高效相变换热器Word格式.docx
《高效相变换热器Word格式.docx》由会员分享,可在线阅读,更多相关《高效相变换热器Word格式.docx(15页珍藏版)》请在冰豆网上搜索。
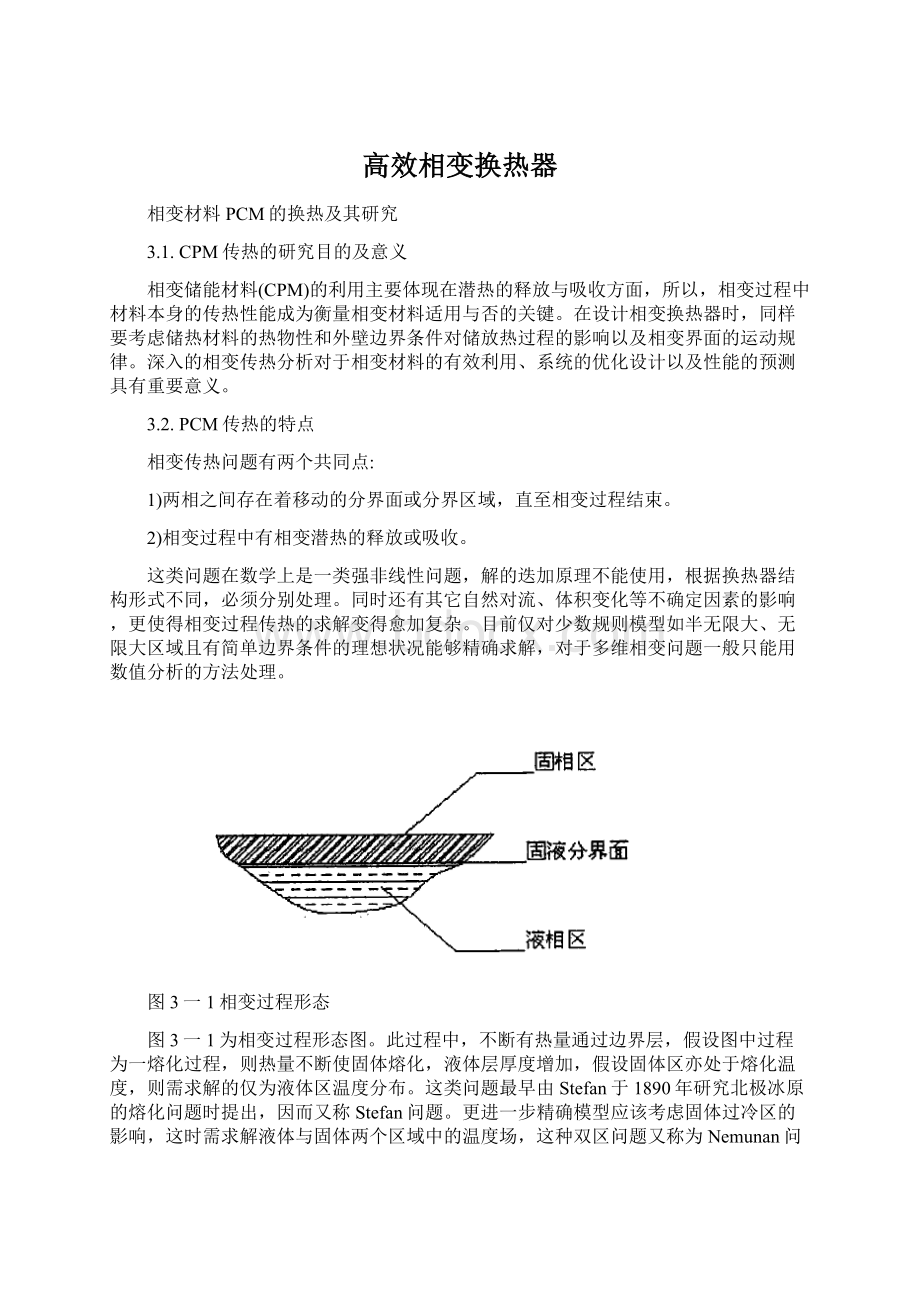
关于相变换热的强化方法有很多种,其中各种不同形式的肋片管是较为常用的。
L.F.Cabeza以冰蓄冷换热过程为例,分析了传热工程中的瓶颈问题,指出随着液一固界面的移动,热阻逐渐增加,热流密度逐渐下降。
他提出这种问题可以通过强化传热来改善。
在实验中他给出了三种方法,并对此做了对比分析。
强化传热方法分别为加装不锈钢管束、加装铜管束和对PCM进行渗碳处理。
另外他还发现,加装肋片强化换热只对使用较高导热系数的CPM时才有明显效果。
D.Buddhi分析了研究相变时液一固界面的两种方法研究,通常采用热电偶测温的方法,另外一种是光导纤维法,即从光学角度通过图象的变化反映相变。
通过对比曲线图分析,发现光导纤维的测量结果要比热电偶准确,较能反映实际过程。
J.Bnaaszek等将PCM(以石蜡即w一20为例)卷绕成层状圆柱形嵌入特制换热器中,通过试验分析其融化和凝固特性。
探讨了影响总换热系数的因素及对换热器进行可用性分析。
uJnFukai〔川等人曾研究过用石墨作为强化传热材料用于PMC的相变换热。
他们将碳纤维散布于PCM中,这些纤维所占体积比很小,且很容易散布。
通过这种方法,显著增强了PCM的导热系数,实验样品为石蜡、丁苯聚合物等。
为了提高石蜡、酉旨酸类PMC的导热能力.通常在其中添加金属粉末、石墨粉、金属网以及在封装壁加肋片,增强导热。
AyerS和Flethcer综述了在金属网中加入石墨.以提高材料有效导热系数的研究进展。
文中强调:
加入石墨,可以显著提高材料的导热系数。
我国梁新刚等和张娜等对两相混合或组合材料的导热能力的理论研究,以及对混合、共融PCM的LTES研究具有重要的意义。
Bugaje对20种低导热系数的PMC做了添加20%v/v星状铝肋片的实验,表明;
储热(融化)时间减少2.2倍,放热(固化)时间减少4.2倍。
Faghri及合作者对内肋化管内PCM的融化TLES系统进行了一系列研究,结果证实:
内肋化可显著提高TLES的储热速率。
另外,velarj等、陈钟顽等也进行了类似的研究,并得到相近的结果。
王超等采用十七烷为相变工质,实验研究了水平圆管和两种肋管外的凝固过程。
通过导热和自然对流两种控制机制下的实验,揭示了自然对流对凝固换热的阻碍作用、肋片管对凝固换热的强化规律以及肋片管的放置位置对凝固量和凝固层形状的影响。
清华大学〔川对板式相变换热器作了实验研究,建立了板式相变储换热器性能实验台,根据蓄冷装置在实际应用中的运行情况选择了实验工况(流量和温度),进行了相应实验,研究了不同因素对其储热特性的影响,整理出相应的蓄冷曲线、取冷曲线。
模拟结果与实验结果基本吻合,从而为利用所建模型进行相变储能系统的设计和性能优化提供了可靠性支持。
复合相变换热器技术与装置
1技术简介
煤、石油、天然气等均为含硫燃料,燃烧时都会产生二氧化硫、三氧化硫,其中三氧化硫与水蒸气结合形成硫酸蒸汽。
锅炉尾部设备中的金属壁面温度若低于硫酸蒸汽的凝结点(酸露点),就会在其表面形成液态硫酸(酸露)。
长期以来,空气预热器作为锅炉尾部受热装置因壁温过低而引起的酸露腐蚀、灰堵现象经常发生,并一直得不到有效解决,因而.以往的各种锅炉设计通常以牺牲锅炉热效率为代价.通过提高排烟温度来缓解(而不是根除)酸露腐蚀现象.而单纯提高排烟温度势必造成大量的低温热源浪费。
尽管如此,空气预热器往往运行一至两年后依然出现腐蚀,直至穿孔,这是困扰锅炉界的一个世界性难题。
“复合相变换热器技术与装置”是一种广泛适用于各种燃煤、燃油、燃气锅炉、工业窑炉以及冶金、石化等各种换热设备的新型高效节能专利产品。
它来源于上海交通大学杨本洛教授的原创性设计理念及其9项发明专利技术,是“热力学、传热学与锅炉原理、自动控制以及现代计算技术”的综合创新和高效集成,它较好地解决了锅炉排烟温度难以降低的世界性难题,是中低温热源利用上的一次世界性突破。
其核心内涵在于:
1)大幅度降低各种锅炉热流体(烟气)的排烟温度。
在世界范围内,首次提出并实现了将“排烟温度与壁面温度之差”从“倍数”关系转变为“加减”关系,使排烟温度出现“量级”意义上的变化:
一般工业锅炉可降低30~90℃,个别可降100℃以上,电站锅炉可降低20~50℃;
从而使大量中低温热能被有效回收利用(提高锅炉热效率1.5%~6%,个别可达7%以上),并相应大量减少燃烧尾气(S02、C02)排放,具有节能、减排双重功效,经济效益、社会效益十分可观。
2)在世界上,首次提出并实现了锅炉尾部换热器金属受热面最低壁面温度始终处于“可控可调”状态,并适应各种燃煤、燃油、燃气锅炉及传热负荷的变化。
3)大幅度降低锅炉检修停机损失和换热器维护成本。
在降低排烟温度的同时,使锅炉换热器金属受热面壁温保持较高温度水平,远离酸露点的腐蚀区域,从根本上避免了酸露腐蚀和堵灰现象的出现。
4)大大延长了锅炉尾部换热器的使用寿命。
在保留了热管换热器高效传热的同时。
克服了一般热管换热器使用一段时间后容易产生不凝气体,从而逐渐老化以至失效的致命弱点。
复合相变换热器作为原创性节能发明专利技术.2000年12月通过了由两院院士参加的国家级鉴定,鉴定意见指出:
“该项技术是相关设计理念的一次创新,为国内外首创,处于国际领先水平”,建议“将此技术进一步在锅炉、工业炉窑以及石油化工等行业的换热设备上推广应用,尤其在大型电站
锅炉的应用上提高自动化水平。
”2007年3月,“复合相变换热器在锅炉上的应
用专家研讨会”会议纪要指出:
“复合相变换热器原理与实用技术方案可行,并在实际应用中得到了验证.使用该产品将对工业锅炉的节能改造起到良好的推动作用”。
2设计原理
由于是“设计理念”的创新,所以可根据不同应用背景,设计和组合出复合相变换热器的许多变化形式(如图1所示)。
复合相变换热器(FxH)的基本
工作原理是:
蒸发段:
烟道内的F>
(H吸收烟气热量.使得FXH管内热工质处于相变状态。
冷凝I段:
管内蒸汽(相变态热工质)沿上升管进入冷凝I段,在冷凝I段中管内蒸汽对管外冷空气加热。
冷凝¨
段:
管内蒸汽经冷凝l段后继续上升至冷凝lI段,在该段中蒸汽被冷凝成液体,并沿下降管回到FXH下段。
通过流量调节,从而实现了壁面温度可控可调
图1FXH复合相变换热器基本工作原理
3与热管技术的不同
热管是一种高导热性能的传热部件,它通过管内介质在高度真空下从加热段吸收热量,通过沸腾蒸发形成蒸汽,向冷凝段流动,把热量输送到冷却段。
从而实现热量转移。
具有很高的导热性,良好的等温性,冷热两侧的传热面积可任意改变。
可远距离传热,可控翎温度等优点。
由于传热是通过管内部介质相变进行的,管内的工质因为反应会产生不凝性气体,不凝性气体的存在大大影响了其工作效率。
因此,热管存在一定使用年限。
分析不凝性气体产生的原因有以下几点:
1)热管工质内部的微溶性气体经长时间工作的析出,造成热管性能下降。
2)热管内表面和工质内杂质存在,在热作用下发生化学反应造成不凝气体产生。
3)热管管壳有微漏,那些不凝气体,如氢,氦等微溶或不溶性气体分子的向内渗透。
4)工质与管壳的不相溶,造成不凝气体产生。
现有的热管换热器大都是由很多根热管拼装而成,由于热管生产过程中的制造差异,每根热管不凝性气体的产生比率也不一样,只要其中部分热管的不凝气达到许可极限,整个热管换热器换热效率就会下降,下降到一定程度时,传热效率急剧下降,这台热管换热器就报废了。
而热管的替换和更新费用巨大。
因为热管是利用高度真空下管内低温介质的相交过程进行热量传递的,因此,一根热管一旦成型。
其传热性能也将确定,其璧面温度即固定为管内介质在该真空度下的饱和温度,不能调整。
因此,用其组装的热管换热器也是不能根据用户的工况变化而对其璧温进行调节的。
当用户工况变化时其尾部受热面的最低壁面温度仍有可篦会低于酸露点温度.不能避免酸露导致的腐蚀。
上世纪九十年代初,热管换热器曾在空预器改造中一度被推广,但后来由于热管普遍存在产生和积累不凝气体。
逐渐老化和璧温不可调节等不足,厂家却对应用热管换热器采取了谨慎的态度。
复合相变换热器技术中“相交段”的概念是将原来热管换热器中一根根相互独立的热管,构造成整体热管。
保证“相变段”受热面最低壁面温度只有微小的梯度温降。
同时,利用相变传热的原理将被壁面温度的可控可调(恒定或调高调低)。
换热器金属受热面最低壁面温度处于可控可调状态,使复合相变换热器能够在相当大幅度内,适应锅炉的各种煤种以及传热负荷的变化,使排烟温度和壁温保持相对稳定;
保持金属受热面壁面温度处于较高的温度水平,远离酸露点的腐蚀区域,从根本上避免了酸露腐蚀和堵灰现象的出现,复合相交换热器的最低壁温不仅是设计时可以任意选取,且在锅炉运行时可通过自动控制设备容易地保持在一个不变的数值。
例如在70%负荷时,如果希望最低壁温保持不变,则可以通过自动控制,排烟温度会自动升高,从而使最低壁温仍保持在原设计的烟气酸露点温度以上的水平,这一点对锅炉来说是极其安全的,与传统节能方法相比是基本设计理念的变化,该技术在世界上首次提出和实现换热器的局部在“整体意义上壁温可控可调”的概念,将制约有效利用余热的。
壁面温度与排烟温度的差”从以往的“倍数”关系变为“加减”关系(见图2)。
从而能够在有效避免“低温腐蚀和灰堵”的同时。
使”节能幅度”出现了“量级”意义的变化。
图2FXH换热器温度分布
热管空气预热器和复合相变换热器空预器的最低壁温与排烟温度问的关系由表1所示:
复合相变换热器壁温达105℃时,排烟温度仅120℃,若热管换热器壁温也要达到105℃时,排烟温度必须达到190℃。
这里排烟温度之差为70℃。
这就是热管空气预热器与复合相变换热器空气预热器的节能幅度差值。
设高硫渣油燃烧的蒸汽锅炉要求空预器最低壁温为145℃,采用复合相变换热器要求排烟温度为160℃,若用热管换热器则得排烟温度为270℃。
这里排烟温度之差为110℃。
可见在烟气酸露点温度愈高时,复合相变换热器愈能显示出它在节能领域中的独特优势。
FXH在世界范围内首次提出并做到:
将锅炉低温换热器的最低壁面温度作为“第一”设计参数;
将换热器最低壁面温度与排烟温度从“倍数”关系转化为“加减”关系;
将换热器的最低壁面温度处于。
整体均匀、可调可控”状态。
将换热器的最低壁面温度独立(无关联)于被加热流体的进口温度。
4适用范围
适用于燃煤、燃油、燃气发电锅炉及工业锅炉,可大幅降低锅炉排烟温度,提高锅炉热效率,亦可广泛应用于石油、化工、电力、冶金等各种行业的空气预热器、煤气预热器、余热锅炉、热风炉、工业窑炉等设备。
3.复合相变换热器基本原理及特性
3.1基本原理和特性
和一般热管换热器以及其他节能技术不同,复合相变换热器技术的核心在于“复合”和“相变”,即通过“相变换热器”的设置,并利用不同“强化传热技术”与不同“控制技术”的合理配置,借助于优化设计,改变包括热管技术在内的一般换热器壁面温度分布的“函数”特征,在始终保证金属壁面温度处于酸露点以上以避免出现低温结露和腐蚀的同时,为大幅度回收烟气低温余热提供了可能。
复合相变换热器中的“相变段”是整个技术得以实施的核心部件之一,它将原热管换热器中相互独立的部分,通过优化设计构造成一个相互关联的整体,充分利用气(化)液(化)间“两相同向流动”、“汽液相变换热”、“工质自然循环”,将气化与液化交替进行,以2243kJ/kg的热容量进行高效传热。
在换热平均温差20℃时,与传统的烟气横向冲刷列管换热的气气换热器的20kJ/kg、20℃换热能力相比,二者具有102以上数量级的传热量差别。
复合相变换热器是在多根并联的密闭管排束构件内利用软化水相变潜热传递热量,在热管下端面加热,水吸收热量汽化为饱和蒸汽,在一定的压差下上升到热管上端面,向外界放出热量,并凝结成液体,饱和水经汽水分离器回到受热段,并再次汽化,往复循环,完成了把热量从高端传向低端的单向导热。
复合相变换热器多根并联的密闭管排束构件上的金属壁面整体温度分布均匀,与烟气温度保持“较小梯度温降(温差10~20℃℃)”,并具备“独立于被加热工质温度”的特殊功能。
复合相变换热器通过“相变段”换热流量的调节,实现对整个设备可能出现的不同最低壁面温度的闭环控制,保证面对燃料种类如煤质等变动引发酸露点变化后,对壁温同步可控可调。
在保证设备安全运行的前提下,实现最大幅度回收烟气余热的节能目标。
图1为相变换热器的控制系统流程图。
图1为相变换热器的控制系统流程图
3.2相变换热器安全有效运行的关键调试
3.2.1注水及排气
(1)注水可以在锅炉运行状态进行,也可以在停炉状态进行。
注水操作直接影响相变换热器的安全、经济运行,须严格按照说明进行操作。
图2为相变换热器结构示意图,在有注水量计量的场合,注水操作如下:
汽包注水前记下水表数值;
打开相变下段的排污阀待放干水后,关闭排污阀,关闭放气球阀1,打开针形阀、注水球阀2,开始注水;
注水时密切注视水表指示的水量:
汽包注水量
达481kg时,停止注水(即关闭注水球阀2),同时立即打开放气球阀1;
若注水量超过565kg,则应打开相变下段的排污阀待放干水后,重新注水。
图2相变换热器结构示意图
(2)排气在关闭汽包的注水球阀2,停止注水后进行。
首先依次打开针形阀和放气球阀1,待相变下段受热产生蒸汽,可见放气球阀1有气体排出,即开始排气。
排气持续1小时左右。
先关闭针形阀,检查针形阀的严密性,同时观察注水球阀是否严密,不得有水迹;
然后关闭气球阀1,排气结束。
排气过程中应适时适量开大相变换热器热网回水系统的出水阀(进水阀),以排气口不产生负压、壁温显示仪显示温度在105~115℃为宜。
排气过程中,注意控制壁温显示仪显示温度不得超过120℃。
3.2.2调节相变段壁面温度和排烟温度
排气结束后,切换调节阀控制仪表为自动状态,调节阀自动调整相变换热器汽包的进水量,此后显示壁温值围绕105℃上下波动。
此时,排烟温度约120℃,设备进入正常运行状况。
3.2.3注意事项
(1)排气时操作人员应避开排气口,以免烫伤。
(2)正常运行中,无论何时相变段壁面温度显示仪显示温度值都不得低于100℃,或高于120℃。
(3)在锅炉运行时,进入换热器的供热回水流量不允许中断。
3.3管壳式换热器
该换热器是当前应用最广,理论研究和设计技术完善,运用可靠性良好的一类换热器。
目前各国为改善该换热器的传热性能开展了大量的研究。
强化传热主要有3种途径提高传热系数、扩大传热面积和增大传热温差,研究主要集中在强化管程和壳程传热面方面。
3.3.1管程强化传热
人们想尽各种办法实施强化传热,归结起来不外乎两条途径,即改变传热面的形状和在传热面上或传热流路径内设置各种形状的插入物。
改变传热面形状的方法有多种,用于强化管程传热的有:
横纹管、螺旋槽管、螺纹管(低翅管)
和缩放管以及螺旋扁管(瑞典ALLARDS公司生产)。
我国螺纹管的标准翅化率为113~219(<
3),美、英、日、德等国均有商品化低翅管。
德国Hde公司的螺旋槽管,管内传热效率明显优于光管,在2300<
Re<
105范围内,提高传热效率213~1111倍,当200<
1500时,提高传热效率210~22倍。
沈阳市广厦热力设备开发制造公司开发的超薄壁(δ=015mm)不锈钢波纹管换热器,其承压能力可达8MPa。
该换热器不仅强化了管内外的给热,还由于温差作用下换热管的可伸缩性,使表面结垢容易脱落,因此具有较强的防垢和自动除垢能力。
其传热系数较光管式提高2~3倍。
管内插入物是强化管内单相流体传热行之有效的方法之一。
目前管内插入物种类很多,如螺旋线、纽带、错开纽带、螺旋片和静态混合器等。
最近,英国CalGarinLtd公司开发的一种称之为HitranMatrixElements的花环式插入物,它是一种金属丝制翅片管子插入物(Wire2FinTubeInserts),能增强湍流。
中国石化北京设计院与华南理工大学联合研制的交叉锯齿型插入物,是华南理工大学对12种内插件(在Re=300~3500和Pr=135范围内)进行比较后优选的型式,可直接形成流体的混合,尤其适用高粘度流体的换热。
其在上海乙烯厂原油2蜡油介质换热器中使用,其总传热系数与光滑管相比提高了50%。
3.3.2强化壳程传热
传统的管壳式换热器,流体在壳侧流动存在着转折和进出口两端涡流的影响区,影响了壳侧的给热系数。
壳侧的传热强化研究包括管型与管间支撑物的研究。
a.采用折流杆式换热器
美国在70年代初为解决换热器管束振动开发了这种结构的换热器。
目前美国已直接应用强化传热管设计制造折流杆式换热器,如菲利普公司使用螺纹管作为换热管,不仅解决了振动问题,而且由于壳侧流动的改善使折流杆式换热器比传统的弓形折流板换热器传热系数提高30%左右,管束的压降减少50%。
华南理工大学和大庆石油化工总厂共同开发的折流杆螺旋槽管再沸器已应用于在无相变及冷凝传热方面,其总传热系数比普通光管再沸器提高了112~117倍,抗振性能好。
化工部化工机械研究院开发的折流杆式换热器替代了某化肥厂压缩机级间套管式冷却器,节省了占地面积。
b.空心环管壳式换热器
空心环管壳换热器是华南理工大学发明的一种新型管壳式换热器,已获得国家专利。
长沙化工机械厂设计制造的横纹管空心环管壳换热器使用横纹管作为传热管,空心环作为支撑形式,已成功地应用于小型氮肥厂。
在某化肥厂应用与原光管换热器相比,换热面积减小68%,抗振性能好。
c.采用纵流管束换热器
德国GRIMMA公司制造的一种整圆形折流板换热器,其结构为折流板上开横排管孔,以4个孔为一组将管桥处铣通,壳侧流体在管桥处沿着轴向流动,避免了流体因转折引起的滞留区。
该公司用不同粘度的甘油和水混合进行实验,结果表明在中低粘度范围内,纵流管束换热器传热效果优于传统的圆缺形折流板换热器。
d.强化沸腾传热的传热管
用于强化沸腾传热的传热管有:
烧结多孔表面管、机械加工的多孔表面管(如日本的Themoexcel2E管、改进型Ea管,德国Wieland2Werke公司的T管)、电腐蚀加工的多孔表面管、T型翅片管、ECR40管和Tube2B型管。
武汉冷冻机厂分别用表面机加工的多孔管与目前制冷业流行的低肋管组装而成的两台蒸发器进行比较,结果表明:
多孔管的热流密度比低肋管高36%,可减少传热面26%。
国内近年开发的碳钢T管也已成功地应用于重沸器,紫铜材质E管应用于氟里昂蒸发器。
e.强化冷凝传热的传热管
用于强化冷凝传热的传热管有:
纵槽管、低螺纹翅片管、锯齿形翅片管和径向辐射肋管式翅片管等。
近年来,Hamon2Lummus公司又推出一种SRC翅片管(SRCFinTube),用于冷凝传热。
德国GEWA公司开发的TXV管其翅片外缘呈V字型。
华南理工大学研制的花瓣形翅片管是一种特殊的三维翅片结构强化传热管,研究表明:
在自然对流条件下,其单管冷凝传热膜系数比锯齿形翅片管提高了8%~10%;
在强制对流条件下,是光滑管的5~6倍。
3.4新型换热器
3.4.1可拆式板式换热器
近20年来由于结构的改进,密封垫片材料和密封槽结构型式的发展,板片大型化制造技术的提高,板式换热器应用范围已经十分广泛。
英国APV公司制造的单片最大面积为4.75m2,单台换热面积可达2500m2,单台最大容板量为700片。
垫片与板片的连接固定方法如α2Laval公司的“按扣”式垫片,垫片直接扣压在板片上。
GEA公司的板片,板片槽口上窄底宽呈梯形,垫片与板片槽过盈配合将垫片压紧。
开发无粘接剂连接垫片的技术,使板式换热器安装和维修的时间节约80%。
我国板式换热器在80年代得到较大的发展,继四平板式换热器总厂、天津板式换热器厂开发单片面积2m2后,1992年邯郸板式换热器工贸公司试制成功国内最大的300MN板片专用压机,单片面积已达2.7m2。
3.4.2焊接式板式换热器
用焊接结构替代橡胶垫密封,全焊式和半焊式板式换热器的出现,消除了由于垫片材料耐温、耐腐蚀、耐压方面的限制,对于腐蚀介质使用板式换热器,近年来达到很大发展。
德国与日本合作的千代田BAVARIA混合焊接板式换热器,操作压力可从真空到6MPa,单元换热面积可达1480m2以上。
Nouvelles应用技术公司发明的Packinox换热器,代替列管式换热器用作炼油厂催化重整装置混合料换热器,并且得到了推广应用。
紧凑、轻型的Packi2nox换热器可用各种合金制成,能提供的表面积为1000~10000m2。
3.4.3螺旋板换热器
国外螺旋板换热器主要结构为可拆式,多为板边结构,即两端通道端面密封不用圆钢结构,整体中心隔板,制造水平较高。
在材料上除多数使用不锈钢外,还使用一些可焊的镍铬合金、蒙乃尔合金、钛和钛合金、铜铝合金等。
其大型化情况如下。
我国螺旋板换热器结构多数为不可拆式。
近年来仿制和自行设计的可拆式螺旋板结构也逐渐增多,使用材料一般为碳钢和不锈钢,也有少量的钛和钛合金。
3.4.4热管换热器
热管是一种新型高效的传热元件。
在60年代首先被应用于宇航技术中,70年代国外在电子、机械、石油、化工等方面有了广泛的应用。
热管换热器在国外已经系列化生产,用户选择甚为方便。
如美国Q2Dot公司开发的热管换热器已有5000多台的实际运行经验。
日本古田电器公司设计的热管换热器已应用于7