操作型计算和特殊精馏.doc
《操作型计算和特殊精馏.doc》由会员分享,可在线阅读,更多相关《操作型计算和特殊精馏.doc(11页珍藏版)》请在冰豆网上搜索。
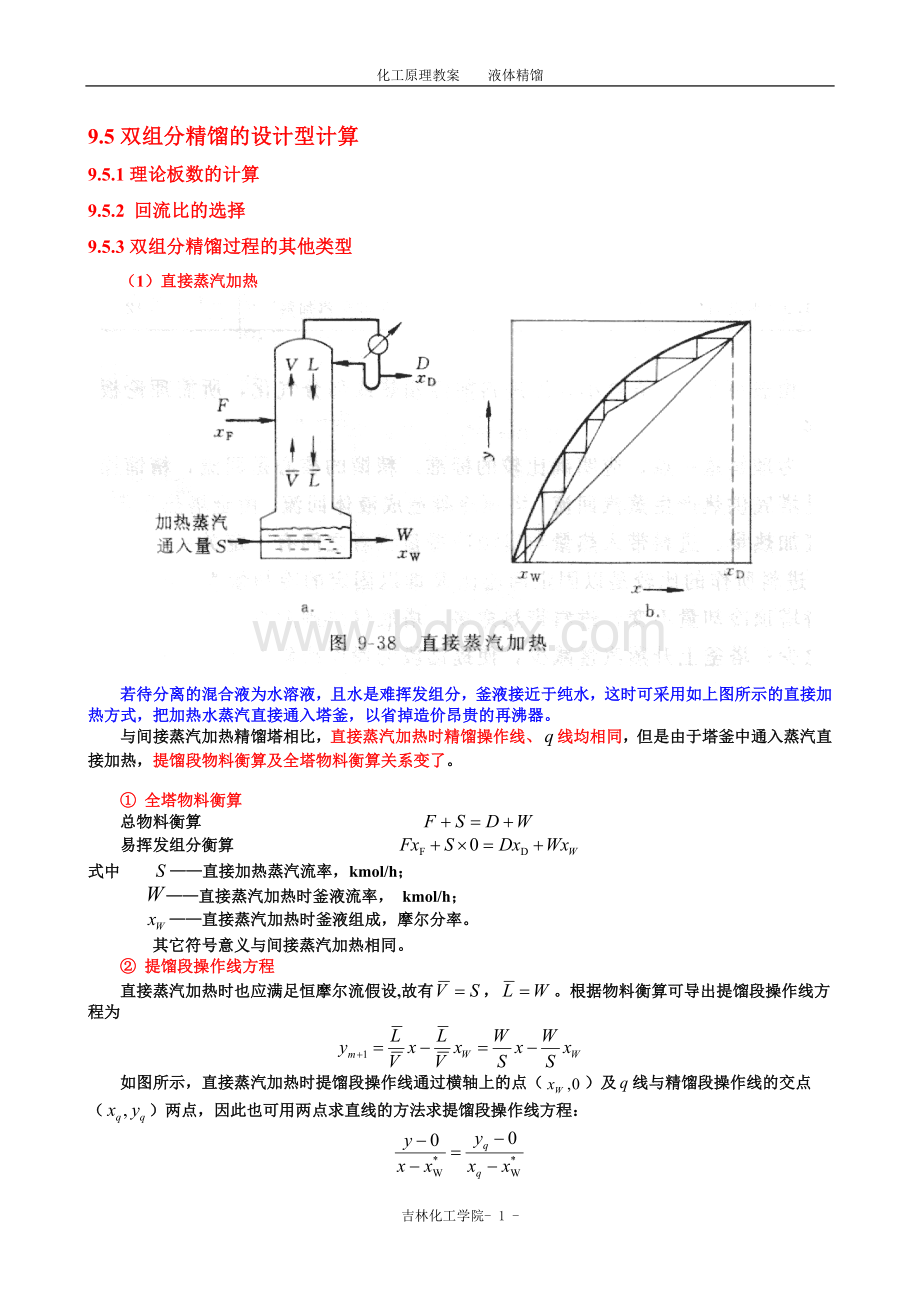
化工原理教案液体精馏
9.5双组分精馏的设计型计算
9.5.1理论板数的计算
9.5.2回流比的选择
9.5.3双组分精馏过程的其他类型
(1)直接蒸汽加热
若待分离的混合液为水溶液,且水是难挥发组分,釜液接近于纯水,这时可采用如上图所示的直接加热方式,把加热水蒸汽直接通入塔釜,以省掉造价昂贵的再沸器。
与间接蒸汽加热精馏塔相比,直接蒸汽加热时精馏操作线、线均相同,但是由于塔釜中通入蒸汽直接加热,提馏段物料衡算及全塔物料衡算关系变了。
①全塔物料衡算
总物料衡算
易挥发组分衡算
式中——直接加热蒸汽流率,kmol/h;
——直接蒸汽加热时釜液流率,kmol/h;
——直接蒸汽加热时釜液组成,摩尔分率。
其它符号意义与间接蒸汽加热相同。
②提馏段操作线方程
直接蒸汽加热时也应满足恒摩尔流假设,故有,。
根据物料衡算可导出提馏段操作线方程为
如图所示,直接蒸汽加热时提馏段操作线通过横轴上的点()及线与精馏段操作线的交点()两点,因此也可用两点求直线的方法求提馏段操作线方程:
用上式求直接蒸汽加热时提馏段操作线方程比较方便,问题归结为两操作线交点坐标()如何求。
因为线及精馏段操作线均与间接蒸汽加热时相同,所以仍可用前述方法求、值。
若用式求,则需根据,等关系导出可利用题给已知条件的形式才能求解。
(2)多股进料
两种成分相同但浓度不同的料液可在同一塔内进行分离,两股料液应分别在适当位置加入塔内。
整个精馏塔可分成三段,每段均可按图中所示符号用物料衡算推出其操作线方程。
①操作线方程Ⅰ段
Ⅱ段
式中
特别,当为泡点进料,则Ⅱ段操作线可写成
Ⅲ段
式中
无论何种进料热状况,操作线斜率必有(Ⅲ)>(Ⅱ)>(Ⅰ)。
②全塔物料衡算
总物料衡算
易挥发组份衡算
联立以上两式可得)
回收率
③线方程
线方程数与进料股数相同,两股进料线方程有两个,即
,
④最小回流比
回流比减小,三条操作线均向平衡线靠拢。
当减小至某个值时,挟点可能出现在Ⅰ-Ⅱ两段操作线的交点处,也可能出现在Ⅱ-Ⅲ两段操作线的交点处。
对非理想性很强的物系,挟点也可能出现在某个中间位置,先出现挟点时的回流比为最小回流比。
(3)侧线出料
如下图所示,此时操作线数目,因而整个精馏塔可分成三段,每段均可按图中所示符号用物料衡算推出其操作线方程。
以下仅讨论侧线抽出的产品为泡点液体的情况。
(操作线方程Ⅰ段
Ⅱ段(泡点采出)
以上两式中定义为。
Ⅲ段
式中
有侧线出料时操作线斜率通常(Ⅱ、Ⅰ)),在最小回流比时,挟点一般出现在线与平衡线交点处。
9.6双组分精馏的操作型计算
9.6.1精馏过程的操作型计算
(1)操作型计算的命题:
此类计算的任务是在设备(精馏段板数及全塔理论板数)已定的条件下,由指定的操作条件预计精馏操作的结果。
计算所用的方程与设计时相同,此时的已知量为:
全塔总板数及加料板位置(第块板);相平衡曲线或相对挥发度;原料组成与热状态,回流比;并规定塔顶馏出液的采出率。
待求的未知量为:
精馏操作的最终结果——产品组成及逐板的组成分布。
操作型计算的特点:
①由于众多变量之间的非线形关系,使操作型计算一般均须通过试差(迭代),即先假设一个塔顶(或塔底)组成,再用物料衡算及逐板计算予以校核的方法来解决。
②加料板位置(或其它操作条件)一般不满足最优化条件。
下面以两种情况为例,讨论此类问题的计算方法。
回流比增加对精馏结果的影响
设某塔的精馏段有块理论板,提馏段为块板,在回流比操作时获得塔顶组成与釜液组成(参见图9-43a)。
现将回流比加大至,精馏段液气比增加,操作线斜率变大;提馏段气液比加大,操作线斜率变小。
当操作达到稳定时馏出液组成必有所提高,釜液组成必将降低,如图(9-43b)所示。
定量计算方法是:
先设定某一值,可按物料衡算式求出
然后,自组成为起交替使用精馏段操作线方程及相平衡方程进行次逐板计算,算出第1至板的气、液组成。
直至算出离开加料板液体的组成。
跨过加料板以后,须改用提馏段操作线方程
及相平衡方程进行次逐板计算,算出最后一块理论板的液体组成。
将此值与所假设的值比较,两者基本接近则计算有效,够则重新试差。
必须注意,在馏出液流率规定的条件下,藉增加回流比一提高的方法并非总是有效:
a.的提高受精馏段塔板数即精馏塔分离能力的限制。
对一定板数,即使回流比增至无穷大(全回流)时,也有确定的最高极限值;在实际操作的回流比下不可能超过此极限值。
b.的提高受全塔物料衡算的限制。
加大回流比可提高,但其极限值为。
对一定塔板数,即使采用全回流,也只能某中程度趋近于此极限值。
如的数值大于1,则的极限值为1。
此外,加大操作回流比意味着加大蒸发量与冷凝量。
这些数值还将受到塔釜及冷凝器的传热面的限制。
(2)进料组成变动的影响
一个操作中的精馏塔,若进料组成下降至,则在同一回流比及塔板数下塔顶馏出液组成将下降为,提馏段塔釜组成也将由降至。
进料组成变动后的精馏结果、可用前述试差方法确定。
图9-44表示进料组成变动后操作线位置的改变。
此时欲要维持原馏出液组成不变,一般可加大回流或减少采出量。
值得注意,以上两种情况的操作型计算中,加料板位置不一定是最优的。
图9-43b说明了这一问题。
9.6.2精馏塔的温度分布和灵敏板
(1)精馏塔的温度分布
溶液的泡点与总压及组成有关。
精馏塔内各块塔板上物料的组成及总压并不相同,因而塔顶至于塔底形成某种温度分布。
在加压或常压精馏中,各板的总压差别不大,形成全塔温度分布的主要原因是各板组成不同。
图9-45a表示各板组成与温度的对应关系,于是可求出各板的温度并将它标绘在图9-45b中,即得全塔温度分布曲线。
减压精馏中,蒸汽每经过一块塔板有一定压降,如果塔板数较多,塔顶与塔底压强的差别与塔顶绝对压强相比,其数值相当可观,总压降可能是塔顶压强的几倍。
因此,各板组成与总压的差别是影响全塔温度分布的重要原因,且后一因素的影响往往更为显著。
(2)灵敏板
一个正常操作的精馏塔当受到某一外界因素的干扰(如回流比、进料组成发生波动等),全塔各板的组成发生变动,全塔的温度分布也将发生相应的变化。
因此,有可能用测量温度的方法预示塔内组成尤其是塔顶馏出液的变化。
在一定总压下,塔顶温度是馏出液组成的直接反映。
但在高纯度分离时,在塔顶(或塔底)相当高的一个塔段中温度变化极小,典型的温度分布曲线如图9-46所示。
这样,当塔顶温度有了可觉察的变化,馏出液组成的波动早已超出允许的范围。
以乙苯-苯乙烯在8下减压精馏为例,当塔顶馏出液中含乙苯由99.9%降至90%时,泡点变化仅为0.7℃。
可见高纯度分离时一般不能用测量塔顶温度的方法来控制馏出液的质量。
仔细分析操作条件变动前后温度分别的变化,即可发现在精馏段或提馏段的某些塔板上,温度变化量最为显著,或者说,这些塔板的温度对外界干扰因素的反映最灵敏,故将这些塔板称之为灵敏板。
将感温元件安置在灵敏板上可以较早觉察精馏操作所受到的干扰;而且灵敏板比较靠近进料口,可在塔顶馏出液组成尚未产生变化之前先感受到进料参数的变动并即使采取调节手段,以稳定馏出液的组成。
9.7间歇精馏
9.7.1间歇精馏过程的特点
当混合液的分离要求较高而料液品种或组成经常变化时,采用间歇精馏的操作方式比较灵活机动。
从精馏装置看,间歇精馏与连续精馏大致相同。
作间歇精馏时,料液成批投入精馏釜,逐步加热气化,待釜液组成降至规定值后将其一次排出。
由此不难理解,间歇精馏过程具有如下特点:
①间歇精馏为非定态过程。
在精馏过程中,釜液组成不断降低。
若在操作时保持回流比不变,则馏出液组成将随之下降;反之,为使馏出液组成保持不变,则在精馏过程中应不断加大回流比。
为达到预定的要求,实际操作可以灵活多样。
例如,在操作初期可逐步加大回流比以维持馏出液组成大致恒定;但回流比过大,在经济上并不合理。
故在操作后期可保持回流比不变,若所得的馏出液不符合要求,可将此部分产物并入下一批原料再次精馏。
此外,由于过程的非定态性,塔身积存的液体量(持液量)的多少将对精馏过程及产品的数量有影响。
为尽量减少持液量,间歇精馏往往采用填料塔。
②间歇精馏时全塔均为精馏段,没有提馏段。
因此,获得同样的塔顶、塔底组成的产品,间歇精馏的能耗必大于连续精馏。
间歇精馏的设计计算方法,首先是选择基准状态(一般以操作的始态或终态)作设计计算,求出塔板数。
然后按给定的塔板数,用操作型计算的方法,求取精馏中途其他状态下的回流比或产品组成。
为简化起见,在以下计算中均不计塔板上液体的持液量对过程的影响,即取持液量为零。
9.7.2保持馏出液组成恒定的间歇精馏
设计计算的命题为:
已知投料量及料液组成,保持指定的馏出液组成不变,操作至规定的釜液组成或回收率,选择回流比的变化范围,求理论板数。
1.确定理论板数
间歇精馏塔在操作过程中的塔板数为定植。
不变但不断下降,即分离要求逐渐提高。
因此,所设计的精馏塔应能满足过程的最大分离要求,设计应以操作终了时的釜液组成为计算基准。
间歇精馏的操作先线如图9-48所示。
在操作终了时,将组成为的釜液提浓至必有一最小回流比,在此回流比下需要的理论板数为无穷多。
由图9-48b可知,一般情况下此最小回流比为
为使塔板数保持在合理范围内,操作终了的回流比应大于上式的某一倍数。
此最终回流比的选择由经济因素决定。
选定后,即可从图9-48c中a点开始,以为截距作出操作终了的操作线并求出理论板数。
在操作初期可采用较小的回流比,此时的操作线如图9-48c中虚线所示。
2.每批料液的操作时间
设:
——每批料液的投料量,Kmol;
——馏出液量,Kmol,其值随精馏时间而变化;
——釜液的摩尔分数组成,其值在操作中由降为;
——蒸馏釜的气化能力,Kmol/s,在操作中可保持为某一常数。
在时间内的气化量为,此气化量应等于塔顶的蒸汽量
任一瞬时之前已馏出的液体量由物料衡算式确定,即
将此式代入式(9-93)
积分得
在操作过程中因塔板数不变,每一釜液组成必对应一回流比,可用数值积分从上式求出每批料液的精馏时间。
9.7.3回流比保持恒定的间歇精馏
因塔板数及回流比不变,在精馏过程中塔釜组成与馏出液组成必同时降低。
因此只有使操作初期的馏出液组成适当提高,馏出液的平均浓度才能符合产品的质量要求。
设计计算的命题为:
已知料液量及组成,最终的釜液组成,馏出液的平均组成。
选择适宜的回流比求理论板数。
计算可以操作初态为基准,假设一最初的馏出液组成,根据设定的与釜液组成求出所需的最小回流比(参见图9-4