车工15车刀几何角度的初步选择Word格式文档下载.docx
《车工15车刀几何角度的初步选择Word格式文档下载.docx》由会员分享,可在线阅读,更多相关《车工15车刀几何角度的初步选择Word格式文档下载.docx(13页珍藏版)》请在冰豆网上搜索。
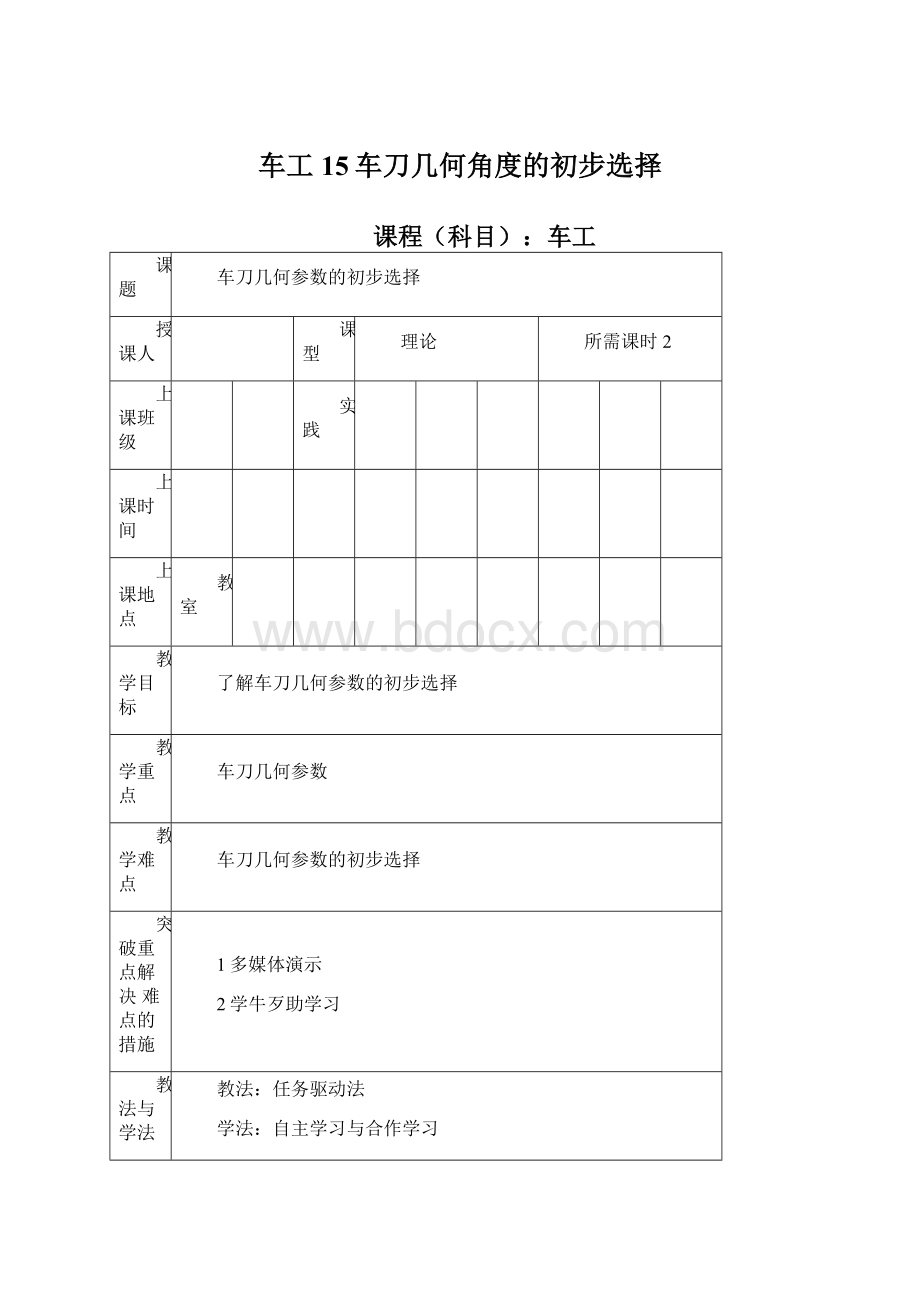
(1)刖角(丫0)和刖刀面
前角的数值与工件材料、加工性质和刀具材料有尖,选择前角的大小主要根据以下几个原则:
1工件材料软,可选择较大的前角;
工件材料硬,应该选择较小的前角;
车削塑性材料时,可选择较大的前角;
车削脆性材料时,应该选择较小的前角。
2粗加工,尤其是车削有硬皮的铸锻件时,为了保证切削刃有足够的强度,应该取较小的前角;
精加工时,为了减小工件的表面粗糙度,一般应取较大的刖角。
3车刀材料的强度、韧性较差,前角应该取小值;
反之,可取大
车刀前角的参考数值见表1
工件材料
刀具材料
咼速钢
硬质合金
前角(丫0)数值
灰铸铁HT150
0°
〜5c
5°
〜10。
咼碳钢、合金钢((T
b
=800〜1000MPa)
15°
〜25°
中碳钢、中碳合金钢
((Tb
=600〜800MPa)
25°
〜30°
10°
〜15°
低碳钢
30°
〜40°
25〜30°
铝及镁的轻合金
35°
〜45°
30°
〜35°
④工艺系统的刚性较差或机场精度不足时应取较大的前角
⑤成形刀具或齿轮刀具等为了防止齿形误差常取很小的前角,甚至是零度的前角O
前角的作用:
前角大,刃口锋利,切削层的塑性变形和摩擦阻力小,切削力和切削热减小。
但前
角过大将使切削刃的强度降低,散热条件变差,刀具的使用寿命降低,甚至会造成崩刃的现象。
虽然前角和前刀面的作用各不相同,但是它们之间有着密切的联系。
前刀面的形状有平面型、曲面型和带带倒棱型三种。
平面型又可以分成正前角平面型、负前角平面型和负前角双面型;
曲面型又
可分为
弧曲面、波纹曲面和其他形式曲面;
带倒棱型又可分为平面带倒棱型和曲面带倒棱型两种。
如
下图所示°
a)
b)
c)
图1前刀面平面型
a)正前角平面型b)负前角单面型c)负前角双面型
图2曲面型
图3带倒棱型
(1)后角(ao)后角太大,会降低切削刃和刀头的强度;
后角太小,会增加后刀面与工件表面的磨擦,选择后角主要诊所以下几个原则:
1粗加工时,应取较小的后角(硬质合金车刀:
ao=5。
〜7。
;
高速钢车刀:
ao=6°
〜8。
);
精加工是时,应取较大的后角(硬质合金车刀:
ao=8°
〜10°
;
高速钢车刀:
ao=8°
〜12°
)
2工件材料较硬,后角宜取小值;
工件材料较软,则后角取大
值。
车刀前角和后角的参考值
高速钢车刀
硬质合金车刀
工件材
料
前角
(°
后角
钢
2o〜25
8〜12
结构
钢、合金
钢及
铸钢
1o〜15
6〜8
5〜io
5〜8
咼强度
钢及表面
有杂质的
-5〜
银縮钢
5〜15
5〜7
不锈钢
15〜3o
8〜1o
和铭钢
可锻铸
铁
15
耐热钢
10〜12
8〜10
铜、铝、
巴氏合
金
25〜30
变形锻
造咼温
合金
5〜10
10〜15
20
铸造咼
温合金
0〜5
0〜15
20〜25
12〜15
钛合金
钳合金
30
淬火钢
-5〜j0
镁合金
25〜35
咼镒钢
_5〜5
电木
铸镒钢
-2〜-5
纤维纸
板
14〜16
灰铸
铁、青
铜、脆性
黄铜
硬橡皮
■2〜0
18〜12
韧性黄
铜
15〜25
软橡皮
40〜75
15〜20
纯铜
塑料、有机玻璃
铝合金
20〜30
中硬青
铜和黄
10
8
纯铁
硬青铜
5
6
铸钩铸
锭
灰铸铁
12
铸鸨铸
锭及烧
结钳棒
15〜35
副后角(aJ)—般磨成与后角(ao)相等但在等特殊情况下,为了保证刀具的强度,副后角应该取较小的数值。
后角的作用:
减少刀具后刀面与工件之间的摩擦,但是后角过大会使切削刃的强度下降,并使散热条件编差,从而降低刀具的使用寿命。
后角的主要作用减少刀具后刀面与工件加工表面之间的摩
擦。
由于切削刃钝圆半径和切屑形成过程中的弹性变形和塑性变形的作用,在工件的加工表面上有一个弹性恢复层。
后角越小,后刀面与工件的加工表面的接触面积就越大,就会使摩擦加剧,使刀具磨损加剧,零件的加工表面的质量变差,冷硬程度加大,尤其是在切削深度较小的时候。
但是减小后角,可使刀具的强度提高,散热条件变好。
此外,在磨损量VB相冋的条件下,减小后角刀具经重磨后材料消耗率较小o
(2)主偏角(Rr)常用车刀的主偏角有45。
、60。
、75。
、90°
等几种选择主偏角首先应考虑工件的形状。
如加工台阶轴之类的工件,车刀主偏角必须等于或大于90。
加工中间切入的工件,一般选用45。
〜60喲主偏角,一下是主偏角的选择原则:
1在工艺系统允许的条件下,应该采用较小的主偏角,以提咼刀具的使用寿命。
加工细长轴时应该使用较大的主偏角,目的是为了减小径向力。
2加工硬度较高的材料时,为减轻单位切削刃上的载荷,应该选取较小的主偏角。
3在车削过程中,刀具需要作中间切入时,应该取较大的主偏角。
4竹片名叫的大小还应该与工件的形状位置有尖系。
比如手在教工阶台轴时,车刀的主偏角可以选90°
・
主偏角主要影响切削宽度和切削厚度的比例,并影响刀具的强度。
主偏角减小,使切削宽度增大,刀尖角增大,刀具强度高、散热条件好,所以刀具的耐用度就高,但是吃刀抗力增人,容易
引起震动的现象和弓箭的加工变形
主偏角参考值
工作条件
主偏角
在系统刚性特别号的情况下,以小的被吃刀量进仃精车。
加工硬度很高的工件材料
10〜30
在系统刚性较好的条件下,加工盘套类类零件
30〜45
在系统刚性较差的条件下
60〜75
在毛坯上不留残心的切断加工
80
在刚性差的条件下车削阶台表面、细长轴
90〜93
(1)副偏角(RL)减小副偏角,可以减小工件的表面)®
糙度,相反,副偏角太大时,刀尖角(£
r)就减小,影响刀头的强度。
副偏角一般采用6°
〜8°
左右,当加工中间切入的工件时,副偏角应取的较大(45。
〜60。
),副偏角的作用时减小副切削刃与工件以加工表面之间的摩擦,一般取较小的副偏角,可减少工件表面的残留面积。
但过小的副偏角会使径向切削力增大,在工艺系统刚性不足的情况下容易产生整栋的现象。
选择原则:
①在不引起振动的情况下,一般取较小的副偏角。
精加工刀具必要时磨出一段修光刃,以加强切削刃对以加工表面的修光作用,从而提高工件的表面粗糙度值。
2工艺系统的刚性较差时,应该取较大的副偏角。
3切断、切槽刀及孔加工刀具的副偏角只能取很小的数值,以保证刀具重磨后的尺寸变化量小。
副偏角参考值
副偏角(°
宽刃车刀及具有修光刃的车削加工
切槽及切断加工
1〜3
精车加工
粗车加工
粗铿加工
有中间切入的切削加工
(1)刃倾角(NS)—般车削时(指工件圆整、切削厚度均匀)取零度的刃倾角,继续切削和加力切削时,为了增加刀头强度,应取负的刃倾角;
精车时为了减小工件的表面粗糙度,刃倾角应取正值。
刃倾角的作用是:
①刃倾角能够控制切屑的流向,当刃倾角为正值时,切削流向待加工表面:
当刃倾角为负值时,切屑流向以加工表面;
当刃倾角为零值时,切屑流向过渡表面。
②单刃刀具米用较大的刃倾角可使原理刀尖的切削刃首先接触工件,使刀尖避免受到冲击力的影响。
③可增大实际前角,使切削轻快。
所以说,刃倾角的主要作用是控制切屑的流向和道具的强度。
刃倾角的选择原则:
①加工硬度较咼的材料或者刀具承受冲击载荷时,应该取较大的负值刃倾角,以保护刀尖不受到伤害。
②精加工时应该取正值的刃倾角,使切屑流向待加工表面,还可以使车刀的刃口锋利。
③内孔加工刀具的刃倾角的方向应该根据孔的加工性质来进行决定o钱通孔时,为使切削向前排出,应该米用负的刃倾角;
攻螺纹时,为使切屑向后排出可以采用正值的刃倾角。
④工艺系统刚性较小时,尽量不选用负的刃倾角<⑤微量切削外圆、内孔时可以采用较大的刃倾角。
刃倾角参考值
刃倾角(°
粗车'
精镇加工
主偏角等于90。
车刀的车削及
铿孔、切断机切槽
钢料的粗车及粗镇
0〜・5
铸铁的粗车及粗镇
-10
带冲击的不断连续车削、刨削
-10〜
带冲击的粹硬钢
-30〜・45
(5)过渡刃
过渡刃是起到调节主偏角和副偏角作用的一个重要的参数。
许多刀具如车刀、麻花钻等,都可能由于减小主偏角和副偏角而使切削力加大,加大主偏角和副偏角而使加工表面粗糙O但是如果选择合适的过渡刃尺寸参数,便能改善上述不利的因素,起到粗加工时提咼刀具的强度和耐用度,精加工时减小工件的表面粗糙度值的作用。
过渡刃的选择原则是:
普通切削刀具常刃磨较小的过渡刃,以增加刀尖的强度、提高刀具耐用度和减小加工表面的表面粗糙度值。
随着工件的强度和硬度的提高,切削用量增大,尤其时切削深度增加,过渡刃尺寸可相应增大。
在精加工时,要根据表面粗糙度的要求,计算或者确定过渡刃偏角或圆弧半径。
(6)修光刃
当过渡刃与进给方向平行时,该过渡刃就称为修光刃,修光刃的作用是在切削过程中起到提高表面粗糙度的作用。
修光刃的选择原则是:
必须要与车刀的进给方向平行且修光刃的长度必须要大于一个进给量。
总之,在实际的加工过程中要根据加工阶段来确定车刀几何角度的大小,如,在粗车时,车刀的切削神的大,所产生的切削力也比较大。
这时候就要要求车刀有一定得强度。
如果要保证车刀有足够的强度,那么所有的车道的集合角度都应该取小值,这样刀头的体积大,刀头的体积越大刀头的强度就也好,就能满足实际的加工要求。
在精加工时,加工余量钱少,切削深度也比较小,所产生的切削力也小。
这时不必过多的考虑车刀的强度,应该侧重考虑车刀的锋利程度,为了保持车刀的锋利,那么车刀各个几何角度应该选择较大的数值。
许多刀具如车刀、麻花钻等,都可能由于减小主偏角和副偏角而使切削力加大,加大主偏角和副偏角而使加工表面粗糙。
但是如果选择合适的过渡刃尺寸参数,便能改善上述不利的因素,起到
粗加工时提高刀具的强度和耐用度,精加工时减小工件的表面粗糙度值的作用。
(7)车刀的工作角度
以上介绍的是车刀在静止状态下的角度,那么在实际生产
中,我们的车刀的几何角度由于受到切削力,切削用量等因素的影响,在一定程度上会发生变化。
车刀安装的高低,车贷刀杆的轴线是否垂直对车刀角度也有恒大的影响。
因此,车刀的工作角度与切削力、切削用量、车刀安装的高低、歪斜程度有较大的尖系
00
1)车刀安装的高低对车刀角度的影响
以车外
(或者横车)为例,当车刀刀尖高于工件中心
时,因其切削平面与挤满的位置发生变化,使前角增大,后角减小5反之,则前角减小,后角增大。
b}C)g
2)车刀安装的歪斜对车刀角度的影响
车刀安装歪斜,对车刀的主偏角、副偏角的影响较大,
特别是在车削螺纹时,会使牙型半角产生误差。
3)车刀在切削过程中受到切削力的影响
在实际的生产中,车刀由于受到进给例的作用车刀与工件的实际接触面积就会加大,在一定程度上会使车刀的诸侯叫或者时复后角减小。
当车刀纵向进给时,主后角减小,当车刀横向进给时,车刀的副后角减
板书设计
课后反思