秭归县坑口火电厂汽轮发电机组施工方案Word下载.docx
《秭归县坑口火电厂汽轮发电机组施工方案Word下载.docx》由会员分享,可在线阅读,更多相关《秭归县坑口火电厂汽轮发电机组施工方案Word下载.docx(26页珍藏版)》请在冰豆网上搜索。
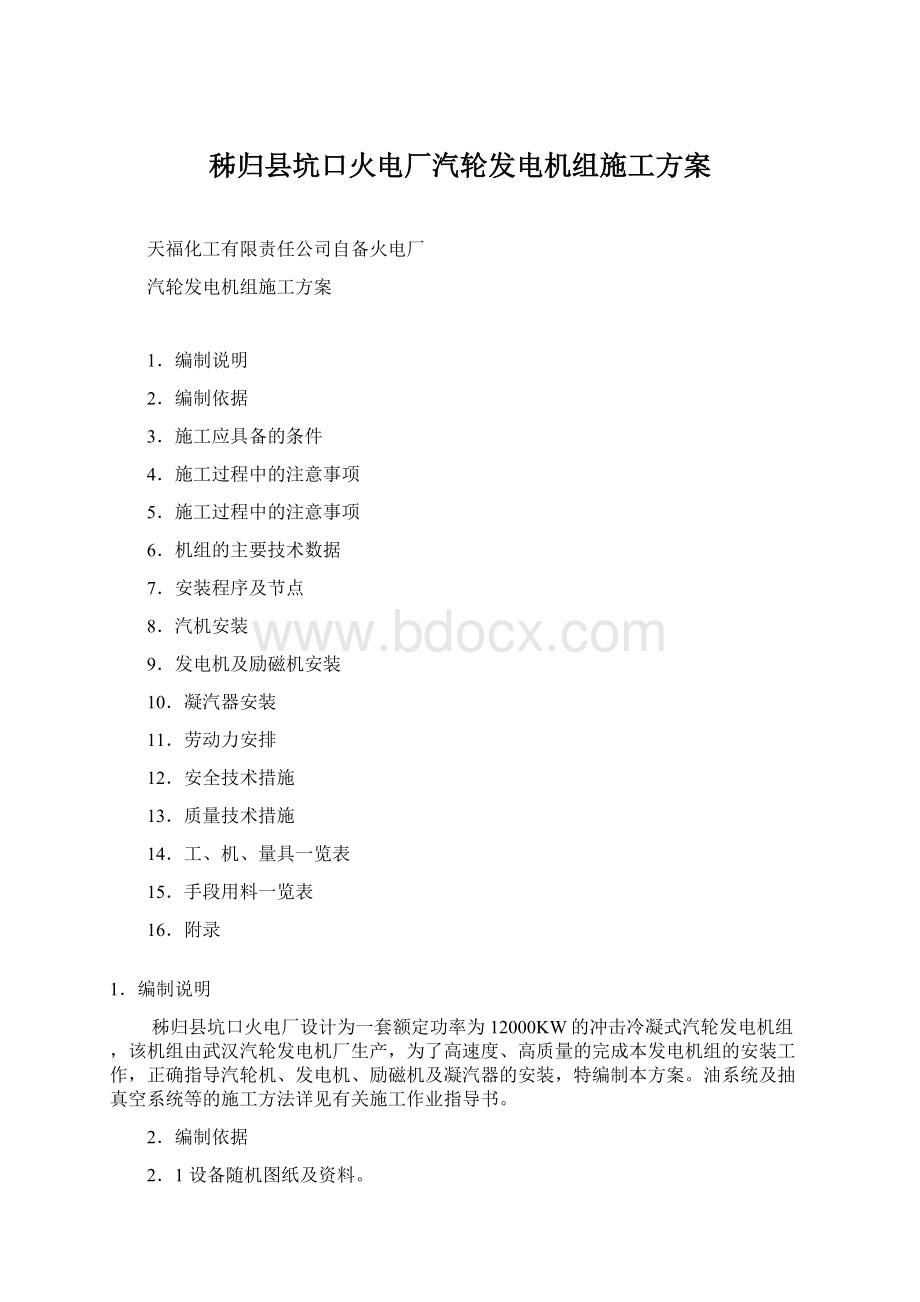
4.4根据设备的安装顺序及位置,合理的安排设备的放置地点。
4.5准备存放零部件的仓库及货架。
4.6制作安装所需的专用工具、索具。
4.7组织各方有关人员进行基础验收、中间交接。
4.8对机组的合金钢部件进行光谱复查。
4.9对凝汽器的铜管按1/1000的比例抽样进行压扁试验,扩张试验以及残余应力试验。
4.10按垫铁座浆混凝土的配比做试块进行强度试验。
5.1设备开箱后,不同材质的零部件必须分开存放并作出明确标识,不得混淆。
5.2不得在设备上随意进行引弧、切割,对设备的精密加工面应做好安全保护。
5.3大件设备的摆放位置应选择在有足够承载能力的地方。
5.4大件设备的吊装应采用随机提供的专用工具进行。
5.5在吊装过程中,对设备的精密加工面应妥善保护,禁止索具直接与设备的精密部位接触,设备部件吊运,就位用两个10t导链作徽调节用。
5.6对拆下的零部件,洗净后用干净塑料布包好,并做好标识。
5.7设备本体配管不得强行对口,应架百分表监视。
5.8使用燃油清洗设备时,要注意防火,预留孔洞要用临时盖板盖好,注意人身安全。
5.9由于汽轮机安装好后,不可能立即投入试车及运行,对设备内部部件要作好防锈处理。
序号
名称
单位
数量
备注
1
主汽门前蒸汽压力
Mpa
3.43
2
主汽门前蒸汽温度
℃
435
3
冷却水温
25
4
汽机工作转速
rpm
3000
5
额定功率
kw
12000
6
前汽缸上半重
kg
2850
7
中汽缸上半重
2700
8
后汽缸上半重
2800
9
上缸总重(不含隔板)
8350
10
上缸下半重
1950
11
中缸下半重
2900
12
后缸下半重
7400
13
下缸总重(不含隔板)
12300
14
汽机本体最大尺寸
mm
5325×
3590×
3530
长×
宽×
高
15
汽机转子总重
6641
16
汽机转子总长
Mm
4158
17
汽机转子最大直径
φ1904
第十级叶轮
18
发电机定子总重
20800
19
发电机转子总重
8800
20
发电机转子总长
5839
21
凝汽器净重
21660
22
汽机临界(一级)转数
1610
7.1施工程序方框图
发电机穿转子
8.1垫铁安装
8.1.1斜垫铁与平垫铁之间以及台板与垫铁之间应进行研刮,接触面积应大于75%,0.05mm塞尺一般塞不进,局部塞入部分的深度及宽度不得大于垫铁边长的四分之一。
8.1.2本机组垫铁的安装采用座浆法。
8.1.3座浆时按座浆混凝土配比做好试块送理化实验室进行试验。
8.1.4座浆混凝土配比(重量比):
425#硅酸盐水泥:
水:
砂子(0.4~0.5mm):
铝粉=1:
0.4:
2.0:
0.0004
8.1.5在基础上按垫铁布置划出垫铁位置,铲出麻面,清理油污,并用压缩空气吹干净(并根据设备安装标高精确计算出座浆垫铁标高)。
8.1.6在清理好的基础上刷一层薄的425#硅酸盐水泥素浆层,并养护24小时。
8.1.7将配制好的混凝土灌入160×
160×
55的模具中捣实,将平垫铁放置在上面调整标高和水平,其水平偏差应不大于0.04mm/m,标高允许差为1mm。
8.1.8平垫铁标高的确定
平垫铁上平面标高=汽机中心标高-汽机中心至台板下底面的距离-斜垫铁厚度(一组两块)。
8.1.9本机且采用垫铁规格
斜垫铁100×
100,薄边厚度15mm,斜度1/10,平垫铁120×
120×
19。
8.1.10垫铁座浆的养护时间由实验室测得的试块达到要求强度的时间确定,其强度达75%以上方可承载。
8.2台板安装
8.2.1台板就位前在基础需进行二次灌浆的地方凿出新的麻面并清理干净。
8.2.2对台板进行外观检查,其与轴承座及汽缸的接触面应光洁无毛剌,与二次浇灌混凝土结合的部位应清洁无油漆、污垢。
8.2.3用涂色法检查台板与轴承座及汽缸的结合面,每平方厘米有接触点的面积占全面积的75%以上,接触面应密实,0.05mm塞尺一般塞不进,不合格时进行刮研,反复检查直到符合要求。
8.2.4安放好斜垫铁,将台板吊装就位并进行调整,其标高允差为±
1mm,且其偏差方向应一致(同为正或同为负),台板螺栓孔中心线允差为2mm。
8.2.5螺栓下部的垫板应安放平正,与基础接触应密实,螺栓垂直度的允许偏差为L/200,且不大于5mm。
8.3前轴承座安装
8.3.1对轴承座的油室及油路进行彻底清理,保持其清洁畅通,无任何杂物,如有能溶于汽轮机油的油漆应予清除。
8.3.2对轴承座油室进行煤油渗漏试验,灌油高度应不低于回油管的上口外壁,时间持续24小时。
8.3.3测量前轴承座纵向键及键槽尺寸,沿滑动方向取三点测量,三点测得的尺寸相互差均不得超过0.03mm,键槽与键的宽度之差应与键槽两侧向隙相符。
8.3.4将前轴承座吊装就位并进行调整,在轴瓦洼窝处测量轴承座的纵、横向水平允差为0.20mm/m。
8.3.5调整滑动面,使汽机的膨胀余量达到设计要求。
8.4汽缸安装
8.4.1对汽缸进行外观检查应无裂纹、夹渣、重皮、焊瘤、气孔、铸砂和损伤,各结合面、滑动承力面、法兰、洼窝等加工面应光洁无锈蚀和污垢、防腐层应全部清除掉,蒸汽室内部应彻底清理,无任何附着物。
8.4.2汽缸组合
8.4.2.1根据现场设备放置情况,汽缸的组合选在汽机间的7米层进行。
8.4.2.2用桁车将前中缸下半及后缸下半吊至7米层,后缸下半找平后垫平稳,桁车吊起前中缸下半进行对接,垂直中分面紧三分之一螺栓后检查,前中缸与后缸接合部位的高低差应小于0.02mm,汽缸的水平度应一致定位销孔不得错位,如不合要求,则需研究处理。
8.4.2.3以上检查合格后,解体在两垂直结合面分别涂上密封胶,加上垫片,打入定位销,对称紧固垂直中分面螺栓,再次检查,前中缸与后缸接合部位的高低差,汽缸水平度及垂直中分面间隙。
8.4.2.4检查合格后,将垂直中分面螺母与汽缸壁点焊固定。
8.4.3将组合好的下汽缸吊装就位,其横向水平偏差一般不应超过0.20mm/m,在中分面口初找纵向水平。
8.4.4合缸检查
8.4.4.1上缸的组合方法同下缸一样,上缸组合好后,采用双钩法翻缸。
8.4.4.2将上缸吊起进行合缸,将上缸吊起后应保证其中分面的水平,使用导链使汽缸平稳落下。
8.4.4.3紧三分之一螺栓后检查汽缸的结合面,其间隙应符合要求,如不合格,则涂色刮研,直到符合要求。
8.4.4.4汽缸结合面要求
汽缸种类
高压缸
中压缸
低压缸
结合面类型
水平结合面
垂直,水平结合面
按冷紧要求紧固三分之一螺栓,用塞尺检查应达到的要求
0.03mm塞尺自内外均不得塞入
0.05mm塞尺自内外两侧检查一般不得塞入,个别塞入部分不得超过汽缸法兰密封面宽度的三分之一
0.05mm塞尺不得通过,在汽缸法兰同一段面处从内外塞入长度,不得超过法兰宽度的三分之一
8.5轴承安装
8.5.1检查轴承乌金有无夹渣、气孔、凹坑、裂纹等缺陷,承力面部位不得有粘合不良现象,检查轴瓦进油孔,应保证其畅通。
轴承的各部件应有钢印标记,以保证安装位置和方向的正确。
8.5.2推力轴承前轴承的安装
8.5.2.1检查轴承体球面与球面座的接触情况,其接触面积应不小于50%,并均匀分布,接合面用0.03mm密尺塞不进,如尽责接触不良,不宜修刮,应通知制造厂处理。
8.5.2.2组合后的球面瓦水平结合面不允许错口,用0.05mm塞尺应塞不进。
8.5.2.3检查推力瓦块,推力瓦应逐个编号,测其厚度差应不大于0.02mm,如超过此数值,不宜立即进行调整,待总装时将推力盘压向推力瓦块,视磨痕情况再进行调整。
8.5.2.4用塞尺检查轴瓦与轴颈的侧间隙,应为0.12~0.16mm,且沿轴向全长均匀一致,塞入深度以15~20mm为宜。
8.5.2.5用压保险丝法测轴瓦与轴颈的顶间隙应为0.24~0.32mm。
8.5.3径向轴承的安装
8.5.3.1检查轴承垫块与轴承座洼窝的接触情况,其接触面积不应小于50%。
8.5.3.2轴承下部垫块在未放转子时与轴承座之间应有0.03~0.05mm的间隙,以保证放入转子后三处垫块均与洼窝接触良好。
8.5.3.3径向轴承的顶间隙应为0.38~0.48mm,侧间隙应为0.19~0.24mm,测量方法同推力轴承间隙的测量方法。
8.5.3.4检查轴承中分面间隙,0.05mm塞尺应塞不进。
8.5.4轴瓦刮研
8.5.4.1轴瓦与轴颈的接触角应为30°
~50°
。
8.5.4.2径向轴承在接触角弧段内沿轴向与轴颈的接触应均匀,接触面积应大于75%,如不合要求,则需进行刮研,反复进行检查直到达到要求。
8.6转子找中心
8.6.1转子对中是一项同转子中心位置,转子与轴承、轴承与轴承体接触情况、滑销间隙、汽缸纵向水平、转子扬度等诸多因素互相关联的重要工作,应综合考虑,慎重调整。
8.6.2测量转子的椭圆度和不柱度,应不大于0.02mm,转子找中心以前后汽封洼窝为基准,测量部位应光洁,且作出记号,保证每次都在同一位置测量。
8.6.3在轴瓦上浇上透平油,用专用工具起吊转子,并调整好转子后轴颈水平,将转子缓缓落到轴瓦上。
8.6.4在转子对中调整时,对前汽封洼窝处,通过整前轴承座的三维坐标满足要求,调整的同时检测前轴承座的水平、汽缸的水平和扬度、推力轴承承力面与推力盘的平行度、后轴颈水平。
8.6.5转子在后汽封洼窝处的对中,首先应考虑在调整轴承的影响,调整机后轴承座垫块和缸的三维坐标,同时检测8.6.4项的内容。
8.6.6转子对中应达到的要求
后轴颈扬度为0,向高压端扬起,在前后汽封窝处测得的a、b、c值满是:
|a-b|=0~0.05mm
|c-(a+b)/2|=0~0.04mm
8.6.7在转子对中调整好后应复查轴颈和轴瓦的接触情况。
并在前后轴颈上测量主轴的水平,汽缸中分面等各处的水平。
8.7垫铁检查地脚螺栓紧固
8.7.1再次检查垫铁接触情况,用0.05mm塞尺一般塞不进,局部塞入部分的深度和宽度不得超过其边长的四分之一。
8.7.2检查合格后,正式紧固地脚螺栓,将下端螺母与垫块点焊,在垫铁侧面点焊,并进行一次灌浆。
8.8通流部分安装
8.8.1清洗汽缸、汽封体、汽封圈、转子向导叶环、隔板等,作外观检查应无缺陷。
8.8.2测量隔板中分面键与键槽的尺寸,隔板与汽缸装配的键与键槽的尺寸,并作记录,键与键槽的配合应符合图纸要求。
8.8.3检查隔板悬挂销与隔板及汽缸的水平面接触面积,应不小于60%且接触均匀。
8.8.4检查上下隔板中分面间隙,用0.05mm塞尺一般塞不进,局部塞入部分的深度和宽度不得超过其边长的四分之一。
8.8.5以前后汽封洼窜中心为基准拉钢丝对隔板进行找中心,钢丝对洼窝中心位置的偏差应不大于0.05mm,钢丝的直径选为φ0.3,拉钢丝的紧力应为钢丝极限强度的四分之三左右,隔板对中应达到如下要求:
|a-b|≤0.05mm
(a+b)/2-c≤-0.05mm
8.8.6隔板对中调整可将隔板挂耳补焊,修刮或加整张钢质调整垫片。
8.8.7测量各级通流部分间隙并作记录,其数据应与图纸依尺寸相符,对不合格的进行研究处理,测量点应在动静部分最突出的位置。
8.8.8隔板推力盘轴向间隙至0.40mm。
8.8.9检查汽封套的水平结合面及垂直接合面,在紧固螺栓的情况下,0.05mm塞尺应塞不进。
8.8.10用塞尺及贴胶布法测量汽封间隙,对不合格的进行调整。
8.8.11按压汽封块,应能用手自由按入,松手后自动弹回原位,一般应有3.5mm的退让间隙。
附1:
通流部分间隙(mm)
附2:
汽封间隙(mm)
8.9汽机扣大盖
8.9.1扣大盖前应作好充分准备,明确分工,统一指挥,保证扣盖工作顺利连续进行。
8.9.2扣盖前对汽缸内部及中分结合面进行清理,保证彻底清洁,无任何杂物,对通流部分作详细检查,保证准确无误。
8.9.3用双钩法翻上缸并缓缓吊起,找好其水平结合面的纵、横向水平度,使之与下汽缸一致。
8.9.4试扣大盖
装上汽缸导杆涂上黄油,将上缸沿导杆缓缓落至下缸上,分别在不紧螺栓和紧1/3螺栓的情况下同时测取汽封套、隔板间隙,检查汽缸水平中分面间隙,盘动转子,用听棒监听汽缸内部有无异常声音。
8.9.5正式扣大盖
试扣大盖检查合格后,将上缸续续吊起,再次清理汽缸结合面,在下汽缸法兰结合面上均匀涂上0.5mm厚的铁锚604密封胶,缓缓落下大盖,当大盖落至离下缸5~10mm时,打入定位销,将大盖全部落下。
8.9.6螺栓紧固
8.9.6.1紧固螺栓的顺序,宜从汽缸中部开始,左右两侧对称的分别向前后汽封处依次拧紧。
8.9.6.2冷紧
用1米长加套管扳手由两人进行冷紧,冷紧力矩为400NM。
8.9.6.3热紧
用电加热器从螺栓中心孔对螺栓进行加热,直至一人用一米长扳手可转动螺帽至需要角度为止,热紧时应特别注意螺栓不得转动,热紧值:
M64×
4×
40026°
M72×
35036°
M68×
46036°
8.9.7热紧完毕后,对滑销系统进行检查,其间隙应满足图纸要求。
8.9.8安装后汽缸导板,使其达到设计要求。
附3:
转向导叶环及隔板与汽缸的配合间隙(mm)
8.10汽轮机与发电机联轴节对中
8.10.1联轴节对中以调整好的汽机转子中心线为基准,调整发电机转子来满足对中要求。
8.10.2测量联轴节端面瓢偏,不应大于0.02mm。
8.10.3联轴节对中时两法兰的相对位置应按制造厂的记号对正。
8.10.4在测量轴向误差时,必须在互成180°
半径相等的两个对应点同时测量,以消除转子的窜动引起的误差,并架一百分表测量轴的轴向窜量。
8.10.5联轴节对中的径向允许偏差为0.04mm,轴向允许偏差为0.03mm,并保证上张口0~0.03mm。
8.10.6联轴节对中合格后,在进行铰孔前,须进行复测,且铰孔工作在混凝土强度达到70%以上方可进行。
8.10.7在铰孔过程中,不允许进行任何影响联轴节中心的工作。
8.10.8孔铰制完毕,安装螺栓时应加润滑剂,用小榔头轻轻敲人,不得过松或过紧,装好后,螺栓与螺栓孔应作对应的钢印标记。
8.10.9联轴节螺栓的锁紧螺钉不得用其他螺钉随意更换,否则会影响转子的动平衡。
8.11调节保安系统安装
8.11.1将调速器解体检查、清理、保证油室、油路清洁通畅。
8.11.2检查滑阀与滑阀套的间隙,滑阀行程,滑阀重合度应符合图纸要求,滑动部件应滑动自如,无卡涩现象,滑阀的定心小孔应通畅,检查错油门下的逆止阀,应能上下滑动自如。
8.11.3油动机活塞行程,油动机活塞环与筒壁间隙应符合图纸要求。
8.11.4油动机底部与轴承座上部接触面积应达75%以上且分布均匀,在不紧螺栓时0.05mm塞尺应塞不进。
8.11.5调整调节汽阀阀碟升程,调整时使六个阀碟与横梁下平面贴紧,用块规测量阀碟上部螺母至横梁上平面的距离,应分别为1.5mm、18.07mm、24.64mm、31.21mm、39.08mm、46.59mm(按阀碟顺序)调整好后,将背帽锁紧并点焊。
8.11.6测量油动机活塞行程及调节汽阀行程调整边杆长度,使调节汽阀在全关时,油动机活塞行程有1~2mm的余量。
8.11.7检查自动主汽门及操纵座,各部分尺寸应符合图纸要求,阀盖与阀壳结合面的齿形钢垫片应完好,不应有连通内外的沟槽。
8.11.8用涂色法或划铅笔印法检查阀碟与阀座的严密性,不合格时应研究处理。
8.11.9测量主汽门操纵座节流孔尺寸及活塞与下盖间距,应保证在全关时d=5mm,c=7mm。
8.11.10主汽门的标高及中心线应符合设计要求,偏差不得超10mm。
8.11.11检查危急遮断器的行程是否符合要求,各油路是否畅通,检查滑阀能否滑动自如。
8.11.12调整危急遮断器拉钩至轴颈的距离为0.8~1.2mm,安装完毕后,用手按下危急遮断器,拉钩应能挂上,手拍危急遮断器,危急遮断器应能迅速脱钩弹出。
8.12前轴承担盖
8.12.1对轴颈用桥规测量并记录。
8.12.2对轴承座内作彻底洹,保证内部清洁。
8.12.3检查轴承座与上盖接合面间隙,在通油孔周围0.03mm塞尺不得塞入,不合格时应研究处理。
8.12.4在结合面上涂密封胶,扣盖对称紧固螺栓。
8.13盘车装置安装
8.13.1用百分表测量出啮合齿轮的齿侧间隙,用涂色法检查啮合情况,用压铅丝法测齿顶间隙。
8.13.2检查盘车装置的供油控制器,就保证在套管压下位置时接通油路,在套管升起位置时,切断油路。
8.13.3盘车装置与轴承座的接合面在不加密封胶紧固螺栓后,0.05mm塞尺应塞不进,检查合格后,加密封胶,对称紧固螺栓。
8.13.4组装好的盘车装置,用手操作应能灵活脱开和咬合。
8.14基础二次灌浆
8.14.1二次灌浆宜将汽轮机、发电机、励磁机一次浇完。
8.14.2灌浆前应按要求做出试块与二次灌浆层在同样的条件下养护,按要求的时间做强度试验。
8.14.3灌浆前在基础上打出新的麻面,并清理干净用水养护24小时。
8.14.4装设模板,并检查二次灌浆部位不得妨碍汽轮机及管道的膨胀。
8.14.5浇灌完毕后应按要求进行养护,养护期满后拆除模板,外观和质量应符合设计要求。
9.发电机及励磁机的安装
9.1底板安装
9.1.1根据垫铁布置图,在基础上放置垫铁,放置位置应在地脚螺栓两侧和负荷集中的地方。
9.1.2将发电机底板吊装就位,进行找正、找平。
9.1.3将后轴承座吊装就位,用拉钢丝法初步与汽轮机转子对中。
9.1.4将轴瓦清洗后,装入轴承座内,浇上透平油,然后用桁车将发电机转子吊装就位,以汽机转子为基准进行联轴初次对中。
9.1.5检查轴瓦与轴颈的顶间隙与侧间隙,对不合要求的进行研刮或调整。
9.1.6吊开转子,紧固地脚螺栓。
9.2发电机定子安装
将定子吊装腔作势到底板上,调整好纵、横中心线。
9.3发电机穿转子
9.3.1发电机穿转子利用接长轴法进行。
9.3.2在电子转子靠近汽机端装上接长轴,同时将后轴承连同轴承座一并装到转子的另一端,将转子吊起,调好标高和水平后,缓缓向定子移动,当第一次绑扎点靠近定子端部时,接长轴已从定子另一端伸出,此时在定子内放一适当厚的橡皮垫,将转子落在定子铁芯上,将钢丝绳更换绑扎在接长轴上和靠近后轴承座处,重新起吊,缓缓将转子移到规定位置。
在后轴承座就位时,应在轴承座与台板之间加整张绝缘垫片,在与台板联接的螺栓孔中加绝缘套筒。
轴承座下的垫片调整好后,在联轴节精找中之前,应测试后轴承座绝缘,如不合格,应调整好后再进行联轴节精找中,以免造成找中工作的返工,同时,在找正完毕,打定位销孔及铰孔的过程中,以及打入定位销时,不可将轴承座的钢质垫片打出飞边和台板及轴承座接触上。
9.3.3检查并调整空气气隙使之符合要求。
9.3.4先找出转子和定子的磁力中心线并作标记。
调整发电机定子与转子的磁力中心,使定子中心线向励磁机端偏移3.5mm。
9.4端盖安装
9.4.1检查风挡及端盖密封圈间隙。
9.4.2端盖与定子试配、铰孔。
9.4.3对定子内部进行彻底清理,检查确保内部清洁无杂物,办理封闭签证,最后封闭端盖。
9.5励磁机安装
9.5.1将励磁机吊装就位,进行找正。
9.5.2调整间隙达到图纸要求。
9.5.3最后紧固与底座连接螺栓。
10.1排气接管的安装
10.1.1此工作在汽缸组合时一起进行。
10.1.2对后汽缸排汽法兰及排汽接管法兰接合面仔细检查,如发现由于运输装卸而造成的擦伤等缺陷,应在安装前消除。
10.1.3将两法兰接合面清理干净,涂上熬熟的亚麻仁油混合石墨粉,放上垫片后进行组装,并且必须均匀对称地拧紧法兰螺栓,以保证结合面接合良好,然后同后汽缸一起就位。
10.2凝汽器顶入位
将凝汽器底板放到基础上,进行找正,调整其标高为+1660,用桁车将凝汽器吊装就位,进行临时支撑。
10.3对凝汽器内部进行彻底清扫,清除一切杂物和灰尘,并将顶部妥善封闭。
10.4检查凝汽器管孔应无毛剌、锈蚀,两边有1×
45°
倒角,管孔应比铜管外径大0.20~0.50mm。
10.5在正式胀管前应通过试胀,确定扩张系数(一般为4~6%),胀口应无欠胀和过胀现象,胀口和翻边应平滑光洁,无裂纹和显著切痕,试胀合格后方可进行正式胀接。
10.6正式胀管
铜管胀接应先再管扳四角及中央各胀一根标准管以检查两端管板距离是否一致,以确定管子长度是否足够,以标准管为基准由内到外对称进行胀接。
胀管长度约为管板厚度的7/8到6/8,进水端应伸出管板1~1.5mm并进行翻边,出水端应伸出管板1~3mm。
10.7凝汽器胀管结束后,汽侧作