微电子专业毕业论文资料Word文件下载.docx
《微电子专业毕业论文资料Word文件下载.docx》由会员分享,可在线阅读,更多相关《微电子专业毕业论文资料Word文件下载.docx(16页珍藏版)》请在冰豆网上搜索。
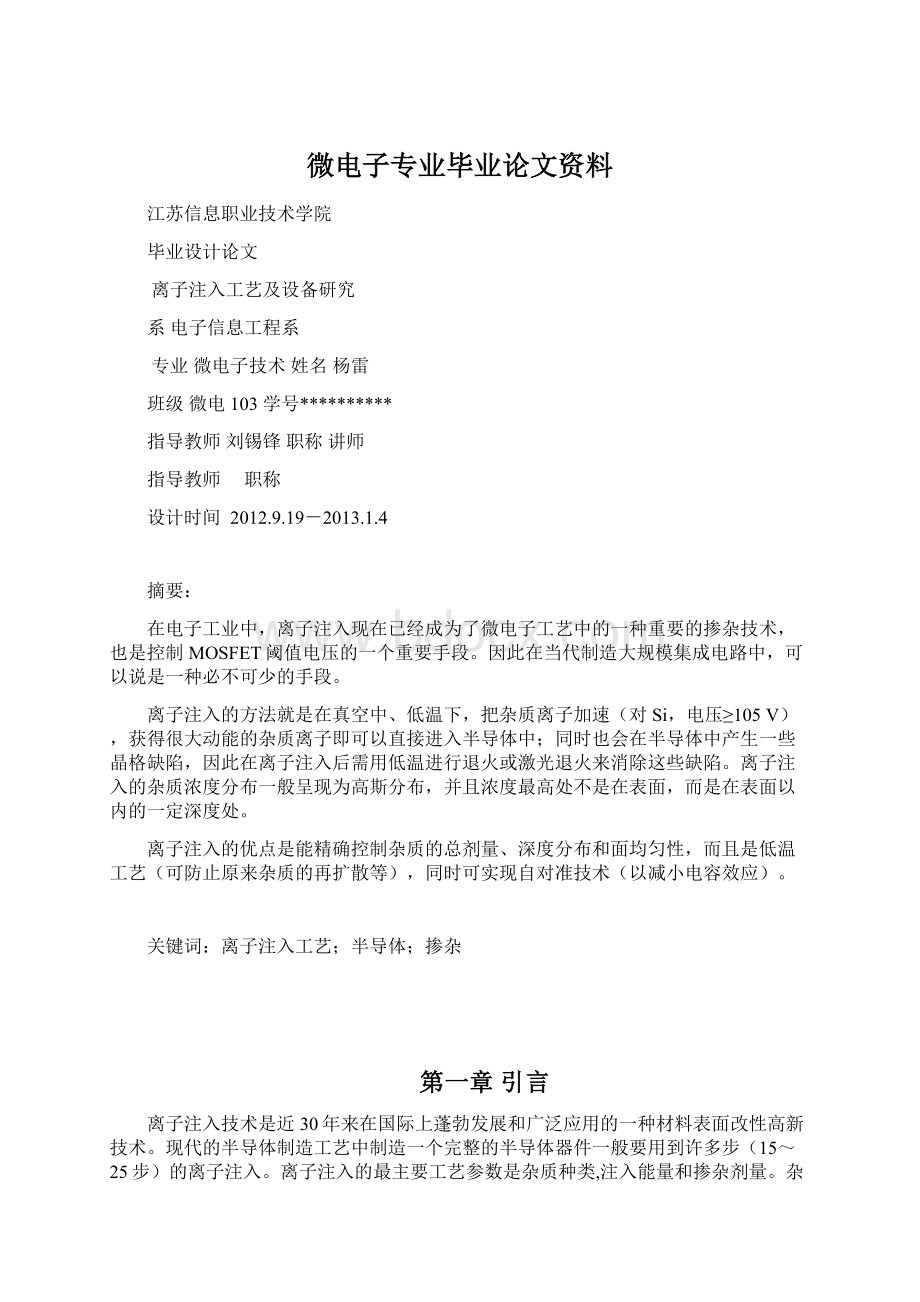
离子注入工艺;
半导体;
掺杂
第一章引言
离子注入技术是近30年来在国际上蓬勃发展和广泛应用的一种材料表面改性高新技术。
现代的半导体制造工艺中制造一个完整的半导体器件一般要用到许多步(15~25步)的离子注入。
离子注入的最主要工艺参数是杂质种类,注入能量和掺杂剂量。
杂质种类是指选择何种原子注入硅基体,一般杂质种类可以分为N型和P型两类,N型主要包括磷,砷,锑等,而P型则主要包括硼,铟等。
注入能量决定了杂质原子注入硅晶体的深度,高能量注入得深,而低能量注入得浅。
掺杂剂量是指杂质原子注入的浓度,其决定了掺杂层导电的强弱。
通常半导体器件的设计者需要根据具体的目标器件特性为每一步离子注入优化以上这些工艺参数。
离子注入工艺离子注入是现代集成电路制造中的一种非常重要的技术,其利用离子注入机实现半导体的掺杂,即将特定的杂质原子(Dopant)以离子加速的方式注入硅半导体晶体内改变其导电特性并最终形成晶体管结构。
随着半导体集成电路的高速发展,对工艺提出了更高的要求,特别是对关键工艺的影响更大。
本文对半导体集成电路工艺中的离子注入工艺的主要特点、工艺中存在的几个问题及工艺质量检测等方面进行了重点阐述。
第二章离子注入工艺
2.1离子注入的原理
离子注入是将离子源产生的离子经加速后高速射向材料表面,当离子进入表面,将与固体中的原子碰撞,将其挤进内部,并在其射程前后和侧面激发出一个尾迹。
这些撞离原子再与其它原子碰撞,后者再继续下去,大约在10-11s内,材料中将建立一个有数百个间隙原子和空位的区域。
这所谓碰撞级联虽然不能完全理解为一个热过程,但经常看成是一个热能很集中的峰。
一个带有100keV能量的离子通常在其能量耗尽并停留之前,可进入到数百到数千原子层。
当材料回复到平衡,大多数原子回到正常的点阵位置,而留下一些“冻结”的空位和间隙原子。
这一过程在表面下建立了富集注入元素并具有损伤的表层。
离子和损伤的分布大体为高斯分布。
整个阻止过程的时间仅用10-11s,位移原子的停留也是在相近时间内完成的,所以全过程很像发生在长约0.1μm和直径为0.02μm的圆柱材料总的快速加热与淬火。
离子注入处理的这种快速加热-淬火与新原子注入材料中相结合,其结果可产生一些独特的性能。
离子注入的深度是离子能量和质量以及基体原子质量的函数。
能量愈高,注入愈深。
一般情况下,离子越轻活基体原子越轻,注入越深。
一旦到达表面,离子本身就被中和,并成为材料的整体部分,所以注入层不会像常规那样有可能脱落或剥离。
注入的离子能够与固体原子,或者彼此之间,甚至与真空室内的残余气体化合生成常规合金或化合物。
由于注入时高能离子束提供反应后的驱动力,故有可能在注入材料中形成常规热力学方式不能获得的亚稳态或“非平衡态”化合物这就可能使一种元素的添加量远远超过正常热溶解的数量。
用能量为100keV量级的离子束入射到材料中去,离子束与材料中的原子或分子将发生一系列物理的和化学的相互作用,入射离子逐渐损失能量,最后停留在材料中,并引起材料表面成分、结构和性能发生变化,从而优化材料表面性能,或获得某些新的优异性能。
离子注入技术是把某种元素的原子电离成离子,并使其在几十至几百千伏的电压下进行加速,在获得较高速度后射入放在真空靶室中的工件材料表面的一种离子束技术。
材料经离子注入后,其表面的物理、化学及机械性能会发生显著的变化(参考文献[1])。
图2-2离子注入系统
2.2离子注入的分类
离子注入设备根据具体的应用分为三类:
中束流,大束流和高能量。
这三种离子注入设备在半导体工艺中各有其特殊的应用。
中束流(MC)离子注入设备用于那些掺杂剂量适中或较低但精度控制要求非常重要的掺杂工艺,其在半导体器件制造中的具体应用例如栅阀值调整(ThresholdAdjust),Halo注入等;
大束流(HC)离子注入设备用于掺杂剂量很高且精度控制不重要的场合,例如源极,漏极的形成和多晶硅栅极的掺杂。
高能量(HE)离子注入设备用于杂质原子注入硅基体深度需要很深的场合。
随着晶体管的缩小,高能量注入逐步减少,其中N/P井的形成,尤其是倒掺杂井(retrogradewell),主要需要HE注入设备。
2.3离子射程
离子射程就是注入时,离子进入wafer内部后,从表面到停止所经过的路程。
入射离子能量越高,射程就会越长。
投影射程是离子注入wafer内部的深度,它取决于离子的质量、能量,wafer的质量以及离子入射方向与晶向之间的关系。
有的离子射程远,有的射程近,而有的离子还会发生横向移动,综合所有的离子运动,就产生了投影偏差。
图2-3离子射程
2.4离子注入剂量
注入剂量是单位面积wafer表面注入的离子数,可通过
下面的公式计算得出,式中,Q是剂量;
I是束流,
单位是安培;
t是注入时间,单位是秒;
e是电子电荷,1.6×
10-19C;
n是电荷数量;
A是注入面积。
2.5离子注入的要求
离子注入的工艺要求主要包括均匀性和可重复性,能量纯度,注入角度准确性,杂质微粒(particle),污染等等。
高度敏感的器件要求离子注入的剂量尽可能的均匀一致。
典型的均匀性指标上限可以是3倍标准方差波动1.5%。
这样的要求必须在300mm直径的晶圆上始终如一地得到满足。
晶圆之间(wafer-to-wafer)和批次之间(lot-to-lot)的可重复性也同等地重要。
离子入射角度不同将造成离子注入深度改变而影响器件的电参数,因此对于离子束入射角度的控制非常必要。
污染包括能量污染,金属污染,以及交叉污染。
先前注入杂质的原子可能被溅射到晶圆表面形成交叉污染(cross-contamination),或是注入的虽然是正确的杂质但是却是错误的能量或电荷状态形成能量污染(energycontamination),或者通常来自于电子束流通路组件的溅射而形成的金属污染(metalliccontamination)。
杂质微粒(Particle)既可能通过离子束的运动带至晶圆表面,也可能在晶圆传送的过程中产生。
即使是象120nm那么小的微粒也足以导致器件产出的损失。
现代半导体器件对这些问题是如此敏感以至于工艺工程师需要不停地监控这些工艺参数确保它们在设定范围之内。
随着半导体工业的进步,半导体器件的尺寸不断缩小,要求源极、漏极以及源极前延和漏极前延(Source/DrainExtension)相应地变浅,这大大地增加了对低能量离子注入的需求,见图2-4。
由于低能量的离子本身就难以萃取;
加上低能量离子束行进速度慢,其由于空间电荷自排斥而产生的离子束扩散使得更多的萃取离子损失在路径中,如何增加能量在10keV以下的离子束电流以增加生产力成为离子注入设备的最大挑战之一(参考文献[2])。
图2-4P型源、漏极前延(PLDD)离子注入参数随器件缩小的变化趋势(2001ITRS)
第三章离子注入的特点
3.1离子注入的特点
注入的离子经过质量分析器的分析,纯度很高、能量单一。
而且注入环境清洁、干燥,大大降低了杂质污染。
注入剂量可精确控制,杂质均匀度高达±
1%;
注入在中低温度下进行,二氧化硅、光刻胶、氮化硅等都可以作为注入时的掩蔽层。
衬底温度低,就避免了高温扩散所引起的热缺陷;
离子注入是一个非平衡过程,不受杂质在衬底中的固溶度限制;
对于化合物半导体采用离子注入技术,可不该变组分而达到掺杂的目的;
离子注入的横向掺杂效应比扩散大大减少了;
离子注入最大的缺点就是高能离子轰击wafer对晶格结构造成的损伤;
3.2离子注入与扩散工艺的比较
我们可以通过表3—1直观看出来关于离子注入和传统扩散工艺的相比较的优缺点:
表3—1离子注入和扩散工艺的比较
比较项目
离子注入法
扩散法
温度
低温工艺,小于125°
下也可进行
高温(800℃~1200℃)
掩蔽层
金属、光刻胶、二氧化硅、氮化硅
耐高温材料,一般为二氧化硅
可用掺杂源
各种掺杂源均可
要考虑许多因素,一般采用硼、磷、砷、锑
结特性
能制作浅结,超浅结(125nm范围内),结深易控制,适于突变结
适于制作结深(几微米到几十微米)缓变结
掺杂浓度
杂质纯度高、注入浓度范围广
受杂质固溶度影响
浓度控制
由束流和时间可精确控制
受源温、气体流量、扩散温度、时间等多种因素影响
均匀性
大面积掺杂面内均匀性高(扫描)
杂质污染
小
易受钠离子污染
横向扩散
很小,几乎没有
有横向扩散
晶体损伤
大
掺杂深度
注入杂质含量不受硅片固溶度的限制
受固溶度限制
第四章离子注入设备
离子注入机体积庞大,结构非常复杂。
根据它所能提供的离子束流大小和能量可分为高电流和中电流离子注入机以及高能量、中能量和低能量离子注入机。
离子注入机的主要部件有:
离子源、质量分析器、加速聚焦器、扫描系统以及工艺室等。
图4-1离子注入机
4.1离子源
4.1.1离子源
作用:
产生所需种类的离子并将其引出形成离子束。
分类:
等离子体型离子源、液态金属离子源(LMIS)。
掩模方式需要大面积平行离子束源,故一般采用等离子体型离子源,其典型的有效源尺寸为100m,亮度为10~100A/cm2.sr。
聚焦方式需要高亮度小束斑离子源,当液态金属离子源(LMIS)出现后得以顺利发展。
LMIS的典型有效源尺寸为5~500nm,亮度为106~107A/cm2.sr。
4.2.2离子束吸取电极
吸取电极将离子源产生的离子收集起来形成离子束。
电极由抑制电极和接地电极构成,电极上加了很高的电压,离子受到弧光反应室侧壁的排斥作用和抑制电极的吸引作用,被分离出来形成离子束向吸取电极运动(如图4-1)。
图4-2离子注入
4.2质量磁分析器
4.2.1E×
B质量分析器
由一套静电偏转器和一套磁偏转器组成,E与B的方向相互垂直。
图4-3E×
由
得
,代入
,得:
当时
,即当
时,离子不被偏转。
由此可解得不被偏转的离子的荷质比
为
对于某种荷质比为
的所需离子,可通过调节偏转电压
或偏转磁场
,使之满足下式,就可使这种离子不被偏转而通过光阑:
或
当荷质比为
的离子不被偏转时,具有荷质比为
的其它离子的偏转量
为:
将前面的
的表达式:
代入
讨论
(1)为屏蔽荷质比为
的离子,光阑半径
必须满足:
(2)若D固定,则具有下列荷质比的离子可被屏蔽: