毕业设计毕业论文液压活塞杆制造工艺设计Word下载.docx
《毕业设计毕业论文液压活塞杆制造工艺设计Word下载.docx》由会员分享,可在线阅读,更多相关《毕业设计毕业论文液压活塞杆制造工艺设计Word下载.docx(23页珍藏版)》请在冰豆网上搜索。
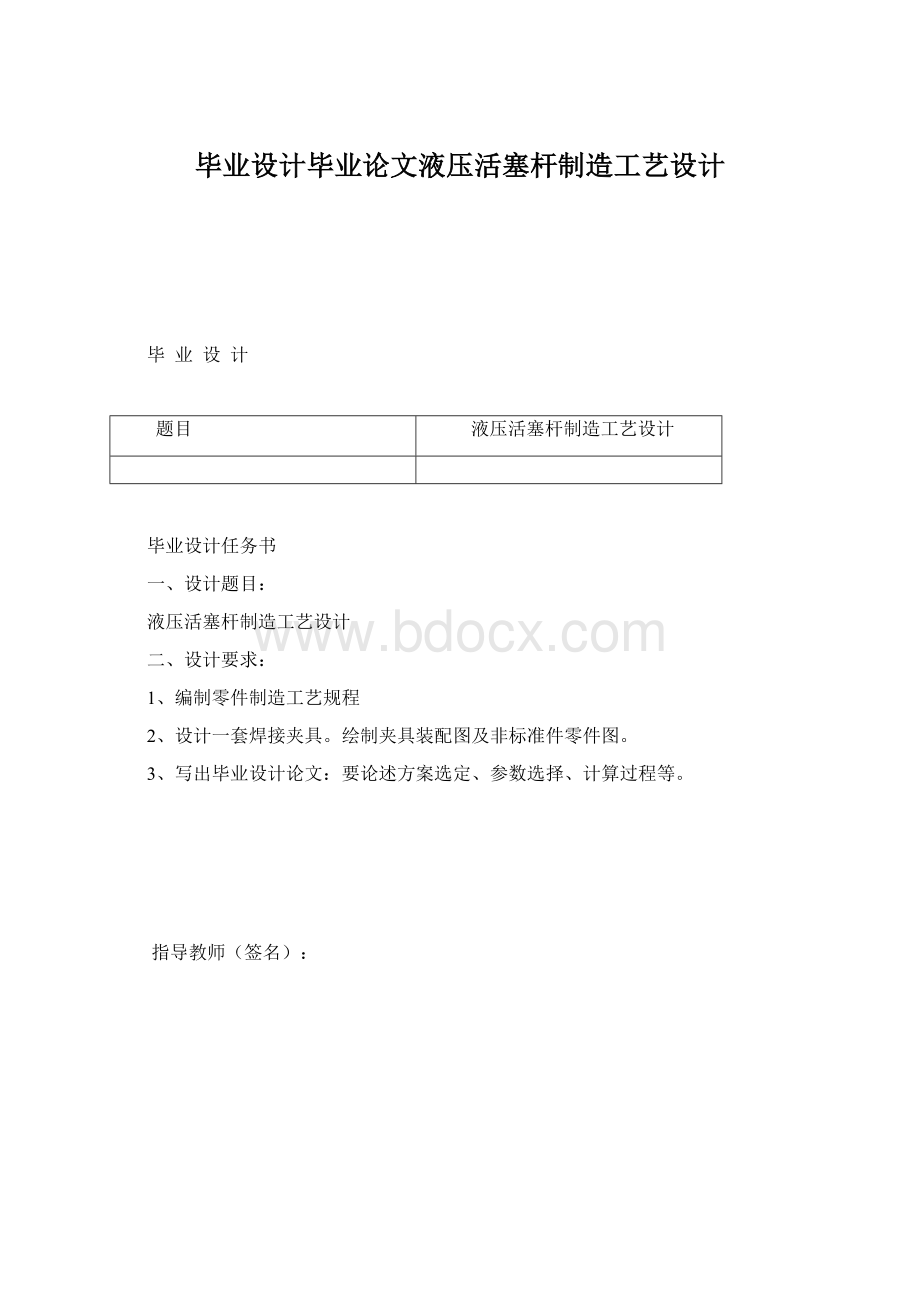
装配时用来确定零件或部件在机器上位置的表面。
本工件以ф90f8的外表面作为装配基准。
制订工艺路线的出发点,应当是使零件的几何形状、尺寸精度及位置精度等技术要求能得到合理的保证。
在生产纲领已确定为大批量生产的条件下,可以考虑采用万能性机床配以专用工夹具,并尽量使工序集中来提高生产率。
除此以外,还应当考虑经济效果,以便使生产成本尽量下降。
杆头的加工工序如下:
工序一:
选择外径为ф76mm,内径为ф44mm的标准钢管,在下料机上取150mm长。
工序二:
在CA6140x1500车床上车端面,保证总长为145
mm。
工序三:
检验。
杆体的加工工序如下:
工序一:
选择ф95的圆钢,在下料机上取1080mm长
工序二:
选用W200H落地式镗铣床铣工件一端面打中心孔A3,保证总长1076mm。
工序三:
在CA6140x1500车床上利用四爪单动卡盘,一夹一顶进行车削工件粗车小头尺寸留余量5~mm。
工序四:
在XD6132型万能立式升降台铣床上铣工件大端面的R38mm圆弧深为12mm,注意分中,在两侧倒角6x45°
。
活塞杆的加工工序如下:
钳工:
①将焊接件备齐,并清洗干净。
②用自制夹具按焊接图装配并点焊牢固。
焊接:
按图焊成。
在焊接过程中,焊接速度不应过快或过慢,应以
焊缝的外观与内在质量均达到要求为适宜。
要保证焊接后不
得有任何缺陷。
按图检验
热处理:
硬度为HB255~285
工序五:
在车床上精车ф90f8,ф50g8以及退刀槽等,并保证各个尺寸公差达到要求,同时保证各形位公差。
工序六:
铣杆头保证长度尺寸140
mm,并保证两边对称度在范内。
工序七、镗ф50
、ф51孔(找正活塞杆外圆),铣2X45°
,保证形位公差。
工序八、在外圆磨床MG1432A上磨外圆ф90mm成ф90
mm。
工序九、电镀ф90mm单边镀铬mm,并抛光,保证尺寸ф90f8
工序十:
磨外圆ф50g8适图纸要求。
工序十一:
按图检验
杆头的加工工序:
选择标准钢管外径为ф76mm、内径为ф44mm,在下料机上取150mm长。
确定毛坯长度尺寸:
取粗车加工余量为3mm
取精车加工余量为2mm
取精铣加工余量为2mm
所以,圆钢尺寸长度为:
140
+3+2+2=147
mm取为:
150mm
工序二:
在CA6140x1500车床上车端面,保证总长为145
选用45°
YT硬质合车刀车端面,依《金属机械加工工艺手册》可查得:
切削深度ap取2mm,进给量f取,切削速度V取151m/min,车床转速S取800r/mim。
检验利用精度为0.2的长度卡尺检验总长是否合格。
杆体的加工工序:
选择毛坯ф95圆钢,在下料机上取1080mm长。
1、确定毛坯的外圆尺寸:
各工序加工余量:
粗车精车
精磨:
0.03mm粗磨
总余量:
3mm
各工序工序尺寸:
粗车前:
精车前:
粗磨前:
精磨前:
取为95mm
2、确定毛坯长度尺寸:
取粗车µ
m端面加工余量为4mm
m端面加工余量为2mm
取精车µ
m端面加工余量为m
所以,毛坯尺寸长度Lm为1071+2.6+5.5≈1080mm
坯体积:
Vm=πd2xLm/4=πx922x1080x10-3
坯重量:
Gm=Vmxρ=7.85x10-3x7175.8=
3、选择下料方法和下料工具:
弓锯床下料:
切口宽度查表取为
切口损耗:
Gq=Lqπd2ρ/4=4.5XπX902X7.85X10-6
每个零件分摊的残料量:
Gc=10·
πd2/4n图二、在镗铣床上铣端面示意图
其中:
(n为每根棒料的切件数,Gc为残料长度)
零件材料消耗总耗:
N=Gc+Gq+Gc
选用万能卧式镗铣床铣工件一端面打中心孔A3并保证总长1076mm。
工步①:
水平放置工件,利用镗床夹具合理的定位工件,并找正工件中心,选用硬质合金端铣刀,铣单一端面。
可根据加工精度经济合理要求,选用机夹-焊接式中的外刃磨刀具。
它不仅刃磨方便,并且能保证径向跳动量和端面跳动量合格。
铣削速度V:
V=πd0n0/1000(m/s)(d0铣刀直径mm,n0铣刀转速r/s)
取d0=80mmn0=380r/s
所以,V=πd0n0/1000=πx80x380/1000=/s
进给量:
(可用进给速度Vf表示)
Vf=fxn0=afxzxn0(mm/min)
其中:
(af:
每齿进给量f:
每转进给量z:
铣刀刀齿数目)
取af=z=10mmn0=380r/s
所以:
Vf=0.25x10x380=950mm/min
工步②:
在铣过的端面打中心孔,镗床转速可取800~1600r/m。
在CA6140x1500车床上利用四爪单动卡盘,一夹一顶进行车削工件粗车小头尺寸留余量5~。
图三、在车床上粗加工ф55外圆示意图
依《金属机械加工工艺手册》中的“切削用量”章篇可知:
表1刀具选择
工件材料
刀具材料
主偏角Kr
副偏角Kr1
系数Cv
45号钢
YT12
90°
10°
3/3
表2硬质合金刀具
r(前)
a(后)
12°
~15°
粗8°
精12°
表3粗车外圆进给量
刀杆直径(mm)
工件直径(mm)
切削深度ap(mm)
进给量f(mm/r)
25X25
95
8
①切削速度Vc:
=πdn/1000=dn/318(m/s)
d为工件旋转直径(mm)n为工件或刀具转速(r/mim)
取n=280r/m可得Vc=dn/318=95X280/318≈83.64(m/s)
②进给量f:
f=0.5(mm/r)
③进给速度Vf:
Vf=nf=0.5X280=140mm/r
④切削时间(机动时间)tm(min)
tm=LA/(Vfap)(L为刀具行程长度mm,A为半径方向加工余量)
取A=20mm,L=123mm
因此,tm=123X20/(140X8)=2.2min
⑤材料切除率θ:
(mm3/min)
θ=1000apf·
Vc=1000X8X0.5X83.64=33456mm3/min
工序四:
在立式升降台铣床上铣工件大端面的R38mm圆弧,深为12mm,注意分中,在两侧倒角6x45°
图四、在铣床上铣工件R38圆弧的示意图
表4刀具选择
铣刀类型
主后角a
端面后角a1
偏角kr
过渡刃偏角kr1
过渡刃长度
d(铣刀)
高速钢
三面刃圆盘铣刀
20°
6°
1°
~2°
45°
1~2
75
表5铣削进给率
机床功率[kw]
工件、夹具系统刚度
每齿进给量fz(mm)
5~10
中等
~
找正工件轴向中心,在外表面画一条平行与轴线的直线,并用卡尺量取12mm,作为铣圆弧的终端位置。
依据选择计算的具体参数进行铣削粗加工。
留加工余1mm。
铣削速度:
V=πd0n0/1000(mm/min)
取n0=280r/min
V=πd0n0/min
进给速度Vf:
Vf=fxn0=afxzxn(mm/min)
取af=,z=14,n0=280,Vf=afxzxn=0.1x14x280=392(mm/min)
取被吃刀量ap:
3mm
工步③:
对工件图纸进行精加工,并保证圆弧铣为R38mm,深12mm分中。
表6参数选择
n0
V(mm/min)
Vf(mm/min)
ap
380
113
532
工步④:
在两侧倒角6X45°
注意:
在加工过程中需要加冷却液
活塞杆的加工工序:
①将杆头和杆体两个焊接件备齐,并清
洗干净
②用自制夹具按焊接图装配并点焊牢固
按左图焊成。
在焊接过程中,焊接速度不应过快
或过慢,应以焊缝的外观与内在质量均达到要求
为适宜。
要保证焊接后不得有任何缺陷。
图五、杆头和杆体焊接成形示意图
表7焊接厚度、焊条直径与焊接电流关系:
焊接厚度/mm
焊条直径/mm
焊接电流/A
>
13
5-6
260~300
按图检验:
用游标卡尺测量杆头的轴向中心相对杆头左、右两边是否对称。
用游标卡尺检验杆头的径向中心相对杆体大端面的距离是否保证了26mm,为车削工序是否能够保证总长1097mm作基础。
利用热处理达到技术要求(硬度为HB255~285):
考虑到本工件在实际应用以及后面工序的需要,必须有良好的综合力学性能。
选择调质方法来满足,强度较高,有良好的塑性及韧性,也便于切削加工,易得到较好的表面质量。
为了能达到这种要求,经过热处理冷却后得到的外圆尺寸为:
ф93mm;
总长为:
1074mm;
杆头长为:
142mm。
工序五:
利用四爪卡盘、顶尖,一夹一顶加工杆体中ф90f8外圆
选用90°
YT硬质合车刀车外圆,用45°
硬质合金车刀倒角6x45°
依《金属机械加工工艺手册》可查得:
切削深度ap取2mm,进给量f取,切削速度V取151m/min
则:
n主轴=1000Vc/(πd)=1000x151/(3.14x93)=517(r/min)
取n主轴=540r/min
利用上述参数,先把工件车成ф90
外圆达到技术要求
ap取1mm,f取0.2min/r,Vc取165m/min
换用45°
车刀完成6x45°
n主轴=1000Vc/(πd)=1000x165/(3.14x91)=577r/min
取n主轴=580r/min
利用四爪卡盘夹住杆头一端,用中心架支承工件ф95,并接
近小端ф55处,用45°
硬质合金车刀车端面,保证杆体总长
为1074mm。
依《机械加工工艺手册》可查得:
ap取2mm,f取/r,Vc取116mm
n主轴=1000Vc/(πd)=671.7r/min
取n主轴=640r/min
在依下面参数把工件车为1071mm
ap取1mm,f取/r,Vc取165m/min
n主轴=1000Vc/(πd)=955.4r/min
取n主轴=1000r/min
利用顶尖,四爪卡盘,一夹一顶车削杆体中ф50外圆选用90°
YT5硬质合金车刀车外圆,45°
车刀倒角3mm宽的切断刀切槽,半径为mm的圆弧切槽刀及螺纹刀。
先加工ф50g8外圆,保证长度120mm,可依以下参数切削:
n主轴=1000Vc/(πd)=671r/min,取n主轴=640r/min
f取/r,Vc取116m/min,ap取1mm
在加工2个
两个槽,换用切槽刀
可依如下参数切削:
f取/r,n主轴取380r/min
Vc=πdn/1000=πx50x380/1000=/min
一个槽切两次,切出槽宽为3mm,直径为ф46
mm,保证公差要求。
在用半径为mm的圆弧切槽刀,在以右端面为长度基准的57mm处切圆弧槽,直径保证为ф42mm。
然后加工右端ф45x2-6gmm外圆,并倒角2x45°
依下列参数加工:
f取/r,Vc取116m/min,ap取1mm
n主轴=1000Vc/(πd)=1000x116/(3.14x50)=738r/min,
取n主轴=750r/min
在加工最右端ф45外圆,并倒角2x45°
,依下列参数加工:
ap取2mm,f取/r,Vc取116m/min
n主轴=1000Vc/(πd)=820r/min,取n主轴=800r/min
最后加工M45x2-6g的三角形螺纹部分:
依《机械加工工艺手册》可查得加工如下参数:
此螺纹大径d=45mm,螺距为2mm细牙普通右旋螺纹,小径中径公差带,中等旋合长度皆为6g。
小径d1
中径d2=d-0.65t=45-0.65x2=
切削深度ap为:
螺距x0.65x2=2x0.65x2=
n主轴取90r/min
切削速度:
Vc/min
进给量:
f=0.5min/r
进给速度:
Vf=nf=90x0.5=45mm/min
以上步骤完成杆体右端部分全部加工。
调头上中心架找正外圆,在接头打中心孔,用中心架夹住工件右端ф90外圆,通过工件旋转,查看工件是否跳动,直到调好,找正为至。
保证形位公差,用中心钻在杆头中心打中心孔。
工序六:
铣杆头140
mm,并保证两边对称度在范围内。
利用自制的镗床夹具把工件按要求夹在夹具上,选用端面铣刀把工件铣成总长为140
mm,并使杆头两边对称相等,各端各铣。
可依以下参数加工:
n主轴取380r/min
进给量:
Vf=afxzxn0=0.25x10x380=950mm/min
其中:
af为每齿进给量z为铣刀刀齿数目图六、铣杆头长为40
的示意图
被吃刀量取各边铣削总数为1mm
切削速度V=πd0n0/1000=πx80x380/1000=/min
d0铣刀直径mm;
n0铣刀转速r/s
工序七:
镗ф50
孔(找正活塞杆外圆),镗ф51孔及铣2X45,保证形位公差。
将零件放在普通卧式镗床T68上,用两个V形架固定不让其横向移动,另外还需要用非标准夹具挡住另一端以保证其在镗削过程中零件纵向移动。
首先应注意的是镗刀必须与孔平行,如左图
毛坯孔为ф44,镗成ф50
mm,粗糙度为µ
m
经查表得需要:
粗镗半精镗即可达到图纸要求
其镗削用量如下:
图七、镗ф50
、ф51孔示意图
表8镗削用量
加工方式
刀具类型
V/(m/min)
f/(mm/r)
粗镗
硬质合金
刀头
40~60
半精镗
80~120
然后倒角,转动刀头,完成2x45°
完成之后,还要镗削ф51长40孔,因为从фф51之间所要镗削的量很小,因此,用半精镗就可以了,其镗削用量如上图可知。
倒角转动刀头,完成2x45°
此工序完毕可用内径百分表、万能角度尺等工具测量是否合格。
工序八:
磨外圆ф90成ф90
mm
选用高精度外圆磨床MG1432A进行磨削加工,选用PDAPA60#KV或PWA60#KV砂轮。
因为下一工序要镀铬,所以不需要精磨,直接粗磨。
其参数如下:
砂轮线速度35m/s,工件转速60~80r/min,横向进给量单程,工作台纵向进给速度0.5~1m/min。
为了提高耐磨性的防锈蚀目前国内传统工艺是表面镀耐磨性铬单边,恢复尺寸要研磨,为了保证表面粗糙度,研磨前要粗磨,再研磨,其粗磨参数上即可。
而其研磨参数如下
表9磨削参数
工艺参数
超精磨削
砂轮粒度
80#~320#
修整工具
单颗粒金刚石
砂轮线速度
17~20
修整砂轮时工作台进给速度(mm/min)
6~12
修整砂轮时横向进给量(mm)
修整时表面修出后横向进给次数(次/单程)
2~3
光修次数(次/单程)
1
工件线速度(m/min)
6~10
磨削时横向进给量
磨削时横向进给次数(次/单程)
光磨次数(次/双程)
4~6
磨削前工件余量
磨削时工作台进给速度(mm/min)
40~100
磨削前工件表面粗糙度(µ
m)
砂轮修整:
砂轮在磨削过程中,磨粒会逐渐磨钝而失去能力,从而使磨削质量下降,因此必须及时进行修整,以恢复原来的切削能力。
其砂轮修整用量的选择参数如上表。
磨削时要用磨削液为水溶性磨削液(69-1乳化液)
工序九:
电镀ф90单边镀铬mm,并抛光
此组焊件必须具有坚硬、耐磨、耐热、耐腐蚀及摩擦阻力低等特点,在正常情况下,如果全采用合金钢制造,然后经过热处理,可以达到上述要求。
但在目前,我国优质合金钢材缺乏加之也不实际,也不经济。
因此采用镀铬可以满足上述要求。
工序十:
磨外圆ф50g8适图纸要求:
磨削参数如下:
工序十一:
按图检验
可用千分游标卡尺,内径百分表以及螺纹检验卡片,万能角度尺等工具按图纸要求进行检验,保证合格产品上市。
3机械加工工艺过程卡片(见附录)
4焊接夹具设计
理由
活塞杆杆头和杆体在粗加工后,要将杆体和接头焊接到一起,再进行热处理,并进行最后的成型加工。
固本工件是大批量的生产,为了提高加工效率,并能保证加工精度。
因此,需设计制造专用焊接夹具来保证装配关系和焊接优势。
图八、焊接夹具示意图
1为挡板、2为支撑板、3为支撑挡板,6为M10X50的螺钉(起顶紧作用),4为4根ф10的圆钢用于连接挡板1、支撑板2、支撑挡板3。
活塞杆为轴类零件,一般都以中心轴线为基准来加工其外表面。
焊接夹具就是以活塞杆的轴线为基准而设计的。
将活塞杆ф90f8的部分放到支撑板2上,ф50g8的部分放于支撑挡板3上,并将ф90f8的端面顶住支撑支撑挡板板3的左端面,这样活塞杆就被固定了;
挡板1和支撑板2之间将放上活塞杆接头,然后定好位置,调节M10X50的螺钉,使其端面顶着杆头的外表面并加紧,这样就固定好了两焊件。
用电焊机进行点焊,使工件的位置固定。
点焊后,取下工件,按照技术要求进行焊接就可以了。
此焊接夹具结构简单,便于制造,经济实用,定位作用好。
使用时要注焊接夹具和地面的平行度。
1、定位基准的选取:
(1)ф90f8的右端面。
(2)活塞杆的中心轴线。
2、挡板、支撑板、支撑挡板、圆钢的作用:
(1)用支撑板2固定ф90f8部分。
(2)用支撑挡板3固定ф50g8的部分,支撑挡板3还可控制活塞杆的轴向移动。
(3)挡板1通过调节紧固螺钉来对调整好的杆头与杆体的位置进行固定。
(4)用四根ф10mm的圆钢来联结固定挡板、支撑板、支撑挡板,并保证其之间距离。
图九、焊接夹具中各零件之间距离确定示意图
图十、粗加工成的活塞杆杆头图样
图十一、粗加工成的活塞杆杆体图样
图十二、杆头、杆体组焊后的图样
1、长度方向的参数选取原则:
如图九所示,考虑到挡板的厚度为10mm,支撑板2和支撑挡板3之间的距离应控制在894mm,保证总长1050mm。
挡板1和支撑板2之间的实际距离(除挡板的厚度)为136mm,支撑板2和支撑挡板3之间的实际距离为874mm。
(1)支撑板2和支撑挡板3之间距离的选择
如图十一所示,粗加工后ф90f8的长度为956mm,圆弧深为12mm,为了方便焊接,就将挡板从圆弧方向向杆的右方向移动50mm,所以就得到了支撑板2和支撑挡板3的总长距离:
S=总长-圆弧深-12-50=956-12-50=894mm
(因考虑到板的厚度为10mm,所以支撑板2和支撑挡板3的之间距离为874mm)
(2)总长的确定:
如图十二所示,