第七章液压基本回路Word文档格式.docx
《第七章液压基本回路Word文档格式.docx》由会员分享,可在线阅读,更多相关《第七章液压基本回路Word文档格式.docx(23页珍藏版)》请在冰豆网上搜索。
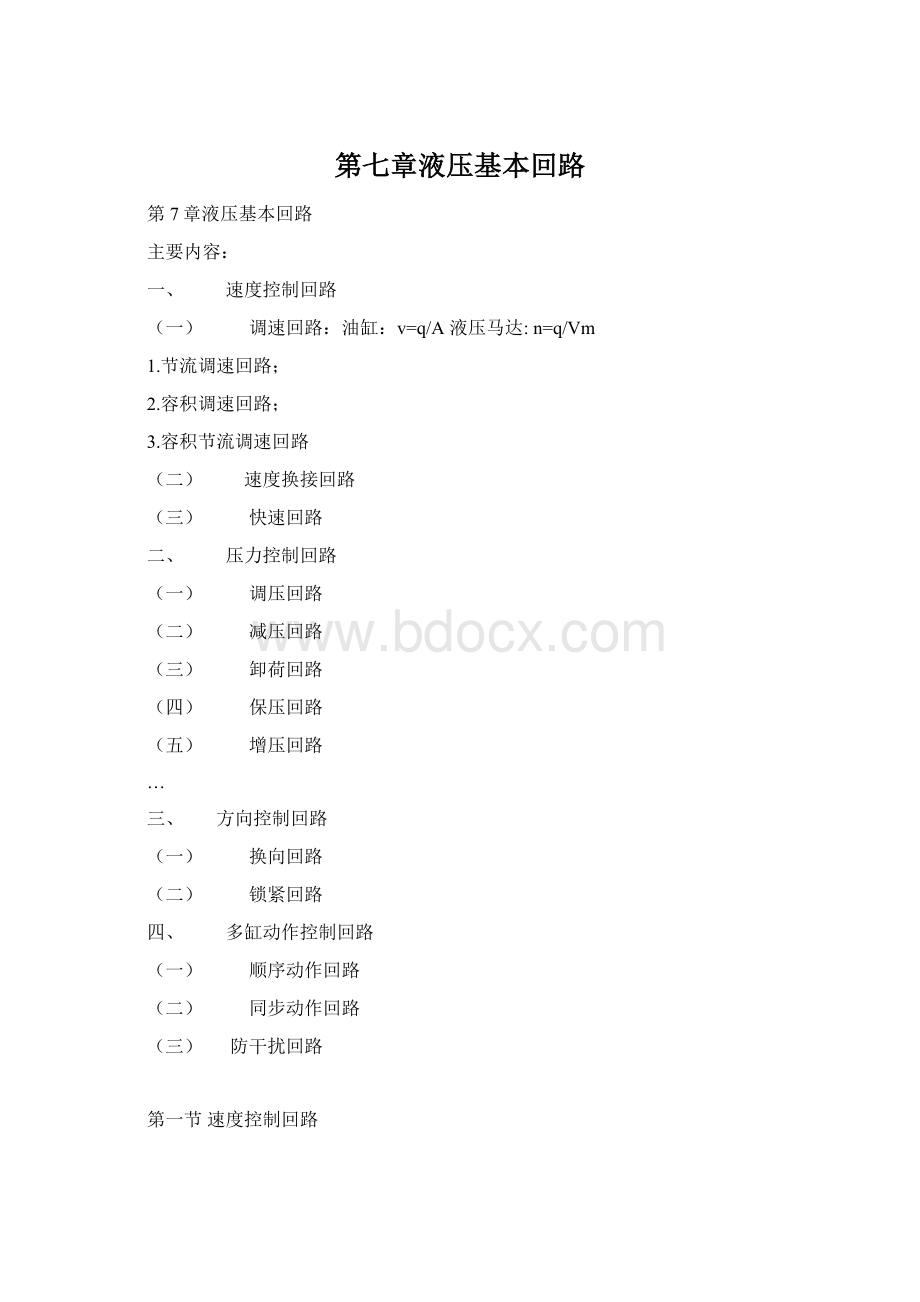
同步动作回路
防干扰回路
第一节速度控制回路
速度控制回路是研究液压系统的速度调节和变换问题,常用的速度控制回路有调速回路、快速回路、速度换接回路等,本节中分别对上述三种回路进行介绍。
一、调速回路
调速回路的基本原理从液压马达的工作原理可知,液压马达的转速nM由输入流量和液压马达的排量Vm决定,即nM=q/Vm,液压缸的运动速度v由输入流量和液压缸的有效作用面积A决定,即v=q/A。
通过上面的关系可以知道,要想调节液压马达的转速nM或液压缸的运动速度v,可通过改变输入流量q、改变液压马达的排量Vm和改变缸的有效作用面积A等方法来实现。
由于液压缸的有效面积A是定值,只有改变流量q的大小来调速,而改变输入流量q,可以通过采用流量阀或变量泵来实现,改变液压马达的排量Vm,可通过采用变量液压马达来实现,因此,调速回路主要有以下三种方式:
1)节流调速回路:
由定量泵供油,用流量阀调节进入或流出执行机构的流量来实现调速;
2)容积调速回路:
用调节变量泵或变量马达的排量来调速;
3)容积节流调速回路:
用限压变量泵供油,由流量阀调节进入执行机构的流量,并使变量泵的流量与调节阀的调节流量相适应来实现调速。
此外还可采用几个定量泵并联,按不同速度需要,启动一个泵或几个泵供油实现分级调速。
1、节流调速回路
图7—1
节流调速原理。
节流调速回路是通过调节流量阀的通流截面积大小来改变进行执行机构的流量,从而实现运动速度的调节。
如图7—1所示,如果调节回路里只有节流阀,则液压泵输出的油液全部经节流阀流进液压缸。
改变节流阀节流口的大小,只能改变油液流经节流阀速度的大小,而总的流量不会改变,在这种情况下节流阀不能起调节流量的作用,液压缸的速度不会改变。
1)进油节流调速回路
进油调速回路是将节流阀装在执行机构的进油路上,起调速原理如图7-2(a)所示.
图7—2(a)进油节流调速回路
A.A.
回路的特点
因为是定量泵供油,流量恒定,溢流阀调定压力为pt,泵的供油压力p0,进入液压缸的流量q1由节流阀的调节开口面积a确定,压力作用在活塞A1上,克服负载F,推动活塞以速度v=q1/A1向右运动。
因为定量泵供油,q1小于qB,所以p0=溢流阀调定供油压力pt=const
活塞受力平衡方程:
p1A1=F+p2A2
进入油缸的流量
q1=Ka▽pm
▽p=pb-F/A1
q1=Ka(pb-F/A1)m
B.B.
进油节流调速回路的速度-负载特性方程为
(7-1)
式中:
k为与节流口形式、液流状态、油液性质等有关的节流阀的系数;
a为节流口的通流面积;
m为节流阀口指数(薄壁小孔,m=0.5)。
由式(7-1)可知,当F
增大,a一定时,速度v减小。
C.进油节流调速回路的速度-负载特性曲线
图7-2(c)速度负载特性
D.进油节流调速回路的优点是:
液压缸回油腔和回油管中压力较低,当采用单杆活塞杆液压缸,使油液进入无杆腔中,其有效工作面积较大,可以得到较大的推力和较低的运动速度,这种回路多用于要求冲击小、负载变动小的液压系统中。
E.回路效率
η=FV/qBp0
qBp0=p0q1+p0qY
=p1q1+▽pq1+p0qY如图:
p1q1=FV有用功率
▽pq1节流损失
pbqY——溢流损失
所以在20%左右
2)回油节流调速回路:
回油节流调速回路将节流阀安装在液压缸的回油路上,其调速原理如图7-2(b)所示。
图7-2(b)回油节
A.回路的特点
因为是定量泵供油,流量恒定,溢流阀调定压力为pt,泵的供油压力p0,进入液压缸的流量q1,液压缸输出的流量q2,q2由节流阀的调节开口面积a确定,压力p1作用在活塞A1上,压力p2作用在活塞A2上,推动活塞以速度v=q1/A1向右运动,克服负载F做功。
因v=q1/A1=q2/A2
q1=q2A1/A2
q1小于qB,所以p0=溢流阀调定供油压力pt=const=p1
p2=(p1A1–F)/A2
F=0时p2=p1A1/A2>p1
q2=Ka▽pm
▽p=p2=(p1A1-F)/A2
q2=Ka[(p1A1-F)/A2]m
B.回油节流调速回路的速度-负载特性方程为:
(7—2)
由式(7-1)可知,当F增大,a一定时,速度v减小。
C.C.
回油节流调速回路的速度-负载特性曲线如图7—2c
D.D.
回油节流调速回路的优点:
节流阀在回油路上可以产生背压,相对进油调速而言,运动比较平稳,常用于负载变化较大,要求运动平稳的液压系统中。
而且在a一定时,速度v随负载F增加而减小。
E.回路效率
η=FV/qBpb
qBpb=pbq1+pbqY
=q1(F+A2p2)/A1+▽pq1+pbqY
=vF+q2p2+pbqy 如图:
q2p2
=▽pq2_______节流损失
所以在20%左右
如图7—2(a)、(b)所示,将节流阀串联在回路中,节流阀和溢流阀相当于并联的两个液阻,定量泵输出的流量qB不变,经节流阀流入液压缸的流量q1和经溢流阀流回油箱的流量
q的大小,由节流阀和溢流阀液阻的相对大小决定。
节流阀通过改变节流口的通流截面,可以在较大范围内改变其液阻,从而改变进入液压缸的流量,调节液压缸的速度。
3)旁路节流调速回路
这种回路由定量泵、安全阀、液压缸和节流阀组成,节流阀安装在与液压缸并联的旁油路上,其调速原理如图7-3所示。
图7—3旁路节流调速回路
定油泵输出的流量qB,一部分(q1)进入液压缸,一部分(q2)通过节流阀流回油箱。
溢流阀在这里起安全作用,回路正常工作时,溢流阀不打开,当供油压力超过正常工作压力时,溢流阀才打开,以防过载。
溢流阀的调节压力应大于回路正常工作压力,在这种回路中,缸的进油压力p1等于泵的供油压力pB,溢流阀的调节压力一般为缸克服最大负载所需的工作压力的p1max1.1~1.3倍.
4)采用调速阀的节流调速回路前面介绍的三种基本回路其速度的稳定性均随负载的变化而变化,对于一些负载变化较大,对速度稳定性要求较高的液压系统,可采用调速阀来改善起速度-负载特性。
图7—4调速阀进油节流调速回路
采用调速阀也可按其安装位置不同,分为进油节流、回油节流、旁路节流三种基本调速回路。
图7-4为调速阀进油调速回路。
图7-4(a)为回路简图,图7-4(b)为其速度—负载特性曲线图。
其工作原理与采用节流的进油节流阀调速回路相似。
在这里当负载F变化而使p1变化时,由于调速阀中的定差输出减压阀的调节作用,使调速阀中的节流阀的前后压差Δp保持不变,从而使流经调速阀的流量q1不变,所以活塞的运动速度v也不变。
其速度—负载特性曲线如图7-4(b)所示。
由于泄漏的影响,实际上随负载F的增加,速度v有所减小。
在此回路中,调速阀上的压差Δp包括两部分:
节流口的压差和定差输出减压口上的压差。
所以调速阀的调节压差比采用节流阀时要大,一般Δp≥5×
105Pa,高压调速阀则达10×
105Pa。
这样泵的供油压力pB相应地比采用节流阀时也要调得高些,故其功率损失也要大些。
这种回路其他调速性能的分析方法与采用节流阀时基本相同。
综上所述,采用调速阀的节流调速回路的低速稳定性、回路刚度、调速范围等,要比采用节流阀的节流调速回路都好,所以它在机床液压系统中获得广泛的应用。
2.容积调速回路
容积调速回路是通过改变回路中液压泵或液压马达的排量来实现调速的。
其主要优点是功率损失小(没有溢流损失和节流损失)且其工作压力随负载变化,所以效率高、油的温度低,适用于高速、大功率系统。
按油路循环方式不同,容积调速回路有开式回路和闭式回路两种。
开式回路中泵从油箱吸油,执行机构的回油直接回到油箱,油箱容积大,油液能得到较充分冷却,但空气和脏物易进入回路。
闭式回路中,液压泵将油输出进入执行机构的进油腔,又从执行机构的回油腔吸油。
闭式回路结构紧凑,只需很小的补油箱,但冷却条件差。
为了补偿工作中油液的泄漏,一般设补油泵,补油泵的流量为主泵流量的10%~15%。
压力调节为3×
105~10×
容积调速回路通常有三种基本形式:
变量泵和定量液动机的容积调速回路;
定量泵和变量马达的容积调速回路;
变量泵和变量马达的容积调速回路。
(1)变量泵和定量液动机的容积调速回路。
这种调速回路可由变量泵与液压缸或变量泵与定量液压马达组成。
其回路原理图如图7-5所示,图7-5(a)为变量泵与液压缸所组成的开式容积调速回路;
图7-5(b)为变量泵与定量液压马达组成的闭式容积调速回路。
图7-5变量泵定量液动机容积调速回路
(a)开式回路(b)闭式回路(c)闭式回路的特性曲线
其工作原理是:
图7-5(a)中活塞5的运动速度v由变量泵1调节,2为安全阀,4为换向阀,6为背压阀。
图7-5(b)所示为采用变量泵3来调节液压马达5的转速,安全阀4用以防止过载,低压辅助泵1用以补油,其补油压力由低压溢流阀6来调节。
其主要工作特性:
1①
速度特性:
当不考虑回路的容积效率时,执行机构的速度nm或(Vm)与变量泵的排量VB的关系为:
nm=nBVB/Vm或vm=nBVB/A(7-5)
上式表明:
因马达的排量Vm和缸的有效工作面积A是不变的,当变量泵的转速nB不变,则马达的转速nm(或活塞的运动速度)与变量泵的排量成正比,是一条通过坐标原点的直线,如图7-5(c)中虚线所示。
实际上回路的泄漏是不可避免的,在一定负载下,需要一定流量才能启动和带动负载。
所以其实际的nm(或Vm)与VB的关系如实线所示。
这种回路在低速下承载能力差,速度不稳定。
②转矩特性、功率特性:
当不考虑回路的损失时,液压马达的输出转矩Tm(或缸的输出推力F)为Tm=VmΔp/2π或F=A(pB-p0)。
它表明当泵的输出压力pB和吸油路(也即马达或缸的排油)压力p0不变,马达的输出转矩Tm或缸的输出推力F理论上是恒定的,与变量泵的VB无关。
但实际上由于泄漏和机械摩擦等的影响,也存在一个“死区”,如图7-5(c)所示。
此回路中执行机构的输出功率:
Pm=(pB-p0)qB=(pB-p0)nBvB或Pm=nmTm=VBnBTm/Vm(7-6)
式(7-6)表明:
马达或缸的输出功率Pm随变量泵的排量VB的增减而线性地增减。
其理论与实际的功率特性亦见图7-6(c)。
③调速范围:
这种回路的调速范围,主要决定于变量泵的变量范围,其次是受回路的泄漏和负载的影响。
采用变量叶片泵可达10,变量柱塞泵可达20。
综上所述,变量泵和定量液动机所组成的容积调速回路为恒转矩输出,可正反向实现无级调速,调速范围较大。
适用于调速范围较大,要求恒扭矩输出的场合,如大型机床的主运动或进给系统中。
(2)定量泵和变量马达容积调速回路。
定量泵与变量马达容积调速回路如图7-6所示。
图7-6(a)为开式回路:
由定量泵1、变量马达2、安全阀3、换向阀4组成;
图7-6(b)为闭式回路:
1、2为定量泵和变量马达,3为安全阀,4为低压溢流阀,5为补油泵。
此回路是由调节变量马达的排量Vm来实现调速。
①速度特性:
在不考虑回路泄漏时,液压马达的转速nm为:
nm=qB/Vm
式中qB为定量泵的输出流量。
可见变量马达的转速nm与其排量Vm成正比,当排量Vm最小时,马达的转速nm最高。
其理论与实际的特性曲线如图7-6(c)中虚、实线所示。
由上述分析和调速特性可知:
此种用调节变量马达的排量的调速回路,如果用变量马达来换向,在换向的瞬间要经过“高转速—零转速—反向高转速”的突变过程,所以,不宜用变量马达来实现平稳换向。
②转矩与功率特性:
液压马达的输出转矩:
Tm=Vm(pB-p0)/2π
液压马达的输出功率:
Pm=nmTm=qB(pB-p0)
马达的输出转矩Tm与其排量Vm成正比;
而马达的输出功率Pm与其排量Vm无关,若进油压力pB与回油压力p0不变时,Pm=C,故此种回路属恒功率调速。
其转矩特性和功率特性见图7-6(c)所示。
图7-6定量泵变量马达容积调速回路
(a)开式回路(b)闭式回路(c)工作特性
综上所述,定量泵变量马达容积调速回路,由于不能用改变马达的排量来实现平稳换向,调速范围比较小(一般为3~4),因而较少单独应用。
(3)变量泵和变量马达的容积调速回路。
这种调速回路是上述两种调速回路的组合,其调速特性也具有两者之特点。
图7-7所示为其工作原理与调速特性,由双向变量泵2和双向变量马达9等组成闭式容积调速回路。
该回路的工作原理:
调节变量泵2的排量VB和变量马达9的排量Vm,都可调节马达的转速nm;
补油泵1通过单向阀3和4向低压腔补油,其补油压力由溢流阀10来调节;
安全阀5和6分别用以防止正反两个方向的高压过载。
液控换向阀7和溢流阀8用于改善回路工作性能,当高、低压油路压差(pB-p0)大于一定值时,液动滑阀7处于上位或下位,使低压油路与溢流阀8接通,部分低压热油经7、8流回油箱。
因此溢流阀8的调节压力应比溢流阀10的调节压力低些。
为合理地利用变量泵和变量马达调速中各自的优点,克服其缺点,在实际应用时,一般采用分段调速的方法。
图7-7变量泵变量马达的容积调速回路
(a)工作原理(b)调速特性
第一阶段将变量马达的排量Vm调到最大值并使之恒定,然后调节变量泵的排量VB从最小逐渐加大到最大值,则马达的转速nm便从最小逐渐升高到相应的最大值(变量马达的输出
转矩Tm不变,输出功率Pm逐渐加大)。
这一阶段相当于变量泵定量马达的容积调速回路。
第二阶段将已调到最大值的变量泵的排量VB固定不变,然后调节变量马达的排量Vm,
之从最大逐渐调到最小,此时马达的转速nm便进一步逐渐升高到最高值(在此阶段中,马达的输出转矩Tm逐渐减小,而输出功率Pm不变)。
这一阶段相当于定量泵变量马达的容积调速回路。
上述分段调速的特性曲线如图7-7(b)所示。
这样,就可使马达的换向平稳,且第一阶段为恒转矩调速,第二阶段为恒功率调速。
这种容积调速回路的调速范围是变量泵调节范围和变量马达调节范围之乘积,所以其调速范围大(可达100),并且有较高的效率,它适用于大功率的场合,如矿山机械、起重机械以及大型机床的主运动液压系统。
3.容积节流调速回路容积节流调速回路的基本工作原理是采用压力补偿式变量泵供油、调速阀(或节流阀)调节进入液压缸的流量并使泵的输出流量自动地与液压缸所需流量相适应。
常用的容积节流调速回路有:
限压式变量泵与调速阀等组成的容积节流调速回路;
变压式变量泵与节流阀等组成的容积调速回路。
图7-8限压式变量泵调速阀容积节流调速回路
(a)调速原理图(b)调速特性图
图7-8所示为限压式变量泵与调速阀组成的调速回路工作原理和工作特性图。
在图示位置,活塞4快速向右运动,泵1按快速运动要求调节其输出流量qmax,同时调节限压式变量泵的压力调节螺钉,使泵的限定压力pC大于快速运动所需压力〔图7-8(b)中AB段〕。
当换向阀3通电,泵输出的压力油经调速阀2进入缸4,其回油经背压阀5回油箱。
调节调速阀2的流量q1就可调节活塞的运动速度v,由于q1<qB,压力油迫使泵的出口与调速阀进口之间的油压憋高,即泵的供油压力升高,泵的流量便自动减小到qB≈q1为止。
这种调速回路的运动稳定性、速度负载特性、承载能力和调速范围均与采用调速阀的节流调速回路相同。
图7-8(b)所示为其调速特性,由图可知,此回路只有节流损失而无溢流损失。
当不考虑回路中泵和管路的泄漏损失时,回路的效率为:
ηc=〔p1-p2(A2/A1)〕q1/pBq1=[p1-p2(A2/A1)]/pB
泵的输油压力pB调得低一些,回路效率就可高一些,但为了保证调速阀的正常工作压差,泵的压力应比负载压力p1至少大5×
当此回路用于“死档铁停留”、压力继电器发讯实现快退时,泵的压力还应调高些,以保证压力继电器可靠发讯,故此时的实际工作特性曲线如图7-8(b)中AB′C′所示。
此外,当pC不变时,负载越小,p1便越小,回路效率越低。
综上所述:
限压式变量泵与调速阀等组成的容积节流调速回路,具有效率较高、调速较稳定、结构较简单等优点。
目前已广泛应用于负载变化不大的中、小功率组合机床的液压系统中。
4.调速回路的比较和选用
(1)调速回路的比较。
见表7-1。
表7-1调速回路的比较
回路类
主要性能
节流调速回路
容积调速回路
容积节流调速回路
用节流阀
用调速阀
限压式
稳流式
进回油
旁路
机械特性
速度稳定性
较差
差
好
较好
承载能力
调速范围
较大
小
大
功率特性
效率
低
较高
最高
高
发热
较小
最小
适用范围
小功率、轻载的中、低压系统
大功率、重载高速的中、高压系统
中、小功率的中压系统
(2)调速回路的选用。
调速回路的选用主要考虑以下问题:
①执行机构的负载性质、运动速度、速度稳定性等要求:
负载小,且工作中负载变化也小的系统可采用节流阀节流调速;
在工作中负载变化较大且要求低速稳定性好的系统,宜采用调速阀的节流调速或容积节流调速;
负载大、运动速度高、油的温升要求小的系统,宜采用容积调速回路。
一般来说,功率在3kW以下的液压系统宜采用节流调速;
3~5kW范围宜采用容积节流调速;
功率在5kW以上的宜采用容积调速回路。
图7-9能实现差动连接工作进给回路
②工作环境要求:
处于温度较高的环境下工作,且要求整个液压装置体积小、重量轻的情况,宜采用闭式回路的容积调速。
③经济性要求:
节流调速回路的成本低,功率损失大,效率也低;
容积调速回路因变量泵、变量马达的结构较复杂,所以价钱高,但其效率高、功率损失小;
而容积节流调速则介于两者之间。
所以需综合分析选用哪种回路。
二、快速运动回路
为了提高生产效率,机床工作部件常常要求实现空行程(或空载)的快速运动。
这时要求液压系统流量大而压力低。
这和工作运动时一般需要的流量较小和压力较高的情况正好相反。
对快速运动回路的要求主要是在快速运动时,尽量减小需要液压泵输出的流量,或者在加大液压泵的输出流量后,但在工作运动时又不致于引起过多的能量消耗。
以下介绍几种机床上常用的快速运动回路。
图7-10双泵供油回路
1.差动连接回路这是在不增加液压泵输出流量的情况下,来提高工作部件运动速度的一种快速回路,其实质是改变了液压缸的有效作用面积。
图7-9是用于快、慢速转换的,其中快速运动采用差动连接的回路。
当换向阀3左端的电磁铁通电时,阀3左位进入系统,液压泵1输出的压力油同缸右腔的油经3左位、5下位(此时外控顺序阀7关闭)也进入缸4的左腔,进入液压缸4的左腔,实现了差动连接,使活塞快速向右运动。
当快速运动结束,工作部件上的挡铁压下机动换向阀5时,泵的压力升高,阀7打开,液压缸4右腔的回油只能经调速阀6流回油箱,这时是工作进给。
当换向阀3右端的电磁铁通电时,活塞向左快速退回(非差动连接)。
采用差动连接的快速回路方法简单,较经济,但快、慢速度的换接不够平稳。
必须注意,差动油路的换向阀和油管通道应按差动时的流量选择,不然流动液阻过大,会使液压泵的部分油从溢流阀流回油箱,速度减慢,甚至不起差动作用。
2.双泵供油的快速运动回路这种回路是利用低压大流量泵和高压小流量泵并联为系统供油,回路见图7-10。
图中1为高压小流量泵,用以实现工作进给运动。
2为低压大流量泵,用以实现快速运动。
在快速运动时,液压泵2输出的油经单向阀4和液压泵1输出的油共同向系统供油。
在工作进给时,系统压力升高,打开液控顺序阀(卸荷阀)3使液压泵2卸荷,此时单向阀4关闭,由液压泵1单独向系统供油。
溢流阀5控制液压泵1的供油压力是根据系统所需最大工作压力来调节的,而卸荷阀3使液压泵2在快速运动时供油,在工作进给时则卸荷,因此它的调整压力应比快速运动时系统所需的压力要高,但比溢流阀5的调整压力低。
双泵供油回路功率利用合理、效率高,并且速度换接较平稳,在快、慢速度相差较大的机床中应用很广泛,缺点是要用一个双联泵,油路系统也稍复杂。
三、速度换接回路
速度换接回路用来实现运动速度的变换,即在原来设计或调节好的几种运动速度中,从一种速度换成另一种速度。
对这种回路的要求是速度换接要平稳,即不允许在速度变换的过程中有前冲(速度突然增加)现象。
下面介绍几种回路的换接方法及特点。
1.快速运动和工作进给运动的换接回路图7-11是用单向行程节流阀换接快速运动(简称快进)和工作进给运动(简称工进)的速度换接回路。
在图示位置液压缸3右腔的回油可经行程阀4和换向阀2流回油箱,使活塞快速向右运动。
当快速运动到达所需位置时,活塞上挡块压下行程阀4,将其通路关闭,这时液压缸3右腔的回油就必须经过节流阀6流回油箱,活塞的运动转换为工作进给运动(简称工进)。
当操纵换向阀2使活塞换向后,压力油可经换向阀2和单向阀5进入液压缸3右腔,使活塞快速向左退回。
在这种速度换接回路中,因为行程阀的通油路是由液压缸活塞的行程控制阀芯移动而逐渐关闭的,所以换接时的位置精度高,冲出量小,运动速度的变换也比较平稳。
这种回路在机床液压系统中应用较多,它的缺点是行程阀的安装位置受一定限制(要由挡铁压下),所以有时管路连接稍复杂。
行程阀也可以用电磁换向阀来代替,这时电磁阀的安装位置不受限制(挡铁只需要压下行程开关),但其换接精度及速度变换的平稳性较差。
图7-11用行程节流阀的速度换接回路图7-12利用液压缸自身结构的速度换接回路
图7-12是利用液压缸本身的管路连接实现的速度换接回路。
在图示位置时,活塞快速向
右移动,液压缸右腔的回油经油路1和换向阀流回油箱。
当活塞运动到将油路1封闭后,液压缸右腔的回油须经节流阀3流回油箱,活塞则由快速运动变换为工作进给运动。
这种速度换接回路方法简单,换接较可靠,但速度换接的位置不能调整,工作行程也不能过长以免活塞过宽,