硫磺回收环保专篇Word格式.docx
《硫磺回收环保专篇Word格式.docx》由会员分享,可在线阅读,更多相关《硫磺回收环保专篇Word格式.docx(13页珍藏版)》请在冰豆网上搜索。
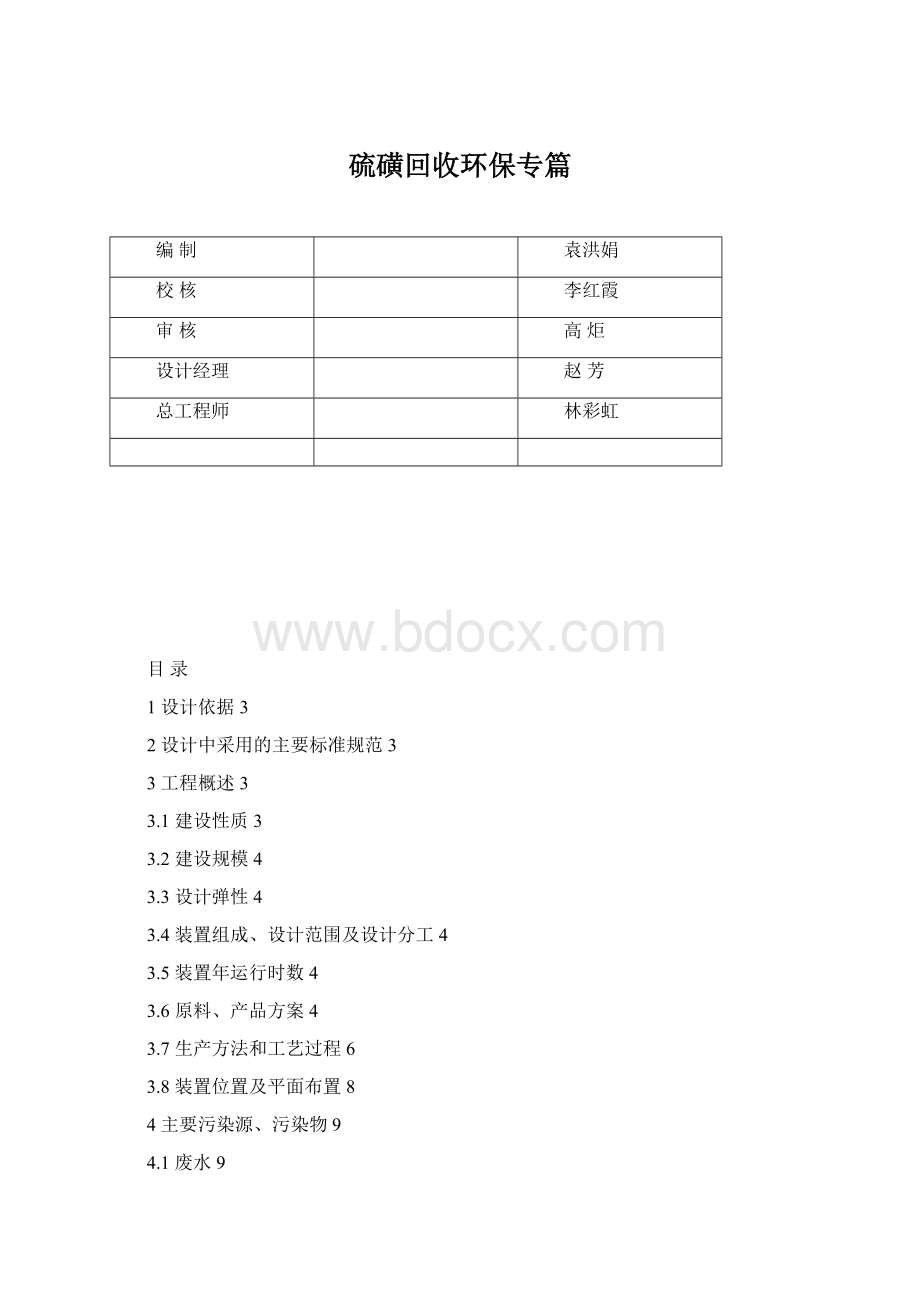
1设计依据
1.1工程项目委托书(委托书编号:
2010068);
1.2工程总体设计批复文件(暂缺);
1.3《石家庄炼油化工股份有限公司油品质量升级改造工程总体设计8万吨/年硫磺回收及溶剂再生装置》31103-01GD-7/2,2009年12月;
(电子版)
1.4《中国石油化工股份有限公司石家庄炼化分公司油品质量升级及原油劣质化改造工程职业病危害预评价报告书》,北京燕山石化职业病防治所,2010年5月;
1.5业主、总体院(中国石化工程建设公司SEI)及河北都邦提供的设计基础资料;
1.6与业主、总体院(中国石化工程建设公司SEI)、河北都邦之间的会议纪要、传真、电子邮件等。
1.7中国石油化工集团公司《石油化工装置基础工程设计内容规定》SHSG-033-2008。
2设计中采用的主要标准规范
《建设项目环境保护设计规定》(87)国环字002号文件
《石油化工企业环境保护设计规范》SH3024-1995
《环境空气质量标准(含修改单)》GB3095-1996
《大气污染物综合排放标准》GB16297-1996
《污水综合排放标准(含修改单)》GB8978-1996
《工业企业噪声控制设计规范》GBJ87-85
《石油化工企业排气筒(管)采样口设计规范》SH3056-1994
《恶臭污染物排放标准》GB14554-93
《工业企业厂界环境噪声排放标准》GB12348-2008
3工程概述
3.1建设性质
硫磺回收装置为石家庄炼化分公司油品质量升级及原油劣质化改造工程的配套子项目,属于新建项目。
3.2建设规模
硫磺回收装置年产硫磺约81263吨(~232.18吨/天)。
3.3设计弹性
硫磺回收装置设计弹性范围60%~120%。
3.4装置组成、设计范围及设计分工
3.4.1装置组成
本装置由制硫(Ⅰ系列、Ⅱ系列)、尾气处理、液硫脱气和储存四部分组成。
3.4.2设计范围和设计分工
1)硫磺回收装置界区内的全部工艺、安装、自控、电气、设备、土建、给排水、暖通、热工及竖向设计由山东三维石化工程有限公司负责;
2)硫磺回收装置界区外的公用工程系统及全厂总平面布置等相应内容由河北都邦石化工程设计有限公司、中国石化工程建设公司负责设计。
界区内外的接口,如地上管廊、地下管道、仪表及电气电信管缆、界区内外道路等,将按相关分工规定执行。
3.5装置年运行时数
装置建成后为连续生产;
设计年运行时数为8400小时。
3.6原料、产品方案
3.6.1原料
3.6.1.1酸性气
本装置的原料为清洁酸性气和含氨酸性气,清洁酸性气来自溶剂再生装置;
含氨酸性气来自酸性水汽提装置,清洁酸性气和含氨酸性气分别用管道输送至本装置。
原料酸性气的来源、规格、数量见下表3.6-1。
表3.6-1原料酸性气数据
酸性气来源
溶剂再生装置
酸性水汽提装置
酸性气合计
温度℃
40
90
压力MPa(g)
0.06
分子量
33.72
25.07
组成kmol/h
H2S
305.615
8.898
CO2
14.281
H2O
15.735
6.351
C1
0.029
N2
0.033
H2
0.268
C2
0.034
C3
0.703
C4+
0.289
NH3
1.015
4.402
合计
19.651
注:
溶剂再生单元的酸性气流量包含了尾气处理溶剂的再生酸性气流量。
从原料数据可以看出,硫磺回收装置原料中含有H2S、NH3、N2等介质,其浓度分别为:
H2S:
87.94%,NH3:
1.51%,N2:
0.01%。
3.6.1.2S-zorb尾气
S-zorb尾气为上游装置管输至硫磺回收装置,其组成见表3.6-2。
表3.6-2S-zorb尾气组成
组成
mol%
2.30
4.90
O2
0.20
90.60
204.7
1.90
0.07
3.6.2产品
硫磺回收单元的产品为液体硫磺。
液体硫磺产量为81263t/a,硫磺产品质量符合GB/T2449-2006中一等品的要求,检测方法参照GB/T2451、2452、2453、2454、2455执行;
其规格如表3.6-3。
表3.6-3硫磺规格表
项目
纯度
砷含量
灰分
酸度(H2SO4)
水份
有机物
铁
指标%(m/m)
≥99.50
≤0.01
≤0.10
≤0.005
≤2.0
≤0.30
3.7生产方法和工艺过程
3.7.1生产工艺
本装置采用“无在线炉硫回收及尾气处理工艺”。
3.7.2工艺特点
3.7.2.1进一级转化器的过程气温度由高温掺合阀自动控制。
尾气处理用烟气废热作热源,外供氢源,全过程不设在线加热炉,工艺节能、降耗、省投资。
3.7.2.2进制硫燃烧炉的酸性气和空气采用比值调节器进行配比调节,在尾气分液罐出口过程气线上设置H2S/SO2在线分析仪,根据在线分析仪的信号反馈微调进燃烧炉的空气量。
3.7.2.3制硫燃烧炉后设置的制硫余热锅炉,产生3.82MPa(g)饱和蒸汽,经尾气焚烧炉后的烟气过热后并网,充分利用高温位余热和烟气废热,降低装置能耗。
3.7.2.4一、二、三级冷凝冷却器为组合式,共用一个壳程,发生0.4MPa(g)低压蒸汽,减少冷侧的控制和调节回路。
3.7.2.5尾气急冷塔和尾气吸收塔为重叠布置二合一设备,节省占地面积。
3.7.2.6装置设计将制硫燃烧炉的自动点火、进料、停车、吹扫、停电保护;
尾气焚烧炉的自动点火、停车、吹扫、停电保护等安全联锁引入SIS,提高了装置运行的安全性和自动化水平。
3.7.3工艺流程简述
3.7.3.1制硫部分(Ⅰ线和Ⅱ线的流程相同,流程仅对Ⅰ线流程进行叙述)。
溶剂再生装置来的清洁酸性气经清洁酸性气分液罐(353-V-1001)脱液后,分为两路进入Ⅰ线和Ⅱ线的制硫燃烧炉(353-F-1001、353-F-2001)的火嘴;
酸性水汽提装置来的含氨酸性气进入含氨酸性气分液罐(353-V-1002)脱液后,分为两路进入Ⅰ线和Ⅱ线,与清洁酸性气合并后,一并进入制硫燃烧炉(353-F-1001、353-F-2001)的火嘴。
在炉内,根据制硫反应需氧量,通过比值调节严格控制进炉空气量,经燃烧,将酸性气中的氨和烃类等有机物全部分解。
通常氨的分解温度为1250℃~1300℃。
为了防止原料性质变化造成炉温偏低,设计了清洁酸性气分流管线,必要时可以将一部分清洁酸性气分流至制硫燃烧炉中部,从而保证炉膛前部温度≮1250℃,避免NOX的生成和铵盐堵塞系统。
在制硫燃烧炉内约73%(v)的H2S进行高温克劳斯反应转化为硫,余下的H2S中有1/3转化为S02,燃烧时所需空气由制硫炉鼓风机(353-K-1001A/B/C)供给,制硫鼓风机(353-K-1001B)采用1.0MPa蒸汽驱动。
制硫燃烧炉(353-F-1001)的配风量是关键,为此,在制硫尾气管道上安装了H2S/SO2在线比值分析仪,随机分析尾气中H2S/SO2比率,并通过反馈信号调节供风管道上的微调阀,使过程气中的H2S/SO2比率始终趋近2:
1,从而获得最高的Claus转化率。
清洁酸性气分液罐(353-V-1001)和含氨酸性气分液罐(353-V-1002)分出的凝液,根据分液包液面信号,启动酸性水泵(353-P-1001A/B)将酸性水送至酸性水汽提装置。
自353-F-1001排出的高温过程气(约1260℃),小部分通过高温掺合阀调节一级转化器(353-R-1001)的入口温度,其余部分进入制硫余热锅炉(353-E-1001),用余热发生3.5MPa饱和蒸汽输至蒸汽过热器(353-E-3003)过热至420℃并网;
过程气温度降至350℃进入一级冷凝冷却器(353-E-1002)冷至160℃,在353-E-1002管程出口,冷凝下来的液体硫磺与过程气分离,自底部流出进入硫封罐(353-V-1004A)。
一级冷凝冷却器(353-E-1002)管程出口160℃的过程气,通过高温掺合阀与1260℃的高温过程气混合后,温度达到264℃进入一级转化器(353-R-1001),在催化剂的作用下,过程气中的H2S和SO2转化为元素硫。
反应后的气体温度为320℃,进入过程气换热器(353-E-1005)管程。
过程气换热器(353-E-1005)管程,与二级冷凝冷却器(353-E-1003)出口的低温过程气换热,温度降至268℃进入二级冷凝冷却器(353-E-1003);
过程气冷却至160℃,353-E-1004冷凝下来的液体硫磺,在管程出口与过程气分离,自底部流出进入硫封罐(353-V-1004B)。
分离后的过程气再返回过程气换热器(353-E-1005)壳程,至218℃进入二级转化器(353-R-1002)。
在催化剂的作用,过程气中剩余的H2S和SO2进一步转化为元素硫。
反应后的过程气进入三级冷凝冷却器(353-E-1004),温度从239℃被冷却至160℃。
353-E-1004冷凝下来的液体硫磺,在管程出口与过程气分离,自底部流出进入硫封罐(353-V-1004C)。
顶部出来的制硫尾气经尾气分液罐(353-V-1003)分液后进入尾气处理部分。
一、二、三级冷凝冷却器(共用一个壳体)的余热均通过发生0.45MPa饱和蒸汽加以回收,产生的饱和蒸汽一部分作为硫磺回收及尾气处理部分的设备、管道伴热(约2.5t/h),剩余部分与制硫鼓风机(353-K-1001B)乏汽混合后送至溶剂再生装置作为溶剂再生热源。
汇入硫封罐的液硫自流进入液硫池(353-T-4001),经注入喹啉和氮气,用液硫脱气泵(353-P-4001A/B)循环脱气处理,液硫中的有毒气体被脱出至气相,用液硫脱气抽空器的中压蒸汽作动力,送至尾气焚烧炉(353-F-3001)焚烧。
脱气后的液硫用液硫提升泵(353-P-4002A/B)送至液硫储罐(353-T-4002A/B)储存或直接外送出厂。
3.7.3.2尾气处理部分
尾气分液罐(353-V-1004)出口的制硫尾气与Ⅱ线尾气分液罐(353-V-2001)出口的制硫尾气合并后,先进入尾气加热器(353-E-3001),与蒸汽过热器(353-E-3003)出口的高温烟气换热,温度升到295℃,混氢后进入加氢反应器(353-R-3001),在催化剂的作用下进行加氢、水解反应,使尾气中的SO2、S2、COS、CS2还原、水解为H2S。
反应后的高温气体约328℃进入蒸汽发生器(353-E-3002)发生0.45MPa饱和蒸汽,尾气温度降至170℃进入尾气急冷塔(353-C-3001)下部,与急冷水逆流接触、水洗冷却至40℃。
尾气急冷塔使用的急冷水,用急冷水泵(353-P-3001A/B)自353-C-3001底部抽出,经急冷水空冷器(353-EA-3001A/B/C)、急冷水冷却器(353-E-3004A/B)冷却至40℃后返353-C-3001循环使用。
因为温度降低凝析下来的不平衡急冷水通过塔底液位调节阀送至酸性水汽提装置处理。
为了防止设备腐蚀,需在急冷水中注入NH3,以调节其pH值保持在7~8。
急冷降温后的尾气自尾气急冷塔(353-C-3001)顶部出来进入尾气吸收塔(353-C-3002)。
溶剂再生装置来的MDEA贫胺液(30%溶液)进入尾气吸收塔(353-C-3002)上部,与尾气急冷塔来的尾气逆流接触,尾气中的H2S被吸收。
吸收了H2S的MDEA富液,经富胺液泵(353-P-3002A/B)升压后返回溶剂再生装置。
自尾气吸收塔(353-C-3002)塔顶出来的净化尾气(总硫≤300ppm),进入尾气焚烧炉(353-F-3001),在760℃高温下,将净化尾气中残留的硫化物焚烧生成SO2,剩余的H2和烃类燃烧成H2O和CO2,焚烧后的高温烟气经过蒸汽过热器(353-E-3003)和尾气加热器(353-E-3001)回收热量后,烟气温度降至330℃左右由烟囱(353-ST-3001)排入大气。
3.8装置位置及平面布置
3.8.1装置位置
中国石化股份有限公司石家庄炼化分公司地处河北省石家庄市东南部,其南侧为石家庄化工基地。
石家庄化工基地西临三环路,一期占地2.95平方公里,与石家庄高新区东区以及东北部的良村开发区成三足鼎立之势。
石家庄化工基地属地处内陆的产业优势区域型化工基地,本项目可依托化工基地共同发展。
本项目改造工程位于石家庄炼化分公司厂区内,其中大部分布置在厂区南部。
根据改造工程总体布置,8万吨/年硫磺回收装置与酸性水汽提装置、溶剂再生装置及S-zorb装置联合布置,位于整个改造工程中部区域,东邻新建500万吨/年常减压联合装置,相距40米;
西侧为原3万吨/年硫回收装置,相距49米;
南侧为第三循环水厂,相距55米;
北侧为液化气罐区最近处相距53米。
3.8.2平面布置
装置设备平面布置在满足生产工艺流程和防火防爆有关要求下,尽量使布置紧凑合理;
设备平面布置设计严格执行GB50160-2008《石油化工企业设计防火规范》和GB50058-92《爆炸和火灾危险环境电力装置设计规范》的有关条款,严格按防爆区域划分,设备平面以满足流程和安全生产为目的,按工艺流程顺序和同类设备适当集中相结合的方式进行布置。
装置界区内的主要工艺设备均为露天布置,使易燃、易爆气体不易积聚。
按防火规范要求:
本装置的框架平台设有斜梯,有两个通向地面的梯子。
框架平台、塔平台均设有消防蒸汽、消防竖管、消防快速接头等以备事故时使用。
装置设备平面布置图见353-PD-00-DW01。
硫磺回收装置周围均布置有6米宽的环行专用消防道路,能够充分保证消防车辆在事故状态下迅速快捷到达现场,充分保证装置生产安全。
4主要污染源、污染物
4.1废水
本装置排出的废水有含硫污水、含油污水及锅炉排污,详细情况见表4.1-1。
4.1.1含硫污水
含硫污水来自尾气急冷塔循环用水中不平衡部分,其中含有硫化物、氨氮等污染物,pH值在6~8之间。
由泵出口管道送至酸性水汽提装置处理。
4.1.2含油污水
含油污水来自乏汽放空筒冷却水、地面冲洗水、设备吹扫水洗等排放污水,见表4.1-1。
表4.1-1
废水名称
排放源
排放规律
排放量
平均(t/h)
排放水质(mg/l)
排放去向
含油污水
地面冲洗
间断
2.0
油:
20;
悬浮物:
~50;
COD:
200;
pH:
7
污水处理场
生产污水
锅炉排污冷却器
连续
1.5
循环热水管网
含硫污水
尾气急冷塔
5.5
硫化物:
~200ppm,wt
氨氮:
~100ppm,wt
pH=6~8
4.2废气
本装置在正常生产时,废气主要为尾气焚烧炉排放的烟气,详细情况见表4.2-1。
烟气中SO2总量约14.272kg/h(计算值),浓度为568mg/Nm3(计算值),采用排气筒高度为120米,GB16297-1996中规定烟气中SO2的允许排放总量二级为170kg/h(100m排气筒),SO2允许排放浓度小于960mg/Nm3。
表4.2-1
废气
排气筒
排放点
kg/h
温度
℃
%(v)
高度
m
直径
mm
大气(SO2排放量计算值14.272kg/h)
烟囱
353-ST-3001
30832
332.7
SO2:
0.0199
CO2:
2.828
H2O:
11.059
120
1600
(出口内径)
4.3废渣
本装置的废渣是定期更换下来的废催化剂,详细情况见表4.3-1。
经过长期运行后,转化器及反应器的催化剂要失活,根据预期寿命或失活情况定期更换。
表4.3-1
序号
名称
米3/次
废渣(液)性质
处置
方法
形态
比重
主要组成
[%(m/m)]
1
废催化剂
一、二级转化器
(353-R-1001,1002)
(353-R-2001,2002)
4年一次
80
Φ4~6mm
球状
0.65~0.80
Al2O3
填埋
2
一级转化器
(353-R-1001)
(353-R-2001)
16
0.7~0.82
3
加氢反应器
(353-R-3001)
5年一次
30
Φ3×
5mm
三叶草形
0.6~0.7
MoO3:
10.0
CoO:
2.5
回收或
4.4噪声
本装置产生噪声源的设备是机泵、空冷风机、鼓风机及气体放空,其噪声级≤85dBA。
当噪声大于85dBA时,人长期在噪声环境下工作,会引起听觉器官损伤和心血管系统病症,并能导致神经衰弱,还能引起胃功能紊乱,视力降低,注意力分散。
5 环境保护措施
5.1废水处理措施
硫磺回收装置产生的含硫污水排至酸性水汽提装置,使净化后的污水达到回用或污水处理场的进水要求。
蒸汽废锅排出的生产废水,没有污染,冷却后排入循环水回水管网。
冲洗地面的污水进入含油污水管网,至污水处理场处理。
5.2废气处理措施
本装置除烟气外,不排放其它废气。
设计中通过对制硫尾气净化处理,使本装置烟气中SO2的排放量及排放浓度均低于国家规定的排放标准。
设计中采取的主要环保措施有:
1)为确保装置安全生产和人身安全,对可能泄漏或聚集H2S气体的地方,按规定设计了H2S有毒气体检测器,并引至控制室进行报警。
2)在工艺上设置了联锁保护措施,当停电或设备故障时可自动切断原料并将其放火炬,避免有毒气体漏到周围环境中。
3)硫磺回收装置设置液硫脱气设施,将液硫中的有害气体脱除送尾气焚烧炉焚烧处理。
4)装置内设置了风向标和警示牌,在事故突发情况下可指示操作人员及时正确地脱离危险场所。
5.3废渣处理措施
硫磺回收装置定期更换下来的废催化剂,由催化剂供应商统一回收或送废渣处理场集中填埋,不会对环境造成污染。
5.4噪声处理措施
设计中选用低噪声的YBXn系列电机、低噪声鼓风机,噪声级小于90dBA,并在鼓风机进口设消音器,同时蒸汽放空设置消音器,减少噪声危害,使装置的工业噪声符合GB12348-2008《工业企业厂界噪声标准》。
6绿化美化
全厂统筹规划,见总体说明。
7环境监测和环境管理机构
石家庄炼化分公司环境管理实行三级管理模式,层层把关,确保环保方针、目标的实现。
公司总经理是环保工作的第一责任人,主管生产的副总经理负责公司的环保工作。
公司设立HSE管理委员会,负责组织贯彻国家和中石化有关环境保护的法律法规和要求;
审定本单位的环保发展规划和有关规定、章程、办法;
协调解决公司有关环保的计划、设计、建设、生产等重大环保问题。
HSE管理委员会设在安全环保处,具体负责公司环境保护日常管理工作及污染防治工作,还聘用了部分兼职环保督察员即时监督各单位的异常排污和违规行为。
生产车间配备具备一定专业技能的环保专职人员,负责全厂环保设施的日常运行和管理工作。
石家庄炼化分公司设有独立行政的环境监测站,负责对污染源及环境设施的废水、废气、噪声以及公司外排废水及厂区噪声等项目的监测。
该监测站配备有实验室通用仪器和环境监测专用仪器,共有各类监测仪器设备100多台(套),主要包括气相色谱仪、液相色谱仪、原子吸收、分光光度计、BOD测定仪、烟气测定仪、烟尘测定仪、CO测定仪、声级计等,可满足常规环境监测和应急监测的需要。
石家庄炼化分公司环境监测站现有人员41人,其中管理人员8人,检验人员33人,下设综合管理组和5个监测班,负责全公司污染源及重点环保设施的废水、废气及噪声的监测;
公司及各分级控制口外排废水的监测;
厂区、生活区空气质量的监测分析。
石家庄炼化分公司环境监测站2008年通过了全国实验室认证。
2009年9月全体化验人员通过了中石化集团公司组织的审核考试。
分析监测人员技术素质较高,大专以上学历在47%以上,中高级职称占17%,确保了监测分析质量。
新建硫磺回收装置的环境监测计划可以依托公司原有的环境保护设施和监测制度进行。
依托现有环境监测站,对该项目的各总排放口、环境质量及装置废气、废渣及噪声排放点进行定期、不定期监测。
8环保专项投资
硫磺回收装置就其性质可视为环保装置,属于环境综合治理项目,因此装置建设投资均属于环保专项投资,其费用约为1.34亿元。
9环境影响分析和预期效果
9.1在本装置设计中充分考虑了环境保护因素,对“三废”进行了有效地治理,尽量压缩“三废”排放,如从工艺上提高技术水平和自控水平,最大限度地提高硫回收率,减少SO2的排放量和排放浓度;
在设计中严格执行各项环境保护标准,针对在生产中产生的各种污染物的特点,能回收利用的回收利用,不能回收利用的,采取了有效的治理措施;
在停工或事故状态下设备放净排出的含硫污水分别送回酸性水汽提装置进行处理,避免了高浓度的含硫污水污染;
设置了硫化氢(有毒气体)报警器,及时发现并避免有毒气体的逸出,污染环境;
所泄放的可燃气体或酸性气,均密闭送往火炬系统;
在设备选型、管道安装等各个环节中采取了有效的措施,减少噪声危害。
9.2项目的建设充分考虑了对环境的保护,对生产中产生的废水、废渣已采取合理、有效措施,进行妥善处理;
废气能够确保达标排放;
所依托的现有各级环境保护机构健全,环境保护措施运行可靠。