起重机械安全规程第1部分GB606711代替GBT60671985全解Word下载.docx
《起重机械安全规程第1部分GB606711代替GBT60671985全解Word下载.docx》由会员分享,可在线阅读,更多相关《起重机械安全规程第1部分GB606711代替GBT60671985全解Word下载.docx(35页珍藏版)》请在冰豆网上搜索。
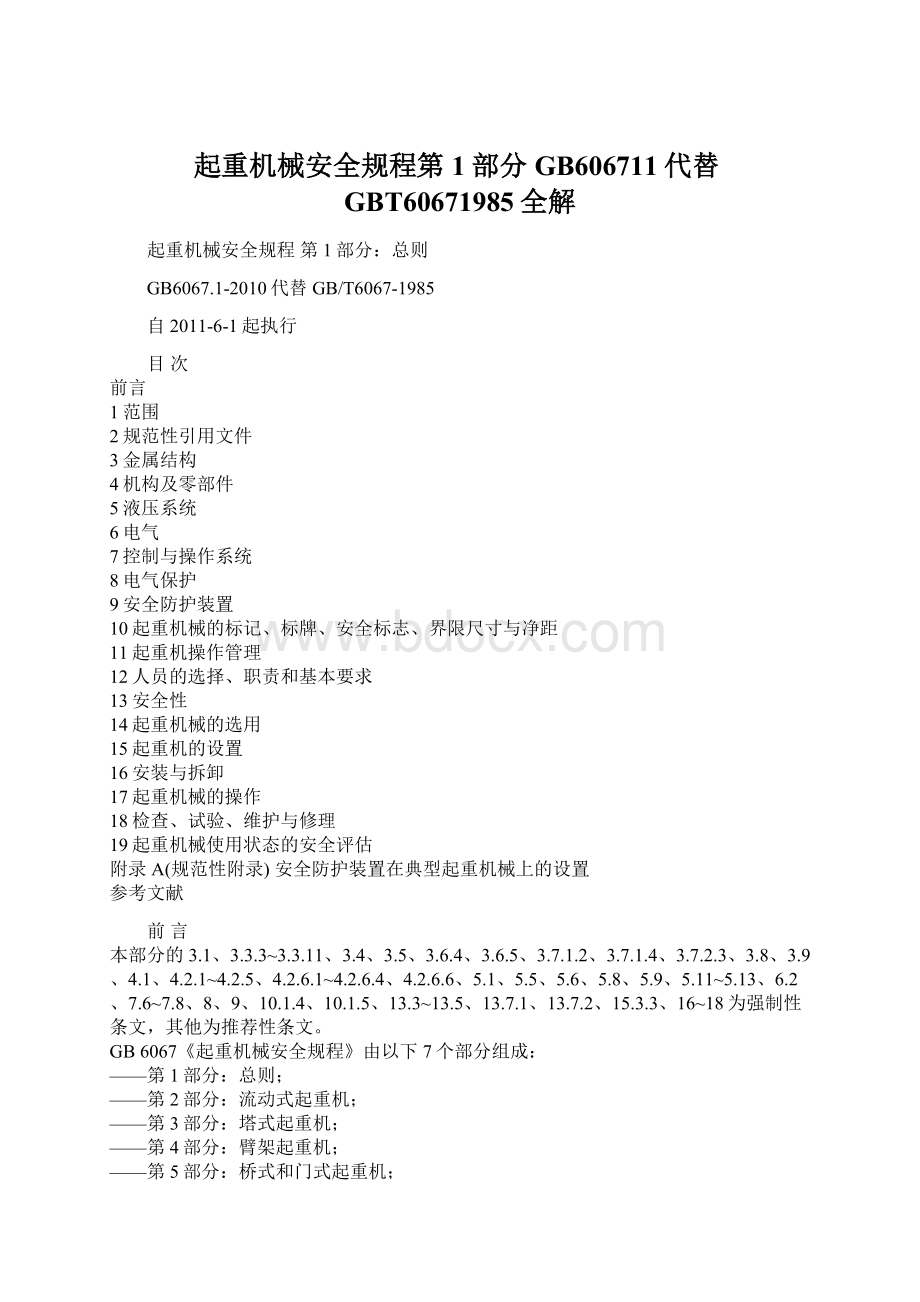
总则;
——第2部分:
流动式起重机;
——第3部分:
塔式起重机;
——第4部分:
臂架起重机;
——第5部分:
桥式和门式起重机;
——第6部分:
缆索起重机;
——第7部分:
轻小型起重设备。
本部分为GB6067《起重机械安全规程》的第1部分。
本部分代替GB/T6067-1985《起重机械安全规程》。
本部分与GB/T6067-1985相比主要变化如下:
——本部分对起重机械及各零部件的安全要求均进行了细化,将原标准中有些属于产品技术要求的内容删除;
——增加了起重机械的标记、标牌、安全标志、界限尺寸与净距的安全要求;
——增加了起重机械操作管理要求;
——增加了起重机械人员的选择、职责和基本要求;
——增加了起重机械的安全性、选用、设置、安装与拆卸、操作、检查、试验、维护与修理、使用状态安全评估等的要求;
——删除了“为吊运各类物品而设的专用辅具”、“常用简易起重设备”的有关要求;
——删除了表1~表5、表7~表15以及表16(部分内容);
将表17改为表A.1。
本部分的附录A为规范性附录。
本部分由中国机械工业联合会提出。
本部分由全国起重机械标准化技术委员会(SAC/TC227)归口。
本部分负责起草单位:
辽宁省安全科学研究院、北京起重运输机械设计研究院。
本部分参加起草单位:
大连重工•起重集团有限公司、太原重型机械集团有限公司、徐州重型机械有限公司、上海振华港机(集团)股份有限公司、卫华集团有限公司、上海起重运输机械厂有限公司、山东丰汇设备技术有限公司、德马格起重机械(上海)有限公司、国电郑州机械设计研究所、长沙建设机械研究院、广东省特种设备检测院。
本部分主要起草人:
尤建阳、崔振元、陶天华、王中平、王福绵、路建湖。
本部分所代替标准的历次版本发布情况为:
——GB/T6067-1985。
GB6067的本部分规定了起重机械的设计、制造、安装、改造、维修、使用、报废、检查等方面的基本安全要求。
本部分适用于桥式和门式起重机、流动式起重机、塔式起重机、臂架起重机、缆索起重机及轻小型起重设备的通用要求。
对特定型式起重机械的特殊要求在GB6067的其他部分中给出。
本部分不适用于浮式起重机、甲板起重机及载人等起重设备。
如不涉及基本安全的特殊问题,本部分也可供其他起重机械参考。
下列文件中的条款通过GB6067的本部分的引用而成为本部分的条款。
凡是注日期的引用文件,其随后所有的修改单(不包括勘误的内容)或修订版均不适用于本部分,然而,鼓励根据本部分达成协议的各方研究是否可使用这些文件的最新版本。
凡是不注日期的引用文件,其最新版本适用于本部分。
GB2893安全色
GB/T3323金属熔化焊焊接头射线照相(GB/T3323-2005,EN1435:
1997,MOD)
GB/T3811-2008起重机设计规范
GB/T4842氩
GB/T5117碳钢焊条(GB/T5117-1995,eqvANSI/AWSA5.1:
1991)
GB/T5118低合金钢焊条(GB/T5118-1995,neqANSI/AWSA5.5:
1981)
GB5226.2-2002机械安全机械电气设备第32部分:
起重机械技术条件(idtIEC60204-32:
1998)
GB/T5293埋弧焊用碳钢焊丝和焊剂(GB/T5293-1999,eqvANSI/AWSA5.17:
1989)
GB/T5905起重机试验规范和程序(GB/T5905-1986,idtISO4310:
GB/T5972起重机钢丝绳保养、维护、安装、检验和报废(GB/T5972-2009,ISO4309:
2004,IDT)
GB/T8110气体保护电弧焊用碳钢、低合金钢焊丝(GB/T8110-2008,AWSA5.18M:
2005,MOD;
AWSA5.28M:
2005,MOD)
GB8918重要用途钢丝绳(GB8918-2006,ISO3154:
1988MOD)
GB/T10051.1起重吊钩机械性能、起重量、应力及材料(GB/T10051.1-1988,eqvDIN
15403-3:
1982)
GB/T10051.2起重吊钩直柄吊钩技术条件(GB/T10051.2-1988,eqvDIN15401-2:
GB/T10051.3起重吊钩直柄吊钩使用检查(GB/T10051.3-1988,eqvDIN15405-1:
1979)
GB/T12470埋弧焊用低合金钢焊丝和焊剂
GB15052起重机安全标志和危险图形符号总则
GB/T17908起重机和起重机械技术性能和验收文件(GB/T17908-1999,idtISO7363:
1986)
GB/T17909.1起重机起重机操作手册第1部分:
总则(GB/T17909.1-1999,idtISO9928-1:
1990)
GB/T18453起重机维护手册第1部分:
总则(GB/T18453-2001,idtISO12478-1:
1997)
GB/T18875起重机备件手册(GB/T18875-2002,ISO10973:
1995,IDT)
GB/T19418钢的弧焊接头缺陷质量分级指南(GB/T19418-2003,ISO5817:
1992,IDT)
GB/T20303.1起重机司机室第1部分:
总则(GB/T20303.1-2006,ISO8566-1:
GB/T20652M(4)、S(6)和T(8)级焊接吊链(GB/T20652-2006,ISO4778:
1981,IDT)
GB/T20947起重用短环链T级(T、DAT和DT型)高精度葫芦链(GB/T20947-2007,
ISO3077:
2001,IDT)
GB/T25196.1起重机状态监控第1部分:
总则(GB/T25196.1-2010,ISO12482-1:
GB50054低压配电设计规范
GB50058爆炸和火灾危险环境电力装置设计规范
HG/T2537焊接用二氧化碳
JB/T6061无损检测焊缝磁粉检测(JB/T6061-2007,ISO17638:
2003,MOD)
JB/T6062无损检测焊缝渗透检测
JB/T10559起重机械无损检测钢焊缝超声检测
JGJ81建筑钢结构焊接技术规程
JGJ82钢结构高强度螺栓连接的设计施工及验收规程
3.1总则
3.1.1起重机械金属结构设计时,应合理选用材料、结构型式和构造措施,满足结构构件在运输、安装和使用过程中的强度(含疲劳强度)、稳定性、刚性和有关安全性方面的要求,并符合防火、防腐蚀要求。
3.1.2在金属结构设计文件中,应注明钢材牌号、连接材料的型号,对重要的受力构件还应注明对钢材所要求的力学性能、化学成分及其他的附加保证项目。
另外,还应注明所要求的焊缝形式、焊缝质量等级。
3.2材料
起重机械承载结构构件的钢材选择应符合GB/T3811-2008中5.3的规定。
3.3结构件焊接要求
3.3.1金属结构制作或安装施工单位应根据JGJ81或有关标准制定本单位的钢结构焊接技术规程。
3.3.2制造单位或安装施工单位对其首次采用的钢材型号、焊接材料、焊接方法、接头形式、焊接位置、焊后热处理工艺以及焊接参数、预热或后热工艺措施等各种参数的组合条件,应进行焊接工艺评定。
3.3.3结构件焊接材料应符合下列要求:
a)手工焊接采用的焊条型号应与主体金属力学性能相适应,且应符合GB/T5117或GB/T5118的规定。
焊丝应符合GB/T8110或GB/T5293的规定。
b)自动焊接或半自动焊接采用的焊丝和相应的焊剂应与主体金属力学性能相适应,应符合GB/T5293和GB/T12470的相关规定。
c)气体保护焊使用的氩气应符合GB/T4842的规定,其纯度应不低于99.95%;
使用的二氧化碳气体应符合HG/T2537的规定。
3.3.4全焊透熔化焊焊接接头的焊缝等级应符合JB/T10559中焊缝等级1、2、3级的分级规定。
3.3.5焊缝内部缺陷的检验应符合下列要求:
a)1级焊缝应进行100%的检验。
采用超声波检验时其评定合格等级应达到JB/T10559中1级焊缝的验收准则要求。
采用射线检验时应达到GB/T3323的规定,其评定合格等级不应低于Ⅱ级;
b)2级焊缝可根据具体情况进行抽检,采用超声波检验时其评定合格等级应达到JB/T10559中2级焊缝的验收准则要求。
采用射线检验时应达到GB/T3323的规定,其评定合格等级不应低于Ⅲ级;
c)3级焊缝可根据具体情况进行抽检,采用超声波检验时其评定合格等级应达到JB/T10559中3级焊缝的验收准则要求。
射线探伤不作规定。
3.3.6有下列情况之一时应进行表面探伤:
a)外观检查怀疑有裂纹;
b)设计文件规定;
c)检验员认为有必要时。
磁粉探伤应符合JB/T6061的规定;
渗透探伤应符合JB/T6062的规定。
3.3.7钢的弧焊接头缺陷质量分级应符合下列规定:
a)1级焊缝钢的弧焊接头缺陷质量分级应符合GB/T19418的B级;
b)2级焊缝钢的弧焊接头缺陷质量分级应符合GB/T19418的C级;
c)3级焊缝钢的弧焊接头缺陷质量分级应符合GB/T19418的D级。
3.3.8焊工应经专业部门考试合格并取得合格证书且在有效期内。
持证焊工应在其考试合格项目及其认可范围内施焊。
3.3.91级焊缝施焊后应具有可追溯性。
3.3.10焊缝无损检测人员应取得相应无损检测资格;
报告编制人员和签发人员应持有相应探伤方法的Ⅱ级或Ⅱ级以上资格证书。
3.3.11焊接质量检验人员应在金属结构制造、检验和测试方面经过培训并取得相应资质。
检验人员应至少完成下列工作任务:
a)应证实使用的相关材料符合本规程要求。
b)应审核操作过程中的焊接程序符合焊接技术规程规定的要求。
c)验施工所用焊接设备符合规定的要求。
d)检验焊缝尺寸、长度和位置符合焊接技术规程或设计图样的要求。
e)应检查焊接材料符合所规定的适用位置,且焊接电流和极性符合焊条型号有关分类的要求。
f)应采用合适的量具测量焊缝的尺寸和外形。
应采用强光、放大镜以及其他有助于这种检验的手段目测检验焊缝、母材上裂纹以及其他不连续性的缺陷。
3.4高强度螺栓连接
3.4.1高强度螺栓连接的设计施工及验收应符合JGJ82的规定。
3.4.2高强度螺栓连接处构件接触面应按设计要求作相应处理,应保持干燥、整洁,不应有飞边、毛刺、焊接飞溅物、焊疤、氧化铁皮、污垢等,除设计要求外接触面不应涂漆。
3.4.3高强度螺栓应按起重机械安装说明书的要求,用扭矩扳手或专用工具拧紧。
连接副的施拧顺序和初拧、复拧扭矩应符合设计要求和JGJ82的规定。
扭矩扳手应定期标定并应有标定记录。
高强度螺栓应有拧紧施工记录。
3.5司机室
3.5.1起重机司机室应符合GB/T20303.1的规定。
3.5.2当臂架俯仰摆动或臂架及物品坠落会影响司机室安全时,司机室不应设置在起重臂架的正下方。
3.5.3当存在坠落物砸碰司机室的危险时,司机室顶部应装设有效的防护。
3.5.4在室外或在没有暖气的室内操作的起重机(除气候条件较好外),宜采用封闭式司机室。
在高温、蒸气、有尘、有毒或有害气体等环境下工作的起重机,应采用能提供清洁空气的密封性能良好的封闭司机室。
在有暖气的室内工作的起重机司机室或仅作辅助性质工作较少使用的起重机司机室,可以是敞开式的,敞开式司机室应设高度不小于1m的护栏。
3.5.5除极端恶劣的气候条件外,在工作期间司机室内的工作温度宜保持在15℃~30℃之间。
长期在高温环境工作的(如某些冶金起重机)司机室内应设降温装置,底板下方应设置隔热板。
3.5.6司机室应有安全出入口;
当司机室装有门时,应防止其在起重机工作时意外打开;
司机室的拉门和外开门应通向同一高度的水平平台;
司机室外无平台时,一般情况下门应向里开;
流动式起重机司机室回转门应向外开,滑动门应向后开。
3.5.7司机室的窗离地板高度不到1m时,玻璃窗应做成不可打开的或加以防护,防护高度不应低于1m;
玻璃窗应采用钢化玻璃或相当的材料。
司机室地板上装有玻璃的部位也应加以防护。
司机室底窗和天窗安装防护栏时,防护栏应尽可能不阻挡视线。
3.5.8司机室地板应用防滑的非金属隔热材料覆盖。
3.5.9司机室工作面上的照度不应低于30lx。
3.5.10重要的操作指示器应有醒目的显示,并安装在司机方便观察的位置。
指示器和报警灯及急停开关按钮应有清晰永久的易识别标志。
指示器应有合适的量程并应便于读数。
报警灯应具有适宜的颜色,危险显示应用红灯。
3.6通道与平台
3.6.1起重机上所有操作部位以及要求经常检查和保养的部位(包括臂架顶端的滑轮和运动部分),凡离地面距离超过2m的,都应通过斜梯(或楼梯)、平台、通道或直梯到达,梯级的两边应装设护栏。
不论起重机在什么位置,通道、斜梯(或楼梯)、平台都应有安全入口。
如臂架可放到地面或人员可到达的部位进行全面直接检查,或者设有其他构造能进行直观检查时,则臂架上也可以不设置通道。
3.6.2起重机处在正常工作状态下的任何位置时,人员应能方便安全地进出司机室。
如果起重机在任何位置,人员不能直接从地面进入司机室,且司机室地板离地面的高度不超过5m,司机室内配备有合适的紧急逃逸装置(例如绳梯)时,则司机室进出口可以限制在某些规定的位置。
如果起重机在任何位置,人员都不能直接从地面进入司机室,以及司机室的地板离地面的高度超过5m时,起重机应设置到达司机室的通道;
对于桥式起重机等,如能提供适当的装置使人员方便安全地离开司机室,则司机室进出口可以限制在某些规定的位置。
一般情况下应通过斜梯或通道,从同司机室地板一样高且备有栏杆的平台直接进入司机室。
平台与司机室入口的水平间隙不应超过0.15m,与司机室地板的高低差不应超过0.25m。
只有在空间受到限制时,才允许通过司机室顶部或地板进入司机室。
3.6.3斜梯、通道和平台的净空高度不应低于1.8m。
运动部分附近的通道和平台的净宽度不应小于0.5m;
如果设有扶手或栏杆,在高度不超过0.6m的范围内,通道的净宽度可减至0.4m。
固定部分之间的通道净宽度不应小于0.4m。
起重机结构件内部很少使用的进出通道,其最小净空高度可为1.3m,但此时通道净宽度应增加到0.7m。
只用于保养的平台,其上面的净空高度可以减到1.3m。
3.6.4工作人员可能停留的每一个表面都应当保证不发生永久变形:
a)2000N的力通过直径为125mm圆盘施加在平台表面的任何位置;
b)4500N/m2的均布载荷。
3.6.5任何通道基面上的孔隙,包括人员可能停留区域之上的走道、驻脚台或平台底面上的狭缝或空隙,都应满足如下要求:
a)不允许直径为20mm的球体通过;
b)当长度等于或大于200mm时,其最大宽度为12mm。
3.6.6通道离下方裸露动力线的高度小于0.5m时,应在这些区域采用实体式地板;
当通道靠近动力线时,应对这些动力线加以保护。
3.7斜梯与直梯
凡高度差超过0.5m的通行路径应做成斜梯或直梯。
高度不超过2m的垂直面上(例如桥架主梁的走台与端梁之间),可以设踏脚板,踏脚板两侧应设有扶手。
3.7.1斜梯
3.7.1.1斜梯的倾斜角不宜超过65°
。
特殊情况下,倾斜角也不应超过75°
(超过75°
时按直梯设计)。
3.7.1.2斜梯两侧应设置栏杆,两侧栏杆的间距:
主要斜梯不应小于0.6m;
其他斜梯可取为0.5m。
斜梯的一侧靠墙壁时,只在另一侧设置栏杆,栏杆高度不小于1m。
3.7.1.3梯级的净宽度不应小于0.32m,单个梯级的高度宜取为0.18m~0.25m,斜梯上梯级的进深不应小于梯级的高度,连续布置的梯级,其高度和进深均应为相同尺寸。
3.7.1.4梯级踏板表面应防滑。
3.7.2直梯
3.7.2.1直梯两侧撑杆的间距不应小于0.40m,两侧撑杆之间梯级宽度不应小于0.30m,梯级的间距应保持一致,宜为0.23m~0.30m,梯级离开固定结构件至少应为0.15m,梯级中心0.1m范围内应能承受1200N的分布垂直力而无永久变形。
3.7.2.2人员出入的爬越孔尺寸,方孔不宜小于0.63m×
0.63m,圆孔直径宜取为0.63m~0.80m。
3.7.2.3高度2m以上的直梯应有护圈,护圈从2.0m高度起开始安装,护圈直径宜取为0.6m~
0.8m。
护圈之间应由三或五根间隔布置的纵向板条联接起来,并保证有一根板条正对着直梯的垂直中心线,相邻护圈之间的距离:
当护圈设置三根纵向板条时,不应大于0.9m,当护圈设置五根纵向板条时,不应大于1.5m。
安装了纵向板条的护圈在任何一个0.1m的范围内应可以承受1000N的分布垂直力,不允许有永久变形。
3.7.2.4除非提供有其他合适的把手,直梯的两边撑杆至少要比最上一个梯级高出1.0m,当空间受限制时此高出的高度也不应小于0.8m。
3.7.2.5装在结构内部的直梯,如果结构件的布置能够保证直径为0.6m的球体不能穿过,则可不设护圈。
3.7.2.6直梯每10m至少应设一个休息平台。
如果空间不够,可以将平台靠在整个连续直梯的旁边。
3.7.2.7直梯的终端宜与平台平齐,梯级终端踏板或踏杆不应超过平台平面。
3.7.2.8如梯子在平台处不中断,则护圈也不应中断,但应在护圈侧面开一宽为0.5m、高为1.4m的洞口,以便人员出入。
3.8栏杆
3.8.1在起重机上的以下部位应装设栏杆:
——用于进行起重机安装、拆卸、试验、维修和保养,且高于地面2m的工作部位;
——通往离地面高度2m以上的操作室、检修保养部位的通道;
——在起重机上存在跌落高度大于1m的危险通道及平台。
3.8.2栏杆的设置应满足以下要求:
——栏杆上部表面的高度不低于1m,栏杆下部有高度不低于0.1m的踢脚板,在踢脚板与手扶栏杆之间有不少于一根的中间横杆,它与踢脚板或手扶栏杆的距离不得大于0.5m;
对净高不超过1.3m的通道,手扶栏杆的高度可以为0.8m;
——在手扶栏杆上的任意点任意方向应能承受的最小力为1000N,且无永久变形;
——栏杆允许开口,但开口处应有防止人员跌落的保护措施;
——在沿建筑物墙壁或实体墙结构设置的通道上,允许用扶手代替栏杆,这些扶手的中断长度(例如为让开建筑物的柱子、门孔)不宜超过1m。
3.9金属结构的修复及报废
3.9.1主要受力构件失去整体稳定性时不应修复,应报废。
3.9.2主要受力构件发生腐蚀时,应进行检查和测量。
当主要受力构件断面腐蚀达设计厚度的10%时,如不能修复,应报废。
3.9.3主要受力构件产生裂纹时,应根据受力情况和裂纹情况采取阻止措施,并采取加强或改变应力分布措施,或停止使用。
3.9.4主要受力构件因产生塑性变形,使工作机构不能正常地安全运行时,如不能修复,应报废。
4.1机构
起重机械各机构的构成与布置,均应满足使用需要,保证安全可靠。
零部件的选择与计算应符合GB/T3811中的有关规定。
4.1.1起升机构应满足下列要求:
a)按照规定的使用方式应能够稳定的起升和下降额定载荷;
b)吊运熔融金属及其他危险物品的起升机构,每套独立驱动装置应装有两个支持制动器;
在安全性要求特别高的起升机构中,应另外装设安全制动器;
c)起升机构应采取必要的措施避免起升过程中钢丝绳缠绕;
d)当吊钩处于工作位置最低点时,卷筒上缠绕的钢丝绳,除固定绳尾的圈数外,不应少于2圈;
当吊钩处于工作位置最高点时,卷筒上还宜留有至少l整圈的绕绳余量。
4.1.2运行机构应满足下列要求:
a)按照规定的使用方式应能够使整机和小车平稳地启动和停止;
b)露天工作的轨道运行式起重机应设有可靠的防风装置。
4.1.3回转机构在工作状态下,按照规定的使用方式应能够平稳地启动和停止。
4.1.4变幅机构应满足下列要求:
a)按照规定的使用方式,起升机构悬吊额定载荷时,动臂变幅机构应能够提升和下降臂架并能保持在静止状态(不允许带载变幅的变幅机构应保持臂架在静止状态);
b)采用钢丝绳变幅的机构,变幅机构的卷筒必须有足够的容绳量,保证完成起重臂从最大幅度到最小幅度位置的作业。
4.2零部件
4.2.1钢丝绳
4.2.1.1钢丝绳安全系数应符合GB/T3811-2008中表44的规定。
4.2.1.2载荷由多根钢丝绳支承时,宜设置能有效地保证各根钢丝绳受力均衡的装置。
如果结构上无法消除载荷在各钢丝绳之间分布的不均匀性,则应在设计中予以考虑。
4.2.1.3起升机构和非平衡变幅机构不应使用接长的钢丝绳。
4.2.1.4吊运熔融或炽热金属的钢丝绳,应采用性能不低于GB8918规定的钢丝绳。
4.2.1.5钢丝绳端部的固定和连接应符合如下要求:
a)用绳夹连接时,应满足表1的要求,同时应保证连接强度不小于钢丝绳最小破断拉力的85%。
表1钢丝绳夹连接时的安全要求
b)用编结连接时,编结长度不应小于钢丝绳直径的15倍,并且不小于300mm。
连接强度不应小于钢丝绳最小破断拉力的75%。
c)用楔块、楔套连接时,楔套应用钢材制造。
d)用锥形套浇铸法连接时,连接强度应达到钢丝绳的最小破断拉力。
e)用铝合金套压缩法连接时,连接强度应达到钢丝绳最小破断拉力90%。
4.2.1.6钢丝绳的保养、维护、安装、检验、报废应符合GB/T5972的有关规定。
4.2.2吊钩、吊钩夹套及其他取物装置
4.2.2.1锻造吊钩的机械性能、起重量、应力及材料应符合GB/T10051.1的规定。
4.2.2.2起重机械不应使用铸造吊钩。