硅片质量对太阳能电池性能的影响Word文档下载推荐.docx
《硅片质量对太阳能电池性能的影响Word文档下载推荐.docx》由会员分享,可在线阅读,更多相关《硅片质量对太阳能电池性能的影响Word文档下载推荐.docx(15页珍藏版)》请在冰豆网上搜索。
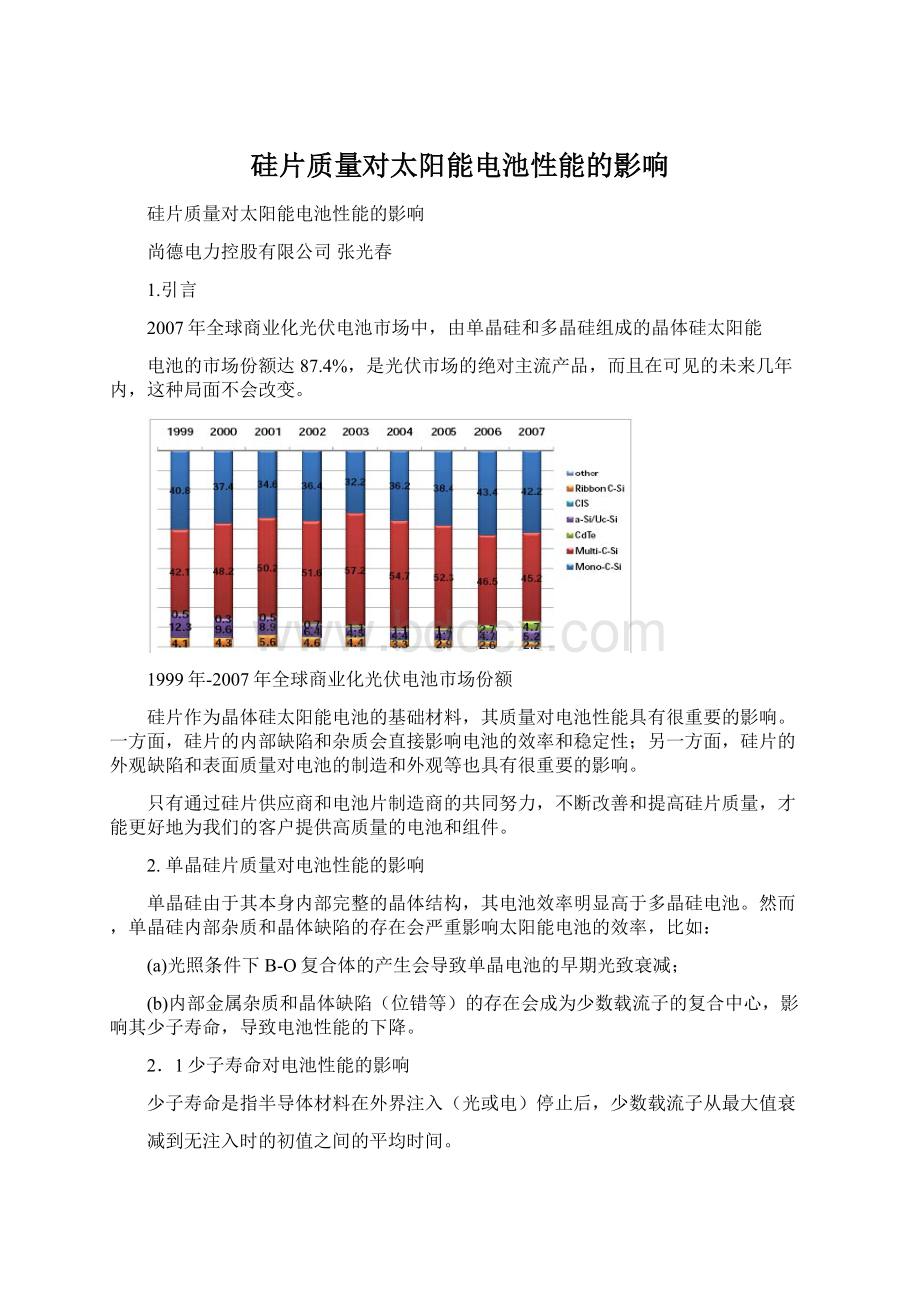
减到无注入时的初值之间的平均时间。
少子寿命是用于表征材料的重金属沾污及体缺陷的重要参数,少子寿命值越大,相应的材料质量越好。
少子寿命已成为生产线上常规测试的一个参数。
我们选取某供应商某批单晶硅片进行实验,将硅片按不同少子寿命区分后,
按正常电池工艺做成电池,其少子寿命和电池效率具有很好的对应关系,如下图所示。
2.2早期光致衰减对电池性能的影响
早期光致衰减机理
P型掺硼晶体硅太阳电池的早期光致衰减现象最早在30多年前就有相关报道。
大量的科学研究发现它与硅片中的硼氧浓度有关,大家基本一致的看法是光照或电流注入导致硅片中的硼和氧形成硼氧复合体,从而使少子寿命降低,但经过退火处理,少子寿命又可恢复,其反应为:
正是由于掺硼单晶硅在光照条件下硼氧复合体的生成,引起少子寿命的下降,最终导致太阳电池和组件功率的下降。
关于这方面的详细研究,尚德公司已在第十届光伏大会上发表论文“P型晶体硅光伏电池和组件早期光致衰减问题的研究”。
光致衰减的危害
光伏组件的早期光致衰减
(一)会引起组件功率在使用的最初几天内发生较大幅度的下降,使标称功率和实际功率不符,使组件供应商面临客户投诉或索赔。
(二)光伏组件的光致衰减主要是由电池衰减导致的,同一组件内各个电池片由于光致衰减的不一致性造成原本分选时电性能一致的电池片,经过光照后,电性能会存在很大偏差,引起组件曲线异常和热斑现象,导致组件的早期失效。
低质电池光致衰减不一致性实例
我们将某供应商提供的质量较差的硅片做成的初始分选效率为16%的电池
片,经弱光光照1.5小时后(光源为节能灯),发现电池片效率衰减很多,且离散性也很大,效率最高的为15.4%,最低的仅为13%,衰减比率达3.75%至18.75%。
低质硅片做成的同一档次电池经弱光光照后效率分布图
上述经弱光光照的电池片重新分选检测后,按转换效率的分布情况做成14
块组件,经太阳光光照1天和2天后的功率对比如下图所示。
试验结论:
1.此供应商的硅片制作的电池片本身衰减较为严重,如果电池片不经过光照和二次分选而直接做成组件,尤其是衰减较为严重的那部分电池片,会分散在各个组件内,影响到组件的整体功率下降更多,并且将导致组件曲线异常和热斑。
2.上述结果也说明,普通的节能灯没有使该电池片衰减到稳定的程度,因此做成的组件在太阳光光照后仍然出现了较大的衰减。
但是通过光照后二次分选剔出了效率极低的电池片,并使得每个组件内电池片效率均匀性基本一致。
3.初始分选效率16%的电池片理论上可做成172W的组件,但经过光致衰减后,最终的做成最大仅155.71W组件和最小仅143.78W的组件,衰减比率达9.47%至16.4%!
因此,严格把控硅片质量是保证电池和组件性能稳定的根本措施。
早期光致衰减导致的组件台阶曲线和热斑现象
台阶曲线和热斑现象分析:
•光伏组件的核心组成部分就是太阳电池,如果太阳电池发生光致衰减,就必然导致光伏组件的输出功率下降,并极易在组件中引起热斑。
•若一串电池中产生的电流不一致时,通过这串电池的电流将在问题电池上引起热斑;
若电池串与串之间电流不一致,在接了旁路二极管的组件特性曲线上可看到“台阶曲线”。
•通过测量光照前后组件的输出特性曲线和红外成像分析,可以考察组件的初始光致率减现象。
如果组件中电池的衰减不一致,将导致I-V曲线出现台阶。
对于出现台阶曲线的组件用红外成像检查,可发现有组件出现热斑,如右图所示,该组件温差大于20℃。
这种热斑的温度与周围电池的温度相差较大,过热的区域可引起EVA加快老化变黄,使该区域透光率下降,从而使热斑进一步恶化,导致组件的早期失效。
早期光致衰减的解决方案
(一)改善硅单晶质量
硅片自身的性质决定了太阳电池性能的早期光致衰减程度。
(A)利用磁控直拉硅单晶工艺(MCZ)改进单晶硅棒产品质量;
(B)使用掺磷的N型硅片;
(C)改变P型掺杂剂,用镓代替硼。
尚德公司与供应商合作在掺Ga单晶方面做了大量研究工作,克服了相关技术难题,并于今年8月份联合供应商召开了掺Ga工艺推广会,把这一技术成果无偿
提供给社会。
(二)电池片光照预衰减
通过对电池片进行光照预衰减,使电池的早期光致衰减发生在组件制造前,组件的衰减就完全可以控制在测量误差之内。
同时也大幅度地减少了光伏组件出现热斑的几率,提高了光伏组件的输出稳定性,为我们的用户带来更多的效益。
尚德公司利用光照预衰减设备,将衰减比率大的电池片全部进行光照预衰减,主动承担因电池衰减而造成的损失,保证了光伏组件输出稳定性和客户的利益。
2.3位错对电池性能的影响
组件EL和电性能测试
我们对大量低档电池片及其组件进行了研究,某低档电池片做成的组件其EL测试如下左图所示。
组件的电池片中存在着大量黑心和黑斑的情况。
电致发光EL(Electroluminescence)照片中黑心和黑斑反映的是在通电情况下该部分发出的1150nm红外光相对弱,故在EL相片中显示为黑心和黑斑,发光现象和硅衬底少数载流子寿命有关。
由此可见,黑心和黑斑处硅衬底少数载流子寿命明显偏低。
组件电性能测试如下右图所示。
由图可见,组件短路电流Isc(4.588A)和最大功率Pmax(143.028W)明显偏低;
此类正常组件短路电流Isc一般为5.2A,最大功率Pmax一般为175W以上。
说明组件中存在着大量低效率电池片,导致组件功率的严重下降。
组件EL测试光照条件组件电性能测试
电池片EL和电性能测试
电池片EL测试如下图所示,其黑心和黑斑现象如组件EL测试所见。
光照条件电池电性能测试如下所示。
两片电池效率和Isc均明显偏低,而此类正常电池片效率约为17.5%左右,Isc为5.3A。
Uoc
Isc
Rs
Rsh
FF
NCell
Urev2
Irev2
样片1
0.613
4.73
0.026
16.99
56.67
0.1106
-12
1.041
样片2
0.587
4.62
0.005
104.21
76.6
0.1399
0.165
硅片少子寿命测试
电池经过去SiN膜、去正反电极、去铝背场和n型层,再经碘酒钝化后,硅片少子寿命测试如下图所示。
电池片EL测试黑心和黑斑区域少子寿命明显偏低。
硅片位错密度
硅片经化学腐蚀后,其形貌如下图所示。
硅片“黑心内”位错密度均最高达1E6~1E7个/cm2左右;
另一硅片,EL测试黑斑区域位错密度达1E5~1E6个/cm2左右,如下图所示。
“黑心内”位错密度1E6~1E7(×
500倍)另一硅片位错密度1E5~1E6(×
500倍)
综上所述,正是由于硅片中存在着极高的位错密度,成为少数载流子的强复合中心,最终导致电池性能的严重下降。
3.多晶硅片质量对电池性能的影响
多晶硅太阳电池的市场份额已远远超过单晶硅太阳电池,成为光伏市场的主要产品。
然而,与直拉单晶硅相比,多晶硅中存在着高密度的缺陷和杂质,如晶界、位错、氧碳和金属等。
一方面,作为位错、晶界和杂质最集中的微晶区域会显著影响材料的电学性能,并最终影响电池性能;
另一方面,由于多晶硅中各部分缺陷和杂质分布的不均匀性,造成单片多晶硅片性能上的明显差别,研究表明,其少子寿命最低区域对电池性能具有决定性的影响。
3.1少子寿命分布对电池性能的影响
由于多晶硅片内部杂质和缺陷的不均匀性,其少子寿命分布也具有很大的不均匀性,而最终决定所做电池效率的是硅片少子寿命最小值。
我们选取一批硅片,每片测试五个点(边角四个点和中心一个点)的少子寿命(去损伤层后碘酒钝化),再按正常工艺做成电池测试其电池效率。
硅片少子寿命五点中最大值由小到大排列时,相应电池片的效率如下图所示。
硅片少子寿命五点平均值由小到大排列时,相应电池片的效率如下图所示。
硅片少子寿命五点中最小值由小到大排列时,相应电池片的效率如下图所示。
切方之后的硅锭需要通过少子寿命扫描,将头尾少子寿命很低的区域切除,如下图所示。
否则,这些低少子寿命的硅片会严重影响电池的效率。
3.2微晶和分布晶对电池性能的影响
微晶和分布晶的描述和形貌
微晶分布晶
微晶:
晶粒尺寸小于2mm,呈连续分布,具有一定面积的晶体。
分布晶:
大晶粒上分布具有一定特征的小晶粒。
微晶和分布晶的SEM分析
微晶和分布晶的EDS分析
微晶和分布晶的少子寿命和漏电分析
硅片少子寿命扫描图电池片Rsh扫描图
微晶和分布晶区域大量晶粒的形成,必然有大量杂质作为形核中心参与形核,甚至造成硅熔液中成分过冷,而形成大量微晶和分布晶。
另一方面,由于微晶和分布晶区域大量杂质和晶界的存在,必然也伴随着大量位错的存在,因此,
微晶和分布晶区域是晶界、位错和杂质三者的聚集区。
反过来,晶界和位错对杂质具有很强的偏聚和沉淀作用,而且低温热处理过程,会加速晶界和位错对杂质的偏聚和沉淀。
所以,微晶和分布晶区域是少数载流子的强复合中心,会导致材料电学性能的严重下降。
如上图硅片少子寿命扫描图。
对微晶和分布晶区域SEM和EDS分析显示,在微晶和分布晶区域尤其是其晶界处具有很深的腐蚀坑,而且存在大量长条状SiC和SiN。
一方面说明了微晶和分布晶区域晶界处存在大量的位错、杂质和缺陷,所以具有很高的腐蚀速度,容易形成较深的腐蚀坑。
另一方面,如下图所示,太阳能电池可认为是无数二极管的并联,但是由于贯穿PN结的长条状导电型SiC的存在,会造成电池的严重漏电Ileak甚至PN结短路,使电池性能严重下降甚至报废。
如上图电池片Rsh扫描图所示漏电。
典型微晶和分布晶模拟光强电池性能测试
0.248
7.324
-0.035
0
24.906
0.0186
12.177
结论:
在多晶硅片上,作为晶界、位错和杂质三者聚集的微晶区域,是少数载流子的强复合中心,会严重影响硅片的少子寿命。
而微晶区域,尤其是晶界处垂直于PN结的长条状导电型SiC的存在,会造成多晶硅电池的严重漏电甚至PN结局部短路,使电池性能严重下降甚至报废。
4.硅片各种不良对电池性能的影响
4.1硅锭研磨抛光对电池性能的影响
作为脆性材料,多晶大锭切方后,在小硅锭表面会有机械损伤层存在,包括碎晶区、位错网络区和弹性应变区,其结构如下图所示。
碎晶区又称微裂纹区,是由破碎的硅晶粒组成的;
位错网络区存在大量位错;
弹性应变区则存在弹性应变,硅原子排列不规整。
由于损伤层的存在,尤其有大量微裂纹的碎晶区的存在,在后续的切片、电池片生产和组件生产过程中,很容易成为裂纹的起始点,引起硅片或电池片的隐
裂、微裂纹、崩边和碎片。
因此,多晶大锭在切方成小硅锭后一般都需要通过机械研磨或化学抛光,去除或减小硅锭表面损伤层。
如下图所示,我公司某供应商四五月份硅锭未经机械研磨或化学抛光的硅片在电池线生产的平均碎片率约为1.5%左右,而其硅锭经过机械研磨之后的硅片,平均碎片率仅为0.7%,降低了一倍多。
4.2硅片锯痕、台阶和厚薄不均对电池性能的影响
我公司针对某供应商的锯痕、台阶和厚薄不均片等不良硅片进行了批量实验。
其中锯痕片凹凸深度大于30um,台阶片深度为30~40um,厚薄不均片范围为130~330um。
锯痕、台阶和厚薄不均片由于在硅片上存在局部区域的高低起伏和厚度差异,在电池制造的各道工序会因受力不均而引起碎片率的上升。
在丝网印刷工序,尤其对于硅片局部区域高低突变的锯痕和台阶片,很容易造成电极或背场的漏印,引起电极不良。
如下图所示,锯痕、台阶和厚薄不均片的碎片率、电极不良率和总报废与不良率均明显高于正常硅片,其中总报废与不良率比正常硅片高了4%~10%。
各种不良硅片电池生产对比图各种不良硅片组件生产对比图
4.3硅片的表面沾污对电池性能的影响
手指印造成的硅片表面沾污,在制绒过程中,会出现如下异常图:
原始硅片未清洗干净,表面有有机油污污染或清洗液残留等造成的硅片表面沾污,在制绒过程中,会出现如下异常图:
硅片表面因为有油污等存在,制绒后未
能长出金字塔结构的绒面,如下图所示。
正常金字塔结构的绒面:
由于原始硅片手指印和油污的存在,在制绒过程中无法去除,在PECVD工序会引起色斑。