钢结构监理实施细则Word格式.docx
《钢结构监理实施细则Word格式.docx》由会员分享,可在线阅读,更多相关《钢结构监理实施细则Word格式.docx(15页珍藏版)》请在冰豆网上搜索。
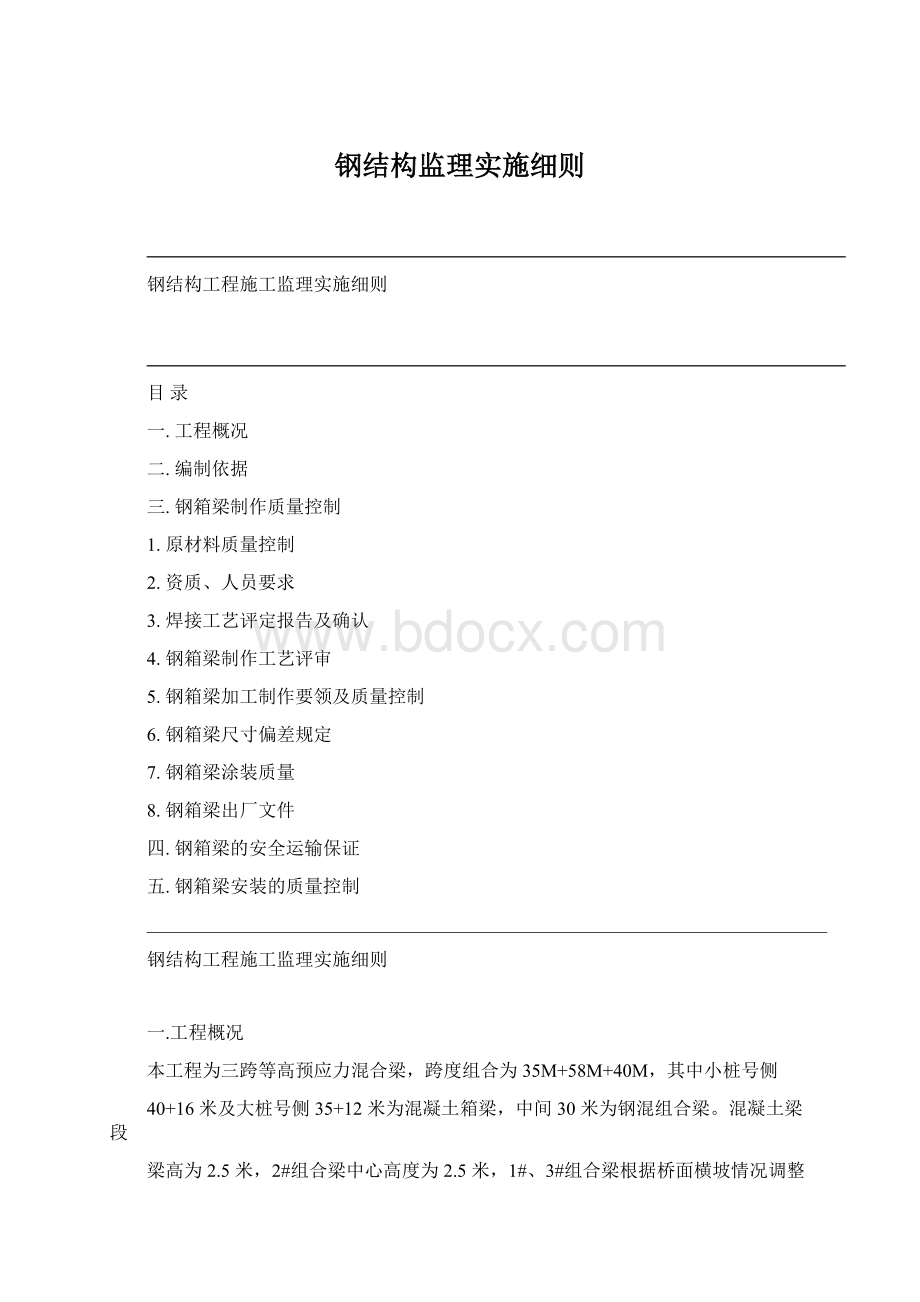
位
于
道
缓
和
曲
为
34.111
钢箱梁上翼缘板宽
0.6
米,厚
厘米,腹板均宽
2.039
1.6
厘
米,底板宽度
3.060
2.0
厘米,所用钢材均采用
Q345qc
级钢。
二.编制依据
设计图纸、设计交底及相关说明;
招、投标文件及施工合同、监理委托合同;
《中华人民共和国建筑法》;
《工程建设标准强制性条文》;
《钢结构设计规范》
GB50017-2003;
《铁路钢桥制造规范》TB10212-98;
《桥梁用结构钢》GB/T714-2000;
《电弧螺栓焊用圆柱头焊钉》GB10433-2002;
9.
《公路桥涵施工技术规范》JTJ041-2000;
10.《钢结构工程施工及验收规范》GB50205-2001;
11.《建筑钢结构焊接技术规程》JGJ81-2002;
12.《对接焊缝超声波探伤》TBI558;
13.《钢熔化焊接接头射线照像和质量分级》GB3323;
14.《钢焊缝手工超声波探伤方法和探伤结果分级》GB11345-89
15.《碳素钢焊条》GB/T5117;
序号
检验项目
取样数量
取样方法及部位
试验方法
1
化学成分
1
个
(
每
炉
罐)
GB/T222
GB/T223
2
拉伸
GB/T2975
GB/T228
3
冲击
GB/T229
4
冷弯
GB/T232
5
表面
逐张
-
目视
6
尺寸
卡尺、直尺
16.《低合金钢焊条》GB/T5118;
17.《熔化焊用钢丝》GB/T14957;
18.《铁路钢桥保护涂装》TB/T1527-95;
19.《涂装前钢材表面锈蚀等级和除锈等级》GB/T8923-1988;
三.钢箱梁制作质量控制
板材
1.1.1
本工程所用钢材均采用
级钢,其材质应符合《桥梁用结构钢》
GB/T714-2000
及设计文件要求。
1.1.2
钢材外观不应有裂纹、气泡、结疤、夹杂、折叠、分层、翘曲、锈蚀、
油污等影响号料或切割质量,若有应清理、矫正后再号料。
矫正宜采用冷矫,
矫正后表面不应有明显的凹痕或损伤,当采用热矫时,加热温度应控制在
600-
800℃,温度降至室温前不得锤击钢材。
1.1.3
钢
材
应
按
同
一
厂
家
、
质
厚
出
状
态
10
(批)号抽验一组试件。
钢材要有明显的标识、产品合格证、材料质量证明
书。
1.1.4
每批钢材的检验项目、取样数量、取样部位及试验方法应符合表-1
的规
定。
表-1
1.1.5
第一批钢材进厂时必须及时报验,经建设单位、监理抽样送检,复试合
格后方可进入放放样、号料等制作程序。
1.2
剪力钉(焊钉)
1.2.1
本工程剪力钉采用
ML15
钢,其材质应符合《电弧螺栓焊用圆柱头焊钉》
GB10433-2002
要求,与剪力钉焊接瓷环应符合
JB4146
的要求。
1.2.2
剪立钉表面应无锈蚀、氧化皮、油脂和毛刺等质量缺陷。
其杆部表面不
允许有影响使用的裂缝,但头部裂缝的深度(径向)不得超过
0.25(dk-d)
MM。
1.2.3
剪立钉应在焊钉头部顶面用凸字制出制造者的识别标志,同时要有产品
合格证和质量证明书。
1.2.4
剪
立
钉
焊
接
性
能
复
试
检
验
项
拉
力
弯
方
法
按
GB/T228
的规定。
1.2.5
剪立钉进厂时要及时报验,经建设单位、监理抽样送检,复试合格后方
可使用于工程中。
1.3
焊接材料
1.3.1
焊接材料牌号、规格的选用应符合设计文件的要求,具有钢厂和焊接材
料厂出具的产品使用说明书、质量证明文件或检验报告;
其化学成分、力学性
能和其它质量要求必须符合国家现行标准规定。
1.3.2
重要钢结构采用的焊接材料应进行抽样复试,复试结果应符合国家产品
标准和设计要求。
焊条应符合《碳素钢焊条》GB/T5117
和《低合金钢焊条》
GB/T5118
的规定;
焊丝应符合《熔化焊用钢丝》GB/T14957
和《气体保护电弧
焊用碳钢、低合金钢焊丝》GB/T8110
埋弧焊用焊丝和焊剂应符合《埋
弧焊用碳钢焊丝和焊剂》GB/T5293
和《低合金钢埋弧焊用焊剂》GB/T12470
的
规定。
1.3.3
焊接材料应通过焊接工艺评定确定;
焊剂、焊条必须按产品说明书烘干
使用;
焊剂中的脏物,焊丝上的油锈等必须清除干净;
CO2
气体纯度应大于
99.5%。
1.4
涂装材料
1.4.1
钢结构防腐涂料、防火涂料、稀释剂、固化剂等材料的品种、规格、性
能、颜色等应与其质量证明文件相符,并经具有资质的检测机构检测符合国家
产品厚度
试板厚度
8-16
12-16
17-32
24-32
现行有关标准的规定。
1.4.2
涂装材料开启后,不应存在结皮、结块、凝胶等现象。
按桶数抽查
5%,
且不应少于
桶。
2.1
钢结构生产厂家和检测机构必须具有国家核准的生产资质和检测资质,并
只能在许可的资质范围内从事生产和检测业务。
2.2
焊工的操作技术水平和熟练程度对钢结构焊接质量影响很大,为此规定焊
工应经考试合格并取得合格证书后方可上岗担任相应合格项目的施焊。
无损检
测人员也必须通过考试取得相应的资格证书,且只能从事资格证书认定范围内
的检测工作。
3.焊接工艺评定报告及确认
3.1
评定条件应与产品条件相对应。
3.1.1
评定试板必须使用母材;
。
3.1.2
焊接材料的牌号、规格、化学成分、力学性能应明确,一经评定通过,
在后续的制作过程严禁擅自替换。
3.2
试板的选用
3.2.1
试板宜选用碳、磷、硫等化学成分偏标准上限且冲击韧性偏标准下限的
母材制备,对接接头试板可按产品的每一板厚范围在表-2
中选择。
表-2(单位
MM)
3.2.2
试板长度应根据样坯尺寸、数量(含附加试样数量)等因素予以综合考
虑,自动焊不得小于
600MM,手工焊、CO2
气体保护焊不得小于
400MM。
试件的
宽度为焊缝每侧不得小于
150MM。
3.2.3
绘制试板图。
试件的焊接条件及施焊工艺参数
3.3.1
试件的焊接条件及施焊工艺参数一经确认,将成为后续制作施焊时应严
项目名称
评审内容
评审级别
备
注
厂内
业主、总
包
焊接工艺评定
评定过程和评定结果
√
施工组织设计
施工组织设计计划安排
钢结构制作方案
申请开工
零件下料
切割质量和切割工艺
首件构件制作
制作质量和制作工艺
格执行的焊接工艺标准,焊接条件、施焊工艺参数的评定记录必须真实有效,
监理工程师可采取旁站和平行检验的方法加以控制。
3.4
焊缝检验
3.4.1
所有焊缝的外观质量必须在全长范围内进行外观检查,应符合
TB10202-
98
的标准。
3.4.2
对接焊缝应沿全长进行超声波探伤,质量等级为
I
级;
并在
200-300MM
的长度范围内进行射线探伤。
双面贴角焊缝应沿全长进行超声波探伤,质量等
级为
II
级焊缝。
3.5
机械性能试验及宏观断面酸蚀试验
3.5.1
机械性能的试验项目、试样数量及试验方法应符合
TB10202-98
表
C.3.5
3.5.2
每一评定应作一次宏观断面酸蚀试验,试验方法应符合《钢的低倍组织
及缺陷酸蚀试验方法》GB226
3.6
结论
试板加工焊接完成并经具有资质的检测机构检验合格后,再以书面形式形成
焊接工艺评定报告。
焊接工艺评定报告、评定记录、评定试样检验结果一起报
工程质量监督验收部门和有关单位审查备案。
4.钢箱梁制作工艺评审
钢箱梁制造过程中分阶段对其制造工艺进行评审并及时总结,根据评审结论
完善制作工艺,指导后续生产。
根据钢结构制造程序,拟定表-3
评审项目。
表-3
(钢箱梁制造评审项目一览表)
在评审项目中,首件单元件评审通过后,才能进行单元件大批量生产。
通
过钢结构制造评审,工厂将对钢梁制造各阶段制造工艺进行完善处理并及时总
目
允许偏差
基准线,孔距位置
≤0.5mm
零件外形尺寸
结,并向业主和监理提交书面总结报告。
5.钢箱梁加工制作要领及质量控制
5.1
放样及质量控制
5.1.1
放样前,放样人员必须熟悉施工图和工艺要求,核对构件及构件相互连
接的几何尺寸和连接有否不当。
如发现施工图有遗漏或错误,以及其它原因需
要更改施工图时,必须取得原设计单位签具的设计变更文件,不得擅自修改。
5.1.2
为保证所有尺寸的精确性,放样应以计算机辅助进行放样
5.1.3
放样工作完成后,对所放大样和样杆样板(或下料图)进行自检,无误
后报专职检验人员检验。
5.2
划线(号料)及质量控制
5.2.1
号料前应先确认材质和熟悉工艺要求,然后根据排版图、下料加工单、
配料卡和零件草图进行号料。
5.2.2
号料的母材必须平直无损伤及其它缺陷,否则应先矫正或剔除。
5.2.3
划线公差要求符合表-4
的要求:
表-4
5.2.4
划线后应标明基准线、中心线和检验控制点。
作记号时不得使用凿子一
类的工具,少量的样冲标记其深度应不大于
0.5mm,钢板上不应留下任何永久
性的划线痕迹。
5.2.5
划线号料后应做好材质标记的移植工作。
5.2.6
划线(号料)的质量控制:
5.2.6.1
号料前,号料人员应熟悉下料图所注的各种符号及标记等要求,核对
允
许
偏
差
零件的长度
长度±
1.0mm
零件的宽度
板制
H
钢的翼、腹板:
宽度±
另件板:
切割面不垂直度
e
t≤20mm,e≤1mm;
t≥20,e≤t/20
且≤2mm
割纹深度
0.2mm
局部缺口深度
对≤2mm
打磨且圆滑过度。
对≥2mm
电焊补后打磨形成圆滑过渡
材料牌号及规格、炉批号。
5.2.6.2
号料时,针对本工程的使用材料特点,复核所使用材料的规格,检查
材料外观质量,制订测量表格加以记录。
5.2.6.3
根据锯、割等不同切割要求和对刨、铣加工的零件,预放不同的切割
及加工余量和焊接收缩量。
5.2.6.4
因材料长度或宽度不足需焊接拼接时,必须在拼接件上注出相互拼接
编号和焊接坡口形状。
如拼接件有眼孔,应待拼接件焊接、矫正后制孔。
5.2.6.5
下料完成,检查所下零件的规格、数量等是否有误,并做记录。
5.3
切割及质量控制:
5.3.1
切割前应清除母材表面的油污、铁锈和潮气;
切割后气割表面应光滑无
裂纹,熔渣和飞测物应除去。
剪切边应打磨。
5.3.2
气割的检验公差符合表-5
要求:
表-5
5.3.3
切割后应去除切割熔渣。
图纸上的直角切口应以
15mm
的圆弧过度(如小
梁端翼腹板切口)。
钢的对接若采用焊接,在翼腹板的交汇处应开合适的圆弧,
保证焊缝质量。
5.3.4
火焰切割后须自检零件尺寸,然后标上零件所属的构件号、零件号,再
由质检员专检各项指标,合格后才能进入下一道工序。
坡口角度△a
△a=±
2.5°
a=±
5°
坡口钝边△a
1.0
5.3.5
切割的质量控制:
5.3.5.1
根据钢结构工程结构要求,构件的切割应宜采用数控、等离子、自动
或半自动气割,以保证切割精度。
5.3.5.2
钢材的切断,应按其形状选择最适合的方法进行。
5.3.5.3
切割前必须检查核对材料规格、牌号是否符合图纸要求。
5.3.5.4
切口截面不得有撕裂、裂纹、棱边、夹渣、分层等缺陷和大于
1mm
缺棱并应去除毛刺。
5.3.4.5
切割前,应将钢板表面的油污、铁锈等清除干净.
5.3.4.6
切割时,必须看清断线符号,确定切割程序。
5.4
坡口加工
5.4.1
加工工具的选用
选用半自动割刀或铣边机(厚板坡口尽量采用机械加工)
5.4.2
坡口加工的检验精度符合表-6
表-6
5.5
矫正、打磨
5.5.1
钢材的机械矫正,一般应在常温下用机械设备进行,如钢板的不平度可
采用七辊矫平机。
5.5.2
热矫正时应注意不能损伤母材,加热的温度不得超过规定的温度。
5.5.3
构件的所有自由边角应有约
2mm
的倒角,以免涂层开裂。
5.6
部件组装
5.6.1
组装前先检查组装用零件的编号、材质、尺寸、数量和加工精度等是否
符合图纸和工艺要求,确认后才能进行装配。
5.6.2
组装用的平台和胎架应符合构件装配的精度要求,并具有足够的强度和
刚度,经验收后才能使用。
5.6.3
构件组装要按照工艺流程进行,焊缝处
30mm
范围以内的铁锈、油污等应
清理干净。
5.6.4
对于在组装后无法进行涂装的隐蔽部位,应事先涂装。
5.6.5
计量用的钢卷尺应经二级以上计量部门检定合格才能使用,且在使用时,
当拉至
5m
时应使用拉力器拉至
5kg
拉力,当拉至
10m
以上时,应拉至
10kg
拉
力。
并尽量与总包单位现场使用的钢卷尺核对一致。
5.6.6
组装过程中,定位用的焊接材料应注意与母材的匹配,应严格按照焊接
工艺要求进行选用。
5.6.7
构件组装完毕后应进行自检和互检,填制测量表,准确无误后再提交专
检人员验收,若在检验中发现问题,应及时向上反映,待处理方法确定后进行
修理和矫正。
5.6.8
各部件装焊结束后,应明确标出中心线、水平线、分段对合线等,打上
洋冲并用色笔圈出。
5.6.9
构件组装精度符合表-7
项次
简
图
允许偏差(mm)
T
形接头的间隙
e≤1.5
搭接接头的间隙
长度△L
L:
±
5.0
对接接头的错位
e≤T/10
且
≤3.0
对接接头的间隙
(无衬垫板时)
-1.0
≤e≤1.0
根部开口间隙△a
(背部加衬垫板)
埋弧焊、
-2.0≤△a≤3.0
手工焊、半自动气保焊
-2.0≤△a
名称
检查方法
允许偏差(MM)
梁高
h≤2M
测量腹板处高度
表-8
表-7
6.钢箱梁尺寸偏差规定
6.1
钢箱梁尺寸偏差应符合
TB10212-98J
及
JTJ041-2000
的相关规定。
6.2
钢箱梁尺寸允许偏差应符合表-8
h>2M
跨度
L
测两支座中心距离,L
以
M
计
(5+0.15L)
全长
—
15
腹板中心距离
测两腹板中心距
盖板宽度
b
横断面对角线差
测两横断面对角线差
旁弯
L
3+0.1L
拱度
+10,-5
支点高度差
腹板平面度
h
盖
板
与
加
劲
肋
或
劲
肋与加劲肋之间的距离
<h/250
且≤8
扭曲
每段以两端隔板处为准
每米≤1
且每段≤10
7.钢箱梁涂装质量
7.1
钢箱梁表面除锈后的钢表面洁净度等级应达到《涂装前钢材表面锈蚀等级
和除锈等级》GB/T8923-1988
标准规定的
Sa2.5
级,外观相当于该标准规定的
A
Sa2.5、B
Sa2.5、C
Sa2.5。
7.2
整体涂装施工前,通过试验确认表面处理及表面喷涂的工艺参数和涂装过
程合理性,试件的制备采用与涂装现场施工相同的程序,严格按照《涂装工艺
规程》各道工序的相关要求,由涂装施工人员进行涂装,做好试验记录,提交
检测部检测。
试件现场附着力检测:
底漆附着力检测制作相应试板,送相关检
测部门或进行现场拉拔;
层间附着力检测制作试板,进行现场划格试验;
做好
试验记录,由工艺部门根据以上试验及检测资料做出评定结果。
7.3
喷漆作业采用高压无气喷涂法,局部结合刷涂法,刷涂只在预涂和修补时
质量要求
检验仪器和方法
参照标准
干膜厚度
按各道涂层设计要求
磁性测厚仪测厚
GB4956
附着力
≤1
级
涂层划格仪划格法测试
(1mm、2mm、3mm)
GB9286
外观
漆膜连续、平整、颜色与色卡一致,漆膜不
得有流挂、针孔、气泡、裂纹等表面缺陷。
目测
/
采用。
喷漆房内环境温度一般为
5~38℃(不同涂料要求不同,以涂料说明书
为准),底材表面温度高于空气露点
3℃以上,空气相对湿度控制在
80%以下。
喷漆前,预涂所有焊缝。
所有预涂均采用刷涂。
7.4
工地焊缝
50~100mm
范围内暂不涂装底漆(拼装完成后现场涂装),以后每
层涂料涂装前,焊缝边缘再留出
50mm,形成阶梯状保护层。
7.5
涂层外观、厚度、附着力的检验
8.钢箱梁出厂文件
8.1
产品合格证。
8.2
钢材和其他材料质量证明书或检验报告。
8.3
施工图、拼装简图和设计变更文件,设计变更内容应在施工图中相应部位
注明。
8.4
产品试板的试验报告。
8.5
焊缝重大修补记录。
8.6
工厂试拼装记录。
8.7
构件发运表和包装清单。
四.钢箱梁的安全运输保证
1.钢箱梁确需分段分段加工、运输时,必须通过设计部门的确认,分段位置的
设置,现场焊接的方案必须有设计部门的认定。
2.钢箱梁制作段吊装运输过程中,应正确使用专用吊具,严防钢梁发扭转、翘
曲和侧倾,轻吊轻放,支垫平稳,正确就位。
装运时构件与车辆之间应妥善捆扎,以防车辆颠簸而发生构件散落。
运输过
程中应注意保护构件,使用软性材料对构件之间及构件与包装运输车辆之间进
行隔离和衬垫,特别是一些较薄的连接板,应尽量避免与其它构件直接接触。
装车与堆放应考虑构件的堆放位置,以免构件受压变形。
大型构件间应设置捆
扎点和吊点,确保构件吊运时不受损伤。
构件装车应布置合理,易于卸车搬
运,构件做好防雨措施,构件的连接摩擦面应有保护。
4
装车必须整齐、有序、标识明确、记录完整。
整个运输过程责任到人,运输
管理人员应对运输过程进行全方位的监督,确保运输计划科学合理。
五.钢箱梁安装的质量控制
施工顺序:
必须先施工
第
联桥梁(上层),后施工
NH
联桥梁(下
层)。
2
钢箱梁的现场安装必须严格执行经施工单位技术安全部门及监理工程师批准
的《钢箱梁吊装方案》。