铁路货车轮轴无损检测技术.ppt
《铁路货车轮轴无损检测技术.ppt》由会员分享,可在线阅读,更多相关《铁路货车轮轴无损检测技术.ppt(171页珍藏版)》请在冰豆网上搜索。
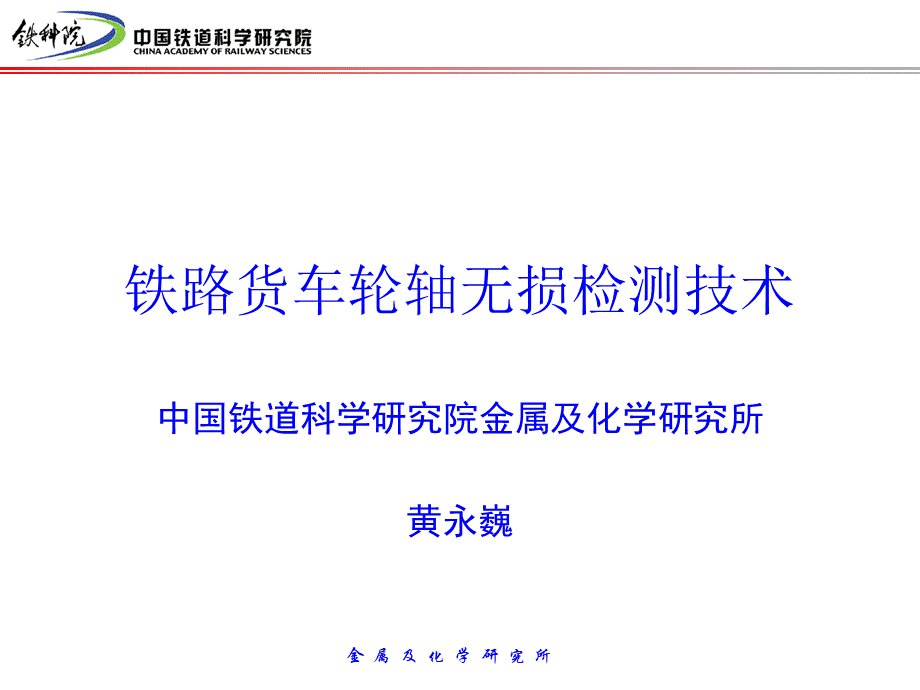
铁路货车轮轴无损检测技术,中国铁道科学研究院金属及化学研究所黄永巍,目录,第一章无损检测技术简介1无损检测含义2超声波探伤3磁粉探伤第二章轮对超声波探伤1新制车轮超声波探伤2检修车轮超声波探伤3镶入部探伤,目录,第三章轮对磁粉探伤1新制车轮磁粉探伤2检修车轮磁粉探伤第四章轴承探伤1轴承磁粉探伤2轴承超声波探伤,目录,第五章新技术1超声相控阵2TOFD3导波第六章新工艺1荧光磁粉探伤时高强度紫外线灯的应用2轮对卸荷槽裂纹的检测3列车车轮在线检测4空心货车车轴,第一章无损检测技术简介,无损检测是在不破坏被检测对象的物理化学性能和几何完整性的情况下,对其物理性能、参数、状态和内部结构等进行检测和测量,从而判定其是否合格。
无损检测技术是一门新兴的应用学科。
从本世纪20年代后期起步,40年代得到较快发展。
1941年,美国无损检测学会(ASNT)成立,1943年创刊会刊“材料评价”,标志这一技术逐步走向成熟。
1955年,第一届世界无损检测会议召开,则标志着这门学科在世界范围内的建立。
现代工业是建立在无损检测基础之上的。
据资料统计,在发达工业国家中,无损检测占一般工业产品生产总工时的13%,电机产品占13%,国防工业产品占1218%,火箭发动机等高新技术产品高达20%以上。
所以工业发达国家都凭借其雄厚的经济实力和技术基础,大力发展无损检测技术,在基础理论、实际应用、检测设备和检测新技术的开发方面都处于世界领先水平。
国内无损检测技术现状,1978年11月在上海成立了中国机械工程学会无损检测分会,同时召开了第一届学术交流会。
从那时起国内无损检测技术得到了蓬勃的发展。
目前国内已有17所学校先后设立了无损检测专业课程,培养出了无损检测专业本科生、专科生、硕士研究生、博士研究生和专业证书班学生,一些中专和技工学校也先后培养了一批无损检测专业生。
至今,全国已培训、鉴定了12万名NDT人员,并颁发了各种方法、各个等级的资格证书。
1990和1991年学会又先后与德国NDT学会签订了UT、RT、MT、PT四种方法的证书互认协议,为我国NDT人员论证制度与国际接轨打开了渠道。
在国内,铁道部是较早开展无损检测工作的部门。
由于历史的原因,机车车辆的制造、修理都是在工厂系统进行的,因此机车车辆工业无损检测技术实际上代表了铁道部的无损检测技术水平。
早在解放前夕,铁路工厂中就有磁粉探伤,但设备简陋,仅为马蹄形磁轭探伤器,人员少,技术差。
解放后,从开始时的简单手工磁轭探伤到90年代高精尖的自动化探伤设备,从50年代单一的磁粉探伤到90年代多种探伤方法的应用,铁路部门无损检测技术得到了极大的发展。
纵观50年发展史,可以分为两个阶段。
国内无损检测技术现状,解放初至70年代末在此期间,各种无损检测技术相继得到应用,各工厂都开展了无损检测工作,相互之间相对独立,但常进行技术交流。
1950年,铁道部引进前苏联产的电磁探伤仪进行磁粉探伤。
当时的磁粉都是干法探伤用磁粉,颗粒较大,适用于粗糙表面的质量检查或检查比较大的表面缺陷。
例如连杆等的表面疲劳裂纹检查。
随着铁路运输的飞速发展,对机车车辆配件的性能要求越来越高,车轴轴颈的表面光洁度很高,干法磁粉探伤不能满足要求。
此时发展了湿法磁粉探伤。
湿法探伤用的磁粉很细,能有效地探出轴颈表面的细小磨削裂纹。
国内无损检测技术现状,1950年,铁道部采用了超声波探伤技术。
最早使用穿透式超声波探伤。
这种探伤方法设备简单,结果易于说明,但由于缺陷的可探出性随缺陷面积与超声波束面积之比、缺陷相对于波束的取向及缺陷与超声源之间距离的不同而异,且工件几何形状的微小改变又会引起接收信号幅值的变化,所以穿透法探伤使用范围不广,很快被脉冲反射式超声波探伤技术所替代。
铁道部于1958年从前苏联引进了十套钴60射线源,分给有关机车制造工厂使用,进行蒸汽机车锅炉焊缝射线透照。
这是铁道部射线探伤的开端。
放射性源透照的特点就是可把射线源放置在容器中心,一次就可完成全表面透照,但时间长,底片清晰度不高。
所以在1959年又从苏联引进了X射线探伤机,用X射线探伤,拍出的射线照片清晰度好,成为蒸汽机车锅炉焊缝的主要无损检测手段。
国内无损检测技术现状,60年代铁道部开始采用渗透探伤,最早为着色探伤法。
着色探伤法所用的渗透剂一般为红色液体,在白光下显示鲜艳的红色,灵敏度较高。
为了进一步提高探伤灵敏度,又出现了荧光探伤法,渗透液中掺有荧光物质,在紫外线照射下可发出明亮的黄绿色光。
渗透探伤在铁道部主要用于检测气阀、涡轮叶片等。
1976年,部分机车厂及机务系统采用点式涡流探伤仪探测气阀表面。
由于受交流电趋肤效应的影响,涡流探伤仅能够探出工件表面下面1个毫米深度的缺陷,而渗透探伤只能探出表面开口型的缺陷。
国内无损检测技术现状,1953年10月12日第82期铁道公报公布了铁机电郭(53)字第185号铁道部令公布机务段车辆段及机车车辆修理工厂机车车辆重要配件电磁探伤细则,规定了车轴、车钩、曲拐销等十四种配件的探伤方法。
这是铁道部第一个无损检测规范。
这个无损检测规范的颁布实施,对铁道部无损检测工作产生了深远的影响,无损检测工作从此走上了标准化管理的道路。
1958年,铁道部在总结锅炉焊缝探伤的经验上又颁布了锅炉焊缝射线探伤细则。
从1973年起,铁道部工业总局开始进行无损检测人员技术交流,1977年,举办了两期超声波探伤培训班。
培训的学员在后来的工作中都成了技术骨干,发挥了重要作用。
1979年,第一届铁路无损检测年会在成都召开。
与会代表交流了车轴、曲轴、气阀等机车车辆配件的无损检测技术,讨论了铁路无损检测工作的发展。
从此,铁路无损检测工作进入了一个崭新的阶段。
常规无损探伤方法的能力和适用范围,常规无损检测方法分五类:
超声、磁粉、射线、渗透和涡流。
每种无损探伤方法均有其优点和局限性,各种方法对缺陷的检出机率既不会是100%,也不会完全相同,例如超声探伤和射线照相探伤法,对同一被检物的探伤结果不会完全一致。
1超声探伤,11适用对象和能力111锻件:
超声探伤能发现锻件中与超声波束基本垂直的裂纹、白点、分层大片或密集的夹渣等缺陷。
通常用直射法探测内部缺陷,其最大有效探测深度可达1m左右。
用斜射法和表面波法进行探伤,可探测与表面不平行的缺陷或表面缺陷。
超声探伤能测定缺陷位置和相对尺寸,缺陷的种类一般较难判定。
注:
用不同方法测定的相对尺寸的概念是不同的,其大小也不能相比。
112焊缝:
包括熔焊的对接焊缝我角焊缝。
超声探伤能发现焊缝中的裂纹、未焊透、未熔合、夹渣和气孔等缺陷。
通常采用斜射法,用2.5MHz时最大有效探测深度约为200mm。
超声探伤能测定缺陷位置和相对尺寸,但较难判定缺陷的种类。
113型材:
包括金属板材、管材、棒材及其他型。
超声探伤能发现材料内部及表面的裂纹、折叠、分层、片状夹渣等缺陷。
一般用液浸法或局部水浸法进行探伤,对管、棒等材料通常需用聚焦斜射法探伤。
能测定缺陷位置和相对尺寸,较难判定缺陷的种类。
114铸件:
形状简单、表面平整或经过加工修整的铸钢件球墨铁件,可采用超声方法探伤。
能发现热裂、冷裂、疏松、夹渣、缩孔等缺陷。
能测定缺陷的位置和相对尺寸,但较难判定缺陷的种类。
1超声探伤,12不适用对象粗晶材料:
如奥氏体钢的锻件和焊缝。
形状复杂或表面粗糙的工作。
2射线照相探伤,21适用对象和探伤能力211焊缝:
能发现焊缝中的未焊透、气孔、夹渣等缺陷。
对于裂纹和未熔合,由于其缝隙宽度极窄,且射线照射方向不易与裂纹和未熔合的方向一致,故射线法较难发现焊缝中的裂纹和未熔合。
射线探伤的穿透深度,主要由射线能量决定。
400KVX射线透照钢铁的厚度可达85mm左右,钴60Y射线的透照厚度可达200mm左右,9Mev的直线加速器的透照厚度可达85mm左右。
射线照相法一般能确定缺陷平面投影的位置和大小以及缺陷的种类。
212铸件:
能发现铸件中的缩孔、夹渣、疏松、热裂等缺陷。
一般能确定缺陷平面投影的位置和大小,以及缺陷的种类。
2射线照相探伤,22不适用对象锻件型材,3磁粉探伤,31适用对象铁磁性材料和工件,包括锻件、焊缝、型材、铸件等,能发现表面和近表面的裂纹、折叠、夹层夹杂、气孔等缺陷。
一般能确定缺陷的位置、大小、和形状但难以确定缺陷的深度。
32不适用对象非铁磁性材料,如奥氏体钢、铜、铝等。
4渗透探伤(包括着色探伤和荧光探伤),41适用对象金属材料和致密性非金属材料。
能发现表面开口的裂纹、折叠、疏松、针孔等缺陷。
通常能确定缺陷的位置、大小和形状,但难以确定缺陷的深度。
42不适用对象疏松的多孔性材料,4渗透探伤(包括着色探伤和荧光探伤),41适用对象金属材料和致密性非金属材料。
能发现表面开口的裂纹、折叠、疏松、针孔等缺陷。
通常能确定缺陷的位置、大小和形状,但难以确定缺陷的深度。
42不适用对象疏松的多孔性材料,5电磁(涡流)探伤,51适用对象导电材料,如铁磁性和非铁磁性的型材和零件=石墨制品等。
能发现裂纹、折叠、凹坑、夹杂、疏松等表面和近表面缺陷。
通常能确定缺陷的位置和相对尺寸,但难以判定缺陷的种类。
52不适用对象非导电材料,第二章轮对(车轮)超声波探伤,1新制车轮超声波探伤1.1新制车轮应进行超声波探伤的主要有以下2种缺陷型式,1新制车轮超声波探伤,
(1)较大颗粒的非金属夹杂物,属于冶金制造缺陷该种缺陷通常位于踏面下1015mm处,在轮轨作用力下形成疲劳裂纹,即车轮内部疲劳裂纹及掉块,简称“辋裂”。
如不及时发现,在列车运行时发生轮辋掉块,很可能造成切轴事故。
图1发展到轮辋内侧面轮辋疲劳裂纹形貌,1新制车轮超声波探伤,
(2)严重异型偏析、疏松、内裂、白点等车轮钢存在严重异型偏析、疏松、内裂、白点等不允许有的冶金缺陷,可使车轮沿径向裂开或整体崩裂成数块,在列车运行中有可能造成列车颠覆事故。
图2车轮低倍试片上内部裂纹及异形偏析,1新制车轮超声波探伤,图3车轮崩裂后剩余部分形貌,1.2探伤原理车轮质量直接影响着车轮使用安全和可靠性,对车轮内部缺陷进行检测,是确保车轮质量和运行安全的重要技术措施。
新制车轮探伤主要探测部位是轮辋,探伤灵敏度为2mm当量平底孔缺陷。
探伤原理图如图4所示。
(a)轮辋踏面扫查(b)轮辋内侧面扫查图4RWI超声探伤系统原理,1.3探伤设备目前新制车轮的探伤尚未全部开展,已经开展的车轮生产企业所用的新制车轮超声探伤设备主要是国外的。
图5所示为太原智奇公司新制车轮超声波探伤设备。
图5智奇公司新制车轮超声探伤设备,该超声探伤系统由意大利生产,主要技术参数如下:
检测车轮直径:
600mm1300mm;检测灵敏度:
最高可达1mm平底孔;显示方式:
A、B、C型;检测速度:
1分钟/车轮(不包括辐板)检测部位:
轮辋;放大器带宽:
0.520MHz;最大重复频率:
40kHz;探伤盲区:
10mm,1.3探伤设备大同ABC轮厂采用的是美国GE检测科技公司的UTXX车轮超声探伤系统,该系统采用相控阵技术,对车轮轮辋部分进行检测,如图6所示。
该系统还在我国太重车轮厂得到应用。
图6GE公司车轮超声探伤系统,其主要技术参数如下:
标准配置的晶片数:
256个;同时激发一组最大晶片数:
32个;最大可以激发序列数:
256个;每个晶片延时:
02.5s/2.5ns;初始激发晶片:
可编程;组晶片数:
可编程;脉冲发生器电压:
65伏、50欧、负脉冲;放大器带宽:
0.02512MHz;最大脉冲重复频率:
20KHz前置放大器增益:
10dB/0.1dB步长;数字分辨力:
50MHz。
2检修车轮超声波探伤,2.1检修车轮缺陷与新制车轮缺陷的区别车轮运行一段时间后,轮辋内部缺陷会扩展形成辋裂,严重危害行车安全。
若不能及时发现,很可能在车辆运行中发生轮辋部分的开裂和脱落,造成行车重大事故。
因此,在轮对解体检修时需要对轮辋内部进行超声波探伤。
检修车轮所需探伤的缺陷应该是扩展后的“大”缺陷。
大的程度?
2.2探伤设备2.2.1国