双螺杆挤出机的毕业设计全套图纸44页word资料Word格式文档下载.docx
《双螺杆挤出机的毕业设计全套图纸44页word资料Word格式文档下载.docx》由会员分享,可在线阅读,更多相关《双螺杆挤出机的毕业设计全套图纸44页word资料Word格式文档下载.docx(32页珍藏版)》请在冰豆网上搜索。
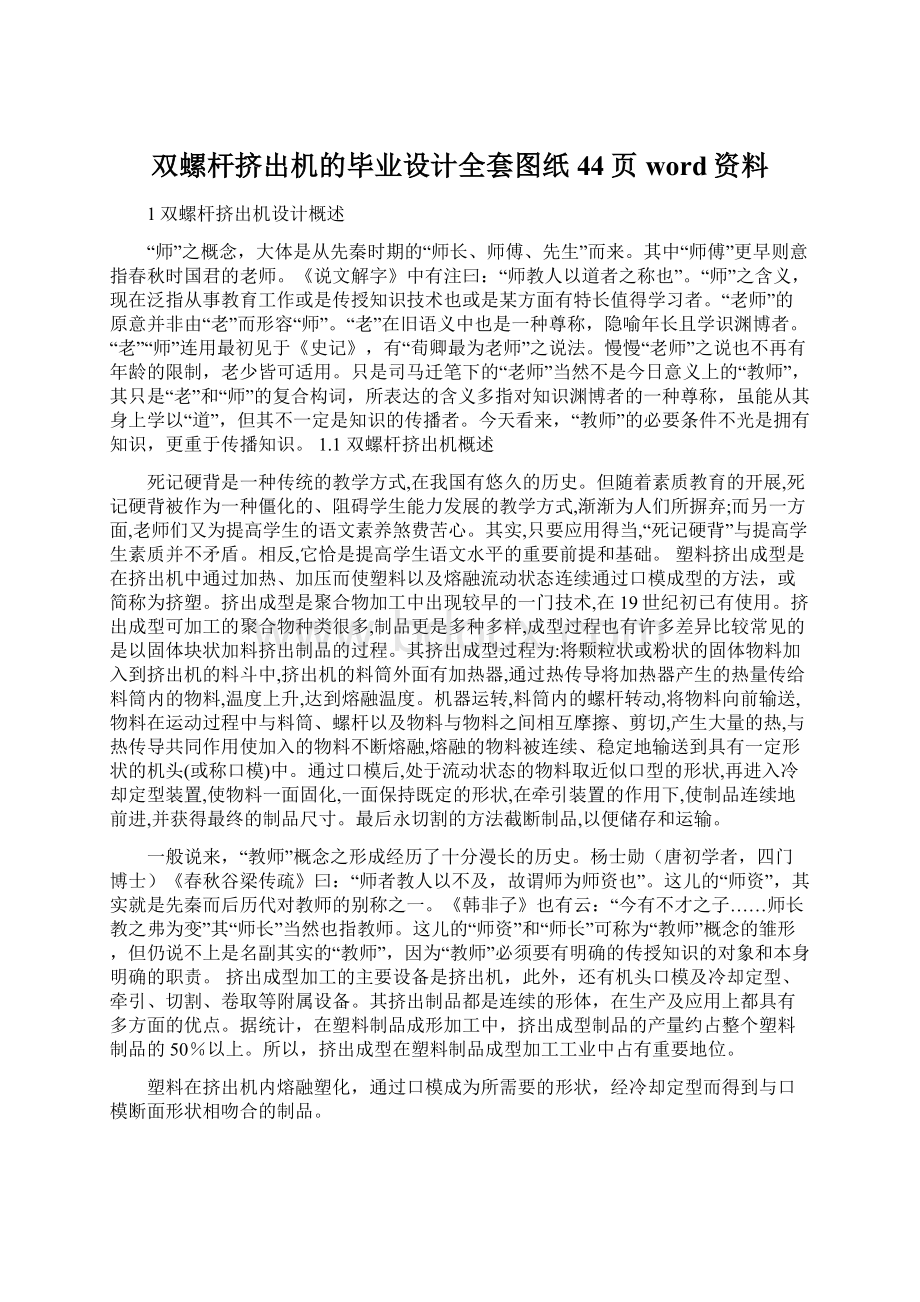
杨士勋(唐初学者,四门博士)《春秋谷梁传疏》曰:
“师者教人以不及,故谓师为师资也”。
这儿的“师资”,其实就是先秦而后历代对教师的别称之一。
《韩非子》也有云:
“今有不才之子……师长教之弗为变”其“师长”当然也指教师。
这儿的“师资”和“师长”可称为“教师”概念的雏形,但仍说不上是名副其实的“教师”,因为“教师”必须要有明确的传授知识的对象和本身明确的职责。
挤出成型加工的主要设备是挤出机,此外,还有机头口模及冷却定型、牵引、切割、卷取等附属设备。
其挤出制品都是连续的形体,在生产及应用上都具有多方面的优点。
据统计,在塑料制品成形加工中,挤出成型制品的产量约占整个塑料制品的50%以上。
所以,挤出成型在塑料制品成型加工工业中占有重要地位。
塑料在挤出机内熔融塑化,通过口模成为所需要的形状,经冷却定型而得到与口模断面形状相吻合的制品。
挤出成型是塑料加工工业中最早的成型方法之一。
早在19世纪初期,挤出机就用于生产铅管、面条。
早期的挤出机是柱塞式的,直到1936年才研制成功电加热的单螺杆挤出机,这就是现代塑料挤出机的起源。
同其他成型方式相比,挤出成型具有以下突出优点。
1.设备成本低,制造容易,因此投资少,见效快,占地面积小,生产环境清洁。
2.生产效率高。
挤出机的单机产量较高。
特别适合于较长的尺寸的制品。
如制造较长的管材,板材、型材、薄膜等,而且产品质量均匀、密实。
其生产效率的提高比其它成型方法快。
3.挤出成型可以实现连续化、自动化生产。
生产操作简单,工艺控制容易,产品质量稳定。
4.可以根据产品的不同要求,改变产品的断面形状。
其产品为管材、棒材、片材、板材、薄膜、电缆、单丝、中空制品及异型材等。
5.应用范围广。
只要改变螺杆及辅机,就能适用于多种塑料及多种工艺过程。
例如,可以加工大多数热塑性塑料及部分热固性塑料,也能用挤出法进行共混改性、塑化、造粒、脱水和着色等。
6.可以进行综合性生产。
挤出机与压延机配合,可以喂料生产压延薄膜,与油压机配合生产各种模压制品。
随着聚合物加工业的发展,作为聚合物的主要加工设备之一的挤出机得到了飞速发展,并以其优异的加工性能得到了越来越广泛的应用。
一套完整的挤出设备由主机和相应的辅机以及其它控制系统组成。
通常这些组成部分统称为挤出机组。
它主要包括挤出系统、传动系统和加热冷却系统及控制系统。
1.挤出系统它由料斗、螺杆和机筒组成,是挤出机工作的核心部分。
其作用是使塑料塑化成均匀的熔体,并在此过程中建立压力,再被螺杆连续、定压、定温、定量地挤出机头。
2.传动系统它由电机、调速装置及传动装置组成。
其作用是驱动螺杆,并保证供给螺杆在工作过程中所需的扭矩和转速。
3.加热冷却系统它由温度控制设备组成。
其作用是通过对机筒进行加热和冷却,保证挤出系统的成型在工艺要求的温度范围内进行。
4.控制系统它主要由电器、仪表和执行机构组成。
其作用是调节控制螺杆的转速、机筒温度、机头压力等。
在挤出成型中,应用得最广的是单螺杆挤出机和双螺杆挤出机。
双螺杆挤出机是在挤出机机筒中并排地安装两根螺杆的一种挤出机,它是在单螺杆挤出机的基础上发展起来的。
最初的双螺杆挤出机是20世纪30年代后期在意大利开发的。
RotertoColombo开发了同向旋转式双螺杆挤出机,CarloPasqutti开发了异向旋转式双螺杆挤出机。
单螺杆挤出机易于加工粒料,对粉料则不易加工。
对那些形状不规则的或是含湿度很大的悬浮料、乳剂料或分子量很高因而粘度很高的料等,实际上无法加工。
单螺杆挤出机对于加入无机填料的适应能力也是差的,且混炼效果较差。
与单螺杆挤出机相比,双螺杆挤出机具有一系列的优点,如双螺杆挤出机可以用在混炼、排气、脱水、造粒粉料直接挤出以及玻璃纤维或其他填料的填充增强改性等方面。
据资料介绍,近年来西欧工业国家的双螺杆挤出机的数量已达到挤出机台数的40%左右。
特别是在成型加工中,应用更多、更广。
例如,在管材和造粒中几乎全部使用双螺杆挤出机,在板材和型材的成型中,双螺杆挤出机约占80-90%。
尤其对RPVC粉料、LDPE塑料的加工,双螺杆挤出机更是具有极大的优越性。
因为其剪切速率较低(主要指异向旋转的双螺杆挤出机)、自洁性好、在机筒中物料停留时间短。
此外,双螺杆挤出机还具有剪切力大、传热面积大、计量准确、回流少、供料性能好、混炼效果好、塑化效果好等优点。
目前,双螺杆挤出机主要用作成型加工、预塑混炼、聚合反应以及废料处理方面。
近几年来,我国在双螺杆挤出机的生产和应用方面同样也都得到了迅速的发展。
目前,双螺杆有许多种类型,其主要可以分为:
1.从螺杆轴线是否平行可分为平行式和锥形式双螺杆;
前者两根螺杆的轴线互相平行,后者两螺杆的轴线相交成一角度。
平行双螺杆挤出机相比较于锥形双螺杆基础机的优点是:
平行双螺杆挤出机具有压延长度较大,压延有强烈的塑化与均化能力的效果,而且螺杆平均直径小,转速较低,因此,平均剪切速率也较低,压延频率高,有效停留时间并不低于锥形螺杆。
2.从两根螺杆的相对位置又可以分为啮合型和非啮合型,啮合型又可以分为部分啮合和全啮合型。
非啮合型的一根螺杆的螺棱不伸到另一根螺杆的螺槽中去,而非啮合型则是两根螺杆的轴线分开的距离小于两根螺杆外半径之和,即一根螺杆的螺棱插到另一根螺杆的螺槽中去。
根据啮合程度(即一根螺杆的螺棱插到另一根螺杆的螺槽中的深浅程度),啮合型又可以分为部分啮合和全啮合型。
3.从螺杆旋转方向的不同,可以分为同向旋转与反向旋转。
顾名思义,同向旋转双螺杆挤出机的两根螺杆的旋转方向相同,异向旋转双螺杆挤出机的两根螺杆的旋转方向相反。
它可以是向内旋转或向外旋转。
1.2挤出机整体方案设计
近年来,双螺杆挤出机得到了迅速的发展,但由于双螺杆挤出机的复杂性和种类的多样性,以及双螺杆理论的不成熟,所以至今还没看到有关双螺杆挤出机参数设计和结构设计的比较系统的文献,因此对双螺杆挤出机的设计更多地只能停留在经验设计的水平上。
当然,经验设计是必须服从挤出工程的基本规律的,所以由此所进行的有关双螺杆挤出机的设计是具有一定的科学性与理论性的。
双螺杆挤出机的应用,都是以机组的的形式出现。
挤出机组包括主机(即通常说的挤出机)、机头和辅机。
因而就双螺杆挤出机的总体设计而言,它可以包括主机(螺杆挤出机)、机头和辅机的设计,也可以单指主机的设计。
因此双螺杆挤出机的设计应当包括双螺杆挤出机类型的确定、整体方案的确定、主要技术参数的确定、挤压系统的设计、传动系统的设计、机头的设计、加料系统的设计以及双螺杆挤出机辅助系统的设计等。
1.2.1开式设计和闭式设计的选择
所谓开式设计,一般指双螺杆挤出机的挤压系统、冷却加热系统都裸露在外面,这种设计的优点是各部分出现故障时,检查、维修及拆装比较方便,也一目了然。
啮合同向双螺杆挤出机大多采用这种设计。
所谓闭式设计,其挤压、冷却加热系统的外面都有罩子,其余各部分有时也封闭起来。
这种设计看上去外形比较整齐,但检修不太方便。
所以本设计中采用开式设计。
1.2.2一阶机和二阶机的选择
所谓一阶机,是指主机只有一个挤压系统,包括一套螺杆、机筒和传动箱;
而二阶机是指主机有两个挤压系统,包括两套螺杆、机筒和传动箱,柔性串起来组成主机。
就目前见到、用于成型制品的双螺杆挤出机组的主机多是一阶的,如啮合平行异向双螺杆挤出机和锥形双螺杆挤出机。
用于配混料造粒的啮合同向双螺杆挤出机有的情况下设计成二阶的,其第一阶用来塑化、混合物料,第二阶用来建压、挤出造粒。
本设计中以采用一阶式为宜。
1.2.3整体式和积木式的选择
一般啮合异向旋转的双螺杆挤出机(也有例外)和锥形双螺杆挤出机都是整体式,即其各大组成部分(螺杆、机筒、减速箱)在使用中不再拆开并进行重新组合安装。
国外流行的啮合同向双螺杆挤出机绝大多数都设计成积木式的,即其机筒、螺杆有若干组件组成,可根据使用需要进行重新组合安装。
也有的厂家生产的双螺杆挤出机,除了其机筒、螺杆是组合式外,其扭距分配器和齿轮箱做成积木式,通过更换扭距分配器可以将双螺杆挤出机改变成异向旋转或同向旋转;
去掉扭距分配器,其齿轮箱还可以与单螺杆挤压系统相接,组成单螺杆挤出机。
本设计中采用整体式设计。
1.2.4封闭式机筒与剖分式机筒的选择
双螺杆挤出机的机筒有的是整体式的,有的是由若干段组成,但机筒均不能打开分成两段,它们是封闭的。
因此,要想了解挤出过程中物料沿螺杆的输送、混合、反应情况,只有停转将机筒通过水骤冷,然后把螺杆抽出来才能看清楚。
这样很不方便,有时为了会破坏过程反应的原貌。
为了克服上述缺点,人们把双螺杆挤出机的机筒做成剖分式,停车冷却后靠液压系统或手动机械打开,观察取样,进行研究。
挤出机再工作前,再靠液压系统或手动机械合起来。
本设计采用封闭式设计。
1.2.5挤压系统的选择
对某些大型同向双螺杆挤出机造粒机组(有时是挤出片材挤出机组),为了高效、节能、精确地控制挤出机熔体的压力以保证制品的尺寸精度,在挤压系统末串接熔体齿轮泵,由双螺杆完成塑化、混炼,由齿轮泵建立、控制挤出压力。
串联齿轮泵后会给整个双螺杆主机得整体设计带来了重大影响。
所以本设计中没有使用串接齿轮泵的设计。
另一个影响双螺杆挤出机整体方案确定的是在某些机组上将要采用的加料系统。
一般双螺杆挤出机大多采用计量加料,对大多数情况下得双螺杆挤出机(如啮合异向双螺杆挤出机和锥形双螺杆挤出机),其计量加料系统对挤出机组整体设计不会有多大影响,但对某些没有多组分加料系统的配混料啮合同向双螺杆挤出机,将会有多个加料口和加料装置,它们得联合使用和布置将对双螺杆挤出机的整体布置带来影响。
2挤出系统设计
双螺杆挤出机的挤压系统是双螺杆挤出机的核心部分。
其作用是把加入的固体物料熔融塑化、混合,为口模提供定温、定压、定量的容体,并将在这一过程中产生的气体排除,最后通过口模,得到合乎质量要求的制品。
双螺杆挤出机的挤压系统主要由螺杆、机筒组成。
因此,双螺杆挤出机挤压系统的设计实际上就是螺杆、机筒的设计。
2.1螺杆设计
螺杆设计包括螺杆参数的确定,螺杆结构设计和螺杆材质选择等。
螺杆设计的核心问题就是设计出的螺杆应具有优异的混合能力和其它的特定能力(如脱挥发分)。
螺杆参数包括螺杆直径、螺杆长径比、螺杆导程(升角)、螺纹和螺槽的断面形状、螺棱厚度、四个间隙等。
备注:
具体的设计过程由本组成员张伟俊同学负责设计,有关设计数据请参照张伟俊同学的设计过程。
2.2机筒设计
机筒和螺杆共同组成了挤出机的挤压系统,完成对塑料的固体输送、熔融和定压定量输送作用。
机筒的结构形式关系到热量传送的稳定性和均匀性。
并且对于一些新型的挤压系统来说,机筒在加料段上的结构形式也影响到固体输送效率。
机筒的机械加工和使用寿命也影响到整个挤压系统的工作性能。
因此,机筒在挤压系统中是仅次于螺杆的重要零件。
普通机筒的结构类型有整体式,分段式和双金属式。
一般的异向旋转双螺杆挤出机采用的是整体式机筒。
而本次设计中的螺杆采用的是整体式,因此机筒也相应的采用整体式机筒。
具体的设计过程由本组成员董武林同学负责设计,有关设计数据请参照董武林同学的设计过程。
3传动系统设计
双螺杆挤出机的传动系统是双螺杆挤出机的重要组成部分。
它的重要性表现在它所完成的功能在双螺杆挤出机中致关重要,也表现在其设计、制造难度和成本在整台机器中占的比重。
双螺杆挤出机传动系统的作用是在设定的工艺条件下,向两根螺杆提供合适的转速范围、稳定而均匀的速度、足够且均匀相等的扭矩(功率)。
并能承受完成挤出过程所产生的巨大的螺杆轴向力。
双螺杆挤出机的传动系统主要由驱动电机(联轴器)、齿轮箱(包括扭矩分配和减速部分)等组成。
与单螺杆挤出机相比,双螺杆挤出机传动系统的设计、制造要困难的多。
这是因为,一方面,双螺杆挤出机比单螺杆挤出机承受的扭矩要大得多,而且这么大的扭矩是在有限的中心距内传递,且扭矩的传递和减速交织在一起的。
另一方面,挤出过程在螺杆末端产生的轴向力很大,该轴向力需要止推轴承来承受。
按一般情况,轴向力越大,所需的止推轴承的外径越大,但在两螺杆中心距已限定的情况下,不可能任意选择大外径的止推轴承,这就要求另想办法——譬如采用止推轴承串来解决这个问题。
但这是比较困难的。
另外抵消齿轮传动的径向力,防止螺杆弯曲,提高齿轮的承载能力和传动精度,也是双螺杆传动设计不同于单螺杆挤出机之处。
双螺杆传动箱的散热和润滑也比单螺杆挤出机重要、复杂得多。
3.1主驱动电动机选型
双螺杆挤出机所用电机的选择如下。
双螺杆挤出机中常用的电机有直流电机、交流变频调速电机、滑差电机、整流子电机等。
其中以直流电机和交流变频调速电机用的最多。
直流电机系统:
可实现无级调速,且调速范围宽,启动较平稳。
以国产Z2系列电机为例,当改变电枢电压时,其转速可自同步转速(1500r/min)往下调1:
8;
当改变激磁电压时,转速可往上调1:
2,因此其最大调速范围可达1:
16。
图2.1所示为直流电机的外特性曲线。
由图可以看出改变电枢电压时可以得到恒扭矩调速:
改变激磁电压时可以得到恒功率调速,此时随着转速升高其功率不变,但扭矩相应地减少。
但国产的Z2、Z3系列直流电机,在其转速低于(100~200)r/min时,工作不稳定,而且这时电机冷却风扇冷却性能下降。
20世纪80年代以后生产的Z4系列电机则比Z2、Z3系列直流电机性能好得多,其低速性能稳定,因而在双螺杆挤出机中得到广泛采用。
图3.1直流电机外特性曲线
根据图3.1可知,选用功率为55KW的直流电动机已可以满足需要,所以本设计中所采用的主驱动电动机型号为Z4-180-41,功率为55KW,额定电压为440V,转速为1510r/min,并带有冷却鼓风机和热保护装置,采用三相全控桥双闭环无级调速,另外还带有测速发电机。
3.2减速箱设计
双螺杆挤出机的传动箱由两大部分即减速部分和扭矩分配部分组成。
这两部分的功能虽有不同,但它们紧密联系,有时还相互制约。
根据目前流行的结构看,其设计布置大致有两种方案,一种是将减速部分和扭矩分配部分很明显的分开,即所谓的分离式;
另一种是将二者和在一起。
在本设计中,选用分离式,因螺杆的转速范围为40~400r/min,而电动机的转速为1510r/min,所以要求减速箱的总传动比为:
1:
1510/144=1:
10.5。
根据所选电机的功率、转速、电机伸出端的直径和减速箱轴的直径选择联轴器的型号为
,减速箱通过弹性柱销联轴器与直流电动机相连,采用三级斜齿传动,使总传动比与所要求的传动比吻合。
另外,减速箱润滑油采用150号极压齿轮油,一次加油量为25升。
为了防止油量过热,箱内悬有蛇形冷却管,冷却方式为水循环式。
具体设计及校核略。
3.3分配箱设计
在设计过程中,实现规定的螺杆转速(范围)、扭矩均匀分配、轴承合理布置的前提下,通过传动方案的确定和结构设计,采取措施,降低齿轮载荷,抵消或减少传动齿轮的径向载荷,传递更大的功率和轴向力,提高轴承的寿命,装配维修方便。
设计、加工的难点在于螺杆中心距限定的狭少的空间。
因而必须调动一切可能的手段,寻找特殊的结构形式、材料和热处理工艺来实现上述的目标。
与锥形双螺杆挤出机相比,平行双螺杆挤出机螺杆尾部空间比较小,不能平行地放下两根传动轴。
本设计中两螺杆异向旋转,为达到这一目的,大致设想如下:
动力由减速箱输出轴齿轮输入到分配箱的一根轴上,这根轴的齿轮齿数与主轴相等,且与一根主轴外啮合同时与大齿轮内啮合,从而带动与此大齿轮内啮合的另一主轴转动。
这样,两根主轴以相同的角速度异向旋转,同时也使得分配箱尾部空间增大。
双螺杆挤出机分配箱的设计所涉及的问题很多,要想设计好分配箱,除了应具有扎实的机械设计理论和知识外,更需要有丰富的实践设计经验,下面仅以双螺杆挤出机中目前最流行的分离式传动箱的结构设计中的几个主要问题进行讨论。
3.3.1分配箱的总体结构设计
⒈双螺杆中心距与分配箱设计中齿轮、轴与轴承之间的关系
对于全啮合双螺杆挤出机,一旦两根轴的外径、根径(或螺槽深度)初步确定,则为两螺杆提供转速和扭矩的传动箱中与两螺杆相连的输出轴之间的中心距也就确定了。
现以一般分离式传动箱轴承、齿轮、轴之间的几何关系,来讨论传动箱结构参数之间的关系。
图3.2表示出了分离式传动系统齿轮、轴、轴承的布置。
图3.2分离式传动系统齿轮、轴、轴承布置
支持两输出轴的径向轴承有如下关系:
…………………………3.1
一根轴的外径与另一根轴上所装齿轮的外径之间应满足以下关系:
…………………………3.2
齿顶圆直径:
…………………………3.3
或
…………3.4
以上各式中
Amin—双螺杆最小中心距
A—双螺杆实际中心距
DZC—所选径向轴承外径
dZ—螺杆驱动轴直径
Δ1—两根螺杆上两个径向轴承外径之间的径向间隙
Δ2—一根螺杆驱动轴外径与另一根螺杆驱动轴上齿轮顶圆之间的间隙
da—赤顶圆直径
m—齿轮模数
Z1—齿数
ha*—齿顶高系数
X1—齿轮变位系数
ΔY—齿顶高变位系数
由以上关系可见,中心距A对其它几何参数的限制,特别是对齿轮承载能力的关键参数m、Z的限制。
2、双螺杆中心距的确定与齿轮参数的选择
由同组的同学已初选定了螺杆直径及螺槽深度,进而给出了双螺杆中心距的可选范围,但尚不能将中心距最后确定。
道理很明显,因为双螺杆直径、槽深、中心距的设计是从双螺杆挤出机的主要参数、规格和螺杆几何学出发的,而传动箱齿轮传动的设计要考虑齿轮几何学及受力、结构设计,二者不一定完全一致。
对分离式的传动箱的设计而言,一般是根据初步的受力分析,算出轴径再结构化,同时根据轴承系列规格圆整(对轴承寿命与轴径强度核算平衡),进而轴承组合设计。
根据式3.1先确定出两螺杆驱动轴的最小中心距Amin(即两螺杆最小中心距)。
式中Δ1主要考虑轴承定位及箱体的结构,一般取
,并随轴承直径的增大而适当增大。
然后根据式3.2初定扭矩分配齿轮的齿顶圆直径da。
而驱动轴的轴径dZ主要受所选外径dZC的限制,一般取
。
确定间隙Δ2时主要考虑一根轴上的齿顶圆与另一根轴径不发生干涉的情况下,使轴径最大,这样螺杆驱动轴可获得最大刚度和强度。
在初定的da范围内,根据传递功率(扭矩)对齿轮进行强度计算(校核其接触强度和弯曲强度),最后确定出齿轮参数m、Z、X1。
并在强度允许的范围内对dZ进行调整,同时根据实际情况对初定的Amin进行适当调整、增大。
经反复优选后,得到较佳的齿轮参数及所对应的合适中心距。
这样的设计过程可以在尽可能小的双螺杆中心距下进行,以求设计出较大输出扭矩的传动箱,一旦传动箱的中心距确定,再反过来最后确定双螺杆的外径和槽深。
在以上设计中,要对扭矩分配齿轮进行强度计算,这不可避免地用到所谓齿宽系数(即齿轮轴向宽度与分度圆直径之比,
)。
由于扭矩分配齿轮径向尺寸受到限制,而又要传递比一般传动中大得多的扭矩,为了满足强度要求,除采用优质材料和提高加工精度外,还有一个可行的途径,就是增加齿宽系数,即增加齿宽。
有的资料介绍,齿宽的取值范围可为
,或
(A为螺杆中心距,m为模数)。
但齿宽系数也不能过大,否则,若传动箱的加工精度不高和轴的刚度不够,实际上沿齿宽两齿不会均匀接触,反而对齿轮的实际承载不利。
由上述的讨论可以看出,在齿轮箱的设计中,采用双啮合齿轮传动的效果要比在齿宽系数上打主意要好得多,采用双啮合传动可大大降低齿轮载荷。
这里要附带讨论一个问题,即关于用一个传动箱来适应不同螺杆直径和螺槽深度的双螺杆挤压系统的问题。
前以述及,在双螺杆中心距一定的情况下,根据挤出过程和加工物料的需要以及双螺杆挤出机的发展趋势,可以设计成普通型、深糙型和浅槽型几种类型的双螺杆。
与传动箱的设计、制造和使用联系起来,为减小设计、制造差别不大但规格繁多的传动箱,提高效益,提高系列化水平,可以在同一个中心距下,设计制造出具有最大输出扭矩的齿轮传动箱,分别与普通型、深槽型和浅槽型挤出机的挤压系统相配,配套出中心距相等、螺干直径、螺槽深度不等的三种规格的双螺杆挤出机,以适应用户对不同规格和类型的双螺杆挤出机的需求。
这是一种经济的、减小设计制造传动箱工作量的有效方法。
这些方法早已在国外某些著名双螺杆挤出机生产厂家得到采用。
在本设计中齿轮的材料采用40Cr合金,轮齿表面经调质处理。
下面将对其进行有关的计算及设计。
3.3.2齿轮轴的设计
<
一>
齿轮设计
1>
齿轮传动设计参数的选择
1力角α的选择
由机械原理可知,增大压力角α,轮齿的齿厚及节点处的齿廓曲率半径亦皆随之增加,有利于提高齿轮传动的弯曲强度及接触强度。
为了设计、制造、检验及使用的方便,GB1356—88中对一般用途的齿轮传动规定的标准压力角α=200另外我国航空齿轮传动标准还规定了α=250的标准压力角。
但增大压力角并不一定都对传动有利。
对重合度接近2的高速齿轮传动,推荐采用齿顶高系数为1~1.2,压力角为160~80的齿轮,这样做可增加轮齿的柔性,降低噪声和动载荷。
⑵齿数的选择
若保持齿轮传动的中心距不变,增加齿数,除能增大重合度、改善传动的平稳性外,还可减小模数,降低齿高,因而减少金属切削量,节省制造费用。
另外,降低齿高还能减小滑动速度,减少磨损及减小胶合可能性。
但模数小了,齿厚随之减薄,则要降低轮齿的弯曲强度。
不过在一定的齿数范围内,尤其是当承载能力主要取决于齿面接触强度时,以齿数多一些为好。
⑶齿宽系数Φd的选择
载荷一定时,齿宽系数大,可减少齿轮的