热处理生产实习报告文档格式.docx
《热处理生产实习报告文档格式.docx》由会员分享,可在线阅读,更多相关《热处理生产实习报告文档格式.docx(30页珍藏版)》请在冰豆网上搜索。
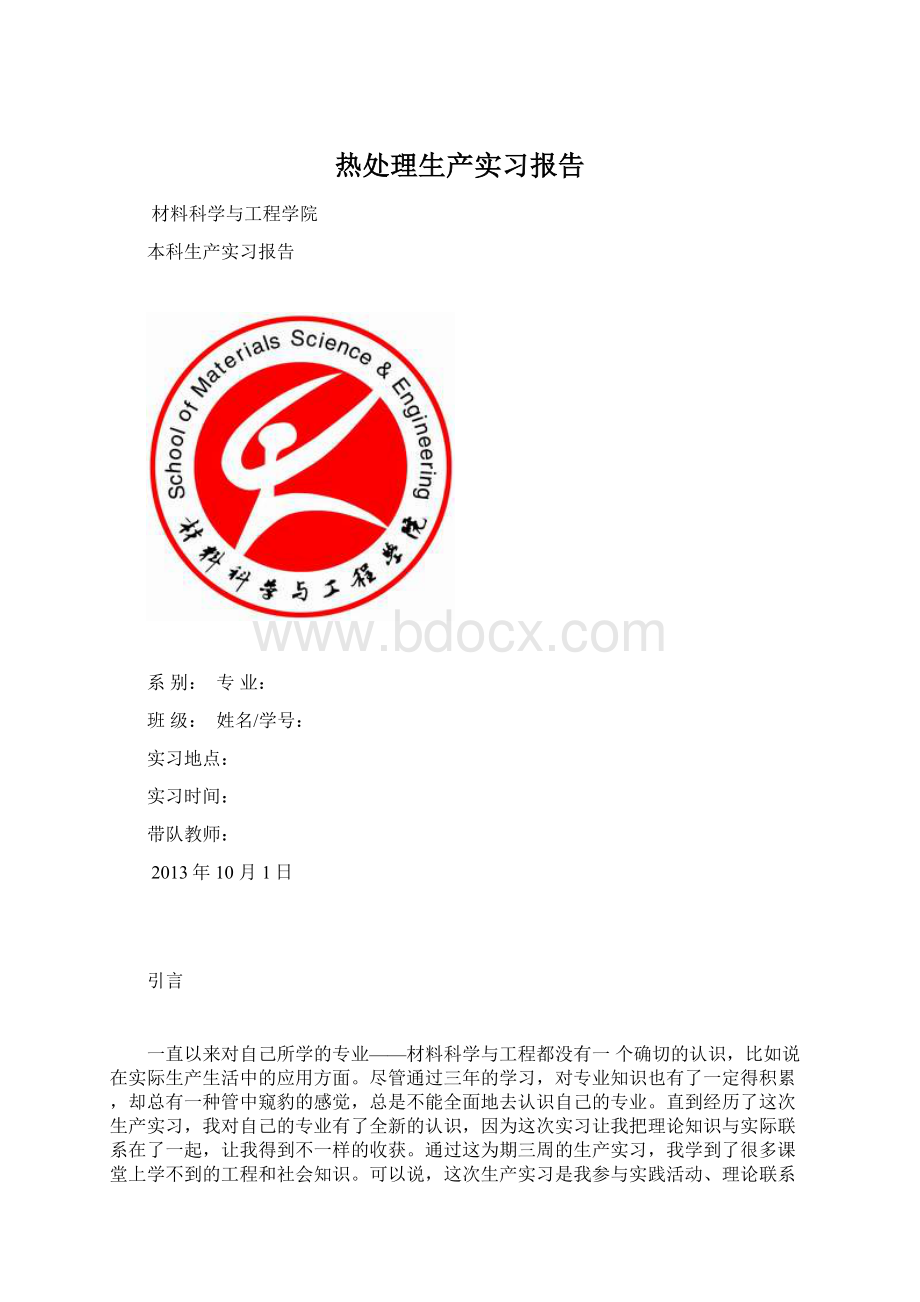
50~60年代连续热处理工艺在镀锡原板的生产中得到广泛运用。
随后,日本采用高温轧制(Ar3点以上)、高温卷取(Ar1点以上)工序同退火时过时效处理(见时效处理)工序合并的方法,生产深冲用冷连铸轧钢板获得成功。
1971年和1972年日本先后建成了两条连续退火生产线。
到了80年代连续退火得到了广泛应用。
连续退火机组的工艺流程如图所示。
冷轧带钢厂连续退火机组工艺流程
1-开卷和焊接;
2-清洗;
3-活套;
4-连续退火;
5-平整和拉矫;
6-卷取
连续退火炉按作业方式分立式(塔式)与卧式两种。
塔式退火炉用于每月必须退火1万t以上的带钢时才是经济的。
产量低时,用卧式连续退火炉较经济,因为这种炉子投资低、热量消耗较少。
目前,在生产中运行的有4种工艺:
(1)新日铁公司的NSC-CAPL方法;
(2)日本钢管公司的NKK-CAL方法;
(3)川崎公司的KM-CAL方法;
(4)比利时公司的NOWAQ方法。
它们的不同点在于加热后的冷却方法不同,有水冷、气冷、辊冷、水一气复合冷却、辊一气复合冷却、浸冷、喷冷等。
各种冷却方法用来控制冷却速度,以得到所需组织结构的冷却带钢。
4种方法原则上有两种不同的退火周期。
一种是加热到退火温度后保温,冷却到过时效温度时再保温,随后冷却到室温。
另一种是加热到退火温度后保温,冷却到室温,再重新加热到过时效温度,在此温度上保温,最后冷却到室温。
对双相钢,无需加热到过时效温度。
用上述两种不同退火周期,可生产CQ(商用质量)、DQ(冲压质量)、DDQ(深冲质量)、HS(高强度钢)和双相钢。
1.2热镀锌简介
热镀锌(galvanizing)也叫热浸锌和热浸镀锌:
是一种有效的金属防腐方式,主要用于各行业的金属结构设施上。
是将除锈后的钢件浸入500℃左右融化的锌液中,使钢构件表面附着锌层,从而起到防腐的目的。
热镀锌工艺流程:
成品酸洗-水洗-加助镀液-烘干-挂镀-冷却-药化-清洗-打磨-热镀锌完工1、热镀锌是由较古老的热镀方法发展而来的,自从1836年法国把热镀锌应用于工业以来,已经有一百四十年的历史了。
然而,热镀锌工业是近三十年来伴随冷轧带钢的飞速发展而得到了大规模发展。
1.2.1原理
1热镀锌层防护性能
通常电镀锌层厚度5~15μm,而热镀锌层一般在35μm以上,甚至高达200μm。
热镀锌覆盖能力好,镀层致密,无有机物夹杂。
众所周知,锌的抗大气腐蚀的机理有机械保护及电化学保护,在大气腐蚀条件下锌层表面有ZnO、Zn(OH)2及碱式碳酸锌保护膜,一定程度上减缓锌的腐蚀,这层保护膜(也称白锈)受到破坏又会形成新的膜层。
当锌层破坏严重,危及到铁基体时,锌对基体产生电化学保护,锌的标准电位-0.76V,铁的标准电位-0.44V,锌与铁形成微电池时锌作为阳极被溶解,铁作为阴极受到保护。
显然热镀锌对基体金属铁的抗大气腐蚀能力优于电镀锌。
2热镀锌层形成过程
热镀锌层形成过程是铁基体与最外面的纯锌层之间形成铁-锌合金的过程,工件表面在热浸镀时形成铁-锌合金层,才使得铁与纯锌层之间很好结合,其过程可简单地叙述为:
当铁工件浸入熔融的锌液时,首先在界面上形成锌与α铁(体心)固熔体。
这是基体金属铁在固体状态下溶有锌原子所形成一种晶体,两种金属原子之间是融合,原子之间引力比较小。
因此,当锌在固熔体中达到饱和后,锌铁两种元素原子相互扩散,扩散到(或叫渗入)铁基体中的锌原子在基体晶格中迁移,逐渐与铁形成合金,而扩散到熔融的锌液中的铁就与锌形成金属间化合物FeZn13,沉入热镀锌锅底,即为锌渣。
当工件从浸锌液中移出时表面形成纯锌层,为六方晶体。
其含铁量不大于0.003%。
3生产工序
热镀锌(钢管)生产工艺:
上料→酸洗、水洗→溶剂→烘干→热镀锌→内、外吹→滚标、标识→钝化→检验→包装。
按照习惯往往根据镀前处理方法的不同把热镀锌工艺分为线外退火和线内退火两大类。
a.线外退火:
就是热轧或冷轧钢板进入热镀锌作业线之前,首先在抽底式退火炉或罩式退火炉中进行再结晶退火,这样,镀锌线就不存在退火工序了。
钢板在热镀锌之前必须保持一个无氧化物和其他脏物存在的洁净的纯铁活性表面。
这种方法是先由酸洗的方法把经退火的表面氧化铁皮清除,然后涂上一层由氯化锌或由氯化铵和氯化锌混合组成的溶剂进行保护,从而防止钢板再被氧化。
属于这个类别的热镀锌方法包括:
湿法热镀锌法、单张钢板法和惠林热法。
b.线内退火:
就是由冷轧或热轧车间直接提供带卷作为热镀锌的原板,在热镀锌作业线内进行气体保护再结晶退火。
属于这个类别的热镀锌方法包括:
森吉米尔法、改良森吉米尔法、美钢联法(同日本川崎法)、赛拉斯法和莎伦法。
1.2.2工业方法
湿法工艺、单张钢板、惠林热法、线内退火、森吉米尔法、美钢联法、赛拉斯法、莎伦法、改良森吉米
1.2.3热镀锌原理
将铁件清洗干净,然后溶剂处理,烘干后浸入锌液中,铁与熔融锌反应生成一合金化的锌层,其流程为:
脱脂--水洗--酸洗--助镀--烘干--热浸镀锌--分离--冷却钝化。
热镀锌的合金层的厚度主要取决于钢材的硅含量等化学成份,钢材的横截面积大小,钢材表面的粗糙程度,锌锅温度,浸锌时间,冷却快慢,冷轧变形等。
1.2.4热镀锌的优点
1、处理费用低:
热浸镀锌防锈的费用要比其他漆料涂层的费用低;
2、持久耐用:
在郊区环境下,标准的热镀锌防锈厚度可保持50年以上而不必修补;
在市区或近海区域,标准的热镀锌防锈层则可保持20年而不必修补;
3、可靠性好:
镀锌层与钢材间是冶金结合,成为钢表面的一部份,因此镀层的持久性较为可靠;
4、镀层的韧性强:
镀锌层形成一种特别的冶金结构,这种结构能承受在运送及使用时受到机械损伤;
5、全面性保护:
镀件的每一部分都能镀上锌,即使在凹陷处、尖角及隐藏处都能受到全面保护;
6、省时省力:
镀锌过程要比其他的涂层施工法更快捷,并且可避免安装后在工地上涂刷所需的时间。
7、初期成本低:
一般情况下,热浸锌的成本比施加其他保护涂层要低,原因很简单,其他保护涂层如打砂油漆是劳力密集的工序,反之热浸锌的工序为高机械化,紧密控制的厂内施工。
8、检验简单方便:
热浸锌层可以目视及简单的非破坏性涂层厚度表作测试
9、可靠性:
热浸锌的规格一般按照BSENISO1461执行,规限其最低的锌层厚度,所以其防锈年期及表现是可靠及可预计的。
1.3电镀简介
电镀是指在含有欲镀金属的盐类溶液中,以被镀基体金属为阴极,通过电解作用,使镀液中欲镀金属的阳离子在基体金属表面沉积出来,形成镀层的一种表面加工方法。
镀层性能不同于基体金属,具有新的特征。
根据镀层的功能分为防护性镀层,装饰性镀层及其它功能性镀层。
铝件电镀液配方工艺流程:
高温弱碱浸蚀→清洗→酸洗→清洗→浸锌→清洗→二次浸锌→清洗→预镀铜→清洗→氰化镀银→回收洗→清洗→浸亮→清洗→烘干。
从工艺流程看,所选保护材料必须耐高温(80℃左右)、耐碱、耐酸,其次,保护材料在镀银后能易于剥离。
市售的保护材料有可剥性橡胶、可剥性漆、一般粘性胶带及胶带等。
分别试验这些保护材料的耐酸、碱腐蚀、耐高温(碱蚀溶液最高温度80℃左右)性能以及可剥离性。
1.3.1工作原理
1.概述
电镀需要一个向电镀槽供电的低压大电流电源以及由电镀液、待镀零件(阴极)和阳极构成的电解装置。
其中电镀液成分视镀层不同而不同,但均含有提供金属离子的主盐,能络合主盐中金属离子形成络合物的络合剂,用于稳定溶液酸碱度的缓冲剂,阳极活化剂和特殊添加物(如光亮剂、晶粒细化剂、整平剂、润湿剂、应力消除剂和抑雾剂等)。
电镀过程是镀液中的金属离子在外电场的作用下,经电极反应还原成金属原子,并在阴极上进行金属沉积的过程。
因此,这是一个包括液相传质、电化学反应和电结晶等步骤的金属电沉积过程。
2.电镀原理图
在盛有电镀液的镀槽中,经过清理和特殊预处理的待镀件作为阴极,用镀覆金属制成阳极,两极分别与直流电源的负极和正极联接。
电镀液由含有镀覆金属的化合物、导电的盐类、缓冲剂、pH调节剂和添加剂等的水溶液组成。
通电后,电镀液中的金属离子,在电位差的作用下移动到阴极上形成镀层。
阳极的金属形成金属离子进入电镀液,以保持被镀覆的金属离子的浓度。
在有些情况下,如镀铬,是采用铅、铅锑合金制成的不溶性阳极,它只起传递电子、导通电流的作用。
电解液中的铬离子浓度,需依靠定期地向镀液中加入铬化合物来维持。
电镀时,阳极材料的质量、电镀液的成分、温度、电流密度、通电时间、搅拌强度、析出的杂质、电源波形等都会影响镀层的质量,需要适时进行控制。
首先电镀液有六个要素:
主盐、附加盐、络合剂、缓冲剂、阳极活化剂和添加剂。
电镀原理包含四个方面:
电镀液、电镀反应、电极与反应原理、金属的电沉积过程。
电镀反应中的电化学反应:
下图是电镀装置示意图,被镀的零件为阴极,与直流电源的负极相连,金属阳极与直流电源的正极联结,阳极与阴均浸入镀液中。
当在阴阳两极间施加一定电位时,则在阴极发生如下反应:
从镀液内部扩散到电极和镀液界面的金属离子Mn+从阴极上获得n个电子,还原成金属M。
另一方面,在阳极则发生与阴极完全相反的反应,即阳极界面上发生金属M的溶解,释放n个电子生成金属离子Mn+。
3.电极及反应机理
A、电极电位 当金属电极浸入含有该金属离子的溶液中时,存在如下的平衡,即金属失电子而溶解于溶液的反应和金属离子得电子而析出金属的逆反应应同时存在:
Mn++ne=M 平衡电位与金属的本性和溶液的温度,浓度有关。
为了精确比较物质本性对平衡电位的影响,人们规定当溶液温度为250℃,金属离子的浓度为1mol/L时,测得的电位叫标准电极电位。
标准电极电位负值较大的金属都易失掉电子被氧化,而标准电极电位正值较大的金属都易得到电子被还原。
B、极化 所谓极化就是指有电流通过电极时,电极电位偏离平衡电极电位的现象。
所以,又把电流-电位曲线称为极化曲线。
产生极化作用的原因主要是电化学极化和浓差极化。
1、电化学极化 由于阴极上电化学反应速度小于外电源供给电子的速度,从而使电极电位向负的方向移动而引起的极化作用。
2、浓差极化 由于邻近电极表液层的浓度与溶液主体的浓度发生差异而产生的极化称浓差极化,这是由于溶液中离子扩散速度小于电子运动造成的。
电镀过程是镀液中的金属离子在外电场的作用下,经电极反应还原成金属原子并在阴极上进行金属沉积的过程。
电镀原理简单而言,就是在含有欲镀金属的盐类溶液中,以被镀基体金属为阴极,通过电解作用,使镀液中欲镀金属的阳离子在基体金属表面沉积出来,形成镀层。
电镀的要素:
1.阴极:
被镀物,指各种接插件端子。
2.阳极:
若是可溶性阳极,则为欲镀金属。
若是不可溶性阳极,大部分为贵金属(白金,氧化铱)。
3.电镀药水:
含有欲镀金属离子的电镀药水。
4.电镀槽:
可承受,储存电镀药水的槽体,一般考虑强度,耐蚀,耐温等因素。
5.整流器:
提供直流电源的设备。
(磨光→抛光)→上挂→脱脂除油→水洗→(电解抛光或化学抛光)→酸洗活化→(预浸)→电镀→水洗→(后处理)→水洗→干燥→下挂→检验包装
电镀工作条件是指电镀时的操作变化因素,包括:
电流密度、温度、搅拌和电源的波形等。
4.阴极电流密度
任何镀液都有一个获得良好镀层的电流密度范围,获得良好镀层的最小电流密度称电流密度下限,获得良好镀层的最大电流密度称电流密度上限。
一般来说,当阴极电流密度过低时,阴极极化作用小,镀层的结晶晶粒较粗,在生产中很少使用过低的阴极电流密度。
随着阴极电流密度的增大,阴极的极化作用也随之增大(极化数值的增加量取决于各种不同的电镀溶液),镀层结晶也随之变得细致紧密;
但是阴极上的电流密度不能过大,不能超过允许的上限值(不同的电镀溶液在不同工艺条件下有着不同的阴极电流密度的上限值),超过允许的上限值以后,由于阴极附近严重缺乏金属离子的缘故,在阴极的尖端和凸出处会产生形状如树枝的金属镀层、或者在整个阴极表面上产生形状如海绵的疏松镀层。
在生产中经常遇到的是在零件的尖角和边缘处容易发生“烧焦”现象,严重时会形成树枝状结晶或者是海绵状镀层。
5.电镀溶液温度
当其它条件(指电压不变,由于离子扩散速度加快,电流会增大)不变时,升高溶液的温度,通常会加快阴极反应速度和离子扩散速度,降低阴极极化作用,因而也会使镀层结晶变粗。
但是不能认为升高溶液温度都是不利的,如果同其它工艺条件配合恰当,升高溶液温度也会取得良好效果。
例如升高温度可以提高允许的阴极电流密度的上限值,阴极电流密度的增加会增大阴极极化作用,以弥补升温的不足,这样不但不会使镀层结晶变粗而且会加快沉积速度,提高生产效率。
此外还可提高溶液的导电性、促进阳极溶解、提高阴极电流效率(镀铬除外)、减少针孔、降低镀层内应力等效果。
6.搅拌
搅拌会加速溶液的对流,使阴极附近消耗了的金属离子得到及时补充和降低阴极的浓差极化作用,因而在其它条件相同的情况下,搅拌会使镀层结晶变粗。
采用搅拌的电镀液必须进行定期或连续过滤,以除去溶液中的各种固体杂质和渣滓,否则会降低镀层的结合力并使镀层粗糙、疏松、多孔。
7.电镀方式
电镀分为挂镀、滚镀、连续镀和刷镀等方式,主要与待镀件的尺寸和批量有关。
挂镀适用于一般尺寸的制品,如汽车的保险杠,自行车的车把等。
滚镀适用于小件,如紧固件、垫圈、销子等。
连续镀适用于成批生产的线材和带材。
刷镀适用于局部镀或修复。
电镀液有酸性的、碱性的和加有铬合剂的酸性及中性溶液,无论采用何种镀覆方式,与待镀制品和镀液接触的镀槽、吊挂具等应具有一定程度的通用性。
1.3.2镀层分类
若按镀层的成分则可分为单一金属镀层、合金镀层和复合镀层三类。
[2]
若按用途分类,可分为:
①防护性镀层;
②防护性装饰镀层;
③装饰性镀层;
④修复性镀层;
⑤功能性镀层
1.单金属电镀
单金属电镀至今已有170多年历史,元素周期表上已有33种金属可从水溶液中电沉积制取。
常用的有电镀锌、镍、铬、铜、锡、铁、钴、镉、铅、金、银等l0余种。
在阴极上同时沉积出两种或两种以上的元素所形成的镀层为合金镀层。
合金镀层具有单一金属镀层不具备的组织结构和性能,如非晶态Ni—P合金,相图上没有的各蕊sn合金,以及具有特殊装饰外观,特别高的抗蚀性和优良的焊接性、磁性的合金镀层等。
2.复合镀
复合镀是将固体微粒加入镀液中与金属或合金共沉积,形成一种金属基的表面复合材料的过程,以满足特殊的应用要求。
根据镀层与基体金属之间的电化学性质分类,电镀层可分为阳极性镀层和阴极性镀层两大类。
凡镀层金属相对于基体金属的电位为负时,形成腐蚀微电池时镀层为阳极,故称阳极性镀层,如钢铁件上的镀锌层;
而镀层金属相对于基体金属的电位为正时,形成腐蚀微电池时镀层为阴极,故称阴极性镀层,如钢铁件上的镀镍层和镀锡层等。
按用途分类可分为:
①防护性镀层:
如Zn、劢.Ni、Ni、Cd、Sn和Cd-Sn等镀层,作为耐大气及各种腐蚀环境的防腐蚀镀层;
②防护.装饰镀层:
如Cu—Ni—Cr、Ni-Fe-cr复合镀层等,既有装饰性,又有防护性;
③装饰性镀层:
如Au、A9以及Cu.孙仿金镀层、黑铬、黑镍镀层等;
④修复性镀层:
如电镀Ni、cr、Fe层进行修复一些造价颇高的易磨损件或加工超差件;
⑤功能性镀层:
如Ag、Au等导电镀层;
Ni-Fe、Fe-C0、Ni-C0等导磁镀层;
Cr、Pt-Rll等高温抗氧化镀层;
Ag、Cr等反光镀层;
黑铬、黑镍等防反光镀层;
硬铬、Ni.SiC等耐磨镀层;
Ni.VIEE、Ni.C(石墨)减摩镀层等;
S小Pb、Cu、sn、Ag等焊接性镀层;
防渗碳镀Cu等。
1.3.3电镀电源
1.电源组成
主电路主要包括主变压器、功率整流器件和一些检测、保护装置等。
电镀电源中的主变压器是将交流电源电压降低为电镀工艺所需要的电压值。
晶闸管整流器中使用的是工频(50Hz)变压器,高频开关电源中使用的是高频(10~50kHz)变压器。
检测装置包括电压表、电流互感器等。
保护装置主要是用于功率整流器件的过流保护。
控制电路主要包括晶闸管或IGBT等的触发控制电路,电源的软启动电路,过流、过压保护电路,电源缺相保护电路等。
2.电源特点
1、节能效果好
开关电源由于采用了高频变压器,转换效率大大提高,正常情况下较可控硅设备提高效率10%以上,负载率达70%以下时较可控硅设备提高效率30%以上。
2、输出稳定性高
由于系统反应速度快(微秒级),对于网电及负载变化具有极强的适应性,输出精度可优于1%。
开关电源的工作效率高、所以控制精度高,有利于提高产品质量。
3、输出波形易于调制
由于工作频率高,其输出波形调整相对处理成本较低,可以较方便的按照用户工艺要求改变输出波形。
这样对于工作现场提高工效,改善加工产品质量有较强作用。
4、体积小、重量轻
体积与重量为可控硅电镀电源的1/5-1/10,便于规划、扩建、移动、维护和安装。
1.3.4局部电镀
通常按其施镀面积可将电镀分为全部镀和局部镀两种。
许多需局部电镀的零件就要对其非镀面进行绝缘保护,这就要用不同的局部绝缘方法来满足施工的技术要求,以保证零件非镀面不会镀上镀层,尤其是有特殊要求的零件。
根据日常的工作经验,现介绍电镀中常用的几种局部电镀工艺方法。
1.包扎法
这种方法是用胶布或塑料的布条、胶带等材料对非镀面进行绝缘保护,其包扎的方法根据零件的形状而定。
包扎法适用于简单零件,特别是形状规则的圆形零件。
包扎法是最简单的绝缘保护方法。
2.专用夹具法
专用夹具法,又叫仿形夹具法。
也就是说,对于某些形状比较复杂的零件,可以仿照零件的形状设计出专用的绝缘夹具,从而可大大提高生产效率。
如轴承内径或外径进行局部镀铬时,就可以设计一种专用的轴承镀铬夹具,且这种夹具还可以重复多次使用。
3.蜡剂保护法
用蜡制剂绝缘的特点是,与零件的粘接性能好,使用温度范围宽,绝缘层的端边不会翘起,因此,适用于对绝缘端边尺寸公差要求高、形状较复杂的零件。
此外,蜡制剂也可重复使用,损耗小,但其使用方法比较复杂,周期较长。
涂覆蜡制剂时,零件应预热到50~70℃,再涂覆熔化了的蜡制剂,先涂一薄层,覆盖整个需绝缘的表面,这时蜡不应中途凝固,然后再反复涂至所需厚度。
涂覆后在尚未冷却到室温之前的温热状态下,用小刀对绝缘端边进行修整,再用棉球沾汽油反复擦拭欲镀表面,该操作要十分仔细。
镀后可在热水或专用蜡桶内将蜡制剂熔化回收,然后用汽油等溶剂或水溶性清洗剂对零件进行清洗。
4.涂料绝缘法
电镀时经常使用漆类绝缘涂料进行绝缘保护。
这种绝缘保护方法操作简便,可适用于复杂零件。
常用的绝缘涂料有过氯乙烯防腐清漆(如G52—1.G52—2)、聚氯乙烯绝缘涂料、硝基胶等。
1.3.5发展阶段
(1)直流发电机阶段这种电源耗能大、效率低、噪声大.已经被淘汰。
(2)硅整流阶段是直流发电机的换代产品,技术十分成熟,但效率低,体积大,控制不方便。
仍有许多企业使用这种电镀电源。
(3)可控硅整流阶段是替代硅整流电源的主流电源,具有效率高、体积小、调控方便等特点。
随着核心器件——可控硅技术的成熟与发展.该电源技术日趋成熟,已获得广泛应用。
(4)晶体管开关电源即脉冲电源阶段脉冲电镀电源是当今最为先进的电镀电源,它的出现是电镀电源的一次革命。
这种电源具有体积小、效率高、性能优越、纹波系数稳定.而且不易受输出电流影响等特点。
脉冲电镀电源是发展的方向,现已开始在企业中使用。
1.4热喷涂简介
热喷涂是指一系列过程,在这些过程中,细微而分散的金属或非金属的涂层材料,以一种熔化或半熔化状态,沉积到一种经过制备的基体表面,形成某种喷涂沉积层。
它是利用某种热源(如电弧、等离子喷涂或燃烧火焰等)将粉末状或丝状的金属或非金属材料加热到熔融或半熔融状态,然后借助焰留本身或压缩空气以一定速度喷射到预处理过的基体表面,沉积而形成具有各种功能的表面涂层的一种技术。
1.热喷涂是一种表面强化技术,是表面工程技术的重要组成部分,一直是我国重点推广的新技术项目.它是利用某种热源(如电弧、等离子喷涂或燃烧火焰等)将粉末状或丝状的金属或非金属材料加热到熔融或半熔融状态,然后借助焰留本身或压缩空气以一定速度喷射到预处理过的基体表面,沉积而形成具有各种功能的表面涂层的一种技术。
2.热喷涂原理:
热喷涂是指一系列过程,在这些过程中,细微而分散的金属或非金属的涂层材料,以一种熔化或半熔化状态,沉积到一种经过制备的基体表面,形成某种喷涂沉积层。
涂层材料可以是粉状、带状、丝状或棒状。
热喷涂枪由燃料气、电弧或等离子弧提供必需的热量,将热喷涂材料加热到塑态或熔融态,再经受压缩空气的加速,使受约束的颗粒束流冲击到基体表面上。
冲击到表面的颗粒,因受冲压而变形,形成叠层薄片,粘附在经过制备的基体表面,随之冷却并不断堆积,最终形成一种层状的涂层。
该涂层因涂层材料的不同可实现耐高温腐蚀、抗磨损、隔热、抗电磁波等功能。
3.定义:
热喷涂,是将熔融状态的喷涂材料,通过高速气流使其雾化喷射在零件表面上,形成喷涂层的一种金属表面加工方法。
我们把特殊的工作表面叫“涂层”,把制造涂层的工作方法叫“热喷涂”,它是采用各种热源进行喷涂和喷焊的总称。
4.用途:
这在高速气流的作用下使之雾化成微细熔滴或高温颗粒,以很高的飞行速度喷射到经过处理的工件表面,形成牢固的覆盖层,从而使工件表面获得不同硬度、耐磨、耐腐、耐热、抗氧化、隔热、绝缘、导电、密封、消毒、防微波辐射以及其他各种特殊物理化学性能。
它可以在设备维修中修旧利废,使报废的零部件“起死回生”;
也可以在新产品制造中进行强化和预保护,使其“益寿延年”。
5.热喷涂材料:
喷涂粉末在整个热喷材料中占据十分重要的地位。
热喷涂合金粉末包括镍基、铁基和钴基合金粉,按不同的涂层硬度,分别应用于机械零部件的修理和防护。
技术特点
1.基体