新型干法水泥生产线回转窑操作技术Word格式.docx
《新型干法水泥生产线回转窑操作技术Word格式.docx》由会员分享,可在线阅读,更多相关《新型干法水泥生产线回转窑操作技术Word格式.docx(12页珍藏版)》请在冰豆网上搜索。
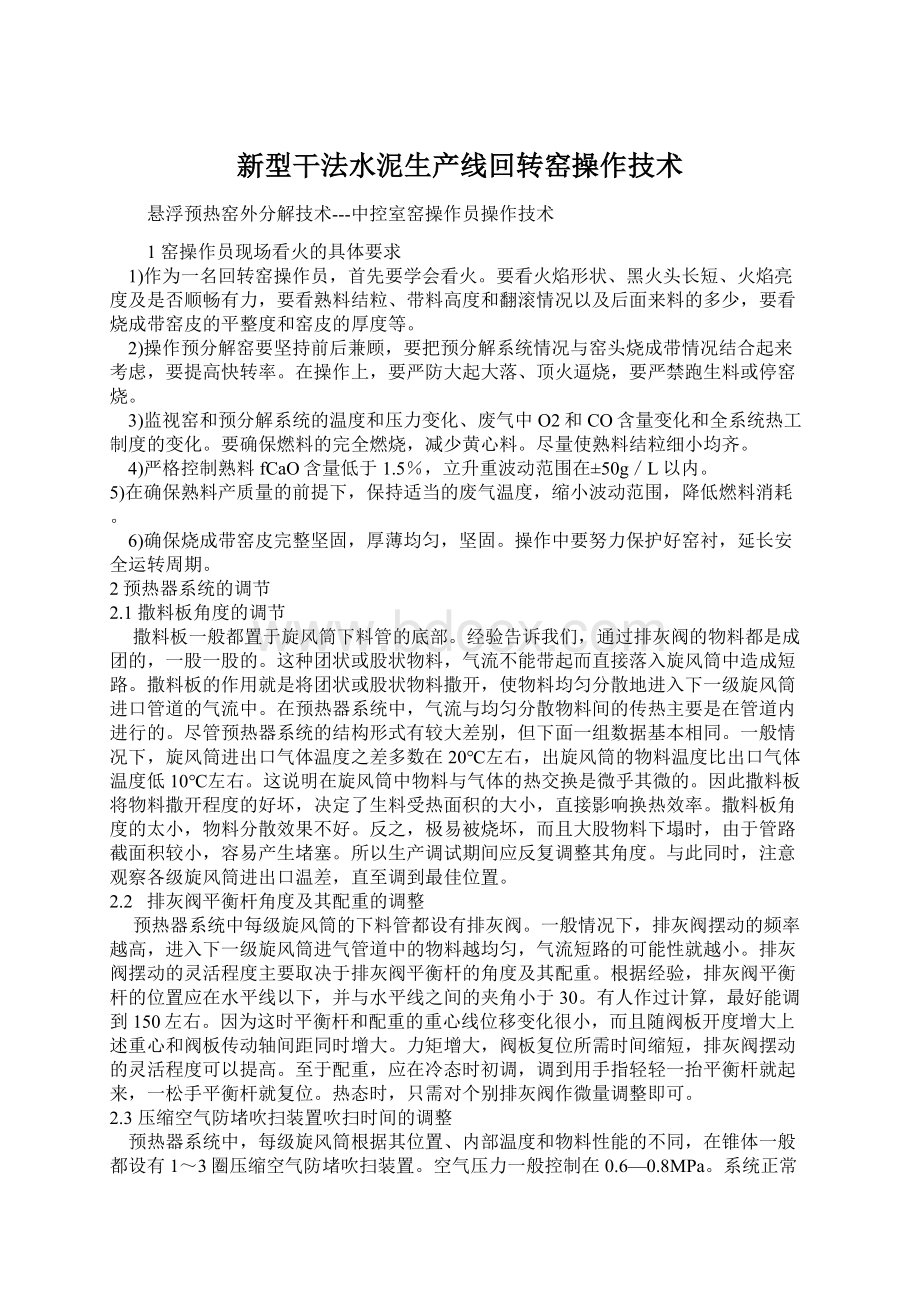
反之,极易被烧坏,而且大股物料下塌时,由于管路截面积较小,容易产生堵塞。
所以生产调试期间应反复调整其角度。
与此同时,注意观察各级旋风筒进出口温差,直至调到最佳位置。
2.2
排灰阀平衡杆角度及其配重的调整
预热器系统中每级旋风筒的下料管都设有排灰阀。
一般情况下,排灰阀摆动的频率越高,进入下一级旋风筒进气管道中的物料越均匀,气流短路的可能性就越小。
排灰阀摆动的灵活程度主要取决于排灰阀平衡杆的角度及其配重。
根据经验,排灰阀平衡杆的位置应在水平线以下,并与水平线之间的夹角小于30。
有人作过计算,最好能调到150左右。
因为这时平衡杆和配重的重心线位移变化很小,而且随阀板开度增大上述重心和阀板传动轴间距同时增大。
力矩增大,阀板复位所需时间缩短,排灰阀摆动的灵活程度可以提高。
至于配重,应在冷态时初调,调到用手指轻轻一抬平衡杆就起来,一松手平衡杆就复位。
热态时,只需对个别排灰阀作微量调整即可。
2.3压缩空气防堵吹扫装置吹扫时间的调整
预热器系统中,每级旋风筒根据其位置、内部温度和物料性能的不同,在锥体一般都设有1~3圈压缩空气防堵吹扫装置。
空气压力一般控制在0.6—0.8MPa。
系统正常运行时,由计算机定时进行自动吹扫。
吹扫时间可以根据需要人为设定。
一般为每隔20min左右,整个系统自动轮流吹扫一遍。
每级旋风筒吹扫3—5s。
当预热器系统压力波动较大或频繁出现塌料等异常情况时,随时可以缩短吹扫时间间隔,甚至可以定在某一级旋风筒上进行较长时间的连续吹扫。
当然无异常情况,不应采取这种吹扫方法。
因为吹人大量冷空气将会破坏系统正常的热工制度,降低热效率,增加系统热耗。
3新窑第一次点火及挂窑皮期间的操作方法
新窑耐火衬料烘干结束后,一般可以继续升温进行投料运行。
但如果耐火衬料烘干过程中温度控制忽高忽低波动较大,升温速率太高,则最好将其熄火,待冷却后进行系统内部检查。
如果发现耐火衬料大面积剥落,则必须进行修补,甚至更换。
3.1窑头点火升温
3.1.1窑头点火
现代化的预分解窑,窑头都采用三风道或四风道燃烧器,喷嘴中心都设有点火装置。
新窑第一次挂窑皮,最好使用轻柴油点火。
因为这样点火,油煤混合燃烧,用煤量少,火焰温度高,煤粉燃尽率也高。
如果用木材点火,火焰温度低,初期喷出的煤粉只有挥发分和部分固定碳燃烧。
煤粉中大部分固定碳未燃尽就在窑内沉降。
而且木材燃烧后留下大量木灰,这些煤灰和木灰在高温作用下被烧融,粘挂在耐火砖表面,不利于粘挂永久、坚固、结实和稳定的窑皮。
窑头点火一般用浸油的棉纱包绑在点火棒上,点燃后置于喷嘴前下方,随后即刻喷油。
待窑内温度稍高一些后开始喷人少量煤粉。
在火焰稳定、棉纱包也快烧尽时,抽出点火棒。
以后随着用煤量的增加,火焰稳定程度的提高,逐渐减少轻柴油的喷人量,直至全部取消。
在此期间,窑尾温度应遵循升温曲线要求缓慢上升。
在RSP型分解炉上,为使RSP分解炉涡流分解室有足够的温度加速煤粉的燃烧,窑头点火前应将2个C4旋风筒排灰阀杆吊起。
这样,窑尾部分高温废气可以进入涡流分解室经排灰阀、下料管人C4旋风筒,对涡流分解室起到预热升温的作用。
3.1.2
升温曲线和转窑制度
系统从冷态窑点火升温到开始挂窑皮期间窑尾废气温度、C5出口温度和C1出口温度以及不同温度段的转窑制度。
当窑点火升温约达24h以后,即窑尾废气温度约为750—800℃时,启动生料喂料系统,向窑内喂入5%左右的设计喂料量,为挂好窑皮创造条件。
3.2投料挂窑皮
当预热器系统充分预热,窑尾温度达950℃左右,这时分解炉涡流分解室温度可达650—700℃,窑头火砖开始发亮发白时,早先喂人的几吨生料也即将进入烧成带。
这时,窑头留火待料,保持烧成带有足够高的温度,并将吊起的2个C4排灰阀复原。
三次风管阀门开至10%左右,打开涡流燃烧室和分解室阀门,开始向涡流分解室喷轻柴油和少量煤粉。
当C1出口温度达400—450℃时,打开置于C1出口至高温风机废气管道上的冷风阀,掺人冷风调节废气温度,保护高温风机。
待C5出口温度达900℃时,适当开大三次风管阀门后即可下料。
喂料量为设计能力的30%-40%。
喂料后逐渐关闭冷风阀,适当加大喂煤量和系统排风量,窑以较低的转速(如0.3—0.6r/min)连续运转并开始挂窑皮。
当系统比较正常,分解炉温度稳定后,就可以撤除点火喷油嘴。
如果系统烧无烟煤,则应适当延长点火喷嘴的使用时间,但油量可以减少,以对无烟煤起助燃作用。
挂好窑皮是延长烧成带火砖寿命,提高回转窑运转率的重要环节。
其关键是掌握火候,待生料到达烧成带时及时调整燃料量和窑速,确保稳定的烧成带温度。
窑速与喂料量相适应,使粘挂的窑皮厚薄一致、平整、均匀、坚固。
挂窑皮期间严防烧成带温度骤变。
温度太高,挂上的窑皮易被烧垮,生料易烧流,在窑内“推车”会严重磨蚀耐火砖;
温度突然降低会跑生料,形成疏松夹心窑皮,极易塌落,影响窑皮质量。
挂窑皮时间,一般约需3—4个班。
窑皮挂到一定程度以后,生料喂料量可以3-5t/h的速度增加,直至100%的设计能力。
窑速和系统排风也随燃料和生料喂料量的增加而逐渐加大。
3.3冷却机的操作
1)挂窑皮初期,窑产量很低。
待熟料开始人冷却机时再启动篦床。
但篦速一定要慢,使熟料在篦床上均匀散开,并保持一定的料层厚度。
2)以设定冷却风量为依据,使篦下压力接近设定值。
注意避免冷却风机阀门开度太大,否则吹穿料层,造成短路。
3)运行中注意观察拉链机张紧情况并检查有无空气泄漏和串风现象。
漏风严重时,可暂时停拉链机,使机内积攒一定量的细料,以提高料封效果。
4)操作中如发现篦板翘起或脱落,要及时处理,严防篦板掉入熟料破碎机,造成严重事故。
3.4三次风管阀门的调节
1)分解炉点火时,三次风温度很低。
因此打开电动高温蝶阀时,宜小且缓慢,以避免涡流分解室温度骤降给点火带来困难。
2)投料后适当地调整涡流分解室顶部3个阀门的开度,以满足它们所在位置管道阻力的差异。
当生料喂料量达设计产量的80%左右时,使总阀门开度达70%-100%。
3.5系统温度的控制
从投料挂窑皮到窑产量达设计能力之前,烧成系统热耗一般都相对较高。
因此系统温度可比正常值偏高控制:
1)窑尾温度:
1000-1050℃;
2)分解炉混合室出口温度:
900℃;
3)C1出口废气温度:
350—400℃。
3.6废气处理系统的操作
1)系统投料之前,一般增湿塔不喷水,但出口废气温度应≤250℃,以免损坏电除尘器的极板和壳体。
2)增湿塔投入运行后,注意塔底窑灰水分,严防湿底。
3)待烧成系统热工制度基本稳定后,电除尘器才能投入运行,并控制电除尘器人口废气CO含量在允许范围以内。
4挂窑皮的影响因素
4.1生料化学成分
所谓挂窑皮就是液相凝固到耐火砖表面的过程。
因此熟料烧成液相量的多少液相粘度的高低直接影响到窑皮的形成,而生料化学成分直接影响液相量及其粘度。
以前湿法窑,人们主张挂窑皮期间的生料硅酸率适当偏低一些,而饱和比适当偏高一些。
但对于预分解窑,目前窑头都使用三风道或四风道燃烧器,回转窑正常运行时,一次风量少,二次风温度又很高。
因此煤粉燃烧速度、火焰温度远高于湿法窑。
如果降低硅酸率,液相量相应增加,物料容易烧流,挂上的窑皮不吃火容易脱落。
所以一般都主张挂窑皮的生料应与正常生料成分相同为好。
4.2烧成温度和火焰控制
挂好烧成带窑皮的主要因素除有一定的液相量和液相粘度以外,还要有适当的温度,气流、物料和耐火砖之间要有一定的温差。
一般应控制在正常生产时的烧成温度。
掌握熟料结粒细小而均齐,不烧大块更不能烧流,严禁跑生料。
升重控制在正常生产指标内。
要保持烧成温度稳定、窑速稳定、火焰形状完整、顺畅。
这样挂出的窑皮厚薄一致、平整、均匀、坚固。
4.3喂料量和窑速
为了使窑皮挂得坚固、均匀、平整,稳定窑内热工制度是先决条件。
挂窑皮期间,稳定的喂料量和稳定的窑速是至关重要的。
喂料量过多或窑速过快,窑内温度就不容易控制,粘挂的窑皮就不平整,不坚固。
所以新窑第一次挂窑皮起始喂料量和窑速最好能控制设计产量的35%左右。
挂到一定程度以后再视窑皮粘挂情况逐渐缓慢增加。
4.4挂窑皮期间的喷嘴位置
一般情况下,喷嘴位置应尽量靠前(往外拉)一点,同时偏料,火焰宜短不宜长。
这样高温区较集中,高温点靠前,使窑皮由窑前逐渐往窑内推进。
随着生喂料量的逐渐增加,喷嘴要相应往窑内移动。
待窑产量增加到正常情况,喷嘴也随之移到正常生产的位置。
挂窑皮期间切忌火焰太长,否则高温区不集中,窑皮挂得远或前薄后厚,甚至出现前面窑皮尚未挂好,后面已经形成结圈等不利情况。
5回转窑火焰的调节
目前国内预分解窑大多采用三风道或四风道燃烧器,而火焰形状则是通过内流风和外流风的合理匹配来进行调整的。
由于预分解窑入窑生料CaC03分解率已高达90%左右,所以一般外流风风速应适当提高,这样可以控制烧成带稍长一点,以利于高硅酸率料子的预烧和细小均齐熟料颗粒的形成。
如需缩短火焰使高温带集中一些或煤质较差,燃烧速度较慢时,则可以适当加大内流风,减少外流风;
如果煤质较好或窑皮太薄,窑简体表面温度偏高,需要拉长火焰,则应加大外流风,减少内流风。
但是外流风风量过大时容易造成火焰太长,产生过长的浮窑皮,容易结后圈,窑尾温度也会超高;
内流风风量过大,容易造成火焰粗短、发散,不仅窑皮易被烧蚀,顶火逼烧还容易产生熟料结粒粗大并出现黄心熟料。
目前国内大中型预分解窑生产线大多设有中央控制室。
操作员在中控室操作时主要观察彩色的CRT上显示带有当前生产工况数据的模拟流程图。
但火焰颜色,实际烧成温度、窑内结圈和窑皮等情况在电视屏幕上一般看不清楚,所以最好还应该经常到窑头进行现场观察。
在实际操作中,假如发现烧成带物料发粘,带起高度比较高,物料翻滚不灵活,有时出现饼状物料,这说明窑内温度太高了。
这时应适当减少窑头用煤量,同时适当减少内流风,加大外流风使火焰伸长,缓解窑内太高的温度。
若发现窑内物料带起高度很低并顺着耐火砖表面滑落,物料发散没有粘性,颗粒细小,熟料fCaO高,则说明烧成带温度过低,应加大窑头用煤量,同时加大内流风,相应减少外流风,使火焰缩短,烧成带相对集中,提高烧成带温度,使熟料结粒趋于正常。
假如发现烧成带窑简体局部温度过高或窑皮大量脱落,则说明烧成温度不稳定,火焰形状不好,火焰发散冲刷窑皮及火砖。
这时应减少甚至关闭内流风,减少窑头用煤量,加大外流风,使火焰伸长或者移动喷煤管,改变火点位置,重新补挂窑皮,使烧成状况恢复正常。
总之,窑内火焰温度、火焰形状要勤观察勤调整,以满足实际生产的需要。
6篦式冷却机的操作和调整
篦式冷却机的操作目标是要提高其冷却效率,降低出冷却机的熟料温度,提高热回收效率和延长篦板的使用寿命。
操作时,可通过调整篦床运行速度,保持篦板上料层厚度,合理调整篦式冷却机的高压、中压风机的风量,以得利于提高二、三次风温度。
当床上料层较厚时,应加快床运行速度,开大高压风机的风门,使进入冷却机的高温熟料始终处于松动状态。
并适当关小中压风机的风门,以减少冷却机的废气量;
当析上料层较薄时,较低的风压就能克服料层阻力而吹透熟料层。
因此,这时可适当减慢床运行速度,关小高压风机风门,适当开大中压风机风门,以利于提高冷却效率。
7增湿塔的调节和控制
增湿塔的作用是对出预热器的含尘废气进行增湿降温,降低废气中粉尘的比电阻值,提高电除尘器的除尘效率。
对于带五级预热器的系统来说,生产正常操作情况下,C1出口废气温度为320~350℃,出增湿塔气体温度一般控制在120—150℃,这时废气中粉尘的比电阻可降至1010Ωcm以下。
满足这一要求的单位熟料喷水量为0.18—0.22t/t。
实际生产操作中,增湿塔的调节和控制,不仅要控制喷水量,还要经常检查喷嘴的雾化情况,这项工作经常被忽视,所以螺旋输送机常被堵死,给操作带来困难。
一般情况下,在窑点火升温或窑停止喂料期间,增湿塔不喷水,也不必开电除尘器。
因为此时系统中粉尘量不大,更重要的是在上述2种情况下,燃煤燃烧不稳定,化学不完全燃烧产生CO浓度比较高,不利于电除尘器的安全运行。
假如这时预热器出口废气温度超高,则可以打开冷风阀以保护高温风机和电除尘器极板。
但投料后,当预热器出口废气温度达300℃以上时,增湿塔应该投入运行,对预热器废气进行增湿降温。
8
煤粉细度的控制原则
关于煤粉细度,各水泥厂都有自己的控制指标。
它主要取决于燃煤的种类和质量。
煤种不同,煤粉质量不同,煤粉的燃烧温度、燃烧所产生的废气量也是不同的。
对正常运行中的回转窑来说,在燃烧温度和系统通风量基本稳定的情况下,煤粉的燃烧速度与煤粉的细度、灰分、挥发分和水分含量有关。
绝大多数水泥厂,水分一般都控制在1.0%左右。
所以挥发分含量越高,细度越细,煤粉越容易燃烧。
当水泥厂选定某矿点的原煤作为烧成用煤后,挥发分、灰分基本固定的情况下,只有改变煤粉细度才能满足特定的燃烧工艺要求。
然而煤粉磨得过细,不仅增加能耗,还容易引起煤粉的自燃和爆炸。
因此选定符合本厂需要的煤粉细度,对稳定烧成系统的热工制度,提高熟料产质量和降低热耗都是非常重要的。
下面介绍几个根据煤粉挥发分和灰分含量来确定煤粉细度的经验公式:
1)用烟煤
对预分解窑来说,目前国内外水泥厂都采用三风道或四风道燃烧器。
由于它们的特殊性能,煤粉细度可以适当放宽。
简单地说,当煤粉灰分<
20%时,煤粉细度应为挥发分含量的0.5-1.0倍;
当灰分高达40%左右时,细度应为挥发分含量的0.5倍以下。
国内某水泥厂用过优质煤也用过劣质煤。
根据该厂多年的生产实践,总结出经验公式如下:
R=0.15*(V+C)/(A+W)*V
另一个厂则用如下经验公式:
R=(1—0.01A—0.0011Ⅳ)X0.5V
式中:
R-----90um筛筛余,%;
V、C、A、W——分别代表人窑和分解炉煤粉的挥发分、固定碳、灰分和水分,%。
下同。
2)用无烟煤
①伯力鸠斯公司介绍烧无烟煤时煤粉细度经验公式:
R≤·
27x*V/C
②国外某公司的研究成果经验公式:
R≤(0.5—0.6)*V
③天津水泥工业设计研究院烧无烟煤煤粉细度经验公式:
R=V/2—(0.5—1.0)
必须指出,许多水泥厂对煤粉水分控制不够重视,认为煤粉中的水分能增加火焰的亮度,有利于烧成带的辐射传热。
但是煤粉水分高了,煤粉松散度差,煤粉颗粒易粘结使其细度变粗,影响煤粉的燃烧速度和燃尽率;
煤粉仓也容易起拱,影响喂煤的均匀性。
生产实践证明,人窑煤粉水分控制≤1.0%对水泥生产和操作都是有利的。
9预分解窑的操作特点
9.1
烧成带较长,窑速很快
预分解窑烧成带的长度约为窑简体直径的5.0—5.5倍,较其它窑型都长。
又由于人窑生料CaC03分解率一般高达90%左右,因此窑内物料预烧好,化学反应速度加快,所以出现窜料的可能性减少,这为提高窑速创造了良好条件。
正常情况下窑速一般控制在3.0r/min左右。
由于窑速快,窑内料层薄,物料填充率只有7%左右,而且来料比较均匀。
所以熟悉预分解窑的窑操作员普遍反映,这种窑料子好烧,好控制,好操作。
但是必须指出,我国绝大多数的预分解窑,包括早期建成甚至在建的,其L/D为15—16,与预热器窑基本相当。
这使出分解带后的生料温度升到1250℃所需时间为预热器窑的近3倍,约15min左右。
这样,使得已形成的C2S和CaO矿物晶体在较长的过渡带内长大,活性降低,不利于C,S的形成。
为了解决这个问题,德国洪堡公司开发了L/D=10的短窑(我国新疆水泥厂4号窑中4.0m*43m就是这种窑型)。
窑简体的缩短,使过渡带也相应缩短,生料通过过渡带的时间约为6min。
这样刚形成的C2S和刚分解出来的CaO活性很高,有利于C3S的形成和熟料产质量的提高。
由于三通道尤其是四通道燃烧器的广泛应用以及碱性耐火砖质量的提高,为进一步提高烧成温度创造了条件。
窑速也由3.0r/min提高到3.5r/min左右,最高已达4.0r/min,使物料在窑内停留时间相应缩短,从而提高了出过渡带矿物的活性。
烧成温度的提高和窑速的加快,也促进了C3S矿物的形成速率。
而第三代空气梁式篦冷机的广泛应用,使出窑熟料得到急速淬冷,冷却机热回收效率已达73%以上。
所有这些使我国预分解窑的产质量都有很大提高,燃料消耗大大降低,3000t/d以上规模的预分解窑熟料热耗已接近3000kJ/kg。
其热工参数和技术经济指标已达到国际先进水平。
9.2
黑影远离窑头
由于入窑生料CaCO3,分解率很高,窑内分解带大大缩短,过渡带尤其是烧成带相应延长,物料窜流性小,一般窑头看不到生料黑影。
因此看火操作时必须以观察火焰、窑皮、熟料颜色、亮度、结粒大小、带料高度、升重以及窑的传动电流为主。
必须指出,因为窑速快,物料在窑内停留时间只有25min左右,所以窑操作员必须勤观察,细调整,否则跑生料的现象也是经常发生的。
9.3
冷却带短,易结前圈
预分解窑冷却带一般都很短,有的根本没有冷却带。
出窑熟料温度高达1300℃以上,这时熟料中的液相量仍未完全消失,所以极易产生前结圈。
9.4
黑火头短,火力集中
三通道或四通道燃烧器能使风、煤得到充分混合。
所以煤粉燃烧速度快,火焰形状也较为活泼,内流风、外流风比例调节方便,比较容易获得适合工艺煅烧要求的黑火头短、火力集中的火焰形状。
9.5要求操作员有较高的素质
预分解窑人窑生料CaC03有90%左右已经分解,所以生料从分解带到过渡带温度变化缓慢,物料预烧好,进入烧成带的料流就比较稳定。
但由于预分解窑系统有预热器、分解炉和窑3部分,窑速快,生料运动速度就快,系统中若出现任何干扰因素,窑内热工制度就会迅速发生变化。
所以操作员一定要前后兼顾,全面了解系统的情况,对各种参数的变化要有预见性。
发现问题,预先小动用煤量,尽可能少动或不动窑速和喂料量,以避免系统热工制度的急剧变化,要做到勤观察、小动作,及时发现问题,及时排除。
10预分解窑风、煤、料和窑速的合理控制
操作好预分解窑,风、煤、料和窑速的合理匹配是至关重要的。
喂多少料,需要烧多少煤,也就决定了系统排风量。
根据窑内物料的煅烧状况,窑速该打多快,窑操作员必须随时做到心中有数。
10.1窑和分解炉风量的合理分配
窑和分解炉用风量的分配是通过窑尾缩口和三次风管阀门开度来实现的。
正常生产情况下,一般控制氧含量在窑尾为1%左右,在炉出口为3%左右。
如果窑尾O:
含量偏高,说明窑内通风量偏大。
其现象是窑头窑尾负压比较大,窑内火焰较长,窑尾温度较高,分解炉用煤量增加时炉温上不去,而且还有所下降。
出现这种情况,在喂料量不变的情况下,应关小窑尾缩口闸板开度(当三次风管阀门开度较小时也可开大三次风阀门,以增加分解炉燃烧空气量,也有利于降低系统阻力)。
与此同时,相应增加分解炉用煤量,以利于提高人窑生料CaCO3分解率。
如果窑尾O2含量偏低,窑头负压小,窑头加煤温度上不去,说明窑内用风量小,炉内用风量大。
这时应适当关小三次风管阀门开度。
需要时增加窑用煤量,减小分解炉用煤量。
10.2窑和分解炉用煤分配比例
分解炉的用煤量主要是根据人窑生料分解率、C5和C1出口气体温度来进行调节的。
如果风量分配合理,但分解炉温度低,人窑生料分解率低,C5和C1出口气体温度低,说明分解炉用煤量过少。
如果分解炉用煤量过多,则预分解系统温度偏高,热耗增加,甚至出现分解炉内煤粉燃尽率低,煤粉到C5内继续燃烧,致使在预分解系统产生结皮或堵塞。
窑用煤量的大小主要是根据生料喂料量、人窑生料CaCO3分解率、熟料升重和fCaO来确定的。
用煤量偏少,烧成带温度会偏低,生料烧不熟,熟料升重低,fCaO高;
用煤量过多,窑尾废气带人分解炉热量过高,势必减少分解炉用煤量,致使人窑生料分解率降低,分解炉不能发挥应有的作用,同时窑的热负荷高,耐火砖寿命短,窑运转率就低,从而降低回转窑的生产能力。
窑/炉用煤比例取决于窑的转速、L/D及燃料的特性等。
一般情况下,控制在(40%~45%):
(60%—55%)比较理想。
生产规模越大,分解炉用煤量也应按高比例控制。
10.3窑速和窑喂料量成正比关系
回转窑的窑速随喂料量的增加而逐渐加快。
当系统正常运行时,窑速一般应控制在3.0r/min,不过近年来又有提高的趋势,最高已达4.0r/min,这是预分解窑的重要特性之一。
窑速快,窑内料层薄,生料与热气体之间的热交换好,物料受热均匀,进入烧成带的物料预烧好。
如果遇到垮圈、掉窑皮或小股塌料,窑内热工制度稍有变化,增加一点喂煤量,系统很快就能恢复正常;
假如窑速太慢,窑内物料层就厚,物料与热气体热交换差,预烧不好,生料黑影就会逼近窑头,窑内热工制度稍有变化,极易跑生料。
这时即使增加喂煤量,由于窑内料层厚,烧成带温度回升也很缓慢,容易出现短火焰逼烧,产生黄心料,熟料fCaO也高。
同时大量未燃尽的煤粉落人料层造成不完全燃烧,还容易出现大蛋或结圈。
10.4风、煤、料和窑速合理匹配是烧成系统操作的关键
窑和分解炉用煤量取决于生料喂料量。
系统风量取决于用煤量。
窑速与喂料量同步,更取决于窑内物料的煅烧状况。
所以风、煤、料和窑速既相互关联,又互相制约。
对于一定的喂料量