扇形板零件工艺及钻床夹具设计说明书Word下载.docx
《扇形板零件工艺及钻床夹具设计说明书Word下载.docx》由会员分享,可在线阅读,更多相关《扇形板零件工艺及钻床夹具设计说明书Word下载.docx(13页珍藏版)》请在冰豆网上搜索。
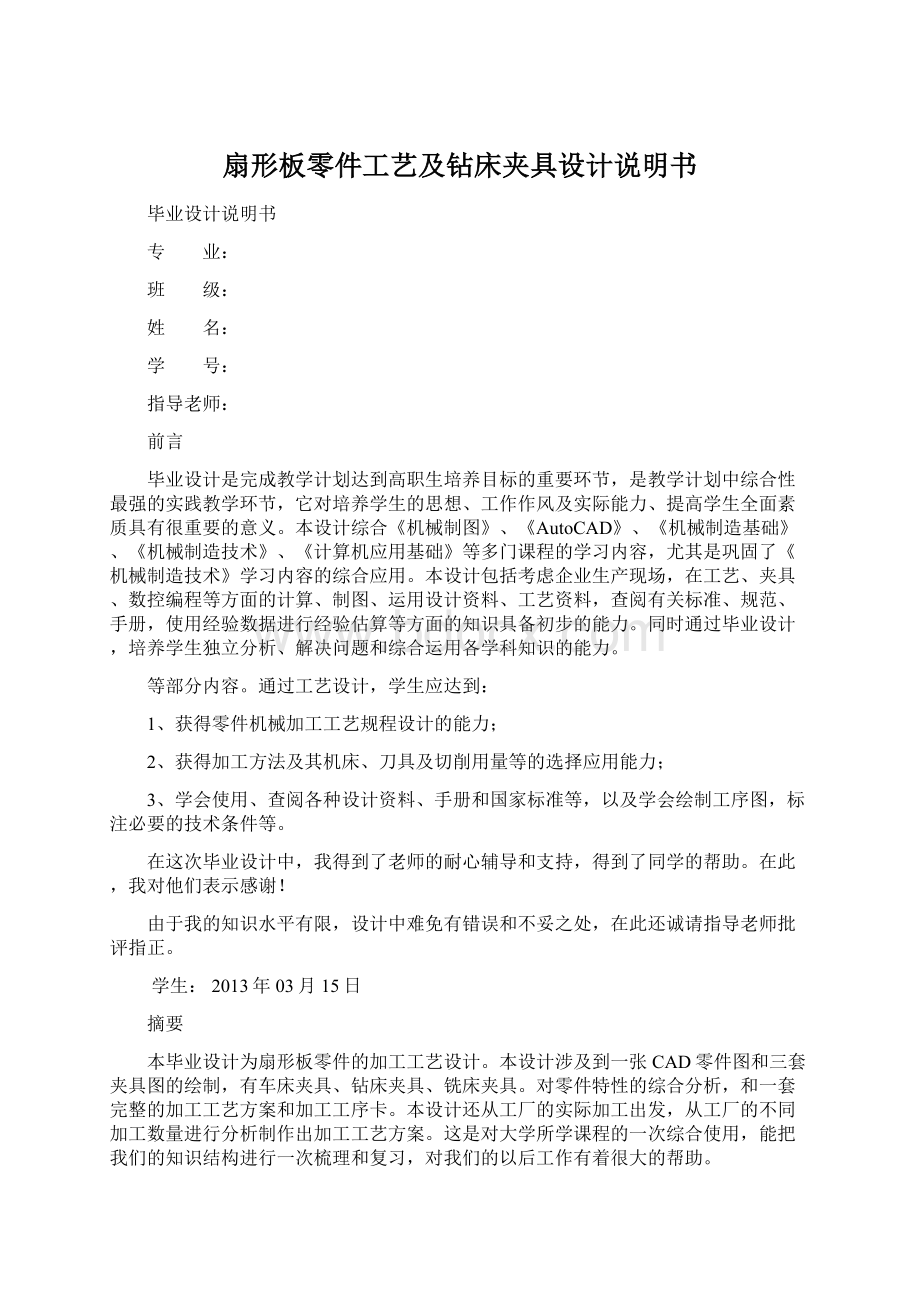
零件图
毛坯图
一、零件的加工工艺分析
(一)生产纲领和生产类型
生产纲领和类型均为提出,本产品为设备常用零件的生产加工,所以设计中把本零件定为大批量生产。
(二)零件的功用
工件一是机器的连接零件,其主要作用是起连接、传递运动和传递动力的作用。
为保证其的精确定位,要求对其内孔加工的精度较高。
其所受的载荷冲击力较小。
所以其同轴度及端面跳动要求较高,连接部位粗糙度要求高。
(三)零件的结构特点
由零件图可以知道,该零件为上下两内孔同轴情况,上面内孔可以采用钻床加工即可满足要求,下面内孔可以采用车床加工即可完成,有CAD图给出了零件的特征,公差标注的按照公差加工生产,凡是未标注公差的情况均为自由公差。
(四)零件的技术要求
1、尺寸精度要求
钻孔内径8,车内孔直径22,以及铣两端面,按照零件图的形位公差要求,达到加工要求即可完成
2、形状精度要求
零件按照标注的行位公差加工即可。
具体见上部提供的零件图。
3、表面粗糙度
零件按照标注的粗糙度加工即可。
4、零件的材料及毛坯
从零件的受力分析可知,它受径向和轴向复合作用力,由于其承受中等载荷,工作又较平稳,冲击力很小,所以可采用铸造,材料为HT200。
为了改善组织、切削性能和提高力学性能,毛坯料要经过正火热处理。
为使零件获得良好的综合理学性能,消除和减少内应力,为后续热处理做组织准备,需对零件进行调质处理(HrC32—38)。
(五)选择定位基准
加工零件的定位精基准,最常用的是内孔和两端面,这遵循了基准重合原则及基准统一原则,以保证零件的精度要求。
为了保证零件的准确定位,先铣两端面。
以两端面为定位基准加工即可
在生产批量较大时,可以在专用的双面铣床上铣端面。
定位粗基准(未加工表面),即首道工序的基准是扇形零件的外A端面。
(六)加工阶段的划分
扇形零件的加工质量在尺寸和粗糙度上都有较高的要求,为保证加工质量的需要和合理的使用机床设备,把零件的加工阶段主要划分为三个阶段:
粗加工阶段、半精加工阶段和精加工阶段。
两端面的尺寸精度和表面粗糙度都要求不高(公差等级为IT11,表面粗糙度值Ra为25,查《机械制图》附表7-4轴的极限偏差可知)。
半精加工主要是各个面的铣削加工,精加工主要是内孔的精车。
1、粗加工阶段
铣削工件两端面上的大部分加工余量。
使毛坯在形状和尺寸上接近零件的图纸要求,为半精加工时提供精基准,留好足够的加工余量为后续加工创造有利条件。
2、半精加工阶段
加工外两端面到一定的精度要求,并保证留有一定的加工余量,为其精加工作准备。
同时完成次要表面的加工。
3、精加工阶段
通过车床加工使零件各尺寸和加工表面达到图纸规定的技术要求。
(七)加工顺序的安排
1、基准先行
先从加工精基准开始,再以精基准定位加工其他表面。
2、先粗后精
精基准加工好后,车削内孔时,粗、精加工分阶段进行。
3、先主后次
先加工零件的主要表面再加工零件的次要表面。
机械加工完毕,最终要进行检验。
(八)零件的加工工艺路线:
铸造→铣削→铣削→铣削→铣削→车削→车削→铣削→铣削→铣削→铣削→铣削→铣削→钳工(钻)→铰削→检验
(九)确定工艺方案
(1)铸造。
(2)粗铣端面A,保证厚度为34,以粗基准B为基准
(3)粗铣端面B,保证厚度为33,以粗基准A为基准
(4)精铣端面A,保证厚度为32.5,以粗基准B为基准
(5)精铣端面B,保证厚度为32,以粗基准A为基准
(6)在上部第二和第三个孔处钻孔直径7.5
(7)粗车内孔,车内孔直径21
(8)精车内孔,保证内孔直径为22+0.021
(9)粗铣弧形槽,保证弧形槽宽度为12
(10)铣圆弧面,保证弧形半径为48.5
(11)铣圆弧面,保证弧形半径为20.5
(12)精铣弧形槽槽宽13,保证到B断面的距离为10
(13)铣圆弧面,保证弧形半径为48
(14)铣圆弧面,保证弧形半径为20
(15)钻孔,钻孔直径为7.8
(16)铰孔,铰孔直径为8
(17)检验入库。
(十)确定各工序的加工余量,工序尺寸和公差
各加工表面的工序间余量,工序尺寸及公差如下表所示。
扇形件的加工工序尺寸及加工余量(单位mm)
加工表面
工序
名称
工序间
余量
工序能达到的公差等
级及其标准公差值
工序尺寸
公差
两端面
铣削
3
粗糙度3.2即可
按图
车内孔
车削
22
粗糙度1.6即可
+0.021
弧形槽
2
GB/T1804-m(自由公差)
弧形面
φ8内孔
钻
7.8
φ7.8
铰
0.2
+0.08
φ8
二、扇形板铣削专用夹具设计说明
铣削夹具图.
(一)夹具设计说明
本设计主要是设计的一套铣削端面的夹具,根据设计工艺,本设计中任意设计了铣削工件B面的夹具设计,根据零件的机构特性,首先固定一端面,本端面与地板焊接为一体,也称为支架,把工件安放在支架上,另一端采用加紧的方式固定即可,因为两个面均为圆弧面,所以固定后在平面内的四个方向上不会运动,只需要在铣刀的铣削力的情况下即可完成。
(二)夹具设计专业刀具设计说明
切削用量包括切削速度、进给量和背吃刀量三要素。
合理选择切削用量,对提高切削速度,保证必要的刀具耐用度和经济性,保证加工质量等都有重要意义。
由于零件的材料为30钢,刀具材料选择范围较大,一般选用硬质合金刀具即可满足要求。
刀具材料选择范围较大,一般选用硬质合金刀具即可满足要求。
合理选择切削用量必须满足下列基本要求:
(1)保证安全,不致发生人身事故或设备事故;
(2)不致加工质量;
(3)在满足上述两要求的前提下,为充分发挥机床的潜力和刀具的切削性能,应尽量选用较大的切削用量;
(4)不允许超过机床功率。
(5)刀具类型确定
此加工精度要求不高,因此可用高速钢镶齿套式面铣刀。
(6)刀具设计参数确定
面铣刀:
高速钢镶齿套式面铣刀,刀片材料硬质合金,刀杆材料高速钢,刀盘直径D=20mm,刀齿数Z=8,主偏角kr=75°
;
前刀面有沿切刃方向的斜坡台阶式分屑槽
5.刀具工作草图(见附图)
(三)铣削设计计算
1、加工条件
工件材料:
HT200,σ
=200HBS,铸造;
加工需求:
粗、精左右面,保证尺寸32mm;
机床:
X6132型铣床;
刀具:
高速钢圆柱形铣刀,根据《金属切削手册》表6-4取铣刀直径d=100mm,根据《金属切削手册》表6-7查得铣刀齿数Z=14;
2、确定铣削深度:
参考有《金属切削手册》确定粗加工的铣削深度a
=2.5mm;
精加工的铣削深度a
=0.5mm;
3、确定每齿进给量:
参考《机械加工工艺手册》(软件版)取粗铣时的每齿进给量f
=0.15(mm/z);
精铣时的每转进给量f=0.8(mm/z);
4、确定主轴转速:
参考《实用金属切削加工工艺手册》表8-4,取粗铣时的主轴转速为150r/min,精铣时的主轴转速为190r/min;
5、计算铣削速度:
前面已经确定铣刀直径d=100mm和主轴转速(粗铣刀时为300r/mm)。
所以,相应的铣削速度分别为:
粗铣时:
精铣时:
6、校核机床功率(只需校核粗加工即可):
关由手册查得功率
取Z=14,
,
,a
=2.5mm,
而
由手册查得
=1,
=1故
1,所以:
起所耗功率远小于机床功率,故可用。
7、计算基本工时:
参考《机械加工工艺手册》(软件版)确定切入和切出的行程长度
,而工件的长度为
,故铣刀的工作行程为
。
所以,基本工时为:
0.41(m/min)(粗铣时);
1.08(m/min)(精铣时);
三、扇形板车削专用夹具设计说明
车削夹具图
(一)夹具设计说明
本夹具的设计是上部使用了一个V行块,下部采用螺栓固定紧的办法,上部的V形块正好加紧扇形零件的上部,使其固定紧固,对V行块进行螺栓固定,然后再下部设计了螺栓顶紧装置,可以调整螺栓的旋转来实现顶紧和放松,即可完成了本夹具设计。
(二)切削用量的选择
粗车时应考虑提高生产率和保证合理的刀具耐用度,应首先选用较大的背吃刀量,然
后再选择较大的进给量,最后根据刀具耐用度选择切削速度。
(1)背吃刀量
背吃刀量根据加工余量和工艺系统刚度来选择。
粗加工时,在保留半精车余量
(1~3mm)和精车余量(0.1~0.5mm)后,一次走刀应尽可能的切除全部余量。
当加工余量太大,机床功率不足,刀具强度不够,加工余量不均匀以及断续切削时需要分多次走刀加工。
(2)进给量
粗加工时,对表面质量没有太大要求时,合理的进给量应是工艺系统所能承受的最大进给量。
机床进给机构的强度、刀具刀杆的强度和刚度、刀具材料的强度和工件的装夹刚度等也将限制进给量的大小。
(3)切削速度
切削速度的确定可根据已选定的背吃刀量、进给量及刀具的耐用度利用下列公式计算:
Vc=
式中f为进给量、a
为背吃刀量、T为刀具的耐用度、K
为切削速度的修正系数、其他的系数可通过查表得出。
也可根据生产实践经验和有关资料确定,必须考虑机床的许用功率。
v=
4)半精车切削余量的选择
半精车必须保证进给精度和表面质量,同时还应兼顾必要的刀具耐用度和生产效率。
半精车和精车时的背吃刀量是根据加工精度和表面粗糙度要求由粗车后留下的余量确定的。
半精车和精车时限制进给量提高的主要因素是表面粗糙度。
(3)切削速度
为了抑制积屑瘤的产生,提高工件表面质量,用硬质合金车刀精车时,采用较高切削速度(80~120m/min),高速钢车刀宜采用较低的切削速度。
在选择切削速度时还应考虑:
粗加工时,背吃刀量和进给量均较大,故选择较低的切削速度;
精加工时,背吃刀量和进给量均较小,则选择较高的切削速度。
(1)粗车
刀具选用硬质合金的外圆车刀(YT15),背吃刀量选择3~5mm(余量较小,一次走刀车完余量,余量较大可多次走刀),进给量0.5~0.6mm/r,切削速度600r/min。
(2)半精车
刀具选用硬质合金的外圆车刀(YT15),因为表面粗糙度Ra1.6µ
m,背吃刀量选择1mm,进给量0.1~0.2mm/r,切削速度为800r/min。
(三)机床功率计算(根据切削用量计算)
在国家标准GB/T122004—1990中将工作功率Pe定义为“同一瞬间切削刃基点的工作力与合成切削速度的乘积”。
所谓的工作力是指(Fe)是指总切削力在合成切削方向的正投影,在工作平面中定义。
工作功率Pe也可以称为切削过程的消耗的总功率。
他包括切削切削功率和进给功率切(分别用Pc和Pf表示)两部分。
前者为主运动消耗的功率,后者为进给运动消耗的功率。
由于后者在工作功率中所占的比例很小(仅为2%--3%),故一般只计算切削功率Pc。
所以工作功率可按下式计算:
Pe
Pc=FcVc×
0.001
其中切削力和速度的单位分别为N和m/s;
工作功率的单位为KW。
根据求出的的切削功率Pe可用下式计算机床主电动机功率Pe:
Pc/
m
式中的
m为机床的传动效率,其值一般为0.75—0.85
m=
由于6.85KW小于机床功率7.5Kw,所以,所选切削用量满足机床要求。
由于此零件年产量为2040件,属于中批量生产。
在生产管理较完善的工厂一般可编制如下表的比较详细的机械加工过程工艺卡片。
车刀图
四、扇形板钻削专用夹具设计说明
钻削夹具图
钻削夹具的设计,主要是根据在上几步工序完成的基础上进行下一步工序设计,首先以孔直径22,设计一根轴,安放后进行把工件牢固,然后再一侧加上固定销,使其紧紧固定,固定轴一侧采用螺栓连接固定,另一侧设计一个顶紧装置,固定紧后,夹具零件不可松动,即可完成了本设计。
(二)钻削计算
钻四个定位孔(2-ø
10mm和2-ø
13mm);
锪两个沉头孔ø
20mm,深2mm;
工步1:
钻两个ø
13mm孔
钻锥度孔ø
10mm,保证零件图上的精度要求;
Z5125A型钻床;
刀具:
,钻头直径13mm,
2、确定切削进给量:
根据《实用金属切削加工工艺手册》中表5-6,取进给量f=0.3(mm/r);
3、确定切削速度:
根据《实用金属切削加工工艺手册》中表5-6,取切削速度
4、计算转速:
,按机床实际转速取
5、计算基本时间:
毕业体会
虽然我有事情耽搁了设计时间,但经过一周时间的抓紧工作,我终于完成了设计。
可能由于时间紧凑,里面还有一些问题,但看着自己的设计成果,一切疲惫与先前的无奈都被遮掩了,喜悦之情油然而生,与此同时,我也深深体会到了自己所学甚少。
从拿到零件图纸的第一天开始,辅导老师就详细的给我们讲了设计的步骤,还安排了辅导时间。
为我们的设计指引了方向,这样使我们不会感到太多的盲目。
我们以前所接触的只是课本上的知识,对机械加工工艺、夹具、量具等只有基本的了解。
但是通过这次设计,我们才全方位的懂得了什么是机械设计,从而更加了解到机械知识的重要性。
刚开始设计的时候,总觉的难度很大,不知道从什么地方下手,对一些设计的步骤根本不知道怎么安排,怎么设计。
好长时间都懒得在去看设计图纸,经过老师在网上给我的指导,才让我有了一定的思路,先从分析零件图开始,然后在得出零件技术要求,在根据零件的技术要求画出毛坯和零件合图等等,一步步的开始设计起来。
在设计期间,遇到不懂的问题时,通过自己查资料、仔细的琢磨、有根据的慢慢分析从而克服困难,实在解决不了的,我们的指导老师能细心的帮助我们,从而设计对我来说更迈进了一步,在这次设计中,学会了运用资料,可以向不同的懂我们知识的人问问题,这次设计,要十分的感谢我们的指导老师,他在设计期间为我解决了很多难题。
相信我们通过这次设计,一定会在以后的工作岗位中得以更好的发挥,也会在以后的人生的道路中更上一层楼。
经过将近一个月的努力,毕业设计终于划上了一个圆满的句号。
对此次毕业设计,我可以说是感触很深,同时在此过程中也学到了很多知识。
虽然本次毕业设计尚存在不足之处,但是通过这段时间的学习,我从中认识和学到了很多关于机械零件制造工艺的设计方法和流程,这对我今后的学习和工作都有着很大的促进作用。
即将收笔之际,我对此次设计作如下总结:
毕业设计是考查学生对自己所学专业知识掌握的程度和解决问题的能力,也是大学毕业之际即将走上工作时的过渡阶段,可以说它能考查出一个学生对专业知识掌握的深度和广度,也是检验我们学习能力的一个良好契机。
致谢
十年寒窗苦读,终于造就了我的大学梦想,如今,一眨眼三年也快过去了,在大学的日子里,我结交了许多新朋友,开阔了新视野,但尤为重要的是,我学习了许多新知识,掌握了社会生存的技能。
这一篇毕业设计不仅融汇了我三年的智慧,更是我向恩师们递交的最完美的答卷。
在此,我要感谢每一位帮助过或得罪过我的人,你们是我生命中不可或缺的一部分。
其次,我要感谢所有的恩师。
他们不仅教给了我求生的知识、技能,更为重要的是他们也教会了我做人的道理,使我明白了为人与处世的道理。
在这次毕业设计完成的过程中,我要特别感谢王玉良老师,因为在设计题目下发了很长一段时间了我都没有着手去做,而林老师总是反反复复、不耐其烦地打电话提醒我着手做,后来又悉心指导我们按时完成设计,他真的很负责任,就是他,深深地感动了我,老师,谢谢您!
在此,我想借此机会表达我心中对老师们那份崇高的敬意:
老师,您辛苦了!
另外,我还要感谢我亲爱的同学们。
感谢他们为我提供了许许多多的帮助,感谢他们在我最需要帮助的时候,向我伸出了援助之手,感谢他们的真诚帮助与付出。
亲爱的同学们,祝你们好人一生平安,幸福!
来吧,在这毕业来临之际,让我们一起来欢呼,一起来感谢所有的老师们,同学们。
参考文献
[1]刘力,《机械制图》,高等教育出版社,2008年第一版,P:
5、62、203、339;
[2]史宇宏,《AutoCAD2007机械设计》,人民邮电出版社,2008年10月第一版,P:
5、34、67;
[3]、邹吉权《公差配合与技术测量》重庆大学出版社2004年06月
[4]张茂,《机械制造技术》,机械工业出版社,2008年第一版,P:
47、89、98、249;
[5]《机械加工工艺手册》(软件版),机械工业出版社,2004年第一版;
[6]杨峻峰,《机床及夹具》,清华大学出版社,2007年第一版,P:
10、240、288;
[7]上海科学技术交流站,《金属切削手册》,上海人民出版社,1974年第一版,P:
158、232;
[8]陈宏钧,《机械工人切削技术手册》,机械工业出版社,2006年第一版,P:
11、22、101;
[9]陈家芳,《车工常用技术手册》,上海科学技术出版社,2007年第一版,P:
5、87、146。
[10]白成轩.机床夹具设计新原理.北京:
机械工业出版社,1997年;
[11]徐鸿本.机床夹具设计手册.沈阳:
辽宁科学出版社,2004年;
[12]赵家齐.机械制造工艺学课程设计指导书(第2版).北京:
机械工业出版社,2000年;
[13]史全富等.金属切削手册(第三版).上海:
上海科学技术出版社,2000年;
[14]陈家芳.实用金属切削加工工艺手册(第二版).上海:
上海科学技术出版社,2005年;
[15]MachineToolsN.chernor1984.
[16]MachineToolMetalworkingJohnL.Feirer1973.
[17]HandbookofMachineToolsManfredweck1984.
[18]Sorsl.fatiguedesignofmachinecomponents.oxford:
pergramonpress.1971