车床拔叉课程设计Word格式文档下载.docx
《车床拔叉课程设计Word格式文档下载.docx》由会员分享,可在线阅读,更多相关《车床拔叉课程设计Word格式文档下载.docx(25页珍藏版)》请在冰豆网上搜索。
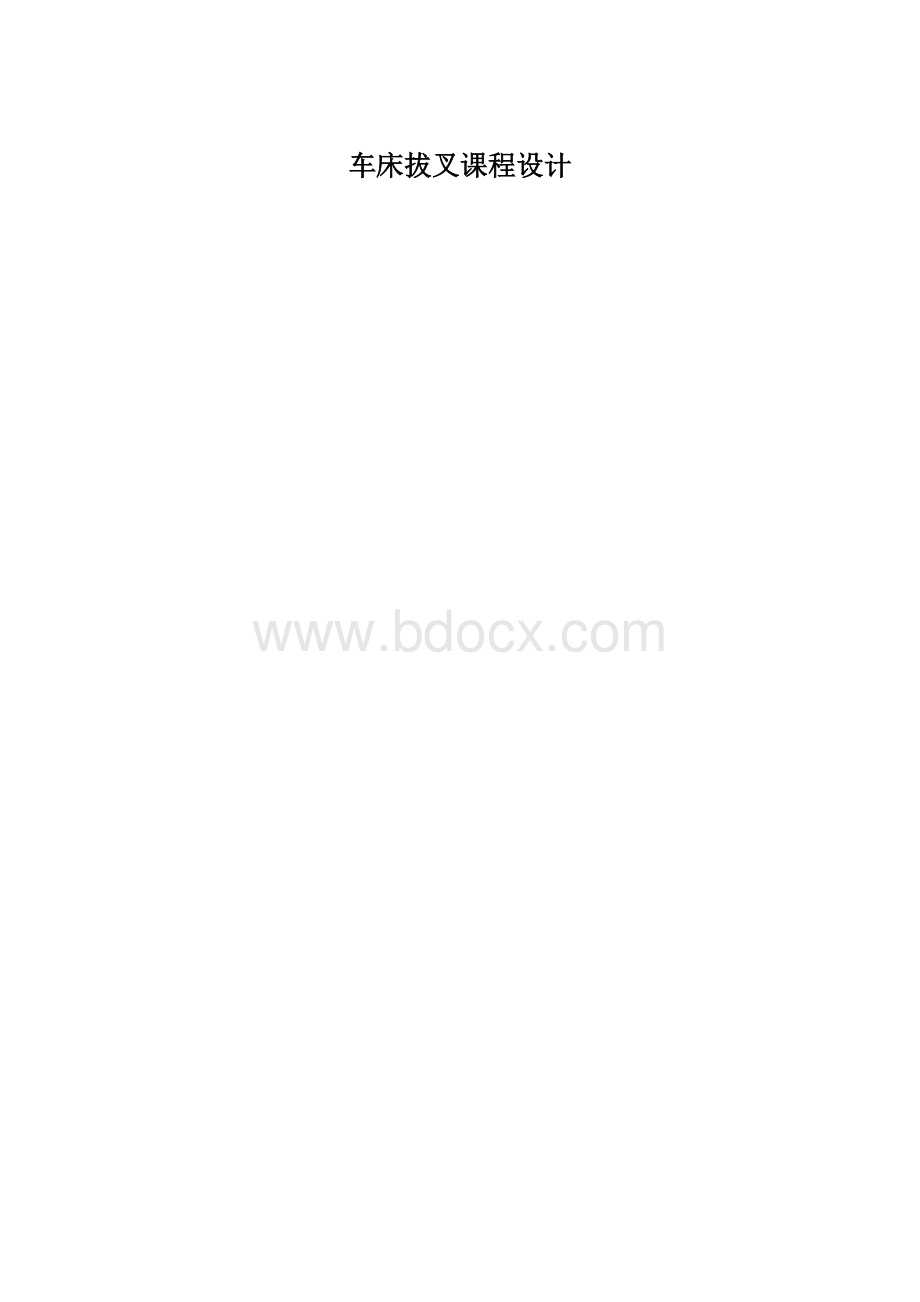
拨叉的生产类型为大批生产。
1.2确定毛坯类型绘制毛坯简图
1.2.1选择毛坯
根据生产类型,零件的结构、形状、尺寸及材料等选择毛坯的制造方式和精度。
1.毛坯的类型选择
①零件的材料及力学性能
当零件的材料选定后,毛坯的类型就大致确定了。
例如,材料为铸铁,就选择铸造毛坯;
材料是钢材且力学性能要求高时,可选锻件等。
锻造材料主要是各种碳钢与合金钢。
②零件的结构、形状、尺寸
形状复杂的毛坯常用铸造方法,如箱体、机架、底座等。
用于铸造的材料有灰铸铁、可锻铸铁、球墨铸铁、铸钢、有色金属合金等。
形状比较简单的零件毛坯,如轴类、套类、盘类、板类、长条类等零件,一般采用型材。
型材的种类主要有圆、方、六方棒料,板材,管材,角钢,工字钢等。
薄壁零件不可用砂型铸造;
常见的一般用途的钢质阶梯轴零件,如各台阶的直径相差不大,可用棒料;
如各台阶的直径相差较大,宜用锻件等。
2.毛坯的制造方法
①生产类型
大量生产时应选精度和生产率都比较高的毛坯制造方法,如金属型铸造、精密铸造、模锻、冷冲压、粉末冶金等,使毛坯的形状更接近于零件的形状。
在单件小批生产中,一般采用木模手工砂型铸造和自由锻造。
②生产条件
③充分考虑使用新工艺、新技术和新材料的可能性。
综合考虑为满足技术要求决定采用铸造成型制造毛坯。
1.2.2确定毛坯的外形、尺寸公差和机械加工余量
1、毛坯外形确定
根据任务书,车床拔叉零件是以一条中心线为对称的一半,并且拔叉内表面的粗糙度要求为1.6,比较高,而侧面要求为25,比较低。
而零件为半圆,如果采用铰刀加工,加工时会因为两侧受力不均达不到精度要求,所以考虑将对称的另一半也同时铸造,等加工好后,用切割机床从中间切断,就可以一次性获得两件成品。
这样加工工艺更简便,并且满足批量生产的要求。
另外除了拨叉脚两端面、拨叉脚内表面和叉轴孔精度要求较高,其他部分都可以直接通过铸造成型,所以毛坯效果图1设计如下。
2、尺寸公差和机械加工余量确定
毛坯余量是指同一表面上毛坯尺寸与零件设计尺寸之差。
零件表面的加工总余量不仅与表面各工序加工余量有关,而且与毛坯的制造方法和精度有关。
(1)铸件毛坯的尺寸公差、加工余量
铸件尺寸公差由高到低分为CT1~CT16共16个等级(GB/T6414—1999),其公差带数值如下表2所示,铸件尺寸公差一般对称分布如95±
4.5(CT13),非对称分布需要在基本尺寸后面标注偏差,如
(CT13)。
成批和大量生产的铸件,毛坯的公差等级按表3选取;
单件和小批生产的铸件,毛坯的公差等级按表4选取。
要求的铸件机械加工余量分10个等级(GB/T6414—1999)如表5所示,由小到大分别为A、B、C、D、E、F、G、H、J和K级,用代号RMA表示。
铸件的机械加工余量等级主要与生产类型、铸造工艺方法、铸造公差等级和铸造材料有关。
推荐用于各种铸造合金和铸造方法的RMA等级按表6选取。
铸件的机械加工余量分单侧(单面)和双侧(双面),双侧加工余量与加工要求的关系
表2铸件的尺寸公差(带)数值(GB/T6414-1999)mm
表3成批和大量生产的毛坯铸件的公差等级mm
方法
公差等级CT
铸件材料
钢
灰铸铁
球墨铸铁
可锻铸铁
铜合金
锌合金
轻金属合金
镍基合金
钴合金
砂型铸造
手工造型
11~14
10~13
9~12
砂型铸造机器
造型和壳型
8~12
8~10
7~9
金属型铸造(重力铸造或低压铸造)
——
压力铸造
6~8
4~6
4~7
熔模铸造
水玻璃
5~8
硅溶胶
注:
1.表中所列出的公差等级是指在大批量生产下、且影响铸件尺寸精度的生产因素已得到充分改进时铸件通常能够达到的公差等级。
2.本标准还适用于本表未列出的由铸造厂和采购方之间协议商定的工艺和材料。
表4要求的铸件机械加工余量(RMA)mm
表5毛坯铸件典型的机械加工余量等级
所以铸件各加工余量的如下表6
序号
基本尺寸mm
加工余量等级
加工余量mm
选择理由和过程
1
H
单侧余量
查表《加工余量等级和数值》,单侧为3.6mm,即28+3.6=31.6,查表2得公差0.7mm,该尺寸及公差为(31.6±
0.35)mm。
2
3
拨叉脚上下表面
双侧余量
10+2×
0.7=11.4mm,查表2得公差1mm,该尺寸及公差为(11.4±
0.5)mm。
4
叉轴孔Φ14mm
J
孔的加工余量等级比底面和侧面的加工余量等级低一级(J级),查《加工余量等级和数值》表,双侧加工余量(一半)为5.5mm,即Φ14-2×
1=Φ12,查表2得公差1.4mm,该尺寸及公差为Φ(12±
0.7)mm。
5
拨叉脚孔Φ40mm
孔的加工余量等级比底面和侧面的加工余量等级低一级(J级),查《加工余量等级和数值》表,双侧加工余量(一半)为6.5mm,即Φ40-2×
1.4=Φ37.2,查表2得公差3.6mm,该尺寸及公差为Φ(37.2±
1.8)mm。
毛坯尺寸图2
毛坯尺寸,其余未标尺寸与设计尺寸相同
1.3拟定拨叉工艺路线
拟订工艺路线是设计工艺规程最为关键的一步,需顺序完成以下几个方面的工作:
选择定位基准,确定各表面加工方法,划分加工阶段,确定工序集中和分散程度,确定工序顺序以及安排热处理、检验及其他辅助工序(去毛刺、倒角等)。
在拟定工艺路线时,需同时提出几种可能的加工方案,然后通过技术、经济的对比分析,最后确定一种最为合理的工艺方案。
1.3.1定位基准的选择
基准选择是拟定零件加工工艺路线的关键,应将粗、精基准的选择原则结合被加工零件的结构特点和技术要求灵活运用,并加以论证。
以拨叉为例:
1.精基准的选择
根据该拨叉零件的技术要求和装配要求,选择拨叉头下端面和叉轴孔
的轴线作为精基准,实现了设计基准和工艺基准的重合,保证了被加工表面的垂直度要求。
另外,由于拨叉件刚性较差,受力易产生弯曲变形,选用拨叉头左端面作为精基准,夹紧力可作用在拨叉头的右端面上,可避免在机械加工中产生夹紧变形,夹紧稳定可靠。
2.粗准基的选择
选择变速叉轴孔Φ14mm的外圆面和拨叉头右端面作为粗基准。
采用Φ14mm外圆面定位加工内孔,可保证孔的壁厚均匀;
采用拨叉头右端面作为粗基准加工左端面,可以为后续工序准备好精基准。
1.3.2表面加工方法的确定
依据零件主要表面的技术要求和工厂具体条件,先选定该表面终加工工序加工方法,然后再考虑各粗、精加工阶段的加工方法。
决定各表面加工方法时还应对照每种加工方法所能达到的经济加工精度,先主要表面,后次要表面。
根据拨叉零件图上各加工表面的尺寸精度和表面粗糙度,查表确定加工件各表面的加工方案,如表7所示。
表7拨叉零件各表面加工方案
尺寸精度等级
加工方案
备注
IT13
粗铣
拨叉脚内表面(ф40mm孔)
IT7
粗扩—精扩—铰
粗铣—精铣
ф14mm孔
1.3.3加工阶段的划分
当零件的加工质量要求较高时,一般都要经过粗加工、半精加工和精加工3个阶段:
如果零件的加工精度要求特别高,表面粗糙度要求特别小时,还要经过精整和光整加工阶段。
在安排加工顺序时将各表面的粗加工集中在一起首先加工,再依次集中各表面的半精加工和精加工工作。
该拨叉加工质量要求较高,可将加工阶段划分成粗加工、半粗加工和精加工3个阶段。
在粗加工阶段,首先要将精基准(拨叉头左端面和叉轴孔)准备好,使后续工序都可采用精基准定位加工;
然后粗铣拨叉头右端面、拨叉脚内表面、拨叉脚两端面、操纵槽内侧面和底面。
在精加工阶段,进行拨叉脚两端面的磨削加工。
1.3.4工序的集中与分散
本例选用工序集中原则安排拨叉的加工工序。
运用工序集中原则使工件的装夹次数减少,不但可缩短辅助时间,而且由于在一次装夹中加工了许多表面,有利于保证各个表面之间的相对位置精度要求。
1.3.5工序顺序的安排
1.机械加工工序
遵循“先基准后其他”原则,首先加工精基准——拨叉头下端面和叉轴孔
。
遵循“先粗后精”原则,先安排粗加工工序,后安排精加工工序。
遵循“先主后次”原则,先加工主要表面——拨叉头下端面和叉轴孔
及拨叉脚两端面,后加工次要表面——操纵槽底面和内侧面。
遵循“先面后孔”原则,先加工拨叉头端面,再加工叉轴孔ф14mm。
表8拨叉机械加工工序安排(初拟)
工序号
工序内容
简要说明
10
粗铣拨叉头上下端面
先基准后其他、先面后孔、先主后次
20
扩、铰两个ф14mm孔(主要表面)
先面后孔、先主后次
30
粗铣拨叉脚两端面(主要表面)
先粗后精(粗加工结束)
40
精铣拨叉脚两端面
先粗后精
50
粗扩—精扩—铰ф40mm孔内表面(次要表面)
先主后次,先粗后精
60
用切割机床将零件按尺寸切成两半
2.热处理工序
模锻成型后切边,进行调质,调质硬度为241~285HBS,并进行酸洗、喷丸处理。
喷丸可以提高表面硬度,增加耐磨性,消除毛坯表面因脱碳而对机械加工带来的不利影响;
叉脚两端面在精加工之前进行局部高频淬火,提高耐磨性和在工作中承受冲击载荷的能力。
3.辅助工序
粗加工拨叉脚两端面和热处理后,安排校直工序;
在半精加工后,安排去毛刺和中间检验工序;
精加工后,安排去毛刺、清洗和终检工序。
综上所述,该拨叉工序的安排顺序为:
基准加工——主要表面粗加工及一些余量大的表面粗加工——主要表面半精加工和次要表面加工——热处理——主要表面精加工。
1.3.6确定工艺路线
在综合考虑上述工序顺序安排原则的基础上,确定拨叉的工艺路线如下表16所示。
表9拨叉机械加工工序安排(修改后)
定位基准
端面、两个ф14mm孔
粗扩、精扩、倒角、铰ф14mm孔
上端面、两个ф14mm孔
粗铣拨叉脚两端面
粗扩—精扩—铰ф40mm孔内表面
下端面、两个ф14mm孔
沿对称线按尺寸切成两半
70
粗铣拨叉脚端面
上端面、ф14mm孔、拨叉脚内表面
80
去毛刺
90
中检
100
热处理(拨叉脚两端面局部淬火)
110
校正拨叉脚
120
磨削拨叉脚两端面
上端面、ф14mm孔
130
清洗
140
终检
150
入库
1.3.7机床设备、工装的选用
针对大批生产的工艺特征,选用设备及工艺装备按照通用、专用相结合的原则,所使用的夹具均为专用夹具。
各工序使用的机床设备、工装及工艺路线如表17所示。
表10加工设备及工艺装备
机床设备
刀具
量具
立式铣床X51
高速钢套式面铣刀
游标卡尺
立式钻床525
麻花钻、扩孔钻、铰刀
卡尺、塞规
粗铣拨叉脚两端面ф40mm
卧式双面铣床
三面刃铣刀
精铣拨叉脚两端面ф40mm
复合钻头、铰刀
用切割机床将零件沿对称线按尺寸切成两半
线切割机床
钳工台
平锉
卡尺、塞规、百分表
淬火机
手锤
M7120A平面磨床
砂轮
清洗机
160
以上工艺过程详见附表1“机械加工工艺过程卡片”
第二章机械加工工序设计
2.1工序简图的绘制
工序简图的绘制原则:
①工序简图以适当的比例,最少的视图,表示出工件在加工时所处的位置状态,与本工序无关的部位可不必表示。
一般以工件在加工时正对操作者的实际位置为主视图。
②工序简图上应标明定位、夹紧符号,以表示出该工序的定位基准、定位点、夹紧力的作用及作用点。
③本工序的各加工表面用粗实线表示,其他部位用细实线表示。
④加工表面上应标注出相应的尺寸、形状、位置精度要求和表面粗糙度要求。
与本工序加工无关的技术要求一律不标。
⑤定位与夹紧符号按标准的规定选用。
(JB/T5061-2006)
例:
工序50——粗扩—精扩—铰ф40mm孔内表面的工序简图
图10钻、倒角、粗铰、精铰ф8mm孔的工序简
2.2加工余量、工序尺寸和公差的确定
2.2.1加工余量的确定
毛坯上留作加工用的材料层,称为加工余量。
某加工表面上切除金属层的总厚度,称为该表面的总余量。
每道工序切除金属层的厚度,称为工序余量。
确定工序余量的方法有计算法、经验估计法、查表法。
实际加工中常用后两种方法。
一般按查表法确定工序间的加工余量。
其选用的原则如下:
①应采用最小的加工余量。
②加工余量应保证得到图样上规定的精度和表面粗糙度。
③要考虑零件热处理时引起的变形。
④要考虑所采用的加工方法、设备以及加工过程中零件可能产生的变形。
⑤要考虑被加工零件尺寸,尺寸越大,加工余量越大。
⑥要考虑被加工零件工序尺寸公差的选择。
⑦本道工序余量应大于上道工序留下的表面缺陷层厚度。
⑧本道工序余量应大于上道工序尺寸公差和几何形状公差。
2.2.2工序尺寸和公差的确定
1.定位基准与设计基准重合时工序尺寸与公差的计算
只要确定了各工序的加工余量和各工序所能达到的经济精度之后,就可以计算出各工序的尺寸及公差。
步骤:
①先订工艺路线。
②查工艺手册,得出加工余量。
③确定经济加工精度及表面粗糙度,查表。
④由最后一道工序向前推算出各工序尺寸、公差等。
2.定位基准与设计基准不重合时工序尺寸与公差的计算
需要解算尺寸链。
2.2.3拨叉零件加工余量、工序尺寸和公差的确定
各表面加工工序
拨叉头上下端面的加工工序见表11-1。
表11-1拨叉头上下端面表面加工工序
工序名称
工序余量(mm)
经济等级
工序基本尺寸
工序尺寸及公差(mm)
7.2
35.2-28=7.2
28mm
粗扩、精扩、倒角、铰ф14mm孔的加工工序见表11-2
表11-2Φ14表面加工工序
粗扩
1.2
12+1.2=13.2
Φ13.2
精扩
0.5
IT10
13.2+0.5=13.7
Φ13.7
倒角
铰
0.3
13.7+0.3=14
Φ14
铣拨叉脚两端面的加工工序见表11-3。
表11-3铣拨叉脚两端面加工工序
IT11
11.4-1=10.4
11.4
精铣
0.4
10.4-0.4=10
粗扩—精扩—铰ф20mm孔内表面的加工工序见表11-4。
表11-4ф40mm孔内表面的加工工序
1.5
37.2+1.5=38.7
ф38.7
38.7+1=39.7
ф39.7
0.2
39.7+0.3=40
ф40
沿对称线按尺寸切成两半加工工序见表11-5。
表11-5沿对称线按尺寸切成两半的加工工序
切
60.5
粗铣拨叉脚端面的加工工序见表11-6。
表11-6粗铣拨叉脚端面的加工工序
铣
2.3切削用量的选择
首先选取尽可能大的被吃刀量;
其次根据机床动力和刚性限制条件或加工表面粗糙度的要求,选取尽可能大的进给量;
最后利用切削用量手册选取或者用公式计算确定切削速度。
1.工序10——粗铣拨叉头两端面
该工序分两个工步,工步1是以右端面B定位,粗铣A面;
工步2是以A面定位,粗铣B面。
由于这两个工步是在一台机床上经过一次走刀加工完成的,因此它们所选用的切削速度vc和进给量f是一样的,只有背吃刀量ap不同。
(1)背吃刀量的确定:
工步1的背吃刀量ap1取Z1,Z1等于A面的毛坯总余量减去工序2的余量Z3,即Z1=7.2mm-4mm=3.2mm;
而工步2的背吃刀量ap2取为Z2,则ap2=Z2=3.2mm。
(2)进给量的确定:
X51型立式铣床功率为4.5kW,按机床功率为5~10kW,工件、夹具系统刚度为中等条件选取,该工序的每齿进给量fz取为0.08mm/z。
(3)铣削速度的计算:
按镶齿铣刀、dw=80mm、齿数z=10的条件选取,切削速度vc可取44.9m/min。
由公式n=1000vc/πd可求得该工序铣刀转速为
X51立式铣床的主轴转速,取转速n=160r/min,故实际切削速度vc为
2.工序20——粗扩、精扩、倒角、铰ф14mm孔
(1)粗扩
孔工步
背吃刀量的确定:
取ap=13.2mm。
进给量的确定:
选取该工步的每转进给量f=0.20mm/r。
切削速度的计算:
按工件材料为45钢的条件选取,切削速度vc=20m/min。
则
Z525立式钻床的主轴转速n=680r/min。
将此转速重新代入公式计算,求出该工序的实际钻削速度为
(2)精扩
取ap=0.5mm。
选取该工步的每转进给量f=0.2mm/r。
(3)铰工步
取ap=0.2mm。
选取该工步的每转进给量f=0.5mm/r。
切削速度vc=3m/min,则
Z525立式钻床的主轴转速n=97r/min。
将此转速代入公式重新计算,可求得该工序的实际切削速度为
2.4机械加工工艺文件的填写(见附件)
将上述拨叉零件的工艺规程设计的结果填入工艺规程文件
第三章专用钻床夹具设计
3.1夹具设计任务
3.1.1专用夹具设计的基本要求
(1)保证被加工要素的加工精度。
(2)提高劳动生产率。
(3)具有良好的使用性能。
(4)经济性。
3.1.2专用夹具设计的一般步骤和需要完成的任务
1.明确设计要求,收集和研究有关资料
在接到夹具设计任务书后,首先要仔细阅读加工件的零件图和与之有关的部件装配图,了解零件的作用、结构特点和技术要求;
其次,要认真研究加工件的工艺规程,充分了解本工序的加工内容和加工要求,了解本工序使用的机床和刀具,研究分析夹具设计任务书上所选用的定位基准和工序尺寸。
2.拟定夹具的结构方案,绘制夹具草图
拟定夹具的结构方案时,主要解决以下问题:
①确定工件的定位方式,设计定位装置;
②确定工件的夹紧方案,设计夹紧装置;
③确定对刀或导向方式,选择或设计对刀块或导向元件。
④确定其他元件或装置的结构形式,例如分度装置、定位键等。
⑤确定夹具的总体结构及夹具在机床的安装方式。
在确定夹具结构方案的过程中,应提出几种不同的方案进行比较分析,选取其中最为合理的结构方案。
3.方案审查
必要的加工精度分析计算,必要的夹紧力分析计算,必要的零部件强度和刚度分析计算,请相关专业人员进行审查,方案优化。
4.绘制夹具总图
应按国家规定标准绘制,尽量采用1: