轧辊基本知识Word格式.docx
《轧辊基本知识Word格式.docx》由会员分享,可在线阅读,更多相关《轧辊基本知识Word格式.docx(28页珍藏版)》请在冰豆网上搜索。
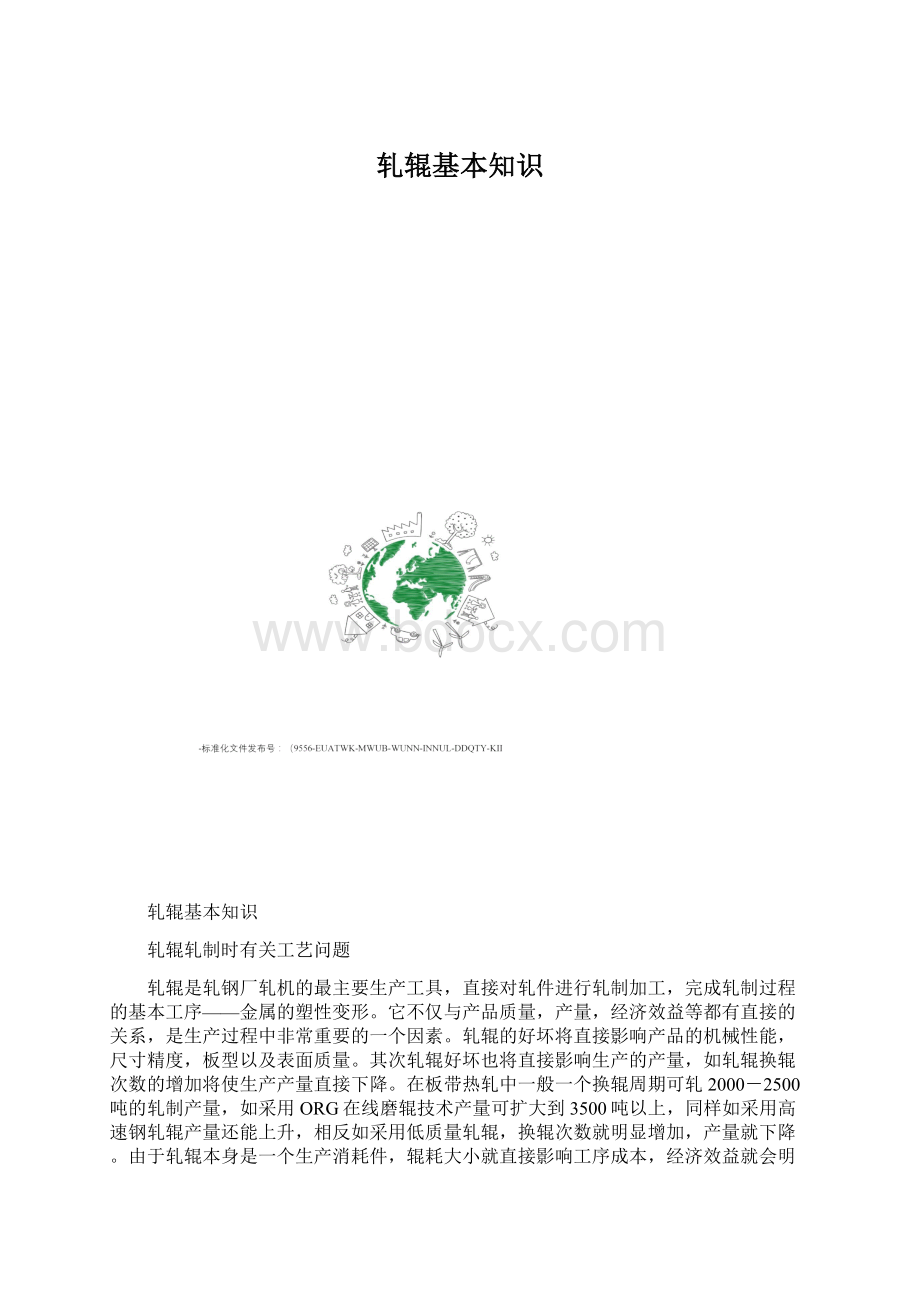
梅花轴头如图2a,万向轴头如图2b,带鍵槽轴头如图2c,不带鍵槽轴头如图2d,带平台轴头如图2e。
直径超过400mm的冷轧辊从热处理工艺需要要在轧辊辊身中心鏜一个中心孔以确保热处理质量。
图2轧辊轴头的基本类型a梅花轴头,b万向轴头,c带鍵槽轴头,d不带鍵槽轴头,e带平台轴头。
2,轧辊重车率
在轧制过程中,轧辊辊面因工作磨损,需不止一次地重车或重磨。
轧辊工作表面每次的重车量为0.1-5mm,重磨量为0.01-0.5mm。
轧辊直径减少到一定程度后,即不能再使用。
轧辊从开始使用直到报废,其全部重车量与轧辊名义直径的百分比称为重车率。
初轧机轧辊的重车率受咬入能力和表面硬度的限制,钢板轧机轧辊只受表面硬度的限制。
表2是各种轧机的轧辊重车率。
表2各种轧机的轧辊重车率
最大重车率%
10-12
工作辊
3-6
8-10
支承辊
6
5-8
四辊冷轧机
薄板轧机
4-6
四辊热連轧
10
3,轧辊材质
轧辊材质是指制造轧辊所用材料。
经过多年的生产实践,对各种轧机的轧辊均已确定了较合适的材料。
在选择轧辊材料时,除考虑轧辊的工作要求与特点外,还要根据轧辊常见的破坏形式和破坏原因,按轧辊材料标准来选择合适材质。
常用的轧辊材料有锻钢,铸钢和铸铁等。
随着1988年铸造高速钢轧辊首先在日本带钢热轧上得到成功应用,随后美国和欧洲也引入铸造高速钢轧辊技术,接着,线材,棒材及冷轧带钢轧机上也开始使用高速钢轧辊铸造,并得到满意效果。
宝钢1580热轧在F1-5轧机工作辊上也采用高速钢轧辊,辊耗已降至0.4kg/t,2008年宝钢1880热轧辊耗下降为0.342kg/t。
其它邯钢,鞍钢1780热轧也得到应用。
1),锻钢,
用于轧辊的合金锻钢在我国“原一机部重型行业统一标准”中已有规定(Q/ZB62-73)。
热轧轧辊有55Mn2,55Cr,60CrMnMo,60SiMnMo等,冷轧轧辊有9Cr,9Cr2,9Crv,9Cr2W,9Cr2Mo,60CrMoV,80CrNi3W,80CrMoV等。
2),铸钢,
用于轧辊的铸钢种类有ZG70,ZG70Mn,ZG8Cr,ZG75Mo等。
3),铸铁,
铸铁可分为普通铸铁,合金铸铁和球墨铸铁。
铸造轧辊时,采用不同的铸型,可以得到不同硬度的铸铁轧辊。
因此,有半冷硬,冷硬和无限冷硬轧辊之分。
半冷硬轧辊表面没有明显的白口层,辊面硬度HS≥50。
冷硬轧辊,表面有明显的白口层,心部为灰口层,中间为麻口层,辊面硬度≥60,无限冷硬轧辊表面是白口层,但白口层与灰口层之间没有明显的界限,辊面硬度≥65。
铸铁轧辊硬度高,表面光滑,耐磨,制造过程简单且价格便宜。
其缺点是强度低于铸钢轧辊。
只有球墨铸铁轧辊的强度较好,因此,得到较广泛的应用。
4,型钢轧辊,
这类轧机的轧辊受力较大且有冲击负荷。
因此,轧辊应要有足夠的强度,而辊面硬度要求可放在第二位(HS<30-40)。
初轧机轧辊常用高强度铸钢或锻钢,主要材料有40Cr,50CrNi,60CrMoV,60CrMnMo,60SiMnMo等。
型钢粗轧机轧辊多采用铸钢,如ZG70,ZG70Mn。
锻钢轧辊的综合机械性能较好,但加工较困难,价格也高,因此,中小型钢轧机上很少应用。
球墨铸铁轧辊价格便宜,耐磨而又有较高的强度。
适合在型钢轧机的第二架粗轧机上应用。
在型钢成品轧机上,由于几何形状及尺寸公差要求严格,需要轧辊有较高的表面硬度和耐磨性。
一般选用冷硬铸铁轧辊,辊面硬度HS≥65。
表3是宝钢高线轧机轧辊材质表:
表3宝钢高线轧机轧辊表
机组名称
机架号
X机型
轧机规格
mm
轧辊直径X身长辊
mm
材质
硬度HS
粗
轧
1H
600
φ650X800
球墨铸铁
62(辊颈65)
2V
φ650
3H
4V
450
φ495
5H
φ495X700
6V
中
7H
400
φ420X650
8V
φ420
9H
10V
11H
12V
13H
14V
预
精
15H
285
φ285(为辊环)
碳化钨
要更高硬度
16V
17H
18V
19V
230
φ228.3(为辊环)
20V
21V
22V
23V
24V
160
φ170.66(为辊环)
25V
26V
减
定
径
27V
28V
29V
150
φ156(为辊环)
30V
5,中厚板轧机轧辊,
中厚板轧机轧辊要求有高的弯曲强度。
高的耐疲劳性能。
良好的抗热裂性,抗冲击性,抗冷热疲劳性。
同时轧辊又要具有较高的硬度,以保证轧辊较高的耐磨性。
因此,轧辊材质的选择,粗轧工作辊主要承担对轧件的宽展和延伸,工作辊承受大的热冲击和大的轧制力,要求轧辊有一定耐磨性,好的咬入能力,因此,在现代中厚板轧机上应采用高镍铬无限冷硬复合铸铁工作辊。
随着冷却系统的不断完善,近来高铬铸铁辊也逐渐得到应用。
精轧工作辊主要考虑轧辊的耐磨性,要求轧辊的硬度高。
目前大部分采用为高镍铬无限冷硬复合铸铁工作辊。
但随着新产品的不断开发,采用更高耐磨性的轧辊材质己成为必切的要求,因而,高铬铸铁辊的采用已成为必然的发展趋势。
支撑辊选择应选择具有高的强度,低的弹性压扁和不易产生挠曲变形,其次辊身表面应具有高的耐疲劳性能,耐剥落,耐掉皮。
第三,轧辊的耐磨性能也要好。
一般选用含2-3%铬的锻钢或铸钢辊。
近来5%铬的锻钢和复合铸钢支撑辊使用得到普遍的好评。
表4是现代5000米宽厚板轧机轧辊表:
表4-1宝钢5000宽厚板轧机轧辊表,
机架
类别
硬度HSC
轧辊牌号
轧辊材质
轧辊尺寸
重量
吨
备注
4辊粗轧机(二期
68-74
Kawasaki
(日川崎)
特殊铸钢
Φ1210X5300(含CVC)
约60
(整个80)
全长9200mm
4辊精轧机
一期
52-60
特殊合金
铸钢
Φ2300X4950
约210
(整个330)
全长10500mm
立辊轧机
立辊
42-47
Φ1000X800
约20
全长4000mm
表4-2沙钢5000宽厚板轧机轧辊表
68-72
无限冷硬铸铁辊
Φ1210-1110X5050
40-50
离心浇铸合金铸钢
Φ2300-2110X4900
45-50
Φ1000-900X600
6,热轧带钢轧辊,
带钢热連轧中除少数粗轧机的工作辊受轧辊强度和咬入条件限制,采用铸钢材料外,其它各架轧机工作辊的特点是:
主要承受扭矩和压力,弯曲应力较小,轧制速度较高,辊面要求光滑以保证轧件表面质量。
为此,选择工作辊材料时应以辊面硬度要求为主,多采用铸铁轧辊。
目前轧机工作辊多采用冷硬铸铁(化学成分:
C=3.0-3.5%,Si=0.5-1.87%,Mn=0.4-0.7%,Mo=0.3%,P≤0.4%,S≤0.11%),辊面硬度HS=58-68。
有的厂在精轧机组前几架也采用半钢轧辊,以减缓表面的粗糙过程,在后几架采用含Ni,Cr的高硬度铸铁,进行复合浇铸,表面形成无限冷硬层,以提高轧辊的表面硬度(硬度可达HS=75-83)。
有的厂在精轧机组中使用高铬铸铁复合浇铸轧辊,这种轧辊的高硬度层很厚,耐磨,使用寿命长。
随着产品要求越来越高,使用离心复合铸造镍铬无限冷硬铸铁和离心复合铸造高铬合金铸铁已成为现代热轧轧辊材料发展的必然趋势。
带钢热轧机的支承辊在工作中主要受弯曲,且直径较大,因此,多采用9CrM0,9CrV锻钢(辊面硬度HS=45-50)。
选含Cr合金钢主要考虑大直径轧辊的淬透性。
国产1700热轧机的镶套支承辊,辊心用37SiMn2MoV锻钢,轴套用8CrMoV或8MnMoV锻钢。
国外的轴套则常用含C=0.4-0.8%,Ni=2.5-3.0%,Cr=0.6-2.0%,Mo=0.6%的合金锻钢,以保证轴套的高强度。
也有采用铸铁或铸钢材料做轴套的。
表5是宝钢1580热轧和1880热轧轧辊材质表:
表5-1宝钢1580热轧厂轧辊材质表
轧辊规格ΦXLmm
E1
1000-900X430
高铬合金铸铁
离心复合铸造工艺
R1
1350-1230X1580
E2
R2
1160-1060X1580
支撑辊
1480-1330X1560
锻钢
F1前
630-570X350
F1-3
825-735X1580
68-75
1600-1450X1560
F4-7
650-575X1580
镍铬无限冷硬铸铁
75-83
表5-2宝钢1880热轧厂轧辊材质表
1350-1200X1880
75-80
1200-1100X440
45±
3
1250-1100X1880
F1-4
835-735X1880
72±
F5-7
695-605X1880
80±
R2,
F1-7
1600-1450X1860
5%铬锻钢
68±
7,冷轧带钢轧辊,
冷轧工作辊是直接承承受轧制时的轧制力和传动扭矩,因此对工作辊的强度,硬度,韧性,耐磨性和辊面质量要求都有很高的要求,它比其它任何轧制类型轧辊要求都高。
我国常用冷轧工作辊的材料是9Cr2W,9Cr2Mo等,辊面硬度HS=90-95。
在国外,为了提高冷轧辊的耐热裂性和减缓辊面的糙化过程,曾试验使用高碳低铬,钼,钒钢(0.8%C,2.2%Cr,0.25%Mo,0.1%V,1.0%Si,1.5%Co),取得了良好的效果。
为了轧制高碳钢和其它难变形的合金钢,在冷轧机上也采用带硬质合金辊套的复合式冷轧工作辊。
其辊心材质与辊套材质的热膨胀系数就十分接近,以防轧辊发热时,损坏辊套。
应该指出,尽管冷轧工作辊的硬度要求很高(达到HS=100),但即不使用铸铁轧辊,这是因为当工作辊直径D确定以后,可能轧出的轧件最小厚度值和轧辊的弹性模数E值成反比。
即轧辊材料的弹性模数E越大,可能轧出轧件的厚度越小。
而铸铁的E值只有钢的一半,为此,在冷轧带钢时,使用铸铁轧辊是不利的。
带钢冷轧机支承辊的工作特点与热轧机相似,可选用9Cr,9Cr2Mo,9CrV锻钢,也可选用镶辊的复合式锻钢轧辊,所不同的是辊面硬度要求较高(HS=50-65)。
支承辊的辊颈硬度一般HS=35-45。
表6是宝钢冷轧轧辊材质表:
表6宝钢冷轧轧辊表
厂名
项目
2030
1800
辊径mm
硬度
HS“C
HS“C”
1工
φ615X2030
86GrMov7
94-98
6.23
φ405X1850
5%Cr合金锻钢
90-96
2工
3工
4工
5工
1-5中
φ530X1885
1-5支
φ1550X2030
40Cr3MoV
58-65
40.48
φ1370X1850
二,有关轧制工艺问题
1,轧制咬入条件,
热轧轧制时不是任何轧辊的辊径和坯厚都可以进行轧制的,它要符
图3轧制咬入条件
合轧制的基本条件,即咬入条件,见图3轧制咬入条件所示:
轧辊给轧件一个轧制力P,水平分力PX,轧件与轧辊接触产生摩擦力T其水平分力为TX,同样下辊也产生上辊同样的力。
因此,要使轧件前进必须符合以下条件,即:
2TX>2PX件或
μP
Cosα>PSinα
μ>Sinα/Cosα=tgα
式中:
α为咬入角,即轧辊前进时与轧辊最先接触的点与中心的连线和中心线之间的夹角α为咬入角(热轧咬入角一般为180∽220)。
因此,热轧的咬入条件必须满足μ≥tgα
如果摩擦系统等于咬入角正切,则轧件平衡不动,或出现打滑现象。
如摩擦系数大于咬入角正切则轧件前进。
这就是咬入的基本条件,即摩擦系数必须大于咬入角的正切,这就是轧制前进的基本条件。
这在热轧粗轧机上是非常重要的条件。
热轧摩擦系数一般为0.26∽0.34。
这也就说明轧辊小到某一值时轧辊就不能用了。
满足咬入条件时的最大压下量为
△hmax/2=R―RCOSα
△hmax=D―DCOSα
所以:
△hmax=D(1―COSα)。
各种轧制条件下的允许最大咬入角见表7所示:
表7各种轧制条件下的允许最大咬入角
轧制条件
咬入角α
在有表面刻痕或堆焊的轧辊上热轧
270-340
在型钢轧机上热轧
220-240
在钢板轧机上热轧
150-240
在表面粗糙的轧机上冷轧
50-60
在表面光滑带润滑的轧机上冷轧
30-40
例某精轧机工作辊半径为R=400mm,轧件轧制前厚度为40mm,压下量为16mm,
求咬入角为多大,
COSα=1-
=1-
=0.98
α=11047'
2,轧制力
当轧辊轧制时,轧辊将受到轧件的反作用力称为轧制力,轧制力等于轧辊接触面上的轧制力分布的总和。
在热轧厂内,轧制力是操作上的重要数据,轧辊生产者也应了解轧制力计算一般情况。
平均单位压力Kw=Kf+Kr+Ki
式中:
Kf—金属塑性变形阻力所引起的单位压力,
Kr—克服轧件与轧辊间摩擦力所引起的单位压力,
Ki—克服轧件变形时的内摩擦力所引起的单位压力,
在考虑轧辊压扁时的轧制力的计算公式为:
Wk=KwXA'd=KwXBX
式中:
Kw为平均单位压力
B为平均宽度,B=(B0+B1)/2
R'为压扁后的轧辊半径,R'=R(1+
)
例:
已知F7的轧辊半径为350mm,压下量△h=0.5mm,
B0=1000mm,Kw=90kg/mm2
求F7的轧制力
代入以上公式可求得轧制力Wk=1191吨,辊径压扁后的轧制力Wk'=1492吨,可知辊径压扁后增加轧制力为301吨。
对热轧来说并不大,但对冷轧来说就要大得多了。
3,轧制时轧辊的压扁
轧制时,由于轧辊受轧件的反作用力,使得在轧辊和轧件相接触部位发生轻微的弹性变形,称做轧辊的压扁。
处在变形区的轧辊表面被压扁后,使接触弧长度增大,这会导致单位轧制压力增加,如图4所示。
希考克(Hitchcock)假设接触弧上的压力公布为椭圆形,轧辊发生弹性变形后也呈圆弧形状,并且不考虑轧件的弹性变形,推导出下列公式:
R'=R(1+
)式中C=16
R'为轧辊压扁后的假想半径,
R为工作辊未压扁的半径,
C为材料常数,C=0.222X10-3mm2/Kp
F为轧制力
B为轧件宽度
γ为泊桑系统,γ=0.3
△h为压下量
E为弹性模数,E钢=21000Kp/mm2
图4为轧辊压扁的示意图。
图5轧辊压扁的R'/R曲线
如不考虑压扁:
ℓd=
Ad=B
考虑压扁:
ℓd'=
A'd=B
为了求得Ad',首先要求得ℓd'为了求得ℓd'可通过图5的曲线来得到,以F/B△h为自变量,按照轧辊的材质的曲线,求得R'/R的值,再乘以R,即可得R',从而可求出ℓd'和A'd。
压扁对粗轧不起作用,对精轧起作用,尤其对F7影响较大。
当然冷轧的压扁现象的影响比热轧要大的多。
尤其在轧制薄钢板时,轧制力较大,轧辊压扁的影响更应重视。
对F7来说,当轧辊辊径增大时,压扁较为显著,因此可以通过减小轧辊直径和使用硬度材料轧辊来减轻压扁的影响。
但是F7的辊径不能太小,否则咬入会产生问题。
F7的轧辊半径为350mm,△h7=0.2mm,F7轧制力为1200吨,轧件宽度为B=1400mm。
求:
压扁前后半径之比R'/R
代入以上公式,可求得R'/R=1.95。
4,轧辊的弯曲
轧制时,轧件对轧辊有反压力,从而使轧辊产生弯曲变形,轧制力越大,轧辊弯曲度也越大。
轧辊存在撓度,轧件就有凸度。
德国梯森贝克威尔特热轧厂规定要测量带钢在B15,B40,B60处的凸度。
为了抵消轧辊撓度带来的影响,予先将辊身中部的直径磨成两端的直径稍许大一些,即将辊身表面作成曲线,即轧辊的磨削凸度如图6。
图6轧辊的凸度
轧辊受力区局限在对应轧件的宽度范围附近,一方面由于轧件边部散热快,另外冷却水从轧件中部流向边部,同时还有侧喷水的作用,使轧件边部温度较中部低。
在相同压下情况下,轧件边部的轧制力较高。
一般来说,轧件边部的温度较轧件中部的温度约低60℃左右。
总的来说,轧件压扁的存在,对轧制较薄的带钢时影响较大。
在理论上,F7是存在压扁的,但在实际操作上,这个压扁的影响其作用不如冷轧显著。
对轧辊辊径与轧件最小厚度的关系时,热轧厂可以不考虑这个问题,冷轧厂是必须考虑这个问题的。
热轧机的辊径不能随便减少,否则会影响轧制力矩,尽管如此,热轧厂精轧机组的后几架的辊径一般较前几架选择得小一些。
例如贝克威尔特热轧厂精轧机F1-F4工作辊辊径为780-715mm,而F5-F7的工作辊辊径为715-650mm,宝钢1580热轧F1-3工作辊辊径为825