后配套在铺设好的钢轨上向前行进;
(4)整机向前移动一个掘进行程的距离后,在第一块钢管片的前方铺设第二块钢管片,但拱底部位不钻孔,该管片仅在图9-7中位连接耳板上用螺栓与第一块钢管
片固定,以防止TBM前进过程中钢管片翘曲;
(5)第二块钢管片铺设完毕,再次以辅助推进油缸推动整机向前行进;
(6)以此类推,共铺设8~9块钢管片后,连接桥前支架后部将会有12.5~13m的空间,则在此部位铺设钢轨,同时拆除已经铺设好的第一块钢管片,在盾尾重新钻孔锚固;
图9-7钻爆法施工段预埋滑轨安装位置
(7)向前推进一个掘进循环的距离后,将目前最后一块钢管片拆除,安装在尾盾部位,并与刚刚锚固的该画性工作循环的第一块钢管片纵向连接;
(8)依照上述方法,推动TBM向前行进,同时完成TBM尾部风水管、电缆的延伸。
TBM滑行过程参见图9-8。
9.3.3滑行注意事项
滑行过程中需注意以下几个方面:
(1)滑行过程中,需对主机及后配套加强巡视,确保TBM各部位与洞壁没有干涉,特别是刀盘前方,必须派专人负责观察;
(2)加强TBM姿态控制;
(3)控制滑行速度,不可太快;
(4)滑行过程中,相关部位的人员之间以对讲机相互联系,确保信息畅通;
(5)滑行过程中,刀盘前方负责观察的人员与TBM主司机密切联系;
图9-8TBM滑行过程示意图
(6)根据复核的钻爆法施工段隧洞轴线误差,确定各组主推进油缸的行程,确保TBM的前进方向;
(7)密切观察锚固环钢管片及其他钢管片的工作状态;
(8)推进过程中,钢管片范围内不得站人。
9.4TBM始发与试掘进
9.4.1始发与起始环管片安装
始发是TBM施工的关键环节之一,必须予以高度重视。
9.4.1.1TBM就位
始发前,复核TBM滑轨,确保滑轨顺直,严格控制标高、间距及中心线,调整好TBM的姿态,主机轴线应该与即将开挖的隧洞轴线一致,以保证掘进方向准确。
根据“TBM段与钻爆段接头大样”,由于钻爆法施工段与TBM施工段轴线有偏差,断面形式也不能满足TBM始发要求,因此需要进行扩挖,并且滑轨铺设需根据TBM姿态调整的需要施工,TBM始发就位所需空间及滑轨铺设参见图9-9。
图9-9TBM始发就位空间示意图
9.4.1.2钢管片与负环管片拼装
由于从钻爆法施工段向TBM施工段过渡部分空间狭小,不具备安装普通反力架的条件,根据该洞段的工程地质条件,TBM掘进将采取双护盾模式,因此需要专门加工部分特殊的钢管片,用以承受始发时拼装管片的反力。
TBM始发就位后,由下向上分块将钢管片锚固在洞壁上,将其焊接为一个整体,确保安装位置精确,为负环管片的准确安装做好准备。
钢管片为箱型结构,沿圆周方向分为五块,内设筋板,预留两圈交错布置的锚固孔。
始发时边掘进边拼装负环混凝土管片,并从左右两侧加以支撑,确保拼装精度,为起始环管片的精确拼装创造条件。
待TBM掘进60m之后,拆除钢管片、负环混凝土管片以及接口密封。
钢管片与负环管片的拼装参见图9-10,负环管片的加固参见图9-11。
图9-10钢管片与负环管片拼装示意图
图9-11负环管片加固措施
9.4.1.3起始环管片拼装与回填
负环管片拼装完毕,从里程22+965.83处开始拼装起始环管片,起始管片应准确定位:
定位支撑应锚固牢靠,不变形;
上下左右对称,误差不大于1mm;
起始环管片拼装完成后,需填充豆砾石并注浆,因而制作安装接口密封,密封结构参见图9-12。
9.4.1.4TBM始发扩挖段断面恢复
TBM始发扩挖段钢管片、负环管片及接口密封拆除后,根据TBM段与钻爆段接头断面设计喷射混凝土予以恢复。
9.4.2TBM试掘进
本标段工程采用双护盾掘进机施工,试掘进长度为1000m。
在试掘进段阶段,施工人员必须熟练的掌握掘进机施工的技术与参数控制,实现信息化施工。
在施工过程中,应注意研究掘进参数的设定方法和原理;
掘进时推进速度要保持相对平稳,控制好每次的纠偏量,为管片拼装创造良好条件;
学会根据设计图纸及超前地质预报结果,判断围岩类别、岩性、稳定性、整体性、抗压强度等参数,对掘进时各种设备操作
图9-12起始环管片接口密封示意图
及工程地质等技术数据进行采集、统计和分析,争取在1000m内熟练掌握盾构机的操作方法,确定本机在各种地质条件下掘进施工的参数设定范围,形成一套相对完善的施工方法。
此阶段工作重点如下:
(1)用最短的时间熟悉掌握掘进机的操作方法、机械性能,培训合格的设备操作人员;
(2)了解和认识本标段工程地质条件,掌握本机在该地质条件下的操控方法;
(3)熟悉管片拼装的操作,掌握拼装质量的控制方法,提高拼装质量与速度;
(4)通过试掘进,掌握本机在不同围岩下掘进模式与掘进参数的选择;
(5)整合施工组织,使之更加有利于提高施工质量与施工速度。
9.5TBM正常掘进
9.5.1TBM破岩机理
双护盾硬岩掘进机使用盘形滚刀,将刀圈的刀刃挤压楔入岩体进行破岩,其破岩形式属于楔入式滚压破碎。
刀尖压入岩体,当压力大于岩石的抗压强度时,与刀尖接触部位的岩石被压碎,在刀尖前形成一压碎区,如图9-13。
压碎区向外形成的压力,使压碎区的周边产生裂纹,裂纹随压力增加而扩展,直到渣片形成而剥离,完成一个成渣过程。
随刀盘的转动和刀具在岩面上继续向前滚压又开始下一渣片的形成。
刀盘上的盘形滚刀在破岩掘进面上形成同心圆的滚动轨迹。
刀尖前的岩石被压碎,碾成细小的岩粉,而刀尖两侧的岩体被剥成一块块的渣片。
岩渣是一片片形成的,有时在刀圈的内侧形成,有时是在外侧。
轨迹之间是鱼鳞状凹坑。
刀圈滚压生成的岩渣块形状呈中间厚周边薄的长片形,近似鱼背的形状。
渣块的大小与刀间距和切深有关。
图9-13破岩机理
9.5.2掘进
双护盾掘进机有双护盾和单护盾两种掘进模式,掘进施工过程中,需根据工程地质图纸、石渣、前序掘进参数、超前地质探测结果等,对掌子面围岩状态作出准确判断,据此选择相应的掘进模式及掘进参数。
TBM施工采取三班制,两班掘进一班整备,掘进工班每班工作9小时,整备工班工作6小时,整备工作安排在每天上午。
9.5.2.1掘进准备
(1)接通隧洞内的照明。
(2)接通洞外开闭所和TBM主机变压器之间的电源。
(3)接通TBM上变压器的主开关,使变压器投入使用。
然后待变压器工作平稳后,接通二次侧的电源输出开关,检查TBM所需的各种电压,同时接通TBM及后配套上的照明系统。
同时检查TBM上的漏电监测系统,确定接地的绝缘值可以满足各个设备的工作要求。
(4)检查气体监测系统、火灾监测系统监测的数据、结果。
确定TBM可以进行掘进作业。
(5)确认所有灯光、声音指示元件工作正常。
所有调速旋钮均在零位。
(6)检查液压系统的液压油油位、润滑系统的润滑油位,如有必要马上添加油料。
(7)确认给水、通风正常。
(8)接通TBM的控制电源,启动液压动力站、通风机、TBM自身的给水(加压)水泵。
根据施工条件,确定是否启动排水水泵。
(9)确定皮带机风水电管线延伸等各种辅助施工进入掘进工况。
(10)检查测量导向的仪器工作正常,并提供正确的位置参数和导向参数。
(11)根据测量导向系统提供的TBM的位置参数,调整TBM的姿态,确保方向偏差(水平、垂直、圆周)在允许误差范围内,撑紧撑靴达到满足掘进需要的压力,或将辅助推进油缸顶紧在已经安装好的管片上。
9.5.2.2掘进作业循环基本步骤
(1)顺序启动后配套皮带机、主机皮带机,并确定运转正常。
(2)启动掘进机各个部位的声电报警系统,提示进入工作状态。
(3)顺序启动变频驱动电机。
(4)启动主轴承的油润滑系统、各个相对移动部位的润滑系统。
并确定各个润滑系统正常工作。
(5)调整扭矩反作用油缸支撑扭矩支承梁,使刀盘的转动扭矩可靠传递到支撑护盾。
如岩石不能满足支撑护盾的支撑,利用转环转动推进油缸使油缸旋转一定角度来产生抵抗刀盘旋转扭矩的圆周力。
以上工作完成后启动刀盘旋转并调整刀盘转速至预先选定的转速。
同时启动除尘系统风机。
(6)慢速推进刀盘靠紧掌子面,确定刀盘已经靠紧掌子面后选择合适的推进速度进行掘进作业。
在刀盘和岩石表面接触之前启动刀盘喷水系统对岩石喷水(在土层地段施工时,不进行喷水,避免破坏土层的稳定)。
(7)时刻监控TBM掘进时各种参数的变化、石渣状态等。
掘进时根据TBM的掘进参数和预计的前方围岩的情况选择适当的掘进参数,包括刀盘转速、推进力、驱动变频电机频率、推进速度、皮带机转速等。
并根据围岩的状况变化及时的进行调整。
如围岩满足双护盾掘进模式的要求,采取双护盾掘进方式,掘进和管片安装、豆砾石回填、注浆、钢轨铺设等同时进行;
如围岩状况较差,不能满足双护盾掘进模式的条件,则采取单护盾掘进方式,掘进施工和管片安装不能同时进行,安装完管片后,利用辅助推进油缸完成一个循环推进作业后再进行管片安装。
(8)掘进至行程结束后,停止推进并将刀盘后退约3~5cm,顺序停止刀盘喷水、刀盘旋转、驱动电机、皮带机。
(9)伸出前护盾液压支撑机构并撑紧,推进油缸拖动支撑盾前移、拖拉后配套到位,完成换步,重复掘进准备工作,准备开始下一掘进行程。
当掘进机采用单护盾形式掘进时,支撑护盾和后配套的前移通过推进油缸和辅助推进油缸共同作用完成。
9.5.2.3双护盾模式掘进
双护盾模式掘进是指在硬岩条件下的隧洞开挖时,TBM依靠支撑盾上的支撑靴支撑在洞壁上,掘进的同时可完成在尾盾拼装管片、豆砾石回填等作业。
9.5.2.3.1双护盾模式掘进步骤
双护盾模式掘进作业循环主要分为两个阶段:
第一阶段,换步与调向。
掘进行程完成之后,停止推进、停止刀盘旋转,收回撑靴油缸,刀盘底部支撑于洞底,主推进油缸收回带动支撑盾向前移动,辅助推进油缸撑紧已拼装好的管片;
当支撑盾到达预定位置时,调整各位置推进油缸以调整掘进方向,待TBM方向调整完成后,撑靴再次撑紧洞壁,换步完成。
第二阶段,掘进的同时拼装管片。
推进油缸推动旋转的刀盘向前掘进1.5m,掘进反力传递到撑紧于洞壁的撑靴,出渣列车停放于后配套区域,刀盘切削下来的石渣通过主机皮带机、后配套皮带机卸入渣车。
与此同时,实施拼装预制混凝土管片,回填豆砾石、灌浆等作业。
9.5.2.3.2双护盾模式掘进流程
双护盾模式下掘进的工艺流程如图9-14所示。
(1)判断掌子面围岩状态。
根据工程地质图纸,参考上一循环掘进参数、石渣状态判定掌子面围岩状况,通常可据此断定前方围岩的整体性、岩性、发育程度、含水量等。
如有必要,可采用超前地质探测,进一步确定前方围岩状态。
本TBM配备了两套超前地质探测装置,分别可准确预测前方150m、30m范围内围岩地质情况。
(2)换步、调向。
换步调向操作如前所述,TBM主司机应该在换步过程中,根据测量导向系统所显示的上一循环结束时TBM的方位,本掘进循环调向参考值调整TBM的姿态,确保掘进方向控制在允许的范围之内。
(3)选择掘进参数。
根据判定的掌子面的围岩状态,选择推力、撑靴压力、刀盘转速等掘进参数。
(4)掘进及拼装管片。
掘进过程中结合实际掘进参数的变化判断围岩的变化,适时适当调整,同时结合施工经验达到掘进参数与围岩状况的最佳匹配。
9.5.2.4单护盾模式掘进
单护盾模式掘进是指在软岩条件下的隧洞开挖时,撑靴全部收回(不再撑紧洞壁),主推进油缸也收回,前盾和支撑盾作为一个整体动作,掘进过程中辅助推进油缸顶紧已经拼装好的管片提供推进力,TBM掘进时无法拼装管片,只能在掘进行程完成之后,停止掘进,待管片拼装及换步调向等工序完成后,方可继续掘进。
9.5.2.4.1单护盾模式掘进步骤
单护盾模式下的掘进作业循环可分为三个阶段:
第一阶段,调向。
上一循环管片拼装完成之后,开始本循环作业,此时辅助推进油缸已经收回,也就是换步已经完成。
通过调整辅助推进油缸,使主机以刀盘底部接触洞底的部位作支点在水平和竖直方向旋转,从而调整TBM掘进方向。
第二阶段,掘进。
辅助推进油缸推动旋转的刀盘向前掘进1.5m,掘进反力传递到拼装好的管片,出渣列车停放于后配套区域,刀盘切削下来的石渣通过主机皮带机、后配套皮带机卸入渣车。
与此同时,实施回填豆砾石、灌浆等作业。
第三阶段,拼装管片与换步。
9.5.2.4.2单护盾模式掘进流程
单护盾模式下掘进的工艺流程如图9-15所示。
单护盾模式适用于软弱围岩、断层破碎带等地质洞段,因而应严格按照工艺流程与施组要求施工,加强超前地质探测预报,积极采取加固、固结灌浆等技术措施,最大程度的保证TBM快速、安全地通过。
9.5.2.5出渣运输
TBM施工的掘进施工和出渣运输同时进行,刀盘开挖的石渣通过皮带机卸到停放在后配套上的渣车内,矿车通过牵引机车移动使石渣均匀卸到各节车内。
编组列车利用35t变频电动机车牵引出洞,到达卸渣翻车机,将石渣卸到渣场。
9.5.2.6停机
TBM施工的过程中,经常会需要停机,如连续皮带机皮带的硫化、刀具的检查更换、处理不良的地质等情况会需要停止TBM掘进的作业。
停机的操作如下:
(1)如当时正进行掘进施工,就必须按操作的规程顺序停止推进、后退刀盘、停止刀盘喷水、停止刀盘旋转、停止驱动电机、顺序停止随机皮带和连续皮带机。
在此情况下一定注意将所有皮带上的石渣输送完毕后才能停止皮带机。
(2)如果需要较长时间的停机,在完成上述步骤后,依次停止除尘、给水、通风系统。
(3)根据施工的需要启动施工所需的设备进行作业。
9.5.2.7掘进中的注意事项
TBM掘进过程中,所有的辅助作业都必须从属于主机的掘进,除特别情况下不能影响掘进的作业。
(1)合理安排车辆调度,确保施工用料包括管片、注浆料、豆砾石等及时运送到施工地点。