工艺技术管理Word文档下载推荐.docx
《工艺技术管理Word文档下载推荐.docx》由会员分享,可在线阅读,更多相关《工艺技术管理Word文档下载推荐.docx(12页珍藏版)》请在冰豆网上搜索。
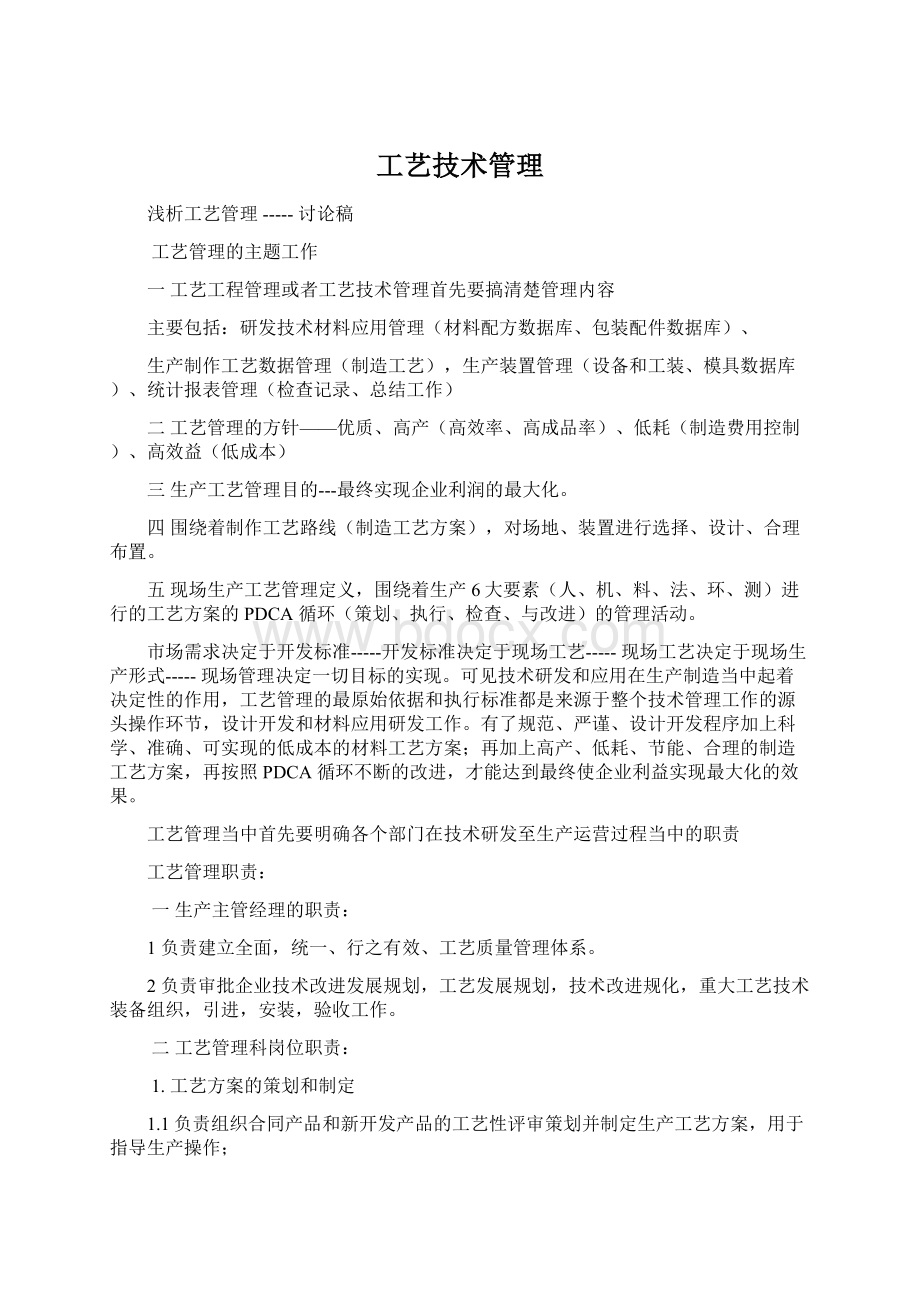
2.4做好工艺管理档案的归集分析和必要的信息共享;
2.5对工艺方案执行中可能发生的影响安全和健康环保的问题做好风险预估和预防改进。
负责组织分析制定产量定额、损耗率。
3.技术服务
3.1负责组织设计和完善现有产品使用设备、工装。
为工艺工程项目提供工艺技术参数和其他技术支持;
3.2对围绕生产及生产准备所发生的活动提供必要的技术支持;
3.3发现并提出工艺工程改造项目。
4.数据库建设与文件管理
4.1工艺方案数据库建立
4.2标准样数据库和生产配方数据库建立
4.3模具数据库建立
4.4产品开发包装数据库建立
4.5工艺技术问题案例分析数据库建立
4.6负责定期向物流部提供更新的材料使用信息表(在基础产品配方数据库基础上增加差异化产品配方信息)。
4..7工艺质量管理台帐,合同生产总结数据库。
三职能部门工艺职责
1设计,研发部门:
负责新项目开发输入评审,以及项目成功后输出相关的报告,确定产品的标准,检验规程,工艺风格,表面效果,燃烧质量,以及简易的操作流程设计,工装、模具等设计图纸。
2采购科
按照工艺要求及时提供主要原材料,辅料,及合格的配件,以及其他外购部件。
3人事行政部
3.1按照工艺要求负责生产人员的招聘,要保证定准时,足量提供。
3.2工艺变化时,及时、准确的制定、修改生产定额,确保生产定额符合现场实际生产情况。
3.3生产操作安全培训。
4生产计划科
(1)根据工艺要求合理地选择生产场地。
(2)按照工艺流程工序的工艺特点合理加工顺序制作成品、半成品、零部件,制定可实现的生产计划。
5品检科
(1)负责组织检查工艺纪律落实情况,严格按照质量标准进行成品半成品检查。
(2)建立产品检验控制管理台帐,针对客户特别关注点,制作检查记录表,制作当中不符点工艺质量问题及时向工艺科反馈,并跟踪进度和改进结果。
(3)负责向技术科提供质量问题检查记录当中,数据统计成品率,产品克重等数据。
(4)参加制定工序控制点的建立和组织产品质量问题评审工作。
6设备科职责:
(1)负责建立设备管理台帐,编制设备操作规程,负责按照工艺要求制做工装。
(2)确保设备运行正常、安全、可靠,并满足生产工艺要求。
定期对工装设备进行维保,确保设备达到95%以上的时间处于正常工作状态。
对车间操作工人进行正确使用设备和日常维护保养培训,监督、检查车间生产设备的使用情况。
负责根据工艺要求进行工艺工程项目改造和生产环境条件改善。
(5)编制设备生产效率定额统计表。
7生产车间职责
1)负责按工艺文件要求组织生产和记录。
2)负责按工艺要求组织现场技术人员对产品进行工艺验证。
3)负责组织车间严格遵守工艺纪律。
4)负责及时反馈工艺验证和生产实施过程中的工艺问题。
5)负责在工艺指导监督下开展现场定置管理。
四工艺设计管理:
工艺研发---市场调研
1工艺调研目的是为了了解市场和用户对产品的需求,了解国内外同工行业工艺水平,了解新工艺,新材料的使用情况,通过了解本企业对手的产品,找到本企业在制作过程中存在的问题,为工艺准备奠基良好的基础,起到促进工艺水平提高的作用。
2产品工艺性审查----输入评审
由技术项目负责人在产品设计定型前,对产品制作当中使用的工装,材料配方,制作工艺,存在风险等问题进行输出评审,作为试生产和批量投产的必要前提。
在新产品设计过程中,重大项目必须有专人进行阶段性工艺评审,产品工艺性审查再设计的各阶段都应进行。
3工艺方案制定---输出评审
工艺方案是产品准备工作的总纲,也是编制工艺性文件的指导性文件。
工艺方案的制定的原则,适应性强,根据实际情况,现场可操作,可实现。
工艺方案是产品进行制作加工的技术方案,它规定了产品加工的生产路线(材料备至状态区分---熔化---配料–成型加工----后期处理---包装---装箱----入库的操作全过程);
当中的各项技术指标或标准的的初步设计技术参数。
包括所使用设备,工装、模具,材料配方,材料用量,加工过程中的基础技术要求,技术参数。
3,2工艺文件的编制是开展工艺工作的依据,主要用于指导工人操作和用于生产、检查、以及工艺纪律管理。
3.3工艺文件的内容包括工艺规程,工艺设备技术参数,劳动定额,原材料使用耗量,检验规程,质量标准,作业指导书,检查记录表等等。
五工艺设备管理:
1工装设计、制作、验收。
产品实现过程中使用的设备,工装、模具、工位器具,操作架等等工艺装备,简称工装。
工装的制作有两种,一种简易工装由公司自主制作,另一种制作精密复杂需要外协制作,工艺装备的制作依据是,工艺方案、依据工艺规程要求的技术参数,确保产品可实现;
工装设备,必须经过验收后,完全达到设计标准后才算验收通过。
2设备维保
定期对设备进行检修,保养,常用故障率高的设备应每日至少两次进行巡检,对于故障率低,且长期运转或不常使用的重要设备要定期进行保养维护。
六现场工艺管理:
现场工艺管理主要围绕着生产的人、机、料、法、环、测六大要素进行PDCA循环的原则进行管理。
定义:
PDCA循环
Plan:
制定目标与计划
Do:
任务展开,组织实施
Check:
对过程中的关键点和最终结果进行检查
Action:
纠正偏差,对成果进行标准化,并确定新的目标,制定下一轮计划。
特点:
①各级质量管理都有一个PDCA循环,形成一个大环套小环,一环扣一环,互相制约,互为补充的有机整体,如上图1、图2所示。
在PDCA循环中,一般说,上一级的循环是下一级循环的依据,下一级的循环是上一级循环的落实和具体化。
②每个PDCA循环,都不是在原地周而复始运转,而是象爬楼梯那样,每一循环都有新的目标和内容,这意味着质量管理,经过一次循环,解决了一批问题,质量水平有了新的提高。
③在PDCA循环中,A是一个循环的关键。
【P(计划)】:
工作计划、策划、职责、目标(人、机、料、法、环、测5W1H);
人---.对人的细化管理
通常按班组、个人、管理者别进行不良数据的统计与分析,可以很容易发现下述差别:
◆工作态度、风气;
◆技能水平;
◆管理能力。
机----对机器的细化管理
通常按不同设备、工器具进行不良数据的统计与分析,可以很容易发现下述差别:
◆设备性能、精度、维护状况;
◆工器具精度、磨损、寿命;
◆不同材质模具、工装的差别。
料---对材料的细化管理
通常按不同厂家、同一厂家不同批次进行不良数据的统计与分析,可以很容易发现下述差别:
◆材质与质量标准的符合性;
◆供应厂家之间的差别;
◆同一厂家的材质均匀性、质量稳定性;
法---方法的细化管理
通常按不同机种、不同班别进行不良数据的统计与分析,可以很容易发现下述差别:
◆不同机种间的工艺条件差别;
◆不同作业者的操作方法、调整方法;
◆调整范围。
环---对环境的细化理
通常按生产线类别、工序类别、季节别进行不良数据的统计与分析及现场观察,可以很容易发现下述差别:
◆现场5S(清洁度、有序度、明朗度)状况;
◆现场物流情况;
◆亮度、温度、湿度、空气流动情况。
测量---对测量系统的细化管理
对不同的测量方法、计测计量仪器、测量人员及其与测量系统的交互作用进行分析,通过测量系统分析(MSA),使测量误差达到可接受的范围。
包括三个方面的策划(危险源识别、法律法规识别、目标指标和方案制订)
【D(执行)】:
--明确职责(部门/岗位的质量、安保职责)
--资源保证(能力、意识,特种作业人员上岗资格。
--编写文件(强调标准依据)
--信息交流和沟通(对内、对外)
--执行:
符合性痕迹管理
运行控制(重点消防安全、防盗抢(财产和资金)、交通安全、信息安全)应急准备和响应(预案文件的演练和执行)
【C(检查)、A(纠正)】:
检查和持续改进
--日常工作(质量)检查、安全检查
--目标、指标完成情况的定期验证
--安全管理绩效的检查
--对不合格项(品)的整改,事故的调查和处理。
PDCA操作当中的八个步骤
(1)分析现状,发现问题;
②分析质量问题中各种影响因素;
③分析影响质量问题的主要原因;
④针对主要原因,采取解决的措施;
——为什么要制定这个措施?
——达到什么目标?
——在何处执行?
——由谁负责完成?
——什么时间完成?
——怎样执行?
⑤执行,按措施计划的要求去做;
⑥检查,把执行结果与要求达到的目标进行对比;
⑦标准化,把成功的经验总结出来,制定相应的标准;
⑧把没有解决或新出现的问题转入下一个PDCA循环中去解决。
七工艺管理精细化
精细化管理的特点有四个方面:
◆细,就是管细、做细、关注细节
◆准,就是准确、及时、准时
◆严,就是严格遵守、实施一次做到位
◆精,就是管精、做精、精益求精
从精细化管理的特点来看,精细化管理是通过细化的实施方法提高时间要求和工作质量要求,实现有竞争力的绩效目标,即低成本、快速反应。
建立内部客户观念要做到:
◆了解产品的工艺流程;
◆了解各工段、工序的主要控制要点;
◆了解前后工段、工序的关系;
◆了解工序质量与市场质量的关系;
◆了解工序质量对后续工序的影响;
◆了解本工序质量控制的要点。
细化管理具体体现---数字化管理
细化管理对系统渠道的要求
细化管理对统计渠道的要求是:
抓住重点,抓住关键,推动改善。
从管细到管精对统计渠道提出了要求:
必须要有完善的统计渠道,这种统计渠道就像管理的神经末梢,它能够伸到一线,伸到班组,伸到每个员工,伸到每一个班次、每一个时段。
具体包括:
◆细化管理X(5M1E)
包括:
不同班组/人员、不同设备/生产线、不同供应商/批次材料、不同工艺/条件、不同作业环境、单位成本管理、使用设备寿命周期成本管理
◆细化管理Y(QCDSF)
不同时间、不同系列、5M1E分层、单位成本管理、寿命周期成本管理
八现场操作具体管理内容
1工艺定额管理
工艺定额管理包括工时,人均产量,材料消耗、能源动力费用消耗。
内容应具有以下特性:
(!
)先进性
(2)合理性,以实际出发制定定额。
(3)完整性,每道工序都有定额不能遗漏。
(4)准确性,按照各个工序消耗的时间指定准确的定额。
2确定工艺条件
根据工艺要求为生产环境确定比要的条件主要对温度、湿度、光照、香味、噪音等采取必要地措施。
要通过技术手段对环境的各项要素进行控制,保证产品在适宜的环境中进行生产。
3人员培训
各种操作都是由人来进行,所以应对所有操作人员进行岗前培训,使之了解操作流程和作业要求,及质量标准。
特别是关键操作岗位必须考核合格后方可允许上岗操作。
4确定工序质量关键控制点
生产过程的质量管理是保证产品质量的关键,因而应积极地对制造过程实行工序控制,保证生产出符合质量标准的合格产品。
对工序控制,主要是通过设置工序控制点来达到的:
(2)在对工序质量控制点进行工序动作分解制定作业指导书,或操作规程。
(3)对工序控制点上使用的工装、设备要定期进行检查,并定期维护保养。
(4)对关键控制点上使用的设备要定期做好状态跟踪记录,并详细记录允许状态。
5现场工艺控制
(1)工艺标准化
工艺术语标准化,工艺术语是工艺领域内的共同的技术语言,是制作工艺标准,编制工艺文件,做好各项工艺工作的基础。
如常用的,工艺风格,表面效果,规格,货号,色号,色差,阻燃、积碳等等。
工艺要素标准化,生产设计相关技术参数统一单位,统一取值标准如产品尺寸公差,浇注温度范围,材料消耗用量,工序步骤使用工时。
工艺操作规程标准化,统一工艺要求严格按照标准作业指导书和操作流程进行生产。
工艺文件标准化,《产品质量标准》《标准实样》是现场生产执行的标准。
是试产,首产验证,正常生产依据。
(2)工艺纪律检查
工艺纪律是生产过程维护工艺严肃性,保证工艺要求贯彻执行,建立稳定的生产秩序,确保产品加工质量和安全生产的而制定的约束性文件。
对人员的要求,
1操作人员是否经过培训合格后上岗。
2操作人员是否按照标准文件规定技术要求和技术指标进行操作。
3操作人员的生产效率,所用工时是否符合技术文件要求。
工艺纪律对设备工装的要求
1设备工装是否按照技术要求达到设定生产效率。
2设备工装是否达到要求的精密度。
3设备工装状态完好率,工作正常使用率是否达标。
对材料的要求
料,是指半成品、配件、原材料包装材料等构成成品产品所用的原料。
遵循5S管理所规定的定制管理要求。
1制造材料存放状态和可追溯性状态、标识是否清晰,有无调整使用要求。
2包装材料,或配件,标识是否清晰准确,发放,退库是否使用设有专人验收,并记录在案。
3半成品,合格状态,检验状态。
对制作方法的要求
法,顾名思义,法则。
指生产过程中所需遵循的规章制度。
它包括:
作业指导书,材料工艺单,作业标准,制作工艺流程、产品标准(标准实样、产品质量标准)检验标准和各种操作规程等。
作用是及时、准确的反映出生产过程中存在那些问题和技术文件当中规定的技术参数、在应用当中是否能够成为产品达标的技术标准指标。
是进行不断技术改进的基础工作;
严格按照规程作业,是保证产品质量和生产进度的重要条件之一。
对环境的要求
环境温度、湿度、车间洁净度等对是否影响产品质量。
对检验的要求
(1)确定测量标准及所要求的准确度,选择精密度满足测试标准要求的计量器具。
(2)定期对所有测量和试验设备进行校准和调整。
(3)规定必要的校准规程。
其内容包括测量器具类型、编号、使用地点、校验周期、校验方法、验收方法、验收标准,以及维修的记录和应急问题处理措施。
(4)保存校准记录。
(5)发现测量和检验设备未处于校准状态时,立即评定以前的测量和试验结果的有效性,并记入有关文件。
九现场工艺管理的步骤
1合同生产工艺评审(产前策划)
1.)质量标准
产品的表面风格,尺寸,克重,燃时,平稳度、等质量标准。
2.)风险评估
类似产品,样品制作当中出现的问题及改进措施,控制方法。
3.)《浇注操作流程》,《.包装操作流程》《标准作业指导书》制定。
使用标准作业指导书,将操作流程连接起来,制作合同操作流程图。
注:
没有对应的标准作业指导书,要从新制作。
要求在试生产结束后完成。
4).使用模具、工装、设备;
确认模具材质,出具模具、工装、图纸、确定使用数量。
5).用料计划
生产顺序,班次各种油号用油时间,使用油量,化蜡缸、周转车使用频次、周转率。
6)人工效率、成品率。
A老产品,根据相同或者类似产品制定相应的人工效率和成品率.(实际效率)
B新开发产品
1参考:
样品制作周期+30%操作周转时间2参考类似产品,用工情况*70%=估计工时。
7)人员工序分配
按照蜡烛制作所需操作工序,合理查出工序,最大限度发挥人员生产效率。
8)预估使用场地面积。
2工艺验证:
工艺验证是在新产品研发或批量试生产阶段中对工艺能否到预订工艺定额的实验过程,并逐步阶段性达到生产定额的实践过程。
1)生产车间在合同生产初期必须留出3-5天时间作为中试和首产检验期。
其间由现场工艺管理员负责现场工艺问题的跟踪和处理,包括必要的人员调配;
2)中试期间,人员和产量安排要从小到大,原则上为正常生产产量的1/4-1/2的生产负荷即可;
3)中试其间,生产现场必须划分清晰,工具齐备,人员岗位明确,经过产前培训并有记录;
4)首产验证工艺员、生产车间负责人和品管员共同进行首产验收,包括表面效果、颜色、规格等等;
现场工艺管理员对车间执行工艺单情况进行监督,记录《标准作业书》和《工艺流程图》的执行情况,并进行考核;
5)在中试和首产验收期内,完成产品的质量合格率(95%)指标,工时定额(达到75%的规定定额)指标,回收蜡正常回收,现场各个工序衔接合理。
既为通过现场验证。
6)以上验证记录通过首产检验记录登记归档,现场工艺管理员应将首产检验记录归档到“合同生产数据库”中。
2工艺总结,在工艺策划的基础上系统整理。
1)以合同或产品排产工艺风格,数量,进度,做基础表述。
2)材料配方,物料消耗。
(材料使用单)更改情况。
3)制作工艺,《制作操作流程》,《----标准作业指导书》(设备、浇注、包装)。
4)质量问题总结,详细分析各类质量问题产生的原因,处理问题制定整改方法。
5)合同设备、工装图纸,技术参数,实际使用数量,使用情况。
6)人工效效率,产值,生产实际成品率。
7)合同生产剩余成品,半成品,多余省料情况。
8)能源动力费用总结。