注塑论文定稿文档格式.docx
《注塑论文定稿文档格式.docx》由会员分享,可在线阅读,更多相关《注塑论文定稿文档格式.docx(25页珍藏版)》请在冰豆网上搜索。
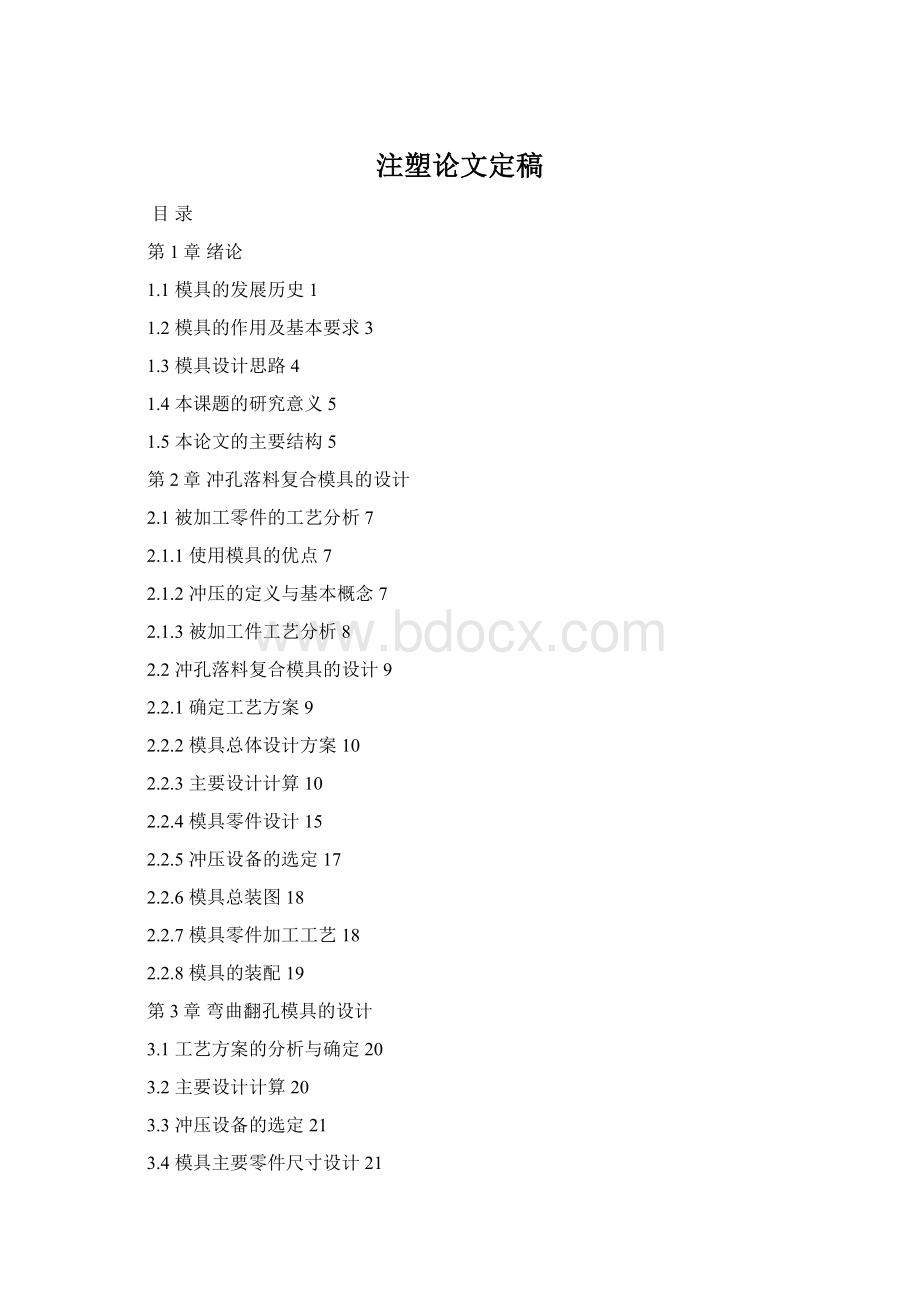
模具工业是“百业之母”,是工业产品的“效益放大器”。
各国对模具的美誉很多,美国工业界认为:
“模具工业是美国工业的基石”;
日本模具协会认为:
“模具是促进社会繁荣富裕的动力”;
国际模具协会认为:
“模具是金属加工业的帝王”。
模具在现代生产中,是生产各种工业产品的重要工艺装备,它以其特定的形状通过一定的方式使原材料成形。
例如,冲压件和锻件是通过冲压或锻造方式使金属材料在模具内发生塑性变形而获得的。
金属压铸件、粉末冶金零件以及塑料、陶瓷、橡胶、玻璃等非金属制品,绝大多数也是用模具成形的。
世界上一些工业发达国家,模具工业的发展是很迅速的。
据有关资料介绍,某些国家的模具总产值已超过了机床工业的总产值,其发展速度超过了机床、汽车、电子等工业。
模具工业在这些国家已摆脱了从属地位而发展成为独立的行业,是国民经济的基础工业之一。
模具技术,特别是制造精密、复杂、大型、长寿命模具的技术,已成为衡量一个国家机械制造水平的重要标志之一。
我国模具CAD/CAM技术的发展已有20多年历史。
由原华中工学院和武汉733厂于1984年共同完成的精神模CAD/CAM系统是我国第一个自行开发的模具CAD/CAM系统[1]。
而汽车覆盖件模具制造技术正在不断地提高和完美,高精度、高效益加工设备的使用越来越广泛。
高性能的五轴高速铣床和三轴的高速铣床的应用已越来越多。
NC、DNC技术的应用越来越成熟,可以进行倾角加工超精加工。
这些都提高了模具面加工精度,提高了模具的质量,缩短了模具的制造周期。
尽管我国的模具工业这些年来发展较快,模具制造的水平也在逐步提高,但和工业发达国家相比,仍存在较大差距,主要表现在模具品种少、精度差、寿命短、生产周期长等方面。
当前,我国工业生产的特点是产品品种多、更新快和市场竞争激烈。
在这种情况下,用户对模具制造的要求是“交货期短”、“精度高”、“质量好”、“价格低”。
模具技术的发展应该与这些要求相适应。
(1)在模具设计制造中将全面推广CAD/CAM/CAE技术[2]
模具CAD/CAM/CAE技术,是模具技术发展的一个重要里程碑。
实践证明,模具CAD/CAM/CAE技术是模具设计制造的发展方向。
现在,全面普及CAD/CAM/CAE技术的条件已基本成熟。
随着微机软件的发展和进步,技术培训工作也日趋简化。
(2)模具高速扫描及数字化系统将在逆向工程中发挥更大作用
高速扫描机和模具扫描系统,已在我国200多家模具厂点得到应用,取得良好效果。
由于模具扫描系统已在汽车、摩托车、家电等行业得到成功应用,相信在“十五”期间将发挥更大的作用。
逆向工程和并行工程将在今后的模具生产中发挥越来越重要的作用。
(3)气体辅助注射技术和高压注射成形等工艺将进一步发展
气体辅助注射成形是一种塑料成形的新工艺,它具有注射压力低、制品翘曲变形小、表面质量好以及易于成形壁厚差异较大的制品等优点,可在保证产品质量的前提下,大幅度降低成本。
国外已比较成熟。
国内目前在汽车和家电行业中正逐步推广使用。
气体辅助注射成形包括塑料熔体注射和气体(一般均采用氮气)注射成形两部分,比传统的普通注射工艺有更多的工艺参数需要确定和控制,而且气体辅助注射常用于较复杂的大型制品,模具设计和控制的难度较大,因此,开发气体辅助成形流动分析软件,显得十分重要。
(4)模具标准化程度将不断提高
我国模具标准化程度正在不断提高,估计目前我国模具标准件使用覆盖率已达到30%左右。
国外发达国家一般为80%左右。
为了适应模具工业发展,模具标准化工作必将加强,模具标准化程度将进一步提高,模具标准件生产也必将得到发展。
(5)模具研磨抛光将向自动化、智能化方向发展
模具表面的精加工是模具加工中未能很好解决的难题之一。
另外,由于模具型腔形状复杂,任何一种研磨抛光方法都有一定局限性。
应注意发展特种研磨与抛光方法,如挤压研磨、电化学抛光、超声抛光以及复合抛光工艺与装备,以提高模具表面质量。
1.2模具的作用及基本要求
1.模具的作用
模具的作用一方面是将压力机的作用力通过模具传递给金属板料,在其内部产生使之变形的内力。
当内力的作用达到一定的数值时,板料毛胚或毛胚的某个部分便会产生与内力的作用性质相对应的变形,从而获得满足一定性能要求及符合所需尺寸及形状的制品;
另一方面,通过模具的作用,可以保证上下模之间的正确导向,并使配料稳固的压紧与精确的定位,从而冲制出一定精度要求的冲件。
在生产实际中,模具的作用在于保证冲件的质量、提高生产率和降低成本等。
为此,除了采用行之有效的工艺手段、进行正确的模具设计及选择合理的模具结构之外,还必须以先进的模具制造技术作为保证。
对于各类模具的制造,一般都应满足如下的几个基本要求[3]。
(1)制造精度高
模具的精度主要由冲件精度和模具结构的要求所决定的。
为了保证冲件的精度,模具工作部分的精度要求一般要比冲件的精度高2-3倍;
为此对于组成模具的零部件也就要提出较高的要求。
如对于凸模和凹模之间的间隙,必须要有严格的控制,并精确的保证其间隙的均匀性;
对拉深凸模和凹模刃口部分的圆角保持相当准确的尺寸,零件其他的尺寸精度、导向精度、空的位置精度也都必须达到规定的加工精度要求。
并且还需保证其装配的质量。
(2)操作性能良好
将模具安装到冲床上时,其方法要简便,调整工作量要少,操作时送料定位要快速、准确可靠,出料顺畅自如。
在整个使用工过程中,重建的尺寸和形状变化极小,可放心的进行生产。
取出制件方便,无螺钉松动及模具零件破损等故障。
(3)使用寿命长
模具加工费用约占成本的10%--30%,其使用寿命的长短直接影响到产品成本的高低、工艺部分负荷的轻重等。
为了保证高效率的生产,都要求模具具有较长的使用寿命。
(4)制造周期短
模具制造周期的长短主要取决于制造技术和生产管理水平的高低。
为了生产的需要,提高产品的竞争力,必须在保证质量的前提下尽量缩短模具的制造周期。
在规定的时间内完成制造,并且在规定的使用期间内,冲件的冲制符合使用要求。
(5)模具成本低
模具的成本应该是生产单件(或千件)时所发生的模具费用。
模具成本与模具结构的复杂程度、模具材料、加工精度和加工方法等都有关。
在设计和加工模具时,应根据实际情况作全面的考虑。
应在保证冲件质量的前提下,选择与冲件生产量相适应的模具结构和方便实用的零件制造方法,尽量降低模具的制造费用和维修费用。
在不影响使用的前提下,模具结构应尽量简单、材料便宜,并尽量采用标准件,使模具成本降低到最低限度。
2.模具的分类
冲模的形式有很多,一般可以按不同的特征来进行分类。
其实,有时在一幅模具中可能同时兼有上述的几种特征。
在表明该模具时往往采用其主要的特征来称呼,诸如导柱导向、带有定距侧刀和固定卸料板的冲孔—落料级进模,硬质合金变薄拉深等。
冲裁模具分类[4]:
按工序组合程度:
简单冲裁模式、连续冲裁模、符合冲裁模
按凹模位置:
正装模、倒装模
按导向方式:
敞开式冲裁模、导板式冲裁模、导柱式冲裁模
按工序性质:
落料模、冲孔模、切断模、切模、切边模、整修模
1.3模具设计思路
模具设计是冲件工艺方案的制定和模具结构的设计[6]。
一般可归纳为以下几点:
(1)取得必要的资料
(2)确定工艺方案及模具结构型式
(3)进行必要的工艺计算
(4)模具的总体设计
(5)模具主要零部件的结构设计
(6)选定冲压设备
(7)绘制模具总图
(8)绘制各非标零件的零件图
(9)填写模具记录卡和编写冲压工艺文件。
对于小批量生产时,应填写工艺路线明细表;
而在大量生产时,则需对每个零件制定工艺过程卡和工序卡。
1.4本课题的研究意义
模具是现代工业生产的一种重要工艺装备,在生产中起着关键的作用。
模具设计是企业模具的数字化设计,包括型腔模与冷冲模,在传统模具设计的基础上,充分应用数字化设计工具,提高模具设计质量,缩短模具设计周期。
近年来模具应用越来越广泛,有很多高校也开设了模具专业,但软硬件设施的缺乏,所培养的学生理论水平与实际技能差距很大。
这并不能满足企业的需求。
本次设计通过对一具体冲压件进行工艺过程分析和模具设计,能够使我们充分掌握模具生产的工艺过程和模具设计的基本原则、方法,并能较为熟练的使用CAD软件,为今后从事模具设计工作打下坚实的基础。
1.5本论文的主要结构
本文主要就模具的设计与制造进行了探讨,通过CAD系统的制图能力,初步完成对冲压模具设计。
在本次论文设计过程中,首先对零件进行工艺分析,通过对零件的分析对模具零件进行设计。
考虑到零件加工的经济效益和加工难易程度,该加工零件需要冲孔落料和弯曲两道工序才能完成。
经过相关资料的查阅,首先要对零件进行工艺分析,经过工艺分析和对比,采用冲孔落料工序,通过冲裁力、顶件力、卸料力等计算,确定压力机的型号。
再分析对冲压件加工所需的模具类型,选择所需设计的模具类型。
设计过程中主要以工艺分析、设计计算、模具总体设计、冲压设备选用模具零件加工工艺、装配、试模等过程进行。
在模具零件进行设计时,尽量选取了标准件,为冲压模具的标准化设计提供了基础。
从对一具体零件进行工艺分析到设计模具完成零件的工程生产,完整的展现了设计方法和查表法,同时运用了CAD的设计软件,使整个设计过程比以前更为合理和节约成本,缩短设计周期。
可以根据最新要求开始新的模拟,直到满足要求为比。
2.1被加工零件的工艺分析
2.1.1使用模具的优点
利用模具成型零件的方法,实质上是一种少切削、无切削、多工序重合的生产方法,采用模具成型的工艺代替传统的切削加工工艺,可以提高生产效率,保证零件质量,节约材料,降低生产成本,从而取得很高的经济效益。
利用模具生产零件的方法已经成为工业上进行成批或大批生产的主要技术手段,它对保证制品质量,缩短试用周期,进而争先占领市场,以及产品更新换代和新产品开发都具有决定性的意义。
冲压生产靠模具和压力机完成加工过程,与其它加工方法相比,在技术和经济方面有如下特点:
(1)冲压件的尺寸精度由模具来保证,具有一模一样的特征,所以质量稳定,互换性好。
(2)由于利用模具加工,所以可获得其它加工方法所不能或难以制造的,壁薄、重量轻、刚性好、表面质量高、形状复杂的零件。
(3)冲压加工一般不需要加热毛坯,也不像切削加工那样,大量切削金属,所以它不但节能,而且节约金属。
(4)对于普通压力机每分钟可生产几十件,而高速压力机每分钟可生产几百上千件。
所以它是一种高效率的加工方法。
2.1.2冲压的定义与基本概念
1.冷冲压的定义
冷冲压也称板料冲压,是塑性加工的一种基本方法[7]。
一般是以金属板料为原材料(也有采用金属管料和非金属材料的),利用压力机上的模具作往复运动,再常温下对金属板料施加压力,使金属板料内部产生变形的应力。
当内力的作用达到一定数值时,板料毛胚的某个部分便产生与内力的性质相对应的变形,使板料分离(或局部分离)或产生塑性变形,从而获得所需尺寸及形状的零件。
2.冲压的特点[8]
在生产技术上,制造出的零件质量轻、刚度好、精度高,并能保证零件尺寸的均一性和互换性。
不需进一步的机械加工即可以满足一般的装配和使用要求。
在经济方面,原材料是冶金厂大量生产的廉价的轧制钢板或带材。
在进行适当的冲压工艺后,可大量节约金属材料,实现少切屑和无铁屑的加工方法。
材料利用率一般可达75%--85%,因而制件的成本相应地比较低。
同时,能够节省能源,在冲压时不需加热,也不像切削加工那样将金属切成碎屑而需要消耗很大的能量。
生产率高,每分钟一台冲压设备可生产零件从几件到几十件。
操作简单,便于组织生产。
在大批量的生产中,易于实现机械化和自动化,进一步提高劳动生产率。
对操作人员的技术要求不高。
当生产发展需要时,用短期培训的方法即可解决操作人员不足的矛盾。
但是不足之处是需要有专用的模具,其制造周期长、费用高。
因此,在生产批量小时,经济上不合适。
并且制造精度较高、冲压工艺要求需要满足相应的应力状态、符合一定的变形要求。
因此,有时不能制造出精度要求极高的制件。
3.冲压件的精度要求
采用普通的模具进行冲压时,冲压件一般能达到的尺寸精度为[9]:
冲裁IT11—IT12
光洁冲裁IT9—IT11
精密冲裁IT6—IT8
整修IT6—IT7
冲孔IT11
压弯IT11—IT12
筒形拉深件的高度IT11—IT12
带凸缘拉深件的高度IT9—IT11
拉深件的直径IT9—IT11
拉深件的厚度IT11—IT12
冷挤压IT9
立体成型(敞开式模具)IT12—IT13
轴向尺寸IT10—IT11
径向尺寸IT7—IT8
2.1.3被加工件工艺分析
零件名称:
光驱零件
主要材料:
为普通碳素结构08钢,抗剪强度300MPa,抗拉强度400MPa。
钢延展率大,它的屈强比和冷弯实验中的弯曲直径小,其塑性好,同时它的硬度较低,材料厚度为1mm,因而20钢很适合冲压和弯曲加工。
工件尺寸全部为自由公差,可看作IT10级。
由零件得零件图。
为了使零件更好的适合冲裁,在不影响主要工作部分的情况下,对零件进行优化设计。
零件图如图2.1所示:
根据2.1图,可以确定3套冲裁工序方案。
(1)先弯曲后冲孔落料。
(2)先冲孔落料,再用弯曲模。
(3)冲孔落料弯曲复合模。
图2.1零件图
方案
(1)模具采用先弯曲后冲裁,一般这样可以保护孔,但整个制件的加工质量就下降了。
方案
(2)采用先冲孔落料后弯曲,加工成本低,而且也能加工出合格的零件。
方案(3)的模具制造复杂,困难,提高了制造成本。
因此采用第2套方案。
2.2冲孔落料复合模具的设计
2.2.1确定工艺方案
材料具有良好的冲压性能,适合冲裁,零件较为简单。
如图2.2零件的3个
图2.2冲裁图
孔采用标准的凸模直接冲裁。
外形较为简单,可以直接在冲孔时冲出零件外形。
零件的冲裁方案主要有以下几种:
(1)先冲孔,落料;
(2)冲孔落料,成形级进模;
(3)冲孔落料,成形复合模。
方案
(1)模具结构简单,但需2套模具,成本高生产效率低,难以满足大批量生产。
方案
(2)在大批量生产前提下采用多工位级进,模具加工制造困难且加工精度低。
方案(3)制造精度较高且安装调试优于级进模。
制件平整,在对零件进行优化设计后采用复合模具是最利于生产的,故选第3套方案。
2.2.2模具总体设计方案
1.选择导料销控制条料送进,无侧压装置,采用挡料销控制条料步进的定距。
2.采用弹性卸料的倒装复合模具。
采用倒装的结构冲模方便出件和卸料,采用弹性卸料可以保证零件的平面度。
3.由于零件精度要求不是很高,结合设计实际与工件工艺要求,本设计选滑动式导柱导套,中间导柱模架结构。
2.2.3主要设计计算
1.排样方式的确定
冲裁件在条料、带料或板料上的布置方法叫排样,同一零件可采用不同的排样形式。
排样方法不同,材料利用程度不同,排样合理就能用同样的材料冲出更多的零件来,降低材料消耗。
大批量生产时,在冲裁件的成本中,材料费用一般占60%以上。
因此,材料的经济利用是一个重要问题,特别对贵重有色金属。
排样的合理与否将影响到材料的经济利用、冲裁质量、生产率、模具结构与寿命、生产操作方便与安全等。
排样的意义就在于保证用最低的材料消耗和最高的劳动生产率得到合格的零件。
根据材料的利用情况,排样的方法可分为三种[10]:
(1)有废料排样沿冲件的全部外形冲裁,冲件与冲件之间、冲件与条料侧边之间都存在着有搭边废料。
有废料排样,材料利用率低,冲裁件质量及模具寿命高,用于冲裁形状复杂、尺寸精度要求较高的冲裁件。
(2)少废料排样沿冲件的部分外形切断或冲裁。
只在冲件与冲件之间或冲件与条料侧边之间留有搭边。
这种排样,材料利用率高,用于某些尺寸要求不高的冲裁件排样。
(3)无废料排样冲件与冲件之间或冲件与条料侧边之间均无搭边废料。
冲件与冲件之间沿直线或曲线的切断面分开。
这种排样,材料利用率最高,但对冲件的结构形状有要求。
零件外形比较复杂,尺寸较大,精度要求较高,采用有废料单排。
具体见排样图,如下图:
图2.3排样图
2.搭边和料宽
搭边及排样时冲件与冲件之间、冲件与条料侧边之间多余的料,其作用是补偿定位误差,使条料在送进时有一定的刚度,以保证送料的顺利进行,从而提高制件质量。
搭边数值的大小,主要与板料厚度、材料种类、制件形状的复杂程度、冲模结构和送料形式有关。
该工件为直边工件,长85.7mm,宽46mm。
因要保证工件表面平整,所以采用弹压卸料装置。
查《实用冲压模具设计手册》得:
a=1.0mm,b=1.2mm,由此可确定条料宽度:
(2.1)
式中:
B为条料宽度(mm);
L为工件垂直于送料方向的宽度(mm);
b为工件与条料侧边的搭边值(mm);
Cmin为条料的偏差(mm)。
3.利用率计算
在冲压生产中,材料的利用率是指在一个进距内工件面积与条料面积之比,用百分率表示。
材料利用率是衡量材料利用情况的指标,它与工件形状和排样方法有关。
一个进距内材料利用率可由下式表示:
(2.2)
F为工件面积(
);
为条料宽度(mm);
L为进料距离(mm)。
4.冲压力的计算及间隙的选择
冲裁力是指冲压时材料对凸模的最大抵抗力。
其大小主要与材料的性质、厚度和冲件分离的长度有关。
查《冲压模具设计手册》选零件刃口间隙值0.06~0.08。
模具选用倒装复合模具弹性卸料,平面刃口冲裁。
冲裁力:
(2.3)
Pa为制件的冲裁力;
τ为抗剪的强度;
l为制件的外轮廓长和内孔周长之和;
T为材料厚度。
查《冲压模具技术手册》得:
推件力系数Ki=0.06;
卸料力系数K=0.06。
推件力:
(2.4)
将套在凸模上的材料脱下的力称卸料力。
根据卸料力系数的取值范围取K=0.025。
卸料力:
(2.5)
Q为卸料力(N);
K为卸料力系数;
P为冲裁力(N)。
总冲压力:
(2.6)
图2.4压力中心图
根据总的冲压力初选250KN压力机。
5.压力中心的计算
求压力中心的方法是:
根据如图2.4所示选出基准轴X,Y,把制件件分成39段线段,求出每段的长度和它的重心坐标,然后得计算公式为:
(2.7)
(2.8)
经计算压力中心是:
(19,0)。
6.凸、凹模刃口尺寸的计算
工作零件相对较为复杂,凸凹模,固定板以及卸料板采用线切割加工。
由于零件轮廓较复杂,故落料凸凹模采用配合加工,冲孔模为标准件,采用分开加工。
根据《冲压模具设计手册》选零件刃口间隙值0.06-0.08。
得
零件精度IT10以上x=1
零件精度IT11~IT13x=0.75
零件精度IT14x=0.5
表2.1磨损后尺寸增大
基本尺寸
尺寸变化d-Δ
凹模尺寸d凹=(d-XΔ)+δ
9.42
9-0.058
8.9420.014
50
50-0.1
44.90.025
10
10-0.058
9.9420.014
7
7-0.058
6.9420.014
24
24-0.084
23.9160.024
2
2-0.04
1.960.01
5
5-0.048
4.9620.012
20
20-0.064
19.9160.021
3
3-0.04
2.960.01
1
1-0.04
以下设计中d为零件原尺寸;
Cmin为双面间隙;
δ凸和δ凹为模具零件的制造公差;
X为零件的制件公差。
(1)落料凹模刃口尺寸:
表2.2磨损后尺寸不变
尺寸变化L±
(Δ/2)
凹模尺寸L±
(Δ/8)
5±
0.024
0.06
1±
0.02
0.005
10±
0.029
0.007
14
14±
0.035
0.009
8
8±
表2.3磨损后尺寸减小
基本尺寸
尺寸变化d+Δ
凹模尺寸d凹=(d+XΔ)-δ
4
40.048
4.0484-0.012
20.04
2.004-0.001
70.058
7.058-0.014
42
420.1
42.010.05
50.048
5.048-0.012
(2)冲孔凸模刃口尺寸:
表2.4磨损后尺寸减小
90.058
9.058-0.014
磨损后尺寸增大或不变:
尺寸无变化。
7.卸料橡胶的使用
橡胶卸料板行程:
(2.9)
h1凸模进入凹模厚度1mm;
h2凸模凹进卸料板厚度1mm;
t料厚
凸凹模修模量h`=3—5mm取h=4mm
橡胶工作行程
(2.10)
由《冲压模具手册》[11]选定橡胶的自由高度:
(2.11)
Fw工作行程;
H橡胶自由高度。
故H=25mm。
卸料力选取压缩量为20%,单位压力P取0.70,橡胶直径D选择直径为32mm,
对橡