化工原理认识实习报告Word文档下载推荐.docx
《化工原理认识实习报告Word文档下载推荐.docx》由会员分享,可在线阅读,更多相关《化工原理认识实习报告Word文档下载推荐.docx(14页珍藏版)》请在冰豆网上搜索。
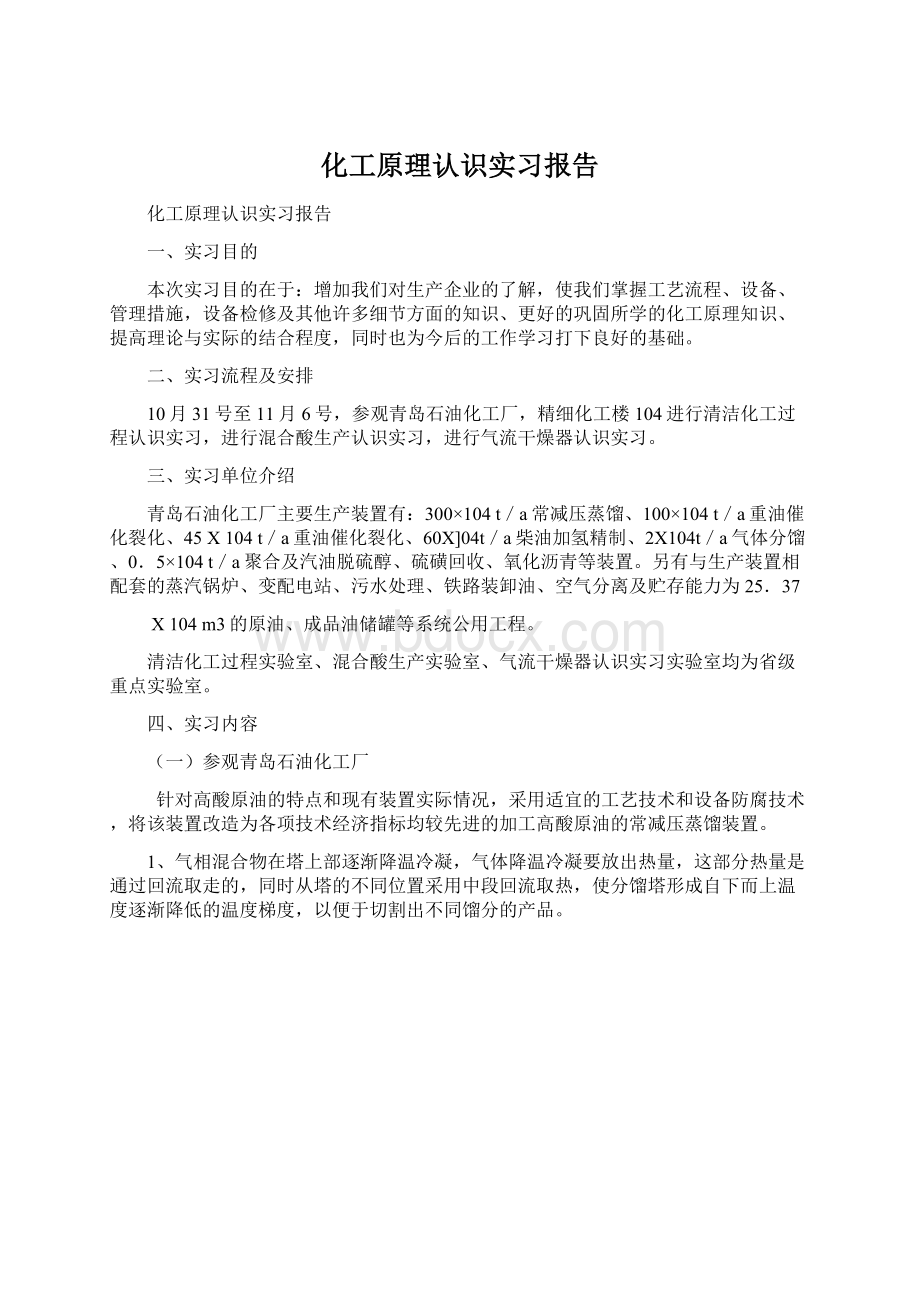
。
精馏过程的实质可概括为:
不平衡的汽液两相,经过热交换,气相多次部分冷凝,与液相多次部分汽化相结合的过程。
蒸气由塔底进入,与下降液进行逆流接触,两相接触中,下降液中的易挥发(低沸点)组分不断地向蒸气中转移,蒸气中的难挥发(高沸点)组分不断地向下降液中转移,蒸气愈接近塔顶,其易挥发组分浓度愈高,而下降液愈接近塔底,其难挥发组分则愈富集,达到组分分离的目的。
2、加氢精制的原料有重整原料、汽油、煤油、柴油和各种中间馏分油、石蜡、重油、渣制工艺流程主要包括:
原料油预处理系统,反应系统,分馏系统和气体压缩机系统四部分。
原料油与加氢生成油换热并与从循环氢压缩机来的循环氢混合,以气液混相状态进入加热炉(有的在炉出口与循环氢混合),加热至反应温度360度,从上而下进入加氢反应器,反应器的催化剂分层填装以便注入冷氢,以控制反应温度(向催化剂层间的空间注入冷氢的量,根据反应热的大小、反应温度和允许温升等因素通过反应器热平衡来决定)。
由反应器底部引出反应产物经换热、冷却到50度后进入高压分离器(因为反应中生成的氨、硫化氢和低分子气态烃会降低反应系统中的氢分压、或氨盐堵塞设备,对反应不利。
因此反应产物进入冷却器前注入高压洗涤水,以便氨、部分硫化氢溶于洗涤水中,随后在高压分离器分出)。
反应产物在高压分离器中进行油气分离,分出的气体是循环氢进入分液器将携带的油进一步分离,经循环氢压缩机升压后循环使用;
分出的液体产物是加氢生成油(高压分离器中的分离过程实际上是一平衡气化过程。
),经减压后进入低压分离器,分出的气体排出装置,液相油品进入分馏塔加热炉加热至245OC后进入分馏塔分割为汽油和柴油。
3、催化重整是最重要的炼油过程之一。
“重整”是指烃类分子重新排列成新的分子结构,而不改变分子大小的加工过程。
重整过程是在催化剂存在之下进行的。
采用铂催化剂的重整过程称铂重整,采用铂铼催化剂的称为铂铼重整,而采用多金属催化剂的重整过程称为多金属重整。
催化重整是石油加工过程中重要的二次加工方法,其目的是用以生产高辛烷值汽油或化工原料––芳香烃,同时副产大量氢气可作为加氢工艺的氢气来源。
下面介绍催化重整的工艺装置。
'
4、催化汽油选择性加氢脱硫醇技术(RSDS技术)
催化汽油加氢脱硫醇装置的主要目的是拖出催化汽油中的硫含量,目前我国大部分地区汽油执行国三标准,硫含量要求小于150ppm,烯烃含量不大于30%,苯含量小于1%。
在汽油加氢脱硫的过程中,烯烃极易饱和,辛烷值损失较大,针对这一问题,石科院开发了RSDS技术。
本技术的关键是将催化汽油轻重组分进行分离,重组分进行加氢脱硫,轻组分碱洗脱硫。
采取轻重组分分离的理论基础是,轻组分中烯烃含量高,可达到50%以上,通过直接碱洗,辛烷值几乎不损失。
而重组分中烯烃大多是环烯烃,经过加氢后变为环烷烃,辛烷值几乎不损失,导致重组分加氢辛烷值损失的是C7以上单烯烃和双烯烃饱和,但以上两种物质所占比例较小,正常情况下重组分加氢后辛烷值损失在1.5以内。
RSDS技术的另一个优点是设立了两个反应器,第一个反应器在低温高空速下操作,目的是将二烯烃饱和成单烯烃,防止在高温反应条件下二烯烃聚合生胶,可以延长运转周期
5、制氢装置
装置采用烃类水蒸气制氢方法,采用的原料是炼厂干气和水蒸气在催化剂上进行反应,产生的氢气在经过变压吸附将氢气提浓,外送氢气纯度达到99.9%。
主要包括以下几个过程。
(1)、干气脱硫部分
进入脱硫部分的原料气,首先进入加氢反应器(R4001),发生将有机硫转化为无机硫,然后再进入氧化锌脱硫反应器(R4002A.B)脱氯段脱除原料中的氯,最后进入氧化锌脱硫段,在此氧化锌与硫化氢发生脱硫反应。
精制后的气体要求硫含量小于0.5ppm,烯烃小于1%(V)、氯小于0.2ppm进入转化部分。
(2)、转化部分
精制后的原料气按水碳比不小于3.2与水蒸汽混合,再经转化炉(F4001)对流段预热,进入转化炉辐射段。
在催化剂的作用下,发生复杂的水蒸汽转化反应,从而生产出氢气、甲烷、一氧化碳、二氧化碳和水的平衡混合物。
主要反应有:
CnHm+nH2O=nCO+(n+m/2)H2
CO+3H2=CH4+H2O△Ho298=-206kJ/mol
转化反应是强吸热反应,转化炉内温度高达900度。
(3)、中变部分
由转化部分来的转化气进入中温变换反应器(R4003),在催化剂的作用下发生变换反应:
CO+H2O=CO2+H2△Ho298=-41.4KJ/mol
将变换气中CO含量降至3%左右,同时继续生产氢气。
中变气经过汽包给水换热器(E4002A.B、E4003)、低温热水换热器(E4004)进行热交换回收部分余热后,再经中变气水冷却器(E4005)冷却至35℃左右,经分水后进入PSA部分。
(二)清洁化工过程认识实习
1、煤的精制
煤的转化作为化学芳烃的原料来源芳烃和杂环芳烃是合成塑料、化纤、橡胶、染料、植物保护剂等化工产品所必需的基础原料。
目前,全世界芳烃的年消耗量约为3000万吨,其中25%来自煤的转化。
煤的一次转化得到的液态产品通常是富含芳烃的混合物,以碳环为主,以杂环芳烃为辅。
典型的煤基芳烃混合物就是煤高温炼焦获得的液态产品—煤焦油和粗苯。
煤炼焦是目前煤的最主要的一次转化过程。
在煤焦油沥青中,由于原料煤及加工过程常含有数量不等的杂原子,其中主要杂原子有氧、氮、硫。
杂原子的存在形式不同,其热稳定性不同,对沥青炭化过程的影响就不同,则炭化产品——焦炭的性能也不同[1]。
文萍等对减压渣油热转化前后的氮分布进行了研究[2],方磊等对神华煤液化残渣热解过程中氮析出的规律进行了研究[3],曹欣玉等对无烟煤燃料氮的热解析出规律进行了研究[4],周俊虎等对煤液化残渣硫析出动态特性进行了研究[5]。
徐志明等对焦炉汽油中富含氮组分进行了分离和表征[6]。
但对煤焦油精制软沥青中杂原子氮、硫的研究相关报道甚少。
本文主要研究针状焦的原料——煤精制软沥青中杂原子氮、硫的分布和热稳定性进行分析,为获得优质的针状焦原料提供基础信息。
现在,全世界每年有4.5亿吨烟煤转化为铁矿石用的还原焦、焦炉气、粗苯和煤焦油。
炼焦的液态产品的获得和加工已经有300多年的历史,业且已经开发了从这些混合物中,例如从煤焦油和粗苯中大规模地获得芳烃的方法。
这就要将各种煤转化工艺所得到的富含芳烃的一次产品加以分离,例如将煤固定床加压气化得到的液态产品和煤浆催化加氢的液态产品加以分离。
同石油化学芳烃的精制相比较,煤化学芳烃混合物的加工特点是要从上述作为主要组分的芳烃中把沸程相似—甚至部分沸点相同—的酚和杂环芳烃相分离(图1)。
要从煤化学加工的这种混合物中获得工业纯的组分的基本原理就是将不同的分离方法进行适当的组合,按不同的加工目的又可得到各种不同的组合。
2、“城市矿山”
经过工业革命300年的掠夺式开采,全球80%以上可工业化利用的矿产资源,已从地下转移到地上,并以“垃圾”的形态堆积在人们周围,总量高达数千亿吨,并还在以每年100亿吨的数量增加。
而靠工业文明发展起来的发达国家,正成为一座座永不枯竭的“城市矿山”。
从金属资源回收循环利用出发,把城市比喻成为一座座储有优良矿产资源的矿山加以开发,确实为经济社会可持续发展寻求矿物资源指出了一条新路,而且“城市矿山”要比天然形成的真正矿山更具开发价值。
从循环经济的角度来看,城市废弃物实为有待开掘的‘富矿’,是以另外一种形式存在的资源。
如果处理得当,便可取得环境和资源的双重效益。
中国是制造业大国,需要大量矿产资源作为支撑,而目前国内原生矿的供给形势并不乐观。
因此,采取开采原生资源和循环利用再生资源并重的资源战略十分必要。
对“城市矿山”的开发在中国总体上尚属起步阶段,实施过程中面临诸多困难。
行业管理制度和法律法规体系缺失、废旧物资回收技术落后、以及社会认知不足导致还有相当数量的废弃物尚未进入规范的循环体系之内,行业的经济效益也未能得到充分体现。
中国有色网。
但是也要看到,由于城市的规模、功能定位、成长历史、产业构成、消费水平,尤其是现代化程度以及居住人群结构等差别很大,既不可能每座城市都成为“城市矿山”,就是在可以作为“城市矿山”的城市中,开发的价值也是千差万别的。
“城市矿山”的开发价值,首先取决于回收利用的各种金属的多少,既要看当前的“存量”,还要预测到未来的“增量”,看“增量”的增长速度。
可充电池资源回收工艺研究较多,可以分为火法和湿法两大类。
火法是利用了电池中各种金属升华温度的不同回收不同的金属,其缺点是温度高、炉子设备昂贵[1-3]。
湿法是首先在550~600℃温度下焙烧固体物[4-6],使金属氧化,用不同的浸取液浸出金属,浸取液有硫酸、盐酸、氨水、醋酸等,而后用不同方法分离回收有价金属,分离方法有H2S沉淀法、电解沉积法、置换法、碳酸盐法和翠取法等。
3、制备生物柴油
生物柴油(Biodiesel)是指以油料作物、野生油料植物和工程微藻等水生植物油脂以及动物油脂、餐饮垃圾油等为原料油通过酯交换工艺制成的可代替石化柴油的再生性柴油燃料。
生物柴油是生物质能的一种,它是生物质利用热裂解等技术得到的一种长链脂肪酸的单烷基酯。
生物柴油是含氧量极高的复杂有机成分的混合物,这些混合物主要是一些分子量大的有机物,几乎包括所有种类的含氧有机物,如:
醚、酯、醛、酮、酚、有机酸、醇等。
(三)混合酸生产认识实习
1、混合酸
混合酸是为了达到特定的目的,而将特定两种或两种以上的酸按特定的比例混合得到。
很多时候酸性会增强。
但不一定。
硝酸和氢硫酸混合生成立硫单质和二氧化氮,酸性可消失,没有实际意义。
王水是一种非常强的混酸,浓硝酸与浓盐酸按体积比1:
3混合得到,利用了氯离子与金属离子的配位作用降低电极电位是反应可以发生。
如金、铂不溶于浓硝酸却溶于王水。
混合算中还有一种特例,如超强酸又称超酸。
是一种比100%硫酸还强许多倍的酸。
特别是液体超强酸,有的比98%硫酸强近10^12倍,有严重腐蚀性和严重公害。
全氟磺酸树脂(Nafion-H)是现在已知的最强固体超强酸,具有耐热性能好、化学稳定性和机械强度高等特点。
一般是将带有磺酸基的全氟乙烯基醚单体与四氟乙烯进行共聚,得到全氟磺酸树脂。
由于Nafion-H分子中引入电负性最大的氟原子,产生强大的场效应和诱导效应,从而使其酸性剧增。
与液体超强酸相比,用作催化剂时,易于分离,可反复使用。
且腐蚀性小,引起公害少,选择性好,容易应用于工业化生产。
硝酸可以氧化绝大多数金属和合金,但是不能氧化金和铂,高浓度的硝酸可使一些金属钝化。
溶解这些金属可以使用混酸或稀硝酸来实现。
HNO3最常用的破坏有机物的酸。
HNO3与其它的酸混合时是一种较强的酸,例如与HF混合。
HCl经常和其它的酸混合使用,最常混合的为HNO3,王水就是HCl和HNO3(HCl+HNO3=3+1)的混合物。
为了提高溶解能力,HF经常与其它酸混合使用,如HNO3。
高氯酸通常与硝酸混合使用,这种混合酸可实现有机物的可控消解,在低温时,混酸中的硝酸首先氧化易被氧化的物质,随着温度的升高,高氯酸将完全消化未被消化的物质。
因为高氯酸可以分解几乎所有的有机基体,所以可以选择它来破坏有机物,并且几乎所有的高氯酸盐都可溶。
但是,许多干燥的高氯酸盐都可爆炸。
2、醋酸乙酯的生产工艺
乙酸乙酯又称醋酸乙酯。
纯净的乙酸乙酯是无色透明具有刺激性气味的液体,是一种用途广泛的精细化工产品,具有优异的溶解性、快干性,用途广泛,是一种非常重要的有机化工原料和极好的工业溶剂,被广泛用于醋酸纤维、乙基纤维、氯化橡胶、乙烯树脂、乙酸纤维树酯、合成橡胶、涂料及油漆等的生产过程中。
其主要用途有:
作为工业溶剂,用于涂料、粘合剂、乙基纤维素、人造革、油毡着色剂、人造纤维等产品中;
作为粘合剂,用于印刷油墨、人造珍珠的生产;
作为提取剂,用于医药、有机酸等产品的生产;
作为香料原料,用于菠萝、香蕉、草莓等水果香精和威士忌、奶油等香料的主要原料。
我们所说的陈酒很好喝,就是因为酒中含有乙酸乙酯。
乙酸乙酯具有果香味。
因为酒中含有少量乙酸,和乙醇进行反应生成乙酸乙酯。
因为这是个可逆反应,所以要具有长时间,才会积累导致陈酒香气的乙酸乙酯。
由于酯化反应是可逆反应,为提高酯的产率,采用增加醇的用量及不断将产物酯和水蒸出的措施,使平衡右移。
反应中,浓硫酸除起催化作用外,还吸收反应生成的水,有利于酯的生成。
反应温度过高,会促使副反应发生,生成乙醚等。
乙酸乙酯生产工艺由酯化、脱轻、精制和回收工段组成,在酯化和脱轻工段之间添加膜分离工段。
酯化塔顶有机相经过膜分离脱除大部分水分,处理后的有机相一部分返回酯化塔回流,另一部分送往脱轻塔精制。
所述膜分离工段包括真空罩(内含膜组件)、冷凝器、渗透液罐、缓冲罐和真空泵。
本发明的方法能够极大减少水在酯化和脱轻工段中循环,节省酯化塔和脱轻塔的加热蒸汽,并能降低酯化塔和脱轻塔的负荷,进而增加酯化塔和脱轻塔的生产能力。
中国科学研究院长春应用化学研究所对乙醇氧化酯化反应催化剂进行了研究,认为采用Sb2O4-MoO3复合催化剂可提高活性和选择性。
化学工业部西南化工研究院等联合开发的乙醇脱氢一步合成醋酸乙酯的新工艺,已通过单管试验连续运行1000小时,取得了满意的结果。
现正在进行工业开发工作。
由于使用硫酸作为酯化反应的催化剂存在硫酸腐蚀性强、副反应多等缺点,近年各国均在致力于固体酸酯化催化剂的研究和开发,但这些催化剂由于价格较贵、活性下降快等原因,至今工业应用不多。
据报道,美DavyVekee公司和UCC公司联合开发的乙醇脱氢制醋酸乙酯新工艺已工业化。
醋酸、过量乙醇与少量的硫酸混合后经预热进入酯化反应塔。
酯化反应塔塔顶的反应混合物一部分回流,一部分在80℃左右进入分离塔。
进入分离塔的反应混合物中一般含有约70%的乙醇、20%的酯和10%的水(醋酸完全消耗掉)。
塔顶蒸出含有83%醋酸乙酯、9%乙醇和8%水分的塔顶三元恒沸物,送人比例混合器,与等体积的水混合,混合后在倾析器倾析,分成含少量乙醇和酯的较重的水层,返回分离塔的下部,经分离塔分离,酯重新以三元恒沸物的形式分出,而蓄集的含水乙醇则送回醋化反应塔的下部,经气化后再参与酯化反应。
含约93%的醋酸乙酯、5%水和2%乙醇的倾析器上层混合物进人干燥塔,将醋酸乙酯分离出来。
3、醋酸丁酯的生产工艺
由羧酸和醇直接合成酯的酯化反应是一个可逆反应,而且在室温下反应速度很慢。
加热、加酸作催化剂,可使酯化反应速率大大加快。
同时为了使平衡向生成物方向移动,可以采用增加反应物浓度(冰醋酸),和将生成物除去的方法,使酯化反应趋于完全。
主反应
溶解性与醇、酮、醚等有机溶剂混溶,与低级同系物相比,较难溶于水。
无色液体,有水果香味。
相对密度(20℃/4℃)0.8825,凝固点-73.5℃,沸点126.11℃,闪点(开口)33℃,燃点421℃,折射率1.3941,比热容(20℃)1.91KJ/(kg·
K),粘度(20℃)0.734mPas,溶解度参数δ=8.5。
溶于醇、酮、醚等有机溶剂,微溶于水。
遇高热、明火、氧化剂有引起燃烧危险。
蒸气与空气形成爆炸性混合物,爆炸极限1.4%-8.0%(vol)。
低毒、有麻醉和刺激性,空气中最高容许浓度300mg/m3(或0.015%)。
用于火棉胶、硝化纤维、清漆、人造革、医药、塑料及香料工业中.是一种优良的有机溶剂,能够溶解松香、聚醋酸乙烯、聚丙烯酸酯、聚氯乙烯、氯化橡胶、杜仲胶、聚甲基丙烯酸甲酯等。
(四)气流干燥器
1、直流降膜式旋风除雾器:
解决了设备内壁物结壳的国际性难题,已在工业上推广应用六套,单台设备处理量达到了55000m³
/h.(主要解决三聚氰胺在生产中的结壳问题,用流动的液体带动固体向下流,保护壁面不结壳)(下图右)
2、钻削洗涤分离试验:
洗涤分离是海上钻屑脱油工艺的技术关键。
本实验目的是研究旋流液固分离器性能,考察脉冲洗涤罐冲洗效果,测试工业设计参数。
操作规程:
1).水压实验达标后方可投料开车2).将溶剂加入溶剂罐后封闭加料口3).在料槽按要求配置带油基岩屑,启动料槽搅拌器4).关闭容积泵入口阀,并检查各阀门开闭情况5).启动容积泵,缓慢将流量调至实验要求值6).启动加料泵,调节加料量7).测系统压降,冲洗分离效率8)缓慢停加料泵,关闭容积泵入口阀,停溶剂泵,将溶剂与岩屑排除系统封存。
3、环流循环除尘系统:
分割直径达到了0.5微米,可用于亚微米粉尘的除尘,已在工业上推广应用。
4、旋风分离器:
净化天然气通过设备入口进入设备内旋风分离区,当含杂质气体沿轴向进入旋风分离管后,气流受导向叶片的导流作用而产生强烈旋转,气流沿筒体呈螺旋形向下进入旋风筒体,密度大的液滴和尘粒在离心力作用下被甩向器壁,并在重力作用下,沿筒壁下落流出旋风管排尘口至设备底部储液区,从设备底部的出液口流出。
旋转的气流在筒体内收缩向中心流动,向上形成二次涡流经导气管流至净化天然气室,再经设备顶部出口流出。
(下图左)
5、气液分离器
气液分离器可安装在气体压缩机的出入口用于气液分离,分馏塔顶冷凝冷却器后气相除雾,各种气体水洗塔,吸收塔及解析塔的气相除雾等。
气液分离器也可应用于气体除尘,油水分离及液体脱除杂质等多种工业及民用应用场合。
气液分离器采用的分离结构很多,其分离方法也有:
1)、重力沉降;
2)、折流分离;
3)、离心力分离;
4)、丝网分离;
5)、超滤分离;
6)、填料分离等。
由于气液混合物总是处在重力场中,所以重力沉降也广泛存在。
由于重力沉降固有的缺陷,使科研人员不得不开发更高效的气液分离器,于是折流分离与离心分离就出现了。
从气液分离器的要求来看,就要求其能将气体与液体尽可能分离,经过气液分离器之后,液体就是液体,不含有气体,而气体就是气体,不含有液体。
当然一个分离器实际上其分离效率不可能100%,因种种原因实际的情况是根据不同分离要求来选择气液分离器。