完整版泵体毕业设计Word格式文档下载.docx
《完整版泵体毕业设计Word格式文档下载.docx》由会员分享,可在线阅读,更多相关《完整版泵体毕业设计Word格式文档下载.docx(17页珍藏版)》请在冰豆网上搜索。
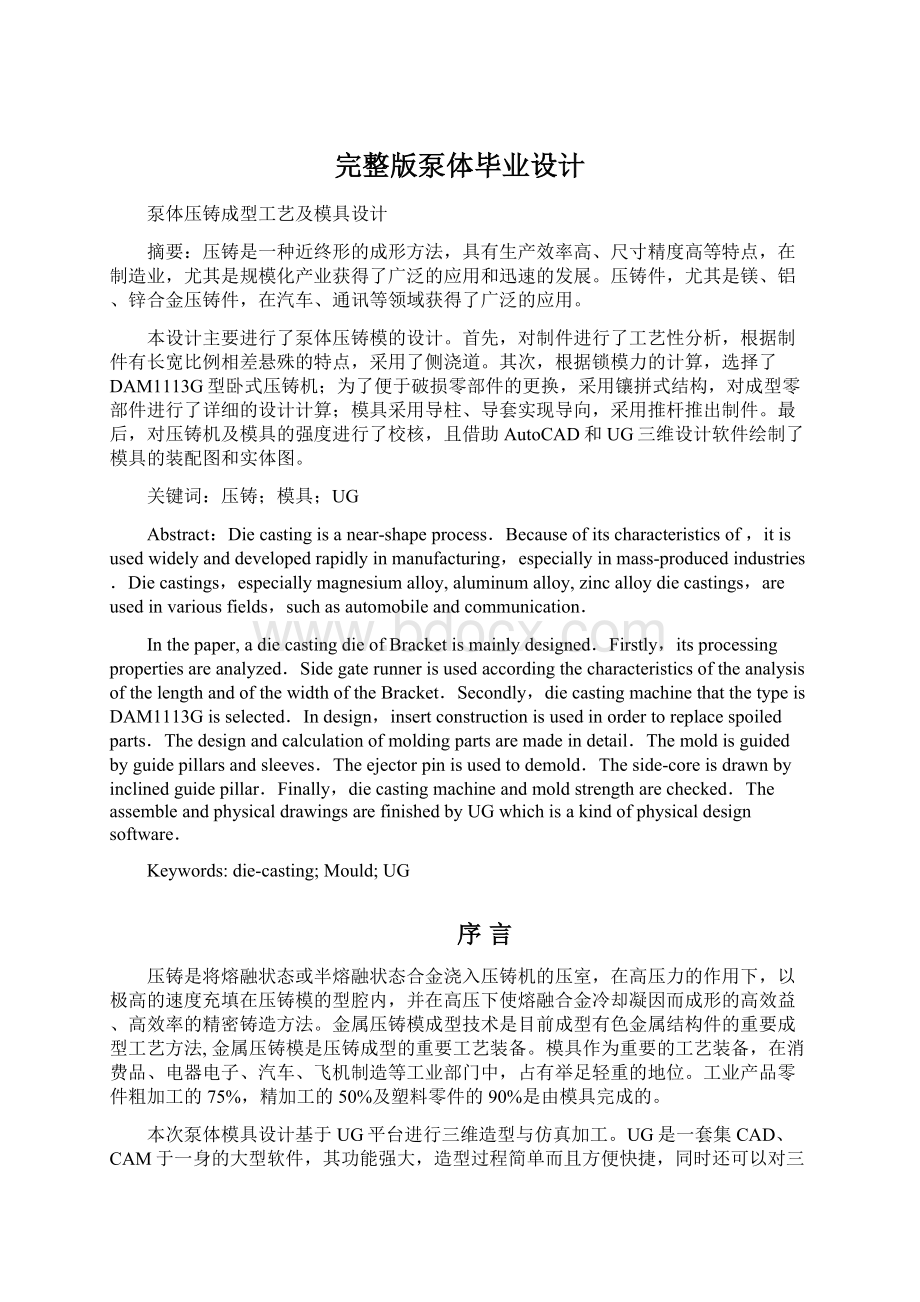
数控加工是现代制造技术的典型代表,数控技术是机械加工自动化的基础,是数控机床的核心技术,其水平高低关系到国家战略地位和体现国家综合国力的水平。
序言2
第1章压铸件结构及工艺分析5
1.1任务介绍5
1.2压铸零件的分析5
1.3拟定模具结构形式7
1.4压铸工艺分析及计算7
1.5压铸机的选用8
第2章压铸模结构设计8
2.1确定模具分型面8
2.2浇注系统的设计10
2.2.1内浇口的设计11
2.2.2直浇道设计13
2.2.3横浇道设计14
2.3排溢系统的设计16
2.3.1溢流槽的设计16
2.3.2排气道的设计17
2.4模具温度及冷却系统的设计18
2.5抽芯结构设计19
2.5.1行位的设计19
2.6推出机构的设计22
2.6.1推出机构设计22
2.6.2推杆设计及强度校核23
2.6.3推出机构其他设计24
2.7模具结构的设计25
2.7.1模具结构主要结构件的设计25
2.7.2压铸模的技术要求27
2.8压铸模选材和热处理要求30
2.9模具组装技术要求31
2.10成型零件的设计31
2.11模具对压铸生产的影响33
设计总结38
致谢39
参考文献40
附录41
第1章压铸件结构及工艺分析
1.1任务介绍
主要内容及基本要求:
1.完成泵体的模具设计
2.在UG或其他三维软件平台上完成模具零件的三维建模
3.完成模具的装配
4.设计说明书一份,字数不少于10000字。
1.2压铸零件的分析
本次设计的零件为泵体的模具设计,如下图1-1所示:
图1-1泵体产品图
泵体是某种型号电机上的零件,生产批量100,000件,铸件要求无欠铸、气孔、疏松、裂纹等缺陷。
产品原始信息
产品大小:
65.57*78.49*18.38单位:
MM
产品平均壁厚:
7.6MM
材质:
锌合金(ZZnAlD4)
重量:
199g
缩水率:
1.005
其物理和力学性能为:
密度6.6gmm³
固相线与液相线温度分别为381º
C和387º
C,抗拉强度283MPa,屈服强度414MPa,硬度82HB,剪切强度214MPa,疲劳强度476MPa。
压铸锌合金的使用性能和工艺性能都优于其他压铸合金,而且来源丰富,所以在各国的压铸生产中都占据极重要的地位,其用量远远超过其他压铸合金。
锌合金的特点是:
比重小、强度高;
铸造性能和切削性能好;
耐蚀性、耐磨性、导热性和导电性好。
锌和氧的亲和力很强,表面生成一层与锌结合得很牢固的氧化膜,致密而坚固,保护下面的锌不被继续氧化。
锌硅系合金在杂质铁含量较低的情况下,粘模倾向严重。
锌合金体收缩值大,易在最后凝固处形成大的集中缩孔。
用于压铸生产的锌合金主要是铝硅合金、铝镁合金和铝锌合金三种。
纯锌铸造性能差,压铸过程易粘模,但因它的导电性好,所以在生产泵体时使用。
锌合金中主要合金元素及杂质对其性能影响如下:
硅:
硅是大多数锌合金的主要元素。
它能改善合金在高温时的流动性,
提高合金抗拉强度,但使塑性下降。
硅与锌能生成固熔体,它在锌中的溶解度随温度升高而增加,温度577℃时溶解度为1.65%,而室温时仅为0.2%。
在硅含量增加到11.6%时,硅与其在锌中的固溶体形成共晶体,提高了合金高温流动性,收缩率减小,无热裂倾向。
二元系铝硅合金耐蚀性高、导电性和导热性良好、比重和膨胀系数小。
硅能提高铝锌系合金的抗蚀性能。
当合金中硅含量超过共晶成分,而铜、铁等杂质又较多时,就会产生游离硅,硅含量越高,产生的游离硅就越多。
游离硅的硬度很高,由它们所组成的质点的硬度也很高,加工时刀具磨损厉害,给切削加工带来很大的困难。
此外,高硅锌合金对铸铁坩锅熔蚀严重。
硅在锌合金中通常以粗针状组织存在,降低合金的力学性能,为此需要进行变质处理。
铜:
铜和锌组成固溶体,当温度为548℃时,铜在锌中的溶解度为
5.65%,室温时降至0.1%左右。
铜含量的增加可提高合金的流动性、抗拉强度和硬度,但降低了耐蚀性和塑性,热裂倾向增大。
压铸通常不用锌铜合金,而用锌硅铜合金。
该产品的成型材料是锌合金,该材料密度小,熔点为381~387度,强度较高,耐磨性能较好,导热、导电性能好,机械切削性能良好,但由于锌与铁有很强的亲和力,容易粘模,加入Mg以后可得到改善。
锌压铸,其锌很容易就粘在模具表面上,造成铆接柱拉伤、拉断,浇注口堵塞现象.
1.3拟定模具结构形式
根据压铸件的产品信息,产品生产所需的数量,产品的强度和精度有较高要求,综合实际考虑,该产品采用一模二穴的成型方法。
1.4压铸工艺分析及计算
(1)锁模力计算
根据压铸产品选择压铸机,锁模力通常的计算方式为用模具分型面上承受金属压力的投影面积乘以铸造比压乘以安全系数。
锁模力的计算如下:
T=K*A*P
其中:
T为锁模力,单位为N;
K为安全系数,热室压铸机一般取1.3
A为铸造投影面积,单位mm²
(包括铸件、料、头、流道、溢流井等,约相当于铸件的1.8倍)
P为压射比压,单位Mpa。
单位换算1T=10KN=100000N
该产品的铸件投影面积为2843*1.8=5117.4mm²
由于该产品为压铸件,压射比压取值为30Mpa。
故该产品的锁模力为:
T=K*A*P=2*1.3*5117.4*3010*100=400KN
1.5压铸机的选用
根据以上数据选择锁模力大于400(KN)的机台(如图)即可,结合锌合金机台设备考虑,本次模具设计采用的是热压室压铸机,其型号与主要技术规格如下:
压铸机型号:
DAM1113G
锁模力KN:
1250
压射力KN:
85-150
第2章压铸模结构设计
2.1确定模具分型面
分型面的定义:
压铸模的定模与动模接合表面通常称为分型面,分型面是由压铸件的分型线所决定的,而模具上垂直于锁模力方向的接合面,即为基本分型面。
分开模具取出压铸制品的界面称为分型面,也可称为合模面。
分型面的类型选择是否恰当,设计是否合理,在模具设计中非常重要。
它不仅直接关系到模具结构的复杂程度,而且对制品的成型质量和生产操作等都有影响。
选择分型面即是决定型腔空间在模内应占有的位置。
选择分型面时应遵循以下原则:
(1)符合压铸件脱模:
为使压铸件能从模具内取出,分型面的位置应设在压铸件断面尺寸最大的部位。
(2)分型面的数目及形状:
通常只采用一个与压铸机开模运动方向相垂直的分型面,特殊情况下才采用一个以上的分型面或其他形状的分型面。
(3)型腔方位的确定:
在决定型腔在模具内的方位时,分型面的选择应尽量防止形成侧孔或侧凹,以避免采用较复杂的模具结构。
(4)确保压铸件质量:
分型面不要选择在压铸件光滑的外表面,避免影响外观质量;
将压铸件要求同轴度的部分全部放在分型面的同一侧,以确保压铸件的同轴度;
要考虑减小脱模斜度造成压铸件大,小端的尺寸差异要求等。
(5)有利于压铸件的脱模:
由于模具脱模机构通常设在动模一侧,故选择分型面时应尽可能使开模后压铸件留在动模一侧。
(6)有利于排气:
当分型面作为主要排气渠道时,应将分型面设计在压铸熔体的流动末端,以利于排气。
(7)模具零件易于加工:
选择分型面时,应使模具分割成易于加工的零件,以减小机械加工的困难。
分型面的选择
图2-1分型面方案
型腔图片
型芯图片
2.2浇注系统的设计
浇注系统对熔融金属流动方向、压力传递、模具温度分布、充填时间长短起到重要的调节和控制作用,浇注系统设计直接影响铸件的机械性能和模具寿命。
浇注系统设计一般步骤:
内浇口设计→浇道设计→过水设计→渣包设计
内浇口宽度的选取及内浇口设计的原则:
1.金属液从铸件壁厚处向壁薄处填充
2.金属液进入型腔后不宜立即封闭分型面,溢流面和排气槽
3.内浇口的位置要使进入型腔的金属液先流向远离浇口的部位
4.从内浇口进入的金属液,不宜正面冲击型芯
5.浇口的位置应便于切除
6.避免在浇口部位产生热节
7.金属液进入型腔后的流向要沿着铸件上的肋和散热片
8.选择内浇口位置时,应使金属液流程尽可能短
2.2.1内浇口的设计
根据其各自应用范围和特点,针对本次设计零件的形状,选择端面侧浇口,使金属液首先填充可能存留气体的型腔底侧,将底部的气体排出后,再逐步充满型腔,避免压铸件中气孔缺陷的产生。
内浇口面积的计算
铸件设计完成后,测量浇铸体积(产品+溢料)的体积,在压铸件的填充时间及填充数度选定后,内浇口面积可采用下式计算:
Ag=VVg*t
其中:
Ag—内浇口截面积(mm²
)
V—铸件的体积(mm³
)(包括渣包和产品)
Vg—充填速度(ms)
t—充填时间(s)
图2-2内浇口示意图
对应参数的计算:
充填时间的计算
充填时间是指熔融金属自到达浇口(gate)起算,至模穴(cavity)及溢流井完全充填完毕为止,所经过的时间。
理论上,充填时间是越短越好;
但实际上,充填时间受以下限制:
(a)逃气
(b)模具冲蚀
(c)机器性能
以下列公式(NADCA)计算出填充时间:
t=k[(Ti-Tf+SZ)(Tf-Td)]×
T
其中k=0.0346秒mm
Ti=熔汤进入模具温度,取650º
C
Tf=合金最低流动温度,取595º
S=容许凝固百分率,取0%
Z=转换系数2.5º
C%
Td=模具温度,取240º
T铸件厚度,取7.6m
t=0.0346×
[(650-595+0.0×
2.5)(595-240)]×
7.6
=0.04(秒)
铸件体积的计算
V=30068*1.2=36000mm³
(包括渣包和产品)
内浇口充填速度的计算
对于不同壁厚的镁、铝、锌压铸合金的充填速度不同:
本产品平均壁厚为7.6MM,材质为锌合金,内浇口填充速度为50ms
本产品的内浇口面积为:
考虑到产品的结构问题,内浇口宽度L取值为18mm,所以内浇口厚度H=H=AgL=1818=1mm
2.2.2直浇道设计
直浇道是金属液从压室进入型腔前首先经过的通道。
卧室热压室压铸模直浇道的由浇口套、浇道镶块和浇道推杆组成。
浇口套与压铸机的压室端面密封对接。
浇口套在压铸模的浇注系统中起着承前启后的作用,直浇道就是在浇口套中形成的。
1.浇口套与压室的连接方式
浇口套与压室的连接方式,根据浇口套结构形式的不同,可分为连接式和整体式。
本次设计采用整体式结构即将压室与浇口套制成整体,这样易于内孔的精度容易保证。
2.浇口套参数的确定
直浇道由压铸模上浇口套构成,能保证压射冲头动作顺畅,有利于压力传递。
直径D:
根据压铸件重量、所需比压、在压室的充满度(一般占23)来选择冲头直径,也就是直浇道的直径D。
厚度H:
称为余料,取直径的12~13,为了易脱模,设1°
30’~2º
斜度。
3.浇口套的配合精度
浇口套的配合精度有:
浇口套与模板孔的配合精度、浇口套内孔与压射冲头的配合精度和定位孔与压铸机压室法兰的配合精度。
(1)浇口套与模板孔的配合精度为(H7a)1+fsinacosa
式中:
p为压铸件对型芯包紧产生的压强(MPa),p经验值一般取8~20MPa,本设计取为15MPa。
f为摩擦系数取0.5,α为型芯斜度,粗略取压铸件型芯整体斜度=2°
。
s为压铸件包紧型芯的侧面积(mm2),因为压铸件存在内凹结构,即对型腔存在抱紧力,所以压铸件对型芯产生的有效脱模力的侧面积s=S(型芯)-S(型腔)
推杆直径的计算
圆截面推杆直径设计公式
d=K(64Qe(mL)2nEp31)4≈6mm
Qe为脱模力(N);
n为推杆数目取n=43;
K为安全系数,K=1.3;
L为推杆长度(mm);
这里L取最长推杆的长度,L=187mm;
μ为压杆的长度系数,取μ=0.5;
E为材料弹性模量(MPa),E=2*105MPa。
以下以43根F10的推杆;
来校核推杆的应力。
s=(4´
481500)(43´
3.14´
102)=142.6Nmm2
一般SKD61钢[s]=32000Nmm2,则s<
[s],满足要求。
实际设计中,须考虑到压铸件结构、表面要求的特殊性、冷却水管的分布、推杆作用力的均布等,本次设计采用Φ6×
187共计30根推杆。
2.6.3推出机构其他设计
1.复位杆的设计
复位杆是控制推出机构在合模状态时,回复到原来位置的主要零件之一,其结构如图2-12所示:
模具采用四根复位杆将模具复位
图2-12复位杆
2.导柱和导套的设计
动、定模的导柱和导套,主要是保证在安装和合模时的正确位置,在合模过程中保持导柱、导套首先一起定向作用,防止型腔、型芯错位,其结构如图2-13,2-14所示:
图2-13导柱
图2-14导套
2.中托司导柱导套的设计
中托司的设计,主要是保证在安装模具在顶出的过程中,起到上、下顶针板的导向作用的,防止顶针板的错位变形,其结构如图2-15所示:
图2-15中托司
2.7模具结构的设计
2.7.1模具结构主要结构件的设计
模具结构主要结构件有定模座板、动模板、动模支撑板、垫块以及模座等。
1.模板尺寸的估定
确定模板尺寸时,一般先按基本的结构考虑,即假定没有侧抽芯机构,或模板上未开有大的缺口槽的情况下,大体估算有关尺寸。
(1)模板的厚度H
H=、Al、Mg是较活泼的金属元素,它们与模具材料有较好的亲和力,特别是Al易咬模。
当模具硬度较高时,则抗蚀性较好,而成型表面若有软点,则对抗蚀性不利。
但在实际生产中,溶蚀仅是模具的局部地方,例内浇口直接冲刷的部位(型芯、型腔)易出现溶蚀现象,以及硬度偏软处易出现铝合金的粘模。
压铸生产中常遇模具存在的问题注意点:
1、浇注系统、排溢系统例
(1)对于冷室卧式压铸机上模具直浇道的要求:
①压室内径尺寸应根据所需的比压与压室充满度来选定,同时,浇口套的内径偏差应比压室内径的偏差适当放大几丝,从而可避免因浇口套与压室内径不同轴而造成冲头卡死或磨损严重的问题,且浇口套的壁厚不能太薄。
浇口套的长度一般应小于压射冲头的送出引程,以便涂料从压室中脱出。
②压铸模具资料压室与浇口套的内孔,在热处理后应精磨,再沿轴线方向进行研磨,其表面粗糙≤Ra0.2μm。
③分流器与形成涂料的凹腔,其凹入深度等于横浇道深度,其直径配浇口套内径,沿脱模方向有5°
当采用涂导入式直浇道时,因缩短了压室有效长度的容积,可提高压室的充满度。
(2)对于模具横浇道的要求
①模具横浇道的入口处一般应位于压室上部内径23以上部位,以免压室中金属液在重力作用下过早进入横浇道,提前开始凝固。
②横浇道的截面积从直浇道起至内浇口应逐渐减小,为出现截面扩大,则金属液流经时会出现负压,易吸入分型面上的气体,增加金属液流动中的涡流裹气。
一般出口处截面比进口处小10-30%。
③横浇道应有一定的长度和深度。
保持一定长度的目的是起稳流和导向的作用。
若深度不够,则金属液降温快,深度过深,则因冷凝过慢,既影响生产率又增加回炉料用量。
④横浇道的截面积应大于内浇口的截面积,以保证金属液入型的速度。
主横浇道的截面积应大于各分支横浇道的截面积。
⑤横浇道的底部两侧应做成圆角,以免出现压铸网早期裂纹,二侧面可做出5°
左右的斜度。
横浇道部位的表面粗糙度≤Ra0.4μm。
(3)内浇口
①金属液入型后不应立即封闭分型面,溢流槽和排气槽不宜正面冲击型芯。
金属液入型后的流向尽可能沿铸入的肋筋和散热片,由厚壁处想薄壁处填充等。
②选择内浇口位置时,尽可能使金属液流程最短。
采用多股内浇口时,要防止入型后几股金属液汇合、相互冲击,从而产生涡流包气和氧化夹杂等缺陷。
③薄壁件的内浇口厚件要适当小些,以保证必要的填充速度,内浇口的设置应便于切除,且不使铸件本体有缺损(吃肉)。
(4)溢流槽
①溢流槽要便于从铸件上去除,并尽量不损伤铸件本体。
②溢流槽上开设排气槽时,需注意溢流口的位置,避免过早阻塞排气槽,使排气槽不起作用。
③不应在同一个溢流槽上开设几个溢流口或开设一个很宽很厚的溢流口,以免金属液中的冷液、渣、气、涂料等从溢流槽中返回型腔,造成铸件缺陷。
2、铸造圆角(包括转角)铸件图上往往注明未注圆角R2等要求,我们在开制模具时切忌忽视这些未注明圆角的作用,决不可做成清角或过小的圆角。
铸造圆角可使金属液填充顺畅,使腔内气体顺序排出,并可减少应力集中,延长模具使用寿命。
(铸件也不易在该处出现裂纹或因填充不顺而出现各种缺陷)。
例标准油盘模上清角处较多,相对来说,目前兄弟油盘模开的最好,重机油盘的也较多。
3、脱模斜度在脱模方向严禁有人为造成的侧凹(往往是试模时铸件粘在模内,用不正确的方法处理时,例钻、硬凿等使局部凹入)。
4、表面粗糙度成型部位、浇注系统均应按要求认真打光,应顺着脱模方向打光。
由于金属液由压室进入浇注系统并填满型腔的整个过程仅0.01-0.2秒的时间。
为了减少金属液流动的阻力,尽可能使压力损失少,都需要流过表面的光洁度高。
同时,浇注系统部位的受热和受冲蚀的条件较恶劣,光洁度越差则模具该处越易损伤。
5、模具成型部位的硬度铝合金:
HRC46°
左右铜:
HRC38°
左右加工时,模具应尽量留有修复的余量,做尺寸的上限,避免焊接。
压铸模具组装的技术要求:
1、模具分型面与模板平面平行度的要求。
2、导柱、导套与模板垂直度的要求。
3、分型面压铸模具设计工程师上动、定模镶块平面与动定模套板高出0.1-0.05mm。
4、推板、复位杆与分型面平齐,一般推杆凹入0.1mm或根据用户要求。
5、模具上所有活动部位活动可靠,无呆滞现象pin无串动。
6、滑块定位可靠,型芯抽出时与铸件保持距离,滑块与块合模后配合部位23以上。
7、浇道粗糙度光滑,无缝。
8、合模时镶块分型面局部间隙<
0.05mm。
9、冷却水道畅通,进出口标志。
10、成型表面粗糙度Rs=0.04,无微伤。
2-17泵体模具结构图
设计总结
此模具在总体上是一个比较简单的模具设计,但是在设计中有许多细微的结构。
我在设计中使用了一模两