减少生产车间七大浪费的有效途径Word文档格式.docx
《减少生产车间七大浪费的有效途径Word文档格式.docx》由会员分享,可在线阅读,更多相关《减少生产车间七大浪费的有效途径Word文档格式.docx(9页珍藏版)》请在冰豆网上搜索。
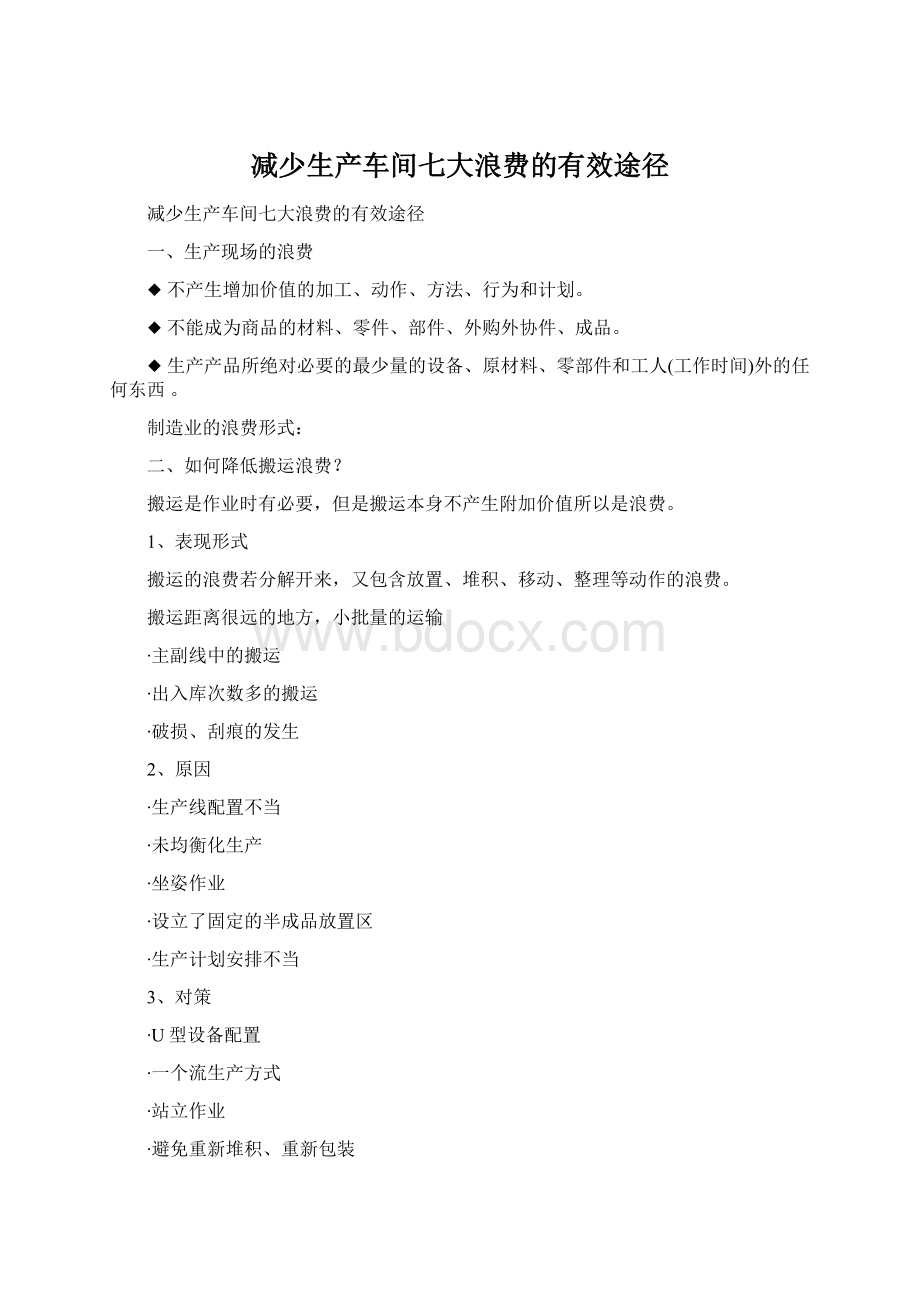
∙U型设备配置
∙一个流生产方式
∙站立作业
∙避免重新堆积、重新包装
4、注意点
∙工作预置的废除
∙生产线直接化
∙观念上不能有半成品放置区
∙人性考虑并非坐姿才可以
案例:
5、搬运浪费改善常用方法
6、精益生产的搬运要求
地点准:
直接送到需求点上
品种准:
只搬运现在需要的品种
质量准:
拿来能用,拒绝次品和返工
数量准:
不多不少
时间准:
不早不迟
方法准:
集成包装、过目知数、快速运输
三、怎样降低等待的浪费
等待浪费:
因时间的延误而造成不能增值的情况
等待材料
等待设备的修理
组装工序不平衡
自动机器操作中,人员的“闲视”等待
作业充实度不够的等待
设备故障、材料不良的等待
生产安排不当的人员等待
上下工序间未衍接好造成的工序间的等待
生产线布置不当,物流混乱
设备配置、保养不当
生产计划安排不当
工序生产能力不平衡
材料未及时到位
管理控制点数过多
品质不良
安排作业不当等
采用均衡化生产
制品别配置—一个流生产
防误措施
自动化及设备保养加强
实施目视管理
加强进料控制
自动化不要闲置人员
供需及时化
作管理点数削减
四、怎样降低动作的浪费?
这些动作占全部动作的50%:
∙工作时的换手作业
∙未倒角之产品造成不易装配的浪费
∙小零件组合时,握持压住的浪费
∙动作顺序不当造成动作重复的浪费
∙寻找的浪费
∙作业流程配置不当
∙无教育训练
∙设定的作业标准不合理
∙一个流生产方式的编成
∙生产线U型配置
∙标准作业之落实
∙动作经济原则的贯彻
∙加强教育培训与动作训练
∙补助动作的消除
∙运用动作经济原则
∙作业标准
5、动作经济的12项原则
人的行为失误分析与对策:
例:
五、怎样降低加工的浪费
加工浪费:
因技术(设计、加工)不足造成加工上的浪费
在加工时超过必要以上的距离所造成的浪费
冲床作业上重复的试模,不必要的动作
成型后去毛刺,加工的浪费
钻孔后的倒角,纹孔作业的浪费
最终工序的修正动作
工程顺序检讨的不足。
作业内容检讨的不足。
工具不好。
原材料未检查
品质保证度的确立
工程检讨的适合化
作业内容的再评价
工具改善和自动化
VA/VE(价值分析/价值工程)的推进
六、怎样降低品质不良的浪费?
制造不良品所损失的浪费,越做损失越大。
∙因作业不熟练所造成的不良
∙因不良而修整时所造成的浪费
∙因不良造成人员及工程增多的浪费
∙材料费增加
∙要用一切办法来消除、减少一切非增值活动,如检验、搬运和等待等造成的浪费
∙标准作业欠缺
∙过分要求品质
∙人员技能欠缺
∙品质控制点设定错误
∙认为可整修而做出不良
∙检查方法、基准等不完备
∙设备、模夹治具造成的不良
∙自动化、标准作业
∙防误装置
∙在工程内做出品质保证“三不政策”
∙一个流的生产方式
∙品保制度的确立及运行
∙定期的设备、模治具保养
∙持续开展“5S活动”
∙推行“零返修率”
∙能回收重做的不良
∙能修理的不良
∙误判的不良
七、怎样降低制造过多的浪费
物流阻塞
库存、在制品增加
产品积压造成不良发生
资金周转率低
材料、零件过早取得
影响计划弹性及生产系统的适应能力
人员过剩
设备稼动过剩
生产浪费大
业务订单预测有误
生产计划与统计错误
顾客为中心的弹性生产系统
单件流动—一个流生产线
看板管理的贯彻
快速换线换模
少人化的作业方式
均衡化生产
生产速度快并不代表效率高
设备余力并非一定是埋没成本
生产能力过剩时,应尽量先考虑减
少作业人员,但并非辞退人员,而
是更合理、更有效率地应用人员
八、怎样降低库存的浪费?
不良所造成的库存,半成品所造成的库存,制造过多所造成的库存都是浪费。
∙不良品存在库房内待修
∙设备能力不足所造成的安全库存
∙换线时间太长造成次大批量生产的浪费
∙采购过多的物料变库存
∙视库存为当然
∙设备配置不当或设备能力差
∙大批量生产,重视稼动
∙物流混乱,呆滞物品未及时处理
∙提早生产
∙无计划生产
∙客户需求信息未了解清楚
∙库存意识的改革
∙均衡化生产
∙生产流程调整顺畅
∙看板管理的贯彻
∙快速换线换模
∙生产计划安排考虑库存消化
∙库存是万恶之源
∙管理点数削减降低安全库存
∙消除生产风险降低安全库存
九、如何正确发现并消除浪费?
1、如何发现浪费
∙运用点检表方式
∙运用5Why原则
∙运用时间分析手法
∙“三现五原则”
制作七大浪费的点检表,定期对现场进行点检,找出浪费最大的五项进行改善。
2、现场管理三现五原则
三现:
现场、现物、现状
五原则:
1.A.发生状况
现象、申诉内容、发生次数、5W2H处置内容
1.B.把握事实
对零部件的确认结果、原因分析、现在正在
生产的该零部件的品质状况
2.A.查明原因
连续问五个“Why”的分析
2.B.查明原因
发生的途径、问题再现试验、WhyWhy分析
3.适当的对策
对策内容、效果预测、PPA
4.确认效果
确认对策的实绩效果
5.对源头的反馈
需要落实到体制、组织或标准化的内容
3、浪费提问(5W1H)
4、浪费提问书(5S)
5、浪费改善Point10
6、形成一个流、节拍化生产
“一个流生产”是指从毛坯投入成品产出的整个制造加工过程,零件始终处于不停滞、不堆积、不超越,按节拍一个一个的流动的生产方法。
◆每道工序加工完一个制件后立即流到下一工序;
◆工序间的在制品数量不超过紧前工序的装夹数量;
◆制件的运动不间断、不超越、不落地;
◆生产工序、检验工序和运输工序合为一体;
◆只有合格的产品才允许往下道工序流。