FPC检验规范 2Word下载.docx
《FPC检验规范 2Word下载.docx》由会员分享,可在线阅读,更多相关《FPC检验规范 2Word下载.docx(35页珍藏版)》请在冰豆网上搜索。
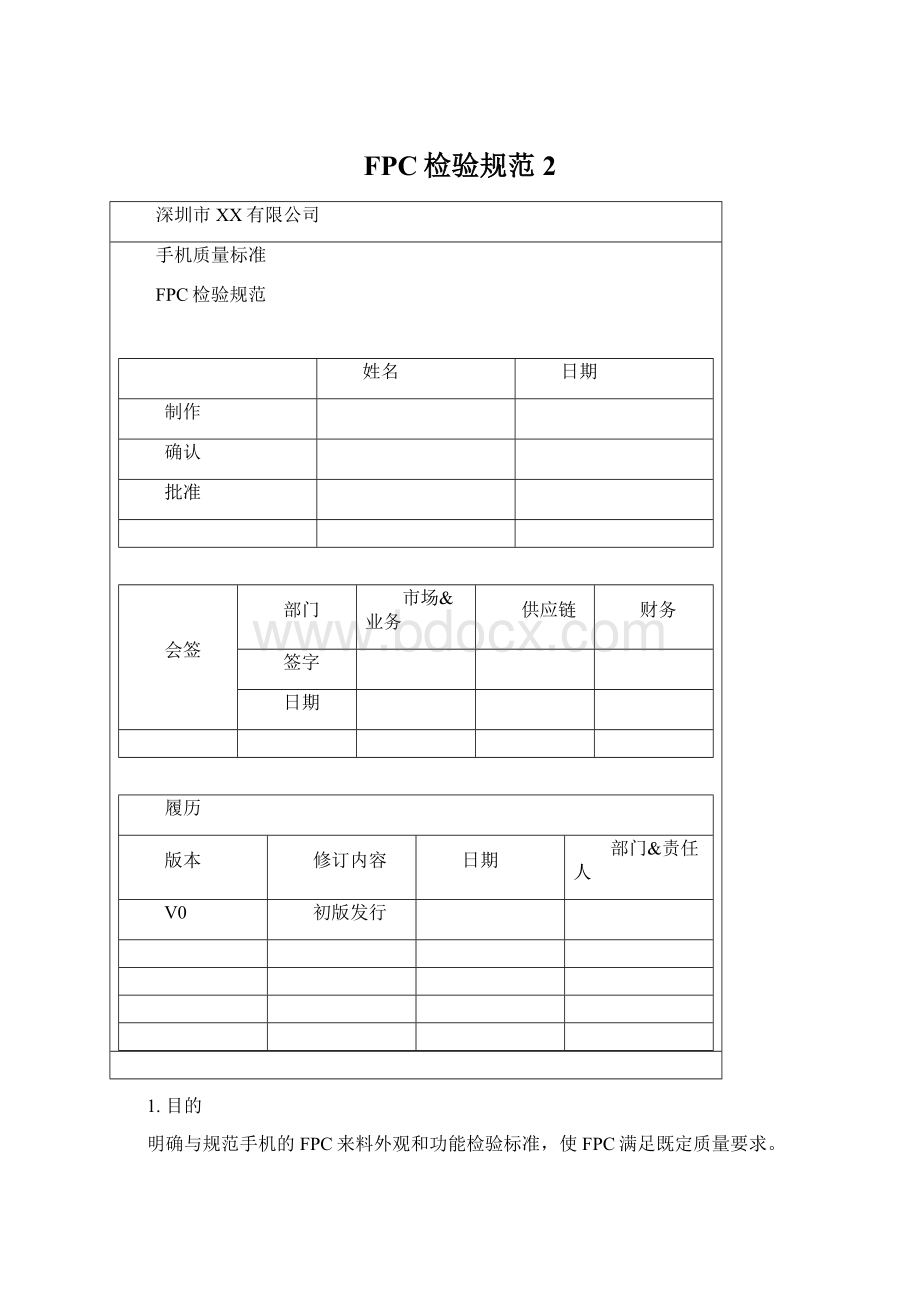
Min:
会引起客户对产品的满意度,但功能仍能使用,并不会导致客户的投诉、退换货,例如轻微外观问题、包装问题等。
5.检验条件及环境
5.1、在60—100W日光灯的照明条件下,样品离检查者眼睛约30-40cm处进行检查。
检验方向以垂直线前后左右45°
(以时钟3点、6点、9点、12点).
5.2、检验者需戴手指套防护。
5.3、检测条件
照度:
800-1200LUXfluorescentlamps.日光灯照度为:
800-1200LUX环境:
22±
3℃
5.4、外观检验者以目视检查,尺寸用卡尺测量。
5.5、电性测试使用夹具,检验功能标准请依样品。
5.6、若标准与规格书不符时,以产品发行之规格书特殊检验规格、工程变更为准。
6.包装要求
6.1包装检验
序号
缺陷名称
描述
1
无标识
内包装袋或外包装箱未贴标签纸或现品票。
2
标识错误
标识的产品名称、编码、数量等与内装产品不符,或标识内容不全。
3
产品混装
不同产品或不同模号的产品混装在一起。
4
包装材料不符
胶袋外箱、珍珠棉、纸箱、吸塑盘的规格尺寸不合要求,或未按规范包装。
5
包装材料破损
包装材料破损,难以对货物起到保护作用。
6.2包装要求
1、产品外包装为纸箱包装,内包装须用指定的袋子和盘;
2、现品票应粘在纸箱的右上角,其内容包括:
物料名称、物料编码、规格、机型、数量、生产日期、QA检验合格章和特殊标示要求。
7.检验内容
7.1外观检验标准
项目
缺点类别
不良定义
不良图片描述
判定标准
检查方法
成型外观
板边破损
重缺陷
FPC本体在成型后,本体表面与板边的破损状态
边缘缺损范围不可超过板边至最近导体所形成间距的1/2或未超过2.5mm(取其中较小者)
10倍放大镜
折/压/针痕
FPC本体(导体、CL、基材)及金手指在成型后,因制程组装或其它外力所造成的损伤痕迹
1.FPC板面不可形成锐角(死折),压痕不可透过FPC背面凸起(背面不可反白),导体针痕应小于0.1mm
2.测试针痕不可露镍、铜
3.镀层区域折、压痕(包含输入、输出端子部位),需平整,不可有裂痕
导体刮痕
是由锐利金属或其他尖锐物对导体所造成的刮痕,对导体形成明显伤害
无保护膜覆盖部位,不可露铜、镍
外型毛边
轻缺陷
FPC在冲切外型时,所造成的FPC外型有毛刺或毛边产生
导体、非导体毛边长度需小于0.2mm或需小于导体线距之1/2(取其中较小者,不可脱落,导体不可与内部线路接触)
孔穴毛边
FPC在冲切孔时,所造成的孔穴毛刺或毛边,有时将会影响后段元件之组装不良
1.零件孔内不可影响组装或焊接功能
2.非零件孔内毛边不可大于0.2mm
冲切段差
FPC遇多段冲切成型时,因前后冲切精度所造成之外型尺寸段差
段差不可大于0.2mm(一、二冲间)
备注:
不可冲切到最外边之导体
板翘
FPC空板成型后之外观产生不平坦、弯曲或皱褶的现象
1.FPC本体以手指按FPC的其中一边,另一边翘曲不得超过15mm(H<
15mm)
2.输出端子部板翘不可超过5mm(置于平台上)
3.条状多片型态出货之产品(简称连扳出货),板翘标准小于8mm,且不可对SMT焊接作业造成影响
目视及尺规
残胶
FPC之接着剂在经制程或冲切成型过程中所形成的接着剂碎屑残留
1.导体不可有残胶
2.残胶直径(d):
1.0mm≤d<
2.0mm,每片FPC不超过5个以上.
表面油污
因制程不慎在FPC空板表面上形成油污,造成FPC外观不佳
不可有表面油污
目视
断路
FPC上的导体线路,因制程或其他因素所产生的导体断线现象
导体不可发生断路
NA
短路
FPC上的导体线路,因制程或其他因素所产生导体的不正常跨接,会产生功能性问题
1.导体不可有短路发生
2.保护膜下共同回路之短路可不判定
残铜
FPC上的导体线路,因制程或其他因素在导体间距中产生导体的残留,残留导体范围过大将引起线路间绝缘度下降,产生绝缘不良现象
L1≤2S1,A1≤1/2S1
L2≤2S2,A2≤1/2S2
针孔
因制程及其他因素,在FPC导体线中所发生之细微孔洞.针孔过大将导致线路阻值过高及讯号传输失真
1.线路针孔宽<
线宽1/3,长度不可超过1mm.
2.无线路(大铜箔区)针孔长度不可大于1mm.
3.焊盘区针孔不可超过焊盘整体面积的20%.
4.输入/输出端子部位,比照导体标准判定(在连接器接触区域不允收)
缺口
因制程及其他因素所引起的FPC线路导体的宽度缺损,其缺损的长度与成品的导体宽度应符合一定之比例原则,避免造成电流传导及讯号传出的障碍
1.L≤WA≤1/3W.
2.焊盘区域缺口不可超过焊盘整体面积的20%.
3.输入/输出端子部位,比照导体标准判定(在连接器接触区域不允收
变色
FPC导体部位因制程因素所产生的线路变色现象
1.不可有手指纹变色.
2.保护膜下线路变色不可超过线路总面积的10%
剥离
FPC导体线路因制程及结构所产生之应力,造成导体与绝缘基材间分离的现象
1.金手指前端浮铜≤0.2mm,可允收.
2.焊盘区:
未超过焊盘面积的10%,可允收.
龟裂
FPC导体线路因制程及结构所产生之应力,造成导体产生裂缝,将造成电流传导及讯号传输之不良或中断
镀通孔孔环破出
FPC在线路曝光制程中,因材料涨缩或对位偏移问题,造成镀通孔部分孔壁区域破出孔环,在蚀刻(DES)制程中由于破出孔环的镀通孔壁未能得到盖孔干膜保护,因此蚀刻液可能会由此渗入,造成孔壁凹蚀或不完整等现象
1.镀通孔之孔环破出之周长超过1/4以上,不允收
2.线路和孔环交接处,不可破环
偏移
FPC贴合透明保护膜时,因贴合精度及对位不良造成的贴合偏差
1.保护膜偏移不可超过+/-0.3mm
2.保护膜偏移不可让邻接线路导体露出
3.圆环式焊盘覆盖膜偏移,最小导体裸露宽度D需大于0.05mm
4.焊盘焊接有效面积需达75%以上
溢胶
FPC于贴合保护膜时,需在高温、高压作业,保护膜接着剂会因制程、产品特性等因素,而有接着剂溢出之现象
1.保护膜接合处溢胶(F)≥0.3mm,不允收
2.焊盘焊接有效面积需达75%以上
气泡
FPC在进行保护膜压合时,因材料搭配因素或压合制程不当,所形成外观有气泡现象
1.保护膜气泡不应跨越2条导线
2.板边气泡不允许
异物
FPC在进行保护膜贴合时,因外来杂质污染,造成保护膜贴合后有异物附着产生
1.导电异物依1-2-3残铜标准判定
2.异物造成保护膜凸起或剥离,不允收
3.非导电性异物横跨第三条线路,不允收
4.非线路区域杂质长度超过2mm,不允收
刮痕
保护膜在贴合制程或之后工序中,受外力及异物刮伤而形成之保护膜外观伤痕
1.刮痕不能露出导体.
2.刮痕深度(d)≤1/3保护膜厚度(L)
液态感光油墨(LPI)/防焊油墨
缺墨
FPC在以油墨或液态感光油墨进行导体线路覆盖时,因印刷制程条件不当或油墨特性不佳,所形成的涂膜印制缺陷
1.不允许导体裸露.
2.非导体区域缺墨小于直径0.5mm.
3.板边缺墨以保护膜破损标准判定.
溢墨
FPC在以油墨或液态感光膜进行导体线路覆盖时,因印刷制程条件不当或涂墨印刷特性(流变特性)不佳,所形成的涂墨渗漏现象
1.溢墨≥0.2mm,不允收
2.焊盘有效面积需达75%
3.残留在接触区中者不允收
FPC在以油墨或液态感光保护涂膜进行导体线路覆盖时,因材料涨缩或曝光对位偏移,所形成的偏移现象
1.偏移不可让邻接线路露出
2.圆环焊盘覆盖偏移,最小圆环导体裸露宽度需大于0.05mm
3.焊盘有效面积需达75%
FPC在以油墨或液态感光保护涂膜进行导体线路覆盖时,因印刷制程及后段硬化烘烤条件不当形成的涂液(膜)产生气泡的现象.
1.不应有气泡跨越2条导线.
FPC在以油墨或液态感光保护涂膜进行导体线路覆盖时,因制程环境外来杂质污染,所形成的涂液(膜)产生杂质异物
1.导电性异物依1-2-3残铜标准判定
2.异物造成油墨凸起超过总厚度或剥离,不允收
表面刮痕
FPC在以油墨或液态感光保护涂膜进行导体线路覆盖后,在后段制程工序中受外力及异物刮伤而形成之保护涂膜外观伤痕
2.刮痕深度(d)≤1/3油墨厚度(L)
印刷油墨
文字偏移
PC在完成线路制程后,以油墨印刷文字及号码作为成品识别及其他标识之用,因油墨印刷制程条件不当,造成油墨印刷偏移之现象
1.焊盘表面不可有印刷油墨附着
2.印刷偏移量需≤0.3mm
文字模糊
FPC在完成线路制程后,以油墨印刷文字、号码作为成品识别及其他标识之用,因油墨品质特性不佳或印刷条件不当,造成印刷之文字产生模糊而无法辨识之现象
1.所印文字无法看出其字体及辨识其意思,判定不允收。
2.所印文字以胶带测试其附着特性,需无法剥离
3M-600胶带
补强板贴合
在FPC接续部位使用接着剂及补强材料进行补强板贴合,因接着剂特性或贴合制程控制不当,造成FPC与补强板间产生气泡,影响两者间的接着特性
1.使用热固型接着剂补强材料,气泡不可大于所粘接补强材料面积的10%。
2.使用其他接着剂补强材料,气泡不可大于所粘接补强材料面积的1/3.
3.气泡造成总厚度增加需符合天珑公司要求
在补强材料贴合制程中因制程环境之外来污染,造成FPC在补强材料贴合后有表面凸起之现象
1.异物面积大小不可超过补强材料贴合面积的10%.
2.补强材料中异物造成之FPC凸起,不可影响其总厚度
贴合偏移
在补强材料贴合制程中因制程条件控制不当,而造成补强材料在贴合后产生贴合位置的偏移
1.接着剂或补强胶片偏移(含胶溢出)不可超过+/-0.3mm.
2.不允许有补强材料因偏移而覆盖FPC孔穴
接着不足(分层)
PC接续部位使用补强材料进行补强板贴合,因接着剂特性不佳或贴合制程控制不当,造成FPC与补强板间贴合性不足而产生二者分层之状况
不可有分层现象发生
补强板毛边
所贴合之补强板材料因冲切制程精度控制不良,在其边缘产生碎屑或毛边
补强板毛边<
0.3mm.
表面处理(镀层或皮膜)
镀层变色
因镀层制程处理不当,造成镀层表面色差、变色之外观现
1.变色(黑化)不允收。
2.不应有目视可见之明显红斑、指纹、污迹
镀层露铜
因镀层前制程处理不完全,造成杂质残留而产生导体局部无法上镀现象
1.整支导体未上镀不允收。
2.输入、输出端子露铜,宽<
1/3线宽,长度<
线宽,连接器接触部位、按键(keypad)不可露铜.
3.焊盘露铜需小于可焊面积25%.
4.大铜面镀层区域裸铜需小于0.2mm
焊锡(金)渗入
因保护膜贴合不良或镀层制程控制不当,致使镀液渗入导体与Coverlay(或防焊油墨)之介面,造成导体表面有轻微变色之现象
导体与保护膜介面其焊锡(金)层之渗入长度≥0.5mm,不允收
镀层厚度不足
FPC表面镀层因制程控制不当,造成镀层厚度不足,可能影响后段组装良率
\
镀层厚度需符合规格书要求
镀层色差(白雾)
FPC表面镀层,因前处理制程或药水使用不当,造成镀层表面有轻微白雾色差现象
1.镀层白雾状无法去除者允收
2.焊接区域允收
3.输入/输出端子部位,目视不允收
镀(化)金残留
以镀(化)金作为FPC表面镀层,因镀层制程条件控制不当或其他因素,造成镀化金残留
1.依据导体残铜允收标准判定
2.线距间残金,不允收
3.线宽需符合图面公差
镀层气泡与浮离
因镀层制程控制不当,使得镀层产生气泡,严重则造成镀层浮离,将会影响镀层品质进而使后段元件组装制程产生不良
不允许有镀层产生气泡与浮离发生
搭载元件组装板:
零件焊接
缺件
因焊接制程不良或其他因素,使零组件没有焊接于其上的缺件现象,将造成FPC组装不良无法发挥其功能.
允收标准
组装制程不允许缺件发生
错件
因焊接制程不良或其他因素,使零组件未按原焊接位置安排,而发生错误焊接现象
组装制程不允许错件发生
元件反向
因零组件未按工程资料中之正确面向或极性进行焊接,而发生元件反向焊接现象,此项FPC组装不良将使FPC无法发挥其正常功能
组装制程不允许发生反向与极性错误之焊接
元件位置偏移
因焊接制程不良或其他因素,使零组件焊接发生位置偏移现象
1.偏移量>
1/2焊盘宽度或1/2零件宽度(取其中较小者),不允收
2.偏移若接触到邻近线路者,不允收
3.零件脚端两端同时偏移突出焊盘,且双向突出不在同一侧(歪斜),不允收
空、冷焊
焊接制程不良或其他因素,使零件进行焊接而发生零组件末端爬锡不良之现象
组装制程不允许元件发生空焊及冷焊
焊接制程不良或其他因素,使零组件进行焊接时发生零组件接脚焊锡产生跨接,造成FPC焊接短路现象
组装制程不允许元件发生焊接短路问题
零件粘锡
因焊接制程不良或其他因素,使零组件进行焊接时发生零组件陶瓷/金属/塑胶(SOT23元件除外)本体粘锡现象
零组件陶瓷/金属/塑胶(SOT23元件除外)本体粘锡现象,不允许
助焊剂残渣
FPC在进行元件搭载组装时,为使焊接状态良好需使用助焊剂,焊接完毕后助焊剂不能残留于零组件导体位置
零件接触内PIN或其他未焊接金手指、焊盘部位残留助焊剂,不允收
吃锡量
因焊接制程不良或其他因素,使零组件在焊接时发生接脚吃锡量不足,造成零件焊接强度不足
1.片式(chip)元件吃锡高度必须高于零件高度的1/4.
2.露焊盘面积小于有效面积的10%,均可接受
元件侧立
FPC在进行后段元件搭载组装时,因焊锡制程不良或其它因素产生零件侧立现象
焊接零件侧立,皆不允收
元件缺陷/破损/污痕
FPC在进行后段元件搭载组装时,因所欲焊接之零组件有缺陷、破损、污痕等缺点
1.零件不可有破裂及破损情况
2.零件及FPC本体区不能有脏污、毛屑及杂质
连接器焊接
焊接偏移
FPC在进行后段元件搭载组装时,因焊接制程不良或其他因素,可能造成焊接位置偏移,导致FPC整体组装外观及连接导通电性不佳
1/3焊盘宽度或1/3零件脚宽度(较小者),不允收
2.偏移若接触到邻边线路,不允收
3.连接器端横向偏移突出基板焊盘端边界,不允收
浮离
FPC在进行后段元件搭载组装时,连接器因焊接制程不良或其他因素发生焊接浮离现象
1.连接器浮高(H)不可超过0.1mm
2.吃锡量须符合元件焊接吃锡规定
FPC空板在进行后段元件搭载组装时,因焊接制程不良或其他因素造成连接器吃锡量不足,可能导致焊接强度不足及连接导通电性能与长期可靠性不佳
1.PIN两侧或前端吃锡高度需高于连接器PIN总高度之1/3
2.如连接器PIN偏移,单侧吃锡需达连接器PIN总高度之1/2
3.露焊盘面积需小于有效面积的10%,可允收
FPC在进行后段元件搭载组装时,因焊接制程不良或其他因素,使连接器未按原位置安排发生错误焊接,使FPC无法发挥正常功能
不允许连接器错件焊接发生
PC在进行后段元件搭载组装时,为使连接器焊接状态良好需使用助焊剂,焊接完毕后助焊剂不能残留于零组件之导体位置,以免影响FPC之最终电性功能
连接器接触内PIN或其他未焊接手指、焊盘部位残留助焊剂者,不允收
端子变形
FPC进行后段元件搭载组装时,连接器端子受不当外力或制程应力变形
连接器端子变形,不允收
溢锡
FPC在进行后段元件搭载组装时,因焊接制程不良或其他因素,使连接器有过多锡量虹吸溢至端子内,造成不必要粘附或形成连接器焊接短路
连接器之接触端子,溢锡超过连接器高度之1/3者,不允收
沾锡
FPC在进行后段元件搭载组装时,因焊接制程不良或其他因素,使连接器端子间或本体产生不必要焊锡沾附,可能造成连接器焊接短路
1.连接器内接触PIN沾锡,不允收
2.连接器塑胶本体不可沾锡。
3.金手指不可沾锡
混料
不同型号板混入
有不同型号板混入现象
不允许
不合格品混入
已经确认为不合格品的产品混入良品
材料误用
使用材料非客户指定或非设计要求
7.2性能检验标准
测量项目
检验方法
接受标准
测量工具
抽样数量
功能测试
把来料产品固定在夹具上测试
测试功能良好
功能测试治具
B类缺AQL:
0.4
7.3尺寸检验标准
测量方法
实装配
按整机组装位置与相应部件(connector等)进行组装适配。
符合整机装配要求
相关附配件
5pcs/lot
尺寸超差
用卡尺或投影仪测量产品的关键、重要尺寸及装配尺寸
尺寸在工程设计规格内
卡尺或投影仪
镀层厚度
镀层厚度依据客户要求
符合产品规格书标准
X-荧光测试仪
8.可靠性试验
检验项目
检验工具
高温贮存
温度85±
2°
C,试验时间96小时,回温2H后检测功能、外观、机械性能和待机电流
FPC外观、性能良好
恒温恒湿箱
2pcs/lot
低温贮存
温度为−40±
3°
C,试验时间96小时,回温2H后检测功能、外观、机械性能和待机电流
恒温恒湿
温度为40±
2℃;
湿度为95±
3%;
放置时间为96小时,回温2H后检测功能、外观、机械性能和待机电流
镀层表面不可产生氧化,产品不可有起泡、剥离、分层,产品电性功能完好线路导通阻抗<
20Ω,线路间绝缘阻抗>
5MΩ
高低温冲击
被测产品不包装、不工作状态放进试验箱内。
低温为-65℃,稳定温度保持时间15min;
高温为125℃,稳定温度保持时间15min;
转换时间不大于1min,在正常大气条件下放置2h。
放置时间满后,被测样机进行试验后检查。
产品镀层表面不可产生氧化,产品不可有起泡、剥离、分层,产品电性功能完好(线路导通阻抗<
5MΩ),测试前后线路阻值变化率≤±
10%
自由跌落试验
FPC正常装配整机,从1.2米的高度自由落体跌至水泥地面,X、Y、Z三个方面各2次
样机
6
机械冲击试验
FPC正常装配整机,被测样机不包装、处于通电待机状态。
脉冲波型:
半正弦波;
峰值加速度:
30g;
持续时间:
16ms;
轴向:
三轴六个方向(若确认试验样品有对冲击最敏感的、最薄弱的方向,则只需要对该方向进行试验);
冲击次数:
每方向冲击3次,共18次。
试验样品应直接用安装夹具钢性的固定在试验台面上,载荷应尽可能均匀分布,作用中心尽量靠近台面中心。
试验结束,取出被测样机进行试验后检查
样机、振动台
7
振动试验
FPC正常装配整机,频率范围10-55Hz,振幅1.5M,轴向:
X/Y/Z三个轴向,持续时间:
每个轴向2小时,共6小时。
持续时间结束,取出被测样机进行试验后检查
震动机
8
弯折测试
FPC弯折区180°
弯折200次后测试功能
FPC性能良好
手动
9
拉力测试
拉力值=FPC金手指长度×
0.62