杯座模具设计范本.docx
《杯座模具设计范本.docx》由会员分享,可在线阅读,更多相关《杯座模具设计范本.docx(22页珍藏版)》请在冰豆网上搜索。
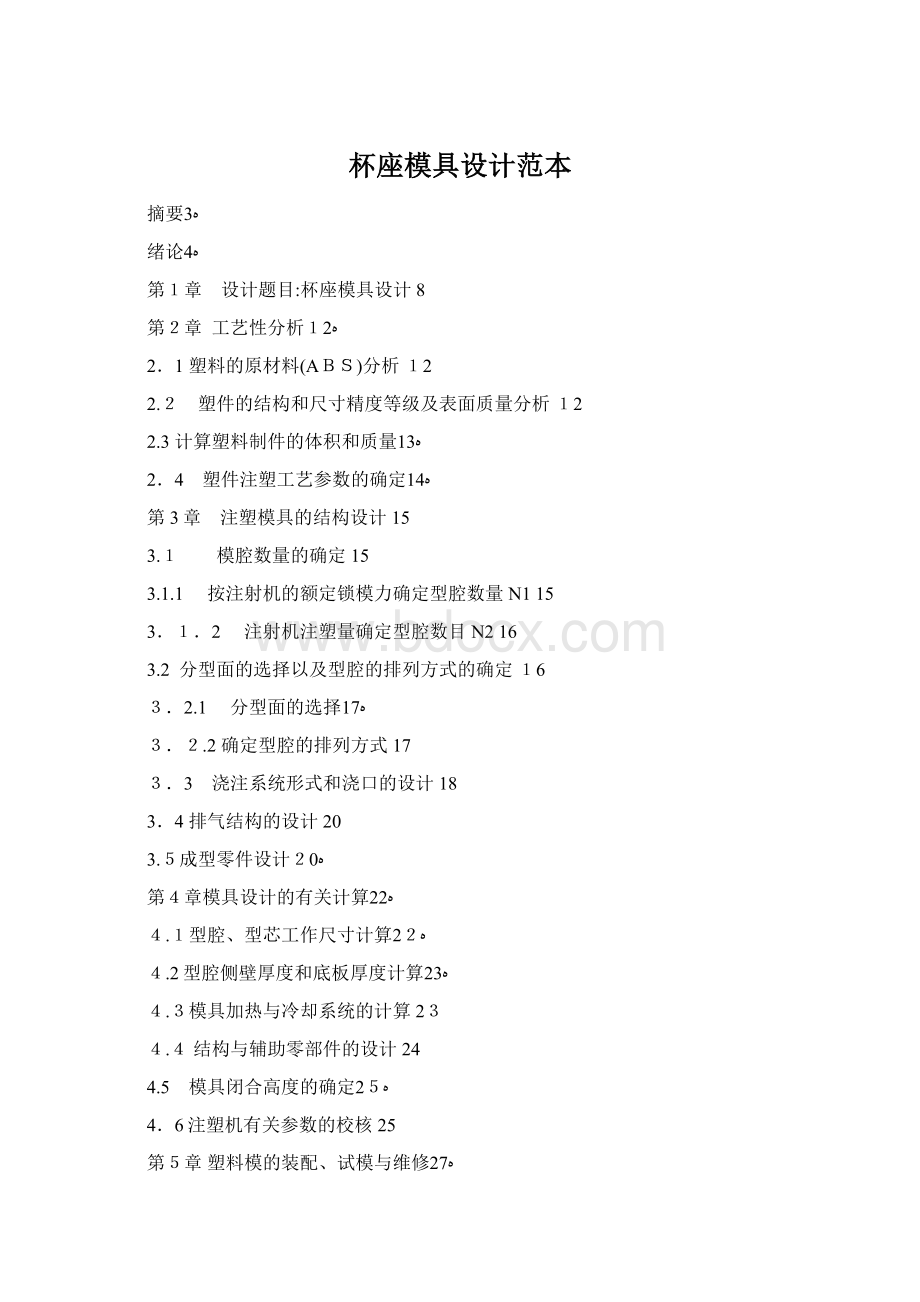
杯座模具设计范本
摘要ﻩ3
绪论ﻩ4
第1章 设计题目:
杯座模具设计8
第2章工艺性分析ﻩ12
2.1塑料的原材料(ABS)分析12
2.2 塑件的结构和尺寸精度等级及表面质量分析12
2.3计算塑料制件的体积和质量ﻩ13
2.4 塑件注塑工艺参数的确定ﻩ14
第3章 注塑模具的结构设计15
3.1 模腔数量的确定15
3.1.1 按注射机的额定锁模力确定型腔数量N115
3.1.2 注射机注塑量确定型腔数目N216
3.2分型面的选择以及型腔的排列方式的确定16
3.2.1 分型面的选择ﻩ17
3.2.2确定型腔的排列方式17
3.3 浇注系统形式和浇口的设计18
3.4排气结构的设计20
3.5成型零件设计ﻩ20
第4章模具设计的有关计算ﻩ22
4.1型腔、型芯工作尺寸计算ﻩ22
4.2型腔侧壁厚度和底板厚度计算ﻩ23
4.3模具加热与冷却系统的计算23
4.4结构与辅助零部件的设计24
4.5 模具闭合高度的确定ﻩ25
4.6注塑机有关参数的校核25
第5章塑料模的装配、试模与维修ﻩ27
5.1模具装配27
5.2试模ﻩ27
5.3试模可能产生的问题及改善措施ﻩ28
5.3.1粘着模腔ﻩ28
5.3.2粘着模芯28
5.3.3粘着主流道ﻩ29
5.3.4成型缺陷29
5.3.5调整措施ﻩ30
第6章绘制模具总装图31
第7章 机械加工工艺过程卡32
第8章用Pro/E画图的过程36
8.1用Pro-E画杯座零件的过程36
8.2用Pro-E画杯座模具的过程36
8.2.1:
加载参照模型ﻩ36
8.2.2:
成型零件设计36
8.2.3:
浇注系统设计及开模36
8.2.4:
模架及其他模具零件设计ﻩ37
8.2.5:
模具元件后期处理ﻩ37
总结ﻩ38
致谢39
参考文献40
第1章设计题目:
杯座模具设计
零件图:
设计要求:
1.材料
2.生产批量
3.未注公差取MT5级精度
杯座模具工艺方案分析
可选方案
方案分析
结论
分 型面
取A-A面作为分型面,它位于零件截面最大的部位,此分型面是一个曲面,且分型线并不是零件的轮廓曲线
合理
型腔布局与浇注系 统
采用一模一件,可以降低模具成本,但不能适应大批量生产的需求,点浇口上端进料,容易保证零件质量。
不合理
一模四件对称分布,虽然模具尺寸增大,制造成本有所提高,但生产效率较高,适应大批量生产的需要,点浇口上端进料容易保证零件质量。
合理
推出结构
虽然塑件包紧动模型芯的力不是很大,但因塑件壁很薄,采用顶杆推出容易将塑件顶变形,甚至破坏塑件
不合理
将顶杆作成锥面,增大顶出部分的接触面积,可以有效地避免顶出时塑件的变形。
合理
第2章 工艺性分析
2.1塑料的原材料(ABS)分析
(1)吸湿性强。
成型前须充分干燥要求其含水量小于1%,对于表面光泽要求较高的制品,需长时间干燥。
(2)流动性较好(溢边值为0.04mm左右)易于充模,粘度对剪切速率较敏感,同时还与注射温度和注射压力有关,其中注射压力影响较为显著,因此提高流动性要从提高注射压力入手。
(3)成型难度大,须采用较高的料温和模温。
对于耐热抗冲击性和中抗冲击性制件,应在允许的范围内料温取较大值。
(4)精度对之制件影响较大,有破坏ABS橡胶相的倾向,通常ABS在250℃左右变色,270℃开始分解。
(5)若制件精度要求较高模温宜采取50~60℃,若制件表面要求具有光泽,模温宜取60~80℃,我们的线圈骨架采用60℃。
(5)注射压力应比聚苯乙烯较大,采用螺杆式注塑机料温可取160~220℃,注射压力可取70~90MPa。
(6)模具设计过程中注意事项,浇注系统流动阻力应尽可能小,浇口位置及形式应合理并能防止熔接痕的产生,同时要考虑模具制造的经济性和加工的合理性。
2.2塑件的结构和尺寸精度等级及表面质量分析
从该制品的零件图可知;形状,结构对制件脱模要求较高,但对尺寸大小,产品精度和表面质量要求都不高。
此零件壁薄且深,斜度比较大,虽然总体尺寸不大但相对较高,无特殊尺寸要求,零件表面要求较光滑。
(1)成型制件的尺寸大小主要取决于塑料原料的流动性和注射时的压力在一定的设备和工艺条件下,流动性较好的塑料品种可以成型较大的制件,塑料ABS的流动性能较好,适于成型较大的制件。
在这里杯座注塑模具的尺寸较小,注塑时的压力要求不太大,一般的注塑压力就能满足。
(2)制品的精度等级;塑料制件的尺寸精度主要取决于塑料收缩率的波动和模具制造误差,此处塑料件未注公差,由于该制件的原材料为ABS,而ABS的制件公差等级较低为MT5级,该塑件的精度等级较低。
受模具活动部分的影响,取公差值和附加值之和,MT2级取0.05,MT3-5级取0.1。
(3)制品的表面质量;塑料制件的精度等级较低,我们所要获得的制件对制品的表面质量除要求无缺陷,毛刺,无特殊要求,一般的模具制造工艺和注塑工艺就能满足要求。
(4)制品的形状结构;制品的壁厚均匀为3mm。
符合ABS的最小壁厚原则,在制件的交叉处的壁厚较小(0.5mm),在模具的设计和加工过程中要特别注意,防止出现缺陷,由于制件的尺寸较小,ABS的强度较大不需增设加强筋。
2.3计算塑料制件的体积和质量
计注塑模具的结构设计
注塑模的结构设计主要包括:
分型面的选择、模具型腔数目的确定、型腔的排列方式、冷却水道布局、模具工作零件的结构设计、侧向分型与抽芯机构的设计、推出机构的设计等内容。
3.1模腔数量的确定
塑件的生产属大批量生产,宜采用多型腔注塑模具,其型腔个数与注塑机的塑化能力,最大注射量以及合模力等参数有关,此外还受制件精度和生产的经济性等因素影响,有上述参数和因素可按下列方法确定模腔数量;
3.1.1 按注射机的额定锁模力确定型腔数量N1
N1=×-
其中:
F 注塑机的锁模力N
PC型腔内的平均压力mpa
A 每个制件在分型面上的面积(m㎡)
B 流道和浇道在分型面上的投影面积(m㎡)
B在模具设计前为未知量,根据多型腔模具的流动分析B为(0.2~0.5),常取B=0.35,熔体内的平均压力取决于注射压力,一般为25~40mpa实际所需锁模力应小于选定注塑机的名义锁模力,为保险起见常用0.8F则
N1===4.7(个)
分析方案:
(一):
采用一模一件,可以降低模具成本,但不能适应大批量生产的需求,点浇口上端进料,容易保证零件质量。
(二):
一模四件对称分布,虽然模具尺寸增大,制造成本有所提高,但生产效率较高,适应大批量生产的需要,点浇口上端进料容易保证零件质量。
故型腔设计应选择一模四件。
3.1.2 注射机注塑量确定型腔数目N2
N2=(G-C)/V
其中:
G 注射机的公称注塑量(cm3)
V单个制件体积 (cm3)
C流道和浇口的总体积(cm3)
生产中每次实际注塑量应为公称注塑量的0.75~0.45倍,取0.7倍计算,同时流道和浇道的体积为未知量,据统计每个制品所需浇注系统是体积的0.2~1倍,现取C=0.4则
N2===
=4.7(个)
从以上讨论可以看到模具的型腔个数必须取N1,N2中的较小值,在这里可以选取的个数是1,2,3,4个,考虑的制件的取出和模具的开模等情况,以及模具的主流道长度最好小于60mm,以防止因为注塑压力的降低而带来的制件充型不足等缺陷。
我们所设计的杯座模具采用一模四腔的方案,即
N=4
3.2 分型面的选择以及型腔的排列方式的确定
3.2.1分型面的选择
该塑件为杯座,表面无特殊的要求,取A-A面作为分型面,它位于零件截面最大的部位,此分型面是一个曲面,且分型线并不是零件的轮廓曲线。
故分型面选择如下图所示的A-A分型面:
3.2.2确定型腔的排列方式
本塑件在设计时采用一模四腔的设计方案,即综合考虑模具的开模行程较短,注塑机有足够的开模空间,浇注系统符合原则(主流道的长度小于60mm),模具结构简单以及制件精度符合图纸要求(这里模具的精度等级图纸无要求,ABS的未注公差等级为MT5)以制件生产的经济性,可采用下图所示的型腔排列方式和分型面选择。
3.3浇注系统形式和浇口的设计
(1)主流道设计。
根据设计手册查得XS-ZY-125注塑机喷嘴有关尺寸:
喷嘴前端孔径:
d=4㎜;
喷嘴前端球面半径:
R=12㎜;
根据模具主流道与喷嘴关系:
R=R+(1~2)㎜
d=d+(0.5~1)㎜
取主流道球面半径R=13㎜;
取主流道小端直径d=4.5㎜;
主流道截面形状设计为椭圆形,可将主流道出料端设计为半径R=5㎜的圆弧过渡。
主流道的末端可开设冷料穴,深度约取4~5㎜,主流道表壁的表面粗糙度应小于0.32~0.63m.
(2)分流道设计。
分流道的形状及尺寸,应根据塑件的体积、壁厚、形状的复杂程度,注塑速度、分流道长度等因素来确定。
根据型腔的排列方式可知分流道的长度较短,为便于加工起见,选用截面形状为半圆形的分流道,查表得R=4㎜。
(3)浇口设计。
根据塑件的成型要求及型腔排列方式,选用点浇口较为理想,为四点浇口,查表6-6得,点浇口直径d0.8-1.3mm,点浇口长度l.0mm,试模时修正。
浇口亦称进料口,是连接分流道与型腔的通道,除直接浇口外,它是浇注系统中截面最小的部分,但却是浇注系统的关键部分,浇口的位置、形状及尺寸对塑件性能和质量的影响很大。
浇口可分为限制性和非限制性浇口两种。
我们将采用限制性浇口。
限制性浇口一方面通过截面积的突然变化,使分流道输送来的塑料熔体的流速产生加速度,提高剪切速率,使其成为理想的流动状态,迅速面均衡地充满型腔,另一方面改善塑料熔体进入型腔时的流动特性,调节浇口尺寸,可使多型腔同时充满,可控制填充时间、冷却时间及塑件表面质量,同时还起着封闭型腔防止塑料熔体倒流,并便于浇口凝料与塑件分离的作用。
从图中可看出,我们采用的是点浇口。
点浇口又称针状浇口。
点浇口一般开设在分型面上,塑料熔体于型腔的底面充模,其截面形状多为矩形狭缝,调整其截面的厚度和宽度可以调节熔体充模时的剪切速率及浇口封闭时间。
浇口的长度很短,不超过其直径,所以脱模后塑件上的浇口残痕不明显,不需要再修正浇口痕迹。
这种浇口被广泛采用,但是采用这种浇口时,常常要在模具上增加一分型面,以便浇口凝料脱模。
具体到这套模具,其浇口形式及尺寸如图所示。
浇口各部分尺寸都是取的经验值。
实际加工中,是先用圆形铣刀铣出直径为Φ4的分流道,再将材料进行热处理,然后做一个铜公(电极)去放电,用电火花打出这个浇口来的。
根据塑件的成型要求及型腔排列方式,选用点浇口较为理想,为四点浇口,查表6-6得,点浇口直径d为0.8-1.3mm,点浇口长度为l.0mm,试模时修正。
(4)冷料穴的设计。
在完成一次注射循环的间隔,考虑到注射机喷嘴和主流道入口这一小段熔体因辐射散热而低于所要求的塑料熔体的温度,从喷嘴端部到注射机料筒以内约10-25mm的深度有个温度逐渐升高的区域,这时才达到正常的塑料熔体温度。
位于这一区域内的塑料的流动性能及成型性能不佳,如果这里温度相对较低的冷料进入型腔,便会产生次品。
为克服这一现象的影响,用一个井穴将主流道延长以接收冷料,防止冷料进入浇注系统的流道和型腔,把这一用来容纳注射间隔所产生的冷料的井