快速处理综采工作面大型断层超深孔扩裂爆破技术方案Word格式.docx
《快速处理综采工作面大型断层超深孔扩裂爆破技术方案Word格式.docx》由会员分享,可在线阅读,更多相关《快速处理综采工作面大型断层超深孔扩裂爆破技术方案Word格式.docx(16页珍藏版)》请在冰豆网上搜索。
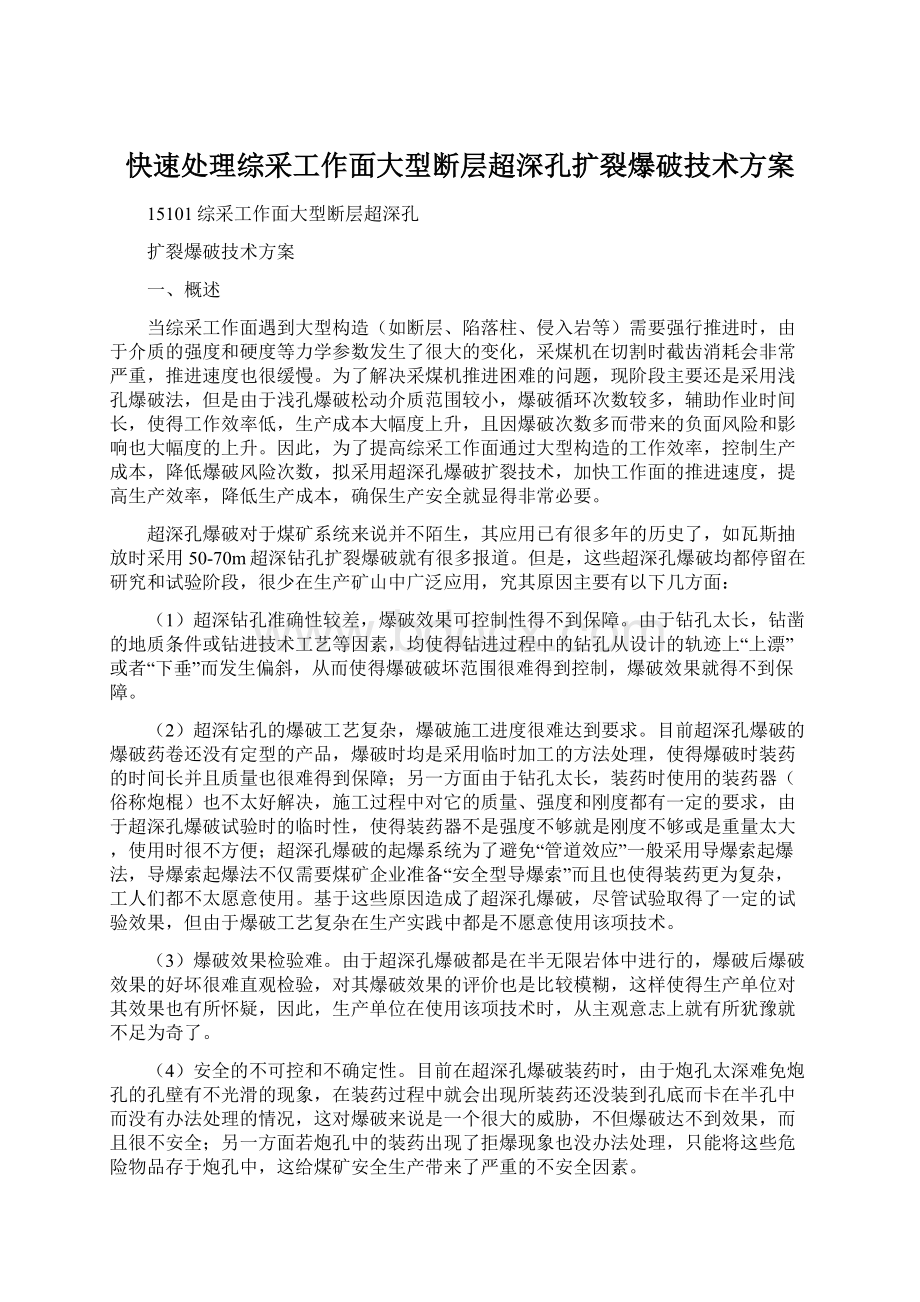
(一)工作面概况
15101工作面走向长150m,倾斜长平均458m,煤层厚度为6.0m,煤层倾角平均为8°
。
15101工作面采用倾斜长壁后退式综合机械化低位放顶煤全部垮落采煤法。
工作面采用MG300/730-WD采煤机,工作面切眼长150m,采高3.0±
0.1m,循环进度0.8m,放煤高度3.0±
0.1m,放顶煤区段平均为135m,“一采一放”为一循环。
工作面共布置102组支架,其中端头支架(型号ZTA6500/19.5/34)6组,中间支架(型号ZF4800/17/32)96组。
目前工作面胶带顺槽推进127.9米,轨道顺槽推进120.6米,平均回采长度124.25米。
截止目前工作面剩余可采长度290米,剩余可采储量34万吨。
(二)工作面煤层及顶底板情况
工作面地面标高+1250—+1340m;
工作面标高+923—+967m。
井下位置及四邻采掘情况:
15101首采工作面南部为专用回风下山、东部为出煤巷、西部为15102工作面回风顺槽。
煤层情况:
工作面开采煤层属下太原组下端下部的15#煤层,该煤层赋存稳定,煤厚变异较小,煤层结构较复杂。
煤体以黑色、块状为主,粒状次之,内夹黄铁矿,呈团块状,煤质为贫煤。
煤层直接顶板为泥岩、砂质泥岩,厚度10m左右,硬度系数3.0;
老顶为K2灰岩,硬度较大,含水性微弱,厚度7m左右,硬度系数6.0;
直接底为铝质泥岩,厚度1.8m左右,硬度系数3.0;
老底为砂质泥岩,厚度3.5m左右,硬度系数3.5—4.0。
(三)工作面地质构造
本工作面总体地势东北高西南低,总体呈一单斜构造。
工作面东部坡度较缓,西部较大,局部地方底板出现起伏变化,形成小型褶曲,在褶曲转折端会造成煤层及顶板裂隙发育,煤层破碎。
在15101工作面轨道顺槽,分别距离内切眼58m处和出煤巷100m处发育有X11和X12两个陷落柱,两陷落柱特征分别为X11:
长轴方向N30º
E,直径42×
26m;
X12:
长轴方向N60º
E,直径54×
32m,且均位于回采范围内,对回采工作有一定的影响。
15101工作面高抽巷在里程269m处揭露一落差1.5m,倾角41°
,倾向为323°
的正断层。
15101工作面胶带顺槽距出煤巷129m处有一小型向斜,在距出煤巷157m处有一小型背斜。
根据首采工作面坑透资料显示,在X11陷落柱距离内切眼10m范围内可能会衍生出一个落差1.5m左右的正断层。
目前工作面在10#支架破煤层底板,割采岩石。
由47#支架位置开始采面进入全岩,全岩至79#结束,其中岩石最厚位于70#支架左右煤层位于回采顶1m,后在90#支架处进入全煤,回采至机尾留有底板三角煤2m左右。
工作面在81#支架处存在一条倾角为50°
,断距为0.5m的Fj1正断层。
预计延伸长度不超过20m,未在轨道顺槽有出露。
(四)工作面水文地质
工作面煤层直接充水含水层为太原组K2灰岩含水层,该含水层赋水性一般较弱。
15101工作面回采范围内地质条件较为简单,局部地方底板出现起伏变化,形成小型向斜及背斜构造,在向斜及背斜转折端会造成煤层及顶板列隙发育,回采至该处时可能会出现涌水增大现象,向斜轴部在回采过程中还会形成积水区。
矿井奥灰水位为:
+823-+825m,本工作面开采最低标高为+923m,故目前不涉及承压开采。
X11和X12陷落柱经钻探验证不导水,高抽巷在掘进至F3断层时,水量无变化。
在回采过程中,由于顶板自然脱落,造成裂隙发育,预计会破坏顶板K2、K3、K4三层含水层,但这三层含水层赋水性都较弱,且已经打设顶板疏放水孔,在回采过程中预计水量约为15m³
/h,施工队组及时完善排水设施保证正常回采。
根据电法勘探显示,15101工作面内无富水区域,
工作面最大涌水量10m3/h;
正常涌水量5m3/h。
(五)煤层自燃性及爆炸倾向性
2015年山西省煤炭工业局综合测试中心对佳瑞煤业14#、15#煤层进行了煤层自燃倾向性鉴定,鉴定结论为:
14#煤层为(Ⅱ)类自燃,
最短发火期为75天;
15#煤层为(Ⅲ)类不易自燃,最短发火期为97天。
2015年山西省煤炭工业局综合测试中心对14#、15#煤层进行了煤尘爆炸性鉴定,鉴定结论为:
14#煤层煤尘具有爆炸性,火焰长度30mm,14号煤煤尘云最大爆炸压力0.56MPa,最大压力上升速率34.71MPa/s,煤尘云爆炸下限浓度20g/m3,煤尘最低着火温度640℃,煤尘层最低着火温度290℃,岩粉用量55%;
15#煤层煤尘具有爆炸性,火焰长度20mm,15号煤煤尘云最大爆炸压力0.55MPa,最大压力上升速率30.09MPa/s,煤尘云爆炸下限浓度20g/m3,煤尘最低着火温度640℃,煤尘层最低着火温度290℃,岩粉用量50%。
(六)瓦斯含量
根据2012年瓦斯等级鉴定报告的批复,佳瑞煤业公司属高瓦斯矿井。
15101工作面15#煤层预抽前瓦斯含量9.8m3/t,预抽后瓦斯含量5.59m3/t,预抽后无明显瓦斯动力现象。
瓦斯压力0.3MPa以下。
三、3207工作面陷落柱超深孔爆破设计
(一)超深钻孔的钻凿与定位
超深钻孔高质量的钻凿和准确定位是实现超深孔爆破关键和基础,因此,正确认识超深钻孔的偏斜机理和影响偏斜的因素,然后针对性这些因素进行改进才是解决问题的正确方法。
1、超深钻孔产生偏斜原因分析
钻进过程中钻孔偏斜是主、客观因素共同作用的结果。
地质因素是钻进时的客观因素,技术和钻进工艺因素是钻进时的主观因素。
在不同的条件下,两类因素对钻孔偏斜的影响程度是不同的,有时地质因素是主导因素,有时技术和工艺因素是主导因素。
(1)地质因素
影响钻孔偏斜的地质因素主要是钻进岩体的产状、硬度、研磨性、密度、矿物成分、变质程度及结构构造等。
地质因素影响的基础是岩体的非均质性,它对钻孔方向及钻孔特征有着多种作用。
岩石的层理、裂隙、断层、软硬互层、溶洞、卵砾石等结构构造使岩层具有非均质性,造成钻头在孔底受力不均衡,形成倾倒力矩,引起钻孔偏斜,其中层理和软硬互层对钻孔的偏斜最具影响。
地质因素是客观因素,一旦选定地层和钻孔的开孔参数,专业技术人员一般不会去改变地质情况,而主要利用钻孔在地层中的偏斜规律合理地设计钻孔轨迹。
(2)技术因素
技术因素影响具体表现在以下几点:
1)在开孔钻进中,因钻孔方位、倾角校放的不是很准确。
造成钻机立轴与钻孔不在同一条中心线上造成钻孔的偏斜。
2)开孔时立轴内的钻杆过长,立轴筒磨损间隙较大,容易使立轴产生较大的摆动,直接影响钻头在孔底钻进时的稳定性。
3)使用了弯曲的接首、钻杆等,都会使钻具连接后不正,导致钻孔歪斜。
4)在扩孔钻进中,因孔内各处的硬度、孔径大小不一致,钻头可在钻孔内左右移动,靠向孔内一侧,使受压弯曲的钻杆挠度加大,钻头轴线与钻孔的轴线不重合,不能和钻进方向保持一致。
(3)钻进工艺参数
钻进工艺参数是指钻压、转速和钻井液等,钻进工艺参数的选取与所用钻进方法、地层情况、组合钻具所要达到的目的以及钻头的技术参数都有关系。
适当的调整钻进工艺参数决定着组合钻具能否很好地发挥作用。
例如钻压的大小直接决定钻具挠曲变形的大小,转速的大小决定回转产生离心力的大小,而离心力的大小决定挠曲变形和钻具自重对钻孔轨迹作用的程度。
所以为使组合钻具充分发挥调整钻孔轨迹的作用,应根据实际钻进情况,合理选用钻进工艺参数。
工艺因素影响具体表现在以下几点:
1)钻机、钻具的组合使用不当。
不能根据钻孔岩性和使用钻机的特点合理配置钻机和组合钻具。
2)钻进施工时,误操作或钻机加压过大,导致钻杆产生严重的弯曲。
3)在松散或较破碎的煤层或岩层中钻进,使用的冲洗液量过大,会较严重地破坏孔壁,造成孔内局部的塌孔,至使孔径无故扩大。
加压钻进时,钻杆有弯曲空间,钻孔易产生偏斜。
2、预防钻孔偏斜措施
从上述对钻孔偏斜的原因分析可知,为了保证钻孔质量,在钻孔施工过程中,贯彻“防斜为主,纠斜为辅;
一旦偏斜坚决纠”的原则,因此加强对钻孔弯曲的预防工作是十分必要的。
预防钻孔偏斜,要看准主要问题,根据实际经验,应从引起钻孔偏斜的三个基本因素的分析,及时抓好以下几条原则:
(1)正确开孔,保证开孔角度(方位角与倾角)符合设计要求;
(2)在保证顺利钻进的前提下,采取一切措施,尽量缩小孔壁间隙;
(3)粗径钻具长度适当,接起来不弯曲;
(4)根据岩层的具体情况和施工的特殊需要,适当减小钻进压力;
具体的实施方法,应当从以下几点出发:
(1)保征安装质量。
地基要修平、要坚固,支架要安平、安正,机器要装平、装正和装稳。
(2)开孔前准确的找好主轴。
可靠地把钻机基脚和主轴变角装置固定牢固。
(3)钻机的有关部件,磨损过大的要换新的。
(4)适当地加粗径钻具。
(5)根据岩层情况,适当地减轻钻进压力。
遇到开孔、换径、换层、扩孔、溶洞、裂隙等情况,更应当把压力控制在最低限度。
3、钻孔方案
(1)钻机型号
根据工作面情况和搬移方便,易于操作的要求,拟采用石家庄万达生产的ZYJ-270/170单腿液压回转钻机,该钻机配备的钻杆直径为42mm,钻头直径为75mm。
(2)钻孔深度
根据勘测资料在工作面处的揭露情况数据可知,断层岩层在当工作面眼12°
向前推进时,前方的岩石分布情况,如图1所示。
根据设计原则重点处理全岩区域以及岩多煤少区,因此确定爆破范围,长度上以支架42#到79#为界,宽度30米。
根据现有钻孔情况,确定最大孔深15米,分两阶段爆破。
因此其炮眼深度为9-15m即可,如图2所示。
(3)钻孔位置及孔间距
根据现场工作面地质勘探情况,结合采煤高度3.0m和以往模拟实验与现场爆破的经验,Φ63mm的药卷的爆破作用半径等因素,现场确定钻孔布置位置。
暂时拟取采高一半为布置钻孔的中位置,波动200mm处布孔,孔间距暂时取2.0m左右。
水平方向打眼拟采用的炮孔布置方案如图2所示。
图1工作面沿12°
推进时可能遭遇的岩石范围
标注单位m
图2超深孔爆破设计方案俯视及正视图
(二)装药量确定与装药工艺
1、装药壳体的设计
为了使超深孔爆破的装药更为顺利、更为方便,根据爆破模拟实验和柱状药包爆破破裂区范围,特设计了适用于煤矿的扩裂爆破壳体结构。
该壳体结构为PVC材质,其外径为63mm、内径60mm;
有效装药长度为1000mm,并且各壳体之间可以通过螺纹连接,有一定的连接力,其示意图如图3所示。
因此,采用这种壳体的装药结构,可以为装药和爆破带来如下好处:
(1)具有抵抗爆炸冲击波或爆炸应力波的压缩作用,减小炸药动压减敏作用;
(2)药包具有一定的刚度,使药包与炮孔之间更具有适应性,装药更为顺利和通畅;
(3)各药包之间可以紧密连接起来形成药柱,并且它们的连接均具有一定的强度,在装药时可以使整个药柱自由进出,可以避免装药还没有装到位而卡在孔中而没有办法处理的情况,有利于爆破安全。
图3装药壳体及其连接
2、装药量的确定
根据扩裂爆破的装药特点,即炮孔内采用连续装药结构,因此,装药量可以根据炮孔长度,计算出装药的药包个数,再乘以每个药包的药量即可。
根据上述装药壳体的设计,每个壳体大概能装药2.85-2.95kg左右。
因此,根据试验确定的炮孔长度计算试验爆破的总药量,但是,为了保证安全一次爆破总药量不大于200kg为好,爆破作业后观察爆破效果,评估现场作业安全情况。
拟用爆破参数如表1。
共50个炮孔,每孔需两发雷管,共消耗雷管100。
分9次起爆,最小单次准备药量80kg,最大单次准备药量160kg。
表1爆破参数表
炮眼编号
炮眼孔深(m)
装药长度(m)
填塞长度(m)
药量(kg)
爆破编号
雷管段位
准备药量(kg)
装药方式
联线方式
2
12.5
7
5.5
20.7
Ⅰ
1
156
(39包)
正向起爆
串联
3
15
9
6
26.6
4
5
8
Ⅱ
160
(40包)
10
11
12
13
14
Ⅲ
16
17
18
19
20
Ⅳ
21
22
23
24
25
26
Ⅴ
80
(20包)
27
28
续表1
装药
长度(m)
30
14.8
Ⅵ
124
(31包)
31
10.5
4.5
17.7
32
11.5
33
34
23.6
35
36
13.5
Ⅶ
144
(36包)
37
38
39
40
41
14.5
Ⅷ
42
43
44
45
46
47
48
Ⅸ
136
(34包)
49
50
51
52
合计
743.5
443
300
1267.6
1280
(320包)
3、装药工艺
超深孔扩裂爆破的装药是一个关键技术之一,装药好坏或顺利与否,关系到爆破效果的好坏和爆破的安全,因此,在进行装药时要按如下步骤进行。
(1)药包准备与加工
本次试验由于没有现成的药包,试验时必须现场进行加工,加工时先将药包壳体清理干净,再将直径35mm的水胶炸药药卷装入已准备好的壳体内,装入时还应边装边震动壳体,使炸药密实的装入壳体中,炸药装入高度达到最下刻线为止。
(2)探孔
在装药前,为避免炮孔的孔壁有不光滑的现象,先要进行探孔作业,即在装药器上装上与药卷直径稍大的导向头(本次试验时采用70mm)对全长炮孔进行探孔,探孔时如炮孔遇有不光滑的点需要反复推察,使探孔探头能顺利通过为准。
如果遇孔壁完整度差、装药安全存在风险的炮孔,应做好标记,报废该孔,不得继续装药作业,需重新施工。
(3)装药
装药时应有四人配合作业,孔口两人,一人抓住已装入的药包,另一个连接新药包,开始时可以两人用手直接将药包送入。
当药包加长到一定长度后,由于药包重量的增加,孔口的两人不能将药包送入孔中时,另外一人则用装药器辅助他们将药柱送入炮孔中,还有一人记录装入的药包个数。
当接入的药包全部连接好后,一次将所有药柱送入孔中。
(三)起爆系统设计
本次超深孔爆破所使用的炸药为水胶炸药,而水胶炸药在超深孔爆破时,由于先爆的炸药所产生的冲击波或爆炸应力波,对后起爆的炸药产生了动压作用,使后起爆的炸药出现减敏作用,直至爆轰熄灭。
因此,为了解决这个问题,在以往的超深孔爆破中,基本上都采用了导爆索起爆法,以增强超深孔炸药的起爆效果。
但是导爆索起爆法由于装药的不便利,使得装药时间很长,工作效率低,因此,使得超深孔爆破在生产单位很难形成实际的生产率,为了改变这种现状,本次在药卷壳体设计时就已经考虑了这种动压减敏的副作用,因此试验时就采用正向起爆即可。
起爆药包并联接入两个同段煤矿许用毫秒电雷管。
药包外的起爆线用1mm2爆破钢丝线接出,连接时要接紧、接牢,并用防水胶布密封接头,且要使起爆线进行短路连接。
当炮孔填塞好后,再将各起爆线串联接入起爆母线网路,起爆母线要达到300m长(达到远距离起爆的要求),并且中间无接头。
(四)填塞工艺
炮孔的填塞材料俗称炮泥,它的作用是保证炸药反应完全、充分,使其放出最大热量和减少有毒气体生成量,提高炸药的热效率,使炸药的化学能尽量多的转变成机械功。
同时在有瓦斯和煤尘爆炸危险的工作面,除了降低爆炸气体逸出自由面的温度和压力外,还起到阻止灼热固体颗粒从炮孔飞出,减少引燃瓦斯的机会。
在炮孔中不同位置的炮泥,爆破后的运动规律是不同的。
爆炸时炮眼内产生的压力不仅作用在孔壁上,也同时作用在炮泥上,但炮泥不是刚体,而是可压缩的材料,在爆轰压力作用下,靠近装药部分的炮泥开始时运动速度增加很快,基本上按线性增长,这时炮泥产生很大的塑性变形,使其密度不断增大,当密度增大到一定程度后,炮泥和孔壁之间的摩擦力和横向推力也增大,如果此时的摩擦力和抗剪强度大于爆生气体的推力,炮泥的运动速度相对要减小,甚至停止运动。
随着爆轰压力的继续升高,对炮泥的推力不断增大,炮泥中的剪应力也不断增大,直至克服炮泥与孔壁之间的摩擦力和炮泥的剪应力,使炮泥迅速向孔外滑动而抛出炮孔。
靠近孔口的炮泥刚开始时,由于惯性作用向外运动的速度很小,但当爆炸应力波传播到孔口后,从自由面产生反射拉伸作用,使孔口炮泥向外抛出;
同时炮孔内爆生气体对内层炮泥的作用不断增强,其运动速度也会越来越大,推动孔口炮泥产生向外运动的速度也增大,最终两者速度相等一起抛出炮孔。
超深孔爆破的填塞也是非常重要的,它不但关系到爆破效果的好坏也关系到爆破的安全。
因此,需要根据超深孔爆破的不同目的,对炮孔进行针对性的填塞。
为了达到本次试验的目的,填塞时需要注意如下几点:
1、填塞长度的确定
根据相关文献,避免冲孔的安全封孔长度计算公式为L≥nR/(2fλ),其中现场试验爆破孔半径R为37.5mm,侧压系数f为0.3,摩擦