纸板生产工作总结.docx
《纸板生产工作总结.docx》由会员分享,可在线阅读,更多相关《纸板生产工作总结.docx(9页珍藏版)》请在冰豆网上搜索。
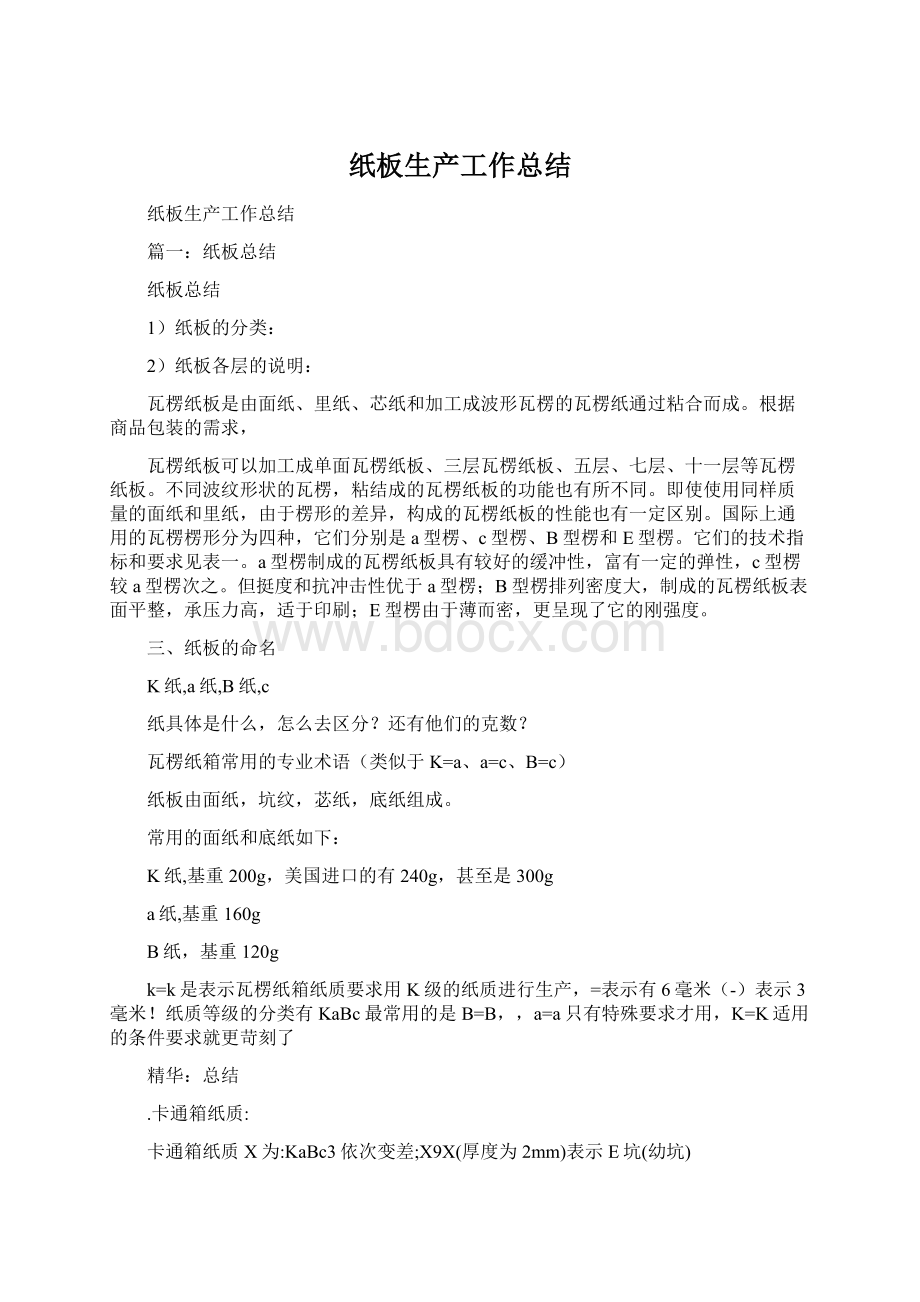
纸板生产工作总结
纸板生产工作总结
篇一:
纸板总结
纸板总结
1)纸板的分类:
2)纸板各层的说明:
瓦楞纸板是由面纸、里纸、芯纸和加工成波形瓦楞的瓦楞纸通过粘合而成。
根据商品包装的需求,
瓦楞纸板可以加工成单面瓦楞纸板、三层瓦楞纸板、五层、七层、十一层等瓦楞纸板。
不同波纹形状的瓦楞,粘结成的瓦楞纸板的功能也有所不同。
即使使用同样质量的面纸和里纸,由于楞形的差异,构成的瓦楞纸板的性能也有一定区别。
国际上通用的瓦楞楞形分为四种,它们分别是a型楞、c型楞、B型楞和E型楞。
它们的技术指标和要求见表一。
a型楞制成的瓦楞纸板具有较好的缓冲性,富有一定的弹性,c型楞较a型楞次之。
但挺度和抗冲击性优于a型楞;B型楞排列密度大,制成的瓦楞纸板表面平整,承压力高,适于印刷;E型楞由于薄而密,更呈现了它的刚强度。
三、纸板的命名
K纸,a纸,B纸,c
纸具体是什么,怎么去区分?
还有他们的克数?
瓦楞纸箱常用的专业术语(类似于K=a、a=c、B=c)
纸板由面纸,坑纹,苾纸,底纸组成。
常用的面纸和底纸如下:
K纸,基重200g,美国进口的有240g,甚至是300g
a纸,基重160g
B纸,基重120g
k=k是表示瓦楞纸箱纸质要求用K级的纸质进行生产,=表示有6毫米(-)表示3毫米!
纸质等级的分类有KaBc最常用的是B=B,,a=a只有特殊要求才用,K=K适用的条件要求就更苛刻了
精华:
总结
.卡通箱纸质:
卡通箱纸质X为:
KaBc3依次变差;X9X(厚度为2mm)表示E坑(幼坑)
X3X(厚度为3mm)---表示单层(单坑)
X=X(厚度为6mm)----表示双层(双坑)
X≡X(厚度为9mm)----表示三层(三坑)
X----表示表面用纸,坑纹----普通之坑纸,中间层平纸----无表示,则为普通纸.w—表示白书纸,
单坑(纸质)双坑(纸质)三坑(纸质)幼坑(纸质)
c33(厚度为3mm)B=3(厚度为6mm)B≡B(厚度为9mm)B9B(厚度为2mm)B33B=cB≡cB9c
B3cB=BB≡3a9a
B3Ba=Ba≡Ba9B
a3Ba=aa≡aw9a
w3Bw=Bw≡Bw9B
b.卡通箱材料之选择:
一般用B=B,纸厚度约为6mm,该种材料最低.如果客人有要求,也可用a=B,这种材质比B=B强度好,价格偏高,而a=a纸质比a=B、B=B好,厚度为6mm,价格也偏高,除非特殊要求才选用.a=B,应该读a孖B(ma)第一声,表示双坑,其它a=a,B=B,也是一样
篇二:
包装车间年终总结报告
20XX年包装车间年终总结报告
时光荏苒,20XX年已经过去,回首一年来的车间作业,内心不禁感慨万千,在公司领导的指导和各部门的协助配合下,通过全体员工的共同努力,克服种种困难在工作中锻炼和提升了我们的生产队伍,取得了可喜的成绩,总结过去、展望未来,为来年的工作做好充分的准备和规划。
20XX年的生产情况汇报如下:
一、人员与产量
20XX年1到12月份车间共生产产量合计:
1953.82万只,月平均产量为412.81万只.相比20XX年的月平均产量474.08万只下降了61.27万只.但是除去受金融危机影响最严重的11月与12月与07年同期(1-10月份)相比,总产能增加了53.6万只.通过对上述07年与08年的产能及人员对比,我们可以看出:
08年的产能变化较07年的产能较平稳有着明显不同,08年产能变化呈现一种“∧”的趋势。
产能上升的也快,回落的也非常的明显。
受此影响,车间在20XX年在人员管理上下了很大的功夫,主要表现在随产能的情况合理的配置相应的人员,因此出现了人员数量的波动性。
二.效率指标分析与总结
20XX年工时利用率平均每月61.04%,比基线59.12%提升1.92%,离目标提升25%.相差13%。
20XX年各月工时利用率(见下表),
从20XX年3月份公司确定效率提升的目标之后,车间与生产管控部就工时利用率的核算与统计方法进行了沟通。
本着公平公正的原则对一些不(:
纸板生产工作总结)合理的现象进行了改正,以利更好的体现车间每个班组的绩效。
比如某些班组因为做了大量的加工单,但未计入理论工时,导致其工时利用率相当的低。
而无法合理评估其绩效。
故在核算工时利用率的时候要求将加工单计入理论工时;将点焊作为独立工站管理,提升了点焊员工的利用率。
以往某个班组点焊完成后,点焊员工会到后面工序担任打杂或帮手。
现在只要有电池,他们就全力点焊;实施工时利用率考核,将目标分解到班组。
此措施在很大程度上改变了领班只注意产量和品质的工作方式。
开始将关注点转移到效率上来。
领班采取了多种的方式来提高工时利用率,主要表现在以下几个方面:
a、严格考勤管理,消除考勤泡沫。
B、实施定额管理,任务细分到个人。
某些领班会要求员工在规定的时间内必须完成定额,否则加班不计工时。
c、变被动接受新员工,新员工上线后少闻寡问为主动筛选员工,主动培训和鼓励新员工。
以上措施的采用,在一定程度上使工时利用率在短期得到了提升。
随着改善的进一步深入,我们取得成绩将越来越困难,并出现反复和倒退,产生了“高原效应”。
为了持续提高工作效率,08年9月份制造二部成立了iE组,负责制造二部产品生产标准工时的制定和维护、车间生产效率的统计核算、车间iE改善的推行等工作,iE组暂由iE工程师和iE技术员组成。
iE组在08年按计划开展了以下几点工作:
1.数据统计及分析
要想进行改善,首先必须知道现状。
以前虽然也在统计核算车间的工时利用率,但基础数据——标准工时和统计方法都不完善和准确,也不统一。
iE组决定工作的入手点从制定一套详细准确的包装生产产品标准工时数据和建立一个统一权威的效率统计核算平台系统开始。
产品生产标准工时的测定以K3系统里的产品代码为单位,做到每个代码都有一套对应的标准工时数据,到目前为止iE组共测定了426个产品型号的标准工时数据,后续不断进行补充,直到建立起一套完整的包装产品生产标准工时数据;
以前生产管控部核算制造二部总的工时利用率,制造二部又要统计车间各生产线的工时利用率,生产管控部使用的是iE组提供的标准工时数据,但由于两者没有联网,数据不能及时同步更新,所以经常导致两个部门核算出来的数据差异很大。
针对此情况iE组用access程序建立了一个通用的工时利用率核算系统,测定的产品标准工时数据全部保存在系统中由iE组维护、由生产管控部输入每日车间的生产订单和出勤工时、生产线上报生产责任外损失工时并经生产管控部确认后录入系统,系统根据基础数据自动生产车间、生产线的时间段内的工时利用率数据。
目前该系统已正常使用并完善增加了员工个人效率核算、车间人员配置、离职人员查询、工时利用率走势图、订单排产查询、产能及负荷评估等功能模块,该系统实现了权威、准确、通用的包装效率核算系统。
2.标准作业表
测定出产品的标准工时后,iE组开始制定产品的生产标准作业表对生产线生产该产品时人员、机器模具的配置提供参考,方便生产线领班布线、对员工进行考核。
该《生产标准作业表》以产品代码为单位,采用文件受控发放到车间,领班使用时借用的形式进行管理。
08年12月份车间试行流动性生产模式后,iE组及时推出了《单件流生产模式工序排置表》,根据订单的产量计算生产节拍,安排工位人员配置,计算线平衡率,图标显示生产瓶颈工序,该《配置表》直观准确,易操作,对流动性生产模式的推行起到了积极作用。
目前为止共制作受控《生产标准作业表》100份,制作使用《单件流生产模式工序排置表》18份。
3.员工效率考核
通过标准工时的制定和核算平台的建立,iE组能准确的统计到车间、生产线甚至员工个人的工时利用率。
统计数据出来后,iE组考虑应该建立效率考核及奖励机制,以促进车间整体生产效率的提高。
08年10月份,公司调整员工薪资核算办法,取消计件工资全部采用计时工资。
记时工资下员工的作业积极性出现明显下降,员工中产生“干多干少一个样”的想法。
如何激励员工的工作效率,避免出现“吃大锅饭”的情况,iE组根据车间实际生产情况,及时制定了《包装组装材料准备线工资核算标准》,在记时工资的基础上设立效率奖,对员工工时利用率超过效率标准的进行奖励。
此《核算标准》的实施,极大的调动了员工的积极性,10月份车间组装准备线只有13位员工超过效率奖励标准拿到绩效奖,到11月份受奖的人数上升到18人,12月份为17人,特别是1-1线在11月份没有一个员工受奖,但在11、12月份1-1线分别有5、7人受奖。
在此基础上,iE组在12月份编制了《包装组装流水线工资核算标准》,针对车间组装生产为单件流动生产模式,设定生产线员工整体记时,订单生产应耗工时包干,实际工时低于应耗工时的部分进行奖励。
目前此办法正在试行并完善中。
4.流动性生产
在标准工时制定、核算系统运行、效率考核机制实施等工作步入正规后,iE组在08年11月下旬将工作重点转移到生产现场开展制程改善。
分析了生产现状后iE组决定开始导入流动性生产模式改变车间以往的工站式作业。
流动性生产模式以前在公司也没有试行过,iE组一边找资料一边结合车间生产进行设计,决定首先从7#线作为试点然后在车间推行。
12月10日对车间领班组长和7#线员工开展了流动生产的培训,12月11日开始上线试行。
试行的型号为H061客户LH055-3a44c4BT烫孔电池组,该型号工序复杂,不良率高,一直是生产线的老大难:
排产3000组25人至少需要10-11小时。
iE组在前期观测时发现生产线的工序配置存在不合理的情况,工序间作业等待造成时间浪费,根据标准工时计算人员排布应该3000组电池在8小时内20员工完成的。
我们就以此作为改善的目标。
通过iE组在前期的培训和现场的指导,7#线经过2天的适应和调整期就达成了20人8小时完成3000组的目标,效率达成96.78%。
产品不良率有改善前的8%下降到4%。
相当于每天节省工时30h,节省费用=30*7.15*1.5=320元。
流动性生产在7#线的成功,让车间其他生产线看到了甜头,实实在在的感受到现金生产模式对生产效率的提升。
员工对流动生产模式的实施十分配合,因为计划早做完他们就可以早下班休息,生产线领班通过实施流动性生产可以减轻管理工作,因为所有的员工都按照生产节拍在作业,产品按计划出成品,线上没有半成品,领班只要关注品质和处理异常就可以了。
iE组相续在包装车间全部组装生产线推行流动性生产模式,对车间生产效率的提升起到极大的推动作用。
08年12月份车间的工时利用率为72.88%,相对与11月份62.55%的利用率提升了10.33个百分点,上升率为16.5%,12月份包装车间生产的理论工时为20XX1小时,效率的提升相当于节省了出勤工时4548h,按加点工价计算当月节省费用=4548*5.17*1.5=35269元。
三:
产品品质
20XX年全年oQc抽检合格率平均93.48%。
离目标99%相差5.5%.特别是20XX年下半年以来,oQc抽检合格率呈直线式下降.原因分析为oQc在检验时判定标准发生转变的因素,但更重要的是车间在产能提升的情况下相因的领班及员工的培训工作没有及时跟上,导致出现员工品质意识下降,生产线管控不力的局面产生;20XX年下半年由于公司工资体制改革,车间原有的相关全检工位的激励机制未及时调整,导致全检工位员工的品质意识下降使oQc抽检合格率呈直线式下降,车间已认识到问题的严重性并已制定实施了新的管控措施,车间的品质状况开始扭转提升,车间计划在20XX年3月份将车间的出货检验合格率提升到96%以上。
四:
制程不良管控:
20XX年全年平均不良率高达7.27%.20XX年制程不良的数据是在生产管控部的监控下统计出来的.20XX年各月制程不良情况(见下表)
真实的数据为日后的生产改善指明了方向,通过对所生产的各种类型产品的不良数据进行分析,在20XX年车间开展了酌有成效的改善活动:
1、车间通过对H-0612B的整理由以前的有胶纸整理改为现在的有透明套整理;定