组合机床动力滑台液压系统设计Word文档格式.docx
《组合机床动力滑台液压系统设计Word文档格式.docx》由会员分享,可在线阅读,更多相关《组合机床动力滑台液压系统设计Word文档格式.docx(15页珍藏版)》请在冰豆网上搜索。
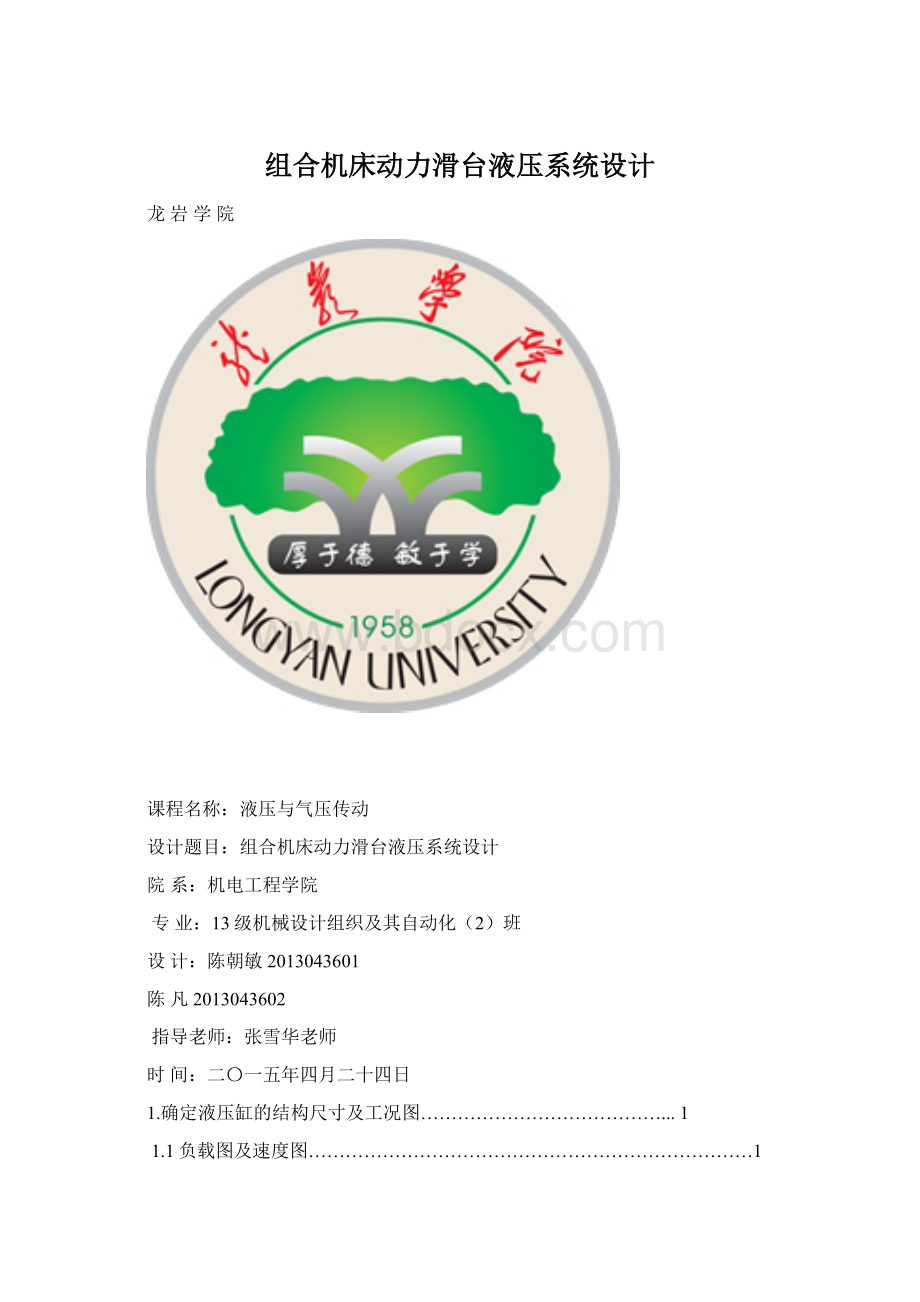
9.8=1000N
Ffd=fd·
FG=0.1×
9.8=500N
c.惯性阻力:
Fm=ma=(FG·
△v)/(g·
△t)
=(4998×
3.5)/(9.8×
0.2×
60)
=149N
d.重力阻力。
由于动力滑台为卧式放置,所以不考虑重力负载。
e.密封阻力。
键密封阻力考虑在液压缸的机械效率中去,取液压缸机械效率
ηm=0.9。
f.背压阻力。
初算时暂不考虑。
根据分析可算出液压缸在各动作阶段中的负载,如表1所示。
工况
计算公式
液压缸负载F/N
液压缸推力F/0.9N
启动
F=Ffs
1000
1111
加速
F=Ffd+Fm
649
721
快速
F=Ffd
500
555
工进
F=Fl+Ffd
24500
27222
反向启动
快退
②负载图、速度图。
快进速度v1与快退速度v3相等,即v1=v3=3.5m/min。
行程分别为l1=200mm、l3=300mm;
工进速度v2=0.03~0.04m/min,即v2min=0.03m/min,v2max=0.04m/min,行程l2=100mm。
根据这些数据和表格中的数值绘制液压缸的F-l负载图和v-l速度图,如图1所示。
(a)(b)
(2)初定液压缸的结构尺寸。
①初选液压缸的工作压力p1。
由课本的表8.4和表8.5初选p1=3.5Mpa。
②计算液压缸的结构尺寸。
因要求v1=v3,故选用双作用但活塞杆缸,是A1=2A2(d=0.707D),且快进时液压缸差动连接。
因为是单面多轴钻孔组合机床加工,为防止钻(镗)通孔时工作部件突然前冲,回油路中应有背压。
由书本表8.3暂取背压为p2=p1+△p=p1+5×
10^5Pa。
快进时,液压缸是差动连接,由于管路中有压力损失,所以这时液压缸有杆腔内的压力p2比大于无杆腔中的压力p1。
若估取这部分损失为△p=5×
10^5Pa,则p2=p1+△p=p1+5×
快退时回油腔中也是有背压的,此时背压也按5×
10^5Pa估取。
因此,根据已知参数,液压缸无杆腔的有效作用面积A1可计算为
A1=F/(p1-p2/2)=27222/(35-8/2)×
10^5=87.8(cm2)
D=√4A1/π=√(4×
87.8)/π=10.57(cm)
按标准取D=110mm。
液压缸活塞杆直径d为
d=D/√2=0.707D=0.707×
110=77.8(mm)
按标准去d=80mm。
由此求得液压缸实际有效工作面积为
无杆腔面积:
A1=πD2/4=π×
1102/4=95.0(cm2)
有杆腔面积:
A2=π(D2-d2)/4=π×
(1102-802)/4=44.7(cm2)
按最低工进速度验算液压缸的最小稳定速度,得:
A1>
qmin/vmin=0.05×
103/3=17.7cm2
同理:
A2>
qmin/vmin=17.7cm2
所以流量控制阀无论是放在进油路上,还是在回油路上,有效工作面积A1、A2都能满足工作部件的最低速度要求。
(3)液压缸工况图。
液压缸工作循环中各动作阶段的压力、流量和功率的实际使用值,如下表2。
各工况下的主要参数值
负载F’/N
回油腔压力P2/MPa
进油腔压力P1/MPa
输入流量q/L.min-1
输入功率P/Kw
快进
——
0.22
P1=(F+A2P2)/(A1-A2)
q=(A1-A2)v1
P=p1q
p2=p1+Δp
0.58
恒速
0.55
17.61
0.161
0.8
3.24
0.29~0.38
0.016~0.021
P1=(F’+p2A2)/A1
q=A1v2
起动
0.25
P1=(F’+p2A1)/A2
q=A2v3
0.5
1.22
1.88
15.7
0.308
根据表2可绘制液压缸的工况图,如图2所示
2)拟定液压回路
(1)选择液压回路。
①调速回路即油源形式。
根据组合机床液压系统的设计任务和工况分析,所设计机床对调速范围、低速稳定性有一定要求,因此速度控制是该机床要解决的主要问题。
速度的换接、稳定性和调节是该机床液压系统设计的核心。
此外,与所有液压系统的设计要求一样,该组合机床液压系统应尽可能结构简单,成本低,节约能源,工作可靠。
由工况图表明,所设计组合机床液压系统在整个工作循环过程中所需要的功率较小,系统的效率和发热问题并不突出,因此考虑采用节流调速回路即可。
虽然节流调速回路效率低,但适合于小功率场合,而且结构简单、成本低。
该机床的进给运动要求有较好的低速稳定性和速度-负载特性,因此有三种速度控制方案可以选择,即进口节流调速、出口节流调速、限压式变量泵加调速阀的容积节流调速。
钻镗加工属于连续切削加工,加工过程中切削力变化不大,因此钻削过程中负载变化不大,采用节流阀的节流调速回路即可。
但由于在钻头钻入铸件表面及孔被钻通时的瞬间,存在负载突变的可能,因此考虑在工作进给过程中采用具有压差补偿的进口调速阀的调速方式,且在回油路上设置背压阀。
由于选定了节流调速方案,所以油路采用开式循环回路,以提高散热效率,防止油液温升过高。
②快速回路及速度换接回路。
因系统要求快进、快退的速度相等,故快进时采用液压缸差动连接的方式,以保证快进、快退时的速度基本相等。
由于快进、工进之间的速度相差较大,为减小速度换接时的液压冲击,采用行程阀控制的换接回路。
③换向回路。
由工况图可看出,回路中流量较小(在快退时,进油路上的流量为15.7L/min,回油路上为15.7
95/44.7=33.37(L/min)。
系统的工作压力也不高,故采用电磁换向阀的换向回路。
④压力控制回路。
在双定量泵供油的油源形式确定后,卸荷和调压问题都已基本解决,即工进时,低压泵卸荷,高压泵工作并由溢流阀调定其出口压力。
当换向阀处于中位时,高压泵虽未卸荷。
但功率损失并不大。
故不再采用卸荷回路,以便油路结构更加简单。
⑤行程终点的控制方式。
选择的液压回路,如下图2所示。
(a)双泵油源(b)调速及速度环节回路(c)换向回路
(2)组成液压系统图。
由于采用双泵供油回路,故采用液控顺序阀实现低压大流量泵卸荷,用溢流阀调整高压小流量泵的供油压力。
为了便于观察和调整压力,在液压泵的出口处、背压阀和液压缸无杆腔进口处设测压点。
将上述所选定的液压回路进行整理归并,并根据需要作必要的修改和调整,最后画出液压系统原理图如图3所示。
为了解决滑台快进时回油路接通油箱,无法实现液压缸差动连接的问题,必须在回油路上串接一个液控顺序阀9,以阻止油液在快进阶段返回油箱。
同时阀8起背压阀的作用。
为了避免机床停止工作时回路中的油液流回油箱,导致空气进入系统,影响滑台运动的平稳性,图中添置了一个单向阀11。
考虑到这台机床用于钻孔(通孔与不通孔)加工,对位置定位精度要求较高,图中增设了一个压力继电器。
当滑台碰上死挡块后,系统压力升高,压力继电器发出快退信号,操纵电液换向阀换向。
(由于找不到继电器图标,此图未画出)
在进油路上设有压力表开关和压力表,钻孔行程终点定位精度不高,采用行行程开关控制即可。
3)计算和选择液压元件
(1)确定液压泵的规格和电机功率。
①液压泵工作压力的计算。
a.确定小流量泵的工作压力Pp1。
小流量在快进、快退和工进时都向系统供油。
由图2可知,最大工作压力为p1=32.4×
105Pa。
在出口节流调速中,引进有路比较简单,故进油路压力损失取∑△p1=5×
105Pa,则小流量泵的最高工作压力为
Pp1=p1+∑△p1=37.4×
105Pa
b.确定大流量泵的工作压力Pp2。
大流量泵只在快进、快退中供油。
由工况图可知,最大工作压力为p1=11.8×
105Pa。
若取此时进油路上的压力损失为∑△p1=5×
105Pa,则大流量泵的最高工作压力为
Pp2=p1+∑△p1=16.8×
②液压泵流量的计算。
由图2可知,液压缸所需要的最大流量为15.7L/min,若取泄漏折算系数K=1.2,则两个泵的总流量为
qp=15.7×
1.2=18.84(L/min)
③液压泵规格的确定。
按式Ppmax=Pp1×
[1+(25~60)%]=(46.75~59.84)×
105Pa及qp=18.84L/min查产品样本或设计手册,选取YB-10/12型双联叶片泵,额定压力为63×
④电机功率的确定。
由工况图得知,液压缸最大功率Pmax=0.308kW。
出现在压力为18.8×
105Pa、15.7L/min的快退阶段,这时泵站输出压力为23.8×
105Pa,流量为22L/min。
若取双泵的总功率为ηp=0.75,则可算出所需电动功率为
P=Ppqp/ηp=2.38×
22/(60×
0.75)=1.2(kW)
按产品目录需选用功率为1.2kW、同步转数为1000r/min的电动机。
(2)液压阀的选择。
根据系统的最高工作压力和通过各阀的最大实际流量,选出的各阀的规格如表3所示。
序号
液压件名称
通过的最大实际流量/(L/min)
型号
规格
接口尺寸
数量
1
双联叶片泵
YB-12/12
(10/12)L/min
6.3MPa
2
溢流阀
10
Y-25B
25L/min
6.3Mpa
φ12
3
单向阀
22
I-25B
4
二位二通电磁换向阀
22D-25B
5
三位五通电磁阀
70
35D-100B
100L/min
φ18
6
可调单向调速阀
I-100B
7
液控顺序阀
12
XY-25B
8
液压源
选择液压件时,在满足要求的条件下应尽量选的使各元件的接口尺寸一致,以使管道的选择和安装方便。
(3)确定管道尺寸。
①压油管道。
d=2√q/πv=2√(22×
10-3/60)/π(2.5~5)=0.0098~0.013(m)
=9.8~13.7(mm)
按已选定的标准元件的接口尺寸取d=12mm
②吸油管道。
d=2√(22×
10-3/60)/π(0.5~1.5)=0.0176~0.0306(m)
=17.6~30.6(mm)
取d=25mm
③回油管道。
d=2√(70×
10-3/60)/π(1.5~2.5)=0.0243~0.0314(m)
24.3~31.4(mm)
3种管道皆为无缝钢管。
(4)确定油箱容量。
按推荐公式V=(5~7)qp,取V=6×
22=132L。
4)液压系统主要性能的估算。
(1)液压缸的速度。
在液压系统各个元件确定之后,液压缸的实际快进、工进和快退的输入、排出流量和移动速度,和原题目所要求的数值不尽相同,故需要重新估算。
估算结果列入表4中。
流量、速度
排出流量
运动速度
输入流量
q1=A1qp/(A1-A2)=95×
22/(95-44.7)=41.551
q2=q1-qp=41.551-22=19.551
v1=qp/(A1-A2)=22×
10-3/(50.3×
10-4)=4.8
q1=0.29~0.38
q2=A2q1/A1=44.7×
(0.29~0.38)/95.0=0.136~0.179
v2=0.03~0.04
q1=qp=22
q2=A1q1/A2=95.0×
22/44.7=48.98
v3=q1/A2=22×
10-3/(44.7×
10-4)=4.92
(2)系统的效率。
①回路中的压力损失。
计算压力损失时,必须知道管道的长度和直径。
管道直径按选定元件的接口尺寸确定,即d=12mm,回路中的进、回油管长度暂且都按l=12m估算。
油液的运动粘度取υ=75×
10-6m2/s。
a.快进时的回路压力损失。
快进时进油管的流态为层流,即Re=vd/υ=4q1/(πdυ)=4×
41.551×
10-3/(π×
12×
10-3×
75×
10-6×
60)=980.2<
2320,故仅有管的沿程压力损失达西公式计算。
△p11=8×
106×
2×
105/124=2.40×
105(Pa)
进油管的局部压力损失估取为
△p
1=0.1△p11=0.240×
进油路上,油液只经过1个三位五通电磁换向阀5,该阀的局部压力损失为
△pv5=6×
105×
(22/100)2=0.29×
由此的快进时油路上的压力损失为
∑△p=2.40×
105+0.29×
105=2.69×
同样,可以判断出油管中也是层流。
并计算的压力损失为
△p12=1.27×
105(Pa);
△pζ2=0.127×
此时,回油经过二位二通电磁阀6,回油量为q2=19.551.阀6的局部压力损失为
∑△p=2×
(19.551/25)2=1.22×
105Pa
由此可得快进时回油路上的压力损失为
∑△p=1.27×
105+0.127×
105+1.22×
105=2.617×
讲回油路上的压力损失折算到进油路上去,便得出差动快速时进油路上的压力损失为
∑△p1=2.69×
105+2.617×
105=5.307×
b.工进时的回路压力损失。
工进时的进油路上的最大压力损失为
∑△p=0.28×
回油路上的最大压力损失(取调速两端最小压力差为5×
105Pa)为
∑△p=5.16×
整个回路压力损失为
∑△p1=3.04×
c.快退时的回路压力损失为。
快退时整个回路的压力损失为
∑△p1=13.92×
②液压泵的工作压力。
小流量泵在工进时的工作压力,
Pp=p1+∑△p1=27222/(95×
10-4)+3.04×
105=31.74×
③顺序阀的调整压力。
顺序阀在快进、快退时关闭,工进时打开,其调整压力必须保障管得住,开得及时。
由表2知,液压缸在快进、快退时的负载相同,但回路中的压力损失不同,快退时为∑△p1=13.92×
105Pa(快进时为∑△p1=2.69×
105Pa)。
故快退时大流量泵的工作压力出现最高值,即
Pp=p1+∑△p1=555/(44.7×
10-4)+13.92×
105=15.16×
105Pa。
(3)液压回路和型、液压系统的效率。
液压缸的工作压力为
p1=27222/(95.0×
10-4)+5.16×
105(44.7/95.0)=31.1×
经阀9使大流量泵卸荷时的压力损失为
Pp2=3×
105(12/25)2=0.69×
则回路效率ηc为
ηc=p1q1/(Pp1q1+Pp2q2)=0.0029~0.0039
泵的效率取ηp=0.75,液压缸效率取ηm=0.9,则系统效率η∑为
η∑=ηpηcηm=0.75×
(0.0029~0.0039)×
0.9=0.002~0.003
由此可见,定量泵系统在低速工作是效率是很低的。
(4)液压系统发热与温升的验算。
快进、工进和快退所占用的时间分别是
快进:
t1=l1/v1=200×
10-3/(4.8/60)=2.5(s)
工进:
t2=l2/v2=100×
60/(0.03~0.04)=150~200(s)
快退:
t3=l3/v3=300×
60/4.92=3.7(s)
在整个工作循环中,工进所占比例最大,故温升应按公斤工况进行验算。
工进时,液压缸输出的有用功率为
P0=Fv2=24500×
(0.03~0.04)/60=12.3~16.3(w)=0.0123~0.0163(kW)
泵的输入功率为
Pi=(Pp1q1+Pp2q2)/ηp=(31.77×
10+0.69×
12)/(0.75×
60×
1000)=724.4(W)=0.724(kW)
顾得系统的发热为
Hi=Pi-P0=0.724-(0.0123~0.0163)=0.708~0.712(kW)
系统温升计算
△t=Hi×
103/
=(0.708~0.712)×
=27.3~27.5(℃)
此值小于书本表8.6中所规定的允许温升值。
5.总结:
经过一周的实训,对于机床设计从不懂到懵懂再到小懂,液压系统设计运用在各个领域,我们估计连皮毛都没摸到。
液压系统的设计,除了满足主机在动作和性能方面规定的要求外,还必须符合客户要求、体积小、重量轻、成本低、效率高、结构简单、工作可靠、使用和维修方便等一些公认的普遍设计原则,在没有了解基础知识的前提下,是做不到的。
液压系统的设计主要是根据已知的条件,来确定液压工作方案、液压流量、压力和液压泵及其它元件的设计。
本次设计培养了我们对设计工程的设计能力,学习和掌握课件的基本制作方法和步骤,并给我们以后的工作打下初步的基础,通过本次设计,我们把以前在课本中学习到的理论知识在此次设计中加以综合运用对于设计资料能够抓住重点,并懂得简化设计步骤与工序,节省生产材料与成本,这样才不至于使设计过于繁杂,也不会在设计过程中出现太多错误。
6.参考文献:
《液压手册》.软件版
《液压与气压传动》.西南交通大学出版社。
《液压系统设计简明手册》.机械工业出版社。