采用小浇口进行注塑成型的优点文档格式.docx
《采用小浇口进行注塑成型的优点文档格式.docx》由会员分享,可在线阅读,更多相关《采用小浇口进行注塑成型的优点文档格式.docx(16页珍藏版)》请在冰豆网上搜索。
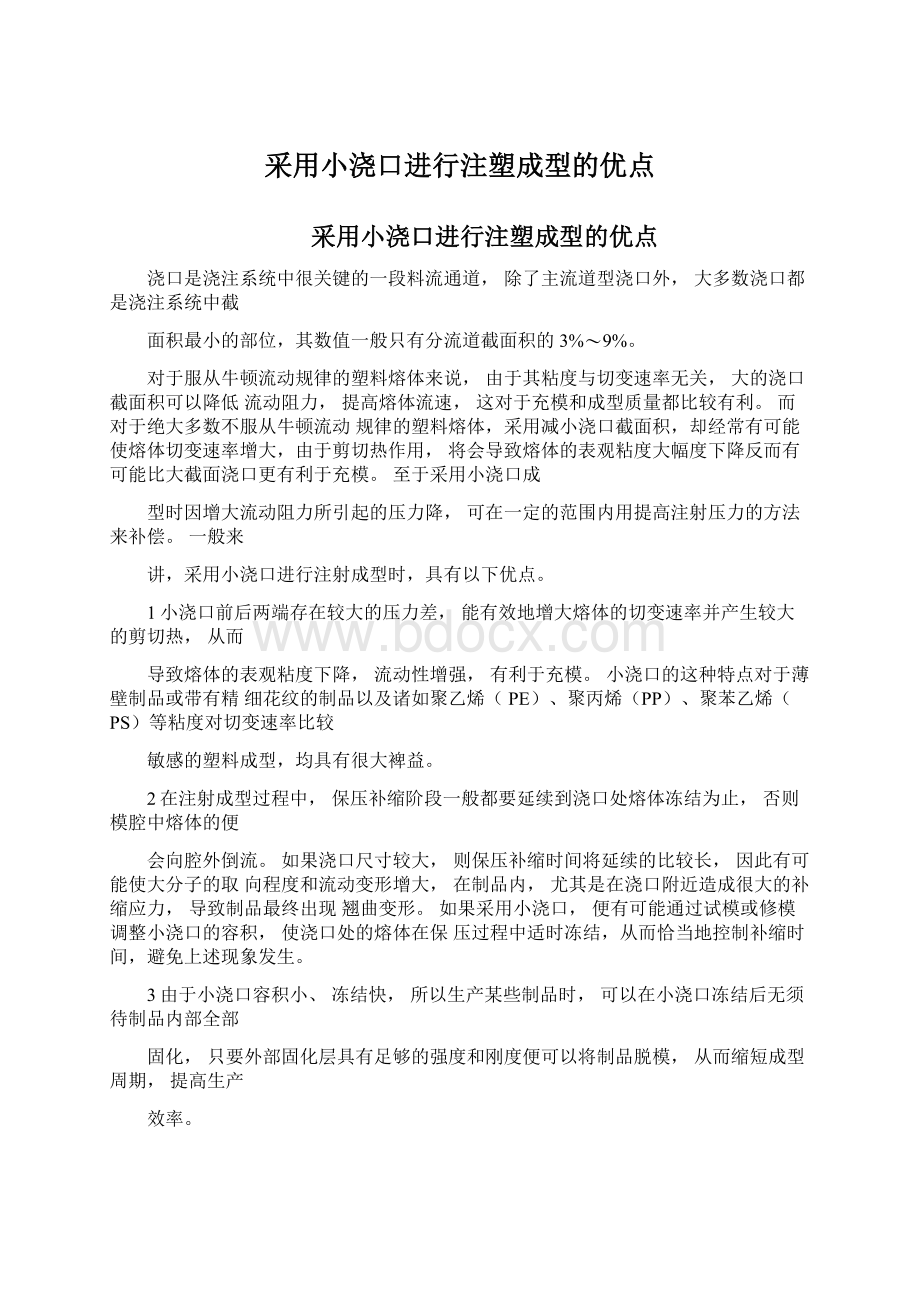
模温分布与塑件内外冷却及密度均匀性也有关,直接影响到各部分收缩量大小及方向性。
另外,保持压力及时间对收缩也影响较大,压力大、时间长的则收缩小但方向性大。
注塑压力高,熔融料粘度差小,层间剪切应力小,脱模后弹性回跳大,故收缩也可适量的减小,料温高、收缩大,但方向性小。
因此在成型时调整模温、压力、注塑速度及冷却时间等诸因素也可适当改变塑件收缩情况。
模具设计时根据各种塑料的收缩范围,塑件壁厚、形状,进料口形式尺寸及分布情况,按经验确定塑件各部位的收缩率,再来计算型腔尺寸。
对高精度塑件及难以掌握收缩率时,一般宜用如下方法设计模具:
1对塑件外径取较小收缩率,内径取较大收缩率,以留有试模后修正的余地。
2试模确定浇注系统形式、尺寸及成型条件。
3要后处理的塑件经后处理确定尺寸变化情况(测量时必须在脱模后24小时以后)。
4按实际收缩情况修正模具。
5再试模并可适当地改变工艺条件略微修正收缩值以满足塑件要求。
二、流动性
2.1热塑性塑料流动性大小,一般可从分子量大小、熔融指数、阿基米德螺旋线流动长度、
表现粘度及流动比(流程长度/塑件壁厚)等一系列指数进行分析。
分子量小,分子量分布宽,分子结构规整性差,熔融指数高、螺流动长度长、表现粘度小,流动比大的则流动性就好,对同一品名的塑料必须检查其说明书判断其流动性是否适用于注塑成型。
按模具设计要
求大致可将常用塑料的流动性分为三类:
1流动性好PA、PE、PS、PP、CA、聚(4)甲基戍烯;
2流动性中等聚苯乙烯系列树脂(如ABS、AS)、PMMA、POM、聚苯醚;
3流动性差PC、硬PVC、聚苯醚、聚砜、聚芳砜、氟塑料。
2.2各种塑料的流动性也因各成型因素而变,主要影响的因素有如下几点:
1温度料温高则流动性增大,但不同塑料也各有差异,PS(尤其耐冲击型及MFR值较高的)、PP、PA、PMMA、改性聚苯乙烯(如ABS、AS)、PC、CA等塑料的流动性随温度变化较大。
对PE、POM、则温度增减对其流动性影响较小。
所以前者在成型时宜调节温度来控制流动性。
2压力注塑压力增大则熔融料受剪切作用大,流动性也增大,特别是PE、POM较为敏感,
所以成型时宜调节注塑压力来控制流动性。
3模具结构浇注系统的形式,尺寸,布置,冷却系统设计,熔融料流动阻力(如型面光洁度,
料道截面厚度,型腔形状,排气系统)等因素都直接影响到熔融料在型腔内的实际流动性,凡促使熔融料降低温度,增加流动性阻力的则流动性就降低。
模具设计时应根据所用塑料的流动性,选用合理的结构。
成型时则也可控制料温,模温及注塑压力、注塑速度等因素来适
当地调节填充情况以满足成型需要。
三、结晶性
热塑性塑料按其冷凝时无出现结晶现象可划分为结晶型塑料与非结晶型(又称无定形)塑料
两大类。
所谓结晶现象即为塑料由熔融状态到冷凝时,分子由独立移动,完全处于无次序状态,变成分子停止自由运动,按略微固定的位置,并有一个使分子排列成为正规模型的倾向的一种现象。
作为判别这两类塑料的外观标准可视塑料的厚壁塑件的透明性而定,一般结晶性料为不透明
或半透明(如POM等),无定形料为透明(如PMMA等)。
但也有例外情况,如聚(4)甲基戍烯为结晶型塑料却有高透明性,ABS为无定形料但却并不透明。
在模具设计及选择注塑机时应注意对结晶型塑料有下列要求及注意事项:
1料温上升到成型温度所需的热量多,要用塑化能力大的设备。
2冷却回化时放出热量大,要充分冷却。
3熔融态与固态的比重差大,成型收缩大,易发生缩孔、气孔。
4冷却快,结晶度低,收缩小,透明度高。
结晶度与塑件壁厚有关,壁厚则冷却慢,结晶度高,收缩大,物性好。
所以结晶性料应按要求必须控制模温。
5各向异性显著,内应力大。
脱模后未结晶化的分子有继续结晶化倾向,处于能量不平衡状态,易发生变形、翘曲。
6结晶化温度范围窄,易发生未熔料末注入模具或堵塞进料口。
四、热敏性塑料及易水解塑料
4.1热敏性系指某些塑料对热较为敏感,在高温下受热时间较长或进料口截面过小,剪切作用大时,料温增高易发生变色、降解,分解的倾向,具有这种特性的塑料称为热敏性塑料。
如硬PVC、聚偏氯乙烯、醋酸乙烯共聚物,POM,聚三氟氯乙烯等。
热敏性塑料在分解时
产生单体、气体、固体等副产物,特别是有的分解气体对人体、设备、模具都有刺激、腐蚀作用或※性。
因此,模具设计、选择注塑机及成型时都应注意,应选用螺杆式注塑机,浇注系统截面宜大,模具和料筒应镀铬,不得有*角滞料,必须严格控制成型温度、塑料中加入
稳定剂,减弱其热敏性能。
4.2有的塑料(如PC)即使含有少量水分,但在高温、高压下也会发生分解,这种性能称为易水解性,对此必须预先加热干燥。
五、应力开裂及熔体破裂
5.1有的塑料对应力敏感,成型时易产生内应力并质脆易裂,塑件在外力作用下或在溶剂作
用下即发生开裂现象。
为此,除了在原料内加入添加剂提高开抗裂性外,对原料应注意干燥,合理的选择成型条件,以减少内应力和增加抗裂性。
并应选择合理的塑件形状,不宜设置嵌件等措施来尽量减少应力集中。
模具设计时应增大脱模斜度,选用合理的进料口及顶出机构,成型时应适当的调节料温、模温、注塑压力及冷却时间,尽量避免塑件过于冷脆时脱模,成
型后塑件还宜进行后处理提高抗开裂性,消除内应力并禁止与溶剂接触。
5.2当一定融熔体流动速率的聚合物熔体,在恒温下通过喷嘴孔时其流速超过某值后,熔体表面发生明显横向裂纹称为熔体破裂,有损塑件外观及物性。
故在选用熔体流动速率高的聚合物等,应增大喷嘴、浇道、进料口截面,减少注塑速度,提高料温。
六、热性能及冷却速度
6.1各种塑料有不同比热、热传导率、热变形温度等热性能。
比热高的塑化时需要热量大,应选用塑化能力大的注塑机。
热变形温度高塑料的冷却时间可短,脱模早,但脱模后要防止冷却变形。
热传导率低的塑料冷却速度慢(如离子聚合物等冷却速度极慢),故必须充分冷却,要加强模具冷却效果。
热浇道模具适用于比热低,热传导率高的塑料。
比热大、热传导率低,热变形温度低、冷却速度慢的塑料则不利于高速成型,必须选用适当的注塑机及加强模具冷却。
6.2各种塑料按其种类特性及塑件形状,要求必须保持适当的冷却速度。
所以模具必须按成型要求设置加热和冷却系统,以保持一定模温。
当料温使模温升高时应予冷却,以防止塑件脱模后变形,缩短成型周期,降低结晶度。
当塑料余热不足以使模具保持一定温度时,则模具应设有加热系统,使模具保持在一定温度,以控制冷却速度,保证流动性,改善填充条件或用以控制塑件使其缓慢冷却,防止厚壁塑件内外冷却不匀及提高结晶度等。
对流动性好,成型面积大、料温不匀的则按塑件成型情况有时需加热或冷却交替使用或局部加热与冷却并用。
为此模具应设有相应的冷却或加热系统。
七、吸湿性塑料中因有各种添加剂,使其对水分有不同的亲疏程度,所以塑料大致可分为吸湿、粘附水分及不吸水也不易粘附水分的两种,料中含水量必须控制在允许范围内,不然在高温、高压下水分变成气体或发生水解作用,使树脂起泡、流动性下降、外观及力学性能不良。
所以吸湿性塑料必须按要求采用适当的加热方法及规范进行预热,在使用时防止再吸湿。
1•怎样克服产品注射不足
产品注料不足往往由于物料在未充满型腔之前即已固化,当然还有其他多种的原因。
⑴设备原因:
1料斗中断料;
2料斗缩颈部分或全部堵塞;
3加料量不够;
4加料控制系统操作不正常;
5注压机塑化容量太小;
6设备造成的注射周期反常。
⑵注塑条件原因:
1注射压力太低;
2在注射周期中注射压力损失太大;
3注射时间太短;
4注射全压时间太短;
5注射速率太慢;
6模腔内料流中断;
7充模速率不等;
8操作条件造成的注射周期反常。
⑶温度原因:
1提高料筒温度;
2提高喷嘴温度;
3检查毫伏计、热电偶、电阻电热圈(或远红外加热装置)和加热系统;
4提高模温;
5检查模温控制装置。
⑷模具原因
1流道太小;
2浇口太小;
3喷嘴孔太小;
4浇口位置不合理;
5浇口数不足;
6冷料穴太小;
7排气不足;
8模具造成的注射周期反常;
⑸物料原因:
物料流动性太差。
排气
2•怎样克服产品飞边溢料:
产品溢边往往由于模子的缺陷造成,其他原因有:
注射力大于锁模力、物料温度太高、
不足、加料过量、模子上沾有异物等。
⑴模具问题:
1型腔和型芯未闭紧;
2型腔和型芯偏移;
3模板不平行;
4模板变形;
5模子平面落入异物;
6排气不足;
7排气孔太大;
8模具造成的注射周期反常。
⑵设备问题:
1制品的投影面积超过了注压机的最大注射面积;
2注压机模板安装调节不正确;
3模具安装不正确;
4锁模力不能保持恒定;
5注压机模板不平行;
6拉杆变形不均;
7设备造成的注射周期反常
⑶注塑条件问题:
1锁模力太低
2注射压力太大;
3注射时间太长;
4注射全压力时间太长;
5注射速率太快;
6充模速率不等;
7模腔内料流中断;
8加料量控制太大;
9操作条件造成的注射周期反常。
⑷温度问题:
1料筒温度太高;
2喷嘴温度太高;
3模温太高。
⑸设备问题:
1增大注压机的塑化容量;
2使注射周期正常;
⑹冷却条件问题:
1部件在模内冷却过长,避免由外往里收缩,缩短模子冷却时间;
2将制件在热水中冷却。
怎样防止产品接痕(拼缝线)产品接痕通常是由于在拼缝处温度低、压力小造成。
⑴温度问题:
1料筒温度太低;
2喷嘴温度太低;
3模温太低;
4拼缝处模温太低;
5塑料熔体温度不均。
⑵注塑问题:
1注射压力太低:
2注射速度太慢。
3)模具问题:
<
1>
拼缝处排气不良;
2>
部件排气不良;
3>
分流道太小;
4>
浇口太小;
5>
三流道进口直径太小;
6>
喷嘴孔太小;
7>
浇口离拼缝处太远,可增加辅助浇口;
<
8>
制品壁厚太薄,造成过早固化;
9>
型芯偏移,造成单边薄;
10>
模子偏移,造成单边薄<
11>
制件在拼缝处太薄,加厚;
12>
充模速率不等;
13>
充模料流中断。
(4)设备问题:
1塑化容量太小;
2料筒中压力损失太大(柱塞式注压机)。
⑹物料问题:
1物料污染;
2物料流动性太差,加润滑剂改善流动性。
怎样防止产品发脆产品发脆往往由于物料在注塑过程中降解或其他原因。
⑴注塑问题:
料筒温度低,提高料筒温度;
喷嘴温度低,提高它;
如果物料容易热降解,则降低料筒喷嘴温度;
提高注射速度;
提高注射压力;
增加注射时间;
增加全压时间;
模温太低,提高它;
制件内应力大,减少内应力;
制件有拼缝线,设法减少或消除;
螺杆转速太高因而降解物料。
⑵模具问题:
1制品设计太薄;
3分流道太小;
4制品增加加强筋、圆内角。
⑶物料问题:
1物料污染;
2物料未干燥好;
3物料中有挥发物;
④物料中回料太多或回料次数太多;
5物料强度低。
⑷设备问题:
1塑化容量太小;
②料筒中有障碍物促使物料降解。
怎样克服产品银丝与斑纹
(1)物料问题:
2物料未干燥;
3物料颗粒不均。
(2)设备问题:
1检查料筒-喷嘴流道系统有无障碍物及毛刺影响料流;
2流涎,采用弹簧喷嘴;
3设备容量不足。
(3)注塑问题:
1物料降解,降低螺杆转速,降低背压力;
2调整注射速度;
3增大注射压力;
4加长注射时间;
5加长全压时间;
6加长注射周期。
(4)温度问题:
1料筒温度太低或太高;
2模温太低,提高它;
3模温不均。
4喷嘴温度太高会流涎,降低它。
(5)模具问题:
1增大冷料穴;
2增大流道;
3抛光主流道、分流道、浇口;
4增大浇口尺寸或改为扇形浇口;
5改善排气;
6提高模腔光洁度;
7清洁模腔;
8润滑剂过量,减少它或调换它;
9去除模子内露水(模子冷却造成的);
10料流经过凹穴及增厚断面,修改制品设计;
试用浇口局部加热怎样克服产品浇口处混浊产品浇口处出现斑纹和混浊,通常由于扩张注入模型时造成“熔体破碎”所致。
(1)注塑问题:
3减慢注射速度;
4增大注射压力;
5改变注射时间;
6润滑剂减少或调换润滑剂。
(2)模具问题:
1提高模子温度;
2增大浇口尺寸;
3改变浇口形状(扇形浇口);
4增大冷料穴;
5增大分流道尺寸;
6改变浇口位置;
7改善排气。
(3)物料问题:
1干燥物料;
2去除物料中污染物。
怎样控制产品尺寸
产品尺寸的变化是由于设备控制反常、注塑条件不合理、产品设计不好及物料性能有变化。
(1)模具问题:
1不合理的模子尺寸;
2制品顶出时变形;
3物料充模不均;
4充模料流中断;
5不合理的浇口尺寸;
6不合理的分流道尺寸;
7模子造成的注射周期反常。
(2)设备问题:
1加料系统不正常(柱塞式注压机)
2螺杆停止作用不正常;
3螺杆转速不正常;
4背压调节不均;
5液压系统止回阀不正常;
6热电偶失灵;
7温度控制系统不正常;
8电阻电热圈(或远红外加热装置)不正常;
9塑化容量不足;
10设备造成的注射周期反常。
(3)注塑条件问题:
1模温不均;
2注射压力低,提高它;
3充模不足,加长注射时间,加长全压时间;
4料筒温度太高,降低它;
5喷嘴温度太高,降低它;
6操作造成的注射周期反常。
(4)物料问题:
1每批物料性能有变化;
2物料颗料大小无规律;
3物料不干。
怎样防止产品粘贴模内
如果制品粘贴
产品粘贴模内主要由于模塑不善顶出不足,注料不足以及不正确的模具设计。
模内,注塑过程不可能正常。
(1)模具问题:
如果塑料粘贴模内是由于注料不足造成,不要采用顶出机构;
去除倒切口(陷槽);
去除凿纹、刻痕以及其他的伤痕;
改善模子表面的光滑性;
抛光模子表面动作方向应与注射方向一致;
增加斜度;
增加有效顶出面积;
改变顶出位置;
校核顶出机构的操作;
在深抽芯模塑中,增强真空破坏及气压抽芯;
模塑过程中检查模腔是否变形,模架是否变形;
检查开模时,模子有否偏移;
减小浇口尺寸;
增设辅助浇口;
重新安排浇口位置,(13)(14)(15)旨在减少模腔内压力;
平衡多模槽的充模速率;
防止注射断流;
如果制件设计不善,重新设计;
克服模子造成的注塑周期反常。
(2)注塑问题:
1增加脱模剂或改善脱模剂;
2调正物料供给量;
3降低注射压力;
4缩短注射时间;
5减少全压时间;
6降低模温;
7增加注射周期;
8克服注塑条件造成的注塑周期反常。
(3)物料问题:
1清除物料污染;
2物料中加润滑剂;
3干燥物料。
1修缮顶出机构;
2如果顶出行程不足,加长它;
3校对模板是否平行;
4克服设备造成的注塑周期反常。
怎样克服塑料粘贴流道
塑料粘贴流道是由于注口与喷嘴圆弧接触面不良,浇口料未同制品一起脱模以及不正常的填料。
通常,主流道直径要足够大,使制件脱模时浇口料仍未全部固化。
(1)流道与模具问题:
①流道注口与喷嘴必须配偶好;
2确保喷嘴喷孔不大于流道注口直径;
3抛光主流道;
4增加主流道锥度;
5调正主流道直径;
6控制流道温度;
7增加浇口料拉出力;
8降低模具温度。
(2)注塑条件问题:
①采用流道切断;
②减少注射供料;
6降低物料温度;
7降低料筒温度;
8降低喷嘴温度;
(3)物料问题:
①清理物料污染;
②干燥物料。
怎样防止喷嘴流涎喷嘴流涎主要由于物料过热,粘度变小。
(1)喷嘴与模子问题:
①采用弹簧针阀式喷嘴;
②采用倒斜度喷嘴;
3减小喷嘴孔;
④增加冷料穴。
①降低喷嘴温度;
②采用流道切断;
③降低物料温度;
600
4降低注塑压力;
5缩短注射时间;
⑥减少全压时间。
①检查物料是否污染;
怎样避免产品凹痕和气孔产品凹痕通常由于制品上受力不足、物料充模不足以及制品设计不合理,凹痕常出现在与薄壁相近的厚壁部分。
气孔的造成是由于模腔内塑料不足,外圈塑料冷却固化,内部塑料产生收缩形成真空。
多半由于吸湿性物料未干燥好,以及物料中残留单体及其他化合物而造成的。
判断气孔造成的原因,只要观察塑料制品的气泡在开模时瞬时出现还是冷却后出现。
如果当开模时瞬时出现,多半是物料问题,如果是冷却后出现的则属于模子或注塑条件问题。
①干燥物料
②加润滑剂
3降低物料中挥发物
(2)注塑条件问题
①注射量不足;
②提高注射压力;
3增加注射时间;
4增加全压时间;
5提高注射速度;
⑥增加注射周期;
7操作原因造成的注射周期反常。
(3)温度问题①物料太热造成过量收缩;
②物料太冷造成充料压实不足;
3模温太高造成模壁处物料不能很快固化;
④模温太低造成充模不足;
5模子有局部过热点;
⑥改变冷却方案。
(4)模具问题;
①增大浇口;
②增大分流道;
3增大主流道;
4增大喷嘴孔;
5改进模子排气;
6平衡充模速率;
7避免充模料流中断;
⑧浇口进料安排在制品厚壁部位;
9如果有可能,减少制品壁厚差异;
10模子造成的注射周期反常。
(5)设备问题:
①增大注压机的塑化容量;
②使注射周期正常;
(6)冷却条件问题: