固定管板式换热器设计要求摘要模板Word格式.docx
《固定管板式换热器设计要求摘要模板Word格式.docx》由会员分享,可在线阅读,更多相关《固定管板式换热器设计要求摘要模板Word格式.docx(33页珍藏版)》请在冰豆网上搜索。
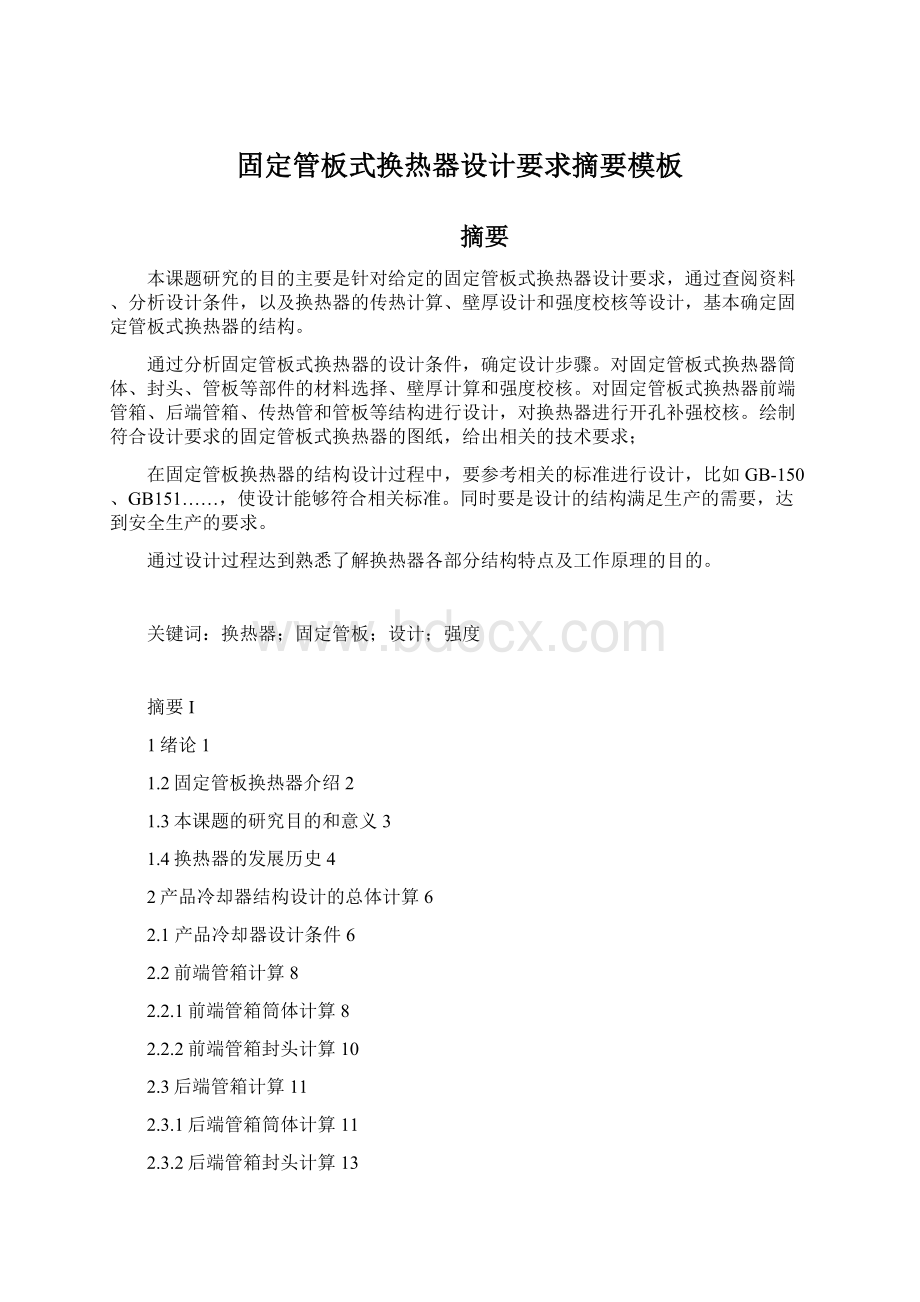
5.1总则34
5.2零部件的制造34
结论43
参考文献:
44
致谢44
1绪论
1.1换热器的作用及分类
在工业生产中,换热设备的主要作用是使热量由温度较高的流体传递给温度较低的流体,使流体温度达到工艺过程规定的指标,以满足工艺过程上的需要。
此外,换热设备也是回收余热、废热特别是低位热能的有效装置。
例如,烟道气、高炉炉气、需要冷却的化学反应工艺气等余热,通过余热锅炉可生产压力蒸汽,作为供热、供气、发电和动力的辅助能源,从而提高热能的总利用率,降低燃料消耗和电耗,提高工业生产经济效益。
换热器还广泛应用于化工、石油、动力和原子能等工业部门。
它的主要功能是保证工艺过程对介质所要求的特定温度,同时也是提高能源利用率的主要设备之一,应用甚为广泛。
按换热设备热传递原理或换热方式分类,可分为以下几种主要形式。
(1)直接接触式换热器
这类换热器又称混合式换热器。
这类换热器具有传热效率高、单位容积提供的传热面积大、设备结构简单、价格便宜等优点,但仅适用于工艺上允许两种流体混合的场合。
(2)蓄热式换热器
这类换热器又称为回热式换热器。
蓄热式换热器结构紧凑、价格便宜、单位体积传热面大,故较适用于气-气热交换的场合。
如回转式空气预热器就是一种蓄热式换热器。
、
(3)间壁式换热器
这类换热器又称表面式换热器。
间壁式换热器式工业生产中应用较为广泛的换热器,其形式多种多样,如常见的管壳式换热器和板式换热器都属于间壁式换热器。
(4)中间载热体式换热器
这类换热器是把两个间壁式换热器由在其中循环的载热体连接起来的换热器。
载热体在高温流体换热器和低温流体换热器之间循环,在高温流体换热器中吸收热量,在低温流体换热器中把热量释放给低温流体,如热管式换热器。
按传热表面结构特点分类
(1)管式:
套管式、壳管式、蛇管式
(2)板式
(3)扩展表面式:
板翅式、翅片管式及管带式
(4)蓄热式
按流程又可以分为单流程和多流程。
1.2固定管板换热器介绍
固定管板式换热器的两端管板采用焊接方法与壳体连接固定。
换热管可为光管或低翅管。
其结构简单,制造成本低,能得到较小的壳体内径,管程可分成多样,壳程也可用纵向隔板分成多程,规格范围广,故在工程中广泛应用。
固定管板式换热器主要特点
固定管板式换热器主要有外壳、管板、管束、顶盖(又称封头)等部件构成。
在圆形外壳内,装入平行管束,管束两端用焊接或胀接的方法固定在管板上,两块管板与外管直接焊接,装有进口或出口管的顶盖用螺栓与外壳两端法兰相连。
它的特点是结构简单,没有壳侧密封连接,相同的壳体内径排管最多,在有折流板的流动中旁路最小,管程可以分成任何管程数,因两个管板由管子互相支撑,故在各种管壳式换热器中它的管板最薄,造价最低,因而得到广泛应用。
这种换热器的缺点是:
壳程清洗困难,有温差应力存在。
当冷热两种流体的平均温差较大,或壳体和传热管材料膨胀系数相差较大,热应力超过材料的许用应力时,在壳体上需设膨胀节,由于膨胀节强度的限制,壳程压力不能太高。
这种换热器适用于两种介质温差不大,或温差较大但壳程压力不高,及壳程介质清洁,不易结垢的场合。
1.3本课题的研究目的和意义
换热器的基建投资在一般化工、石化企业中约占设备总投资的20%,其中固定管板式换热器约占换热器的70%。
固定管板式换热器的两端管板和壳体制成一体,当两流体的温度差较大时,在外壳的适当位置上焊上一个补偿圈,(或膨胀节)。
当壳体和管束热膨胀不同时,补偿圈发生缓慢的弹性变形来补偿因温差应力引起的热膨胀。
特点:
结构简单,造价低廉,壳程清洗和检修困难,壳程必须是洁净不易结垢的物料。
固定管板式换热器主要有外壳、管板、管束、封头压盖等部件组成。
固定管板式换热器的结构特点是在壳体中设置有管束,管束两端用焊接或胀接的方法将管子固定在管板上,两端管板直接和壳体焊接在一起,壳程的进出口管直接焊在壳体上,管板外圆周和封头法兰用螺栓紧固,管程的进出口管直接和封头焊在一起,管束内根据换热管的长度设置了若干块折流板。
这种换热器管程可以用隔板分成任何程数。
固定管板式换热器结构简单,制造成本低,管程清洗方便,管程可以分成多程,壳程也可以分成双程,规格范围广,故在工程上广泛应用。
壳程清洗困难,对于较脏或有腐蚀性的介质不宜采用。
当膨胀之差较大时,可在壳体上设置膨胀节,以减少因管、壳程温差而产生的热应力。
本课题所设计的冷却器属于固定管板换热器,是针对给定的设计参数,按照相关规定的要求,通过壁厚计算和强度校核等,设计固定管板式换热器产品。
熟悉压力容器设计的基本要求,掌握固定管板式换热器的常规设计方法,把所学的知识应用到实际的工程设计中去,为以后的工作和学习打下扎实的基础。
1.4换热器的发展历史
二十世纪20年代出现板式换热器,并应用于食品工业。
以板代管制成的换热器,结构紧凑,传热效果好,因此陆续发展为多种形式。
30年代初,瑞典首次制成螺旋板换热器。
接着英国用钎焊法制造出一种由铜及其合金材料制成的板翅式换热器,用于飞机发动机的散热。
30年代末,瑞典又制造出第一台板壳式换热器,用于纸浆工厂。
在此期间,为了解决强腐蚀性介质的换热问题,人们对新型材料制成的换热器开始注意。
60年代左右,由于空间技术和尖端科学的迅速发展,迫切需要各种高效能紧凑型的换热器,再加上冲压、钎焊和密封等技术的发展,换热器制造工艺得到进一步完善,从而推动了紧凑型板面式换热器的蓬勃发展和广泛应用。
此外,自60年代开始,为了适应高温和高压条件下的换热和节能的需要,典型的管壳式换热器也得到了进一步的发展。
70年代中期,为了强化传热,在研究和发展热管的基础上又创制出热管式换热器。
换热器按传热方式的不同可分为混合式、蓄热式和间壁式三类。
混合式换热器是通过冷、热流体的直接接触、混合进行热量交换的换热器,又称接触式换热器。
由于两流体混合换热后必须及时分离,这类换热器适合于气、液两流体之间的换热。
例如,化工厂和发电厂所用的凉水塔中,热水由上往下喷淋,而冷空气自下而上吸入,在填充物的水膜表面或飞沫及水滴表面,热水和冷空气相互接触进行换热,热水被冷却,冷空气被加热,然后依靠两流体本身的密度差得以及时分离。
蓄热式换热器是利用冷、热流体交替流经蓄热室中的蓄热体(填料)表面,从而进行热量交换的换热器,如炼焦炉下方预热空气的蓄热室。
这类换热器主要用于回收和利用高温废气的热量。
以回收冷量为目的的同类设备称蓄冷器,多用于空气分离装置中。
间壁式换热器的冷、热流体被固体间壁隔开,并通过间壁进行热量交换的换热器,因此又称表面式换热器,这类换热器应用最广。
间壁式换热器根据传热面的结构不同可分为管式、板面式和其他型式。
管式换热器以管子表面作为传热面,包括蛇管式换热器、套管式换热器和管壳式换热器等;
板面式换热器以板面作为传热面,包括板式换热器、螺旋板换热器、板翅式换热器、板壳式换热器和伞板换热器等;
其他型式换热器是为满足某些特殊要求而设计的换热器,如刮面式换热器、转盘式换热器和空气冷却器等。
换热器中流体的相对流向一般有顺流和逆流两种。
顺流时,入口处两流体的温差最大,并沿传热表面逐渐减小,至出口处温差为最小。
逆流时,沿传热表面两流体的温差分布较均匀。
在冷、热流体的进出口温度一定的条件下,当两种流体都无相变时,以逆流的平均温差最大顺流最小。
在完成同样传热量的条件下,采用逆流可使平均温差增大,换热器的传热面积减小;
若传热面积不变,采用逆流时可使加热或冷却流体的消耗量降低。
前者可节省设备费,后者可节省操作费,故在设计或生产使用中应尽量采用逆流换热。
当冷、热流体两者或其中一种有物相变化(沸腾或冷凝)时,由于相变时只放出或吸收汽化潜热,流体本身的温度并无变化,因此流体的进出口温度相等,这时两流体的温差就与流体的流向选择无关了。
除顺流和逆流这两种流向外,还有错流和折流等流向。
在传热过程中,降低间壁式换热器中的热阻,以提高传热系数是一个重要的问题。
热阻主要来源于间壁两侧粘滞于传热面上的流体薄层(称为边界层),和换热器使用中在壁两侧形成的污垢层,金属壁的热阻相对较小。
增加流体的流速和扰动性,可减薄边界层,降低热阻提高给热系数。
但增加流体流速会使能量消耗增加,故设计时应在减小热阻和降低能耗之间作合理的协调。
为了降低污垢的热阻,可设法延缓污垢的形成,并定期清洗传热面。
一般换热器都用金属材料制成,其中碳素钢和低合金钢大多用于制造中、低压换热器;
不锈钢除主要用于不同的耐腐蚀条件外,奥氏体不锈钢还可作为耐高、低温的材料;
铜、铝及其合金多用于制造低温换热器;
镍合金则用于高温条件下;
非金属材料除制作.换热器等。
2产品冷却器结构设计的总体计算
2.1产品冷却器设计条件
图2-1冷却器见图
1前端管箱封头2前端管箱筒体3管板4管箱法兰5壳体法兰6壳程筒体7换热管8壳程筒体开孔法兰9管箱筒体开孔法兰10后端管箱筒体11后端管箱封头
产品冷却器属于固定管板换热器,是利用冷却水将热流体冷却的设备。
卧式固定管板式换热器:
封头管箱,公称直径500mm,管程设计压力4MPa,壳程设计压力4MPa,公称换热面积78.8㎡,Ⅰ级管束为碳素钢较高冷拔换热管,换热管外径19mm,管长4.5m,两管程,两壳程。
压力容器类别为二类容器;
管、壳程介质均为烃;
介质特性:
轻毒、易燃、易爆、易挥发;
左管箱需要做焊后热处理,右管箱不需要做焊后热处理;
进行100%无损检测;
管子与管板连接形式:
强度焊+贴胀;
壳程工作压力2.21MPa,管程工作压力2.31MPa(冬季)/2.26MPa(夏季)。
进/出口工作温度:
壳程55.5/40℃(冬季),55.5/40.4℃(夏季);
管程-14.1/7.4℃(冬季),28.2/45℃(夏季)。
设计温度:
壳程120/-45℃;
管程120/-45℃。
金属壁温:
壳程47.75℃(冬季),47.95℃(夏季);
管程28℃(冬季),44℃(夏季)。
最小设计金属温度:
壳程-45℃@4.00MPa,管程-45℃@4.00MPa。
腐蚀裕量:
壳程1.5mm,管程1.5mm。
焊接接头系数:
壳程1.0,管程1.0。
水压试验压力:
壳程5.0MPa,管程5.0MPa。
管板切割率:
32.5%
根据上述已知条件设计出符合要求的换热器,以满足生产需要。
2.2前端管箱计算
2.2.1前端管箱筒体计算
图2-2-1前端管箱筒体
选用材料:
20R(20号压力容器用钢材,这种钢材一方面在国家规范上满足要求,一方面有害元素较少,综合性能好些。
设计温度下许用应力:
132.6Mpa(参见过程设备设计399页表D1钢板许用应力)
常温下许用应力:
133MPa(参见过程设备设计399页表D1钢板许用应力)
常温下屈服点:
245MPa(参见过程设备设计399页表D1钢板许用应力)
平均温度下弹性模量:
********MPa
平均温度下线胀系数:
********1/
制定板材负偏差为零(设定值)
=式2.1
计算厚度:
7.66mm(见式2.1)
有效厚度:
e=n-C1-C2=8.50mm
名义厚度:
n=10.00mm
重量:
m=62.88
密度为7850Kg/m³
压力试验:
液压试验
PT=1.25P式2.2
试验压力值:
5.0000Mpa(见式2.2)
压力试验允许通过的应力水平:
T0.90s=220.50Mpa
T=式2.3
试验压力下圆筒的应力:
149.56Mpa(见式2.3)
校核条件:
TT
校核结果:
合格
压力及应力计算:
[Pw]=式2.4
最大允许工作压力:
4.43304Mpa(见式2.4)
t=式2.5
设计温度下计算应力:
119.65Mpa(见式2.5)
t=132.6Mpa
t≥t
结论:
2.2.2前端管箱封头计算
图2-2-2前端管箱封头
封头材料类型:
板材
20R
封头形式:
标准椭圆封头
选形状系数为K=1
封头曲面高度h:
125mm
封头直边高度c:
25mm
试验温度许用应力:
133Mpa
设计温度许用应力:
132.6Mpa
K=式2.6
形状系数:
1.0000(见式2.6)
=式2.7
7.60mm(见式2.7)
最小厚度:
min=0.75mm
满足最小厚度要求
24.74=Kg
[Pw]=式2.8
=4.47040Mpa(见式2.8)
2.3后端管箱计算
2.3.1后端管箱筒体计算
图2-3-1后端管箱筒体
132.6MPa
133MPaMPa
245
指定板材负偏差为零
=7.66mm(见式2.1)
PT=5.0000Mpa(见式2.2)
T=149.56Mpa(见式2.3)
[Pw]4.43304Mpa(见式2.4)
t=119.65Mpa(见式2.5)
2.3.2后端管箱封头计算
图2-3-2后端管箱封头
椭圆封头
封头直边高度:
K=1.0000(见式2.6)
=7.60mm(见式2.7)
[Pw]=4.47040Mpa(见式2.8)
合格
2.4壳程圆筒计算
图2-3壳程管筒
材料类型:
材料:
筒体内径:
500mm
筒体长度:
4400mm
1.5mm
筒体名义厚度:
10mm
纵向焊缝焊接接系数:
1
环向焊缝焊接接头系数:
=7.66mm(见式2.1)
553.39Kg
压力试验类型:
压力试验下圆筒的应力:
T=149.56Mpa(见式2.3)
压力及应力计算
[Pw]=4.43304Mpa(见式2.4)
t=119.65Mpa(见式2.5)
t≥t
筒体名义厚度大于或等于GB151中规定的最小厚度6.50mm,合格
3各部分强度校核
图3-1设备上的开孔及接管
3.1开孔补强计算
对筒体上接管为φ89×
10的开孔进行补强
补强设计方法:
单孔补强
开孔处壳体材料类型:
壳体材料:
壳体材料在设计温度下的许用应力:
接管腐蚀裕量:
接管实际外伸高度:
150mm
接管实际内伸高度:
接管材料:
管材
20(GB8163)
接管材料在设计温度下的许用应力:
130Mpa
接管材料在常温下的许用应力:
接管焊接接头系数:
补强结构:
无补强结构
接管和壳体连接结构形式:
插入式接管
焊缝金属截面积:
32mm
计算方法:
GB150-1998等面积补强法,单孔
开孔直径d:
74.5mm
补强区有效宽度B:
149mm
接管材料强度削弱系数fr:
0.98
接管有效外伸长度h1:
27.29.mm
接管有效内伸长度h2:
27.29mm
开孔削弱所需的补强面积A:
572.6mm
壳体多余金属面积A1:
62.57mm
接管多余金属面积A2:
638mm
补强区内的焊接面积A3:
A1+A2+A3=732.6mm2,大于A,不需另加补强。
结论:
补强满足要求,不需另加补强。
对筒体上接管为φ32×
8的开孔进行补强
32mm
21mm
57mm
12.96mm
12.96mm
162.4mm
30.17mm
235.1mm
A1+A2+A3=297.3mm²
,大于A,不需另加补强。
对前端管箱筒体上接管为φ159×
15的开孔进行补强
16Mn(热轧)
163Mpa
135.8mm
271.5mm
45.12mm
45.12mm
1039mm
114.4mm
1818mm
A1+A2+A3=1965mm2大于A,不需另加补强。
对后端管箱筒体上接管为φ25×
14mm
50mm
10.58mm
10.58mm
108.8mm
194.2mm
A1+A2+A3=256.4mm2,大于A,不需另加补强。
3.2壳程圆筒校核
图3-2壳程圆筒
平均金属温度ts:
48C
装配温度ts:
15
平均金属温度下弹性模量Es:
********
平均金属温度下热膨胀系数s:
A=0.25Di2式3.1
壳程圆筒内直径横截面积:
********mm2(见式3.1)
As=s(Di+s)式3.2
壳程圆筒金属界面积:
********mm2(见式3.2)
3.3管箱圆筒校核
设计压力:
4Mpa
120
材料名称:
设计温度下弹性模量:
********Mpa
管箱圆筒名义厚度(管箱为高径法兰取法兰颈部大小端平均值):
16mm
管箱圆筒有效厚度:
8.5mm
管箱法兰设计温度下弹性模量: