设计说明书论文Word文档下载推荐.docx
《设计说明书论文Word文档下载推荐.docx》由会员分享,可在线阅读,更多相关《设计说明书论文Word文档下载推荐.docx(35页珍藏版)》请在冰豆网上搜索。
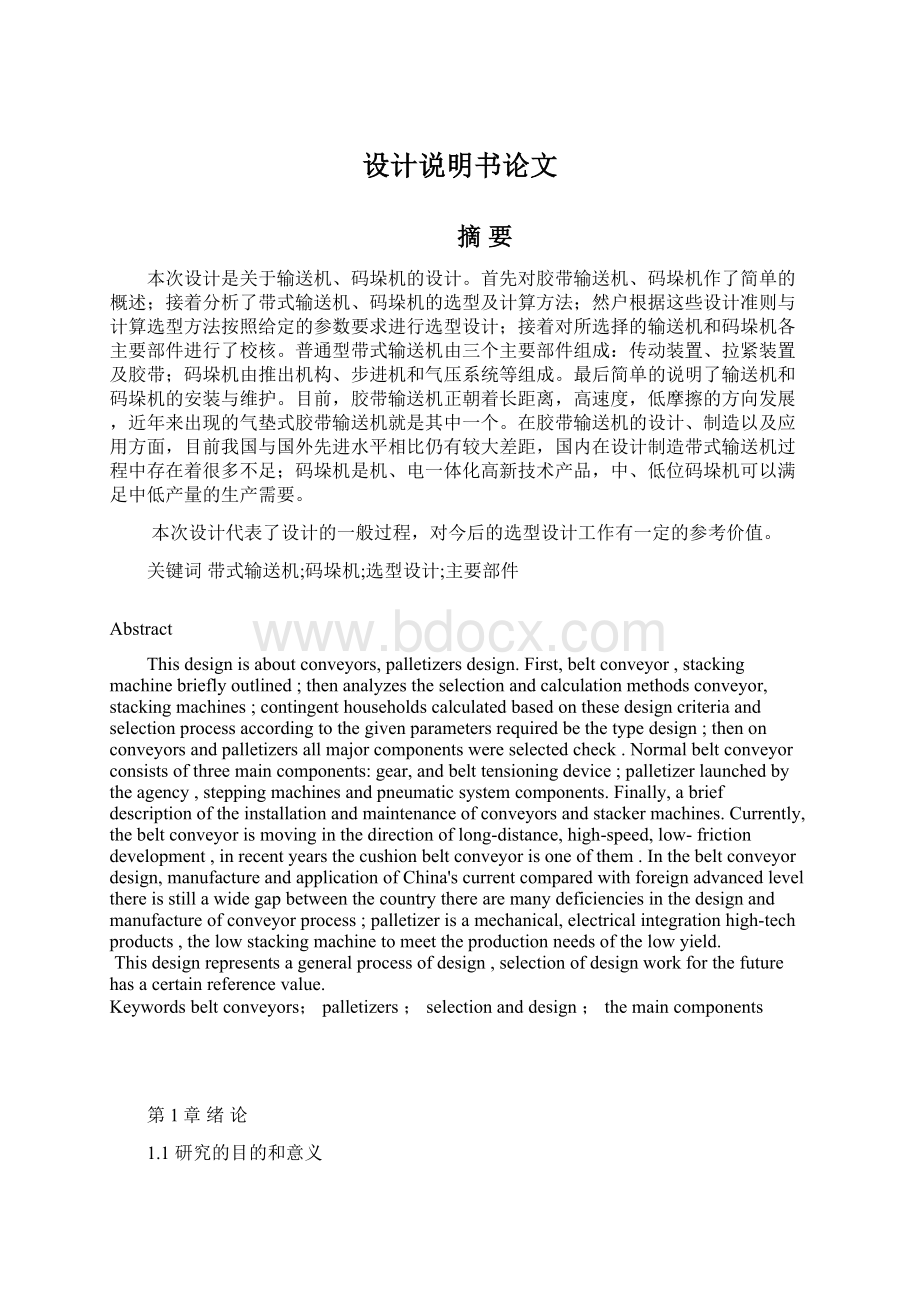
根据市场和目前技术状况的分析以及对现有技术成果的分析、消化和吸收,以经济性、实用性和可靠性等原则,制定总体设计方案,采用优化设计
的方法总体结构设计,在此基础上设计出输送机和码垛机。
1.3课题的基本内容
根基市场和目前技术状况的分析以及对自身技术成果的分析、消化、和吸收,以经济性、实用性和可靠性等原则,制定总体设计方案,采用优化设计的方法总体结构设计,在此基础上设计出输送机和码垛机。
1.4研究方案及目标
方案:
理解输送机、码垛机的工作原理,广泛收集国内外相关资料,对各种主要研究成果进行整理分析并结合老师所给技术参数设计计算出各部件的外形尺寸。
画出设计图,并对所设计的结构进行相应的校核。
目标:
设计出结构合理的输送机、码垛机结构,并对此基础上进行校核,使输送机、码垛机能接近合理结构。
1.5为完成课题所需的条件
熟练掌握设计思路;
了解并掌握校核各零件的计算公式;
能快速准确的通过网络查阅所需材料;
熟练应用CAD等制图软件及工具。
第2章带式输送机和码垛机的概述
2.1带式输送机的应用
带式输送机是连续运输机的一种,连续运输机是固定式或运移式起重运输机中主要类型之一,其运输特点是形成装载点之间的连续物料流,靠连续物料流的整体运动来完成物流从装载点到卸载点的输送。
在工业、农业、交通等各企业中,连续运输机是生产过程中组成有节奏的流水作业运输线不可缺少的组成部分。
2.2带式输送机的分类
带式输送机分类方法有多种,按运输物料的输送带结构可分为两类,一类是普通型带式输送机,这类带式输送机在输送带输送物料的过程中,上带呈槽形,下带呈平形,输送带有托辊托起,输送带外表几何形状均为平面;
另外一类是特种结构的带式输送机,各有各的输送特点。
2.3带式输送机的机构与工作原理
带式输送机由输送带、驱动装置、托辊、机架、拉紧装置和制动装置等组成。
输送带绕经驱动滚筒和改向滚筒形成环形封闭带。
上下两股输送带分别支撑在上托辊和下托辊上。
拉紧装置保证输送带正常运转所需的张紧力。
工作时,驱动滚筒通过摩擦力驱动输送带运行。
物料装在输送带上与输送带一同运动。
通常利用上股输送带运输物料,并在输送带绕过机头滚筒改变方向时卸载。
必要时,可利用专门的卸载装置在输送机中部任意点进行卸载。
2.4带式输送机的发展与现状
国外带式输送机技术的发展很快,其主要表现在2个方面:
一方面是带式输送机的功能多元化,应用范围扩大化;
另一方面是带式输送机的技术与装备有了巨大的发展,尤其是长距离,大运量,高带速等大型带式输送机已成为发展的主要方向,其核心技术是开发应用于带式输送机动态分析与监控技术,提高了带式输送机的运行性能和可靠性。
我国生产制造的皮带输送机的品种、类型较多。
在“八五”期间,带式输送机的技术水平有了很大提高,如大倾角长距离带式输送机成套设备,高产高效工作面顺槽可伸缩带式输送机等均填补了国内空白,并对带式输送机的减低关键技术及其主要元部件进行了理论研究和产品开发,研制成功了多种软件起动和制动装置以及PLC为核心的可编程电控装置,驱动系统采用调速型液力耦合器和行星齿轮减速器。
2.5码垛机的应用
可按照要求的编组方式和层数,完成对料袋、胶块、箱体等各种产品的码垛。
最优化的设计使得垛形紧密、整齐。
2.6码垛机的分类
码垛机按智能化水平分为:
机器人码垛机和机械式码垛2种。
机械式码垛机可以分为:
龙门式码垛码垛机、立柱式码垛机、机械臂式码垛机。
码垛机按照行业分为:
食品饮料行业码垛、水泥自动装车码垛机、工业品码垛机等。
2.7码垛机的工作原理
平板上工件符合栈板要求的一层工件,平板及工件向前移动直至栈板垂直面。
上方挡料杆下降,另三方定位挡杆起动夹紧,此时平板复位。
各工件下降到栈板平面,栈板平面与平板底面相距10mm,栈板下降一个工件高度。
往复上述直到栈板堆码达到设定要求。
2.8码垛机的发展与现状
我国包装机械起步较晚,解放后轻工业开发了一批专用包装设备,为饮料厂、卷烟厂、火柴厂配套,尚未形成行业。
80年代初,包装机械作为新兴的工业部门开始发展起来,经过近二十年的艰苦努力,一支从包装设备科研、设计、生产制造及教育管理的行业队伍已经形成,并初具规模,产品品种不断增加,产量迅速上升,技术水平逐年提高,作为包装机械工业在我国国民经济的崛起中正在不断发展完善。
2.9本章小结
本章主要讲述了输送机、码垛机的分类和工作原理及发展和现状,对输
送机、码垛机有了一定了解。
第3章带式输送机、码垛机的设计
3.1带式输送机设计的技术参数
参数和工作条件
(1)输送物料:
整条烟
(2)物料特性:
1)块度:
0-400mm
2)密度:
0.9kg∕m³
3)在输送带上堆积角:
p=23°
(3)工作环境:
室内、干燥
(4)输送系统及相关尺寸:
1)运距:
10m
2)倾斜角:
β=16°
3.2输送机带速的选择
输送带的带速很大程度上取决于所输送的物料的特性、所期望的输送能力和所采用的输送带的张力。
块状易碎的物料会有带速的限制。
当输送带和所输送的物料通过托辊时,较低的带速可以使易碎的物料在装料和卸料点处不会发生跳动和碎裂。
本设计的输送物料为块状易碎物料,根据所需要的输送量计算得带速为1.6m∕s。
3.3输送带宽度的计算选择
对于块状物料,输送带宽度按下式计算
(3-1)
B—输送带宽度,m;
Q—所需输送量,kg∕h;
按最大输送量Q=50kg∕h;
ρ—物料松散密度,kg∕m³
;
取ρ=0.75kg∕m³
V—输送带速度,m∕s;
取V=1.6m∕s;
C—倾角系数,由《实用机械设计手册》表13.3-14查得当输送机倾角β=16°
时,倾角系数C=0.88;
K—装载系数,一般取K=0.8-0.9,在此去K=0.85;
y—断面系数,堆积角p=23°
,由《运输机械设计选用手册》表3-15查得y=0.12;
代入数据B=0.359m
此时取标注输送带宽度B=0.4m=400mm。
3.4圆周驱动力
3.4.1计算公式
传动滚筒上所需圆周驱动力Fu为输送机所有阻力之和,可用式(3-2)计算。
Fu=FH+FN+Fs1+Fs2+Fst(3-2)
式中FH—主要阻力,N;
FN—附加阻力,N;
Fs1—特种主要阻力,N;
Fs2—特种附加阻力,N;
Fst—倾斜阻力,N。
五种阻力中,FH、FN是所有输送机都有的,其他三类阻力根据输送机侧型及附件装设情况定。
3.4.2主要阻力计算
输送机的主要阻力FH是物料及输送带移动和承载分支及回程分支托辊旋转所产生阻力的总和。
可用式(3-3)计算:
FH=fLg[qRO+qRU+(2qB+qG)cosα](3-3)
式中f—模拟摩擦系数,根据工作条件及制造安装水平决定;
L—输送机长度;
g—重力加速度,g=9.8m∕s²
qRO—承载分支托辊组每米长度旋转部分重量,kg∕m;
qRO=G1∕a0
其中G1—承载分支每组托辊旋转部分重量,kg;
a0—承载分支托辊间距,m;
托辊已经选好,已知G1=12.21kg
计算qRO=12.21∕1.2=10.18kg∕m
qRU—回程分支托辊组每米长度旋转部分重量,kg∕m;
qRU=G2∕au
其中G2—回程分支每组托辊组旋转部分重量;
au—回程分支托辊间距,m
G2—10.43kg
qRU=10.43∕3=3.48kg∕m
qG—每米长度输送物料质量,kg∕m;
qG=Im∕v=Q∕3.6v=400∕(3.6x1.6)=69.44kg∕m
qB—每米长度输送带质量,kg∕m
qB=11.5kg∕m
FH=fLg[qRO+qRU+(2qB+qG)cosα]
=0.022x400x9.8x[10.18+3.48+(2x11.5+69.44)xcos0°
]
=9150.06N
f运行阻力系数,f值应根据表选取。
取f=0.022.
表3-1阻力系数f
输送机工况
f
工作条件和设备良好、带速低、物料内摩擦较小
0.02-0.023
工作条件和设备一般、带速较高、物料内摩擦较大
0.025-0.030
工作条件恶劣、多尘低温、湿度大、设备质量较差
0.035-0.045
3.4.3倾斜阻力计算
倾斜阻力按下式计算:
Fst=qGxgxH
式中H—输送机受料点与卸料点间的高差,m;
输送机向上提升时H为正,反之为负。
Fst=qGxgxH=0
由式Fu=cFH+FN+Fs1+Fs2+Fst(3-4)
Fu=1.09x9150.06+0+2100+0=12073.57N
C—与输送机长度有关的系数,大于80m时,按式计算;
C=(L+L0)∕L
L0—附加长度,一般在70m到100m之间;
C—系数,不小于1.02
表3-2系数C(装料系数在0.7-1.1范围内)
L
80
100
150
200
300
400
500
600
C
1.92
1.78
1.58
1.45
1.31
1.25
1.20
1.17
700
800
900
1000
1500
2000
2500
5000
1.14
1.12
1.10
1.09
1.06
1.05
1.04
1.03
3.5传动功率计算
3.5.1传动轴功率(PA)计算
传动滚筒轴功率(PA)按式(3-5)计算:
PA=Fu·
v∕1000(3-5)
3.5.2电动机功率计算
电动机功率Pm,按式(3-6)计算;
发电工况:
Pm=PA∕ηη′η″(3-6)
发电工况(下运):
Pm=PAη∕η′η″(3-7)
η=η1η2
式中η—传动效率,一般在0.85-0.95之间选取;
η1—联轴器效率;
每个机械式联轴器效率:
η1=0.98;
液力耦合器:
η1=0.96;
η2—减速器传动效率,按每级齿轮传动效率,为0.98计算;
二级减速机η2=0.98x0.98=0.96
三级减速机η2=0.98x0.98x0.98=0.94
η’—电压降系数,一般取0.90-0.95;
η”—多机驱动功率不平衡系数,一般取0.90-0.95,单机驱动时η”=1。
根据计算出的Pm值,查电动机型谱,按就大不就小原则选定电动机功率。
由式(3-5)PA=(12073.57x1.6)∕1000=19320w
由式(3-6)Pm=19320∕(0.94x0.95x1)=21634.94w
选电动机型号为Y200L-4.30KW
3.6输送带张力计算
输送带张力在整个长度上是变化的,影响因素很多,为保证输送机上正常运行,输送带张力必须满足以下两个条件:
(1)在任何负载情况下,作用在输送带上的张力应使得全部传动滚筒上的圆周力是通过摩擦传递到输送带上,而输送带与滚筒间应保证不打滑。
(2)作用在输送带上的张力应足够大,使输送带在两组托辊间的垂度小于一定值。
3.6.1输送带不打滑条件校核
圆周驱动力Fu通过摩擦传递到输送带上(见图3-1)
图3-1作用于输送带的张力
为保证输送带工作时不打滑,需在回程带上保持最小张力应F2min计算:
F2min≥Fumax
式中:
输送机满载启动时或制动时出现的最大圆周驱动力,启动时Fumax=KAFu,启动系数KA=1.3-1.7,;
对惯性小、起制动平稳的输送机可取较小值;
否则,就应取最大值。
μ—传动滚筒与输送带间的摩擦系数,见表3-3
表3-3传动滚筒与输送带间的摩擦系数μ
工作条件
μ
光面滚筒
胶面滚筒
干态运行
0.35-0.40
0.40-0.45
清洁潮湿运行
0.10
0.35
污浊的湿态运行
0.05-0.10
0.25-0.30
取KA=1.5,由式Fumax=1.5x12073.57=18110.355N
对常用:
1∕
﹣1=0.67
该设计取μ=0.25;
φ=210°
。
F2min≥Fumax*1∕(
﹣1)=18110.355x0.67=12133.94N
3.6.2输送带下垂度校核
为了限制输送带在两组托辊间的下垂度,作用在输送带上任意一点的最小张力Fmin,需按式(3-8)和(3-9)进行验算。
承载分支:
F承min≥a0(qB+qG)g∕8(
)adm(3-8)
回程分支:
F回min≥aD*qB*g∕8(
)adm(3-9)
式中(
)adm—允许最大垂度,一般≤0.01;
a0—承载上托辊间距(最小张力处);
aD—回程下托辊间距(最小张力处);
取(
)adm=0.01得:
F承min=1.2(11.5+69.44)x9.8∕(8*0.01)=11898.18N
F回min=3x11.5x9.8∕(8*0.01)=4226.25N
所以按垂度条件应满足F回min=F回min≥11898.18N
3.6.3各特性点张力计算
为了确定输送带作用于各改向滚筒的合张力,拉紧装置拉紧力和凸凹弧起始点张力等特性点张力,需逐点张力计算法,进行各特性点张力计算。
图3-2张力分布点图
3.6.3.1运行阻力的计算:
由分离点起,依次将特殊点设为1、2、3、4、5、6,如图3-2所示。
计算运行阻力时,首先要确定输送带的种类和型号。
在前面我们已经选好了输送带,680S型输送带,纵向拉伸强度750N∕mm;
带厚8.5mm;
输送带质量11.2kg∕m。
1)承载段运行阻力,由式(3-10):
Fz=[(q+q0+qz)Lwzcosβ+(q+q0)Lsinβ]g(3-10)
=[(69.44+11.5+10.18)*400*0.04*1]x9.8
14287.616N
2)回空段运行阻力,由式(3-11):
Fk=[(q0+qk)Lwkcosβ﹣(qk+q0)Lsinβ]g(3-11)
F45=[(11.5+3.48)*298*0.035*1]*9.8
=1531.17N
F23=[(11.5+3.48)*2*0.035*1]*9.8
=10.28N
3)最小张力点:
由以上计算可知,3点为最小张力点
3.6.3.2输送带上各点张力的计算
1)由悬垂度条件确定5点的张力
承载段最小张力应满足
F承min≥1.2(11.5+69.44)*9.8∕(8*0.01)=11898.18N
2)由逐点计算法计算各点的张力
因为S6=11898.18N,根据表选CF=1.05
故有S5=S6∕CF=11331.6N
S4=S5﹣S45=9800.43N
S3=S4∕CF=9333.74N
S2=S3﹣S23=9323.46N
S1=S6+Fz=26185.796N
SY=S1=26185.796N
③用摩擦条件来验算传动滚筒分离点与相遇点张力的关系
滚筒为包胶滚筒,围包角为210°
选摩擦系数μ=0.25。
并取摩擦力系
数备用系数n=1.2.
由式(3-12)可算出允许SY的最大值为:
SYmax=S1(1+
)(3-12)
=26185.796*[1+(e0.25*210∕180﹣1)∕1.2]
=33386.89≥SY
故摩擦条件满足。
3.6.4传动滚筒、改向滚筒合张力计算
根据计算出的各特性点张力,计算各滚筒合张力。
头部180°
改向滚筒的合张力:
F改1=S1+S2=26185.796+9323.46=35509.256N
尾部180°
改向滚筒合张力:
F改2=S5+S6=11331.6+11898.18=23229.78N
3.7传动滚筒最大扭矩计算
单驱动时,传动滚筒的最大扭矩Mmax按式(3-13)计算:
Mmax=
(3-13)
式中D—传动滚筒的直径,mm;
初选传动滚筒直径为80mm,则传动滚筒的最大扭矩为:
Mmax=12.07*0.8∕2=4.83KN∕m
3.8拉紧力计算
拉紧装置拉紧力F0按式(3-14)计算
F0=Si+Si+1(3-14)
式中Si—拉紧滚筒趋入点张力,N;
Si+1—拉紧滚筒奔离点张力,N。
由式(3-14)
F0=S3+S4=9333.74+9800.43=19134.13KN
3.9输送带强度校核计算
纵向拉伸强度Gx按式(3-15)计算
Gx≥
(3-15)
式中n1—静安全系数,一般n1=-10。
运行条件好,倾角好,强度低取小值;
反之,取大值。
输送带的最大张力Fmax=26185.796N
n1选为7,由式(3-15)
Gx≥26185.796*7∕1000=183.30N∕mm
可选输送带为680S即满足要求。
3.10驱动装置的选用与设计
带式输送机的负载时一种典型的恒转矩负载,而且不可避免地要带负荷启动和制动。
电动机的启动特性与负载的启动要求不相适应在带式输送机上比较输出,一方面为了保证必要的启动力矩,电动机启动时的电流要比额定的运行的电流大6-7倍,要保证电动机不因电流的冲击过热而烧坏,电网不因大电流使电压过分降低,这就要求电动机的启动要尽量快,即提高转子的加速度,使启动过程不超过3-5s。
驱动装置是整个皮带输送机的动力来源,它由电动机、耦合器、减速器、联轴器、传动滚筒组成。
驱动滚筒由一台或两台电机通过各自的联轴器、减速器和链式联轴器传递转矩给传动滚筒。
减速器有二级、三级及多级齿轮减速器,第一级为直齿圆锥齿轮减速传动,第二、三级为斜齿圆柱齿轮减速传动,联接电机和减速器的联轴器有两种,一是弹性联轴器,一种是液力耦合器。
为此,减速器的锥齿轮也有两种:
用弹性联轴器时,用第一种锥齿轮,轴头为平键连接;
用液力耦合器时,用第二种锥齿轮,轴头为花键齿轮连接。
传动滚筒采用焊接结构,主轴承采用调心轴承,传动滚筒的机架与电机、减速器的机架均安装在固定大底座上面,电动机可安装在机头任一侧。
3.10.1电机的选用
电动机额定转速根据生产机械的要求而选定,一般情况下电动机的转速
不低500r∕min,因为功率一定时,电动机的转速低,其尺寸越大,价格越贵,而效率低。
若电机的转速高,则极对数少,尺寸和重量小,价格也低。
本设计皮带机所采用的电动机的总功率为21.6kw,所以需选用功率为30kw的电动机。
拟采用Y200L-4型电动机,该型电