基于plc的燃油锅炉控制系统设计方案说明书Word格式文档下载.docx
《基于plc的燃油锅炉控制系统设计方案说明书Word格式文档下载.docx》由会员分享,可在线阅读,更多相关《基于plc的燃油锅炉控制系统设计方案说明书Word格式文档下载.docx(32页珍藏版)》请在冰豆网上搜索。
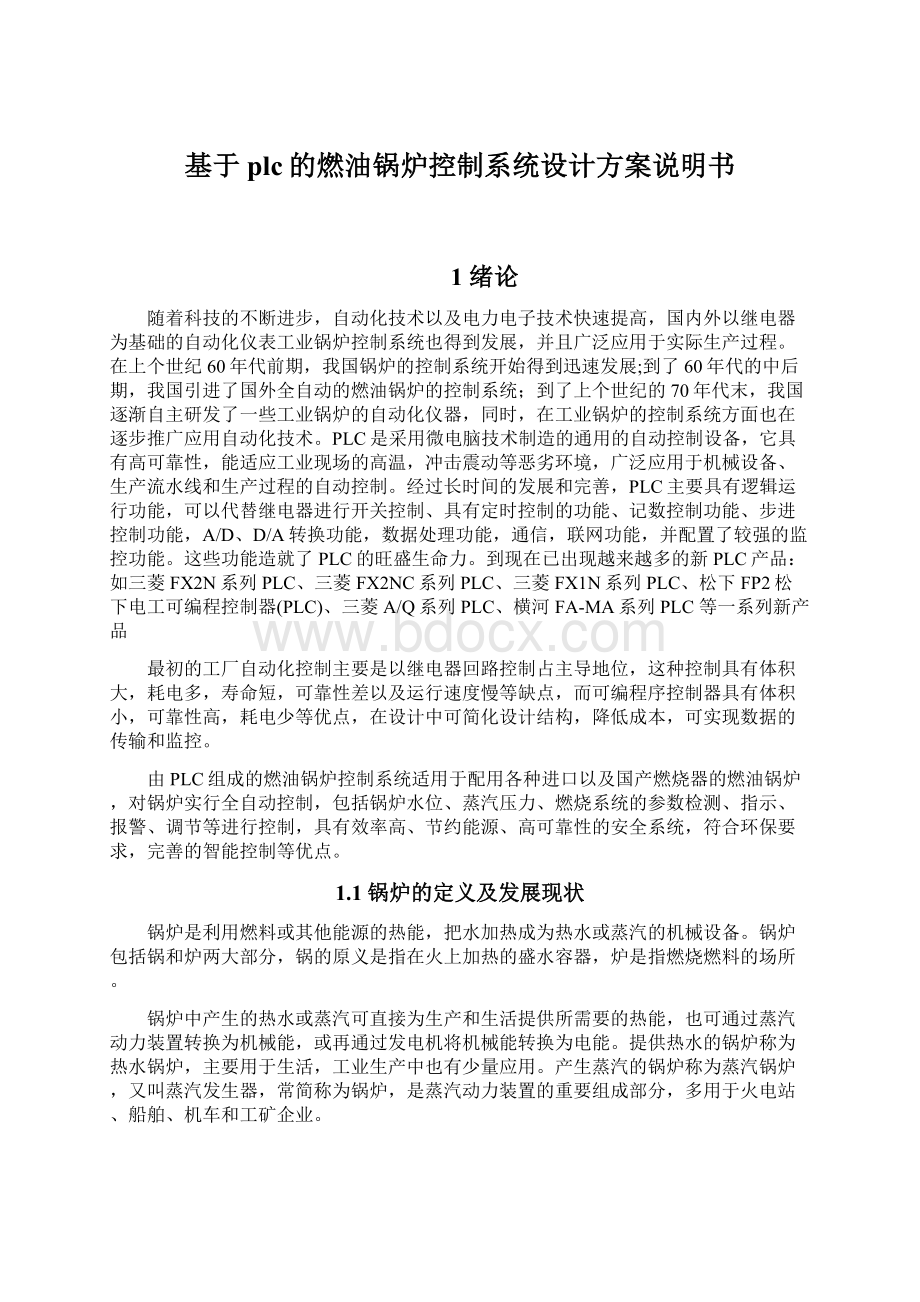
直水管锅炉已不能满足要求。
随着制造工艺和水处理技术的发展,出现了弯水管式锅炉。
开始是采用多锅筒式。
随着水冷壁、过热器和省煤器的应用,以及锅筒内部汽、水分离元件的改进,锅筒数目逐渐减少,既节约了金属,又有利于提高锅炉的压力、温度、容量和效率。
以前的火筒锅炉、火管锅炉和水管锅炉都属于自然循环锅炉,水汽在上升、下降管路中因受热情况不同,造成密度差而产生自然流动。
在发展自然循环锅炉的同时,从30年代开始应用直流锅炉,40年代开始应用辅助循环锅炉。
第二次世界大战以后,这两种型式的锅炉得到较快发展,因为当时发电机组要求高温高压和大容量。
发展这两种锅炉的目的是缩小或不用锅筒,可以采用小直径管子作受热面,可以比较自由地布置受热面。
随着自动控制和水处理技术的进步,它们渐趋成熟。
在超临界压力时,直流锅炉是唯一可以采用的一种锅炉,70年代最大的单台容量是27兆帕压力配1300兆瓦发电机组。
后来又发展了由辅助循环锅炉和直流锅炉复合而成的复合循环锅炉。
在锅炉的发展过程中,燃料种类对炉膛和燃烧设备有很大的影响。
因此,不但要求发展各种炉型来适应不同燃料的燃烧特点,而且还要提高燃烧效率以节约能源。
此外,炉膛和燃烧设备的技术改进还要求尽量减少锅炉排烟中的污染物(硫氧化物和氮氧化物)
早年的锅壳锅炉采用固定炉排,多燃用优质煤和木柴,加煤和除渣均用手工操作。
直水管锅炉出现后开始采用机械化炉排,其中链条炉排得到了广泛的应用。
炉排下送风从不分段的“统仓风”发展成分段送风。
早期炉膛低矮,燃烧效率低。
后来人们认识到炉膛容积和结构在燃烧中的作用,将炉膛造高,并采用炉拱和二次风,从而提高了燃烧效率。
早年制造的煤粉炉采用了U形火焰。
燃烧器喷出的煤粉气流在炉膛中先下降,再转弯上升。
后来又出现了前墙布置的旋流式燃烧器,火焰在炉膛中形成L形火炬。
随着锅炉容量增大,旋流式燃烧器的数目也开始增加,可以布置在两侧墙,也可以布置在前后墙。
1930年左右出现了布置在炉膛四角且大多成切圆燃烧方式的直流燃烧器。
第二次世界大战后,石油价廉,许多国家开始广泛采用燃油锅炉。
燃油锅炉的自动化程度容易提高。
70年代石油提价后,许多国家又重新转向利用煤炭资源。
这时电站锅炉的容量也越来越大,要求燃烧设备不仅能燃烧完全,着火稳定,运行可靠,低负荷性能好,还必须减少排烟中的污染物质。
在燃煤(特别是燃褐煤)的电站锅炉中采用分级燃烧或低温燃烧技术,即延迟煤粉与空气的混合或在空气中掺烟气以减慢燃烧,或把燃烧器分散开来抑制炉温,不但可抑制氮氧化物生成,还能减少结渣。
沸腾燃烧方式属于一种低温燃烧,除可燃用灰分十分高的固体燃料外,还可在沸腾床中掺入石灰石用以脱硫。
1.2PLC控制燃油锅炉的目的和意义
锅炉是一次性能源煤炭、石油、天然气转换成二次能源蒸汽量的重要动力设备。
据有关数据统计,目前我国有各类工业锅炉约25万。
每年耗煤量占全国产量的1/3,同时还消耗大量的石油和天然气。
工业锅炉是生产过程中重要的动力设备。
在石油化工领域,它的主要作用是向生产装置提供所需的合格蒸汽,其控制质量的优劣不仅关系到锅炉自身运行的效果,而且还将直接影响到相关装置生产过程的稳定性。
现代燃油燃烧机多为自动控制的燃烧机,一般采用工业程序控制器、火焰检测器以及温度传感器等组成自动控制系统。
燃油锅炉随着城市的发展而越来越多地被应用。
以前使用燃煤锅炉由于其在燃烧时产生大量的CO2和粉尘污染环境而逐渐被淘汰,相对应的用燃油锅炉来代替燃煤锅炉已被广泛用于酒店、大型商场等建筑。
由PLC组成的燃油锅炉控制系统适用于配用各种进口及国产燃烧器的燃油锅炉,对锅炉实行全自动控制,包括锅炉水位、蒸汽压力、燃烧系统的参数检测、指示、调节等进行控制。
1.3PLC控制燃油锅炉的设计内容
本设计采用可编程序控制器PLC控制燃油锅炉的稳定可靠运行。
通过PLC的选型、检测元件选型、低压电器选型、电源设计完成燃油锅炉的硬件设计部分。
通过仿真软件的模拟和调试完成燃油锅炉的软件设计。
1.4预期实现的目标
实现燃油锅炉的自动控制,不但能很好的控制锅炉的水位和蒸汽压力等参数,还能很方便的加水和排水,基于PLC的控制很容易实现工业化。
我国目前运行的很多锅炉控制系统自动化水平不高、安全性低,工作效率普遍低于国家标准,因此实现燃油锅炉的自动控制对能源消耗来说很重要。
2系统总体设计方案
2.1燃油锅炉控制系统基本组成部分
燃油锅炉主要组成部分:
燃油预热器:
锅炉启动前,将锅炉燃烧用的燃油加热到适当温度以达到良好雾化,保证锅炉的正常燃烧。
汽包:
由上下锅筒和三簇沸水管组成,水在管内受管外烟气加热,在管簇内发生自然的循环流动,并逐渐汽化,产生的饱和蒸汽聚集在上锅筒里边。
下锅筒作为连接沸水管之用,同时储存水和水垢。
炉膛:
是使燃料充分燃烧并放出热能的设备,由供油系统和油枪组成。
引风设备:
包括引风机,烟囱,烟道几部分,用它将锅炉中的烟气连续排除。
送风设备:
由鼓风机和风道组成,用它来供应燃料燃烧所需要的空气。
燃料供给设备:
包括供油管路和油枪等。
燃油锅炉控制系统由燃油预热器、点火变压器、瓦斯阀、引风机、油泵、进水阀、出水阀、水位上限开关、水位下限开关、各种检测仪表及监控设备组成。
系统原理框图如图2.1所示。
图2.1燃油锅炉系统原理框图
2.2燃油锅炉的工作过程
锅炉工作时燃料在炉膛内进行燃烧,将其化学能转化为热能,高温的燃烧产物—烟气通过汽包受热面将热能传递给汽包内温度较低的水,水被加热进而沸腾汽化,生成蒸汽。
燃料在燃烧时,油由油泵从储油罐中抽出,经燃油预热器预热,由喷油电磁阀经喷油口打入锅炉进行燃烧。
燃烧时,鼓风机送风,喷油电磁阀喷油,点火变压器接通(子火燃烧),瓦斯阀打开(母火燃烧),将燃油点燃。
点火完毕后,关闭点火,继续送风、喷油,使燃烧持续。
2.3燃油锅炉工艺控制要求
鼓风机通风10min后,燃油经燃油预热器预1min,,由喷油泵经喷油口打入锅炉燃烧。
点火时,鼓风机送风;
喷油口喷油;
点火变压器接通(子火);
瓦斯阀打开(母火)。
5S后,关闭子火,继续送风,使燃烧继续,控制锅炉的进出水和蒸汽压力。
燃油锅炉系统工艺流程图如图2.2所示
图2.2燃油锅炉运行示意图
燃油锅炉运行的示意图如上所示,燃油经燃油预热器预热,由喷油泵经喷油口打入锅炉进行燃烧。
燃烧时,鼓风机送风;
点火变压器接通(子火燃烧);
瓦斯阀打开(母火燃烧),将燃油点燃。
点火完毕,关闭子火,继续送风、喷气,使燃烧持续。
锅炉的进水和排水分别由进水阀和排水阀来执行。
上、下水位分别由上限、下限水位开关来检测。
蒸汽压力由蒸汽压力开关来检测。
3燃油锅炉控制系统的硬件设计
3.1PLC机型的选择及各硬件性能指标分析
通常选择PLC机型有以下几种方法:
3.1.1方法1.按以下条件选择机型
(1)可编程序控制器的类型:
可编程序控制器按结构可分为整体型和模块型两类,按应用环境分为现场和控制室安装两类;
按CPU的字长分为1位、4位、8位、16位、32位、64位等。
从应用角度出发,通常可按控制功能或输入/输出点数类型。
可按表3.1的控制功能或输入输出点数选择可编程序控制器的类型。
PLC类型
总点数
信号类型
程序容量
结构类型
超小型
小型
中型
大型
超大型
≤64
≤128
≤512
≤1024
≥1024
开关量
开关量、模拟量
有特殊I/O单元
功能强
≤1KB
≤4KB
≤8KB
≤16KB
≥16KB
整体型
模块型
表3.1 根据控制功能或输入输出点数选择可编程序控制器的类型
(2)输入输出模块的选择:
输入输出模块的选择应考虑与应用要求的统一。
例如对输入模块,应考虑信号电平、信号传输距离、信号隔离、信号供电方式等应用要求。
对输出模块,应考虑选用的输出模块类型,通常继电器输出模块具有价格低、适用范围广、寿命短、响应时间长等特点;
可控硅输出模块适用于开关频繁,电感性低功率因素负荷场合,但价格较贵,过载能力较差。
输出模块还有直流输出、交流输出和模拟量输出等,与应用要求应一致。
(3)电源的选择
可编程序控制器的供电电源,除了引进设备时同时引进可编程序控制器应根据产品说明书要求设计和选用外。
一般可编程序控制器的供电电源的应设计选用220V交流电源,与国内电网电压一致。
重要的应用场合,应采用不间断电源或稳压电源供电。
(4)存储器的选择
由于计算机集成芯片技术的发展,存储器的价格已下降,因此,为保证应用项目的正常投运,一般要求可编程序控制器的存储器容量,按256个I/O点至少8K存储器选择。
(5)经济性的考虑
选择可编程序控制器时,应考虑性能价格比。
考虑经济性时,应同时考虑应用的可扩张性、可操作性、投入产出比等因素,进行比较和兼顾,最终选出较满意的产品。
3.1.2方法2
目前,国内外PLC生产厂家生产的PLC品种已达几百个,其性能各有特点,价格也不尽相同。
在设计PLC控制系统时,要选择最适宜PLC机型,一般应考虑下列因素:
(1)系统的控制目标。
设计PLC控制系统时,首要的控制目标就是:
确保生产的安全可靠,能长期稳定运行,保证产品高质量,提高生产效率,改善信息管理等。
(2)PLC的硬件配置。
根据系统的控制目标和控制类型,从众多的PLC生产厂中初步选择几个具有一定知名度的公司,如SIEMENS,OMRON,A-B等,再根据被控对象的工艺要求以及I/O系统考虑具体配置问题。
(3)I/O系统。
PLC控制系统的输入/输出点数的多少,是PLC系统设计时必须知道的参数,在运行硬件配置时这个参数具有两个含义:
一个是实际的控制系统所需要的I/O点数,另一个是所考虑的PLC机型能够提供的I/O点数。
(5)指令系统。
PLC的种类很多,因此它的指令系统是不完全相同的。
可根据实际应用场合对指令系统提出的要求,选择相应的PLC。
从应用的角度考虑,有的场合以逻辑控制为主,有的场合需要算术运算,有的场合可能需要更先进、更复杂的控制系统。
(6)响应速度。
对于以数字量控制为主的PLC控制系统,PLC的响应速度都可以满足要求,不必特殊考虑。
而对于还有模拟量的PLC控制系统,特别是含有较多闭环控制的系统,必须考虑PLC的响应速度。
一般从两个方面来考虑:
一是执行指令时间;
二是扫描周期。
3.1.3PLC容量估算
PLC容量包括两个方面:
一是I/O点数,二是用户存储器的容量。
I/O点数的估算。
根据功能说明书,可统计出PLC系统的开关量I/O点数及模拟量I/O通道数,以及开关量和模拟量的信号类型。
考虑到在前面的设计中I/O点数可能有疏漏,并考虑到I/O端的分组情况以及隔离与接地要求,应在统计后得出I/O总点数的基础上,增加10%~15%的裕量。
考虑裕量后的I/O总点数即为I/O点数估算值,该估算值是PLC选型的主要技术依据,考虑到今后的调整和扩充,选定的PLC机型的I/O能力极限值必须大于I/O点数估算值。
并应尽量避免使PLC能力接近饱和,一般应留有30%左右的裕量。
存储器容量估算。
用户应用程序占用多少内存与许多因素有关,如I/O点数、控制要求、运算处理量、程序结构等。
因此在程序设计之前只能粗略的估算。
根据经验,每个I/O点及有关功能器件占用的内存大致如下:
开关量输入所需存储器字数=输入点数×
10
开关量输出所需存储器字数=输出点数×
8
定时器/计数器所需存储器字数=定时器/计数器数量×
2
模拟量所需存储器字数=模拟量通道数×
100
通信接口所需存储器字数=接口个数×
300
存储器的总字数再加上一个备用量即为存储器容量。
例如:
作为一般应用下的经验公式是:
所需存储器容量(KB)=(1~1.25)×
(DI×
10+DO×
8+AI/O×
100+CP×
300)/1024
其中:
DI为数字量总输入点数;
DO为数字量输出总点数;
AI/AO为模拟量I/O通道总数;
CP为通信接口总数。
根据上面的经验公式得到的存储器容量估算值只具有参考价值,但在明确PLC要求容量时,还应根据其他因素对其进行修正。
综合考虑上述一些选择要求以及对PLC产品的熟悉程度,最后选择日本三菱的FX2系列PLC作为系统控制的机型。
FX2系列可编程序控制器是日本三菱公司继F1、F2系列可编程序控制器之后推出的新产品。
它采用整体式结构,按功能可分为基本单元、扩展单元、扩展模块及特殊适配器等四种类型产品。
基本单元有CPU、存储器、输入/输出(I/O)、电源饿等,是一个完整的PC机,可以单独使用。
基本单元型号表示方法如下:
FX2N—×
×
M×
||
2
式中,1部分表示用两位数表示输入/输出(I/O)总点数,有16、24、32、48、64和80六种;
2部分用字符表示输出类型:
R表示继电器输出,T表示晶体管输出,S表示双向晶闸管输出。
PLC的主要技术性能包括编程方式、指令、存储器、PC的元器件等,是PLC选型时主要的选择依据。
FX2N系列PLC的主要技术性能如表4.4.1所示。
FX2N系列输入类型为直流输入,采用直流(DC24V)供电。
输出类型有继电器、晶体管、双向晶闸管三种输出形式。
继电器输出可靠性高,价格低,使用电压范围广,既可控制交流负载又可控制直流负载,因而使用广泛;
但因有触点输出,尤其在感性负载时继电器触点寿命较短,动作响应时间较长(10ms以下),因而不适应要求高速通断、快速响应的工作场合。
晶体管输出是无触点输出,动作响应时间短(0.5ms以下),用于控制直流负载。
双向晶闸管输出亦是无触点输出,动作响应时间较短,用于控制交流负载。
晶体管和双向晶闸管输出过载、过压能力较差,价格高,因而适应于要求快速通断、快速响应的工作场合。
由前述的燃油锅炉示意图及运行、控制要求可知该控制系统共有5个输入(启动X1、停止X2、蒸汽压力X3、上限X4、下限X5),7个输出(预热Y1、送风Y2、子火Y3、喷油Y4、母火Y5、进水阀Y6、出水阀Y7),输入/输出(I/O)总点数为12,考虑到控制对象系统有可能有所变动或扩展以及保留10~15%裕量,同时该系统的控制要求精度不是很高和对成本的考虑,最后选择FX2N-24MR-001机型(12个输入点,12个输出点)作为该系统的PLC机型。
在锅炉的控制要求中,蒸汽压力,这个值的控制一般用传感器来控制,即当系统压力超过一定值时通过传感器将非电信号转化为电信号传输给控制系统,再由控制系统做相应的动作。
信号有模拟量和开关量两种形式,这里我们采用开关量信号。
具体项目性能指标如表3.2所示:
项目
性能指标
编程方式
梯形图,步进顺控指令
基本指令执行时间
0.74µ
s/步
指令种类
107条(基本指令20条,步进顺序指令2条,功能指令85条)
程序容量/存储器类型
2K步RAM(标准配置)
4K步EEPROM卡盒(选配)
8K步RAM、EEPROM、EPROM卡盒(选配)
输入继电器(DC输入)
24VDC,7mA光电隔离
输出继电器
继电器
250VAC、30VDC、2A(电阻负载)
晶体管
30VDC、0.5A/点
双向晶闸管
242VAC、0.3A/点
辅助继电器
通用型
500点(M0~M499)
停电保持型
524点(M500~M1023),电池后备
特殊型
256点(M8000~M8255)
状态元件
初始化用
10点(S0~S9)用于初始状态
490点(S10~S499)
400点(S500~S899)
报警
100点(S900~S999)
定时器
0.1s(100ms)
200点(T0~T99),0.1~3279.7S
0.01s(10ms)
46点(T200~T245),0.01~327.67S
1ms(积算)
4点(T246~T249),0.001`32.767S,电池后备
100ms(积算)
6点(T250~T255),0.1`3276.7S,电池后备
计数器
通用加数器
100点(C0~C99),1~32767S,电池后备
停电保持加计数器
100点(C100~C199),1~32767S,电池后备
通用加减计数器
20点(C200`C220)
停电保持加减计数器
15点(C220~C234)电池后备
高速计数器
6点(C235~C256)电池后备
寄存器
同用数据寄存器
200点(D0~D199)
停电保持数据寄存器
312点(D200~D511)
特殊寄存器
256点(D8000`D8255)
变址寄存器
2点(V,Z)
文件寄存器
最大2000点(D1000~D2999),电池后备
表3.2FX2系列PLC机的主要技术性能
3.2燃油锅炉的控制过程分析
用PLC控制燃油锅炉的启动、停止、出现异常情况时能暂停且异常情况消失后能自动按照起燃顺序重新工作。
控制要求:
1)起动:
该锅炉的燃烧按一定时间间隔顺序起燃。
其起燃顺序为:
间隔10min间隔1min
间隔5s
间隔5s
送风-----燃油预热--------子火燃烧------喷油-------母火燃烧------关闭子火、预热器、喷油泵
2)停止:
停止燃烧时,要求:
间隔30s
停止----子火、母火、预热器、喷油泵关闭---送风(将废气、杂质吹去)-----送风停止(清炉停止)
3)异常状况自动关火:
锅炉燃烧过程中,当出现异常状况时(即蒸汽压力超过允许值,或水位超过上限,或水位低于下限),能自动关火进行清炉;
异常状况消失后,又能自动按起燃程序重新点火燃烧。
即:
间隔30s
异常情况---------子火、母火、预热器、喷油关闭----送风---------清炉
触发预热器
停止-----------重新起燃
4)锅炉水位控制:
锅炉工作起动后,当水位低于下限时,进水阀打开,排水阀关闭。
当水位高于上限时,排水阀打开,进水阀关闭。
3.3燃油锅炉的运行流程图设计
根据系统的控制要求可得运行流程图,如图3.1所示。
图3.1系统运行流程图
3.4系统的I/O接口以及硬件接线图设计
由前面所述可知该系统有5个输入,7个输出,其I/O接口如表3.3
输入接口
输出接口
启动按钮
X1
燃油预热
Y1
停止按钮
X2
鼓风机送风
Y2
蒸汽压力
X3
点火变压器(子火)
Y3
水位上限
X4
喷油口喷油
Y4
水位下限
X5
瓦斯阀(母火)
Y5
进水电磁阀
Y6
出水电磁阀
Y7
表3.3系统输入、输出接口示意图
由上表以及所选机型FX2N-24MR-001可得该系统的硬件接线图,如图3.2所示:
图3.2系统硬件接线图
3.5系统供电电源设计
上图中,PLC接入了一个电源,可编程控制器CPU所需的工作电源一般都是5V直流电源,一般的编程接口和通信模板还需要5.2V和24V直流电源,这些电源可由可编程控制器本身的电源模板供给,而PLC的电源模板需要外接。
PLC的电源模板可能包括多种输入电压,有220V交流,110V交流和24V直流等。
针对燃油锅炉的实际情况,我们采用220V交流,简单不需添加变压器,是普通电网就能提供。
系统供电电源设计如图3.3所示。
图3.3系统供电电路