油罐沉积物Word文件下载.docx
《油罐沉积物Word文件下载.docx》由会员分享,可在线阅读,更多相关《油罐沉积物Word文件下载.docx(19页珍藏版)》请在冰豆网上搜索。
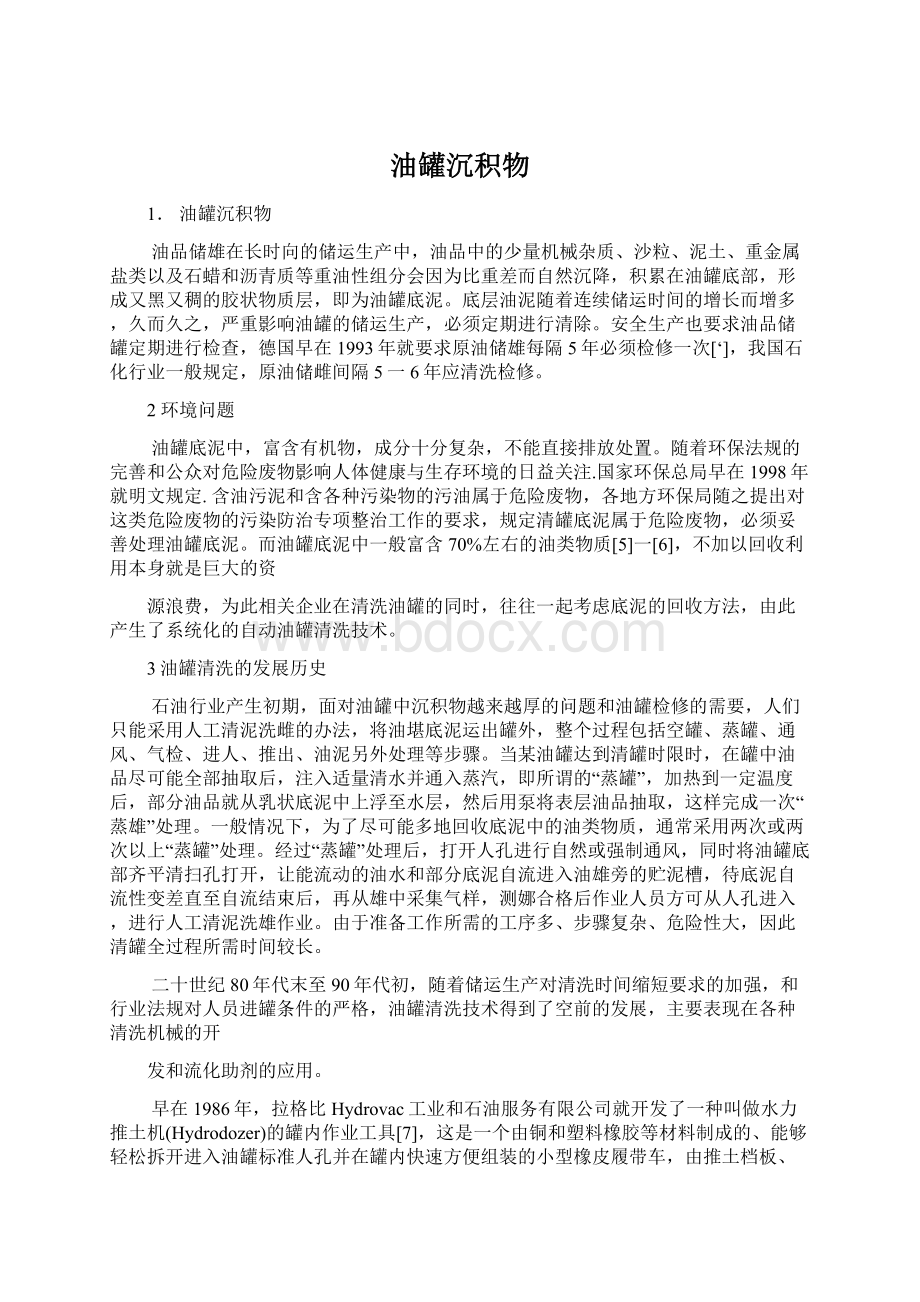
-hoeLTank一Reingung公司在1991年开发了一种原油罐清洗技术[’”〕,其特点是用机械流化的办法,用柴油作为漂洗油,对固着在浮顶原油罐
底部的油泥进行清洗,最后油泥中的烃类物质可全部回收,并且无需人员进罐作业。
机械水力击碎清洗方面,比较典型的是,英国BP石油公司旗下的Leigh服务公司在苏格兰为当时9个大型石油储罐的清洗专门设计了一种用于油罐清洗的机器人水喷头(ro加twaterjetter)[川,利用该技术可以节约50%以上的清洗时间和人工劳动,其原理是水力驱动旋转喷头在罐内上下活动,用水力击松并移走残泥。
加热软化清洗方面的报导很多,但通常不是单纯的加热,经常是伴随着机械击碎(如蒸汽吹扫)和助剂添加。
1989年美国旧金山Nalco化学公司开发了一种原油魄清洗的改进方法[‘2],其开发动机是使油罐清洗处理操作既安全又环保,把油罐清洗工作从以往的开销大、耗时长、体力繁重的老框框中解脱出来。
首先,使原油罐内容量降到尽可能低,此时加入适量的水和化学物质,以使清洗溶液能盖住罐底污泥,然后,加入由柴油或者热油或者类似物组成的稀释剂作为回收烃类物的溶剂,接着加热罐内的混合物至65℃左右,使污泥中的烃类物质流动起来,并穿过清洗液上升到稀释剂中,加热操作通过水循环实现,浮到表层的烃类用泵抽出,经脱盐工序后打入
原油罐回收,最后,将水抽至API分离器,无机固体用冲洗的办法冲走。
类似的蒸汽清洗技术还有FirestoneTire&
Rubber公可发明的专利技术—包含静电场强度和烃汽浓度测量的蒸
汽和不易燃清洗剂清洗〔’3]和BrownED开发的蒸汽法清洗石油储罐和回收烃类技术【’41,以及伪mnichevVA等开发的增强蒸发浓缩清洗〔‘5〕等。
随着工业生产要求的提高,清洗技术得到了不断完善和进化,首先表现在以加强清洗防
爆安全为宗旨的氮气保护技术的不断应用。
巴西氏月emeidaFrancoz等人开发的热化学清洗石油储滚技术[’“〕中就重点介绍了氮气发生体系,该体系由还原性氮盐、氧化性氮盐和酸性活性剂组成,它们相互作用产生氮气和热量,在有利于防爆安全的同时,还有助于污泥和溶剂混合。
其次,为提高清洗效率和洗涤效果,各种专用、高效的喷嘴得到了很大开发。
JePsenEL于1995年开发了清洗油罐内部的液体喷头[‘7〕,该喷头能够自由旋转、绕轴环转,并能以预设的一定角度摆动,这样就能使罐底部的每
个区域都得到有效的清洗。
其它专利还有,ManabeN于1994年发明的在防止清洗喷射过程中喷击压力降低的喷头〔‘“〕,以及1992年RechtzigelA开发的两端喷射的高压喷头〔‘9〕
等。
最后,为了进一步缩短清洗时间,美国BP石油公司甚至提出了不停产清除底泥的罐清洗系统〔20〕_
在喷头流化技术、油泥分离技术和综合安全技术日益完善以及早已成熟的电子自控技术的基础上,具有作业安全、环境友好、经济高效的系统化自动清洗技术自然矜生。
这些技术的共同特点是,油泥清出和分离自动化,油泥彻底无害化和资源化。
其共同的工作原理是,用高效的液体喷头击碎油泥和洗涤罐底,用泵或其它方法抽出,油泥在罐外就地加热并分离,分离后的油相(或适当加入同种油类)作为溶剂加压返回罐内作为喷头冲洗液,达成一个循环回路,在连续的内外循环中,水和无机物在罐外得到不断的去除,罐内的残余相变得越来越纯,最终变成可回炼的原油。
4国外几种系统
4·
1.LABO系统[川
泰福德(般爪荀吨)技术公司在油罐自动清洗领域处于世界领先地位,其开发的BI沪田0系统的原则流程如图1。
主要技术特点有:
一是模块化,整套系统可以分为几个单元模块,根据不同油罐的清洗要求,可把几个模块的设备分开、串联起来灵活使用,以满足不同的需要;
二是自动化,全套清洗、分离设施实现P比控制;
三是密闭化,清罐前不需要蒸罐、通风、开人孔等一系列繁锁又耗时的准备工作,整个清雄、油泥处理过程无需要人员进入罐内,无恶臭污染;
四是专业化,利用其专利喷头和交替使用的容积泵和离心泵,建立特有的油罐体内外大循环,来实现自动清洗油罐、自动清出罐底油泥的目的;
五是便捷
化,全套油罐清洗和油泥分离系统均可以分装在若干个集装箱内,安装移动较为便利。
采用这种方法,在12一16天内即可清洗1座10万衬油罐,回收的烃类物质接近100%。
4.2cow系统[221
日本大凤工业株式会社研制的COW清洗系统其原则流程如图2,在东南亚、欧洲、中东等地区的陆上石油储魄清洗方面得到广泛应用,该技术是利用特殊的液体喷射装置,采用“种类油品、全封闭、机械自动循环”的物理清洗技术。
罐底有机沉积物经过喷射、击碎、溶解等步骤后完全复原成标准质量的原油。
其主要有以下技术特点:
一是罐底有机沉积物全部·
回
收;
二是清洗工期短,固定化,据资料介绍,10万耐油罐的清洗作业时间为巧天,仅为国内传统清维时间的四分之一;
三是全封闭式清洗,无需人员进入罐内作业,惰性气体控制雄内可燃气体,安全有保障;
四是无环境污染;
五是清洗效果好,清洗后罐内表面可现出金属本色;
六是98%沉积物复原成原油,回收率高,综合经济效益十分明显。
5国内进展
我国石化行业由于起步晚,油罐清洗技术与世界先进水平还存在着一定的差距,许多炼油厂尚停留在人工清泥洗罐的现实生产阶段。
最近几年来才有一些科研院所在进行试验研究
和对国外先进技术的应用研究,个别炼油厂正在进行油罐自动清洗技术的国产化探索。
直到1993年,才开始有人关心原油罐底泥的清除和利用[23],高光军等〔2’]于1995年通过对几种原油罐罐底油泥方法的比较后,认为整体加热法清理罐底油泥是一种经济、有效的清理方法,并用该法清理了6座原油罐底泥。
同年,wangC和Chenx等人开发了用于油罐清洗的喷头〔251,具有喷击压力高、能360℃旋转、使用安全等特点。
石油天然气管道技术公司在1998年进行了COW油罐清洗工艺在我国首次现场应用[26〕,结果表明,它比人工清罐具有原油回收率高、无环境污染、施工周期短、安全可靠和机械化程度高等优点。
接着,中国科学院力学研究所环境科学与技术中心也在世纪之交进行了罐体油泥自动清理系统研究[27],通过一个工程应用,给出了一套能解决油田罐体含油泥砂自动清理及无污排放难题的工艺流程。
进入新世纪后,镇海炼化公司首先进行了系统化油罐底泥自动清洗技术的国产化探索。
采用国产设备配套组装的油罐底泥处理成套装置其原则流程如图3,已经能使油罐底泥中油、泥、水得到有效地分离,同时,用于自动清洗的喷头技术以及离心机在油罐底泥综合处理中的优化配置研究也正在紧罗密布的研制试验中,用于油罐自动清洗的整套设备国产化是完全可能的,其性能和效用上可以达到进口成套装置的水平,而其价格上有很大的优势,如果引进处理量为120m3/h的成套设备,泰福德公司的BLABO系统的价格为180万美元,日本大风cow系统的价格为130万美元,而相同处理能力的国产成套系统的价格约为60万美元左右,可见,开发具有我国自主技术产权的油罐清洗成套设备具有很高的经济价值。
5总结
油峨清洗方法包括机械清洗、化学清洗、水力清洗、燕汽清洗等,雌内使用可自动控制的高效喷头,添加适当的助溶、助流化清洗剂或者相同性质的原料油,进行喷击流化,罐外用离心分离等方法就地处理罐底油泥,实现烃类回收。
国外油罐清洗的工艺、方法及设备与设备组合已经实现了模块化、自动化、密闭化、专业化和便捷化。
国内刚开始使用机械法、化学法和加热法清除油罐底泥的研究,油泥处理方面,已经考虑了无污染排放,系统化的油罐自动清
原油储罐清罐方法概述
1前言
根据有关储油罐修理的规范规定,储油罐每运行5一7年要进行开放检查、修理,这时就要对储油罐进行清罐。
清罐就是要除去堆积在油罐底部的淤渣及罐
壁上的凝油和凝蜡。
原油储罐里的淤渣通常由无机沉积物和有机沉积物组成。
无机沉积物包括铁锈、砂、泥浆及湿性碳等;
有机沉积物包括原油、蜡、沥青等。
分析原油储罐的沉积物,发现原油和蜡占全部淤渣的80%一95%,其他除了水之外,无机沉积物很少。
由此可见,原油储罐的
沉积物中大部分是有用的物质,应加以回收利用。
2清罐方法
2.1理想清罐方法应具有的特点
原油储罐的清罐方法很多,最理想的清罐方法应具有以下特点:
(l)清罐工期短。
一般原油储罐的每一次开放检查、修理需要3一6个月的时间。
在我国的原油罐储能力很低的情况下,应尽量缩短原油储罐的停用时间,提高原油储罐的利用率,对大型储罐来说更应如此,因此,在清罐这个环节应尽量缩短工期。
(2)清罐过程应安全可靠。
这不仅指清罐过程要符合防火、防爆的安全规定,也包括操作工作的人身安全。
(3)要尽可能地多回收原油,减少废弃残渣量,提高资源的利用率。
(4)最大限度地减少污染。
(5)节省劳动力。
(6)清罐方法及工艺流程要简便,易于操作。
(7)清罐方法要具有一定的特立性,即不需要太多的外部条件支持。
(8)要具有较高的经济性。
2·
到目前为止,原油储罐的清罐方法主要有以下几类:
2.2.1人力手工清罐法将储罐的油位降到最低点后,打开所有的人孔,用小泵将罐内的剩余原油吸出,用鼓风机向罐内鼓风,然后几乎所有的清淤工作都由人力来完成。
这是一种最落后的清罐方法,作业工人的劳动强度大,作业环境恶劣,危险性很高,且清罐工
期长,造成的环境污染也很大。
2.2.2热油循环清罐法这种方法是采用同种原油作为溶剂油将沉积物完全覆盖,然后通过加热器或热交换器加热,将沉积物升温到它的溶点以上,使沉积物溶解分散到溶剂油中,这一过程中要充分进行搅拌,以促进溶剂油的流动。
该方法需要大量的热源。
一座100000澎的原油储罐,如果按搅拌机可以开动的高度4m高计算,其需要加热的原油量近20000澎,假设提高温度40℃,同时考虑散失的热量,所需蒸汽量达1500t至2000t,并且连续加热20~30天。
这么大的热源需求量,如果不
是邻近炼油厂的储罐很难得到满足。
另外,经加热回收的油分很容易再凝固。
对凝固的沉积物加热后,虽然升温时沉积物具有了流动性,但是冷却后会再次凝固,并且比原来的凝固状态还要硬。
这是因为,加热前积物是微粒状的结晶,轻质油介于结晶之间,微小结晶和轻质油一起沉降堆积;
但是一旦加热后,轻质油就扩散了,只剩下具有结晶性质的沉积物溶化流动,经回收转运到另一个油罐冷却后,就结成巨大的结晶而沉降,产生更难处理的残渣。
2.2.3热水循环清罐法这个方法也是对沉积物加热溶化而除去的,但不使用油而使用水,洗效果比用油要好。
使用热水比用油有两个优点:
第一,热水对沉积物的热传导性好。
第二,溶化的油可以漂浮在水面上,可以长时间起到保温的效果,且油的流动性不丧失,其结果是能够回收较多的原油。
通常使用溢流法使漂浮在水面的原油流出并收集。
即在检修孔盖上安装溢流用的堤坝,抬高水位,原油就流出来了。
该种方法也需要大量的热源,而大部分热量都要浪费掉,经济性很差,并且需要大量的水还要产生同样多的含油废水,如不进行污水处理会严重污染环境。
2.2.4化学药剂清罐法在实验室已经证明有些化学药品具有破坏沉积物的乳性、溶解残渣、提高沉积物分散性的能力,但是在大型储罐的清罐应用中效果并
不理想,还在进一步的研究中。
2.2.5机械清罐法国外搞机械清罐研究的机构有很多,采用的方式也是多种多样,总体上可分为两种:
一种是采用机器人作业方式,机器人在罐内可以自动移动,打散或吸出罐内沉积物。
另一种是采用同种油喷射方式,比较典型的是日本的cow的清罐系统,目前国内已经引进了该系统。
cow方法清洗源油储罐的工艺过程是:
先将被清洗原油罐内的原油全部倒到另一个油罐内,同时将喷嘴安装在罐顶的支柱口或罐壁的人孔上,用管道连接喷嘴、泵和供油罐。
用同种原油作为清洗剂。
然后用氮气填充罐内空间,并在清洗全过程启用气体浓度监视器。
通过高压泵将清洗油泵至喷嘴,使其集中喷射,以破碎沉积物并将其溶解。
回收分离溶解后的淤渣通过排放阀和过滤器将其排除,并将分离出的清洗油打回供油罐。
经过两遍原油喷射清洗和一遍热水喷射清洗,罐内只剩下由砂子、铁锈和含碳物质形成的固态残渣,只需很少的手工清除工作。
COw油罐清洗方法的优点有:
(l)原油的回收率高。
cow方法可以最大限度地回收罐内沉积物中的原油和蜡,仅剩基本不含油的铁锈、砂子等,经济效益极好。
用cow方法清洗100000澎油罐,需人工处理的沉积物只有几十吨。
(2)清洗过程不用蒸汽,清洗成本低,同时不会使沉积物的凝固点增高,不会产生再次沉降。
(3)清罐工期短,可以减少油罐停修期。
该方法的施行不受气候等因素的影响,清洗一座100000扩油罐只需15天。
(4)安全性强,用人工少。
为了操作安全,采用了充入氮气,控制氧气浓度在8%以下,提高油气浓度到11%以上的双保险措施,克服了产生静电的因素。
而且人员进入油罐前,罐内只剩油砂和铁锈,基本消除了油气,操作人员的作业环境得到极大的改善。
cow方法需用人工仅7人。
(5)不造成环境污染,资源可再利用。
cow方法可不使油气挥发,回收油砂可再利用,制造高级的清洁剂,因此不会对环境造成污染。
一座s000om3原油储罐约有沉积物1000一Z000t,一座l00000m3原油储罐约有沉积物3000一s000t,通常国内大多将原油储罐内的沉积物作为废油处理,既浪费了宝贵的资源,同时也造成巨大的经济损失。
目前国内清罐大多采用原始的人力手工清罐方法,随着我国大型原油储罐的增加和环意思的增强,要将我们的储运管理水平向国际标准靠拢,我们应尽早淘汰落后的清罐方法,特别是在大型储罐的清罐中大力推广机械清罐方法。
人工清洗与机械清洗原油罐的比较
中国石化巴陵石油化工有限责任公司烯烃事业部(以下简称烯烃事业部)罐区现有4台3义104时外浮顶原油罐,其中T3n一01、T3n一02、14于1999年12月建成投用。
经过5年左右时间的运行,淤积在罐底的泥沙等杂质越来越多,使油罐有效容量减少。
油泥淤积在罐底使原油加温效率降低,蒸汽消耗量增大。
油泥混合使原油脱水困难,操作人员劳动强度增大。
油罐内壁、浮舱涂料层脱落,存在穿孔漏油危险。
罐顶平台、裙边及附属的楼梯、消防水管线等腐蚀严重,存在安全隐患。
按照《立式圆筒形钢制焊接原油罐修理规程》规定,“油罐的修理周期一般为5一7年,新建油罐第一次修理周期最长不超过10年”。
因此,必须有计划地安排对原油罐进行清罐和检修。
传统的油罐清洗方法主要是人工清罐。
人工清罐虽然设备简单、劳务费用低,但存在施工周期长、环境污染大等问题。
一些炼油厂的清罐经验表明,人工清洗1台3x104耐的原油罐至少需要45天,加上油罐检修时间15天,清洗、检修一台原油罐共需要2个月时间。
目前,烯烃事业部生产任务十分繁重,原油罐容非常紧张,很难腾出油
罐进行这样长时间的清罐和检修。
1原油罐运行现状
烯烃事业部以加工低硫石腊基原油为主。
建厂之初,原油加工设计能力为1xl叭/a,原油罐组正常生产时,一罐收油,一罐沉降脱水,一罐付油。
常压装置加工量按3xl护t/计算,一罐原油可供常压装置加工8天。
加工的大庆原油居多,原油含油泥较少,油水乳化情况不严重,原油收付、加温脱水时间充足。
原油库存量一般能保
持在5xl叭左右。
原油罐容不显得紧张。
2001年6月,配套1.05x106t/aARGG装置扩能改造,常压装置处理量提高到1.92x106t/a,比原设计扩大了约1倍,一罐原油仅供常压装置加工4天。
加工的原油,品种越来越多,除大庆原油外,还有韦杜里、尼罗河、卡宾达、白虎等混合油。
有些品种的原油含油泥较多,油水乳化严重,原油脱水困难。
特别是当原油运输不畅或原油资源紧张时,原油库存量严重偏低,库存量时常不足3x104t,最紧张的时候原油从进厂到送常压装置,加温脱水时间前后不到3天,时间十分匆促,操作人员必须坚持24h现场脱水。
原油罐区以1xlo“t/a的储存能力担负近2xl护t/a的加工任务,原油罐容几乎成了影响装置扩大加工量的瓶颈。
在一时不能增建原油罐的情况下,生产上很难空出原油罐来进行长时间的清罐和检修。
因此,具有机械化程度高、清罐时间短等优点的机械清洗工艺成为烯烃事业部原油罐清罐的首选。
2机械清洗装置与工艺简介
机械清洗装置是一个复杂的系统,主要由移送装置、清洗装置、清洗喷嘴、自动过滤器、气体浓度检测装置等几部分组成。
根据烯烃事业部原油储罐的现场分布及使用情况,可以按照T311一01、邓11一02、T311一11、犯311一14的先后顺序对4台油罐逐一进行机械清洗。
以清洗份11一01为例,为了不影响其它原油罐的正常使用,可将顶水罐犯311一16作为清洁原油供给罐。
首先用倒罐泵把T3ll一01的罐底油抽到不能再抽为止。
将能进行上下摆动和3600转动的清洗喷嘴安装在浮舱的支柱孔、检修孔、排气孔等位置。
用清洗装置中的清洗泵将T2311一16中的清洁原油抽出,打人安装在T311一01浮舱上的清洗喷嘴,清洗喷嘴将清洁原油向止清洗过程中产生的静电引起火灾,要向T311一01油舱内补充一定量的工业氮气,气体浓度由检测装置进行检测,使油舱内的混合气体浓度控制在爆炸极限之外。
溶解的原油和淤渣由移送装置吸到抽吸槽中,经自动过滤器过滤除去泥沙后,再将清洗油送回清洁原油供给罐代311一16,重复使用。
最后用温水代替清洗油,再进行循环清洗。
T3n一01机械清洗工艺流程图如图1所示。
通过这种清洗,T3ll一01罐内的油组合基本上被清除,剩下的泥沙等杂质待打开人孔后,由人工进行浩们_
3机械清洗工艺的优势
3.1清罐工期短、综合效益好
人工清洗1台3x104耐的原油罐至少需要45天。
机械清洗1台3x104耐的原油罐一般只需15天,所需时间只有人工清洗的123。
以清洗
T3ll一01原油罐为例,来估算机械清洗的经济效益。
(1)人工清罐的隐含效益损失
T311一01罐容3x104砰,油罐直径46m。
清罐前检尺,假设淤油平均深度为0.sm,淤油量为3.14X23,火0.5=531耐;
假设残留物约为
3m3。
能以原油价(1500元l耐)收回831一3=828耐,计828x1500=124.200万元。
人工清罐清出的淤油按油泥油渣出售,以600元/耐计算为831x600=49.860万元。
考虑到人工清罐的劳务费一般计算在淤油的折价里,不另外支付劳务费,即49.860万元相当于支付了劳务费。
那么前后二者差价为(831一3)x1500一831只600二74.340万元,也就是人工清洗T3ll一01罐隐含效益损失74340万元。
(2)机械清洗成本计算
根据某施工单位提供的机械清洗预算,3x104砰原油罐机械清洗总成本由以下几方面构成:
人工费5.980万元,设备折旧及仓库租赁费为13.080万元,现场机械费为1.500万元,配件加工及工程材料消耗费为2‘690万元,排污费2.100万元,原材料费4,519万元,办公费为1。
000万元,设备维修费8.350万元,氮气费18.000万元,其它费用为5.450万元,合计总费用为62.669万元_
机械清洗虽然施工费用高,但可将罐底淤渣中的油组分基本全部回收,按正常的原油价格计价,共回收124.200万元,即除支付总费用外,仍有124.200一62.669=61.531万元的直接效益。
而人工清罐方法,虽然施工费用低,但是约占油罐容量2%一4%的罐底淤油需折价按油泥油渣销售。
按前面的计算,人工清罐的隐含效益损失为
74.340万元。
另外机械清洗方法可减少油罐停用周期,提高油罐的利用率,有利于增产增效。
3.2不污染环境、安全性能高
传统的人工清罐方法,清罐前要进行蒸罐,对罐底沉积物加热,造成油气大量挥发,既损失了原油中有用的轻组分,又污染了空气。
对清出的油渣、淤泥进行堆放、废弃,也会造成环境污染。
机械清洗工艺不向外排放污油和污水,也不会挥发出大量油气。
污油经油水分离器分离后,水作为清洗介质再循环使用,分离出的原油被回收,不对环境产牛污染。
人工清罐方法,大量的油泥、淤渣要靠作业人员进人罐底手工清除,工作环境差,劳动强度大。
从安全上考虑,进罐作业存在作业人员缺氧窒息和可燃气体含量超标引起火灾爆炸的危险。
机械清洗工艺,清洗设备代替人工,由清洗喷嘴在密闭的原油罐内进行喷洗作业,施工人员在油罐外面操作机器,清洗过程安全性高。
3.3回收原油质量稳定、收率高
人工清罐方法,用大量蒸汽蒸罐,让凝油直接与蒸汽接触,使凝油融化,回收原油中的轻质组分被挥发掉了,破坏了回收原油的质量。
而机械清洗工艺是用清洁原油冲击沉积物、使其