氨压缩机工段操作规程Word下载.docx
《氨压缩机工段操作规程Word下载.docx》由会员分享,可在线阅读,更多相关《氨压缩机工段操作规程Word下载.docx(57页珍藏版)》请在冰豆网上搜索。
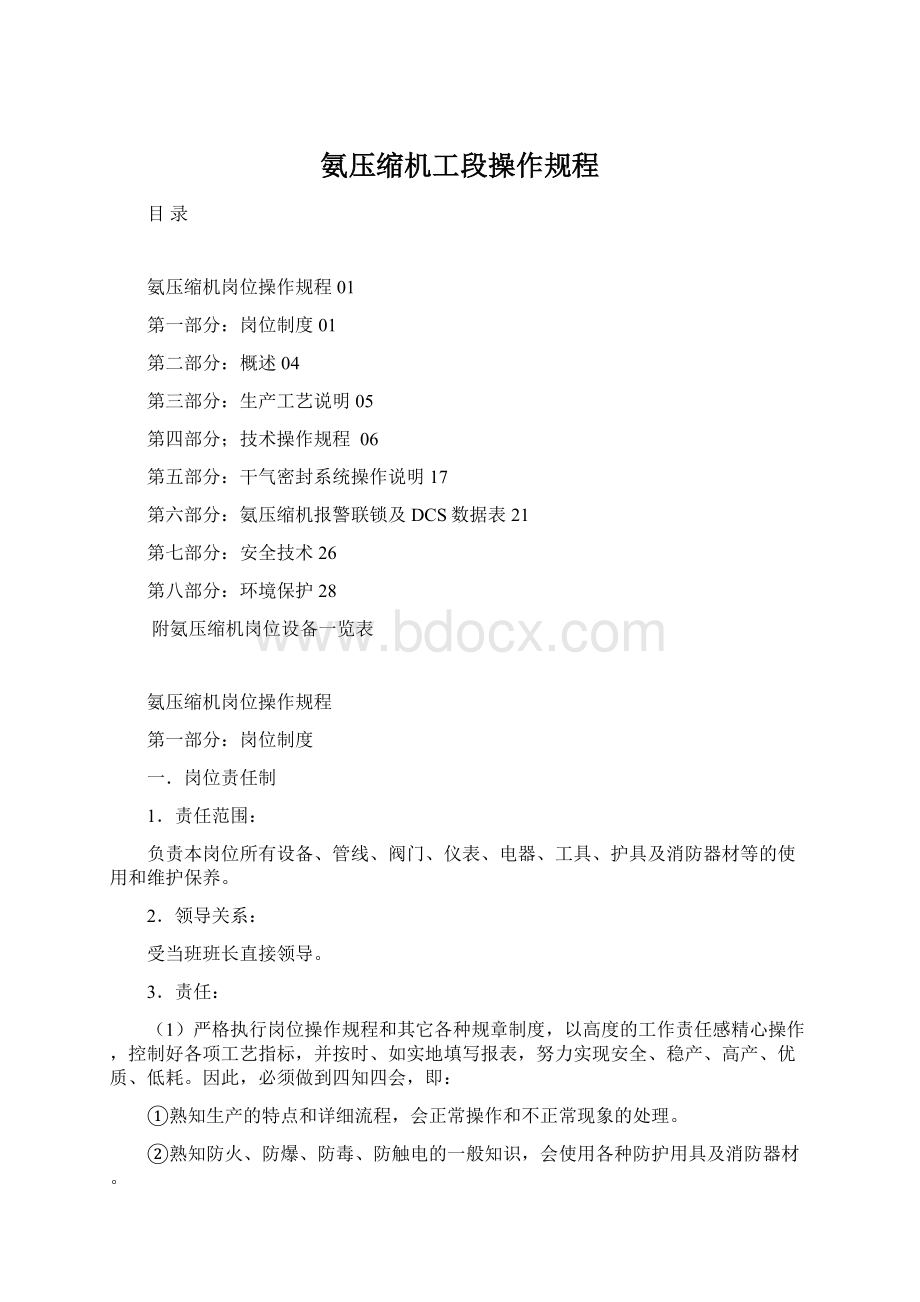
(6)认真总结经验,努力掌握先进技术,不断掌握新工艺操作和设备结构,大胆提出技改、技措项目,挖掘生产潜力。
(7)负责做好设备检修交出前的准备工作和安全措施。
检修过程中积极做好配合和监护工作,修复后认真做好质量验收工作。
(8)每班必须进行清扫,保持本岗位环境及所属设备、管道、阀门等清洁卫生。
4.权利
(1)对班长的指示如觉不妥,有权提出询问和建议。
若其指示有明显违反操作规程或安全规程,并会酿成事故时,有权拒绝执行,并迅速越级汇报。
(2)发生紧急事故,有权先处理后汇报。
(3)对进入本岗位的外来人员有权询问或查看其证明,若手续不符时,可禁止其进入岗位。
(4)有权对本岗位的操作规程提出修改意见。
在未经领导批准前不得试行或更改工艺指标。
二.班组交接制度
1.接班人员应提前20分钟到岗,并按巡检路线进行巡回检查,了解工艺生产情况,工艺指标执行情况,工器具及消防、防护器具的保管使用情况和安全生产存在的问题等。
2.参加班前会。
班前会由班长主持,听取班组成员汇报检查结果;
由交班班长介绍上一班的工作情况,存在的问题以及领导下达的指示;
当班班长要检查本班出勤人员和着装情况,布置本班工作和人员安排,落实领导指示,并进行班前教育。
3.交班者应将现场卫生,设备卫生和室内卫生打扫干净。
4.交班者应主动为下班生产创造有利条件,一般情况下交班前三十分钟不准随意改变工艺操作条件。
5.交班者应主动积极地向接班者介绍本班生产情况,存在问题及注意事项,耐心解答接班者的提问。
对于不正常现象的处理要详细介绍其处理过程和防范措施。
6.交班前应认真填写交班日志,将本班经验,存在问题,上级指示,如实详细记录。
对接班者提出的问题要给予正确处理。
必须遵循交班高姿态,接班高风格的原则,不准故意制造事端。
7.在事故或不正常情况下,应主动推迟交班,并积极组织人员进行处理。
待恢复正常后,再进行交班。
不能尽快处理的事故,等事故处理告一段落后,经双方班长协商,同意后再进行交接班。
8.交班期间的生产由交班者负责,接班者未能按时接班时,上班应继续坚守岗位并及时汇报班长,以便妥善安排。
9.交班完毕后,由班长组织召开班后会,总结经验,找出差距。
10.工具、仪器、护具、消防器材损坏或缺少,应查明原因并做好记录。
11.接班人员在交接班日志上签名,即为接班完毕。
接班后一切工作由接班者负责。
三.设备维护保养制度
1.认真贯彻“维护为主、检修为辅”的方针,严格遵守操作法,努力维持工艺条件正常平稳,运行设备做到“三不超”(不超温、不超压、不超负荷)。
2.操作人员对所使用设备,通过岗位练兵和技术比武,做到“四懂”、“三会”(懂结构、懂原理、懂性能、懂用途;
会维护保养、会操作、会排除故障),新工人须经考试合格后持证上岗。
3.认真执行润滑油管理制度,严格实行“五定”、“三级过滤”(五定:
定质、定量、定时、定点、定期;
三级过滤:
油桶、油壶、注油点),保证油质及用具清洁,各等级的润滑油严禁混用,保证传动设备供有足够的润滑油。
4.设备维护必须做到“三勤一定”(勤检查、勤擦拭、勤保养,定时准确记录),下班之前一小时打扫岗位卫生,保持岗位清洁,尽量做到无灰尘、无油污,消除跑、冒、滴、漏。
5.严格执行巡回检查制度,运用听、摸、察、看、比等操作方法仔细检查,及时消除设备缺陷,发现问题及时处理或汇报。
6.加减负荷应缓慢,非紧急情况下不得带负荷停车,不得带病运转,不冒险生产;
开停车要严防压力憋高,气体倒流,高压流体冲入低压设备、管道。
7.气温低于5℃时应注意防冻,冬季停用设备应将积水放尽或保持流动;
停用蒸汽应将冷凝水放尽;
微开水管及蒸汽管导淋。
8.按规定做好设备切换,备用和停用设备要定期盘车检查、试验,保证随时可以投用。
对不正常设备、管道、阀门、仪表信号及安全装置,要及时修理或更换,设备中修时要校验仪表和安全阀。
9.认真填写设备运行记录,缺陷记录和交接记录。
四.巡回检查制度
1.按车间制定的岗位巡回检查路线和检查内容,作认真详细的检查。
及时了解各设备和阀门及工艺压力、液位的运行情况,并按时倒牌。
2.主控岗位应经常翻动画面,随时掌握各项工艺参数的变化情况和各个调节阀的运作情况,及时与现场仪表对照,细心调节。
3.巡检过程中要通过听、看、嗅、摸及时发现问题,并积极处理,若处理不了,要及时向班长或主操汇报,按班长或主操的意见进行处理,并将系统问题及处理过程做好记录。
4.认真检查现场消防、防护器材的保管情况,确保完好备用。
5.对生产中的薄弱环节要加强检查,密切注意其发展情况。
遇有不正常情况应及时联系处理。
6.正常生产时,现场人员对设备每小时检查一次。
特殊情况下,应增加巡检频率随时检查。
7.巡检人员要认真检查转动设备的振动、声音是否正常,按时加油。
8.真实、按时填写记录报表。
五.质量检查制度
1.车间、班组要要对质量进行全面管理,坚持质量第一的原则,严格控制各项工艺指标,保证工艺指标合格率达98%以上。
遵守规章制度,确保产品质量合格。
2.明确各岗位的质量指标,车间随时掌握各岗位质量指标的完成情况。
逐月统计,并将其列入班组考核内容之中。
3.经常对照室内与现场指标,确保各仪表调节灵敏、好用、指示准确。
对本岗位输出的产品、半成品要经常进行自检,发现问题及时调节处理,严格执行工艺指标,确保产品质量。
4.对本岗位的设备、仪表、管线、阀门等应负交出检修和验收质量的责任。
5.按分析频率,检查各项分析数据是否在规定的指标之内;
发现问题应及时汇报,并联系处理。
6.对质量事故要以“四不放过”的原则,认真分析原因,不得隐瞒,通过分析吸取教训,采取措施,避免类似事故的再次发生。
7.熟练掌握本岗位操作规程,精心操作,加强研究,逐步提高产品质量。
8.各岗位主操对本岗位的产品质量负责,班长对本班的产品质量负管理责任,车间管理人员对全车间的产品质量负管理责任。
概述
氨压缩机是由沈阳鼓风机集团有限公司制造。
主要由MCL706与2MCL707离心压缩机,汽轮机,气体冷却器,气体分离器,省功器,液氨储罐,空气分离器及润滑油站等组成。
压缩机由三段十三级组成,轴端采用干气密封。
汽轮机NKS40∕36∕20由杭州汽轮机有限公司制造,压缩机与汽轮机之间用膜片联轴器联接,整个机组由同一润滑油站提供润滑油。
使用46#汽轮机油。
一、压缩机
MCL706+2MCL707型离心压缩机是一种多级离心压缩机,分低压缸MCL706和高压缸2MCL707。
MCL706为一段压缩,共六级叶轮,顺排布置,叶轮最大名义直径为700㎜。
2MCL707为二段压缩,共七级叶轮,背靠背布置,叶轮最大名义直径为700㎜。
气体进入一段MCL706缸体内经过六级压缩后出压缩机,冷却后与省功器补气混合再进入2MCL707,在二段经过三级叶轮压缩后出压缩机,冷却后进入三段,再经四级叶轮压缩至出口状态。
设计数据:
名称
内容
单位
一段
加气段
二段
三段
介质
氨
流量
31453
6093
37433
37398
Nm3/h
入口压力
0.073
0.368
0.361
0.698
MPa.A
出口压力
0.386
0.709
1.6
入口温度
-36
-4
34
42
℃
出口温度
105.2
103.4
130.6
所需功率
2072.5
1264.5
1630
KW
工作转速
7770
r/min
最高连续转速
8159
跳闸转速
8975
临界转速
3882
二、汽轮机:
编号:
T7243
型号:
NKS40/36/20,该透平为全凝式,透平就地安装盘作为开车和正常监视用,径向轴承为可倾瓦,推力轴承为米切尔。
转子轴承跨距
1780
㎜
润滑油用油量
8
m3∕h
调节油用量
5
正常进汽压力
3.7
MPaA
正常进汽温度
435
正常排汽压力
0.011
正常排汽温度
49.4
正常进汽流量
25.11
t/h
正常功率
4967
Kw
正常转速
最大连续转速
8811
冷却水进口温度
30
凝汽器冷却水量
1890
凝汽器冷却面积
750
㎡
主抽气器汽耗量
101
㎏∕h
启动抽气器汽耗量
173
主抽气器抽干空气量
8.2
启动抽气器抽干空气量
102
生产工艺说明
一.生产工艺原理
高压蒸汽在汽轮机内主要进行两次能量的转化,使汽轮机对外做功。
第一次能量转换是热能转化为动能:
是高压蒸汽经过喷嘴(静叶栅)后压力降低、产生高速汽流而实现的。
第二次能量转换是动能转化为机械能:
是高速蒸汽的冲击力施加给动叶片使转子高速旋转,传递力矩,输出机械功而实现的。
在蒸汽透平的驱动下,离心式压缩机的叶轮随轴高速旋转,叶片间的介质气体也随叶轮旋转而获得离心力,高速气体被甩到叶轮外的扩压器中去,使气体的流动速度能转化为压力能,经过扩压器后的介质气体经弯道、回流器进入下一级继续压缩。
压力提高的同时,介质气体温度也要升高,设置段间冷却器来降低压缩气体的温度,尽量减少压缩功。
二.工艺流程
1.工艺气系统
自低温甲醇洗来的气氨进入1#氨分离器VⅡ2301,与来自温度自调TV22310,防喘阀FV22310,以及中间储氨罐VⅡ2303的气氨,液氨混合后,分离夹带的液氨,进入到压缩机一段入口(DN800mm,31453Nm3/h、0.0736MPaA、-36℃),经过一段六级压缩后(DN500mm,0.386MPaA、105.2℃)进入低压气体冷却器EⅡ2301冷却,与来自2#氨分离器VⅡ2302的气氨混合(DN500mm,37433Nm3/h、0.361MPaA、34℃),进入二段经过三级叶轮压缩后出压缩机,进入高压气体冷却器EⅡ2302冷却后(DN400mm,37398Nm3/h、0.698MPaA、42℃)进入三段经四级叶轮压缩后气体压缩至出口状态(DN350mm,1.661MPaA、130.6℃)。
氨压缩机出口气体经防喘冷却器EⅡ2303冷却后,一小部分经防喘调节阀FV22310和FV22320回到1#氨分离器VⅡ2301和2#氨分离器VⅡ2302循环,大部分经氨冷凝器EⅡ2304A,B后成为液氨回到液氨储槽VⅡ2304,液氨储槽VⅡ2304内液氨经自调阀LV22337减压后进入省功器VⅡ2305,省功器内液氨经总管送低温甲醇洗系统。
液氨在甲醇洗系统经过1#,2#,3#甲醇氨冷器和甲醇再生塔回流氨冷器后成为气氨,并由气氨总管回到1#氨分离器VⅡ2301。
为调节一段,二段进口温度,从液氨储槽引出液氨经自调阀TV22310,TV22320到1#氨分离器VⅡ2301和2#氨分离器VⅡ2302进入系统循环。
为分离进入系统中的空气,从氨冷凝器EⅡ2304A,B引出一股气氨,在空气分离器EⅡ2305管程冷却,液氨从空气分离器EⅡ2305底部回到液氨储槽VⅡ2304,顶部不凝气体放空。
空气分离器EⅡ2305冷源来自液氨储槽VⅡ2304,液氨在空气分离器EⅡ2305壳程吸热气化后,回到中间储氨罐VⅡ2303。
1#氨分离器VⅡ2301和2#氨分离器VⅡ2302分离出的液氨回到中间储氨罐VⅡ2303,中间储氨罐VⅡ2303液氨经过液氨泵PⅡ2301加压后进入液氨储槽VⅡ2304。
中间储氨罐VⅡ2303内气氨经过1#氨分离器VⅡ2301回到系统。
省功器VⅡ2305内气氨经过2#氨分离器VⅡ2302回到系统。
2.蒸汽及冷凝液系统
压力为3.7MPa,温度为435℃的中压蒸汽经速关阀、调速阀后进入汽轮机内膨胀做功,做功后的蒸汽(0.011MPaA)排入凝汽器,在凝汽器中被冷凝为水并形成一定真空度,冷凝液用冷凝液泵送出界区。
为了维持凝汽器的真空,设有蒸汽抽气器,抽出其中不凝气。
抽气器动力蒸汽为3.7MPa中压蒸汽,经冷凝后回收到凝汽器内。
3.油系统
贮存在油箱中的汽轮机油,经油泵加压后采用自力式调节阀PCV22341调节油压至1.05MPa(G),经油冷却器(出口油温45±
2℃)、油过滤器后,一路送往汽轮机调节机构作调速液压油;
另一路经调节阀PCV22343将压力控制到0.28MPa(G),送往各个轴承作润滑用,各路回油汇合后返回油箱。
另外,还设置了由事故发电机驱动的事故油泵,以确保全厂断电时机组各轴承所需润滑油的供给。
为保证事故油泵启动前或特殊情况下机组停机后惰走期间供油,还设置了高位油箱,正常运转中高位油箱注满油,并保持少量溢流,一旦发生意外,可通过位差向机组各轴承提供短时间润滑油,保证机组惰走期间各轴承的润滑。
第四部分:
技术操作规程
一.岗位任务
来自低温甲醇洗四个甲醇氨冷器的气氨经氨压缩机压缩后,在氨冷凝器中冷凝成液氨,液氨收集后送回低温甲醇洗氨冷器蒸发吸收热量,从而达到降低循环甲醇温度的目的。
二.管辖范围
1.工艺气系统
①.自低温甲醇洗来的气氨进入分离器起。
②.自液氨送出省功器止。
2.油系统
3.蒸汽系统
从中压蒸汽管网通往汽轮机的隔离阀起。
4.冷凝液系统
冷凝液管线上自调阀以内的管线及设备。
5.冷却水系统
进入系统的各条循环水管线。
6.干气密封系统
7.机组所属主要设备
汽轮机:
压缩机:
MCL706+2MCL707
油站:
油箱,主、辅油泵,事故油泵,油冷却器,油过滤器,高位油箱,蓄能器。
三.操作规程
(一)开车
A.原始开车或大修后开车
1.开车前准备
(1)机组安装或大修完毕,各联轴器接好,护罩安装好。
(2)油系统清洗完毕,符合清洁要求。
如果具备条件,油箱通入密封氮气,保持微正压。
(3)所有仪表安装、检修完毕,转速控制系统ITCC组态完毕。
(4)转速控制系统ITCC、轴振动及轴位移测量二次仪表、电液转换器供电正常。
(5)水、电、仪表空气供应正常,蒸汽管道吹扫符合要求,低温甲醇洗建立溶液循环。
(6)关闭压缩机、汽轮机缸内导淋阀,关闭辅助设备及工艺管道上导淋阀。
(7)汽轮机盘车器经调试好用;
(8)汽轮机抽真空系统和凝结水系统具备投用条件;
(9)管道支、吊架安装完毕,合格;
(10)汽轮机本体及所属蒸汽管道保温合格,结束;
(11)机组基础二次灌浆合格;
(12)开车现场清洁无杂物,标识清楚,消防器材齐全,消防通道畅通,现场照明合格;
(13)开车用工器具(扳手、手电、听棒、测温仪、测振仪等)齐全,通讯器材(电话、对讲机等)齐备;
开车用资料(操作报表、试车方案、操作法、流程图等)齐全;
(14)开车组织机构完善,责任分工明确;
(15)检查应开、关阀门
应开阀门:
1防喘振阀FCV22310、FCV22320;
2各调节阀前、后切断阀;
3凝汽器、氨冷凝器,低压气体冷却器,高压气体冷却器,防喘冷却器循环水进出口阀。
注意先开出口阀,后开进口阀;
(开进出口阀后要开设备水侧排气阀排气,见水后关闭排气阀。
)
4主、辅冷凝液泵进口阀、排气阀、辅泵出口阀。
应关阀门:
1气氨进口阀HV22310及液氨送出切断阀。
2压缩机放空阀HV22331;
3各调节阀旁路阀;
4油冷却器循环水进口阀;
5中压蒸汽管线上的隔离阀、速关阀;
抽气、汽封用蒸汽阀;
6抽空气阀;
7冷凝液排污及回收阀;
8热井液位调节阀
9热井软水补充阀。
10油系统各阀门开关情况见油系统开车部分。
2.油系统开车及各项试验
(1)油系统开车准备
1油系统运行前十分钟向后置密封通0.4MPa隔离气;
2油箱充油到高限液位1806㎜;
(油箱低限液位1256㎜)
3油温控制在45±
2℃之间(油冷却器出口);
4检查油箱是否送密封氮气,如未送密封氮气送密封氮气,保持微正压即可;
5蓄能器充氮气至0.45~0.5MPa;
6使油冷却器A处于运行,油冷却器B处于备用位置;
7使油过滤器A处于运行,油过滤器B处于备用位置;
8检查应开、关阀门
应开阀门:
a.主润滑油泵进、出口阀,辅助润滑油泵进、出口阀;
b.各调节阀前后截止阀;
c.润滑油泵出口压力调节阀PCV22341及前后截止阀;
d.润滑油总管压力调节阀PCV22343及前后截止阀;
e.各轴承进油阀;
f.油冷却器A/B排气阀,进油管线上连通阀,油冷却器A/B循环水出口阀;
油过滤器A/B进油管线上连通阀,油过滤器A/B排气阀。
a.油系统各调节阀旁路阀;
b.各设备上导淋阀、蓄能器充油阀。
(2)润滑油系统建立
①投用干气密封隔离气;
②手动盘主、辅润滑油泵应无卡涩;
③启动主油泵,待出口压力正常后,利用回路调节阀(PCV22341)调节油泵出口总管压力为1.05MPa;
④向油冷却器A、油过滤器A充油排气;
⑤打开并调整PCV22343,使润滑油总管压力稳定在0.28MPa;
⑥调整各轴承进油压力,支撑轴承进油管压力为0.09-0.13MPa,推力轴承进油管压力为0.025-0.13MPa,并观察轴承回油确保油正在流动。
7缓慢打开蓄能器充油阀;
8打开高位油箱进油管线三阀组中的截止阀,向高位油箱充油,观察回油管视镜,有回油后关充油阀;
正常工作期间,始终有少量的油经三阀组中的孔板进入高位油箱,以维持箱内油温。
9视情况开油冷却器A的循环水进口阀,控制油温在45℃左右。
(3)控制油压力低报警启辅泵及压力低低联锁跳车试验
1联锁解除或旁路,停车电磁阀复位,开启速关阀;
2确认润滑油泵A运行,润滑油泵B处于联锁状态,逐渐开大PCV22341旁路阀,观察控制油压力指示PG22354,确认当压力降至0.6MPa时,控制室报警同时B泵自启动;
3继续开大PCV22341的旁路阀,当压力PG22354降至0.38MPa时,联锁跳车,速关阀关闭。
4随后逐渐关PCV22341的旁路阀,待压力恢复正常后,停B泵。
(4)润滑油总管压力低辅泵自启动及压力低低联锁跳车试验
1各联锁解除或旁路,停车电磁阀复位,开启速关阀;
2逐渐关小PCV22343后的截止阀,观察润滑油总管压力PG22345,确认当压力低于0.15MPa时报警并启动辅泵,低于0.1MPa时联锁跳车,速关阀关闭;
3逐渐开大PCV22343后截止阀,使压力恢复正常。
(5)分别进行现场盘、ITCC调速器面板、中控室紧急停车试验;
(6)进行ITCC调速器--调节汽阀升程调试。
(7)事故油泵自启动联锁试验
事故油泵选自动,现场及DCS紧停按钮复位,主油泵运行,润滑油压力正常。
联系电气人员从配电房中把主、辅油泵进线闸拉下。
主油泵断电停车,事故油泵启动。
确认后,通知电气人员给主、辅油泵送电。
启动主油泵,辅油泵处备用状态,恢复油系统正常,停事故油泵。
3.压缩机缸内氮气置换
(1)现场启动盘车油泵、盘车电磁阀,对机组盘车;
(2)在压缩机充气前给主密封供中压氮气(2.5MPa),投一级密封气。
(3)系统采用憋压法进行置换
(4)关闭系统所有的放空阀和导淋阀。
(5)打开系统所有的联通阀。
打开LV20231、LV20241、LV20242、LV20362、LV22337、LV22320的切断阀及付线阀。
打开防喘振阀FV22310,FV22320的切断阀及付线阀。
打开各切断阀,使系统全部联通。
(6)打开充氮阀,充压至0.4MPa从导淋和各放空处放空,如此进行多次,取样分析氧气含量在0.5%以下为合格。
置换结束后系统保压0.3MPa。
4.缸内气氨充压
卸去系统氮气压力,稍开省功器去液氨总管切断阀,液氨节流膨胀后成气氨,系统充压至0.4MPa从火炬放空处放空。
如此多次分析氨含量大于90%为合格。
置换结束后系统保压0.3MPa。
入口阀HV22310微开。
5.中压蒸汽暖管及辅助设备投运
(1)中压蒸汽暖管
1微开中压蒸汽隔离阀前的导淋阀;
2微开中压蒸汽隔离阀后的导淋阀及其旁路阀,控制压力在0.2-0.3Mpa,升温速率为5-10℃/min,暖管30min,对其至速关阀间的管道进行低压暖管;
3当蒸汽管管壁温度升到低压蒸汽的饱和温度时(>120℃),可以升压暖管;
缓慢开大旁路阀,使蒸汽压力逐渐提高,可以按0.1MPa/min的速率提升管内压力,控制管道升温速率为5℃/min,直至旁路阀全开;
4缓慢打开隔离阀,关旁路阀;
5注意加强疏水,避免产生水击,同时注意检查速关阀的气密性,以防止蒸汽漏入汽轮机缸内。
(2)投用冷凝水系统
1确认主、辅冷凝液泵进口阀、排气阀开;
主泵出口阀关,辅泵出口阀开;
2热井液位调节阀LICA22350去锅炉阀关,回流至热井阀开。
3开脱盐水补充阀给热井补水;
4对主、辅冷凝液泵盘车应无卡涩,启动主泵,压力稳定后开出口阀,使脱盐水回流至热井,将辅泵置‘自动’备用状态;
5抽气冷却器开封头上排气阀排气。
6补充脱盐水使热井液位上升,确认当LICA22350上涨至高限报警值时,辅泵自启动。
关脱盐水补充阀,将LICA22350设定在50%后投自动;
7降低热井液位,当液位降至低限报警值时,控制室报警;
8用同样方法对另一台泵进行试验,两泵互为备用。
(3)投汽封调节系统
1打开隔离阀引轴封汽至调节阀前,暖管5--10min,注意打开导淋疏水。
2稍开调节阀的旁路阀及前、后切断阀,确认调节阀工作正常后,全关其旁路阀,调节阀调节压力至0.108MPa(A),观察