乳化设备及乳化工艺Word下载.docx
《乳化设备及乳化工艺Word下载.docx》由会员分享,可在线阅读,更多相关《乳化设备及乳化工艺Word下载.docx(14页珍藏版)》请在冰豆网上搜索。
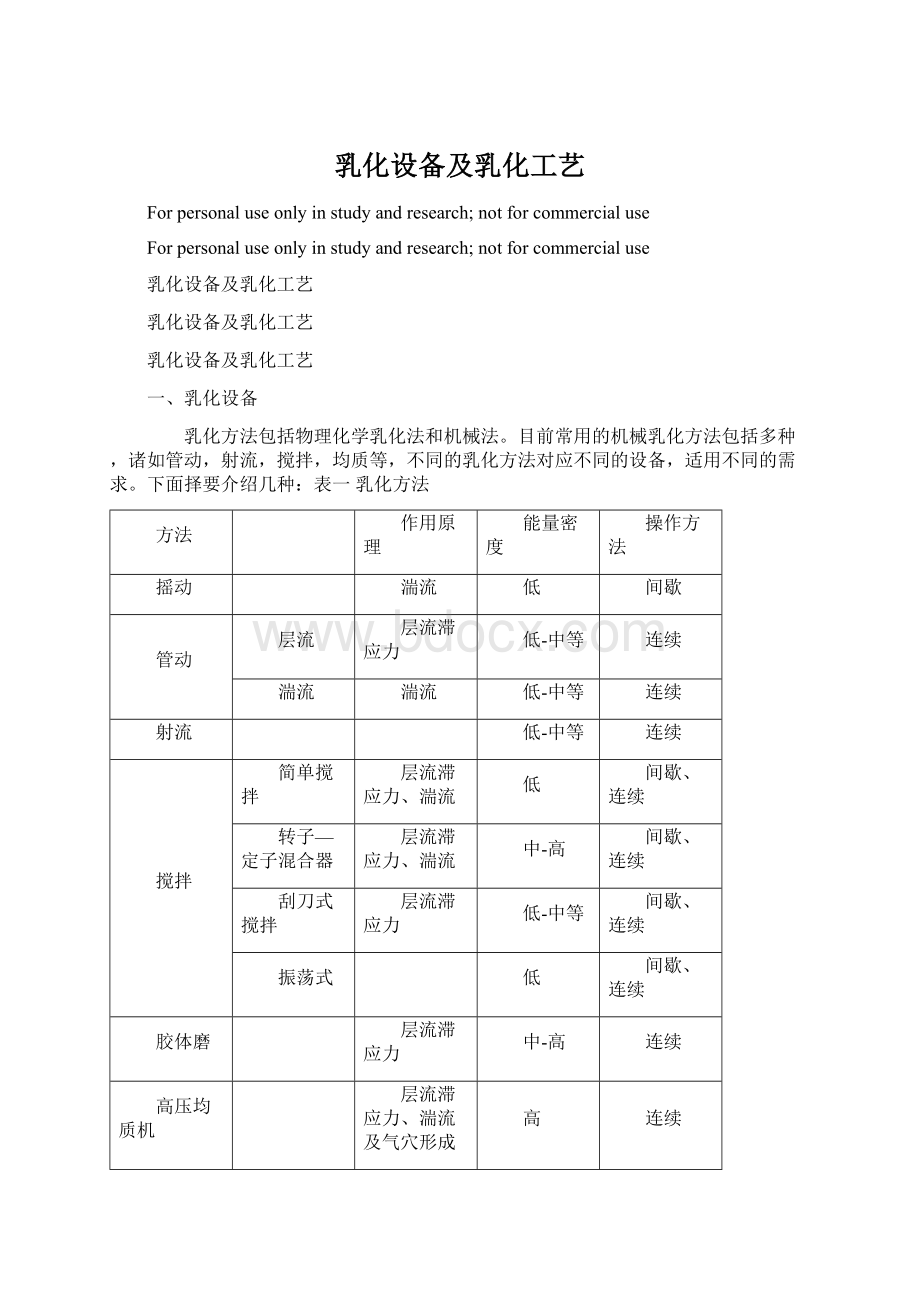
层流滞应力
低-中等
连续
射流
搅拌
简单搅拌
层流滞应力、湍流
间歇、连续
转子—定子混合器
中-高
刮刀式搅拌
振荡式
胶体磨
高压均质机
层流滞应力、湍流及气穴形成
高
超声均质器
振动叶片
湍流、气穴形成
磁致收缩
气穴形成
中-高
1、搅拌
指借助于流动中的两种或两种以上物料在彼此之间相互散布的一种操作,以实现物料的均匀混合,同时还可以促进气体溶解、强化热交换等。
1.1搅拌混合机理搅拌混合机理主要包括对流混合,扩散混合,剪切混合。
(1)对流混合是在搅拌容器中,通过搅拌器的旋转把机械能传给液体物料造成液体的流动,属强制对流。
包括主体对流—物料大范围的循环流动;
涡流对流—漩涡的对流运动。
(2)扩散混合指互溶组分中存的的混合现象,是液体分子间的均匀分布,对流混合可促进扩散混合。
(3)搅拌桨将物料组分拉成愈来愈薄的料层,使某一组分原来占有区域的尺寸越来越小,达到混合的目的。
高粘度物料混合过程主要靠剪切作用。
1.2搅拌器的构造和类型1.2.1搅拌器的构造搅拌器是通过搅拌使物料均匀混合的装置,主要由搅拌装置、搅拌罐和轴与轴封三大部分组成。
1.2.2搅拌器的类型搅拌器主要包括小面积叶片高速运转的搅拌器,诸如涡轮式、桨式搅拌器等,多适用于低粘度的物料;
另外就是大面积低速运转的搅拌器,诸如框式、螺带式及行星式搅拌器等。
1.2.2.1桨式搅拌器桨式搅拌器是最常用的一种,桨叶由条钢制造,有平桨式和斜桨式两种。
平桨式搅拌器由两片叶片平直桨叶构成,主产生径向流和切向流;
斜桨式搅拌器的两叶相反折转一定角度,这样不仅可以产生轴向流,还可以减小阻力。
桨式搅拌器结构简单,适用于低粘度物料的混合,当容器内液位较高时,可在同一轴上同时安装几个桨叶。
桨叶固定轴上的方式主要有三种:
(1)焊接法:
桨叶和轴整体焊接在一起,此结构不可拆卸清洗及更换,强度也不大,且容易打滑,主要适用小容器。
(2)螺钉连接法:
通过螺钉将桨叶连接在轴上,中间有垫片。
当轴式圆形的时候,主要靠桨叶和轴的摩擦力而使桨叶运动,此结构拆卸方便,但功率大时易产生滑动,故多用小功率设备中。
(3)方轴连接法:
这方法主要是客服焊接法容易打滑的缺点,但轴的加工困难。
(4)方轴、螺钉连接法:
为了克服焊接法的易打滑及方轴连接法的难于制造等缺点而设计的,被广泛采用。
1.2.2.2旋桨式搅拌器旋桨式搅拌器类似于无壳的轴流泵,由2~3片旋转桨组成不同形式(见下图),桨叶是用螺母固定在轴上,螺母的拧紧方向与桨叶旋转方向相反,这样才能借阻力作用使螺母在搅拌器运转时愈来愈紧。
旋转直径约为容器直径的0.2~0.3倍,以轴流混合为主,伴有切向流和径向流,但湍流程度不高。
搅拌桨转速高,循环量大,适用于大容器低粘度物料的混合,该搅拌不适用粘稠物料。
1.2.2.3涡轮式搅拌器涡轮式搅拌器类似于无壳的离心泵,由圆盘、轴、及多块叶片组成,结构复杂,种类较多,主要有开启涡轮式和圆盘涡轮式两种(见下图)
涡轮式搅拌器转速高,一般转速为100~2000rpm,平直叶片产生强烈的径向和切线流动,通常加挡板以减小中央旋涡,同时增强因折流而引起的轴向流,工作时,搅拌液沿轴线由中心孔而进入轮内,有各小叶片工作因而加热,然后再以高速度偶轮抛出,湍流程度强,剪切力大,可将微团细化。
涡轮式搅拌器适合处理中低粘度物料,混合生产能力较高,按一定的设计形式,具有较高的局部剪力效应,且易清洗,但价格较高。
1.2.2.4框式和锚式搅拌器框式和锚式搅拌器适用于高粘度物料的搅拌,其外形轮廓与容器壁形状相似,底部形状为适应罐底轮廓,多为椭圆或锥形等,桨叶外缘至容器底部的距离要适当,以30~50mm为宜,但由于高浓度物料搅拌时只能取5mm,这时要求加工及安装的精度却高,否则外片可能碰上器壁而损坏设备。
如上图所知,框式和锚式搅拌器的结构简单坚固,制造方便,而且在搅动时能搅动大量的物料,不会产生死区。
此类搅拌器的转速较慢,所产生的液流的径向速度较大,而轴向速度甚低,为了加强轴向混合,并减小因切线速度所产生的表面旋涡,通常加装挡板。
1.2.2.5螺带式与螺杆式搅拌器螺带式搅拌器是由一定宽度的带材或圆柱棒材制作成螺带形状。
它可以有单条或双条螺带结构。
一般螺带的外廓尺寸接近容器内壁,使搅拌操作遍及整个罐体。
螺杆式搅拌器四用支撑杆使螺带固定在搅拌轴上。
每个螺距设置杆件2~3根。
支撑杆一端与螺带焊接,另一端夹紧在搅拌轴上,也可以采用支撑杆与轴的连接的形式(见下图)。
螺带式与螺杆式搅拌器,转速慢,适用于高粘度的物料的搅拌。
1.2.2.6行星式搅拌器行星式搅拌器旋转桨的轴不仅自转,还能绕容器旋转,搅拌速度高,适用于高粘度液体的搅拌,但是结构复杂,制作繁琐。
2、均质机
均质是一种特殊的操作,通过均质,可使两种互不相容的的液体进行密切混合,是一种液体粉碎为极细小微粒或液滴分散在另一液体中的过程,像乳状液。
目前主要有以下几种均质机:
2.1高压均质机2.1.1高压均质机结构高压均质机主要由泵体和均质阀或安全阀、电动机、传动机与机架几个部分组成。
高压泵多采用三柱塞式往复泵,由共用一根轴的三个作用泵组成,三个单作用泵的曲柄互相错开120度,其吸液泵和排液泵也是三个泵共用。
这样,在曲轴旋转一周的周期里,各泵的吸液或排液依次相差1/3周期,大大提高排液泵流量的均匀性。
三作用泵的流量各为单作用泵的三倍。
均质阀安装在高压泵的排出路上,由阀座、阀杆和冲击环组成,国外多采用钨钴铬合金(用于牛奶均质)或硬质合金(腐蚀性强的液料)等制成,而国内多采用4Cr13。
目前多数高压均质机均采用二级均质阀,以获得更均匀更细小的乳化粒子。
以下即为一级、二级均质阀的结构图及双击均质阀工作示意图。
2.2.2高压均质机的工作原理高压均质机是基于对物料的挤压、剪切、涡流、泄压、空穴作用,从而达到颗粒减小、分散均匀的目的。
(1)剪切学说:
当高压物料在阀盘与阀座间流过时,在缝隙中心流速最大,而在缝隙避面处液体流速最小,促使了速度梯度的产生,液滴之间相互挤压、剪切,从而达到乳化均质。
(2)撞击学说:
由于三柱塞往复泵的高压作用,液滴与均质阀发生高速撞击,从而导致液滴破裂变小,起到均质的作用。
(3)空穴学说:
高压作用下,液料高频振动,导致液料交替压缩与膨胀,引起空穴小泡的产生,这些小泡破裂时会在流体中释放出很强的冲击波,如果这种冲击波发生在大液滴的附近,就会造成液滴的破裂,乳液得到进一步细化。
2.2高剪切均质机高剪切均质机是目前用的最广泛的均质机,由转子或转子-定子系统构成,工作时高速回转,在叶片作用下流入的液体通过窄小的缝隙,在很高的剪切力作用下破碎、分散、混合。
经过高剪切均质机的物料粒径可达到1μm,且稳定性好,能耗低,对材质也无特殊要求。
2.2.1高剪切均质机的分类高剪切均质机可分为轴流式和径流式。
结构如图所示:
2.2.2高剪切均质机的工作原理
2.2.3高剪切均质机的工作流程
2.3胶体磨胶体磨和高剪切均质机一样均属于定子-转子系统,由一可高速旋转的磨盘(转动件)与一固定的磨面(固定件)所组成。
两表面间有可调节的微小间隙,通常为50~150m,当物料从此间隙通过时,由于磨盘高速旋转,附于旋转面上的物料速度最大,而附于固定面上的物料速度为零,其间产生较高的速度梯度,从而使物料受到强烈的剪切摩擦和湍动骚扰,产生微粒化分散化作用。
胶体磨有卧式和立式两种,一般用于中低等粘度的料液。
2.4超声波均质机超声波均质可以由于振动叶片或磁致收缩而使物料变细,达到均质的效果。
下面我简要介绍一下由于振动叶片而产生的均质作用,下图为超声波发生器的简要结构。
当物料从供液管经喷出口高速流入管路时,调节频率,使激发频率与簧片的固有频率相当,从而产生超声波共振。
(其中,激发频率与液体的流速成正比,而与喷嘴和簧片间的距离成反比。
)使得物料在舌簧片附近产生空穴作用,液滴得以破碎;
破碎后的物料可以再一次经过供液管进入管路,进行再一次的破碎,如此反复即可。
搅拌促使物料之间的均匀混合,不同粘度的物料应选择使用不同类型的搅拌。
由于搅拌能量较低,通过搅拌进行乳化只能得到粒径较大的乳液,而通过均质机可以乳液液滴的大小达到0.1m,甚至更小(见下图)其中“1”为搅拌,“2”为胶体磨,“2”超声波,“4”高剪切均质,“5”高压均质。
此外,近来开发了一种新型乳化技术—膜乳化技术。
微孔膜的膜乳化技术采用微孔膜乳化设备,其乳化方式是在压力作用下,使分散相穿过微孔膜的孔道进人连续相而形成乳剂。
当连续相在膜表面流动时,分散相在压力作用下通过嫩孔膜孔在膜表面形成液滴,此液滴的直径达到某一值时就从膜表面剥离进人连续相,溶解在连续相里的乳化剂分子将吸附到液滴界面上.
二、乳化工艺的控制和调整
不同的工艺和不同的设备,即使同样的配方,也有可能在产品黏度、稳定性和乳剂剂型等方面产生不同的结果。
1搅拌强度和搅拌时间在制备中,超声或搅拌时间及速率等会直接影响乳剂的稳定性、黏度等性能。
当将初乳乳滴分散到水相制备复乳时,若搅拌过久或过猛,油滴可能会部分破裂,内外水相合并。
kochi等发现初乳乳滴粒径大小随超声时间的延长而减小,存120S时达到最小,但其稳定性相当差,若再在20000r?
min下匀化10min,所得初乳在4℃下可稳定1个月。
Kim等I在(36±
1)℃下同定第一次超声时间为120s,研究第二次超声时间对复乳稳定性的影响,实验发现第二次超声时间越长,复乳相转变越慢。
2温度每种乳化剂都其最适温度,低于或高于此温度,乳化剂的乳化性能或HLB值也会发生变化,另外,温度还可以影响油脂的黏度及界面膜的稳定性。
温度过高使非离子表面活性剂亲水基的水化程度减少,疏水基周围的结构破坏,影响了界面膜稳定性,使乳状液稳定性降低;
温度过低,油粘度大,所以较低温度下乳化剂和水难以很好分散,也不利于细小液滴的形成。
马宁等探讨了杏仁油乳佐剂的制备工艺,分别研究了25℃,40-60℃,80℃对乳剂制作的影响,发现40-60℃制作的佐剂的稳定性明显优于25℃或80℃时制作的乳剂。
杨晓东等也考察了温度对司班-80和脂肪醇聚氧乙烯醚复配乳化剂乳化性能的影响,分别设了60℃、70℃、80℃、90℃四个不同温度,结果表明乳化温度为80℃时乳化效果最好。
3加料方式在实际操作时还发现,同样的组成和配比,因为操作顺序的不同,乳液粒子大小或分布也会有差异。
鹭谷氏在制造O/W乳液时发现:
水分3次加入,那么乳液的粒子细而均匀;
而已一定速度连续加入的话,就会出现大小不一,即使再使用均质器也达不到分次加入时的水平。
4油相和水相的比例油相所占比例在一定程度上决定复乳的稳定性。
I.augel等以异己烷为油相,以3.1%氯化钠溶液为内水相,1.3%氯化钠溶液为外水相,研究发现,当控制油量占复乳总量的19%~22%时,复乳的稳定性随油相比例的增加而提高。
5乳剂生产工艺示例5.1示例一本部分将以一个配方为例,简单的介绍一下相同的配方,不同的工艺制作不同类型(w/o、o/w或w/o/w)的乳剂。
乳剂中包含0.2%(w/v)的吐温-80,0.5%(w/v)ArlacelP135,其中吐温-80添加在水相,ArlacelP135于60℃时添加于油相,水相和油相的比例60:
40(w/w)。
5.1.1W/O型乳剂的制备此乳剂是将水相缓缓加入油相,然后利用UltraTurraxTypeT25(IKA,Germany).乳化设备在20,000rpm高剪切力下制作而成。
5.1.2O/W型乳剂的制作此型乳剂的制作需要用到高压均质机。
具体操作如下:
部分油相加入pH7.20.01M的磷酸盐缓冲液中,高压均质机800-850bar时高压均质混匀,加入剩余的水相,继续混匀。
最后加入剩余的油相,UltraTurraxTypeT2511,000rpm混匀。
5.1.3W/O/W型乳剂的制作其中内水相:
油相:
外水相=30:
40:
30,佐剂的制作分两步。
第一步:
按w/o型乳剂的制作方法制作w/o初乳;
第二步:
使用Eurostarmixer(螺旋桨叶片)(IKA,Germany)1000rpm乳化即可。
5.2实例二:
双相乳剂A5的制作双相佐剂的制备有一步法和两步法,这里双相佐剂A5的制作采取的是一步乳化法,在二步乳化法的基础上简化了工艺。
具体如下:
5.2.1双相A5佐剂的制备在室温条件下,先将兽用注射级白油在乳化罐中进行乳化,得轻质液体石蜡油;
在轻质液体石蜡油中加入亲油基司班-80,以75-85rpm速度搅拌3-7min至澄清汽泡消失透明,然后在搅拌状态下加入亲水基吐温-80搅拌3-7min,进行搅拌混合均匀,再加入稳定剂至澄清汽泡消失透明后,静置25-35min即可。
5.2.2疫苗乳剂的配置两种佐剂在配制前均经121℃60min高压灭菌。
双向疫苗配置比例为油相(佐剂):
水相(抗原)=50:
50(经多次实验验证,此比例乳化效果最佳)。
双相佐剂疫苗乳化,先将佐剂加入乳化机料桶内,室温状态下边搅拌(100r/min)边缓缓(速度不宜快,否则形成乳剂粒径大小不均一,乳剂剂型不整)将抗原水相滴入佐剂中,滴完后,继续搅拌5min,混匀形成初乳。
接着用乳化机5600r/min,循环乳化4min(乳化速度不宜过大,时间不宜过长,否则双相佐剂易破乳)。
仅供个人用于学习、研究;
不得用于商业用途。
notforcommercialuse.
Nurfü
rdenpersö
nlichenfü
rStudien,Forschung,zukommerziellenZweckenverwendetwerden.
Pourl'
é
tudeetlarechercheuniquementà
desfinspersonnelles;
pasà
desfinscommerciales.
толькодлялюдей,которыеиспользуютсядляобучения,исследованийинедолжныиспользоватьсявкоммерческихцелях.
以下无正文