汽车前轮毂铸造工艺设计范例Word文档下载推荐.docx
《汽车前轮毂铸造工艺设计范例Word文档下载推荐.docx》由会员分享,可在线阅读,更多相关《汽车前轮毂铸造工艺设计范例Word文档下载推荐.docx(19页珍藏版)》请在冰豆网上搜索。
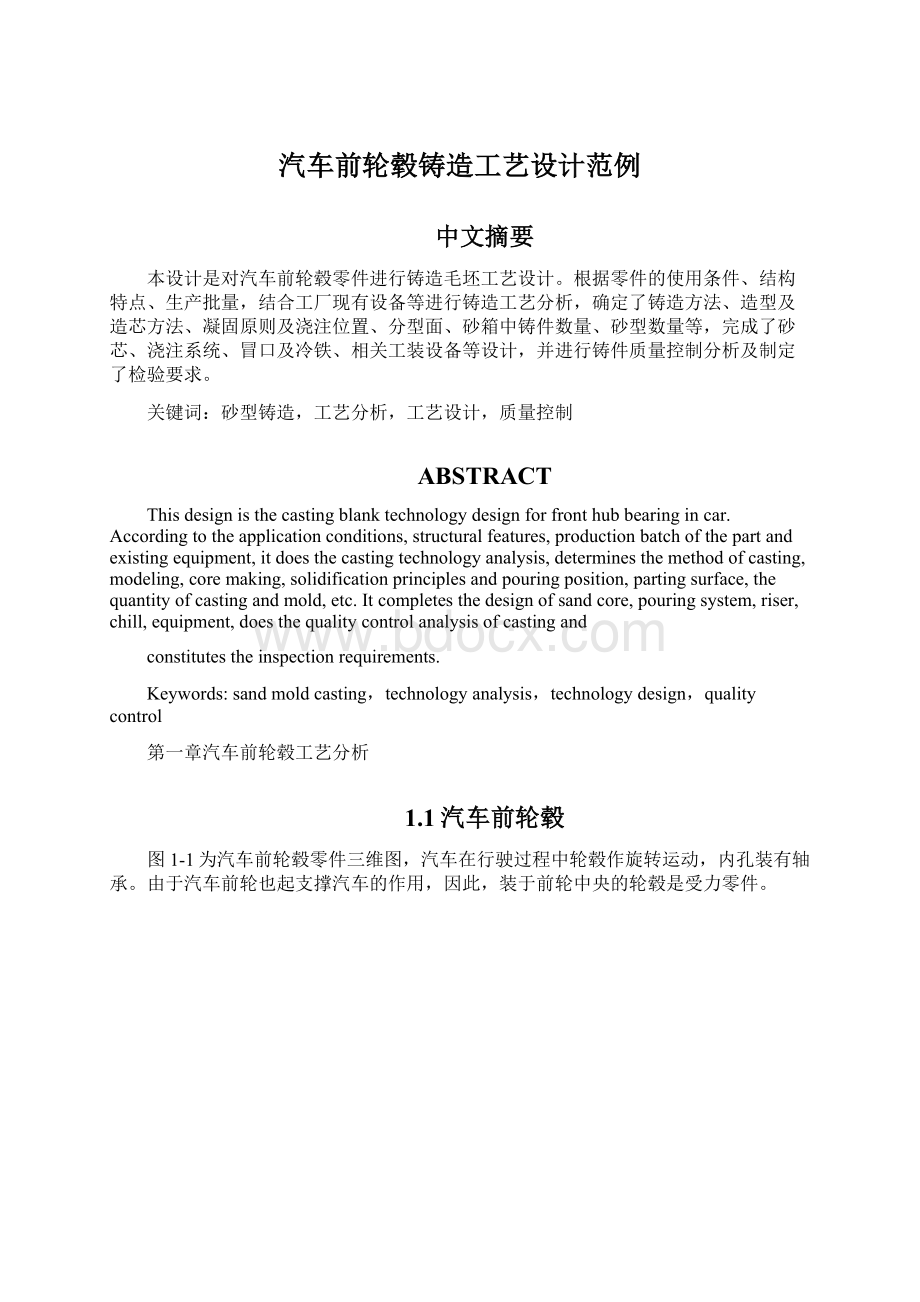
根据零件轮廓尺寸420×
173mm3和工厂设备条件,造型方法为Z148B单机砂箱地面造型,气吊与行车运输,造芯方法为手工芯盒造芯。
2.3凝固原则、浇注位置的确定
凝固原则:
铸件材质为ZG270-500,收缩较大(εV=4.3%),为了有利于补缩,采用顺序凝固。
浇注位置:
为了保证铸件质量,必须把最重要的加工面在浇注时向下或直立状态。
由零件的技术要求知道:
Φ200和Φ210的圆表面光洁度要求高,内部安装轴承,尺寸精度比较高,因此,应将两圆柱面呈直立状态,同时从顺序凝固的原则出发,将厚大部位放在上面,以便于安放冒口,得到顺序凝固。
综合考虑结果:
确定本件的浇注位置如图2-1所示。
图2-1浇注位置
冷却位置与浇注位置一致。
2.4分型面的选择
此件可有三种分型面方案:
方案І:
,如图2-2所示可将铸件对称分布在两铸型内,模样易制作,但造型、下芯不方便,铸件内孔的精度不易保证,且为了保证浇注位置须将铸型翻转90º
,劳动量大。
图2-2方案Ⅰ
方案II:
如图2-3所示铸件在同一铸型内,可以保证其尺寸精度,且下芯后便于检查壁厚是否均匀,砂型稳固,造型简单,但顶注不平稳,易产生冲砂,同时上箱小,下箱大,起模行程大。
有一个砂芯较大,不易制作。
图2-3方案Ⅱ
方案III:
如图2-4所示铸件大部分在同一铸型内,能够保证其尺寸精度,下芯也便于检查,同时满足合箱,浇注,冷却位置一致,采用侧浇,切向引入改善了浇注时的充型不平稳,减少了冲击,防止了冲砂缺陷的产生,上、下箱相差不大,造型简单。
缺点是有一个砂芯复杂,要求高,模样加工困难。
图2-4方案Ⅲ
经过比较,综合考虑,为保证铸件质量,采用方案III较合理。
2.5砂箱中铸件数量的确定
由[3]附录附表1-1查得Z148B造型机所对应的砂箱最大内尺寸长X宽为850X475mm2,四个顶杆间距长X宽为736X538,根据铸件重量63.2kg由[3]表12-3查得其最小吃砂量各参数为:
a=50mm,b=70mm,c=90mm,d=70mm,f=40mm,g=50mm,铸件轮廓为420×
184mm3,因此砂箱中最多只能放一只铸件。
2.6砂芯数量的确定
根据铸件结构和已选定的分型面,必用两个芯子,如图2-5所示。
图2-5砂芯数量图
2.7主要工艺参数的确定
2.7.1铸造收缩率的选择
根据实际生产情况,并参考[3]表3-1,确定该件的收缩率为2%。
2.7.2铸造精度及尺寸、重量偏差的确定
由于铸件的精度要求较高,且是机器造型金属模,确定该件的精度为Ⅰ级,由[3]表3-17查得尺寸偏差为±
2.5mm,表3-20查得重量偏差8%。
2.7.3机械加工余量的确定
按一级精度铸件查[3]表3-7,并考虑实际情况,确定加工余量,具体数值见铸件工艺图。
2.7.4拔模斜度的确定
按零件图尺寸采用增厚法。
根据[3]表3-21确定拔模斜度为1º
30'
-2º
。
2.8砂芯设计
铸件需2个砂芯,均用手工芯盒造芯。
砂芯由砂芯主体和芯头组成,1#砂芯用水玻璃砂,根据铸件放置位置确定为垂直芯头,结合其基本尺寸参考[3]表4-2取下芯头高为50mm,因砂芯高度和直径差不多,不用上芯头,由表4-3确定下芯头斜度为5°
,由表4-4确定下芯头与芯座间隙为1.5mm,由表4-7确定防压环和集砂槽的尺寸,2#砂芯形状复杂,局部有细薄突起,故2#芯选用脂砂,详见铸件工艺图。
合箱时先下1#砂芯,后下2#砂芯。
2.9浇注系统的设计
浇注系统由浇口杯、直浇道、横浇道和内浇道组成。
浇注系统截面积大小对铸件质量影响很大,截面积太小,浇注时间长,可能产生浇不足、冷隔、砂眼等缺陷;
截面积过大,浇注速度快,又可能收起冲砂,带入熔潭和气体,使铸件产生渣孔、气孔等缺陷。
为了使金属液以适宜的速度充填铸型,就必须合理确定浇注系统的面积。
2.9.1浇注系统类型的选择
由于铸件材质为ZG270-500,铸造质量要求较高。
浇注系统应要求较高的防氧化能力,本应采取漏包浇注,但由于铸件较小,使用漏包不易控制,为此使用转包浇注。
采用转包浇注铸钢件,浇注系统应有较好的撇渣能力,需要用封闭式或半封闭式,本设计浇注系统采用封闭式的,根据[6]表5-53,及工厂的情况,选用侧注式浇注系统。
因砂箱中只放置一个铸件,所以浇注系统只需设计浇口杯、直浇道和内浇道,无横浇道,使铸件内腔与内浇道相切,内浇道与直浇道相连,采用梯形的内浇道。
2.9.2浇注系统的设计与计算
因采用了转包浇注,浇注系统是封闭式的,其浇注方式与铸铁件相同,所以计算公式都采用转包浇注铸铁件公式,但式中的系数选择不一样,以此计算出该浇注系统浇注时间、内浇道截面积、浇注系统各组元断面尺寸,并校核最小压力头。
1浇口杯设计:
浇口杯是用来接纳来自浇包的金属液流的,因为铸件是小型的铸钢件,所以浇口杯采用结构简便、制作方便、容积小、在机器造型中广泛使用的普通漏斗形浇口杯,其截面形状与尺寸如图2-6中a所示。
2浇注时间:
其中:
C是系数根据相对密度KV查取,G是浇入砂型内钢水的总重量(kg)。
式中V是铸件的轮廓体积。
V=π/4×
4.22×
1.84=25.5dm3
取铸件重量是零件重量放大15%得到55(1+15%)=63.2(kg)
浇冒口系统选铸件重量的50%,即:
G=63.5(1+15%)=94.8(kg)
由[3]表5-34查得C=1.1
故浇注时间
=10.7秒
选取t=11秒。
3内浇道截面积的计算:
由[3]P132查得以浇注比速为基础的计算公式:
式中:
G=94.8kg,t=11秒,K是浇注速比由表5-34查得0.75(根据KV=3.7查表),L是钢水流动系数,碳钢L取1.0。
代入上式:
则
≈11.5cm2
截面形状为梯形,根据面积确定尺寸如图2-6中b所示:
abc
图2-6浇口杯、内浇道、内浇道截面形状与尺寸
4各组元面积的确定:
因该浇注系统无横浇道,所以只需再确定直浇道,其截面为圆形,形式为无斜度的圆管,H0即内浇道静压头高度为200mm。
参考[3]P132得比例关系为∑F直:
∑F内=1.1:
1
则∑F直=11.5×
1.1=12.7cm2
由面积确定直径尺寸为40mm,如图2-6中c所示。
5最小压力头的校核:
为了保证能充满离最远最高的部分,并且能轮廓清晰完整,上表面无缩凹缺陷的铸件,铸件最高点到浇口杯内液面的高度必须有一最小值,即最小剩余压力头Hm,这就要求直浇道应该有必要的高度。
由所设计的铸件工艺图可得到如图2-7最小剩余压力头的压力角简图:
L=300+210=510mm
Hm=200-30=170mm
校核公式tgα=Hm/L=170/510=0.337
查得α=18º
26'
α是最小剩余压力头的压力角,L是直浇道到铸件最高最远的距离,Hm是最小剩余压力头。
由[3]表5-8查得α=9º
,故压力头足够。
图2-7最小剩余压力头的压力角简图
2.10冒口及冷铁的设计
2.10.1冒口的设计
铸件法兰与轮毂体交接处形成热节,容易产生分散性的缩松,严重降低铸件的机械强度。
该件在汽车工作时是个受力件,其技术条件要求铸件内部不得有缩孔、缩松等缺陷,所以在铸件上必需设置一定数量的冒口以消除缩孔、缩松。
因铸件在上砂箱高度只有30mm,且铸件较小并采用机器造型,为减少冒口的金属消耗而采用暗顶型。
冒口设置在铸件最高最厚的部位。
铸钢件冒口的计算方法很多,常用的方法有按照补缩液量计算、按照比例法计算、按照模数法诸,本设计用按照比例法中的热节圆法计算设计。
1确定热节圆直径
用作图得热节圆直径dy(作图时包括加工余量、补贴等),如图2-8所示。
2-8作图法求热节圆
dy由计算机作图得34,取dy=40mm。
2确定冒口形状、尺寸
冒口的尺寸对于铸件的质量很重要,冒口过小将导致铸件产生缩孔、缩松等缺陷;
冒口过大,浪费金属,增加铸件成本,甚至有时会因冒口过在,使铸件局部组织粗大,内应力过大,造成裂纹,致使铸件报废,所以冒口尺寸应查表确定。
由铸件结构特点在[3]表6-7中选第3号腰形暗冒口:
因为H件/dy=184/40=4.6(H件是铸件高度)
所以B=(2.1~2.5)dy=(2.1~2.5)×
40=84~100(B为冒口宽度)
取B=85mm
H=1.5B=1.5×
85=127.5mm,取H=120mm(H为冒口高度)
冒口形状尺寸如图2-9所示。
图2-9冒口形状及尺寸
3补贴
为了达到顺序凝固的目的,保证有良好的补缩通道,以充分发挥冒口的补缩作用,在冒口下面增加的铸件工艺余量,即为补贴。
补贴尺寸一般是根据生产经验确定的,查[3]图6-8,该件可不加补贴。
为了提高补缩效果,加补贴6mm。
根据铸件的结构特点及冒口的补缩能力,共放两个,布局如图2-10所示。
2-10冒口布局
2.10.1冒口的校核
1冒口补缩距离的核算:
补缩距离冒口的补缩范围,由[3]表6-4查得该铸件有效补缩距离为(4~6)T(此处T为热节圆直径),铸件冒口补缩距离为两段弧长,如图2-11所示。
计算冒口补缩距离=π×
220-[π×
220(38×
2)/360+2×
42.5]×
2=115mm
(4~6)T=(4~6)×
40=160~240mm
因为115<
160~240
所以冒口补缩距离足够。
图2-11补缩距离
也可由冒口延续度来校核。
由[8表3-10]查得普通铸钢件的冒口延续度为38~40%。
实际冒口延续度=(π×
220×
(38×
4)/360+4×
42.5)/(π×
220)=66.8%
因为66.8%>
40%
所以冒口的补缩距离足够。
2冒口补缩能力的较核:
由[3]表6-16冒口补缩能力的计算查得腰形冒口内缩孔的总体积为0.14V冒,能补缩的最大体积为(14%-εV总)/εV总×
V冒,得到V铸件=(14%-εV总)/εV总×
V冒
式中的εV总查[3]表6-2查得金属凝固时的体收缩率εV总=4.5%
V冒=π[0.852+(3.052-1.352)×
38×
2÷
360]÷
4×
1.2=4.3dm3
V铸件=(14%-4.5%)/4.5%×
4.3=9.07dm3
实际V'
铸件=重量/密度=63.2/7.8=8.1dm3
式中密度取7.8kg/dm3。
由于V铸件>
V'
铸件,冒口足够补缩的。
3工艺出品率核算:
冒口各部分尺寸计算后,应用经过大量生产实践总结出来的“铸件工艺出品率”即成品率来校核,衡量。
工艺出品率太大时,说明所设计的冒口偏小或数量不够,应加大冒口或增加冒口数量;
工艺出品率太小,则应适当减小所设计的冒口。
查由[3]表6-5碳钢及低合金铸件的工艺出品率为61~65%。
实际工艺出品率=铸件毛坯重量/(铸件毛坯重量+浇口重量+冒口重量+补贴重量)=63.2/94.8×
100%=66.6%。
两者接近,所以冒口的尺寸是合理和可行的。
2.10.3冷铁的设计
因铸件是小型件,冒口补缩能力和工艺出品率均符合规定,所以不需要再设置冷铁。
2.11排气的设计
铸件浇注过程中,在型腔中的会产生气体,如果不能及时排出,会产生气孔铸造缺陷,所以应合理设计排气系统。
1砂型的排气
两个冒口是排气通道,上箱造完型后,在二冒口顶部各扎直径16的出气孔一个。
2砂芯的排气
1#垂直砂芯,从下砂箱扎出气孔,使气体由上向下排出,2#砂芯形状较复杂,通气道应通到分型面,使气体由下向上排出。
为增加透气性,砂箱开设了出气孔。
2.12铸件图及铸件工艺图
铸件的生产批量为成批生产,可不出铸件图,用铸件工艺图来指导生产。
铸件工艺图如2-12所示。
图2-12前轮毂铸造工艺图
第三章型、芯砂种类及配方的选择
3.1型砂种类及配方的选择
砂型和砂芯直接承受合金液的作用,关系到铸件质量和生产成本,铸件中的一些缺陷都与造型材料有直接关系,造型材料在生产中占有重要的地位。
铸件材质为ZG270-500,湿型机器造型,浇注温度在1500℃以上,要求型砂透气性好,强度、耐火度高。
因铸钢液含碳量较低,型腔中缺乏防止金属氧化的强还原性气氛,在与铸型相接触的界面上金属容易氧化,生成Fe和其他金属氧化物,因而较易与型砂中的杂质进行化学反应而造成化学粘砂。
所以要求原砂中的SiO2含量应较高,含Si量>
96%,有害杂质应严格控制;
为了防止铸件增碳,要求型砂中泥量低、水分低,因而水分控制在4-4.5%;
型砂中不含煤粉和含泥量低,为了保证铸件表面光洁,不产生机械粘砂,选用较细筛号的硅砂,可选用70号或100号的硅砂,粘接剂为铸造用膨润土。
参考[2]表2-8采用2S石英砂,粒度均匀,其配比和性能见表3-1:
表3-1(面砂配方)
配比(重量%)
型砂性能
新砂
膨润土
重油
水分%
湿压强度
透气性
100(70/100)
7.5
1-1.5
4-4.5
5-7.5N/cm2
110-150
3.2芯砂种类及配方的选择
铸件中需个砂芯,1#垂直芯头,原砂与型砂相同,粘接剂采用水玻璃砂,用CO2硬化,在压力为0.15-0.2.5MPa下,吹气为时间2-3分钟。
芯砂配方见表3-2:
表3-2(水玻璃砂配方)
芯砂配比(重量%)
芯砂性能
水玻璃
湿透气性
干拉强度
100(70/140)
6-7
>
300
90-100N/cm2
2#芯结构较为复杂,原砂与型砂相同,为减少铸件缺陷,采用合脂砂,烘干温度为220℃,烘干时间为3小时,在末冷却前,不宜般动,以防损坏砂芯,合脂配方见表3-3:
表3-3(合脂砂配方)
芯砂配比(%)
干燥规范
合脂
纸浆
湿拉强度
加热温度
保温时间
2.5-3
0.5-1
2.2-3
100-300N/cm2
1.5-2.5N/cm2
220℃
3小时
砂芯表面一般都要刷上涂料,用以提高型芯表层的耐火度、保温性、化学稳定性,使型芯表面光滑,并提高其抵抗高温熔融金属的侵蚀能力。
本铸件砂芯表面涂料成分确定为:
石英粉100、陶土2-4、粘土2、水柏油4、适量的水
第四章工艺装备的设计
铸造工艺装备是铸造生产过程中所用的各种模具、工夹量具,下面就简单介绍一下铸件的模样、模板、芯盒、砂箱的设计。
4.1模样的设计
模样是用形成铸型的型腔,关系到铸件的形状和尺寸精度,铸件的模样是金属模。
1材料
为满足生产的要求:
耐磨、有足够的强度,同时考虑便于加工制造,用ZL104。
2结构设计
如图4-1所示,因模样尺寸较大,所以设计成整铸式空心模样,壁厚为10mm,中间设计加强筋,上、下模样都无特殊要求,与模板配合均采用平放式、上固定法。
用M10的螺钉紧固和两个定位销定位,螺钉孔及销孔与型板配钻,沉头螺钉安装后,均用塑料填平修光。
a上模板装配简图
b下模板装配简图
图4-1模板装配简图
4.2模板的设计
铸件的模板由模样和浇冒口系统模样与模底板通过螺钉、螺栓、定位销装配而成。
模底板的工作面形成铸型的分型面。
模底板的设计:
为满足一定的机械性能要求,同时考虑便于手工加工制造,成本低,选用材料HT150。
结构设计
根据砂箱尺寸,造型机的要求,确定底板板面尺寸为730×
730,高度为90mm,设计的加强筋见上、下模板装配图,定位销与导向销安装在底板上,模上设四个紧固耳,用螺栓把其固定在制造机上,为搬运方便,模底板上设置了四个吊轴。
4.3芯盒的设计
芯盒制造型芯必需的模具,其尺寸精度和结构是否合理,对型芯的质量和造芯效率影响很大,由于本设计为手工制芯,芯盒要求结构简单,体积小,重量轻,操作方便,且要易于制造、修理,故芯盒材料选用ZL104。
根据芯盒的轮廓尺寸和材料,由[3]表11-4选取壁厚为8mm。
外型随形处理,为增加强度和刚度,设置了加强筋,为延长芯盒的使用寿命,刮砂面加设了耐磨片。
根据1#芯的形状特征,采用对开芯盒,由两个可折式定位销定位,夹紧装置采用蝶形螺母和活节螺栓。
4.4砂箱的设计
砂箱的结构既要符合砂型工艺的要求,又要符合车间的造型、运输设备的要求。
铸件砂箱采用整铸式,材料为ZG35,为增加强度,其内设有加强筋,为防止在翻箱过程中发生塌箱,箱壁呈斜形,为增加透气性,开设了出气孔。
根据[3]表12-3,考虑合理的吃砂量及Z148B造型机的要求,砂箱内部尺寸定为650×
650×
200/320,合箱时采用插销定位,合箱后采用锲形卡锁紧。
第五章铸件的熔炼、浇注、落砂、清理、热处理要求
5.1熔炼
原钢水成分:
C:
0.32~0.42%Si:
0.2~0.45%Mn:
0.05~0.80%S<
0.05%P<
0.05%
熔炼设备:
三相电弧炉。
5.2浇注
采用转包浇注,浇注温度:
1510℃~1530℃,浇注前,应把熔融金属表面的熔渣除尽,以免浇入铸型而影响质量。
浇注时,须使浇口杯保持充满,不允许浇注中断,并注意防止飞溅和满溢砂型。
铸型浇注后,铸件在砂型内应有2.5小时的冷却时间。
5.3落砂
落砂方法分为手工落砂和机械落砂。
根据铸件特点并结合工厂落砂设备情况,选用L128落砂。
5.4清理
清理是落砂后从铸件上清除表面粘砂、型砂、多余金属(包括浇冒口、飞翅和氧化皮)等过程的总称。
本铸件采用悬链抛丸室清理,气割浇冒口;
抛丸清理去除氧化皮,喷丸清理内腔,手工剔磨后涂漆。
5.5热处理
为消除铸造应力、细化组织、改善铸件的加工性能,应对清理好后的铸件进行正火处理,正火温度850℃~870℃,保温时间5.5~6.5小时后空冷。
第六章铸造质量控制
6.1铸造缺陷分析及防止措施
本铸件常见的铸件缺陷分析及防止措施:
1.缩孔、缩松
由于铸钢的收缩大,虽然采用了冒口补缩,也可能因浇注工艺不同,而出现缩孔、缩松。
防止措施
严格控制浇注温度。
钢水吸气严重,可能出现气孔,为此,要严格控制型砂水分,砂型要适当的扎气孔,排除气体,更重要的是熔炼过程中把气渣除净。
2.粘砂
铸钢湿型造型,铸件表面金属氧化,氧化物与造型材料作用生成低熔点化合物或浇注时金属液渗入到砂粒间隙。
保证有足够透气性的前提下,尽可能选用粒度细的原砂,提高砂型的紧实度。
3.偏芯
由于1#砂芯没有上芯头,只有下芯头一个定位,抗冲击力差,砂芯在浇注时可能倾倒,使内腔形状和尺寸不符合要求。
在合箱前严格检查砂芯位置。