7附件七铁包修复规程Microsoft Office Word 文档Word文档格式.docx
《7附件七铁包修复规程Microsoft Office Word 文档Word文档格式.docx》由会员分享,可在线阅读,更多相关《7附件七铁包修复规程Microsoft Office Word 文档Word文档格式.docx(22页珍藏版)》请在冰豆网上搜索。
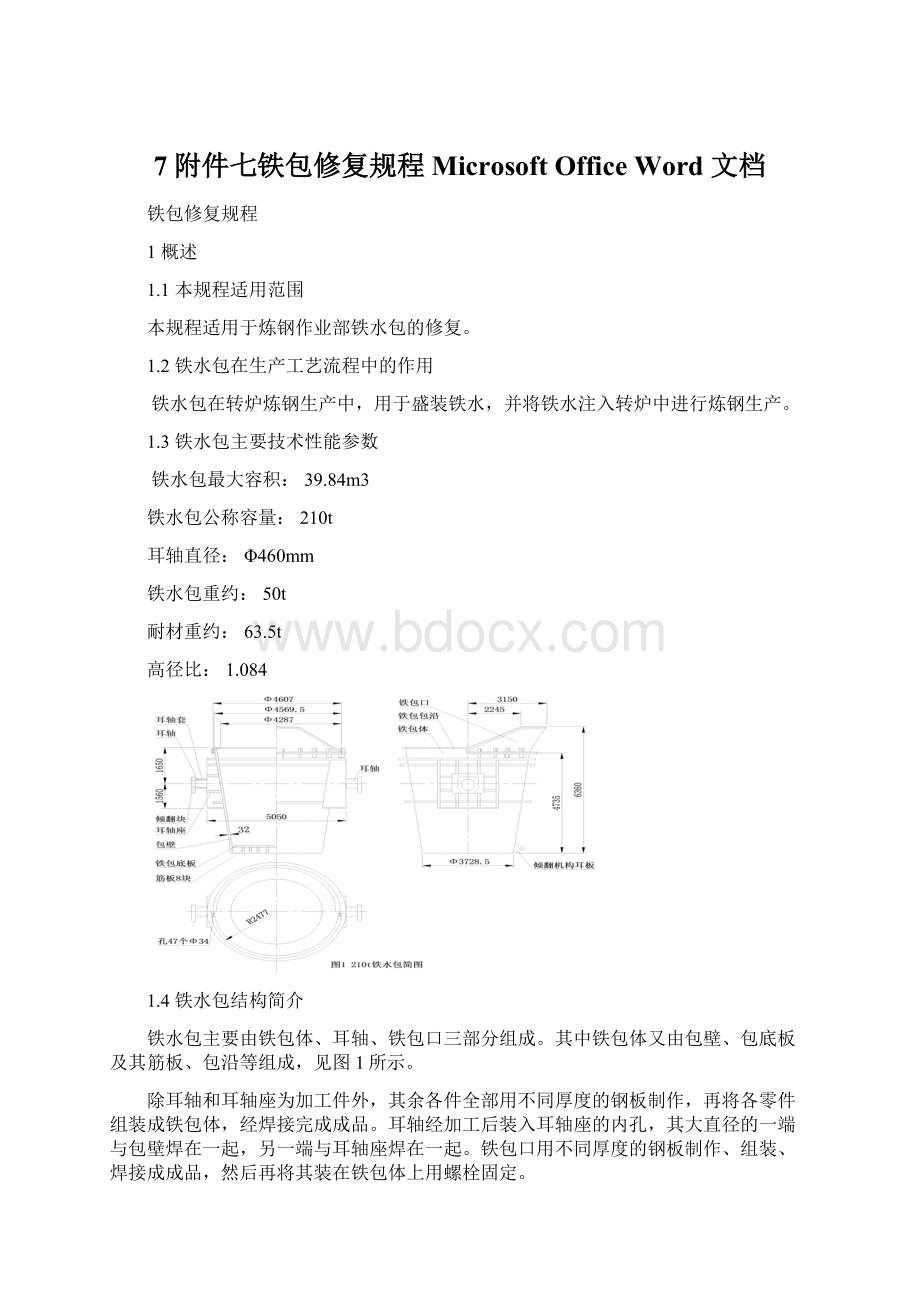
2.2.1.1修复人员的准备
(1)电焊工的准备
1)持有电焊工资质证书的电焊工2名。
2)电焊工应熟知包壁的材质、焊接性能及焊接方法。
3)电焊工应严格执行本规程有关焊接的各项规定。
(2)气焊工的准备
1)气焊工2名,用于旧件的拆除切割,新件的切割安装。
2)气焊工应熟知新、旧件的切割要求(含切割线、坡口角度、切割面的质量等)。
(3)铆工的准备
1)铆工2~4名,用于旧件挖补部位的划线、拆除及新件的制作安装。
2)铆工应熟知挖补部位的尺寸,新件制作的尺寸,安装要求等。
2.2.1.2设备工具的准备
(1)焊接设备工具的准备
1)额定电流500A的直流弧焊机2台(含电缆及焊条夹钳)。
2)清渣用的尖锤、手锤、砂轮磨光机、手砂轮机、扁铲等。
3)焊条烘干箱1台,焊条保温筒2个。
4)碳弧气刨枪(含风管、电缆、碳棒、风源等)1套。
(2)气割工具的准备
气割工具(含减压表、胶管等)2套。
(3)铆工工具的准备
铆工用工具:
大锤、手锤、盘尺、盒尺、钢板尺、直角尺、线坠、洋冲、石笔等,按需准备。
2.2.1.3挖补材料的准备
(1)电焊条的准备
1)电焊条型号E5016,焊条直径Φ3.2mm、Φ4mm。
2)焊条必须是正规焊条厂出品,有生产许可证和产品合格证。
3)焊条要在焊条烘干箱内经过350℃1小时的烘干,随用随取。
4)经烘干的焊条要放在焊条保温筒内取用,禁止随意放置。
(2)气割材料的准备
1)瓶装乙炔2瓶。
2)瓶装氧气2瓶。
2.2.1.4挖补备件的准备
(1)备件用材料
备件用材料为16MnR的钢板,厚度为32mm。
(2)备件的加工
1)按挖补的具体位置确定a、b尺寸及弧度,进行下料、捲板、切割坡口,具体要求见图2。
该件应经超声波探伤检验,应到达JB4730-94《压力器器用钢板超声波探伤》规定1级标准。
2)要求坡口表面平滑、无氧化铁渣及其它污物。
2.2.2耳轴及耳轴座更换前的准备
2.2.2.1修复人员的准备
2)电焊工应熟知焊件的材质、焊接性能及焊接方法。
3)电焊工要严格执行本规程有关焊接的各项规定。
1)气焊工2名,用于旧件拆除的切割及新件的安装、焊前及焊接过程的预热。
2)气焊工应熟知旧件拆除的切割要求、切割方法及预热要求(预热部位、预热温度及预热方法等)。
(3)钳工的准备
1)钳工4名,用于旧件的拆除及新件的安装。
2)钳工应熟知旧件拆除及新件安装的要求。
2.2.2.2设备、工具的准备
(1)焊接设备、工具的准备
2)清渣用的尖锤、手锤、手砂轮、砂轮磨光机、扁铲等。
4)碳弧气刨枪(含电缆、碳棒、风源等)1套。
气割工具(含全部附属件)2套。
(3)预热设施的准备
1)煤气燃烧器按预热部位需要准备。
用气焊火焰预热时还要准备大号焊炬2套。
2)红外线测温仪1件。
3)保温材料
a石棉布15m2,耐火纤维毡2m2,粘合剂0.5kg。
b铁丝15m(Φ0.5~1mm)。
(4)钳工用工具的准备
盘尺、盒尺、直角尺、洋冲、划针、手锤、钢板尺、线坠、钢丝16m(Φ1mm)、水平仪等。
2.2.2.3焊接材料的准备
(1)电焊条型号E5016,焊条直径Φ3.2mm、Φ4mm。
(2)电焊条必须是正规焊条厂出品,有生产许可证和产品合格证。
(3)焊条要在焊条烘干箱内经过350℃1小时的烘干,随用随取。
(4)经烘干的焊条要放在焊条保温筒内取用,禁止随意放置。
2.2.2.4更换件的准备
(1)按铁水包的耳轴图X4316B10-14准备耳轴2件。
(2)按铁水包的耳轴套图X4316B10-29准备耳轴套2件。
(3)按铁水包的倾翻块图X4316B10-28准备倾翻块2件。
(4)将耳轴、耳轴套、倾翻块组装成一体(见图3)。
(5)按铁水包耳轴座图4316B10-9准备耳轴座2件(以铁包体中心线为对称轴,对称制作各1件)。
Φ600孔要留二次加工量5mm,实际孔应为Φ(600-10)mm,即590mm。
2.2.3包底板及其筋板更换的准备
2.2.3.1修复人员的准备
1)持有电焊工资质证书的电焊工4名。
2)电焊工应熟知包底板及其筋板的材质、焊接性能及焊接方法。
1)气焊工2名,用于旧件的拆除及新件的安装。
2)气焊工应熟知旧件拆除切割及新件的安装要求。
1)铆工4名,用于旧件拆除及新件的下料、安装(不含机械加工)、包底板的钻孔等。
2)铆工应熟知旧件拆除要求、新件下料安装要求。
2.2.3.2设备、工具的准备
1)额定电流500A的直流弧焊机4台(含电缆及焊条夹钳)。
3)碳弧气创枪(含风管、电缆、碳棒、风源等)1套。
(3)铆工用工具的准备
铆工用工具应准备:
盘尺、盒尺、直角尺、洋冲、手锤、钢板尺、平尺、手电钻及Φ10钻头等。
2.2.3.3材料的准备
(1)母材的准备
1)16MnR钢板3800×
3800×
40mm1块。
2)16MnR钢板10m2,厚60mm。
3)16MnR钢板600×
350mm,厚80mm1块。
(2)焊条的准备
1)焊条型号E5016,焊条直径Φ4mm、Φ5mm。
(3)气割材料的准备
1)瓶装氧气2瓶。
2)瓶装乙炔2瓶。
2.2.3.4包底备件的准备
(1)用16MnR厚40mm钢板制作包底板(见图4)1件,图中尺寸Φ3730为设计图纸尺寸,该尺寸要与旧包底板核对一下,如有矛盾要以旧包底板尺寸为准。
该件应经超声波探伤,达到JB4730-94《压力容器用钢板超声波探伤》1级标准。
(2)按图5制备加强板,以A—A为对称轴,左、右各1块。
(3)按图6制作筋板8块,尺寸L按旧件尺寸确定,材料用已准备的材料。
断面1—1用于L较长的4块。
较短的4块不开坡口,即无40°
的坡口。
(4)按挡块设计图4316B10-12准备挡块1件(此件为加工件)。
2.2.4包壁裂纹修复前的准备
2.2.4.1修复人员的准备
2)电焊工应熟知铁水包的材质、焊接性能及补焊方法。
(2)铆工的准备
1)用于包壁内外坡口尺寸的划线、裂纹端部的钻孔。
2)铆工应熟知裂纹部位、坡口尺寸。
2.2.4.2修复设备、工具的准备
(2)坡口加工工具的准备
碳弧气刨枪(含风管、电缆、碳棒、风源等)1套。
(3)其它工具的准备
1)手电钻1台、钻头Φ12~15mm1个。
2)盘尺、合尺、钢板尺、线坠、洋冲、石笔等按需要数量准备。
2.2.4.3修复材料的准备
电焊条的准备
(2)焊条必须是正规焊条厂出品,有生产许可证和产品合格证。
2.3铁水包的修复方法
2.3.1包壁损坏部位挖补方法
2.3.1.1将包体摆放在便于挖补的操作位置,达到平稳安全可靠。
2.3.1.2挖补部位的包壁拆除
(1)在应挖补的部位包体的外侧划出拆除的切割线。
(2)按切割线用气割割掉应挖掉部位的包壁,并在包体的切口处切割坡口,见图7。
(3)用手砂轮将切口、坡口表面磨平,清除氧化铁渣。
2.3.1.3挖补部位的新件安装
(1)按示意图8安装新件,找好对口间隙及表面平度,错口量不超过2mm。
(2)新、旧件的点固焊
新件与旧件的对口及表面平度找好后要进行点焊,点固焊工艺参数、焊缝尺寸及焊缝间距等可参考表1所示:
点固焊工艺参数及焊缝尺寸参考表表1
焊条直径mm
焊接电流A
焊缝高度mm
焊缝长度mm
焊缝间距mm
Φ4
160~210
4~6
30~50
300~500
2.3.1.4新、旧件接口的焊接
(1)焊前检查
检查坡口及其两侧是否干净,如有油锈及其它污物要全部清除干净。
(2)焊接
1)立缝采用多层焊,横缝采用多层多道焊,焊接工艺参数见表2所示:
焊接工艺参数表表2
焊接层次
焊道宽度mm
焊道(层)厚度mm
第一层
Φ3.2
100~120
8~10
3~5
第二层及以后各层
10~12
4~5
2)先焊包体内口2层后,在外口清焊根。
清完焊根后,可两面同时焊接同一部位的坡口,要求二人的焊接速度、焊条直径、焊接电流、焊层厚度等要保持一致。
3)每层焊道的起止点,要与上一层的起止点错开20~30mm。
4)电弧引弧要在坡口内进行,禁止在坡口外引弧。
5)每焊完一层将渣皮清除干净,检查焊道有无裂纹、未熔合、夹渣、气孔等缺陷,如有必须清除后再焊下一层。
6)焊缝全部焊完以后,清除渣皮,对焊缝进行全面外观检查,发现缺陷后要及时处理。
2.3.1.5在补装的新件部位钻孔Φ10、孔距500×
500,参照旧包壁的孔的位置进行排列。
2.3.2耳轴及耳轴座更换修复方法
2.3.2.1将包体按常规位置(包口向上)放平放稳,达到安全可靠。
要求两耳轴的上平面在同一水平面上(要提前拆掉铁包口及耐火内衬)。
2.3.2.2耳轴座及耳轴的拆除
(1)将两耳轴座的中心留在包壁上。
(2)用吊车或其它起重工具将耳轴及耳轴座拴挂好。
(3)切开耳轴与包体的连接焊缝。
(4)切开耳轴座与包体的连接焊缝及耳轴座与筋板的连接焊缝。
(5)所有切口不要切伤包体及筋板。
(6)将耳轴及耳轴座移开吊走。
2.3.2.3将包体上的切口用手砂轮磨平,并切割、磨平筋板与耳轴座连接部位的坡口,见图9。
2.3.2.4新耳轴座的安装
(1)按旧耳轴座留在包体上的中心及X4316B10-2设计图安装新耳轴座左右各1件,并找平、找正、找好同轴度。
(2)耳轴座点固焊
1)耳轴座的预热
耳轴座采取预热点固焊。
a预热部位
预热距焊缝100~150mm耳轴座的4个侧面。
b预热方法
用气焊火焰预热。
气焊火焰点燃后缓慢地做往返移动加热预热部位。
c预热温度150~200℃。
d测温方法及测温点
用红外线测温仪观测焊口边缘耳轴座的一侧。
2)点固焊
a点焊缝位置
4条焊缝每条焊接2点,每点的位置距接缝端部200~250mm,见图10。
b点焊缝工艺参数及焊缝尺寸见表3所示:
点焊缝工艺参数及焊缝尺寸表3
150~200
400~500
2.3.2.5新耳轴座与包体连接缝的焊接
(1)焊前检查及预热
1)焊前检查
检查焊口及其内侧30mm范围是否干净,如有污物要全部清理干净。
2)焊前预热
预热耳轴座Φ600孔的内表面的全部。
用煤气火焰均匀预热孔的内表面,预热火焰不要过大,以防耳轴座孔内温度过高,孔外温度又偏低的现象。
用红外线测温仪观测耳轴座焊接坡口的边缘。
1)焊接开始的温度必须达到150~200℃。
2)先焊耳轴座两侧接缝,由二人同时分别各焊一道焊口,焊完后再由二人同时分别焊接上口与下口,直至焊接完毕。
3)采用多层焊,每条焊缝的每层起止点要与上一层起止点错开20~30mm。
同时要求4条焊缝的每层相邻的接点处也要错开20~30mm。
4)要求二人同时焊接的焊接速度、焊条直径、焊接电流、焊层厚度应保持一致。
5)焊条型号为E5016,焊接工艺参数及焊道尺寸见表4所示:
焊接工艺参数及焊道尺寸表表4
焊层厚度mm
层间温度℃
80~100
110~140
6)电弧引弧要在坡口内进行,禁止在坡口外引弧。
7)焊接过程中始终保持150~200℃的温度,当层间温度低于150~200℃时要停止焊接,继续预热,预热过程中要用石棉布将耳轴座及其焊缝覆盖好。
当温度达到150~200℃时方可焊接。
8)焊接过程中,从开始焊接到焊接完毕,每隔10分钟测温一次,做好记录,测温点在距坡口边缘100mm处,每条焊缝不少于1点。
9)每焊完一层将渣皮清除干净,检查焊层有无裂纹、未熔合、夹渣、气孔等缺陷,如有必须消除后再焊下一层。
10)接缝全部焊完后,清除渣皮,对焊缝进行全面外观检查,发现焊接缺陷立即在预热温度150~200℃时进行修补(焊接缺陷详见后文)。
2.3.2.6新耳轴座与筋板连接缝的焊接
(1)该焊缝要在耳轴座与包壁的接缝焊完后,立即开始焊接。
(2)以耳轴座竖直中心线为分界线,由二人同时各焊4条接缝。
(3)焊接要求同2.3.2.5-
(1)-1)、2)a~d和2.3.2.5-
(2)-1)、3)~10)中内容。
2.3.2.7焊后保温
对焊缝全面外观检查及缺陷处理后,要用石棉布(不少于5层)将耳轴座及焊缝包壁的一侧200mm范围内覆盖好,同时将耳轴座与包壁贴近的内孔用耐火纤维毡堵盖好,以免孔内通风使耳轴座冷却过块。
待耳轴座冷却至常温后,揭掉石棉布及耐火纤维毡。
2.3.2.8耳轴座内孔加工
按照图纸4316B10-9及4316B10-2加工耳轴座内孔(该道工序另行安排,不属于本规程的范围)。
2.3.2.9新耳轴的安装与焊接
(1)检查耳轴座内孔加工后的尺寸应符合X4316B10-9图的尺寸(该零件图与组装图标注的图号不符,应该标注成X4316B10-9标注的尺寸)。
(2)按X4316B10-1设计图及图11安装新耳轴2套(含耳轴套及倾翻块)。
(3)耳轴与包壁、耳轴座连接缝的焊接
1)用石棉布(不少于5层)将耳轴座及耳轴(装耳轴套的部位)覆盖好,露出两条即将焊接的接缝。
2)耳轴及耳轴座的预热
插入包壁内部的耳轴的一端的端面预热一个环形面,该环形面宽100mm,环形外圆距耳轴外圆周100mm(见图11所示)。
耳轴与耳轴座连接的接缝的预热部位为接缝内、外侧的端面(见图11所示)。
b预热温度200~250℃。
c预热方法
用煤气火焰沿预热部位缓慢加热,火焰应均匀分布在加热部位进行加热。
d测温方法
用红外线测温仪观测,每5分钟测温一次。
e测温点
两条接缝测温点均测Φ600圆周边缘的任意点。
f两条接缝的预热可同时进行。
3)焊接
a两条接缝可同时焊接,每条接缝由一人施焊。
b采用全位置多层焊,焊接工艺参数及焊层厚度见表5所示:
焊接工艺参数及焊接厚度参考表表5
200~250
c引弧要在坡口内进行,禁止在坡口外引弧。
d焊接过程中,每隔10分钟测温一次,做好记录,直至焊接完毕或焊接缺陷处理完毕。
发现温度低于200℃,要停止焊接进行预热。
e每焊完一层将渣皮清除干净,检查焊道有无裂纹、未熔合、夹渣、气孔等缺陷,如有必须消除后再焊下一层。
f接缝全部焊完以后,清除渣皮,对焊缝进行全面外观检查,发现焊接缺陷立即在预热温度200~250℃时进行修补(焊接缺陷见后文)。
4)焊后保温
焊缝经全面检查及缺陷处理完毕后,用石棉布(不少于5层)将耳轴及耳轴座盖好,包内耳轴端部用耐火纤维毡盖好,覆盖面应超过焊缝200mm以上,将焊缝降至常温后拆掉保温材料。
2.3.3包底板及其筋板的更换修复方法
2.3.3.1将铁包口拆掉,并拆除包内的耐火材料。
2.3.3.2将包体口朝地面摆平放稳,达到安全可靠,搭好操作平台。
2.3.3.3包底板及其筋板的拆除
(1)用吊车(或其它起重工具)将包底拴挂牢固。
(2)用气割切开包底板及其筋板与包壁连接的焊缝。
要求切口距包壁留3~5mm的余量。
焊缝全部切开后吊走包底板。
(3)将余留在包壁的3~5mm焊缝用手砂轮磨掉,达到所有切口处与包壁内表面平度一致。
2.3.3.4包底板的安装
(1)包底板安装位置的划线
按图12划两条包底板安装基准线,并将距包底边缘350mm的一条基准线等分4份,在等分点处装焊100×
100mm,厚度15~20mm的支撑板,要求4个支撑板平面位于包底板基准线的平面上。
(2)将包体翻个(将包体口朝上)并摆平放稳。
(3)安装包底板
将包底板吊入包体内(提前装焊好吊耳),使其落在4块支撑板上,并找平、找正、找好与包壁的接缝间隙,不点焊。
见图13。
2.3.3.5包底板与包壁接缝的焊接
(1)焊接顺序
先焊包体内部接缝的坡口,深度达10mm停焊,翻个焊包体外部接缝的坡口,全部焊完再翻个,继续焊包体内未焊完的坡口直至焊接完毕。
(2)焊接方法
1)将接缝圆周均分4大段,由4人同时焊接,每人焊接一段,焊接方向为同时顺时针(或同时逆时针)方向(见图14)。
每大段采取小分段反向焊,焊缝长度增长方向按图中大段箭头所指,焊接电弧移动方向按小段箭头所示。
分段长度为每大段均分8小段。
2)每大段均采用多层焊,要求4人焊接的焊接电流、焊条直径、焊接速度、焊层厚度等均保持一致,焊接工艺参数及焊层厚度见表6所示:
焊接工艺参数及焊接厚度参考表表6
第一、二层
3~4
第三层及以后各层
Φ5
200~270
3)电弧引弧要在坡口内进行,禁止在坡口外引弧。
4)每焊完一层将渣皮清除干净,检查焊层有无裂纹、未熔合、夹渣、气孔等缺陷,如有必须清除缺陷后,再焊下一层。
5)每层分段的起止点要与上一层分段的起止点错开20~30mm。
6)接缝全部焊完后,清除渣皮,对焊缝进行全面外观检查,发现缺陷要及时处理完毕(焊接缺陷详见后文)。
焊完的焊缝要高出坡口1~2mm。
2.3.3.6包底筋板的安装
(1)将包体口朝地面摆平放稳,搭好操作平台。
(2)按图15安装包底筋板8块并点固焊,其工艺参数见表7所示:
包底筋板点固焊工艺参数及焊缝尺寸表表7
30~40
2.3.3.7筋板与包底板、包壁接缝的焊接
按图15标注的数字(1~8)顺序焊接,即焊完接缝1后焊接缝2,以此类推。
每条接缝先焊筋板与包底板的接缝,再焊筋板两端与包壁的接缝。
1)焊条型号E5016,与包底板的接缝采用平焊,与包壁的接缝采用立焊。
2)每条接缝先由一人焊接一面坡口的第一层,然后两面坡口由二人同时、同方向、同层次施焊,要求二人使用的焊条直径、焊接电流、焊接速度、焊层厚度保持一致。
3)平焊采用多层多道焊,每层(道)要采用分段反向焊,分段长度300~400mm。
焊接工艺参数及焊道尺寸见表8所示:
平焊焊接工艺参数及焊道尺寸参考表表8
焊道厚度mm
160~260
4)每层(道)的起止点要与下一层错开20~30mm。
5)电弧引弧要在坡口内进行,禁止在坡口外引弧。
6)每焊完一层将渣皮清除干净,检查焊道有无裂纹、未熔合、夹渣、气孔等,如有必须清除后再焊下一层。
7)筋板与包壁的接缝采用立焊多层焊,焊接工艺参数及焊层尺寸见表9所示:
立焊焊接工艺参数及焊层尺寸参考表表9
120~160
8)接缝全部焊完以后,清除渣皮,对焊缝进行全面外观检查,发现焊接缺陷要及时处理(焊接缺陷详见后文)。
2.3.3.8包底加强板安装与焊接(设计图X4316B10-2中的件号23)
(1)包底加强板的安装
1)包底加强板要在筋板焊接完工后安装