高分子材料成型加工技术的进展Word文档下载推荐.docx
《高分子材料成型加工技术的进展Word文档下载推荐.docx》由会员分享,可在线阅读,更多相关《高分子材料成型加工技术的进展Word文档下载推荐.docx(9页珍藏版)》请在冰豆网上搜索。
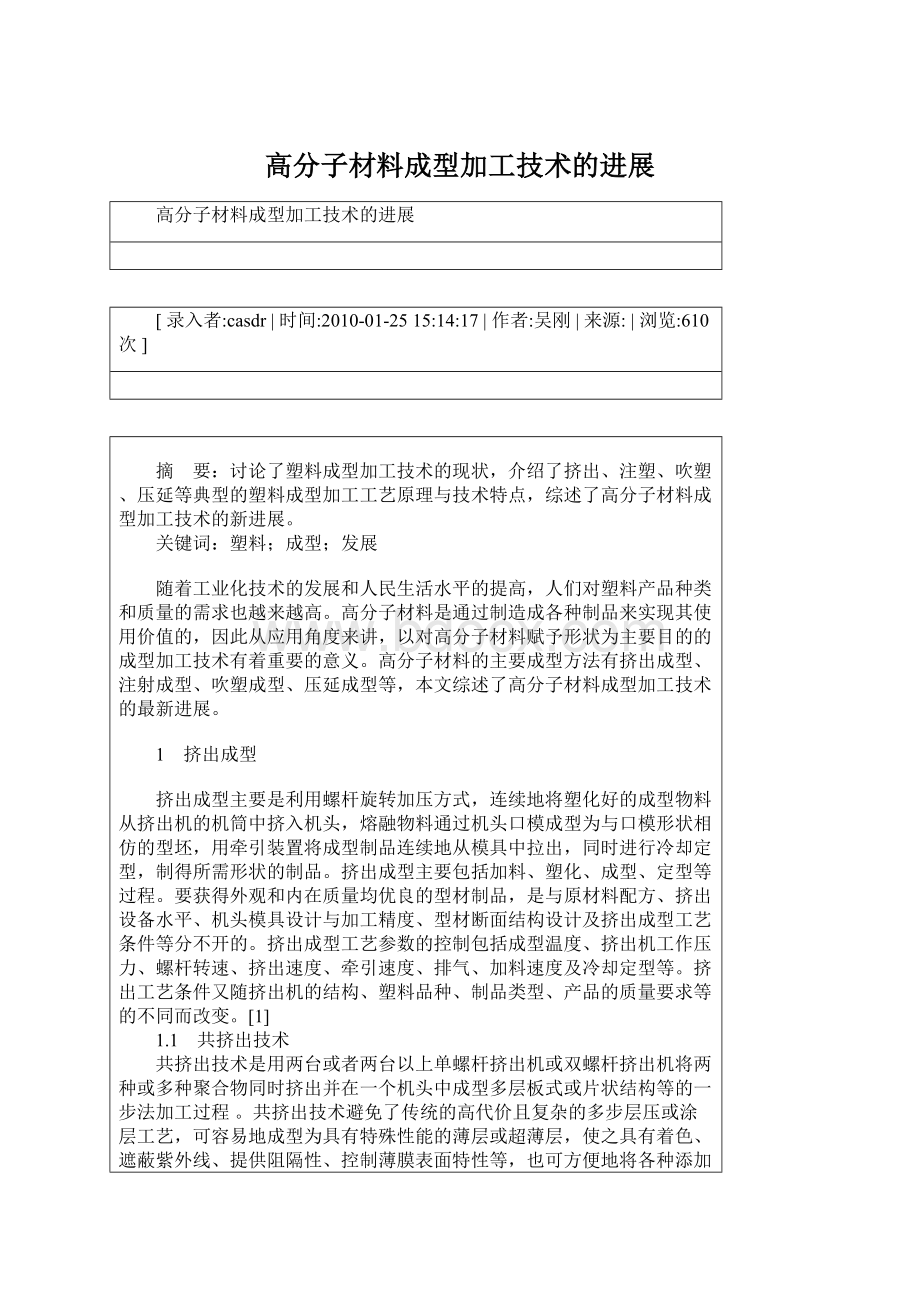
塑料;
成型;
发展
随着工业化技术的发展和人民生活水平的提高,人们对塑料产品种类和质量的需求也越来越高。
高分子材料是通过制造成各种制品来实现其使用价值的,因此从应用角度来讲,以对高分子材料赋予形状为主要目的的成型加工技术有着重要的意义。
高分子材料的主要成型方法有挤出成型、注射成型、吹塑成型、压延成型等,本文综述了高分子材料成型加工技术的最新进展。
1 挤出成型
挤出成型主要是利用螺杆旋转加压方式,连续地将塑化好的成型物料从挤出机的机筒中挤入机头,熔融物料通过机头口模成型为与口模形状相仿的型坯,用牵引装置将成型制品连续地从模具中拉出,同时进行冷却定型,制得所需形状的制品。
挤出成型主要包括加料、塑化、成型、定型等过程。
要获得外观和内在质量均优良的型材制品,是与原材料配方、挤出设备水平、机头模具设计与加工精度、型材断面结构设计及挤出成型工艺条件等分不开的。
挤出成型工艺参数的控制包括成型温度、挤出机工作压力、螺杆转速、挤出速度、牵引速度、排气、加料速度及冷却定型等。
挤出工艺条件又随挤出机的结构、塑料品种、制品类型、产品的质量要求等的不同而改变。
[1]
1.1 共挤出技术
共挤出技术是用两台或者两台以上单螺杆挤出机或双螺杆挤出机将两种或多种聚合物同时挤出并在一个机头中成型多层板式或片状结构等的一步法加工过程。
共挤出技术避免了传统的高代价且复杂的多步层压或涂层工艺,可容易地成型为具有特殊性能的薄层或超薄层,使之具有着色、遮蔽紫外线、提供阻隔性、控制薄膜表面特性等,也可方便地将各种添加剂如抗结块剂、抗滑移剂和抗静电剂等加入到需要的任何一层。
按照共挤物料的特性,可将共挤出技术分为软硬共挤、芯部发泡共挤、废料共挤、双色共挤等。
共挤出技术可以在一个工序内完成多层复合制品的挤出成型,绝大多数共挤出复合制品不需要基材和粘合剂,具有生产成本低、工艺简单、能耗低、生产效率高、制品种类多等特点,特别适合于生产复合薄膜、板材、管材等复合制品,是目前多层复合制品最有发展前景的复合成型技术之一,可供共挤出的物料不仅有聚合物,还可以是金属、无机材料等。
共挤出技术是当代广泛应用的先进的聚合物加工方法,共挤出技术已广泛应用于复合管材、复合薄膜、板材、异型材、光纤、电线、电缆等复合制品的生产,随着共挤出技术的发展,其应用领域会进一步拓宽。
多层共挤复合机头是研究和开发的热点,也是共挤复合研究的难点。
开发高效、节能的多层结构单机共挤出设备是共挤出设备的发展趋势。
[2]
1.2 挤出注射组合技术
挤出和注射成型组合的直接成型技术可将聚合物粉料与磁粉、无机颜料、玻璃纤维等通过双螺杆挤出机混合后直接注塑成型。
其突出优点是可以更加灵活地调节调节复合物的配方。
省去了造粒、包装、干燥等工序,大幅度地降低了设备费用和减少了生产时间、从而降低了成品的成本。
KraussMallei公司推出了型号KMl000-6100IMC的这种组合设备,一个特殊的注射装置与双螺杆挤出机相结合代替了传统的塑化单元,计量器将连续操作的挤出机和间歇操作的成型装置连接在一起。
Husky公司也推出了与阳模相连的OperionWerner&
Pfleiderer40mm双螺杆的挤出注射组合机。
该技术适用于多种材料的成型,即可为单个的聚合物,如ABS、AS、EVA、PA、PC、PE、PET、PBT、POM、PP、PS、PMMA、LCP等;
也可为复合材料,如聚合物与玻璃纤维(GF)、CaCO3、云母、滑石粉、硅石、颜料、Fe2O3的混合物;
还可为聚合物合金.如ABS、AS、PS、PVC、SAN合金;
PA/HDPE、PBT、PET合金及PC/ABS、PET、PBT合金等。
1.3 成型技术
挤胀成型技术是一种塑性成型方法,主要适用于加工细口制件或一些较复杂的中空制品,这些制品通常是采用旋转模塑、注塑或吹塑方法成型的。
其基本过程是:
预成型的管坯在组合外力的作用下沿径向向外扩张,通过塑性变形形成与模具型腔相一致的制品。
挤胀成型的基本工艺过程为:
将管坯放入模具并在管坯内填入胀形介质;
对管坯及其内部的胀形介质施加挤压力,使管坯材料在一定的应力状态下变形并流向其径向的模腔自由空间;
管坯在胀形介质产生的内压作用下不断变形,得到与模腔形状相同的制件;
外力撤消后,胀形介质恢复原状或散开,从制品内部取出。
[3]
挤胀成型技术出现于20世纪40年代的金属成型加工领域,虽然没有在塑料加工领域获得广泛的应用,但与常规的塑料成型技术相比,这种方法具有以下特点:
成型设备结构相对简单,成型模具的结构简洁;
被加工材料不产生相变而且成型过程通常都是在较低温度下进行,能耗低;
控制系统比较简单,工艺控制十分灵活,通过控制挤胀行程,利用同一副模具有可能得到不同尺寸的制品;
能充分利用挤出制型坯的高生产率和低成本;
在生产批量较小的情况下能大幅度降低生产成本。
1.4 反应挤出工艺
反应挤出工艺是连续地将单体聚合并对现有聚合物进行改性的一种方法,因可以使聚合物性能多样化、功能化且生产连续、工艺操作简单和经济适用而普遍受到重视。
该工艺的最大特点是将聚合物的改性、合成与聚合物加工这些传统工艺中分开的操作联合起来。
反应挤出成型技术是可以实现高附加值、低成本的新技术,已经引起世界化学和聚合物材料科学与工程界的广泛关注,在工业方面发展很快。
与原有的成型挤出技术相比,有明显的优点:
节约加工中的能耗;
避免了重复加热;
降低了原料成本;
在反应挤出阶段,可在生产线上及时调整单体、原料的物性,以保证最终制品的质量。
反应挤出机是反应挤出的主要设备,一般有较长的长径比、多个加料口和特殊的螺杆结构。
它的特点是熔融进料预处理容易;
混合分散性和分布性优异;
温度控制稳定;
可控制整个停留时间分布;
可连续加工;
未反应的单体和副产品可以除去;
具有对后反应的控制能力;
可进行粘流熔融输送;
可连续制造异型制品。
1.5 固态挤出工艺
固态挤出有直接固态挤出和静液压挤出两种方法,是指使聚合物在低于熔点的条件下被挤出口模。
固态挤出一般使用单柱塞挤出机,柱塞式挤出机为间歇性操作。
柱塞得移动产生正向位移和非常高的压力,挤出时口模内的聚合物发生很大的变形,使得分子严重取向,其效果远大于熔融加工,从而使得制品的力学性能大大提高。
2 注射成型技术
注射成型技术是目前塑料加工中最普遍的采用的方法之一,可用来生产空间几何形状非常复杂的塑料制件。
由于它具有应用面广,成型周期短,花色品种多,制件尺寸稳定,产品效率高,模具服役条件好,塑料尺寸精密度高,生产操作容易,实现机械化和自动化等诸方面的优点。
因此,在整个塑料制件生产行业中,注射成型占有非常重要的地位。
目前,除了少数几种塑料品种外,几乎所有的塑料(即全部热塑性塑料和部分热固性塑料)都可以采用注塑成型。
注射成型技术的发展主流一般以多种方式的组合为基础,具有如下技术特征:
(1)以组合不同材料为特征的注射成型方法,如镶嵌成型、夹心成型、多材质复合成型、多色复合成型等;
(2)以组合惰性气体为特征的注射成型方法,如气体辅助注射成型、微孔泡沫塑料注射成型等;
(3)以组成化学反应过程为特征的注射成型方法,如反应注射成型、注射涂装成型等;
(4)以组合压缩或压制过程为特征的注射成型方法.如注射压缩成型、注射压制成型、表面贴合成型等;
(5)以组合混合混配为特征的注射成型方法,如直接(混配)注射成型等;
(6)以组合取向或延伸过程为特征的注射成型方法,如磁场成型、注拉吹成型、剪切场控制取向成型、推拉成型、层间正交成型等;
(7)以组合模具移动或加热等过程为特征的注射成型方法,如自切浇口成型、模具滑合成型、热流道模具成型等。
2.1 辅助注塑技术
2.1.1 气体辅助注射成型
气体辅助注塑GAIM技术比普通注塑多一个气体注入阶段,由气体推动塑料熔体充满模具型腔。
GAIM具有节省原料、减少合模力、缩短冷却时间、防止制品缩痕、减少内应力、减少或消除制品翘曲、提高制品表面性能、提高生产效率、降低生产成本等优点。
气体辅助注射成型近年来发展较快,国外很多公司相继开发了具有不同特征的新方法,如日本旭化成公司的AGI法、三菱工程塑料公司的CINPRES法及出光石油化学公司的GIM法等,但各方法的基本原理完全相同。
气体辅助注射成型的工作过程可分为四个阶段:
第一阶段为熔体注射,即将熔融的塑料熔体注射到模具型腔中,分为“欠料注射”和“全料注射”。
第二阶段为气体注射,可于注射期的前、中、后期注入气体,气体的压力必须大于塑料熔体的压力以达到使塑件成中空状态:
第三阶段为气体保压当塑件内部被气体充填后,制件在保持气压的情况下冷却,气体由内向外施压使制品外表面紧贴模壁,通过气体二次穿透从内部补充因冷却带来的体积收缩。
第四阶段为制件脱模,随着冷却周期的完成,排出气体,塑件由模腔取出。
气体辅助成型的塑料制件大致可分为三类:
管形和棒形制件如衣服架、扶手、椅背、刷棒、方向盘,主要是利用气体穿透形成气道来节省材料和缩短成型周期;
板状制件如汽车仪表板、办公家具,主要是减小翘曲变形和对注塑机的吨位要求,以及提高制件的刚性、强度和表面质量;
厚薄不均的复杂制件如家电外壳、汽车部件可通过一次成型简化工艺。
2.1.2 水辅助注塑WAIT成型技术
水辅助注塑WAIT成型中空制品的原理与GAIM的基本相似,其过程由5个步骤组成:
①注射塑料熔体;
②注入水以推动塑料熔体型芯;
③保持水压(还可以不断注水);
④释放压力,通过重力或压缩空气将水排出,如果加工温度高水蒸汽的压力也可以排水;
⑤开模。
WAIT有短射、回流注射、溢流注射和流动注射4种成型方式。
目前,WAIT可以应用于中空弯曲件、杆件、截面厚薄不同的复杂件、较大薄壁件的成型,例如介质导管、汽车门把手、汽车顶梁、踏板、扶手、带支架的板件等制品的生产。
[4,5]
2.2 电磁式聚合物动态塑化注射成型
电磁式聚合物动态塑化注射成型的要点是在电磁式直线脉冲驱动的注射装置中,由电磁场产生的机械振动力场被引人物料的塑化、注射、保压全过程,实现了动态塑化注射成型全过程均处于周期性振动状态.这种过程完全不同传统螺杆式塑化注射过程。
螺杆在电磁式直线脉动驱动装置的作用下向前直线脉动位移,将熔体注入模腔,熔体的压力将随螺杆的脉动而周期性变化,这种作用同样使熔体粘度及弹性降低,流动阻力减小,加速了充模过程。
模腔充满熔体后,螺杆继续作轴向脉动,保持模腔中物料压力周期性变化,使物料的温度、内应力得到均化,同时冷却缩孔能得到快速补充熔料,保压时间可缩短。
如果选用与无振动力场的稳态充模保压过程相同熔体流动阻力,则熔体温度及模腔温度可以降低,制品质量可以提高,解决了传统注射成型技术中注射温度高、成型制品所需冷却时间长的问题。
该成型方式可以降低成型温度及压力,提高生产效率,降低能耗。
2.3 微孔泡沫塑料注射成型
国内外微孔塑料的成型主要有间歇成型、连续挤出成型和注射成型等技术。
与传统塑料发泡技术比较,微孔塑料发泡注射成型技术既不需要化学发泡剂,也不要以烃基为原料的物理催化剂、发泡剂等及其它相关反应成分。
微孔泡沫塑料注射成型已可生产壁厚为0.5mm的薄壁大部件及尺寸精度要求高的、形状复杂的小部件。
它推翻了长期一直认为发泡成型只能完成厚壁制品的生产的观点。
与传统的发泡成型形成的最小孔径为250μm的不均匀的微孔相比。
现在的工艺形成的微孔大小均匀.孔径在5~50μm,这样的微孔结构也赋予比传