木工平刨床安全Word格式文档下载.docx
《木工平刨床安全Word格式文档下载.docx》由会员分享,可在线阅读,更多相关《木工平刨床安全Word格式文档下载.docx(41页珍藏版)》请在冰豆网上搜索。
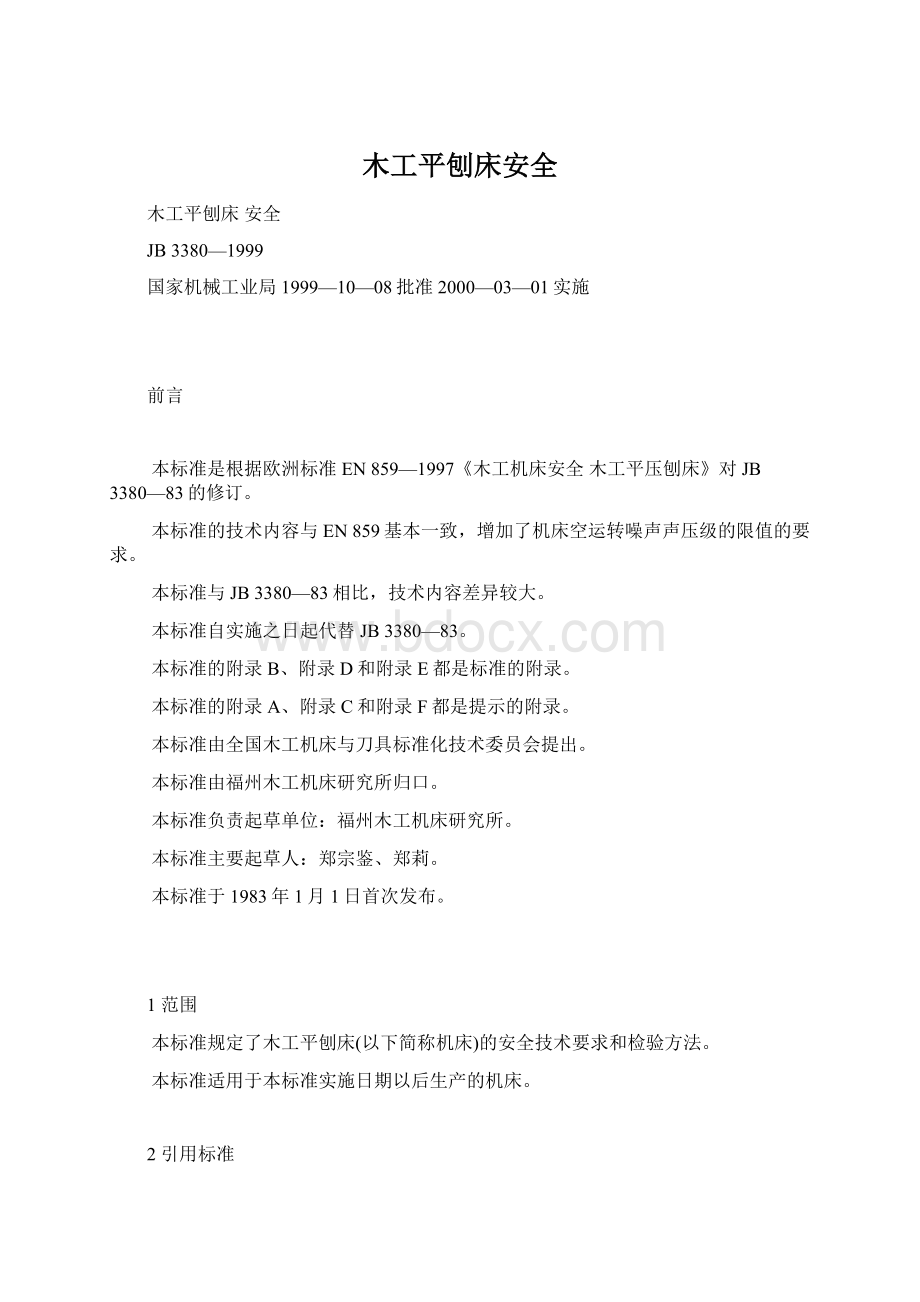
3.1定义
对本标准而言,下列定义是适用的。
3.1.1木工平刨床
见GB/T15377—1994中2.5.1。
3.1.2刨刀体
见GB/T15377—1994中4.1.3。
3.1.3刨刀轴
见GB/T15377—1994中4.1.4。
刨刀轴也称刀具。
3.1.4手动进给
见GB12557—2000中3.3。
3.1.5可拆卸的机动进给装置
见GB12557—2000中3.4。
3.1.6抛射
见GB12557—2000中3.10。
3.1.7返弹
见GB12557—2000中3.11。
3.1.8起动时间
见GB12557—2000中3.13。
3.1.9惯性运转时间
见GB12557—2000中3.14。
3.1.10操作者位置
操作者站着将工件向刀具进给的位置。
3.1.11保证书
见GB12557—2000中3.15。
3.2术语
见GB/T15377和GB/T15379。
4危险一览表
危险一览表(见表1)涉及了本机床的所有危险:
——对于重要的危险通过规定安全要求和/或措施,或者通过指示恰当的B类标准;
——对于不重要的危险,例如一般的、从属的或者次要的危险通过指示适当的A类标准,特别是GB/T15706.1~15706.2,这些危险是按照GB/T16755而提出的。
表1危险一览表
序号
危险
符合本标准的条文
1
机械危险,如由机器部件或工件的下列要素引起的:
形状;
相对位置;
质量和稳定性(各零件的位能);
质量和速度(各零件的动能);
机械强度不足;
由以下原因引起的位能积累:
弹性零件(弹簧)或压力下的液体或气体
1.1
1.2
1.3
1.4
1.5
1.6
1.7
1.8
1.9
1.10
1.11
1.12
挤压危险
剪切危险
缠绕危险
切割或切断危险
引入或卷入危险
冲击危险
刺伤或扎伤危险
摩擦或磨损危险
高压流体喷射危险
(机械或被加工的材料或工件)部件抛射危险
(机械或机床的零件)不稳定
与机械有关的滑倒、倾倒、跌倒危险
5.2.7
不适合
5.2.1,5.2.3,5.2.5
5.2.1
2
2.1
2.2
2.3
2.4
电气危险,诸如下列各因素引起的:
电接触(直接或间接)
静电现象
热辐射或其他现象,如熔化粒子的喷射、短路、化学效应、过载等
电气设备外部影响
5.3.4
5.3.12
3
3.1
3.2
热危险,由下列各因素引起:
通过人们可接触的火焰或爆炸;
热源辐射的烧伤和烫伤
出于热或冷的工作环境对健康的影响
4
4.1
4.2
由噪声产生的危险导致:
听力损失等
干扰语言通讯、听觉信号等
5.3.2
5
由振动产生的危险
6
由辐射产生的危险(例如离子辐射源)
7
7.1
7.2
7.3
由机械加工的、使用的或排出的材料和物质产生的危险,例如:
由于接触或吸人有害的液体、气体、烟雾和灰尘导致的危险
火或爆炸危险
生物和微生物(病毒或细菌)
5.3.3
5.3.1
8
8.1
8.2
8.3
8.4
8.5
8.6
在设计时忽略人类工效学产生的危险(机械与人的特征和能否匹配),产生的例子:
不利于健康的姿态或过分用力
不适当的考虑人的手/手臂或脚/腿构造
忽略了使用个人防护装备
不适当的工作面照明
精神过分紧张或准备不足等
人的差错
5.1.2,5.3.5
5.2.6
6.3
9
各种危险的组合
10
10.1
10.2
10.3
10.4
10.5
由于能源故障、机械零件损坏或其他功能故障产生的危险,例如:
能源故障(能量或控制电路)
机械零件或流体意外抛射
控制系统的失效、失灵(意外起动,意外过流)
装配错误
机械翻倒、意外失去稳定性
5.1.8
5.1.1,5.1.9
5.2.1
11
11.1
11.2
11.3
11.4
11.5
11.6
11.?
11.8
11.9
11.10
由于防护措施中止(短时的)或防护措施设置错误产生的危险,例如:
各类防护装置
各类安全有关的(防护)装置
起动装置和停机装置
安全信号和信号装置
各类信息和报警装置
能源切断装置
急停装置
工件的进给/取出装置
安全调整和/或维修的主要设备和附件
气体等的排送设备
5.2.6,5.2.7
5.1.2
6.1,6.2
6.2,6.3
5.3.16
5安全要求和/或措施
机床的安全除应符合本标准的规定外,还应符合GB12557、GB/T15706.1和GB/T15706.2的规定。
通过设计减小风险的有关的指示按GB/T15706.2—1995中第3章。
5.1控制和指令装置
5.1.1控制系统的安全性和可靠性
对本标准而言,有关安全控制系统包括从最初的手动操纵器或位置开关到最终的传动人口,例如电动机系统。
本机床的有关安全控制部件包括:
——起动(见5.1.3);
——正常停止(见5.1.4);
一一制动(如果需要,见5.2.4)。
这些控制应至少用被验证的元(零)件和原则予以设计和制造。
对本标准而言,经验证的元件和原则是指:
a)下列电气的元件应符合相应国家标准和行业标准,尤其是下列元器件:
——用强制切断的控制开关,其用于联锁的防护装置中作为机械操作的位置开关和用于控制电路上的开关;
——用于主电路的电气机械接触器和电动机起动器;
——橡胶绝缘导线;
——通过布线(例如机床床身内部)附加抗机械损坏的防护的PVC导线。
b)在电的原则方面,它是否符合GB/T5226.1—1996中9.4.2.1规定的前面四种措施。
电子元件另外规定,不采用这项原则。
c)机械的零、部件是否符合GB/T15706.2—1995中3.5的规定。
检验方法:
检查相应的图样和/或电路图,在机床上检验,符合相应标准的证明。
5.1.2操纵器的位置
用于机床起动,正常停止的主要电气控制操作件应是:
—一机床上工件的输入端,离地高度一般不低于600mm的位置上;
——工件输入端的悬挂式的操作面板,其上表面一般不高于地面1700mm,其前面与工件输入端工作台边缘的距离一般不超过600mm。
前面应不伸出乎刨工作台操作者一侧之外。
检查相应图样,在机床上做测量和检验。
5.1.3起动
对于结构上使用可折卸的机动进给装置的机床,只有在刀轴电动机转动后,进给电动机才能起动。
检查相应的图样和/或电路图,在机床上观察或进行功能试验。
5.1.4正常停止
应装有停止所有操作件的正常停止控制,见GB12557—2000中5.2.5。
正常停止应是:
a)1类按GB/T5226.1—1996中9.2.2,适用于装有电气制动器的机床;
b)0类按GB/T5226.1—1996中9.2.2,适用于其他情况。
对于1类停止,停止顺序应是:
——切断一个插头的动力,如果提供作为一个可拆卸的机动进给装置的连接;
——切断刀轴驱动电动机的动力和操作制动器;
——切断制动器的动力,如果是电气的制动器在刀轴停止转动后进行,例如通过一个时间继电器;
——切断机床各操作件的动力。
正常停止的切断顺序必须通过相应的控制电路的结构来实现。
如果使用一时间继电器,则延时至少等于最短的制动时间。
延时装置应是固定的,或延时装置、调整装置是密封的。
检查相应的图样和/或电路图,在机床上观察和进行功能试验。
5.1.5紧急停止
不需要。
5.1.6工作模式的选择
不适合。
5.1.7速度改变
5.1.8能源的故障
对于用电驱动的机床,在电源中断的情况下,电源电压复原以后,自动再起动的防护装置应符合GB/T5226.1—1996中7.5的第1段和第3段要求。
检查相应的图样和/或电路图,在机床上检验和进行功能试验。
5.1.9控制电路故障
见5.1.1。
5.2机械危险的防护措施
5.2.1稳定性
机床的结构应具备将其固定在地面、台或其他稳定的结构上的措施,例如在机床底座有孔。
检查相应的图样,检验。
5.2.2运转中断裂的风险
工作台唇板见5.2.6.1。
对刀具的要求见5.2.3。
对防护装置的要求见5.2.8。
5.2.3刀夹和刀具的结构
机床的刀轴必须是装配式圆柱形结构。
机床的装配式刀具的一般要求见JB6113的相应要求。
附加均要求和更改要求见附录B(标准的附录)。
检查相应的图样。
5.2.4制动
5.2.4.1一般要求
只装有一个开关用于起动、停车和隔离的机床建议装有一个自动的机械制动器。
在机床上装有电的自动制动器的场合,主隔离开关不应固定在机床或悬挂式操作面板上正常停止控制器的同一侧。
在采用反接电流制动的场合,应是不可能使刀轴反转。
当不制动的惯性运动时间超过10s,建议设置一个自动的制动器。
采用制动器制动的时间应是:
小于10s,或在起动时间超过10s的场合,应小于起动时间但不得超过30s。
对于不制动的惯性运动时间、起动时间和制动时间,见下列相应试验。
5.2.4.2所有试验的条件
主轴组件应按制造者说明书进行调整(例如皮带的张紧)。
检验前,机床应至少做15min的空运转,以便刀轴组件的升温。
证明刀轴的实际速度的偏差在额定转速的10%范围内。
当试验一个有手动星三角起动器的情况,应阅读机床制造者的关于起动的说明。
速度测量仪器的精度应为全读数的+1%。
时间测量仪器的精度应为±
0.1s。
5.2.4.3试验
5.2.4.3.1不制动的惯性运转时间
不制动的惯性运转时间按以下测量:
a)切断主轴驱动电动机的动力,测量不制动的惯性运转时间;
b)重新起动主轴,并使其达到正常转速;
c)再重复步骤a)和b)两次。
机床不制动的惯性运动时间是上述三次测量的平均值。
5.2.4.3.2起动时间
起动时间按以下测量:
a)切断驱动电动机主轴的动力,使主轴完全停止;
b)重新起动主轴,测量其起动时间;
起动时间是上述三次测量的平均值。
5.2.4.3.3制动时间
制动时间应按下列测量:
9)停止主轴驱动电动机,测量制动时间;
b)使主轴停止1min;
c)重新起动主轴并空运转1min;
d)重复a)~c)的试验九次。
10次测量的平均值为机床的制动时间。
5.2.4.4制动释放
在装有一个控制器用以释放主轴制动器,以便用手转动和调整刀具的场合,制动器的释放只有当主轴已经停止运转才可进行。
例如通过在控制操作和制动释放之间的延时。
5.2.5将抛射的可能性和影响降低到最小的装置
5.2.6工件的支承和导向
5.2.6.1对工作台的要求
a)在刀轴端部进行裁口加工的机床必须在使用说明书中说明裁口加工的安全工作方法。
b)建议机床后工作台的垂直调整限制到刀轴切削圆直径以下1.1mm。
c)切削深度超过1mm的机床应设置有前工作台垂直方向调整装置。
d)前、后工作台平面度应按GB/T13569—1992中的G1规定。
e)设置有前工作台垂直调整装置的机床,应在整个调整范围上保持与后工作台台面的平行度(要求按GB/T13569—1992中G2);
调整范围限制到切削深度不超过8mm(带裁口的机床除外)。
f)工作台应用轻合金、铸铁或钢制造;
其抗拉强度不低于200N/mm2。
——工作台唇板(做成与工作台一体或可拆卸的零件)应用钢、轻合金或铸铁制造;
——用轻合金、铸铁或型钢板制造的工作台唇板应进行附录E(标准的附录)中的试验;
——用钢制造的带孔和槽的工作台唇板最小的抗冲击韧度为3.5J/cm2。
g)工作台应是:
——无论工作台调整到任何高度,工作台唇板与切削圆之间的径向距离为3mm±
2mm(见图1)。
——工作台或工作台唇板有开槽的(为了降噪),槽宽度不得超过6mm,长度不得超过15mm。
齿的宽度至少为6mm。
在顶部齿的厚度最小值为1.5mm,在槽的根部至少为5mm(见图2);
——槽的长度超过15mm的工作台唇板应按附录E做试验;
——工作台或工作台唇板有孔的(为了降噪),孔应是错开排列的,并且用直径为6mm的圆柱销不得通过。
h)工作台的尺寸,建议按表2的规定。
i)如果机床结构上可带可拆卸的机动进给装置,则该装置应固定在导向板后面。
表2工作台尺寸mm
最大加工宽度B
工作台前端与刀轴回转轴线之间的距离L
(在零切削位置上测量)
≤600
2B
>
600
1200
检查相应图样、材料制造者的保证书,测量、检验。
5.2.6.2工件的导向
机床应装有一个导向板。
导向板连接在机床上,对于最大加工宽度大于160mm的机床,导向板不使用工具应在整个刀轴长度上在侧向可调。
在装有可倾斜导向板的场合,其标准位置是与工作面成90°
,其运动应由一挡块限制,运动的极限是从前工作台的端部看,其应离正常位置/顷时针方向45°
。
倾斜导向板与后工作台在导向板前面之间的自由距离不应超过5mm,在导向板的所有位置上均是如此(例如定位在45°
倾斜加工位置)。
倾斜导向板在后面与刀轴防护装置之间的间隙不得大于防护装置高度。
导向板相对于机床最大加工宽度的尺寸,建议按表3。
在任意位置上后工作台与导向板下表面之间的间隙不得超过5mm。
表3导向板尺寸mm
机床最大加工宽度B
导向板在刀轴轴线两边的最小长度L1)
导向板高度C
≤260
≥1.15B
≥120
260
550
≥150
1)不超过工作台长度。
在采用一整体的导向板加工薄工件的场合,例如将其连接到主导向板上(见图3),其高度应不小于20mm,不大于25mm,其宽度不超过60mm。
检查相应图样,在机床上进行检验测量和功能试验。
5.2.7对进入机床运动零、部件的防护
不同种类的防护装置和安全装置的定义确定和要求的指示见GB/T15706.1和GB/T15706.2。
5.2.7.1手动进给机床的刀具安全防护
导向板前面和后面的防护装置应设计成不将其拆卸就不能将其移动出工作位置。
5.2.7.1.1在导向板前面的安全防护
刀具应由固定在机床上一个可调式或自调式的防护装置来防护。
例如固定在机床后工作台的床身上。
防护装置满足下列要求:
a)不用工具就能对防护装置进行调整;
b)应能手动或自动调整防护装置,以将其与导向板之间的间隙减小到不大于6mm,并覆盖刀轴在导向板前面的暴露长度,而与导向板和工作台的位置无关;
c)防护装置应是形状中凸的,或平的,应设计成加工中人手的部分能与工件保持接触,防护装置的上表面应是平滑没有突出物(实例,见图4);
d)防护装置的下表面应设计当防护装置被压到工作台台面时其不能与刀轴接触;
e)防护装置的结构应使得不拆卸其就能进行换刀。
5.2.7,1.1.1防护装置的类型
在机床最大加工宽度小于或等于100mm的机床上,防护装置可采用桥式防护装置或扇形板式防护装置(扇形板式见图7)。
在最大加工宽度大于100mm的机床上,可采用桥式防护装置。
5.2.7.1.1.2桥式防护装置的特别要求
以下要求[见附录A(提示的附录)]是对5.2.7.1.1要求的增加:
a)防护装置应经附录D(标准的附录)要求的试验合格。
b)它应能在任何工作位置上不借助工具就能锁紧防护装置的调整装置;
当受一个80N的轴向力作用时,防护装置能保持在锁紧位置上。
c)防护装置高度方向能在离后工作台台面0~75mm(max)无级可调;
d)建议防护装置被压下后应能自动返回到预先调整的位置;
e)在静止状态和整个调整范围内:
——当前、后工作台处于最大开口位置时,防护装置应能覆盖住与工作台唇板相切的两个垂直平面围出的区域;
——在前工作台一边的桥板的边与工件的上表面之间的距离最大值为2mm(见图5);
——在后工作台一边的桥板的边与工件上表面距离最大值为3mm(见图5)。
f)防护装置的所有调整装置均应在操作者位置上可达的。
g)桥板的上表面应是中凸形的,下表面应做成不妨碍对工件通过整个机床。
h)防护装置突出机床不得超过550mm。
i)防护装置的最大宽度:
——刀体长度小于或等于350mm的机床为100mm;
——刀体长度大于350mm的机床为120mm。
j)桥板在前工作台这边的引入边缘的形状应满足图6a)和图6b)的要求。
k)自调式的防护装置应设计成能向导向板方向施加15~30N的轴向力。
5.2.7.1.1.3对扇形板式防护装置的特别要求:
a)防护装置应满足附录D中第D1章和第D2章的型式试验的要求,护板应用在与刀体接触的情况下或是刀体或是防护板不会分离的材料制造(例如木材、铝);
b)防护装置应弹簧加载30N±
10%,这力施加在将工件压向导向板的方向上;
c)护板的厚度最大值为10mm;
d)防护装置进给的接触角超过15°
(见图7)。
5.2.7.1.1.4导向板后面的防护装置
在导向板后面进入刀轴应由一固定在导向板上或是固定在导向板支承上的防护装置来防护。
这防护装置应做成:
——随导向板移动;
——能覆盖刀体的全长和直径;
——不能与刀片相接触。
5.2.7.2在机械进给的机床上的防护
5.2.7.3传动的防护
刀具的传动机构应用固定式防护装置防护。
5.2.8防护装置的特性
刀具的防护装置除在导向板前面的防护装置外,应使用下列材料之一制造:
a)钢,抗拉强度大于或等于350N/mm2,壁厚大于或等于2mm;
b)轻合金,抗拉强度大于或等于185N/mm2,壁厚大于或等于5mm;
c)铸铁,抗拉强度大于或等于350N/mm2,壁厚大于或等于5mm;
d)硬木或胶合板,厚度至少8mm。
检查相应的图样,测量、核对材料制造者的证明。
5.3非机械危险的防护措施
5.3.1火和爆炸
应满足5.3.3和5.3.4的要求。
以避免和防护火和爆炸的危险。
5.3.2噪声
5.3.2.1空载噪声声压级限值及测定
机床在空运转条件下,按JB/T9953测定出机床的最大噪声声压级不得超过表4规定。
表4空载噪声声压级限值
mm
≤400
400~630
630
空运转最大噪声声压级
dB(A)
83
85
90
测定时机床的工作(运转)条件及操作者位置上噪声测定按附录F(提示的附录)中表F1。
环境修正值K2A小于或等于4dB。
5.3.2.2噪声声功率级的测定
在标准实施2年之内,应做一次噪声声功率级的测定。
测出的机床噪声声功率连同工作(运转)条件及遵守的测定方法记入机床的使用说明书。
测定方法按GB12557—2000中5.4.2.2.2的规定。
测定时机床的工作(运转)条件按附录F。
5.3.3木屑、粉尘和气体的排放
应提供一个整体的吸收和采集系统,或通过设置一个吸尘口能使机床被接人单独的木屑和粉尘的收集系统中。
注:
为了保证木屑和粉尘从它们原始的点被输送到收集系统,吸尘罩、导管、挡板的结构建议基于抽出气体在导管中的速度为20ms-1(含水率小于或等于18%木屑)和26ms-1(含水率在18%以上的木屑)。