发动机曲轴加工工艺及夹具设计文档格式.docx
《发动机曲轴加工工艺及夹具设计文档格式.docx》由会员分享,可在线阅读,更多相关《发动机曲轴加工工艺及夹具设计文档格式.docx(20页珍藏版)》请在冰豆网上搜索。
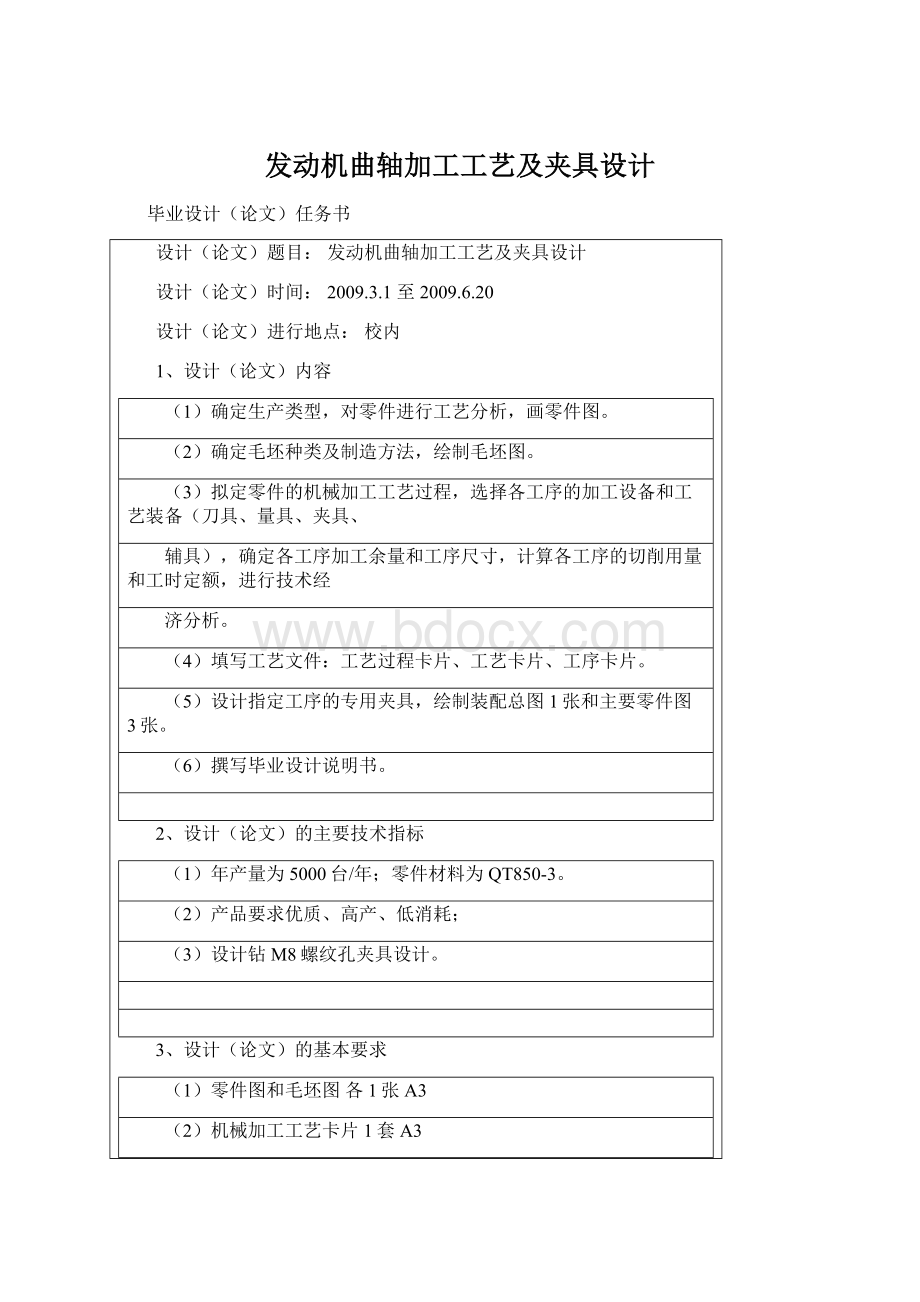
[4]杨宝田.4D型柴油机曲轴加工工艺设计[D].天津大学,2004
[5]李月琴,曾令宜,弓申.拨叉、拨叉体类零件钻径向孔成组夹具设计[J].工具技术,2005,39(8):
74-76
[6]杨黎明,黄凯,李恩至,陈仕贤.机械零件设计手册[M].北京:
国防工业出版社,1986.
5、各阶段任务及时间安排
序号
设计(论文)各阶段任务
时间安排
1
翻译;
明确设计要求,查阅文献,收集有关资料
3月1日~3月28日
2
零件的结构分析,零件的技术要求分析
3月29日~4月2日
3
工艺规程方案选择设计
4月3日~4月10日
4
填写工艺文件
4月11日~4月15日
5
夹具结构方案的设计
4月16日~4月28日
6
夹具精度的校核
4月29日~5月3日
7
夹具总图设计,绘制夹具零件图
5月4日~5月25日
8
编写设计说明书
5月25日~6月10日
9
修改设计;
毕业设计答辩
6月11日~6月20日
学生签名:
指导教师签名:
系主任签名:
2009年3月1日
毕业设计要求:
(零件图:
TH16-43/23机械制造技术基础课程设计指南P275图6-11)
1.图书馆网站上查阅相关中文文献10篇以上。
关键词有:
曲轴、加工工艺、工艺规程、制造工艺、夹具。
2.翻译规定的译文1篇。
用计算机输出。
格式按毕业论文的格式设置。
最后与说明书一起到印刷厂打印。
3.查找相关英文文献2篇。
到图书馆四楼外文期刊阅览室查找或图书馆网站下载。
4.阅读工艺设计和夹具设计等相关书籍,掌握制订工艺文件的步骤和方法。
掌握夹具设计的步骤。
5.绘制零件图(计算机绘图A3)。
6.进行曲轴的工艺分析(用途、技术要求及工艺性等)及生产类型的确定。
7.选择毛坯,计算毛坯尺寸公差和机械加工余量。
确定毛坯图,绘制毛坯零件图。
(计算机绘图A3)。
8.确定曲轴工艺路线。
定位基准的选择,表面加工方法的确定,加工阶段的划分,工序集中和工序分散的安排,工序顺序的安排,工艺路线的安排。
绘制工艺路线粗表(工序号,工序名称,机床设备,刀具,量具)。
9.机床设备和工艺装备的选用。
10.各加工工序的加工余量、工序尺寸和公差的确定。
(详细的计算过程)
11.各加工工序的切削用量、时间定额的计算。
12.绘制机械加工工艺过程卡片1张;
机械加工工序卡片全套。
13.分析零件图和工序图,了解零件的功用、特点、材料、生产类型及技术要求,详细分析工件加工工艺过程和本工序加工要求,如工序尺寸、工序基准、加工余量、定位基准和夹紧部位等。
14.了解本工使用的机床和刀具。
了解机床的规格、主要参数以及在机床上安装夹具的部位的结构和配合尺寸。
了解本工序使用的刀具类型、主要结构尺寸等情况。
15.熟悉夹具设计用的国家标准、行业标准和企业标准。
查阅夹具设计手册和夹具设计指导资料等。
16.了解夹具典型结构。
在着手设计之前,应多参阅一些典型夹具结构图册及夹具部件的典型结构,以增加对夹具结构的认识。
17.确定夹具的结构方案。
确定工件的定位方案;
确定刀具的对刀或引导方式;
确定工件的夹紧方案;
确定夹具其他组成部分的结构形式;
确定夹具体的形式和夹具的总体结构。
18.绘制夹具的装配草图和装配图。
按1:
1绘制。
夹具装配图可按如下顺序进行:
1)把工件视为透明体,用双点画线画出工件的轮廓、定位面、夹紧面和加工表面;
、
2)画出定位元件和导向元件;
3)按夹紧状态画出夹紧装置;
4)画出其他元件或机构;
5)最后画出夹具体,把上述各组成部分联结成一体,形成完整的夹具;
6)标注必要的尺寸、配合和技术条件;
7)对零件编号,填写标题栏和零件明细表。
19.绘制夹具零件图。
对装配图中非标准零件均应绘制零件图,视图尽可能与装配图上的位置一致,尺寸、形状、位置、配合以及加工表面粗糙度等要标注完整。
零件图的编号与装配图的编号一致。
20.编写毕业设计说明书。
说明书必须包括以上所有内容,内容布置必须合理。
格式安排毕业设计说明书格式执行。
每一章必须单独起页。
用Word
输出。
说明书包括:
中文摘要、英文摘要、目录、正文、总结、参考文献、谢辞。
21.英文翻译、论文中英文摘要必须自己翻译,不准用电脑如金山快译等直接翻译句子。
22.需要借的书籍:
TG75-43/1机床夹具设计与制造
TH16-43/23机械制造技术基础课程设计指南
TH16-42机械制造工艺与装备习题集和课程设计指导书
TG5-62/6:
4金属机械加工工艺人员手册
TG75-62-1机床夹具设计手册
TG75-431机床夹具设计与制造
张宏宝;
1.8T曲轴加工工艺的改造[J];
汽车与配件;
2005年51期;
36-37
古连文,邹冕,周克勤;
柴油机曲轴现场加工[J];
中国修船;
2006年02期;
34-35
邓根清;
主动轴机械加工工艺及改进[J];
机械设计与制造;
2005年06期;
92-93
周德生;
曲轴加工新技术[J];
机械工人.冷加工;
2004年05期;
21-25
制造工艺manufacturingprocess
一.零件的工艺分析及生产类型的确定
1.零件的作用
题目所给的零件是CA6140车床的杠杆。
它位于车床制动机构中,主要起制动作用。
杠杆一端与制动带连接,另一端通过刚球与齿条轴的凸起(或凹槽)相接触,当离合器脱开时,齿条轴与杠杆下端接触,是起逆时针方向摆动,将制动带拉紧;
当左右离合器中任一个接合时,杠杆都顺时针方向摆动,使制动带放松,从而达到制动的目的。
2.零件的工艺分析
所加工零件立体图,零件图如下图所视
从零件图上可以看出,主要加工表面可以分为四个部分。
1.
Ф25mm的圆柱内表面,加工时要保证Ф25+00.023的0.023公差要求,以及表面粗糙度Ra1.6,表面要求较高。
2.
连杆的支撑底板底面,粗糙度要求Ra3.2,同时保证连杆的高度30mm。
3.
连杆上端面及下端侧面;
上端面40×
30mm,粗糙度要求Ra3.2,同时保证与Ф25mm的圆柱轴线的距离90mm;
下端侧面保证尺寸17mm,粗糙度要求Ra6.3;
离Ф25mm的圆柱轴线45mm的侧面粗糙度要求Ra12.5。
4.
钻孔及攻螺纹孔;
上端面2×
M6,保证尺寸10mm、20mm,沉头锥角120°
,粗糙度要求Ra6.3;
M8的螺纹孔,锪Ф14×
3mm的圆柱孔,粗糙度Ra3.2;
钻下端Ф12.7+00.1的锥孔,保证公差要求,以及中心线与Ф25mm的圆柱轴线的距离60mm粗糙度要求Ra6.3。
根据各加工方法的经济精度及一般机床所能达到的位置精度,该零件没有很难加工的表面,上述各表面的技术要求采用常规加工工艺均可以保证。
3.零件的生产类型
依设计题目知:
Q=5000台/年,n=1件/台,结合生产实际,备产率α和废品率β分别取为10%和1%。
带入公式得该零件的生产纲领N=5000×
1×
(1+10%)×
(1+1%)=5555件/年
零件是机床的杠杆,质量为0.85kg,查表2-1可知其属轻型零件,生产类型为大批生产。
二.选择毛坯,确定毛坯尺寸,设计毛坯图
1.选择毛坯
该零件材料为HT200,考虑到零件的结构以及材料,选择毛坯为铸件,由于零件年产量为5555件,属于批量生产,而且零件的轮廓尺寸不大,故采用砂型机器铸造。
这从提高生产率,保证加工精度以及节省材料上考虑,是合理的。
2.确定机械加工余量,毛坯尺寸和公差
参见本书第五章第一节,灰铸铁的公差按表-和表5-4确定。
要确定毛坯的尺寸公差及机械加工余量,应先确定如下各项因素。
(1)
铸件机械加工余量等级 该值由铸件的成型方法和材料确定,成型方法为砂型机器铸造,材料为灰口铸铁,确定加工余量等级为G。
(2)
铸件尺寸公差 毛坯铸件的基本尺寸处于100~160之间,而铸件的尺寸公差等级为8~10,取为8级,根据表2.2-1取铸件的尺寸公差为1.8mm。
3.确定机械加工余量
根据表2.25查得的毛坯的加工余量等级为G,以及铸件的尺寸,根据表2.2-4定铸件的机械加工余量为2.5mm。
4.确定毛坯尺寸
根据成型零件的基本尺寸,以及确定的机械加工余量和铸件的尺寸公差确定毛坯的尺寸为基本尺寸加上机械加工余量,即基本尺寸加上2.5mm。
5.确定毛坯尺寸公差
根据表2.2-1毛坯的尺寸公差等级为8级,确定尺寸公差为1.8mm。
6.设计毛坯图
毛坯图如下图所视。
注:
图中尺寸小数点后的4应该为5,即92.5,10.5,17.5,32.5
三.选择加工方法,制定工艺路线
1.定位基准的选择
本零件是带孔的杆状零件,孔是其设计基准,在铣削零件的三个平面以及钻孔的时侯,都应以孔为定位基准,避免基准不重合误差的产生,在铣削底面时应该以不需要加工的面为粗定位基准。
2.零件表面加工方法的选择
本零件的加工面有端面,内孔,螺纹孔,其中端面有一个大底面和二个小端面,内孔有φ25mm和φ12.7mm各一个孔,螺纹孔有M6和M8各一个。
材料为灰铸铁。
以公差等级和表面粗糙度要求,参考本指南有关资料,其加工方法选择如下。
(1)
大底面据表面粗糙度3.2,考虑加工余量的安排,根据表5-16选用先粗铣后半精铣的方法加工。
(2)
25mm的孔根据表面粗糙度,选公差等级为IT8,根据表5-15选用先钻后扩再粗铰再精铰的加工方法。
(3)
端面一据表面粗糙度6.3,根据表5-16采用铣削的加工方法,铣一刀。
(4)
12.7mm的孔根据表5-15选用钻削的加工方法。
(5)
端面二根据表面粗糙度3.2,根据表5-16选用先粗铣后半精铣的加工方法。
(6)
M6螺纹孔根据螺纹的加工方法,选用先钻后倒角再攻丝的加工方法。
(7)
M8螺纹孔根据螺纹的加工方法,选用先钻后倒角再攻丝的加工方法。
3.制定工艺路线
根据该零件的结构以及需要选用的定位基准,按照先加工基准面,以及先粗后精的的原则,该零件应先加工大底面,再钻孔,再加工其他表面的方法,具体工艺路线如下:
工序Ⅰ:
以不需要加工的底面为粗基准,铣削另一个底面;
以铣削过的底面和一个支撑为定位,粗、精铣端面一,保证长度30mm的尺寸和粗糙度为3.2。
工序Ⅱ:
以铣削过的底面和直径45的外圆表面定位,钻、扩、铰直径25的孔。
工序Ⅲ:
以铣削过的底面和钻削后的孔和一个支撑为定位,铣削直径为12.7孔的端面二。
工序Ⅳ:
以铣削过的底面和钻削后的孔和一个支撑为定位,粗、精铣2-M6端面三,保证长度90mm的尺寸和粗糙度3.2。
工序Ⅴ:
以铣削过的底面和钻削后的孔和一个支撑为定位,钻、锪、攻M8的螺纹孔。
工序Ⅵ:
以铣削过的底面和钻削后的孔和一个支撑为定位,钻、攻M6的螺纹孔。
工序Ⅶ:
以铣削过的底面和钻削后的孔和一个支撑为定位,钻、扩直径12.7的孔。
四.工序设计(工序40,50,80)。
1.选择加工设备与工艺装备
(1).选择机床
根据不同的工序选择机床。
a)
工序40是粗铣。
工序的工步数不多,成批生产不要求很高的生产率,故选用立式铣床。
根据零件外廓尺寸,精度要求,选用功率为4.5KW的X51式立式铣床即能满足要求。
b)
工序50是钻、扩孔,80是钻孔、锪孔、攻螺纹。
由于加工面位置分散,表面粗糙度数值要求不同,因而选择Z535钻床。
(2).选择夹具
本零件结构不规则,不易进行装夹、定位,故工序40,50,80均选择专用夹具。
(3).选择刀具
根据不同的工序选择刀具。
工序40铣端面一、二时,在立式铣床上加工,所以选择端铣刀。
按表3.1-27和3.1-37查得,选用镶齿套式面铣刀根据零件加工尺寸,所选铣刀直径d=100mm,齿数Z=10。
材料选择硬质合金钢。
工序50钻孔d=12.7mm时,选择锥柄麻花钻头d=12mm,长度l=182mm,齿数Z=3。
材料选择高速钢,1号莫氏圆锥。
c)
工序50钻底孔2-M6时,选择锥柄麻花钻头d=4.9mm,长度l=52mm,齿数Z=3。
d)
工序50扩孔d=12.7+0.10mm时,选择锥柄扩孔钻的d=12.7mm,长度l=101mm,齿数Z=3。
材料选择高速钢。
e)
工序80钻M8底孔时,选择直柄麻花钻头d=6.8mm,长度l=101mm,齿数Z=3。
f)
工序80锪孔时,选择带导柱直柄平底锪钻。
直径d=14mm,d1=6.6mm,长度L=150mm。
g)
工序80攻螺纹M8时,根据螺纹公称直径选择M8丝锥,直径d=8mm,长度L=72mm,螺距P=1.25。
h)
工序80攻螺纹M6时,根据螺纹公称直径选择M6丝锥,直径d=6mm,长度L=66mm,螺距P=1。
i)
工序80钻120度的倒时,选择直柄锥面锪钻,直径d=16mm,d1=10mm,d2=3.2mm,长度l=20mm,齿数Z=6。
(4).选择量具
本零件属成批生产,一般情况下尽量采用通用量具。
根据零件表面的精度要求、尺寸和形状特点,参考有关资料,选择如下。
选择加工平面所用量具。
铣端面,选择读数值0.02,测量范围0~150游标卡尺。
选择加工孔所用量具。
Φ12.7mm孔经过钻,扩两次加工,选择读数值0.01,测量范围5~30的内径千分尺。
M8和6M螺纹经过钻,锪孔,攻螺纹加工,钻,锪孔时选择读数值0.01,测量范围5~30的内径千分尺,攻螺纹时选择螺纹塞规进行测量。
2.确定工序尺寸
本零件各工序加工余量,工序尺寸及公差,表面粗糙度见下表。
四.
确定切削用量及基本时间
<
一>
粗铣M6孔端面1.切削用量
本工序为铣,已知加工材料为HT200,铸件160Mpa,128-192HBS;
机床为X51式立式铣床,选用镶齿套式面铣刀,直径d=100mm,齿数Z=10,材料选择YG6硬质合金钢,工件装夹在专用夹具上。
(1)确定背吃刀量aP
本工序加工余量aP=1.5mm。
(2)确定每齿进给量fz
本工序要求加工表面粗糙度为Ra≤6.3μm,
查表3.5取每齿进给量fz=0.18mm/z
(3)选择铣刀磨钝标准及寿命
查表3.7得后刀面最大磨损限度为1.5mm,
查表3.8刀具寿命为180min
(4)确定切削速度Vc和工作台每分钟进给量Vf
当寿命为180min,d0/z=100/10=10,aP=1.5mm,fz=0.18mm/z时,
查表3.16得:
Vc=98m/min,n=322r/min,Vf=490mm/min。
其修正系数为kMv=kMn=kMfn=1.0
Kkrv=kkrn=kkrfn=1.1
Ksv=ksn=ksvf=0.8
Kaev=kaen=kaevf=1.13
所以v=98*1.0*1.1*0.8*1.13=97.45m/min
ns=322*1.0*1.1*0.8*1.13=320.2r/min
Vf=490*1.0*1.1*0.8*1.13=487.26mm/min
根据X51立式铣床说明书
由4.2-36选择
nw=300r/min
Vf=480mm/min
实际切削速度为:
v=94.2m/min
工作台每分钟进给量fm=f*Z*nw=540mm/min
查机床说明书取fm=480mm/min
2.基本时间
经计算平面铣削长度为40mm,
入切量及超切量取8.8mm
故铣削该平面的基本时间为
Ti=(40+8.8)/480min=6.1s
<
二>
精铣M6孔端面
1.切削用量
机床为式立式铣床,选用镶齿套式面铣刀,直径d=100mm,齿数Z=10,材料选择YG6硬质合金钢,工件装夹在专用夹具上。
本工序加工余量aP=1.0mm。
(2)确定每转进给量fr
本工序要求加工表面粗糙度为Ra≤3.2μm,
查表3.5取每转进给量fr=0.5mm/r即fz=fr/10=0.05mm/z
查表3.7得后刀面最大磨损限度为0.5mm,
计算得:
Vc=168.4m/min,
ns=1000×
Vc/3.14×
d0=1000×
168.4/3.14×
100=536.3r/min
nw=490r/min
v=3.14*d*nw*10-3=153.9m/min
工作台每分钟进给量fm=fz*Z*nw=245mm/min
查机床说明书取fm=230mm/min
Ti=(40+8.8)/230min=12.7s
<
钻2-M6底孔
本工序为钻,已知加工材料为HT200,铸件;
机床为Z535立式钻床,工件装夹在专用夹具上。
1.切削用量
(1).确定粗加工2-M6螺纹底孔的切削用量。
所选刀具为直柄麻花钻。
Ⅰ.确定背吃刀量ap
钻孔粗加工双边余量4.9mm,显然ap=4.9/2=2.45mm。
Ⅱ.确定进给量f
根据表2.7,在高速钢钻头钻孔时,麻花钻直径为
φ4.9mm,进给量f=0.27~0.33mm/r,选择进给量为0.3mm/r。
Ⅲ.选择钻头磨钝标准及耐用度
根据表2.12,高速钢钻头粗加工灰铸铁,后刀面最大磨损限度0.5~0.8,取值为0.6。
φ4.9mm高速钢钻头平均寿命T=20min。
Ⅳ.确定切削速度v
根据表2-13,钻孔时切削速度的计算公式
vc=16.7m/min,ns=1108r/min
根据机床说明书查表4.2-15,取nw=996r/min,
故实际切削速度为V=3.14*4.9*996/1000=15.3m/min
确定攻2-M6螺纹的切削用量。
所选刀具为M6丝锥。
攻M6螺纹双边余量1.1mm,显然ap=1.1/2=0.55mm。
根据表,攻2-M6螺纹时,加工材料为灰铸铁,进给量为0.3mm/r。
Ⅲ.确定切削速度v
螺纹直径6mm,螺距1,加工灰铸铁,
查表得vc=8m/min。
ns=424.6
根据机床说明书查表4.2-15,取nw=400r/min,故实际切削速度为V=3.14*6*400/1000=7.5m/min
(3).倒2x120度角
采用120度锪钻。
为缩短辅助时间,取倒角时的主轴转速与攻螺纹时相同:
nw=400r/min
手动进给。
(1).确定粗加工2-M6螺纹底孔的基本时间
1)钻深为20mm孔的基本时间为
T=5.0s。
2)钻深为15mm孔的基本时间为
T=4.0s。
(2).确定攻M6螺纹的基本时间
根据表2-30,攻螺纹的基本时间为
T=21s。
以铣削过的底面和钻削后的孔和一个支撑为定位,钻、扩直径12.7的孔。
加工φ12.7×
4.4底孔1.本工序为钻,已知加工材料为HT200,铸件;
1).确定粗加工Φ12mm孔的切削用量。
钻孔粗加工双边余量12mm,显然ap=12/2=6mm。
根据表2.7,在高速钢钻头钻孔时,麻花钻直径为φ12mm,进给量f=0.26~0.32mm/r,选择进给量为0.3mm/r。
根据表2.12,高速钢钻头粗加工灰铸铁,后刀面最大磨损限度0.5~0.8,取值为0.6,高速钢钻头平均寿命T=60min。
由表2.